Maximizing production while maintaining quality is a goal every manufacturing company has. However, getting there can be challenging. To help understand how effective their facilities’ production floor is, manufacturing professionals calculate their production efficiency.
Production efficiency refers to a manufacturer's ability to produce the highest possible quantity of a product without reducing the level of production of other products or compromising quality. In this article, we’ll further define what production efficiency is, how to calculate it, explore challenges to peak production in the manufacturing process, and explore strategies to improve efficiency and marginal cost.
What is production efficiency?
As mentioned above, the concept of production efficiency is used in economics to describe how well a company can make its products. It means making the most of a company’s available resources, like raw materials and machines, without making the products worse or a smaller number of units. A manufacturer can calculate its production efficiency by using the actual output and standard output. To calculate their efficiency, the production of one product must not lower the production level of another.
Productive efficiency is achieved by operating at maximum capacity and without wasting resources. Doing so provides the conditions needed to produce products at the lowest possible unit cost. The higher production leads to higher revenue and lower wasted resources, both of which lead to lower costs. Combined, they translate into more profits.
To be clear, production efficiency assumes no change in the quality of the product. It’s relatively easier to increase production and minimize costs when you lower the quality of the product. However, when calculating it, you must always ensure that the product quality is constant.
How to calculate production efficiency
Production efficiency is the ratio between your actual output and standard output. To achieve production efficiency, your actual output should equal the standard output. You can use the following formula to analyze your current output for efficiency:
Production Efficiency = (Actual Output ÷ Standard Output) x 100
When the answer to this formula is 100%, you’ll have achieved productive efficiency.
Finding Actual & Standard Output
Understanding what actual and standard outputs are, as well as how to find them, is fairly straightforward. First, let’s define both terms:
- Actual Output: Actual output refers to the real quantity of goods produced by a company in a given period. It is the measured output that a company achieves, which can be influenced by various factors such as machine downtime, worker performance, material availability, and quality issues.
- Standard Output: Standard output, also known as expected output or planned output, is the quantity of goods that a company aims to produce in a given period under normal operating conditions. It is typically based on factors such as the company's production capacity, historical performance, and forecasted demand.
To find your actual output, simply count the number of finished units produced during the production period. Usually, this is tracked in manufacturing software and won’t have to be done manually. For example, if a company plans to produce 1,000 units of a product in a week but only manages to produce 800 units due to unexpected challenges, the actual output would be 800 units.
Finding your standard output rate may seem complicated, but there are two easy methods to find it. First, you can refer to the asset manufacturer’s provided data on what the maximum output is at full capacity. For example, if a company has the capacity and plans to produce 1,000 units of a product in a week, assuming no unexpected issues occur, the standard output would be 1,000 units. Another method can be by looking at historical data and using the full capacity units produced from your own facility.
Example of how to calculate production efficiency
Let’s explore an example of how to calculate production efficiency. For instance, say you can produce 10,000 units per month of product A when you utilize full capacity. You produced 7,500 units during the previous month. Here is how you’d calculate it in this case:
(7,500 ÷ 10,000) x 100 = 75%
When calculating efficiency, your inputs for the formula (actual and standard output) will generally be per unit of time. You should ensure that you’re consistent with units of time per output to get an accurate answer.
For instance, in the previous example, if you had produced 7,000 units in 25 days, you’ll need to convert that number into monthly production:
(7,000 ÷ 25) x 30 days = 9,000
Comparing the actual and standard output is the simplest way to calculate production efficiency, but you can also use other metrics like overall equipment effectiveness (OEE) scores.
Why it’s hard to reach peak production efficiency
Reaching peak productivity is the goal every manufacturer wants to achieve. Getting there, however, is often filled with complex challenges. Let’s explore challenges that make it hard to reach peak production efficiency.
Unplanned downtime
Manufacturers face unplanned downtime for many reasons. Aging equipment, poor processes, and more can cause important assets to go offline, screeching production to a halt. Maintaining equipment and avoiding downtime go hand in hand with reaching peak production efficiency.
To help manage maintenance tasks and improve asset health, performance, and reliability, many teams are turning to computerized maintenance management systems (CMMS). MaintainX’s top-rated solution helps reduce unplanned downtime by 32%.
Supply chain disruptions
Disruptions in the supply chain became prevalent and relevant during the COVID-19 pandemic. Years later and the effects are still felt around the world. From parts shortages to increased shipping prices, supply chain issues make it harder to reach peak production.
Many manufacturers and maintenance professionals are starting to understand the value of strong inventory management. CMMSs like MaintainX help ensure your spare parts inventory is easy to manage so nothing cuts into production time. Not only does inventory management help keep assets online and producing, but it can save money. Duracell trusted MaintainX for their parts inventory and saved $50,000.
Regulatory compliance
Some manufacturers face strict regulatory requirements. However, these obligations can take time and be a headache when you’d rather identify waste and improve production processes. The consequences of failing compliance checks can be dire and lead to major fines or even a total halt to production.
Make regulation easy with MaintainX. The user-friendly platform allows for quick and convenient completion of regulatory tasks. A paper trail of regulatory work can easily be found, ensuring you’re ready for an audit and don’t have to worry about digging through filing cabinets to prove compliance. Team members can conveniently access quality control checklists, safety audits, and PMs from a tablet or phone.
4 Strategies to improve production efficiency
Once you’ve calculated your company’s production efficiency, you can start working towards improving it. Below are four ways to improve production efficiency:
1. Standardize your processes
Your workflows and internal processes are crucial to improving production efficiency. Standard operating procedures (SOPs) directly impact productivity and help maintain product quality across batches. Creating and refining SOPs for almost every process in your company is a great way to begin improving production efficiency.
For instance, you can standardize the process of bringing ready-to-ship goods into the warehouse, stacking them per purchase orders, and then handing them over for shipping.
You also can standardize the process of communicating these details to managers and workers. Efficient communication fills in information silos across departments and provides management the visibility it needs to improve a procedure’s efficiency.
2. Identify and eliminate bottlenecks
Equipment-related bottlenecks are easily noticeable when you’re striving for efficient production. In many cases, though, bottlenecks like equipment downtime are a result of inefficient maintenance procedures rather than anything else. A robust preventive maintenance program is key to minimizing equipment errors and improving efficiency.
You also can analyze the equipment that consistently records backlogs in production. Investigate to find the bottlenecks causing the backlog and create work orders to resolve those issues.
Of course, other potential bottlenecks can result from supply chain issues, unplanned downtime, or poor parts inventory management. For instance, your vendor might significantly delay one of your deliveries, causing the production to grind to a halt.
3. Minimize waste
Accidentally creating defective units wastes production capacity. Those wasted units decrease the overall production efficiency, even without equipment downtime.
However, minimizing waste is easier said than done. Luckily, lean manufacturing methodologies can help you make small, incremental improvements that have a significant impact over time.
You can make these improvements by implementing techniques like Kaizen and Six Sigma. They may take a while to bring about a tangible improvement, but you’ll see marginal improvements in your production efficiency right from the early days of implementation.
4. Use technology
Modern technology automates repetitive tasks, fast-tracks internal processes, and frees up employee time for other, more productive tasks. For instance, if you’re still recording inventory on paper, you’re losing out on the efficiencies that an online inventory management tool can offer.
Instead of spending time manually recording inventory movement, let the inventory management software monitor it. This will allow your maintenance team to focus on other strategic aspects, such as better storage space utilization.
Technological solutions no longer come with a hefty price tag, and the return on investment (ROI) is usually worth it.
For instance, CMMS maintenance software like MaintainX helps automate workflows, communicates effectively with your team, and gives you access to an enterprise asset management system for a nominal price. Even with its small price tag, the mobile-friendly CMMS can save you money with its advanced reporting and in-depth KPI insights.
Improving production efficiency with a CMMS
Improving production efficiency isn’t easy, especially when a business is too comfortable with traditional methodologies and reluctant to invest in technology. Adopting a CMMS simplifies the process and helps ensure you have accurate data to work from, allowing you to increase production efficiency.
Eliminate unplanned downtime for greater production
Adopting a powerful CMMS like MaintainX helps improve maintenance processes and efficiency. With better maintenance, asset health increases, and your team can manage maintenance tasks faster.
As asset health improves and maintenance happens more efficiently, your team will experience less unplanned downtime. This, in turn, allows your team to increase production numbers, boosting overall production efficiency.
Identify bottlenecks to reduce waste
MaintainX’s top-rated CMMS software helps teams improve maintenance processes by ensuring no tasks are missed and providing essential information. With greater visibility into your operations, it becomes easier to identify bottlenecks and implement improvements.
With smarter, streamlined processes, you can improve product quality, increase actual output rate, drive down defects, and eliminate waste. This, in turn, improves your team's production efficiency.
Ready to try MaintainX? The #1 rated CMMS on the market is free to try. Get started today and improve your production efficiency with ease!
Production Efficiency FAQs
Production efficiency works by comparing your actual production to the standard, maximum capacity your production floor can handle. This ratio helps provide an understanding of how efficiently your team is working.
Having sound, accurate data is essential to improving production efficiency. By analyzing the data, you can identify areas for improvement. For example, if one production line requires more maintenance than others, it may be a sign that equipment needs to be replaced to reach maximum production efficiency.
Yes, every manufacturer should track production efficiency. While there are other metrics, production efficiency can be used to track month-over-month or year-over-year efficiency to understand a facility’s performance. Doing so makes it easier to identify bottlenecks and protect your bottom line.
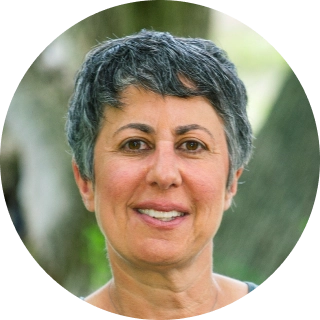
Caroline Eisner
Caroline Eisner is a writer and editor with experience across the profit and nonprofit sectors, government, education, and financial organizations. She has held leadership positions in K16 institutions and has led large-scale digital projects, interactive websites, and a business writing consultancy.
See MaintainX in action