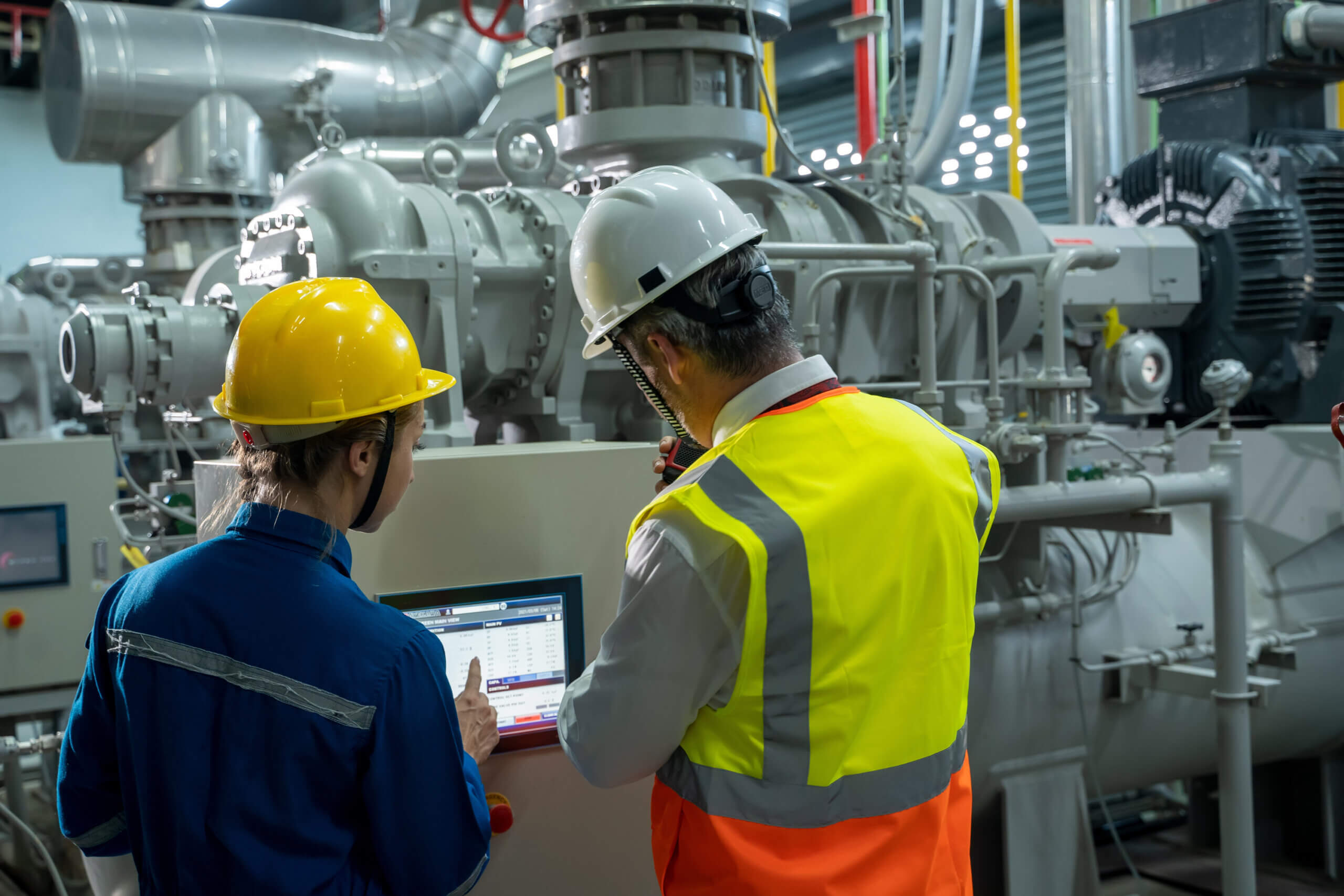
Causal factors help manufacturers understand the factors contributing to an incident, such as equipment failure. Identifying causal factors is required to determine the root cause. This post explains causal factors, how they differ from the root cause, and, more specifically, how determining causal factors helps find the root cause.
What Are Causal Factors?
Causal factors are errors that contribute to an incident, which, if eliminated, could have prevented the incident or reduced its impact. To decide if something is a causal factor, ask yourself, “Had this not happened, would it have averted the incident or reduced its severity?”
When identifying causal factors during an incident investigation, answer these questions:
- What was the sequence of events leading to the problem?
- What were the conditions that enabled or allowed the problem to occur?
- What other issues were related to the main problem?
For example, when the cause of failure was an operator error, the causal factor may be an improperly trained employee. Check the person’s qualifications and experience to determine if they were the best person to operate the machine. If they weren’t, explain why an unqualified employee was operating the machine in the investigation report.
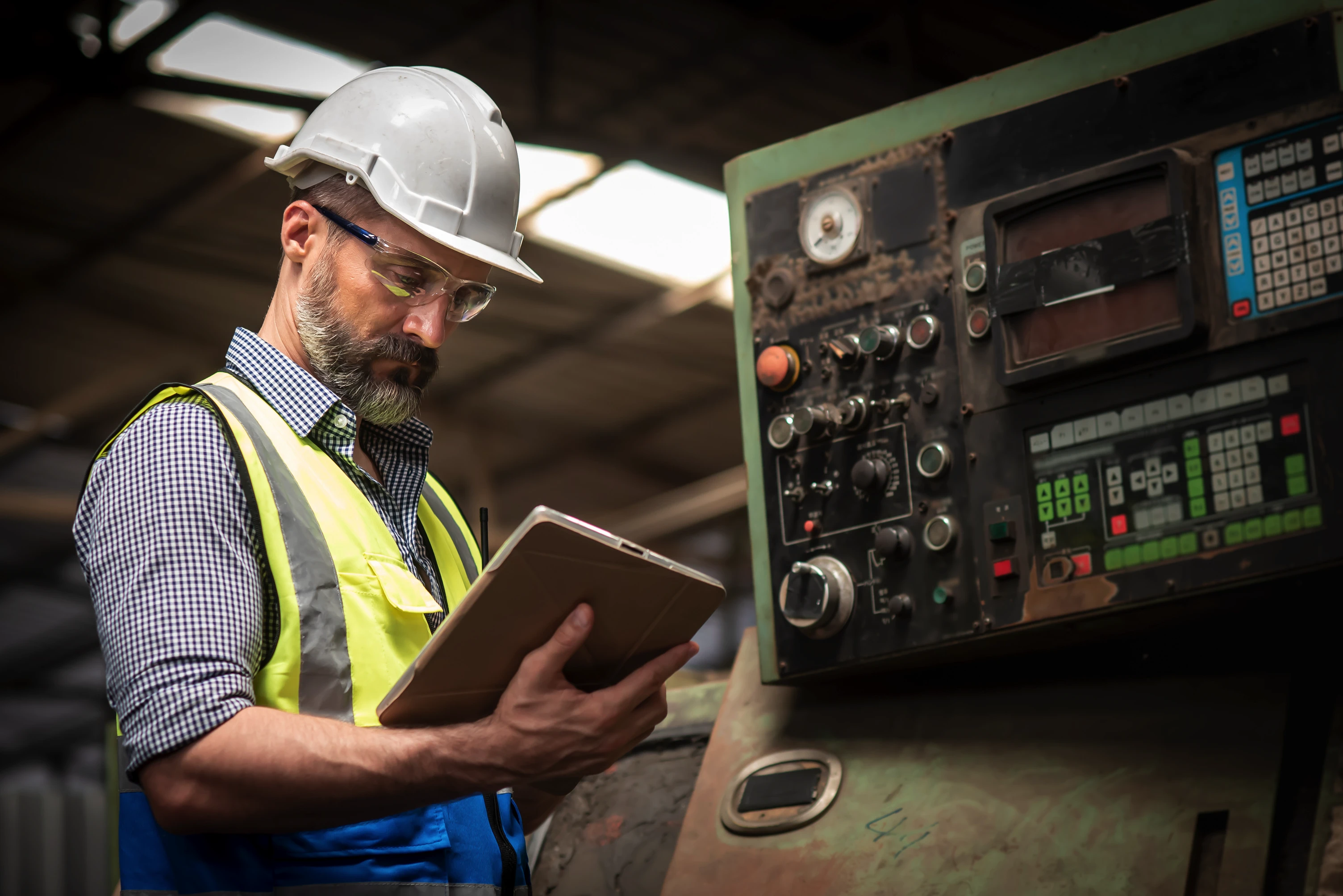
How Is a Causal Factor Different from the Root Cause?
A causal factor is a contributor to failure, while a root cause is a single factor that results in an incident. The event might still occur in a causal factor’s absence, but the same isn’t true for a root cause. Essentially, the root cause is the primary driver of an event, while causal factors are secondary or contributory drivers.
Analysts can use causal factors to determine a root cause. For example, the Five Whys is a root cause analysis (RCA) technique in which analysts identify causal factors to determine the root cause. Then, they ask why something happened until they find the root cause.
Use Five Whys to Find Causal Factors and Root Cause
Sakichi Toyota, the founder of Toyota Industries, developed the Five Whys method. The method continues to be used across industries alongside other lean concepts like kaizen, six sigma, poka-yoke, and jidoka.
The Five Whys method helps determine the root cause by exploring cause-and-effect relationships between problems. It involves asking “why” five times, based on anecdotal experience. However, you may need to ask “why” more often, depending on the problem.
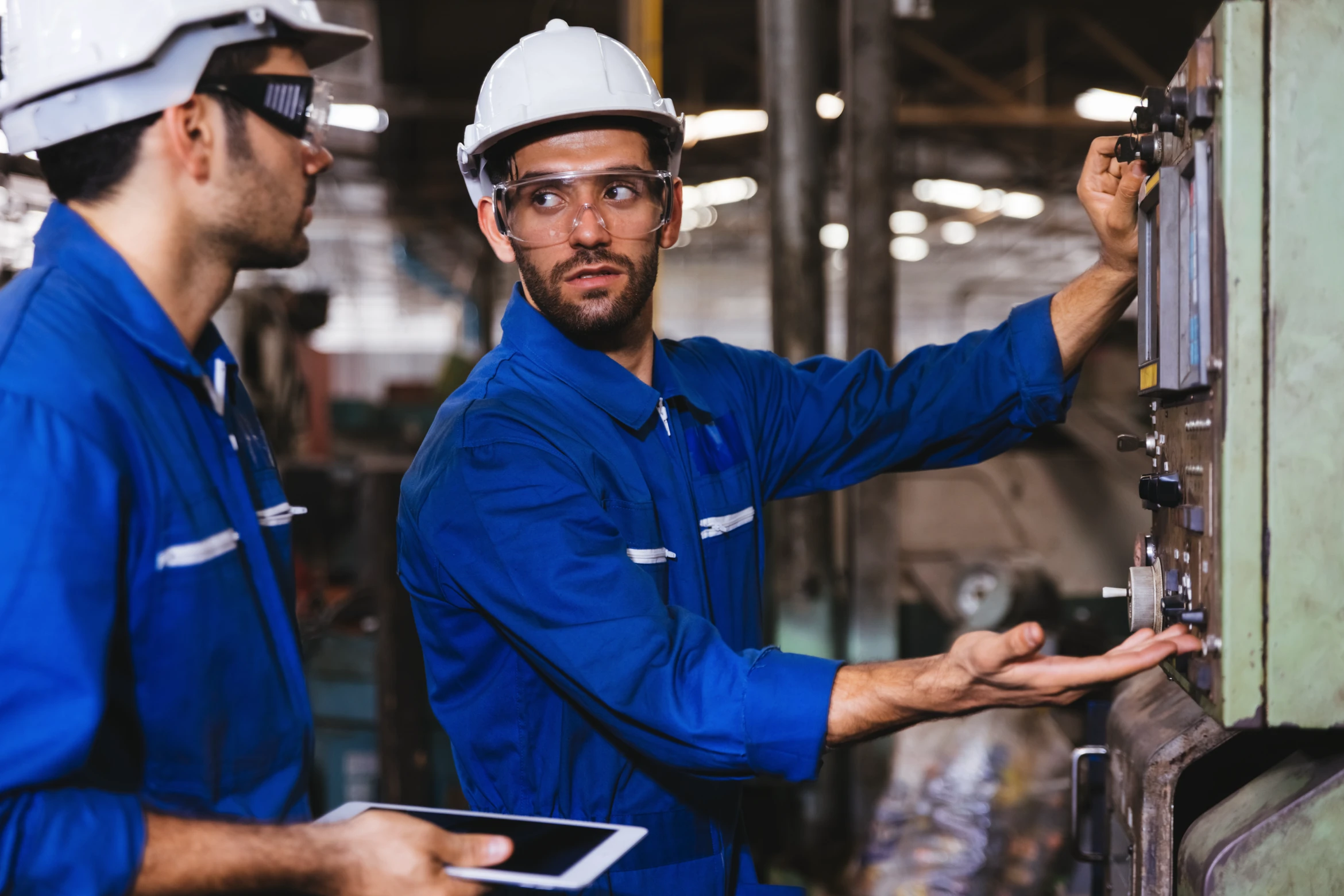
The Five Whys Questions
For example, let’s say the conveyor belt stopped working. You ask and answer the following questions to determine the causal factors and root cause.
1. Why did the conveyor belt stop working?
The main pulley stopped rotating.
2. Why did the main pulley stop?
Insufficient power supply.
3. Why did the pulley have insufficient power?
The motor’s windings burned.
4. Why did the motor windings burn?
Excessive current running through the motor windings resulted in motor overload, causing it to burn.
5. Why was an excessive current running through the motor?
No overcurrent protection to stabilize the current flowing through the motor.
The Five Whys Final Answer
Here, the root cause is the lack of overcurrent protection. The pulley not working, motor windings burning, insufficient power to the pulley, and excessive current running through the motor are causal factors.
A fishbone, or Ishikawa, diagram is a great visual to use to identify causal factors. Once you’ve identified the issues, you can map out your questions and answers on the diagram to find causal contributing factors. These causes will help you visualize the sequence of events to find the root cause.
Experts often criticize the Five Whys methodology because it encourages linear thinking, making analysts lose sight of non-obvious causes during the investigation. Nor does it offer any guidance to solve the problems it identifies. Instead, experts recommend using the Five Whys to identify causal factors, but for a thorough root cause analysis (RCA) for major problems, consider using other RCA tools.
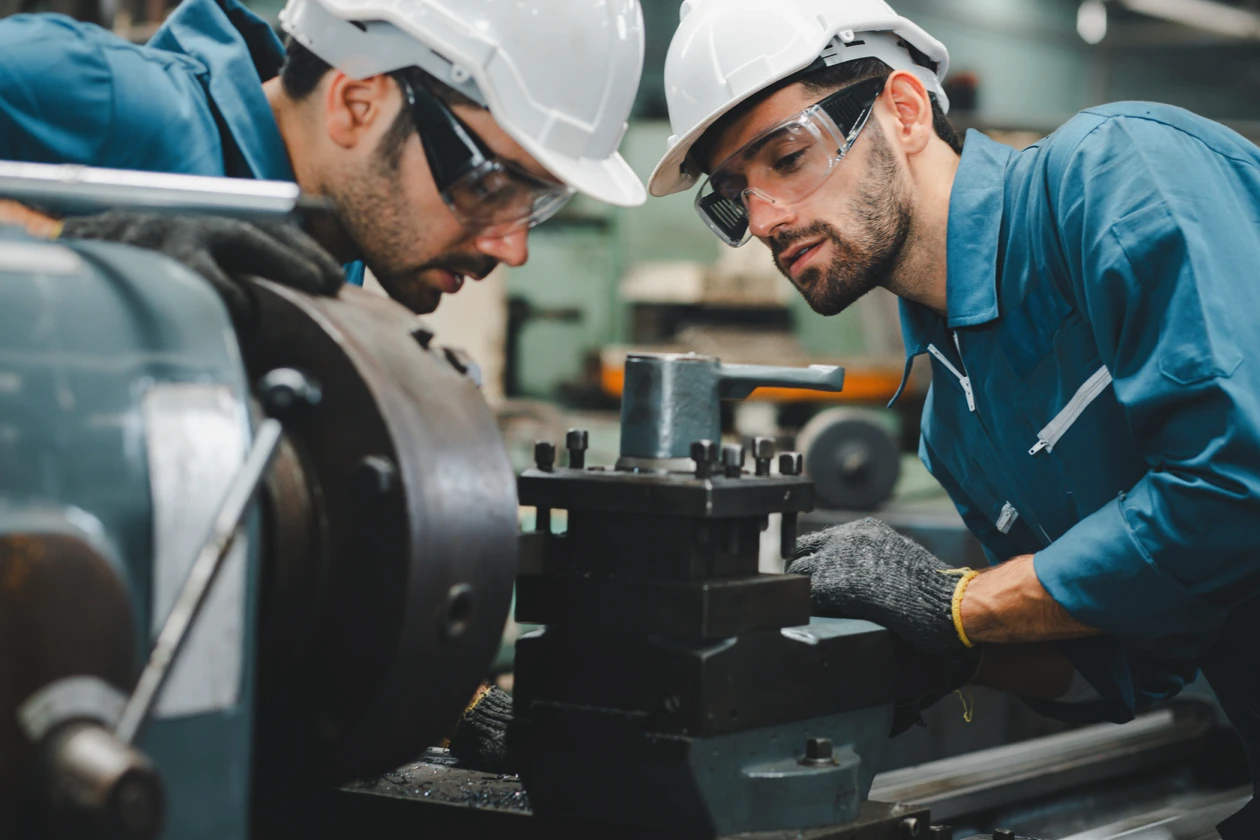
How a CMMS Can Help
Identifying causal factors and a root cause helps you decide on corrective action. The faster you can identify causal factors and take corrective action, the faster you can get your equipment up and running.
However, a well-planned maintenance program is your best bet if you’re looking to reduce asset downtime and achieve production efficiency. You can easily set up a preventive maintenance program using a CMMS, or if you’re already dealing with asset failure, you can create a work order and assign it to a technician within minutes.
A computerized maintenance management system (CMMS) like MaintainX helps catalog assets effectively and allows you to monitor maintenance and repairs. In addition, the technicians can quickly ask questions or request information using MaintainX’s built-in chat function.
You and your team need zero training to get started. Just download the app to your desktop or mobile device.
FAQs
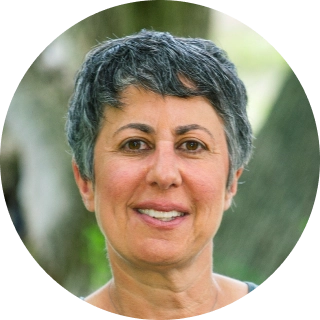
Caroline Eisner is a writer and editor with experience across the profit and nonprofit sectors, government, education, and financial organizations. She has held leadership positions in K16 institutions and has led large-scale digital projects, interactive websites, and a business writing consultancy.