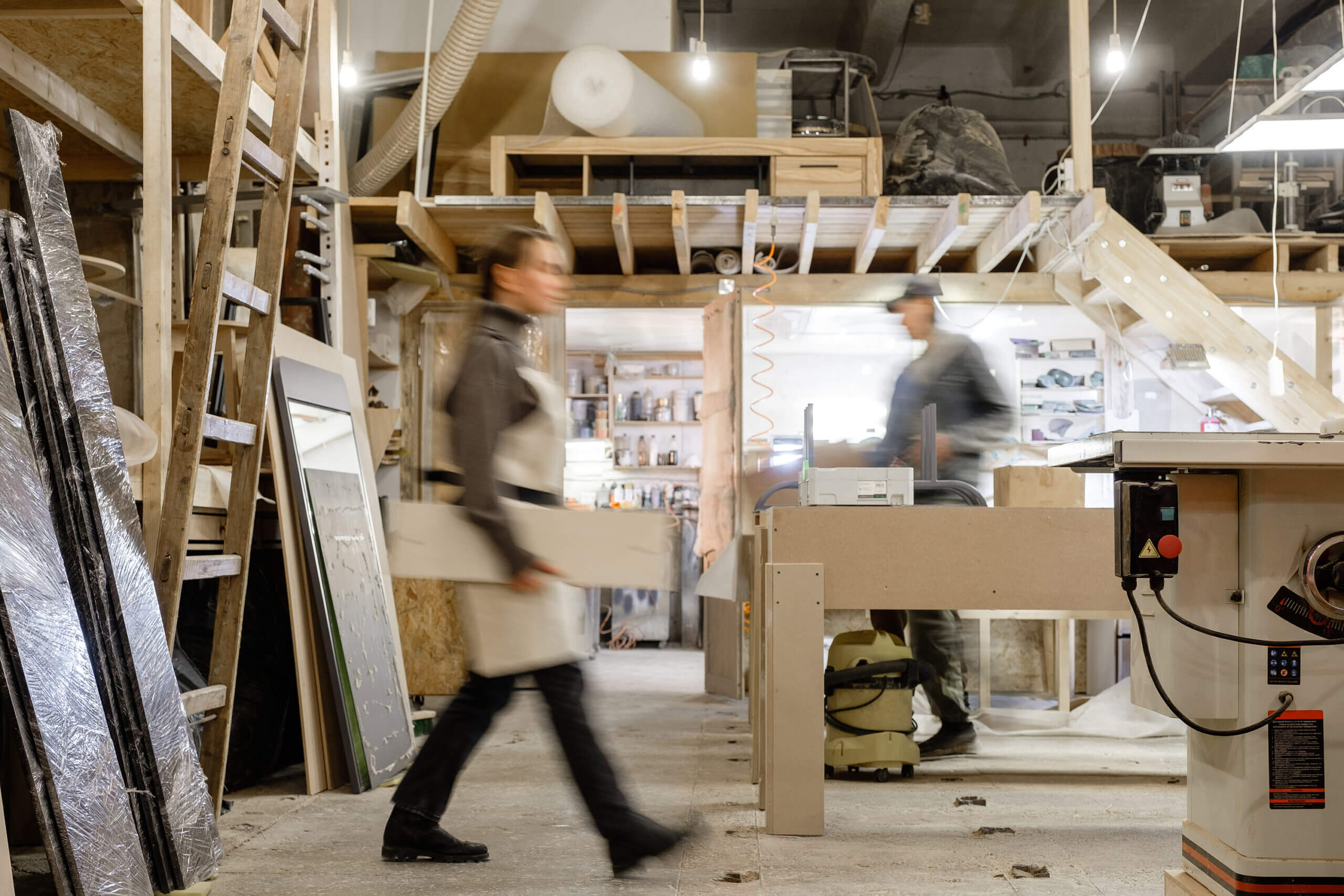
What Is Takt Time?
Takt Time is the rate at which manufacturing products or delivering services should be completed to meet customer demand. It is a concept that relates to the amount of time to complete the entire production process aligned with the frequency of customer demand.
Imagine you receive a new customer order for a unit of a product every two hours. To meet customer needs, your production time for each finished product will need to be 2 hours or less.
The term, Takt, originates from the German word Taktzeit, which means a beat, pulse, or time interval. Toyota later adopted it as a key metric in its car manufacturing process.
Takt Time is a fundamental concept in lean manufacturing, as it is used to analyze process loads and bottlenecks. It is also used to understand excess capacity and improve workflows.
“When businesses develop project plans or try to improve their production rates, Takt Time … can help you produce products on time and enhance your team’s workflow.”
Indeed
Takt Time can easily be mistaken for Cycle Time and Lead Time, which are lean metrics. Cycle Time is the time spent actively working on a customer’s order. Lead Time is the amount of time between receiving an order and the customer receiving the product.
This metric is concerned with the time it takes to complete the value stream and match demand. A value stream in a supply chain refers to all the activities involved in delivering a finished product to a customer. This can include everything from getting through the assembly line to how much time delivery takes.
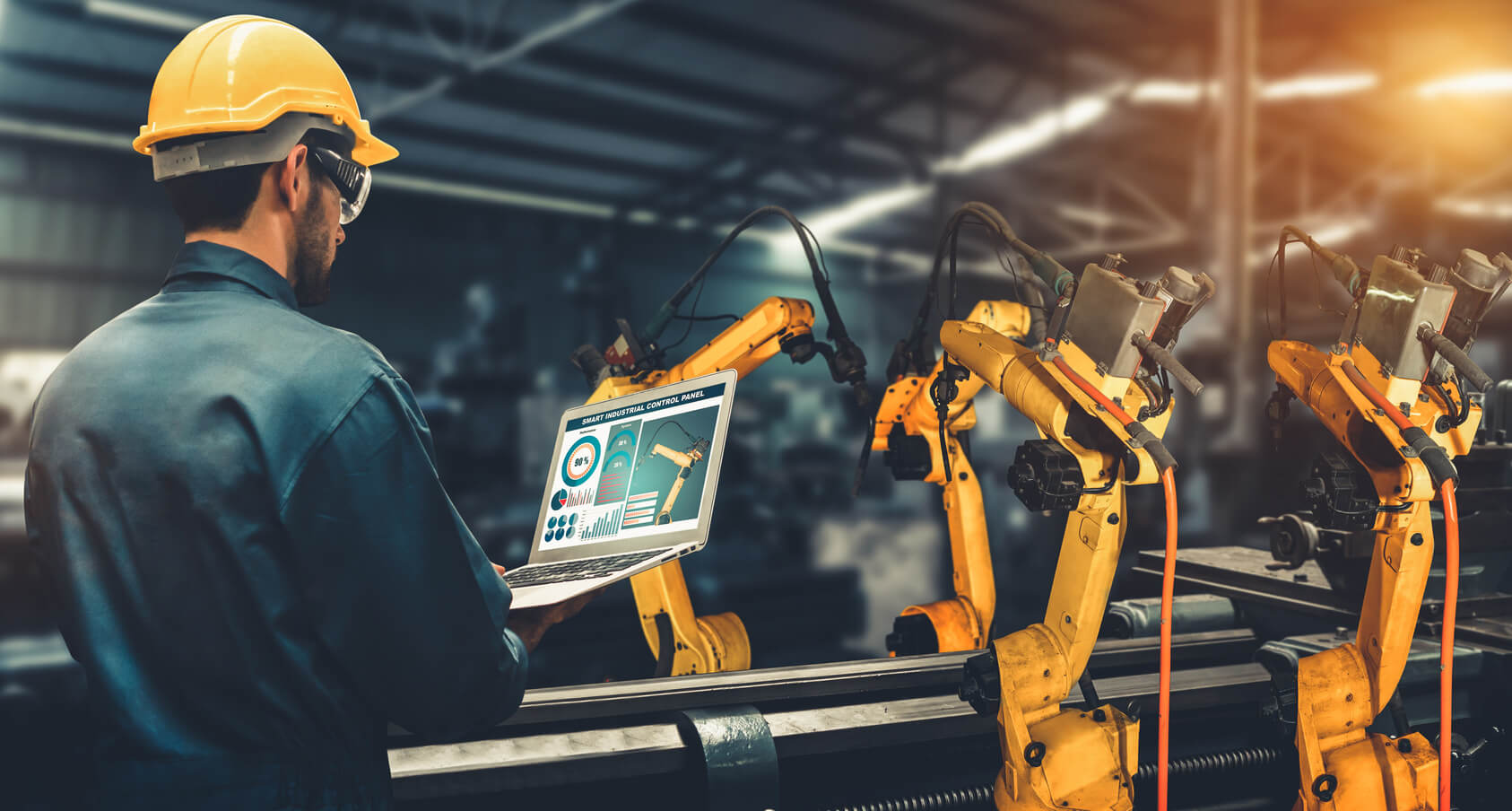
How to Define Takt Time
To define Takt Time, you’ll need to divide the total net available production time by the average customer demand.
Takt Time = Total Net Available Production Time / Average Customer Demand
It’s important to note here that this formula requires the net available production time, which means that you should not include any period when production isn’t taking place. Such periods may include unsupervised work time, downtime, shift changeovers, and breaks, such as lunch or emergency breaks.
However, if production continues during these periods, then the time should be included in your calculation.
Example
So, let’s assume your team runs a regular 8-hour shift, with a 30-minute lunch break somewhere in the middle. This means your team gets paid for 7.5 hours of work. This comes to 7.5 hours x 60 minutes = 450 minutes.
Let’s also assume 20 minutes of scheduled downtime to shut down assets at the close of business. This should be deducted from active or available production time as follows: 450 minutes – 20 minutes = 430 minutes
So, 430 minutes is the total net available production time used in calculating Takt Time.
Next, let’s assume the average customer demand is 100 units per day.
The Takt Time equals 430 available minutes / 100 required units = 4.3 minutes
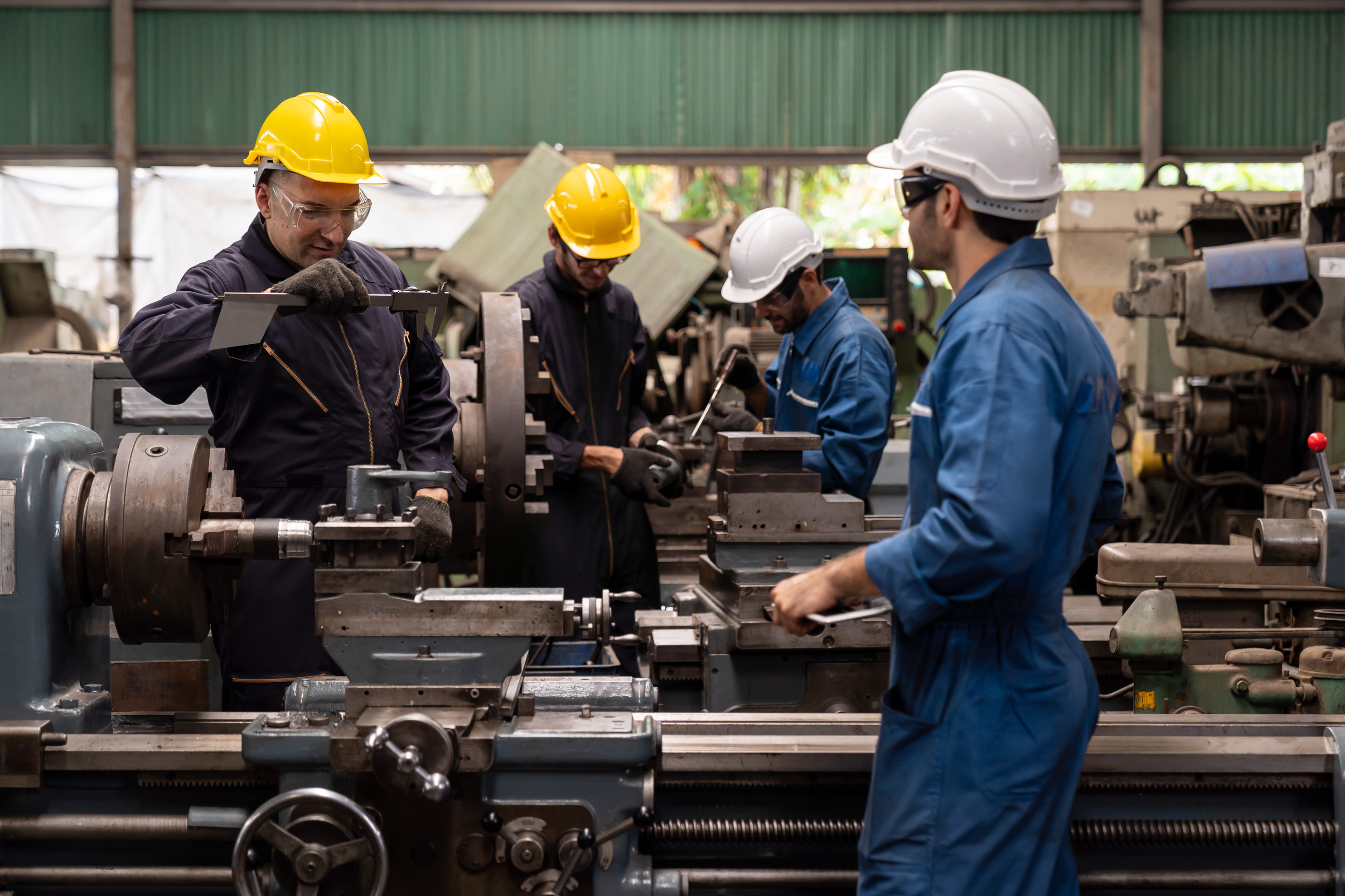
Benefits of Calculating Takt Time
Takt Time is a critical metric in lean management’s Lean Six Sigma approach. One important principle of lean management is the Kaizen philosophy, which refers to continuous improvement.
Producing value with only the most necessary resources is the goal of Kaizen. Calculating your Takt Time helps you know how far off you are from that goal.
You can use this measurement to synchronize the pace of production with the pace of sales. In addition, calculating and benchmarking Takt Time for your workflow can help reduce waste by optimizing for a “just-in-time” process.
The Toyota Production System defines just-in-time as producing “what is needed, when it is needed, and in the amount needed.” In other words, you can save time and costs on overproduction.
In addition, managing Takt Time can reduce storage costs by avoiding excess inventory of raw materials. When you zero in on the most necessary elements in your production line to meet customer demand, you can maintain a continuous flow of work with few interruptions on irrelevant aspects.
Also, this metric brings into focus lapses in business capacity and workflows. It’s a good KPI to determine if you are meeting demand or not and where you might need to improve. This goes hand in hand with cycle time.
A smart project management standard is to keep Cycle Time less than Takt Time. When your cycle time exceeds Takt Time, you are falling short of customer demand. This manufacturing rule will help you optimize your production rate and capacity to meet customer demand while staying lean.
With a CMMS, it’s easy to implement a preventive maintenance schedule to decrease manufacturing maintenance downtime. Reducing downtime increases uptime which in turn improves Takt Time.
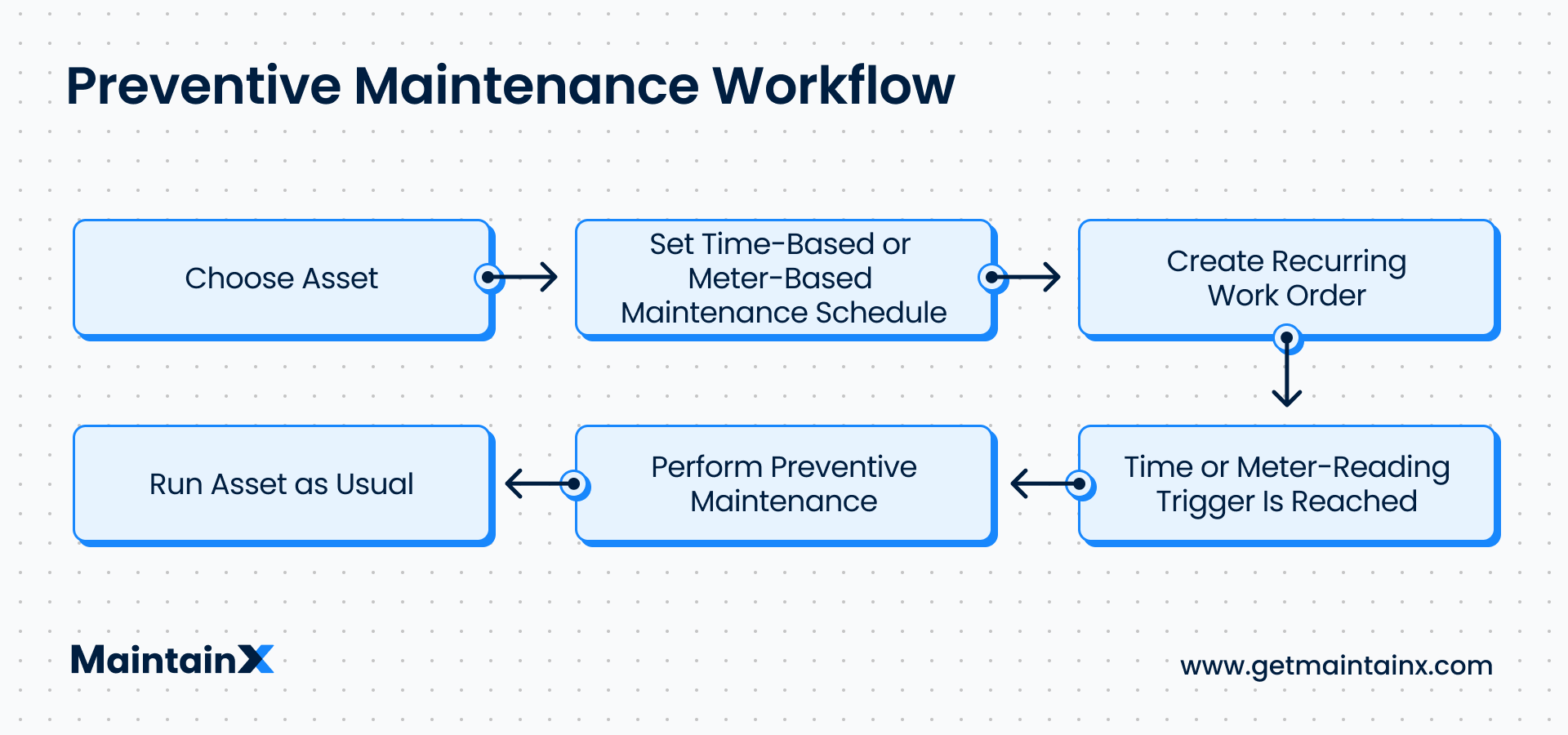
Use MaintainX to Define Takt Time
As noted above, calculating Takt Time properly requires accurate information regarding production activities. MaintainX CMMS offers robust features to streamline collecting this data across manufacturing. With real-time reporting, everything from formulas to inventory to customer orders and staff work hours gets recorded, updated, and accessed right from your mobile device.
So, ready to increase your production with the best maintenance tool?
FAQs
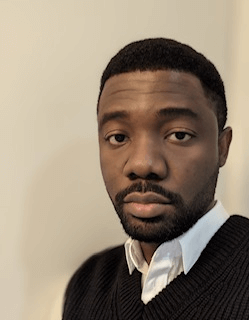
Lekan Olanrewaju is a content writer with years of experience in media and content creation. He has held positions at various media organizations, working with and leading teams at print magazines, digital publications, and television productions.