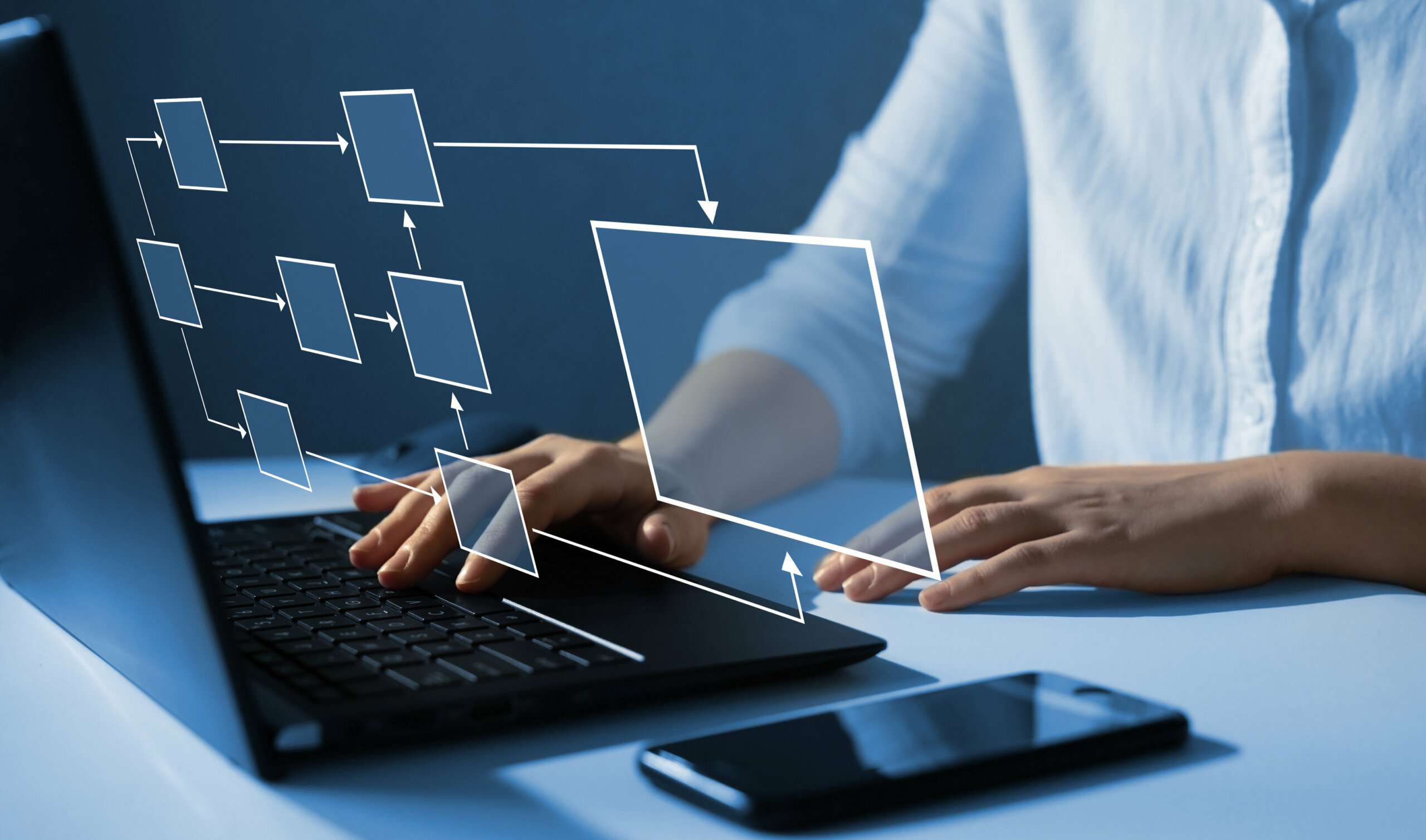
Most of us want to be productive at work. But that can be challenging when we don’t know exactly what to do. This is where a standard operating procedures (SOPs) workflow comes into play. SOPs refer to documented guidelines that break routine tasks into standardized step-by-step instructions.
Effective standardization enhances operational efficiency, improves quality control, and increases worker safety. There’s just one problem—SOPs aren’t always as effective as they could be. One simple way to improve SOP fulfillment is to combine them with workflow charts.
In this guide, we’ll discuss the different types of workflows, their many benefits, and how to create effective maintenance work order process flow chart. Implement the following tips, and you’ll soon find yourself answering fewer questions about work orders and spending more time optimizing processes!
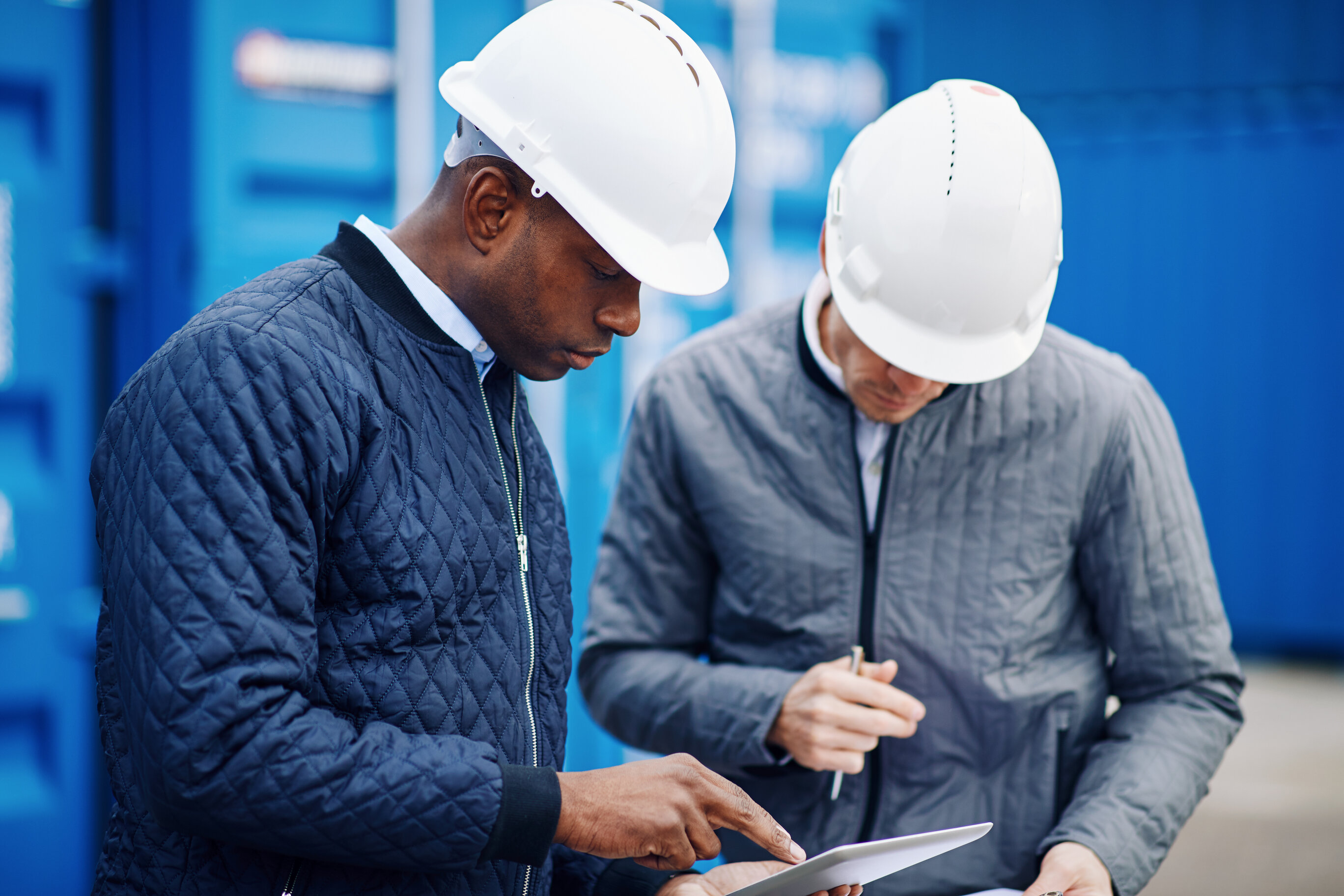
How to Create a Workflow (for Standard Operating Procedures)
First things first—there are no downsides to standardizing business processes. But this doesn’t mean organizations will experience immediate results after implementing SOP programs.
SOPs generally falter for three reasons:
- Employees can’t easily access them (written documents remain in file cabinets).
- Managers don’t write them in clear, concise, and jargon-free language.
- Complex procedures require more explanation than simple checklists can provide.
Beyond using mobile work order software to circulate well-written SOPs, managers can provide workers with illustrated SOP workflows to reduce confusion.
“Efficient manufacturing workflows can help businesses reduce waste and cut costs, ensuring a manufacturer remains competitive in the marketplace.”
Andrew McDermott
A simple way to understand the importance of workflows is to consider a vehicle’s navigation system. Nowadays, if a driver runs into an unexpected roadblock, the driver usually consults the virtual roadmap for alternative routes. Similarly, good workflows make it easier to execute assigned tasks and change directions as needed. So, what exactly is a standard operating procedure workflow process?
What Is a Workflow Process?
Standard operating processes workflows are visual representations of predetermined actions. They help workers execute tasks as efficiently as possible from start to finish. Workflows can involve one employee or several, depending on the work at hand. They include the necessary steps, resources, and instructions to get work done.
Manufacturing project managers, for example, often divide workflows into the categories of sequential and parallel. Sequential workflows direct employees to complete steps in a numbered order. Parallel workflows allow for executing multiple stages simultaneously.
Following either format should lead to the same result every time, regardless of who completes the task. You can assign workflows alone or as a supplement to a comprehensive SOP.
MaintainX users can attach workflow illustrations as PDFs to digital work order assignments. This way, workers can always access the workflow documentation they need via tablet or smartphone.
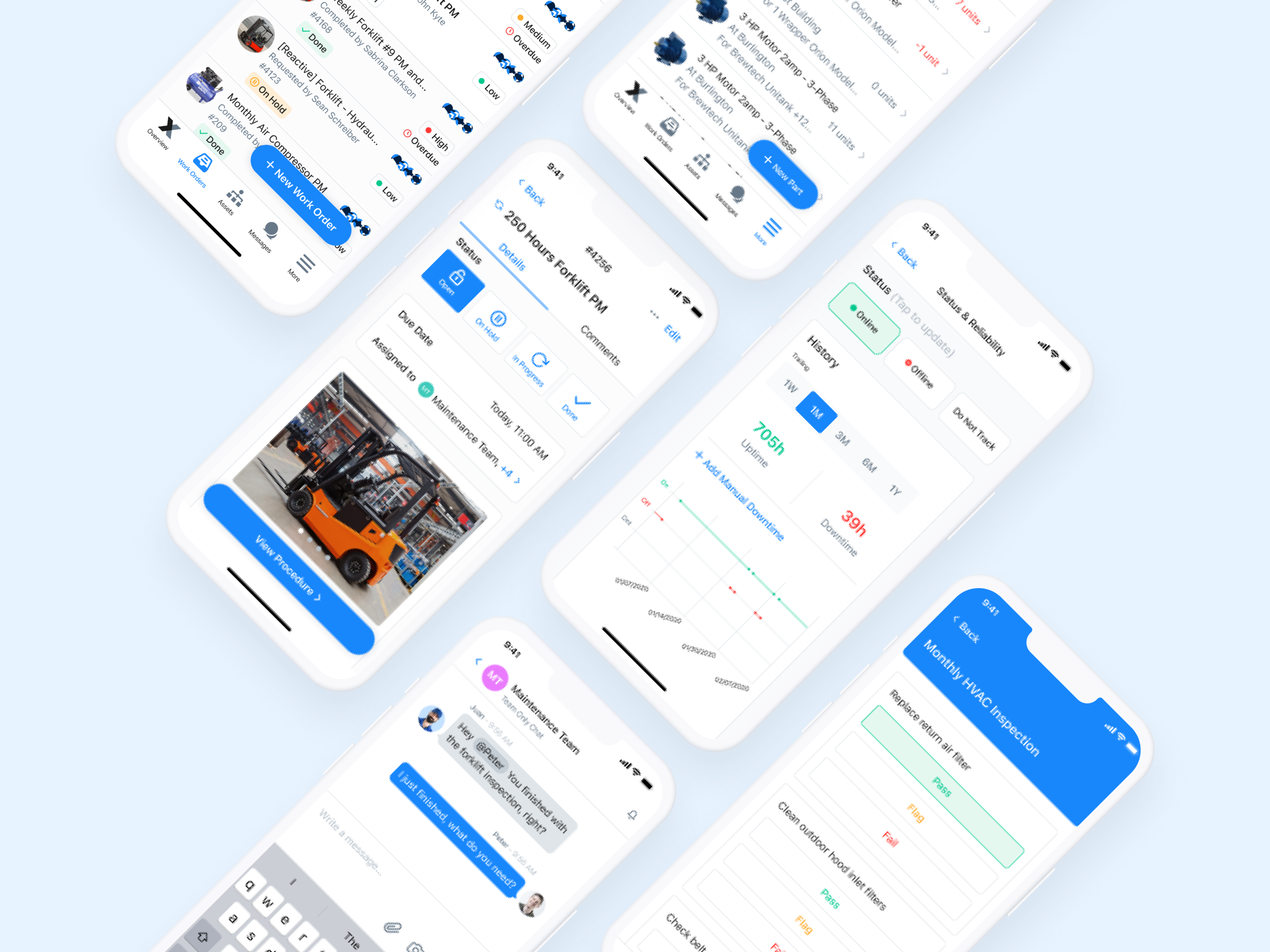
Six Benefits of Using Workflows
As mentioned above, workflows help employees complete tasks with less confusion. Several additional benefits to visually outlining processes, include:
1. Increased Consistency
Consistency is the hallmark of longstanding organizations, regardless of industry. Workflows enable managers to standardize routine processes. These processes lead to consistent output. This is especially vital to manufacturers, warehouses, and sectors that follow stringent quality-control regulations.
2. Enhanced Productivity
Standardizing workflow processes relieves employees from the burden of making difficult decisions under pressure. Instead of wavering over how to resolve unexpected problems, they can quickly identify an approved course of action.
3. Increased Transparency
Many organizations—particularly those in the healthcare, manufacturing, and data security industries—are subject to strict penalties in the event of non-compliance. Documented workflows act as “cheat sheets” to help operational managers monitor activities for oversights, mistakes, and violations. Instead of racking their brains to remember complex regulatory details, managers can quickly reference visual aids within automated workflows. In addition, established workflows can act as audit trails for proof of compliance during third-party inspections.
4. Increased Autonomy
Good workflows empower employees to make good decisions without management input. They ensure that everyone understands their unique responsibilities and how they relate to comprehensive processes. The more autonomy workers have, the more time managers have to optimize operations for greater efficiency.
5. Streamlined Training
Companies spend significant time, money, and energy training new hires. The average cost of onboarding a new employee is $4,129. Onboarding workflow diagrams streamline the process by removing the necessity to walk employees through every procedural step in real time. Furthermore, existing employees can transition into new roles more quickly.
6. Minimized Delays
Workflow management systems enable organizational leaders to identify better project timelines, potential bottlenecks, and necessary resources for completion. Workflow automation further ensures everyone understands their roles.
Other incentives to use workflows include enabling businesses to establish employee ground rules, supporting quality improvement programs, and enhancing company cultures. Before creating your first workflow, it’s helpful to break the document down into its essential elements.
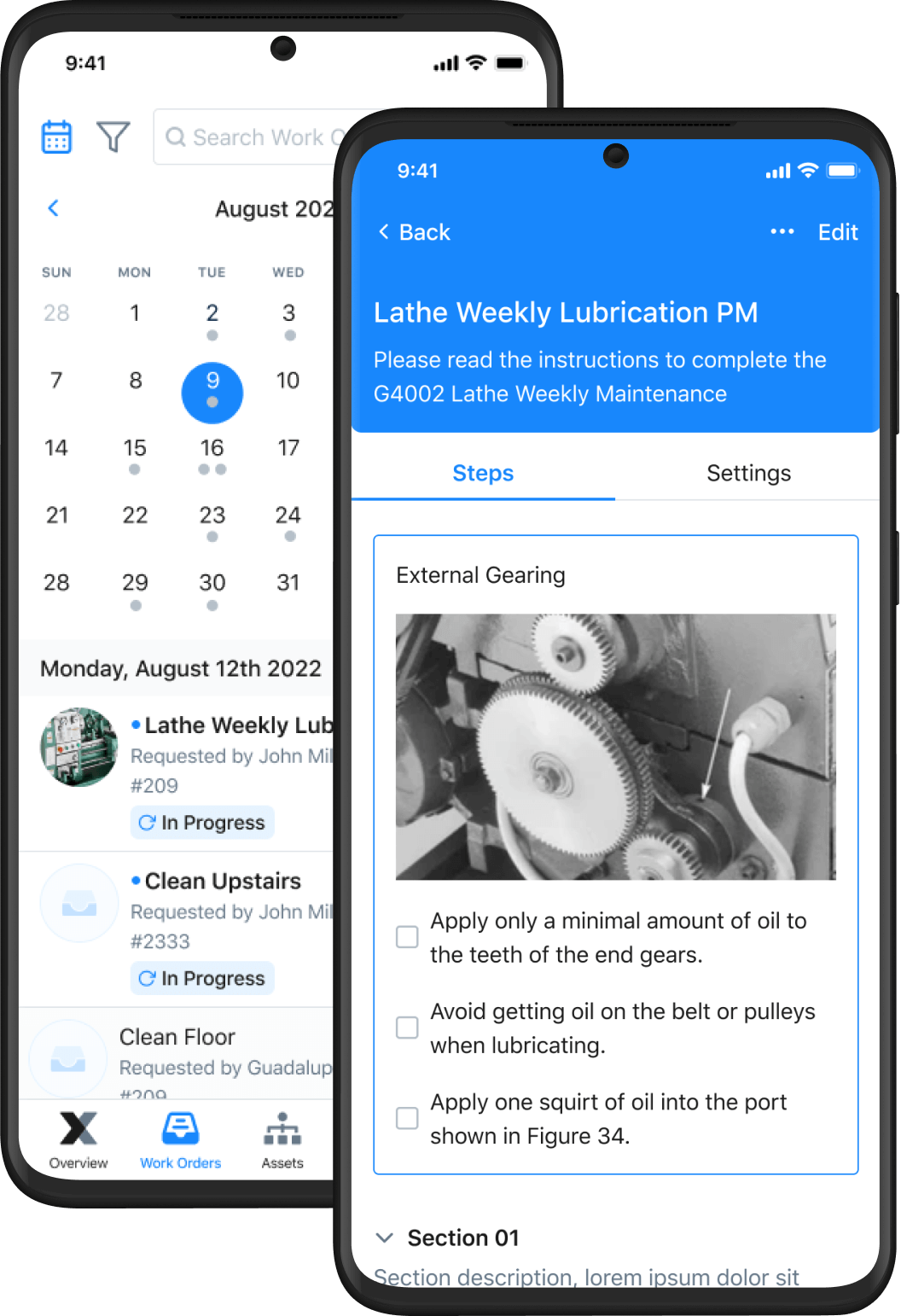
3 Elements of Standard Operating Procedure Workflows
All workflows share the following three components:
- Input: These are the resources needed to perform the given steps. Examples of input include team members, machinery, raw materials, assets, and other workflow tools.
- Transformation: Also referred to as processes, this workflow aspect refers to the workflow steps that illustrate how to apply the input. Predefined rules are the building blocks that lead to the third element—output.
- Output: This includes the planned physical product, service, or desired outcome. It’s worth emphasizing that output isn’t limited to deliverables. For example, an onboarding workflow would result in a skilled employee who is now an asset to the organization.
With that said, business process management includes several types of workflows, as discussed in our next section.
Types of Workflows
Below are the most common workflow types:
Process Workflow
Process workflows are the primary focus of this article and what most managers envision when using the term “workflow.” Also known as sequential workflows, these diagrams break processes into bite-sized steps within a visual format. The primary advantage of process workflows is their ability to convey a large amount of information in a scannable format.
Project Workflow
Project workflows are less common than process workflows. However, they are handy for focusing on particular projects that involve broad benchmarks. For example, we’re currently in the process of redesigning our Website at MaintainX. Before we began the process, our designers created a project workflow to set milestones for task completion. This document has helped us stay on task, on time, and on budget.
Case Workflow
Also known as rules-driven workflows, this type of workflow is ideal for ambiguous projects. For example, say an insurance agent is handling a new case. The initial steps involved are the same for every case, regardless of the scenario. But the roadmap can drastically change as participants reveal further information over time. Case workflows are ideal for such instances where “if, then” booleans determine the next steps.
Now, let’s look at some quick examples of workflows in the wild.
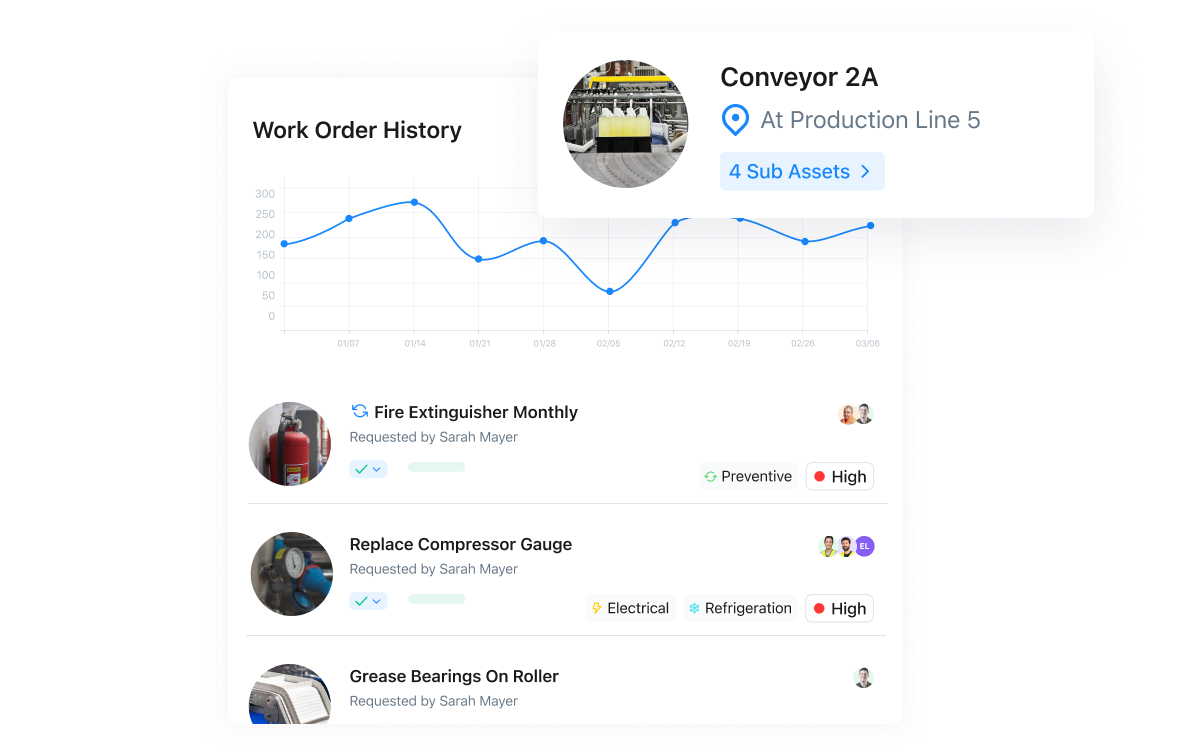
Examples of SOP Workflow Use
Practical workflow applications vary based on business size, type, and industry. Here are a few examples of typical workflow use cases:
Employee Onboarding
Employees always leave; it’s a fact of doing business. In 2018, U.S. companies experienced a 15 percent average voluntary turnover rate. Employee onboarding involves many roles, from accounting to IT departments, within most organizations.
Paperwork must be signed. System access must be granted. Orientations must be scheduled. Many organizations rely on standard operating procedures to streamline these routine processes. The more complex the onboarding process, the more likely the company will use a workflow.
Customer Onboarding
Providing satisfying onboarding experiences for new customers is crucial to nurturing long-term relationships. Depending on the product or service, this process may include coordinating several departments, from sales to marketing to account management. Effective workflows help employees stay on top of the many details that provide exceptional customer service.
Pharmaceutical Manufacturing
Lastly, pharmaceutical manufacturing enterprises are known for using workflows when testing and inspecting raw materials for production and post-production. They follow a particular type of workflow process called cold chain logistics when shipping products. Quality control measures are essential to keeping customers safe and maintaining FDA compliance.
Other sectors that commonly use workflows include military, travel, and human resources.
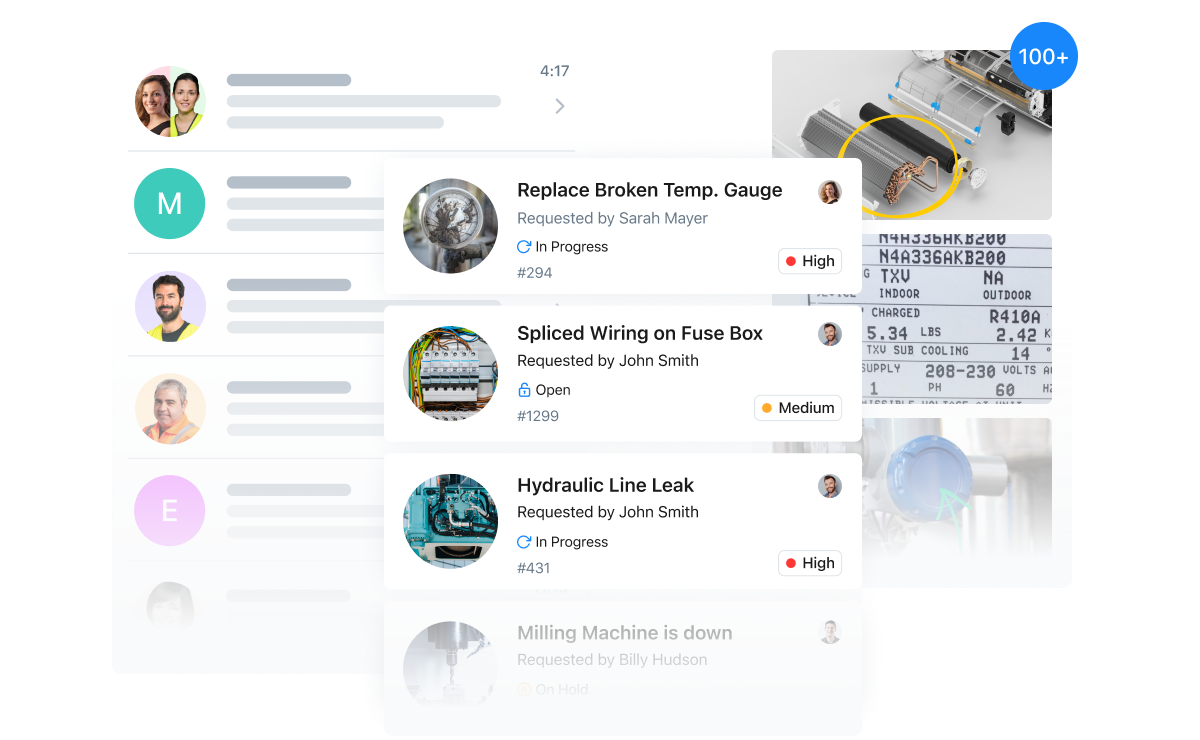
How to Create a Standard Operating Procedure Workflow Chart (in 3 Steps)
Creating a workflow chart is, actually, quite simple. The hard part is making sure the chart includes all the right information and leaves out unnecessary tidbits.
Effective workflows present team members with enough information to understand how to complete tasks at a glance. Complex steps may require additional explanation via attached work instructions in paragraph form. The good news? There are no hard rules on what you can and can’t do. The goal is to find that sweet spot between over- and under-explaining complex processes in visual form.
Step 1. Revisit Your Standard Operating Procedure
Before you create your workflow chart, it’s crucial to have a firm grasp of the procedure at hand. Jumping into drafting a visual representation without conducting your due diligence may result in missed steps that lead to defective deliverables. Follow these basic steps to evaluate what information to include in your illustration:
- Engage relevant employees to glean first-hand insights into the SOP.
- Ask for input from relevant experts, specialists, and executive leaders.
- Consult regulatory agencies for updated safety guidelines (if applicable).
- Identify potential forms of production waste you can eliminate.
- Write your work instructions from the end user’s perspective.
Once you have fine-tuned your SOP documentation, you’re ready to design your workflow chart. Click here to read more about How to Develop Standard Operating Procedures
Step 2. Create Your SOP Workflow Diagram
The best workflow charts are spacious, colorful, and easy to read. You can create a simple diagram using Microsoft Word or make a “fancier” one using workflow-specific software. Some of the best platforms for creating digital workflow charts include Microsoft Visio, Draw.io, and SmartDraw.
Step 3. Distribute the Workflow
Finally, print or export your workflow as a PDF to share with relevant employees.
Depending on your purposes, you may want to use an Enterprise Resource Planning (ERP) system or a CMMS to distribute your chart electronically. MaintainX CMMS makes it easier than ever to digitally attach workflows to work orders, create SOP checklists, and maintain a bird’s eye view of maintenance technician progress in real-time.
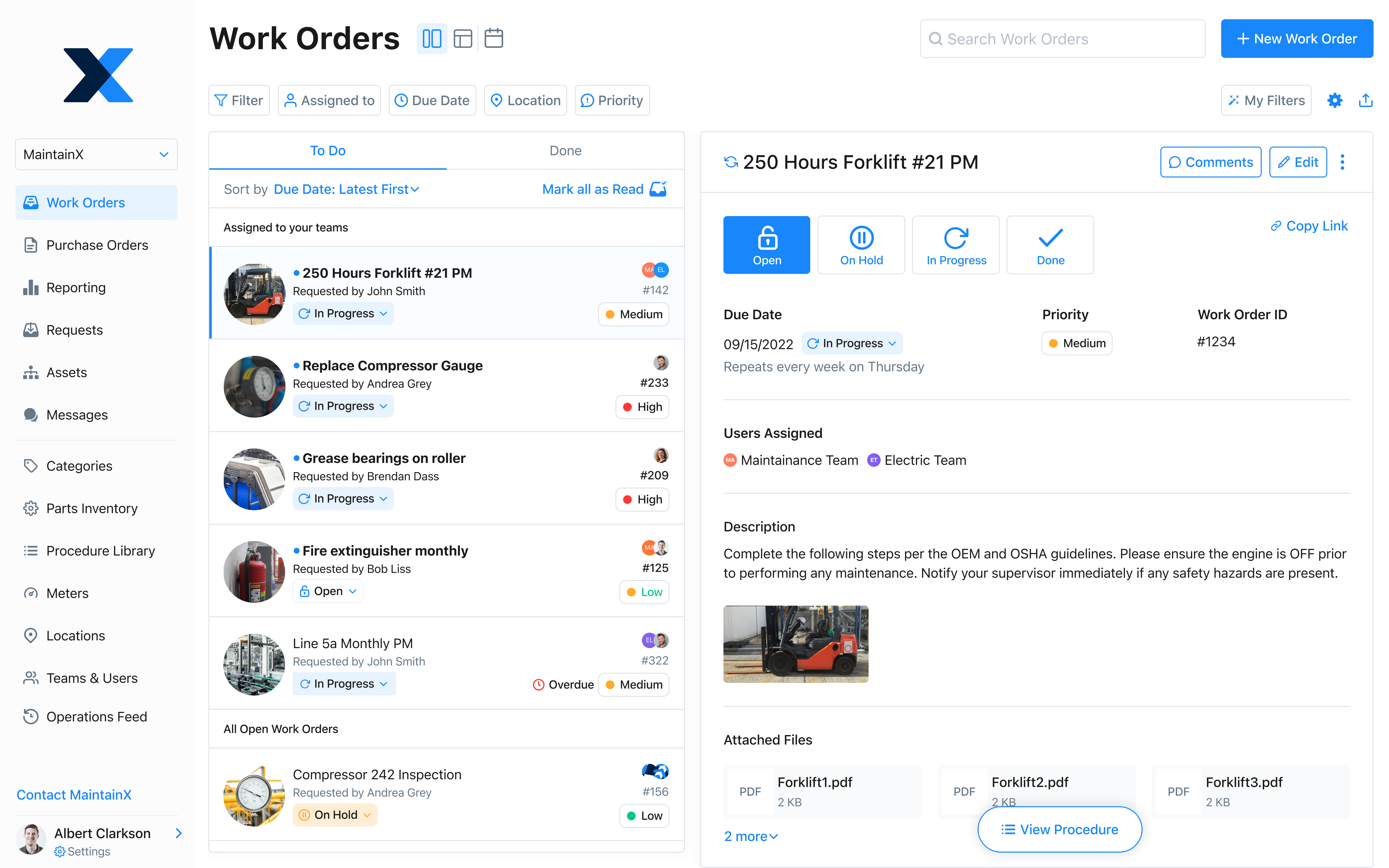
Put simply, MaintainX is the best in class when it comes to mobile work order management toolkits. A variety of workflow management software options exists for organizing operational workflows outside of your business’ maintenance department.
Simplify SOP Workflows with MaintainX
Perhaps, the easiest place to dip your toes into workflow creation is with your facility’s preventive maintenance (PM) procedures. Critical pieces of equipment come with manufacturer’s guidelines that outline routine maintenance procedures to ensure asset reliability, decrease downtime, and extend equipment life cycles.
Visual task representations can reduce technician oversights when reading exceptionally complex SOP checklists and work instructions. If you’re ready to streamline your maintenance project management efforts, we’re here to help!
FAQs
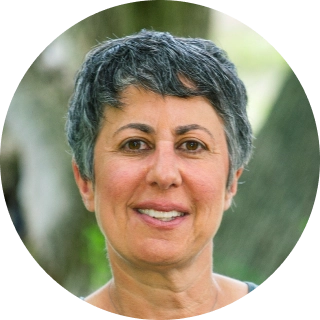
Caroline Eisner is a writer and editor with experience across the profit and nonprofit sectors, government, education, and financial organizations. She has held leadership positions in K16 institutions and has led large-scale digital projects, interactive websites, and a business writing consultancy.