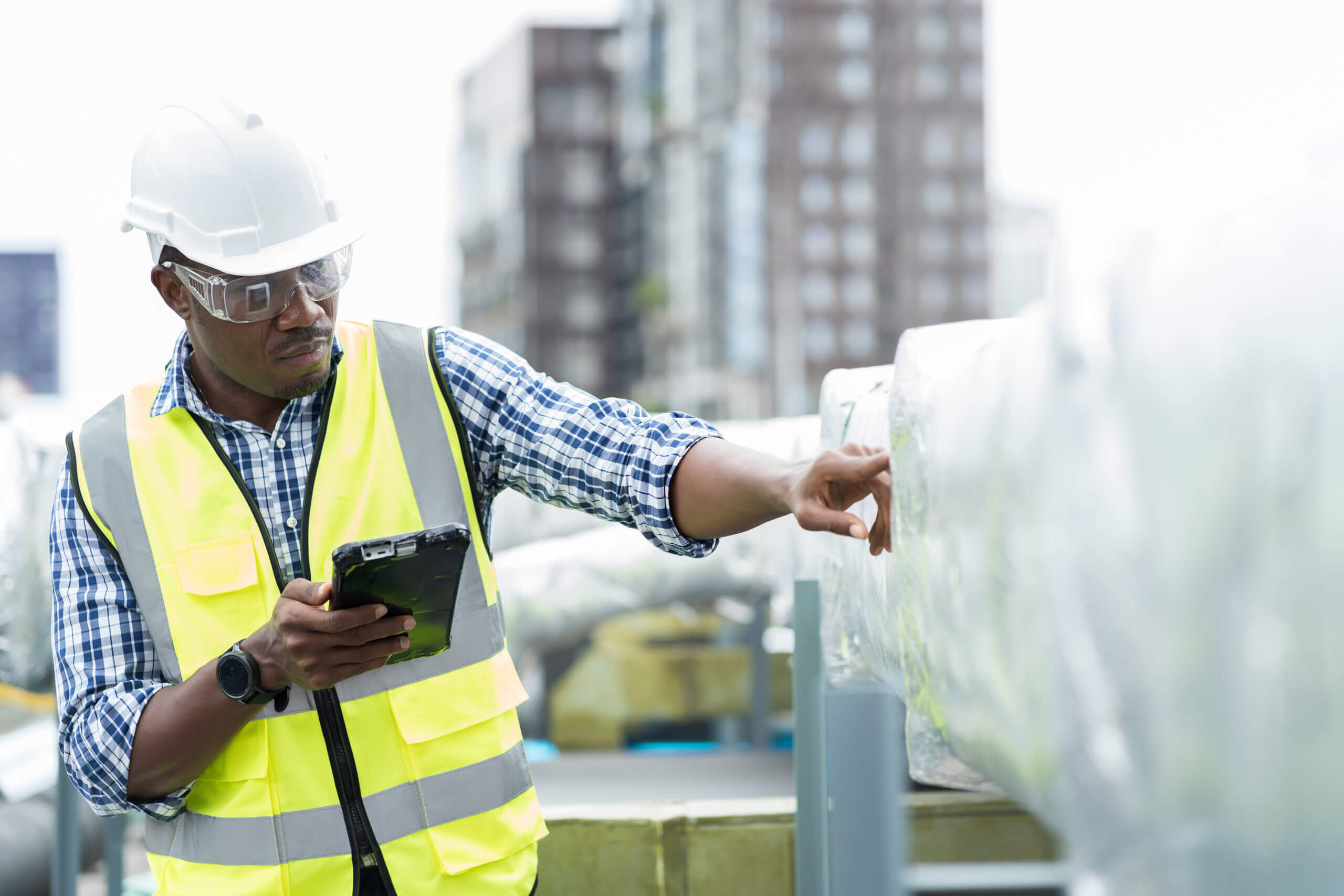
Building maintenance refers to activities performed to retain and restore the functionality of residential and commercial properties. It aims to preserve a safe, functional, and comfortable environment for tenants at all times.
Cleaning, gardening, and maintaining the mechanical and electrical systems are all part of building maintenance. These tasks require consistent efforts and planning. Therefore, you need standard operating procedures (SOP) for building maintenance.
In fact, 44% of companies spend more than 40 hours per week on maintenance tasks. That’s a considerable expense on your income statement. However, understanding how to create and implement SOPs and work orders for building maintenance increases quality standards, can help reduce maintenance costs, and free up your team’s time for more strategic tasks. Here we explain why you need SOPs for building maintenance and how to create a building maintenance SOP.
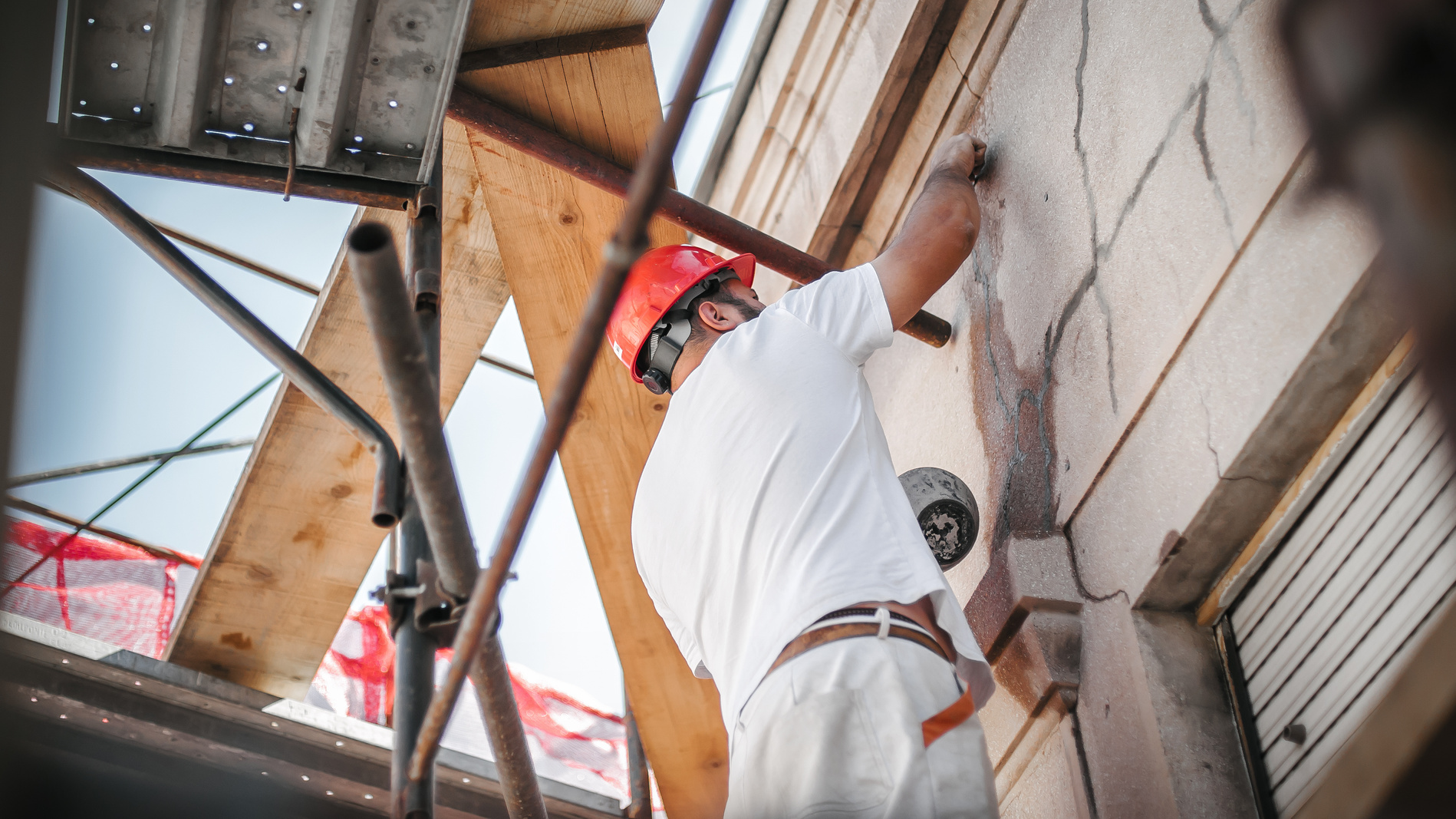
What Is Building Maintenance?
Building maintenance is a set of tasks to maintain, improve, and repair buildings and related systems.
Ensuring that the premises and systems of your facility are cleaned regularly is part of building maintenance. So is performing maintenance tasks on the air handling units, HVAC, drainage, and other systems.
Here are the key roles involved in building maintenance:
- Custodian: Employees responsible for the building’s cleanliness. Their responsibilities include mopping, dusting, vacuuming, and washing the premises.
- Maintenance team: The maintenance team includes technicians and a manager. The technicians perform maintenance tasks on building systems like HVAC, sensors, and machines. The managers oversee the maintenance schedule and assist technicians where needed.
- Third-party vendors: These are vendors you’ve outsourced building maintenance work too. For example, you can outsource snow removal, landscaping, and similar tasks.
Building maintenance is a type of facilities management, working to prevent breakdown maintenance and the need for corrective action. Tenants to your buildings want a sense of quality assurance–that the place they live and work will not cause disruption or discomfort.
Your building facility maintenance—which may include everything from maintaining cooling towers, fire pumps, and HVAC systems to ensuring pesticides are environmentally safe to general grounds upkeep to maintaining clean areas around dumpsters—provides building occupants with the peace of mind they need to carry on their work and lives without disruption.
“If you’re running one of the 72% of U.S. industrial buildings that are 20-plus years old and counting, it’s time to put together a three- to five-year preventive maintenance plan to keep your operations running with the least amount of downtime possible.”
Grainger
How to Create Building Maintenance SOPs
Creating an SOP is a five-step process:
Step 1: Define the Purpose of Building Maintenance
The first step for creating any SOP is to define a purpose. For example, a building maintenance SOP should start by defining the problem it will address, who the SOP is for, and what its purpose is.
Step 2: Create a List of Tasks Related to Building Inspection
Step 2 involves listing maintenance tasks and creating guidelines for performing them. Again, the guidelines should be easy to understand and detailed.
Creating the list of tasks in a logical order requires time. MaintainX templates can give you a head start, though. You can use the following MaintainX templates for building maintenance SOPs:
- Building Inspection
- Exterior Wall Maintenance Inspection Checklist
- 10-Point Roof Inspection Checklist for Commercial Buildings
- Warehouse Maintenance Checklist
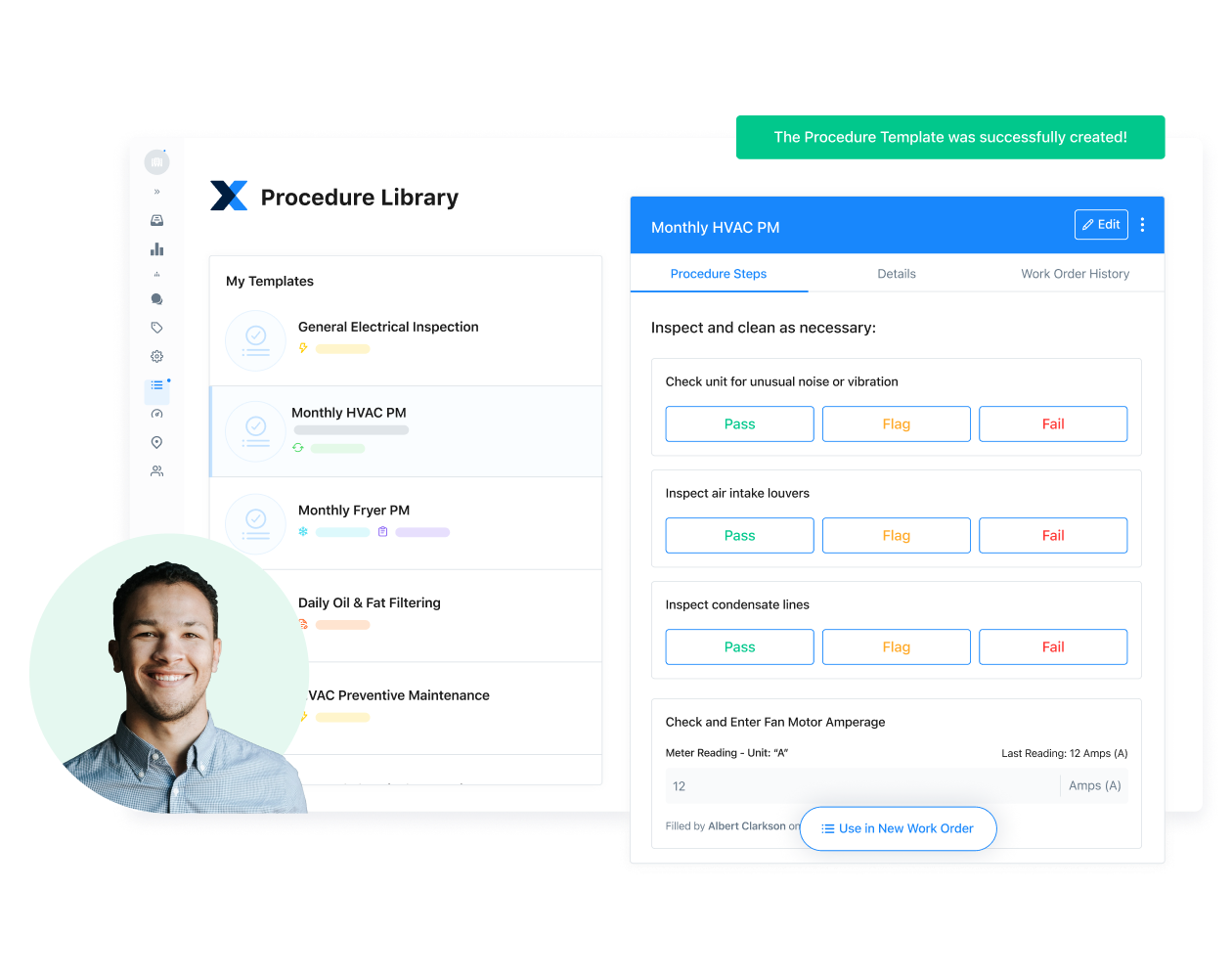
Step 3: Define the Scope of Building Maintenance
State the situations where the SOP will be applicable. For example, an SOP for maintaining electrical systems may apply to internal premises or systems but not necessarily to external premises and systems (lighting in the parking lots, on the walkways, etc.).
Step 4: Assign Responsibilities to Internal and External Building Maintenance Teams
Assigning responsibilities for each task creates accountability. Also, communicating each member’s responsibility through documented SOPs clarifies the tasks they need to work on.
When you document who is responsible for specific tasks, you’ll know exactly who to speak to when communicating unusual circumstances.
Knowing who performed a maintenance task also helps a technician troubleshoot a problem—they’ll be able to request more information from the person who performed the maintenance task without wasting time tracking them down.
You can also collaborate with a third-party vendor to whom you’ve outsourced work. Their team can send real-time messages when they need help, including pictures to provide more context.
Step 5: Add Other Relevant Information
Building maintenance SOPs can look quite different based on the type of building, industry, and other factors. Therefore, add other relevant information to provide your team with sufficient context.
For example, you might request the asset management team or engineering department to provide specific instructions on performing tasks in the production area without damaging sensitive equipment or disrupting the production workflow.
You can add graphics highlighting necessary personal protective equipment (PPE) and warning signs. In addition, consider defining abbreviations and acronyms used throughout the SOP for new hires.
“Facility managers have their hands full every day, ensuring the processes in the structures under their care run efficiently. The systems that make up the building environment often require varying levels of periodic intervention to run optimally. The key to handling these issues lies in identifying the potential problems early to have time to review the most efficient and effective ways to resolve them.”
Buildings
Why Do You Need SOPs for Building Maintenance?
Building maintenance standard operating procedures help with the following:
1. Minimize the Risk of Error
Building maintenance has a broad scope. While your maintenance team works on various mechanical and electrical systems, the maintenance procedure for each system differs based on that system and its maintenance program.
For example, the procedure for performing preventive maintenance on an electrical system differs from reactive maintenance on air-conditioning units on a run-to-failure plan.
Since building maintenance involves maintenance procedures for a wide range of systems, there’s a lot of room for human error. Technicians might overlook a step in the process or perform a maintenance task incorrectly unless you document those processes.
SOPs help minimize this risk by providing complete checklists and procedures to maintain a specific system.
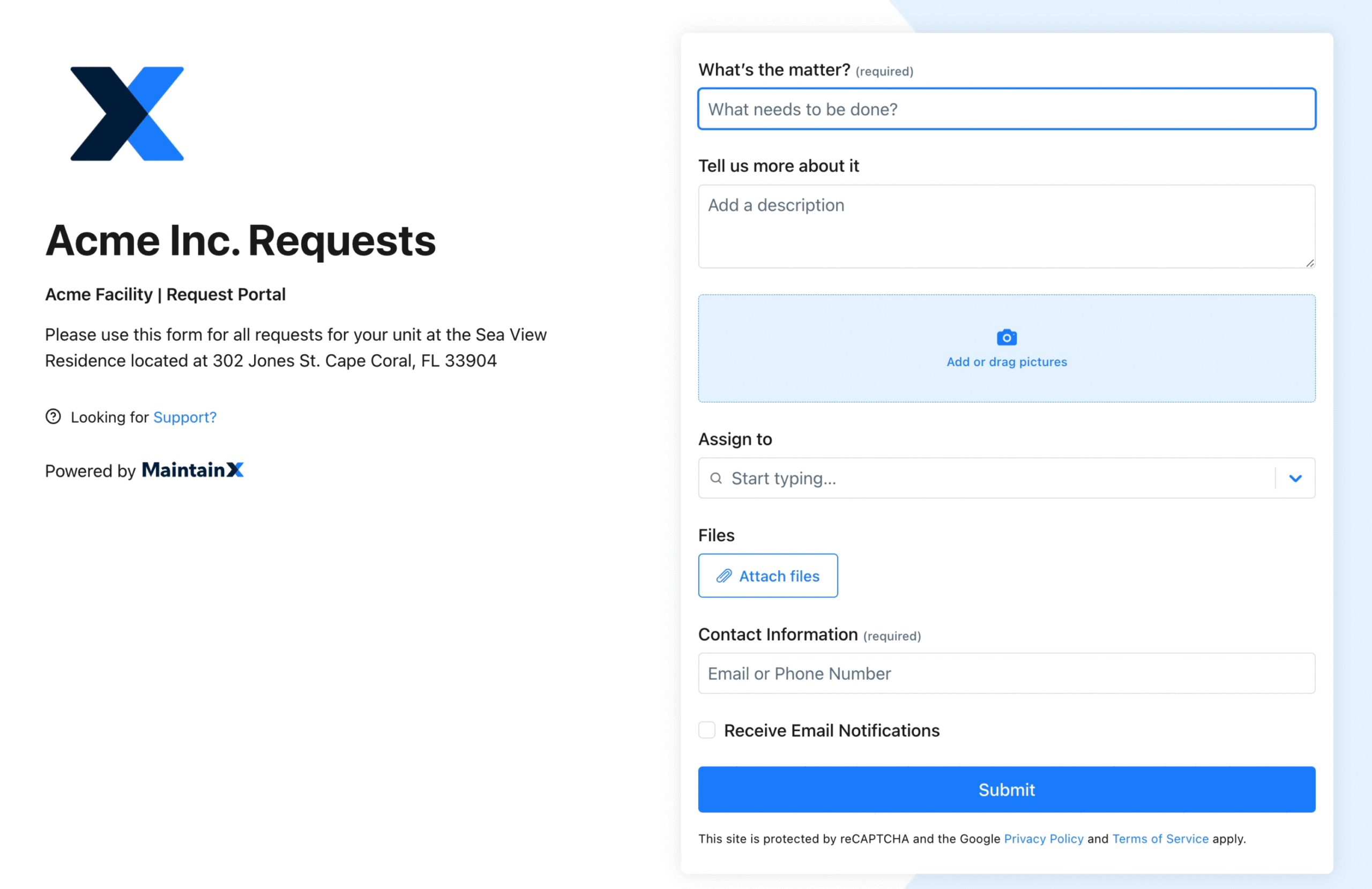
2. Troubleshoot Building Maintenance Problems
Even the best-maintained systems run into problems. When they do, you need to troubleshoot and fix the problem as quickly as possible. A documented maintenance process makes it easier to get to the root cause of a problem. Root cause analysis (RCA) helps your teams quickly repair failures and prevent recurring problems.
For example, suppose you’re trying to fix contamination in your drainage system. You fixed the problem but want to understand how the drainage system was contaminated.
You scan the preventive and corrective maintenance procedures to understand what could’ve caused the contamination.
Maybe you find that cleaning a contaminated surface isn’t included in the preventive maintenance schedule or that some repair work in the past left the drainage system vulnerable to contamination.
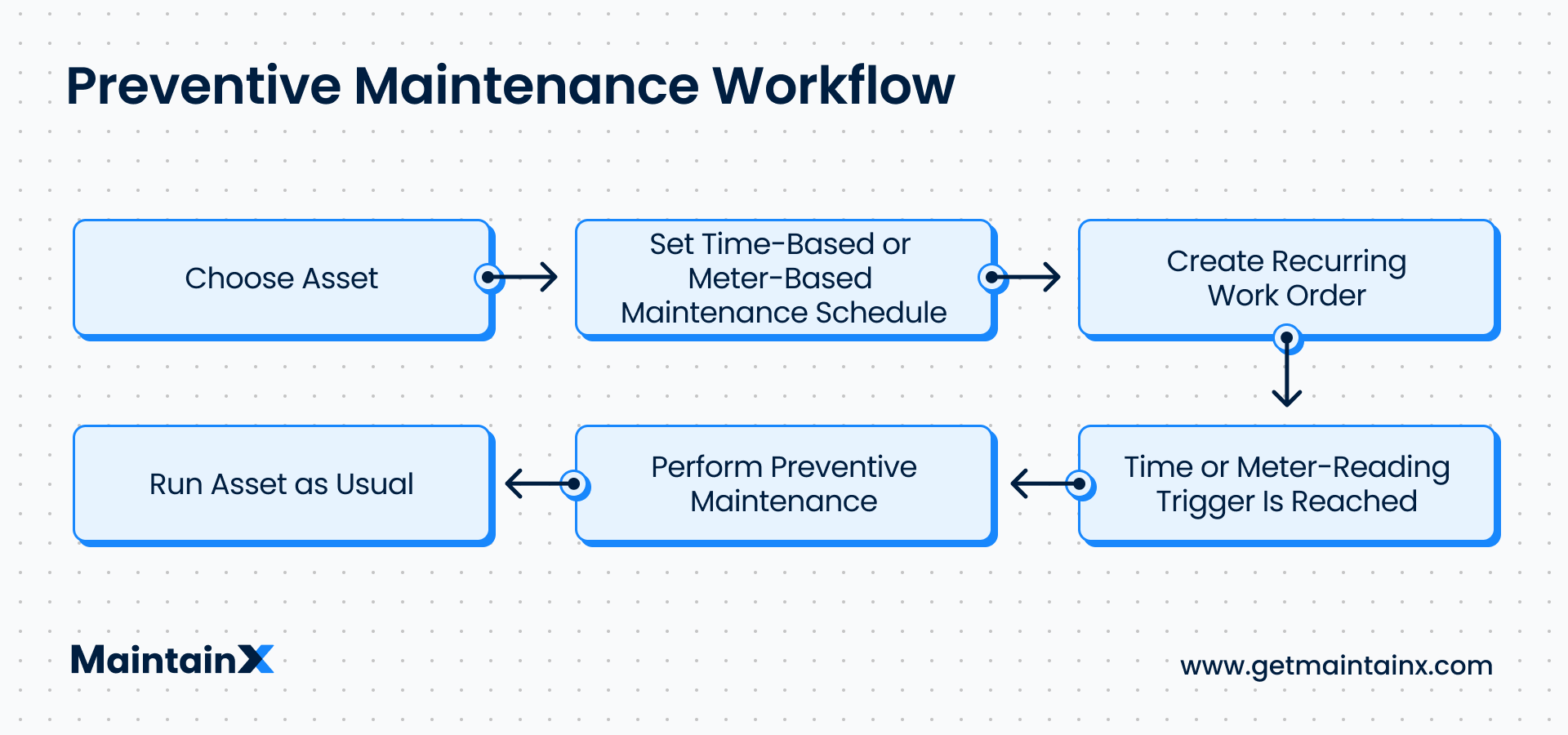
As a result, you can review your PM standard operating procedures and add a more detailed procedure to prevent contamination.
3. Makes Training the Building Maintenance Team Easier
Your team performs dozens, if not hundreds, of building maintenance activities monthly. As you grow and hire new staff for maintenance, you’ll need to train them.
Should you ask more experienced technicians to mentor new hires? Sure, if you don’t mind their work hours being spent mentoring instead of performing maintenance.
But effective SOPs make training more manageable because you’ve documented the procedures more experienced employees will need to explain to newer employees. With the SOP in hand, new hires can then independently perform these activities according to the maintenance procedure and checklist.
To save more time on training, you can use a computerized maintenance management system (CMMS) to digitize and codify the SOPs. For example, MaintainX allows you to add images to instruct technicians on performing specific maintenance tasks. Once you’ve created an SOP, you can create work orders in seconds.
With basics out of the way and more time in your employees’ hands, you can encourage the building maintenance team to upskill with one or more of the following building maintenance certifications:
- Building Systems Maintenance Certification: The certification helps you learn efficient ways to manage critical building systems so they create a productive environment. This includes understanding HVAC, plumbing, and other building systems.
- Building Operator Certification: The nationally recognized training and certification program helps you develop the skill set needed for energy-efficient building operations and preventive maintenance procedures. These new skills enable you to save energy, lowering energy bills.
- HVAC Certification: The HVAC certification has more focused coursework. This certification is an excellent choice if you want to become exceptionally great with HVAC systems.
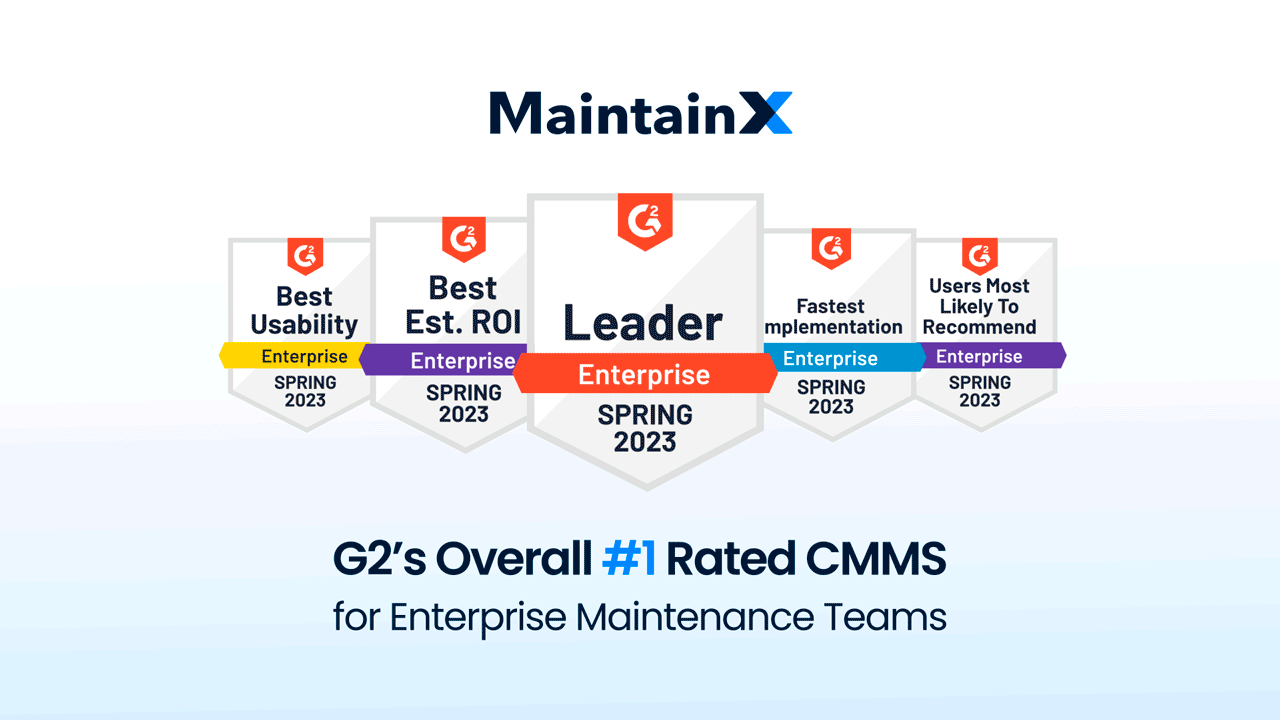
MaintainX: #1 Way to Implement Building Maintenance SOPs
A CMMS enables you to implement SOPs digitally. Imagine using a mobile-friendly CMMS like MaintainX. You’ve created SOPs in the CMMS. So, when you need to issue a maintenance work order, you assign it to a technician right from your dashboard.
The technician receives a notification and starts performing the maintenance tasks. The tech can contact you or a relevant person using MaintainX’s built-in chat feature.
As your team continues performing maintenance tasks, MaintainX collects this data. Then, at the month’s or quarter’s end, you can view reports and analytics in MaintainX for better insights.
Like the idea of streamlining building maintenance with a CMMS?
FAQs
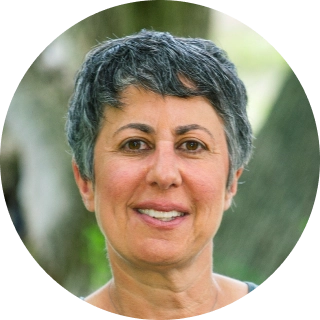
Caroline Eisner is a writer and editor with experience across the profit and nonprofit sectors, government, education, and financial organizations. She has held leadership positions in K16 institutions and has led large-scale digital projects, interactive websites, and a business writing consultancy.