.webp)
Manufacturing leaders are betting on maintenance more than ever to be a strategic advantage. That expectation often comes with more resources—31% of teams expect their budgets to grow this year, according to the 2025 State of Industrial Maintenance report. But it also brings greater pressure to drive efficiency.
Reducing unplanned downtime has long been maintenance’s go-to strategy for boosting efficiency. But it’s not as effective as it once was. While asset failures are trending down, the cost of failure is spiking. Over 30% of maintenance leaders saw an increase in downtime costs, with the average incident costing $25,000 per hour.
Maintenance teams need new ways to improve efficiency. Here are four strategies to optimize your workforce, cut inventory costs, and protect production capacity—plus how MaintainX can help.
Manage Multiple Assets in a Single Work Order
When maintenance tasks apply to multiple assets,like inspecting every fire extinguisher in a building or servicing a conveyor line,managing them individually can slow things down. Grouping this work often requires manual coordination, even in well-organized systems.
Multi-Asset Work Orders simplify this process by letting you include multiple assets under a single work order, while still maintaining individual tracking and history.
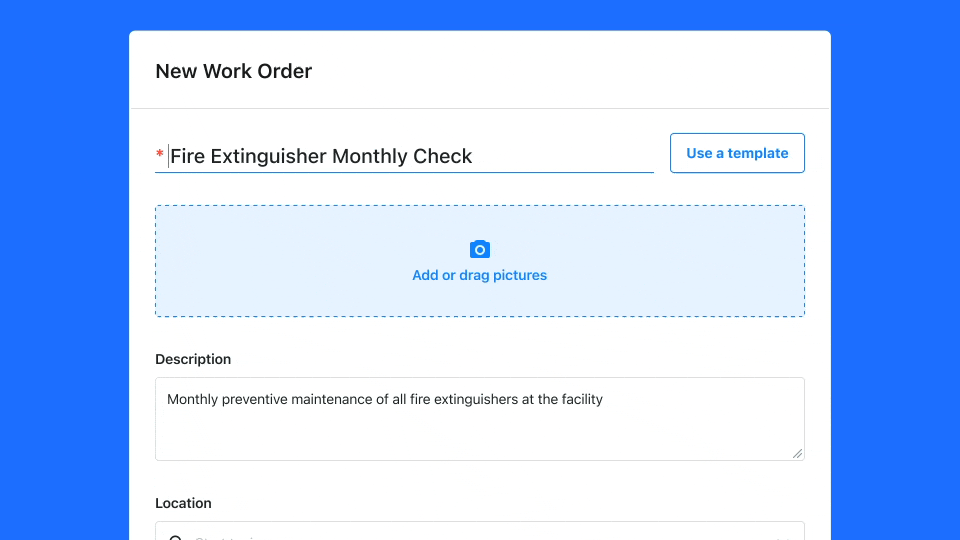
With this enhancement, you can:
- Link multiple assets to any work order
- Apply shared procedures to multiple assets at once
- Track time, labor, and outcomes per asset within a unified workflow
It’s a powerful tool for teams working in high-volume or line-based environments, and a smoother, more scalable way to manage repetitive or batch-based maintenance.
Centralize Parts Data Across All Storage Locations
Work can grind to a halt when your team doesn’t have the right parts. Many facilities store the same parts across multiple locations, but older systems make it hard for teams to see what’s available everywhere. This leads to over-ordering, emergency shipping, and delays.
Multi-Location Parts improves parts inventory management by delivering better visibility into parts information across locations. Paired with recently released Global Parts and Assets, your company’s asset and parts inventory has never been more visible, trackable, and connected.
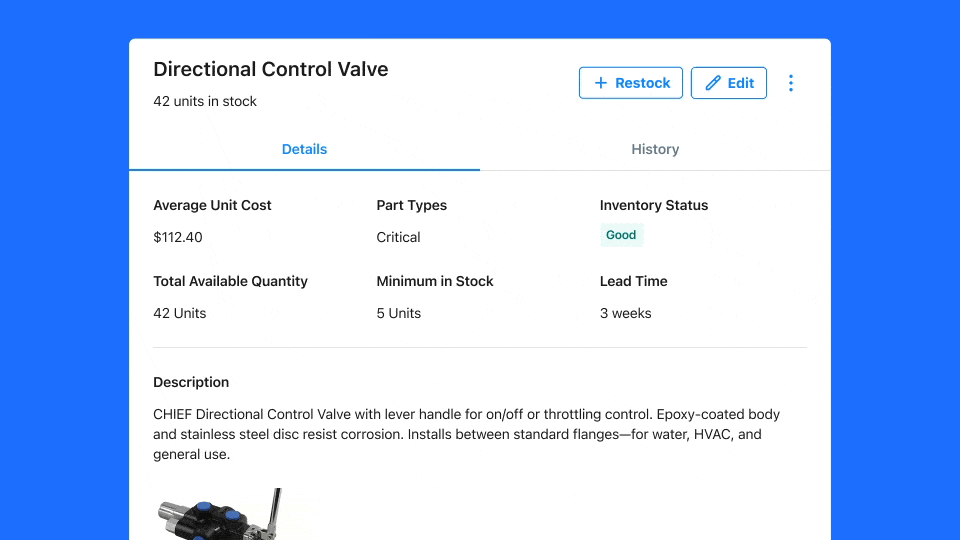
With this new addition, you can:
- Track parts across multiple storage areas
- Eliminate redundant or duplicative parts records and streamline parts reordering
- See total inventory and set reorder thresholds for each location
Customers that use this feature have already seen reduced inventory costs, fewer rush orders, and faster repairs.
Ensure Accountability and Compliance for Critical Work Orders
Safety and compliance are top priorities for MaintainX customers. We’re building tools to support these goals without adding unnecessary steps.
Take this example: A maintenance team is servicing a high-voltage electrical panel. The assigned technician must get a maintenance supervisor or certified electrician to verify the lockout/tagout (LOTO) procedure was completed correctly. With Work Order Approvals, you can assign specific users or teams to review and complete critical steps, ensuring accountability at every stage without adding friction to the process.
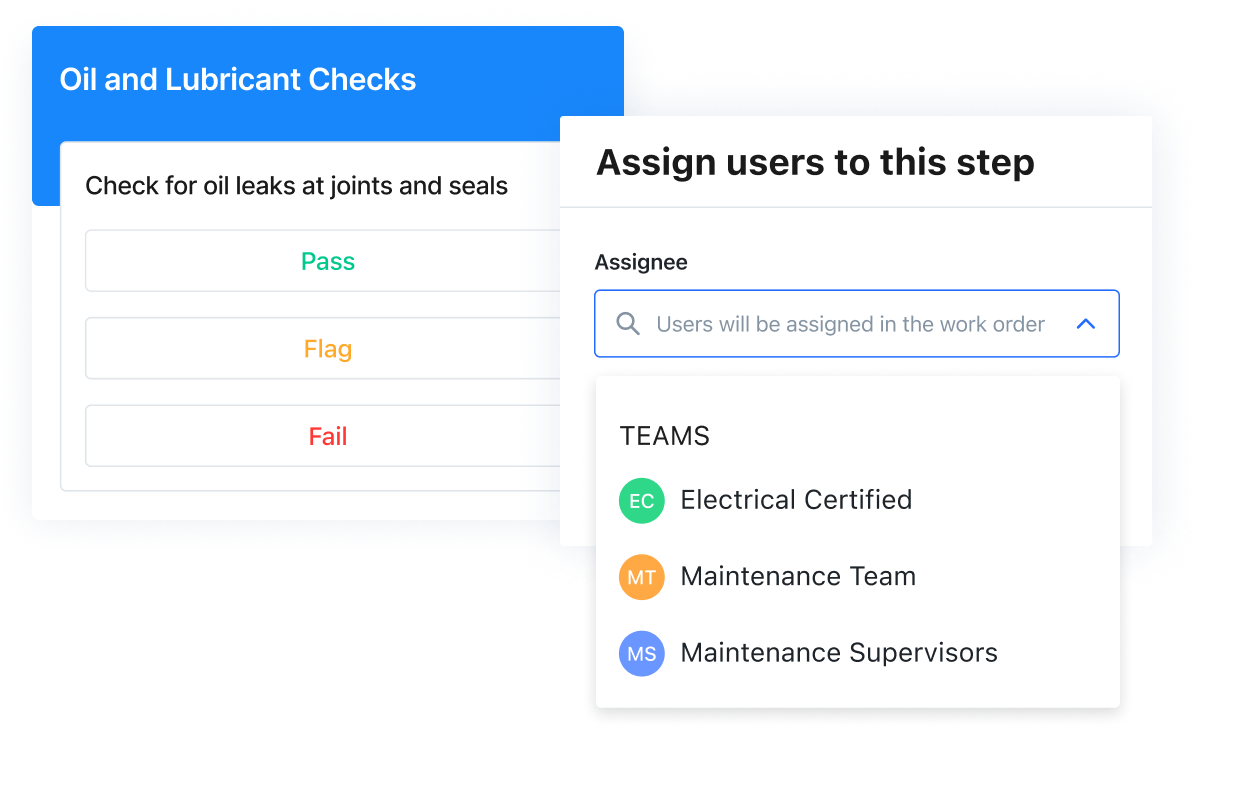
Teams can now:
- Require approvals for specific procedures or entire work orders
- Capture step-level completions and timestamped sign-offs
- Align with industry regulations while boosting accountability
Make Smarter Repair or Replace Decisions
Managing depreciation manually, or outside your CMMS, can create blind spots when it comes to equipment maintenance and lifecycle planning. Pulling this data together often means digging through spreadsheets or toggling between systems, even for finance-savvy teams.
Straight Line Depreciation brings that visibility into MaintainX so teams can easily track asset value over time and make smarter repair-or-replace decisions.
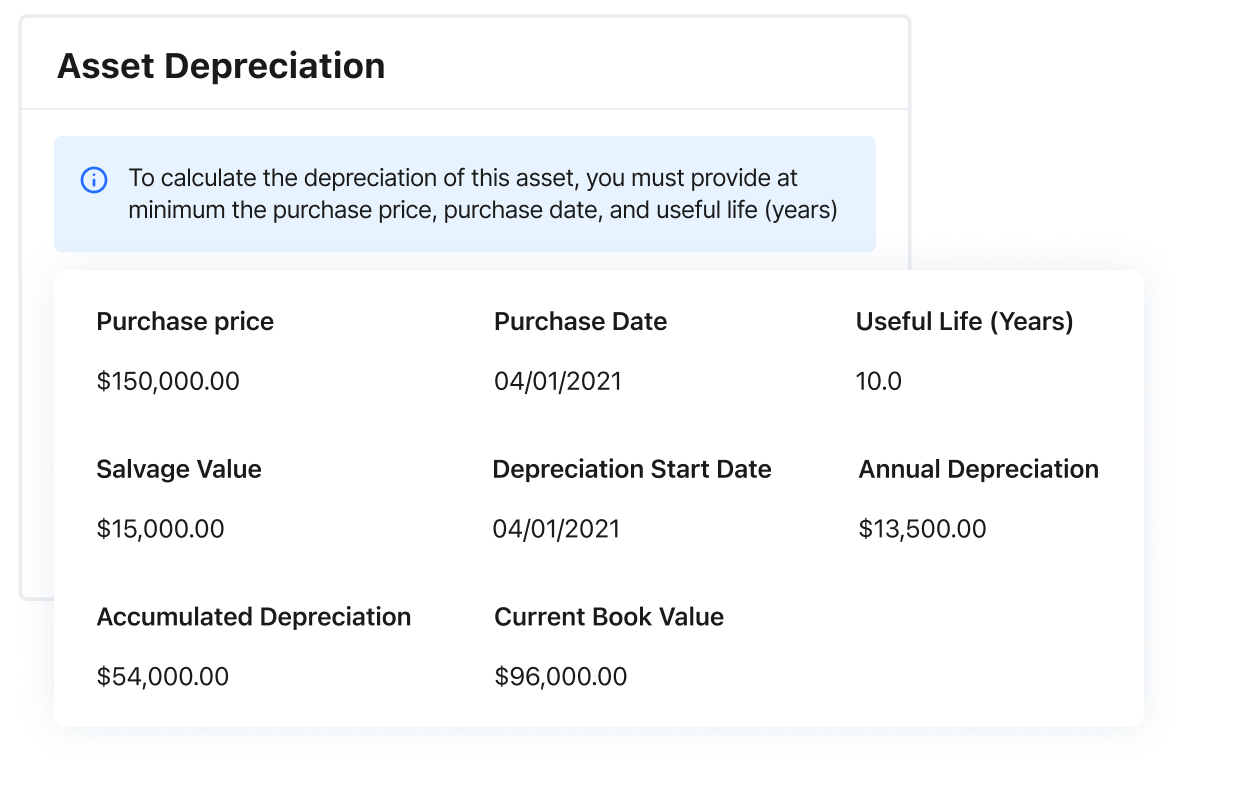
With this enhancement, you can:
- Automatically calculate and track annual depreciation
- Monitor an asset’s current book value over time
- Access quick snapshots or detailed reports when you need them
Ready to get started?
These enhancements are part of a larger shift from reactive, disconnected maintenance to proactive, intelligent asset management.
Whether you're managing a single plant or scaling across regions, MaintainX helps you:
- Execute faster with smarter maintenance processes
- Avoid part delays with full inventory visibility
- Stay audit-ready with step-by-step approvals
- Make every technician hour more valuable
Ready to make maintenance a competitive advantage?
👉 Get a demo or Start your free trial.
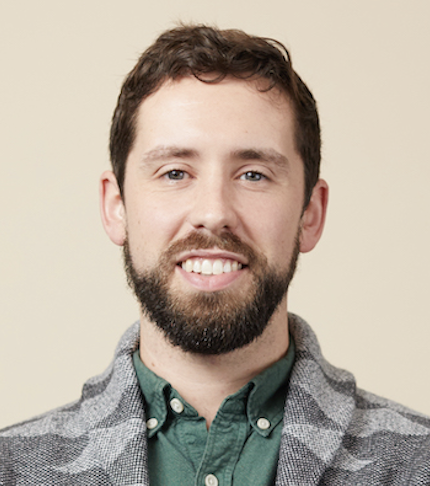
Doug Roberge is the Director of Product Marketing at MaintainX. He has spent over a decade working in SaaS products at companies like Segment, Pave, and others. Prior to his experience working in tech, Doug spent five years at Forrester Research working with Fortune 500 companies on strategies to implement new technology solutions. In recent years, he’s partnered with some of the world’s top enterprises to bring MaintainX into their operations—transforming the way frontline teams manage maintenance and assets, and making work not just more efficient, but a whole lot easier and more enjoyable.