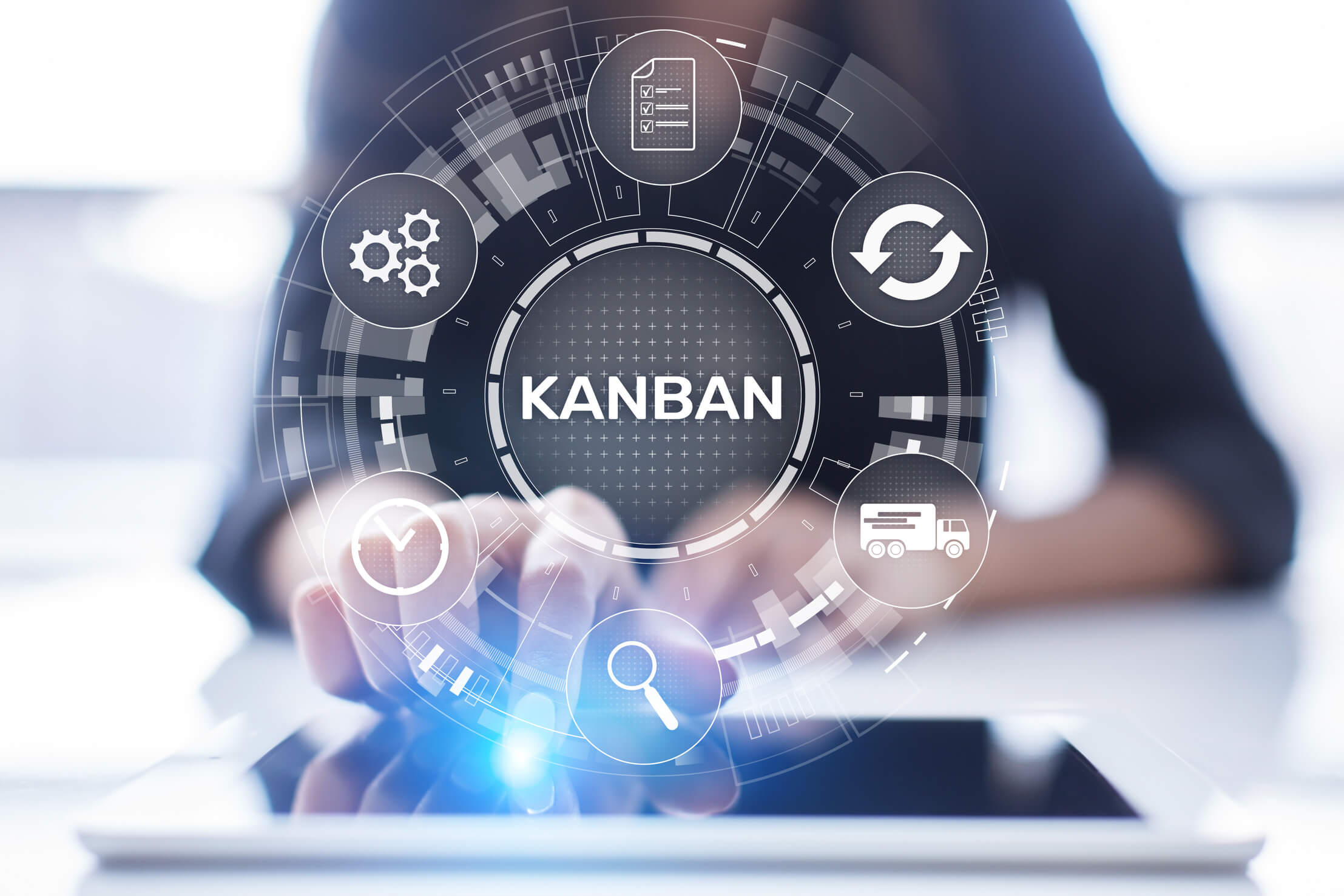
A Kanban system offers a straightforward visual approach to help your team track its workflow effectively and gives everyone on the team a high-level overview of any work in progress.
First developed by Japanese Industrial Engineer Taiichi Ohno, this pull system regulates production through visual cues or signs and creates a situation where each preceding step triggers the flow of work.
The Kanban method is useful for moving physical items and information through a workflow.
Example: Using a Kanban Bin System in Production
A production worker is fitting clamps to hoses. The cue for the worker to request a new bin of 100 hose clamps is triggered when the worker reaches the remaining 10 units in the current bin. The minimum Kanban quantity is set at 10, prompting the worker to send the empty bin (and its Kanban card) back for a refill to have the next full bin delivered to the workstation.
This “gated” request process keeps the team’s workflow moving efficiently without any bottlenecks or wasted waiting time (muda). By the way, a gated request requires the worker to make a formal request (i.e., a purchase order, work order, etc.) for the needed items.
Example: Using Kanban Boards to Shift Information along a Pipeline
A procurement team regularly communicates with its warehouse team to discuss upcoming deliveries, backorders, and out-of-stock items.
A physical Kanban board placed in a common work area allows the procurement employees to update the status of inventory orders so that it is visible to others. As a result, the warehouse team is always informed of stock status. And, it can add its own tasks to the board when components are out of stock and need to be ordered.
Both teams work together to move cards along the process.
Consider these examples on a larger scale, in which many individual Kanban systems are in place and functioning as an ecosystem. Manufacturers can keep production limits in check via the controlled release of parts, assemblies, or tasks.
Such a system is vital when your business adopts a just-in-time production model and seeks to maintain minimum inventory levels. At its core, Kanban aligns inventory levels with consumption. It also seeks to reduce waste caused by overproduction and holding excess inventory.
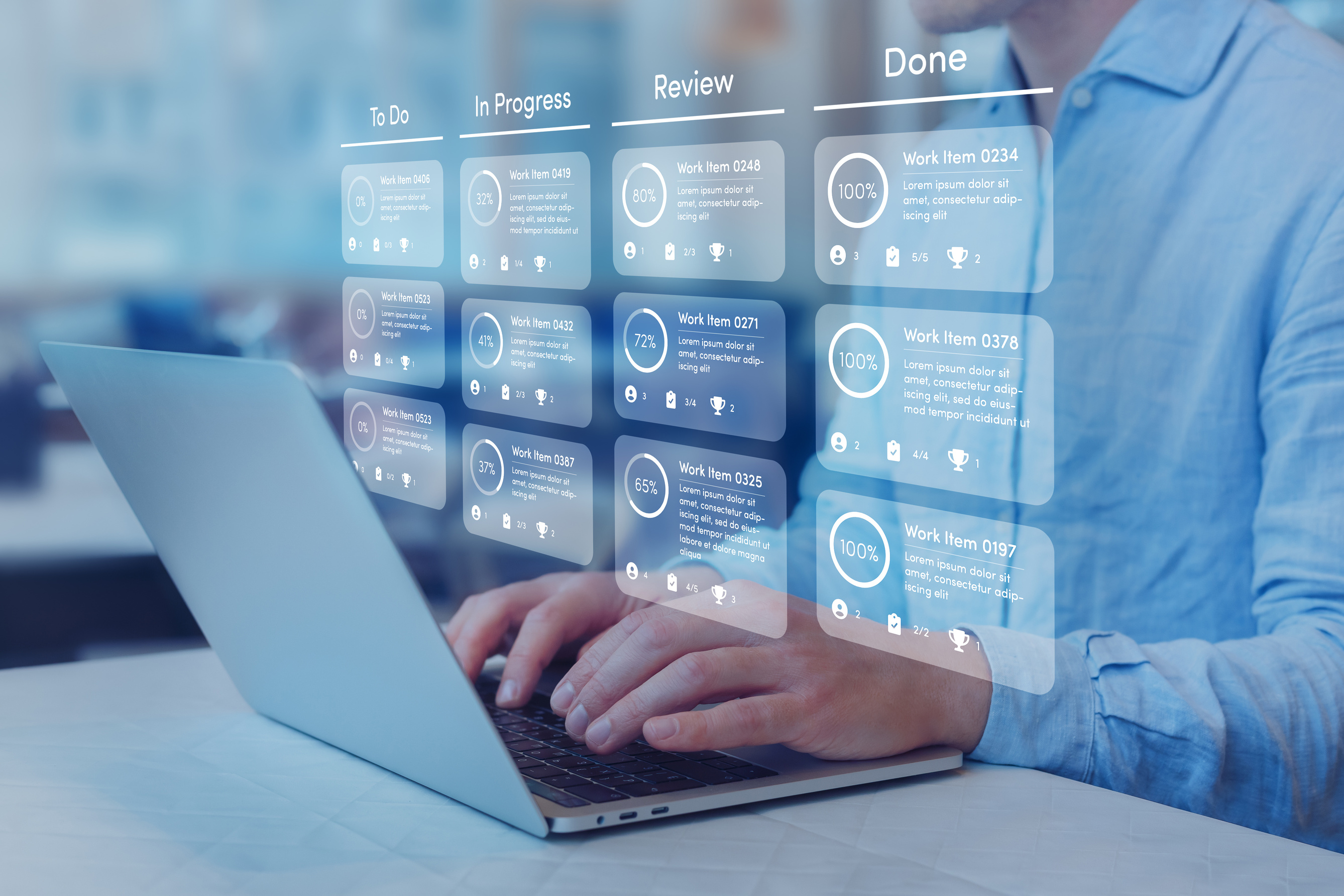
Creating a Kanban Board for Manufacturing
Whether you’re using physical Kanban boards with sticky notes, a whiteboard, or a digital task board (like Notion), you’ll likely need to customize the process to suit your business.
Different stakeholders, approval requirements, and work management preferences mean that you’ll want to create your own version. But, here are the essential steps to creating a basic Kanban board in a manufacturing environment.
1. Create Columns for Each Stage
Split your Kanban board into columns representing different stages of the task or project. For example, an inventory management Kanban could have columns for To Do, Request Raised, On Order, In Transit, and Received. A product management team could use columns titled: Idea, Feasibility, Validation, Development, Evaluation, and Complete.
2. Create Swimlanes for Different Teams
Kanban boards are divided into sections by “swimlanes.” These horizontal lines help to visually separate different types of work that different teams or employees will handle. You can also use swimlanes to demarcate different urgency levels or manage repetitive tasks.
3. Add Your Projects and Tasks
Split the overall project into tasks. These might be work items like individual customer orders, issues observed during a Gemba walk, or the many steps involved in procuring a large piece of equipment. These tasks are placed as Kanban “cards” in the starting position (usually the first column).
It’s easy to get carried away and add every task you can think of to your board. This is why work-in-progress (WIP) limits are essential to streamlined task management.
WIP limits ensure that teams have the capacity and resources to complete what is in progress before adding more work to the pile. Be mindful of the number of work requests and use smart prioritization to work on the most critical tasks first. For example, your board may have WIP categories such as: Not Started, In Progress, Complete, and Backlog.
Likewise, individual cards/tasks may have priority levels, such as Low, Medium, and High, to indicate which tasks you need to complete first.
3. Shift Cards as Things Change
Any project management tool is only as good as the information you feed it. So, for example, as goods move into production or continuous improvement teams tackle issues, ensure you regularly update the status of tasks by moving them through the columns on your Kanban board.
In the flow-based approach of Kanban, this shifting is triggered by a commitment point: the point in the task where the work is ready to start or pulled into the next stage.
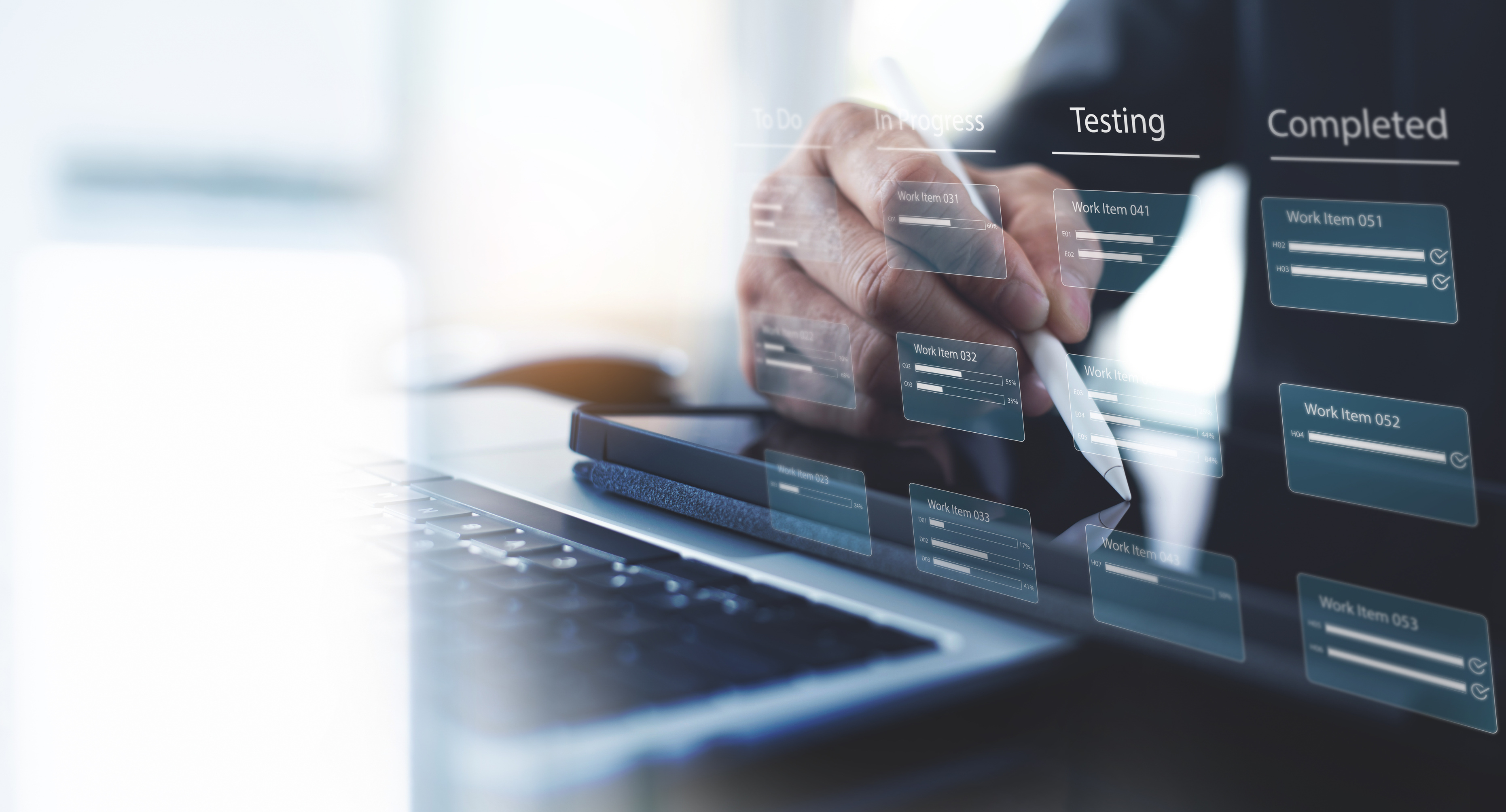
4. Review Your Kanban Often!
The main benefit of Kanban tools is for all stakeholders to see the status of a project in real time.
For example, say your project planning software shows component lead times and due dates via its digital board view. Looking at the board, your production manager can accurately schedule fabrication work. Ensuring your team has access to view and update the board will keep everyone on the same page.
5. Keep Things Moving
The visual element of Kanban means it is easy to see when things aren’t moving efficiently through the process. Obstructions that slow down the process are easy to identify. You may need to tackle persistent bottlenecks using root cause analysis methods such as an Ishikawa diagram.
6. Arrive at the Delivery Point
For most projects, the delivery point represents the end of the Kanban workflow. For example, you may designate the endpoint as when the product is in the customer’s hands. The goal of Kanban is to take cards from the commitment point (when you first create a task) through to the point of completion (delivery point).
“Being agile and embracing structure needs to be driven together. Regardless of the agile methodology selected, it is important to pick one that the team has the capabilities for or can easily understand and that the project environment supports.”
Deloitte
Kanban Applications beyond Manufacturing
Like many lean concepts, the Kanban methodology originated in Toyota’s manufacturing plant in the 1950s. But, it has been readily applied to all kinds of businesses. From software development to managing sales pipelines, Kanban tools have been adapted for today’s remote teams. They are now a regular part of day-to-day project management.
Digital Kanban boards and scrum boards can be seen in apps like Jira, Kanban software like Trello, and Microsoft Teams, allowing employees that use an agile project management framework like scrum to stay aligned.
Online Kanban tools and templates can help agile teams work effectively and develop sprints. Moreover, Kanban works even when those software development teams are spread worldwide.
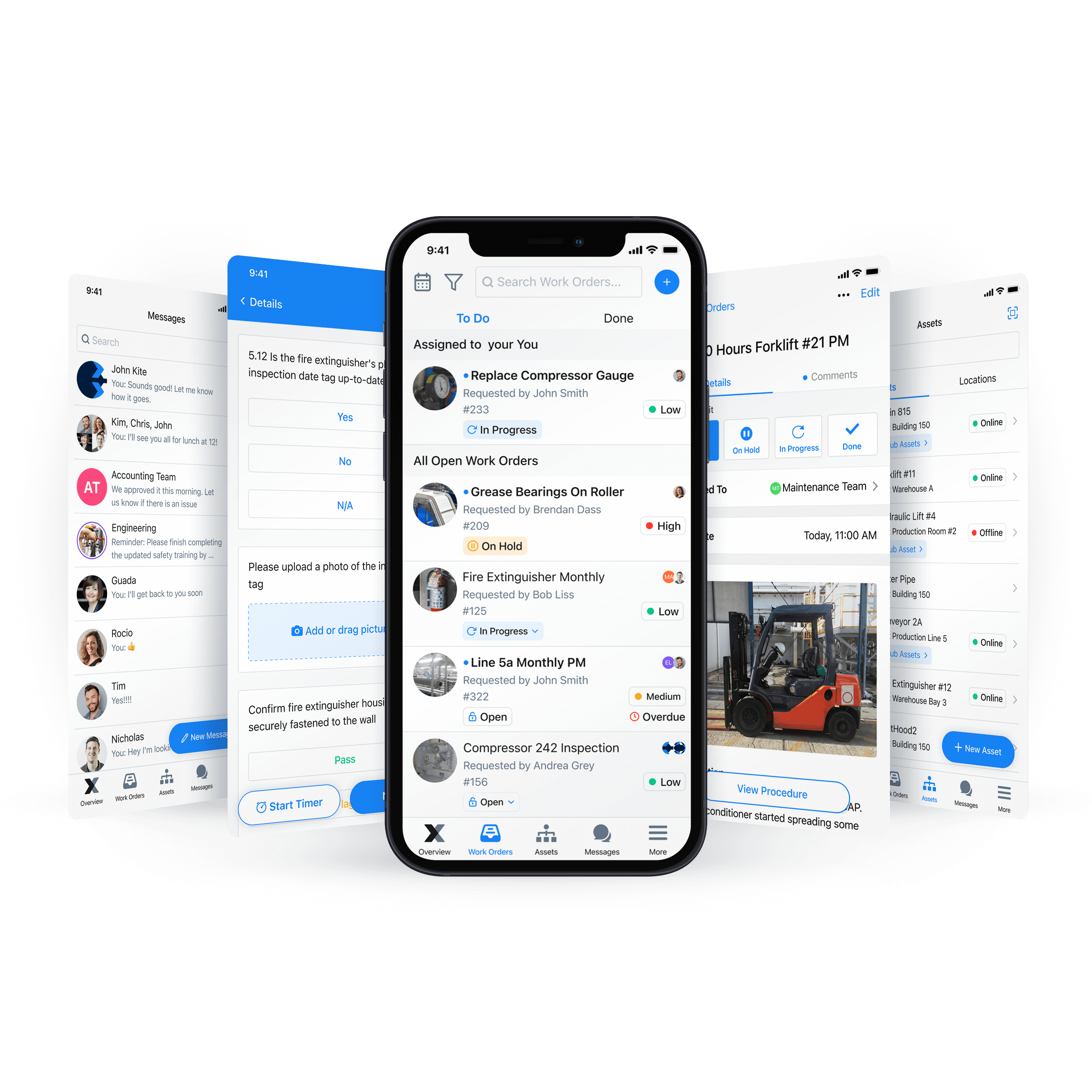
Digital Kanban for Your Modern Manufacturing Plant
One of the key points to understand about Kanban is that teamwork is essential to success. A Kanban system cannot run in a vacuum and requires buy-in from all team members. An online CMMS like MaintainX provides a centralized platform for not only managing tasks in progress and the functionality to encourage collaborative teamwork.
This transparency helps your whole team stay on top of Kanban projects and makes light work of managing work in progress for critical control points like inventory levels and work orders. The strength of your progress will be evident across your key performance indicators (KPIs) and any other metrics you track.
Take a look at our user stories to see how other manufacturers have successfully integrated MaintainX into their organizations.
FAQs
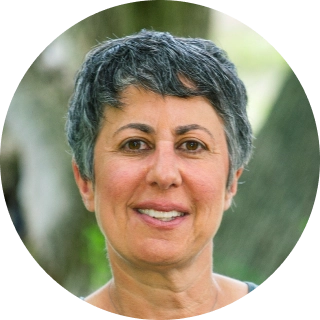
Caroline Eisner is a writer and editor with experience across the profit and nonprofit sectors, government, education, and financial organizations. She has held leadership positions in K16 institutions and has led large-scale digital projects, interactive websites, and a business writing consultancy.