Learning center
Welcome to our Learning Center. We're here to help.
Thank you! Your submission has been received!
Oops! Something went wrong while submitting the form.
No results found.
Maintenance Software
10 Articles
Frequently asked questions from Maintenance Professionals
Maintenance Applications
10 Articles
Frequently asked questions from Maintenance Professionals
Maintenance Type Comparisons
10 Articles
Frequently asked questions from Maintenance Professionals
Maintenance Roles
10 Articles
Frequently asked questions from Maintenance Professionals
Maintenance Types
10 Articles
Frequently asked questions from Maintenance Professionals
Maintenance Concepts
10 Articles
Frequently asked questions from Maintenance Professionals
Get more done with MaintainX
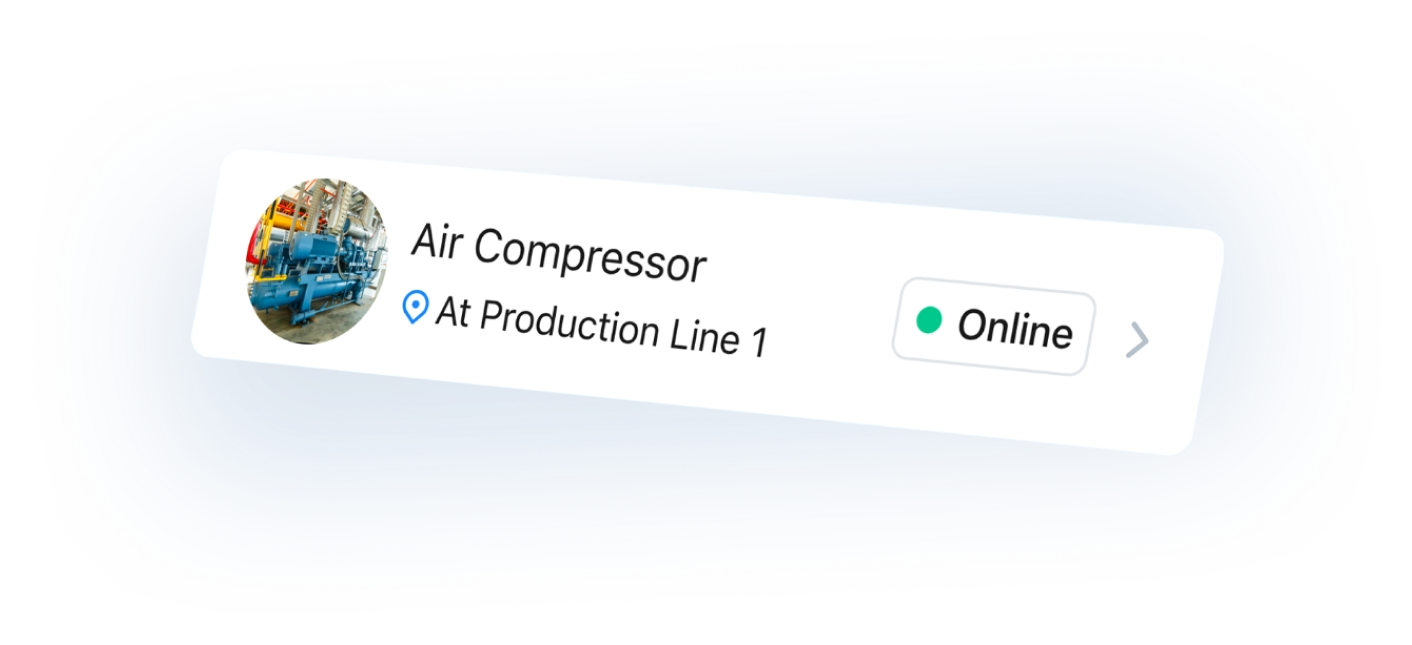
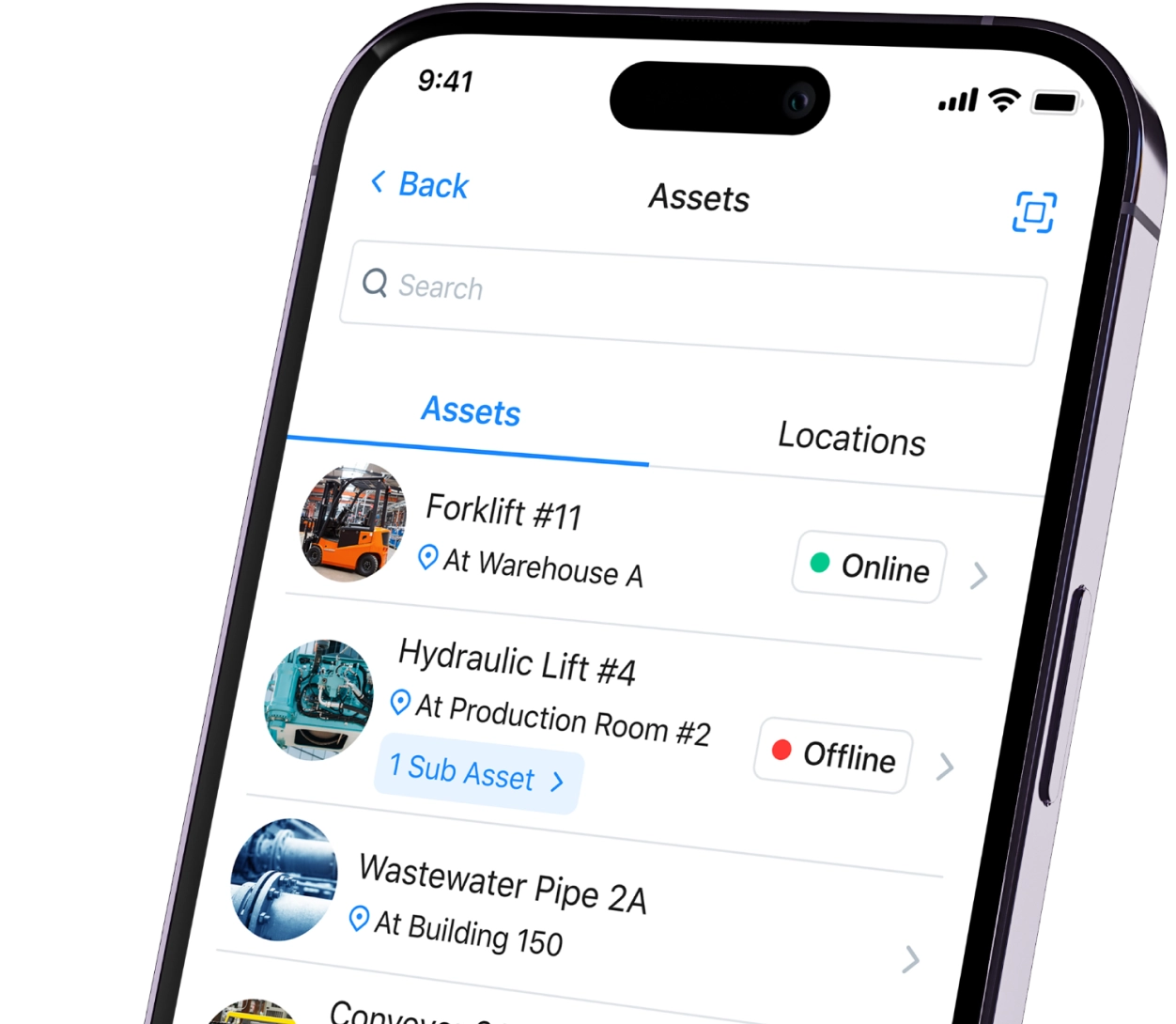