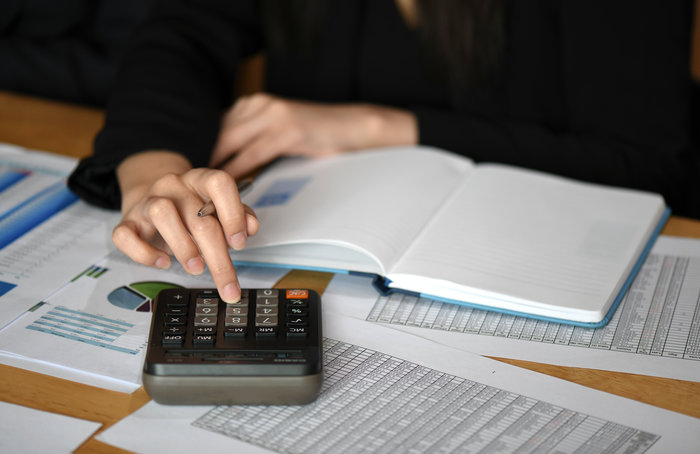
It’s not working…
These are words no facility manager wants to hear. The only other information that could make the situation worse? It might take a week to fix this piece of equipment, and we’re gonna have to pay expedited shipping costs for parts we don’t have on hand!
Of course, it’s no secret that running large facilities is expensive. Facility managers are responsible for overseeing many competing financial priorities, including capital improvements, departmental costs, operational expenses, building maintenance, and more. Those wanting to move ahead in their careers would be wise to develop a skill for cutting costs for a simple reason: The more adept you become at uncovering hidden savings opportunities, the more valuable you become to the facility owners in need of your services.
In this article, we’ll review our best facility management tips for reducing costs, increasing efficiency, and streamlining operations. After reading, you will be poised to make a greater impact within your facilities.
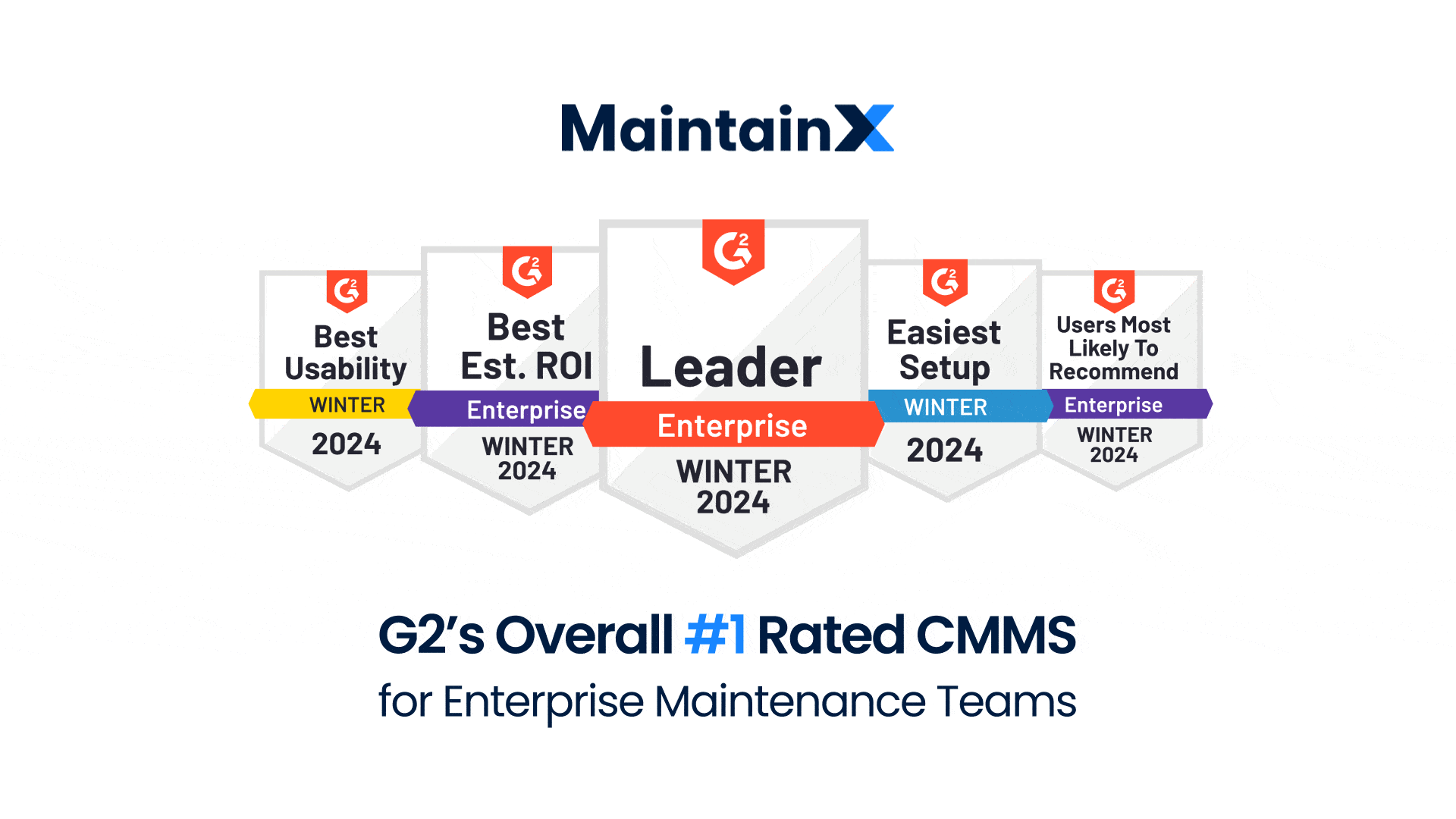
4 Facility Management Tips for Cutting Costs
1. Maintain Updated Documentation on Assets
As of December 2019, public companies are now required to list all lease assets with terms of more than 12 months as liabilities. The new rules implemented by the Financial Accounting Standards Board (FASB) ask organizations to maintain the following data points for each liability:
- Lease agreement and type
- Lease terms
- Start and end date
- The owner and lessee
- Monthly payment
- Fair market value
- Useful life
However, consistently managing assets shouldn’t be seen as an inconvenient compliance standard. It’s an integral component of every successful preventive maintenance program. Updated equipment documentation should also include information about recent service dates, asset locations, manufacturer recommendations, and more.
If you’re responsible for managing a lot of equipment—for a manufacturing plant or an airline, perhaps—chances are you have thousands of assets within your care. Unfortunately, that number often translates to tens of thousands of papers, clipboards, and binders to keep up with. This brings us to facility management tip number two:
2. Download Facility Management Software
There is no reason for facility managers to be wasting time with disorganized paper stacks or spreadsheets in 2020! Yet a large segment of them are still relying on them for an unfortunate reason
Put simply, there is still an industry-wide perception that FM software is expensive to purchase, complicated to use, and not worth the initial setup. Fortunately, those sentiments couldn’t be further from the truth. Today’s best facility management (FM) software options are cloud-based, scalable, and user-friendly. Also called Computerized Maintenance Management Systems (CMMS), these platforms provide a smorgasbord of features designed to reduce your workload, decrease downtime, and identify hidden cost savings opportunities that make you look like a genius.
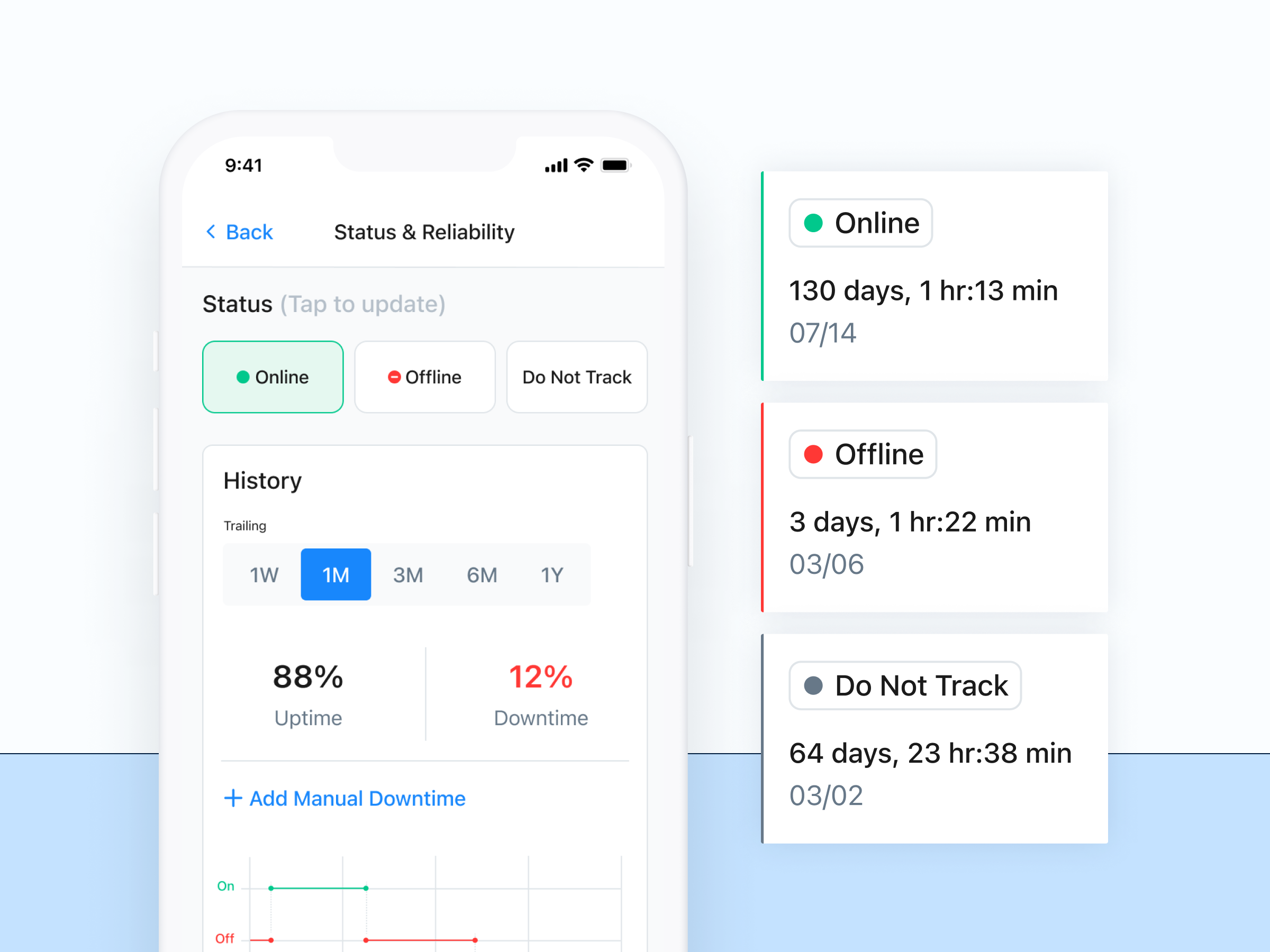
The MaintainX CMMS platform even takes things a step further with integrated instant messaging, work order commenting, and smartphone compatibility designed to streamline communication. Multi-site facility managers can conveniently create recurring work orders, index assets, track completion times, monitor data analytics, and more. The best part? The basic plan is free to download for iOs, Android, and desktop.
3. Practice Preventive Maintenance (and Life Cycle Cost Analysis)
As previously mentioned, asset management is vital to maintaining smooth facility operations. Document the lifespan of each machine within your care, and follow through with recommended upkeep, and you can better anticipate incoming repairs and replacement costs.
For example, say your facility’s copy machine is on the fritz: Should you buy a new, $10,000 model that might last for a decade or should you repair your 3-year-old machine for $3,000? While proper preventive maintenance reduces the likelihood of such breakdowns happening in the first place, life cycle cost analysis helps facility managers answer these kinds of questions with confidence.
FM software-driven PM programs often reveal organizational inefficiencies by providing data-driven answers to questions like:
- What is the cost per hour of downtime for asset X?
- What are the most time-consuming tasks in our facility?
- How much overtime have we paid because of asset X?
Honestly, once you become accustomed to having this type of information at your fingertips, you will never return to Excel spreadsheets.
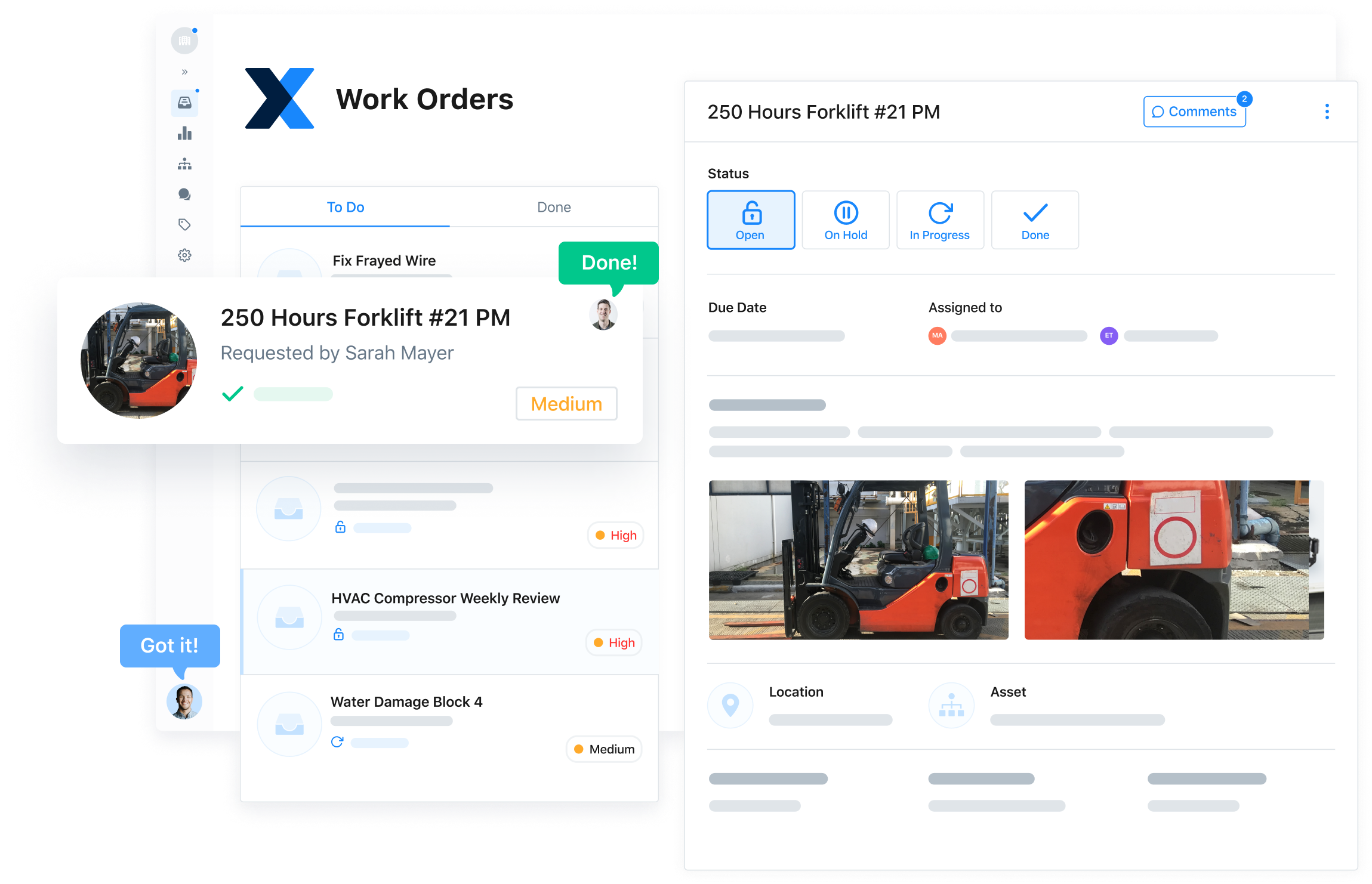
4. Equip Your Team for Success
Your new preventive maintenance and asset management program will only be as successful as the people behind it. One of the biggest challenges faced by facility managers is cultivating compliance. While work order software like MaintainX enhances accountability with time-stamp task completion, facilities must also strive to shape organizational culture. According to a McKinsey report on the psychology of change management, facilities can take four steps to effectively change staff mentality:
- Articulate a larger purpose that team members can get behind.
- Reinforce new facility systems by repeating information.
- Provide opportunities for workers to gain new skills
- Never underestimate the power of role models.
Facility managers must ask themselves which workers are impacting downtime the most––technicians, supervisors, line operators— and direct their attention toward equipping those individuals for success. The second most common cause of downtime after equipment failure is operator error. Your team members should feel confident in diagnosing, fixing, and problem-solving assets in all types of situations.
Beyond hosting technical workshops, facility managers should provide accessible and updated documentation that allows operators to act quickly. Again, the right FM software designed for smartphones can help with this. Consider combining the roles of operator and maintenance technician into a hybrid position that empowers workers to “fix their own problems.”
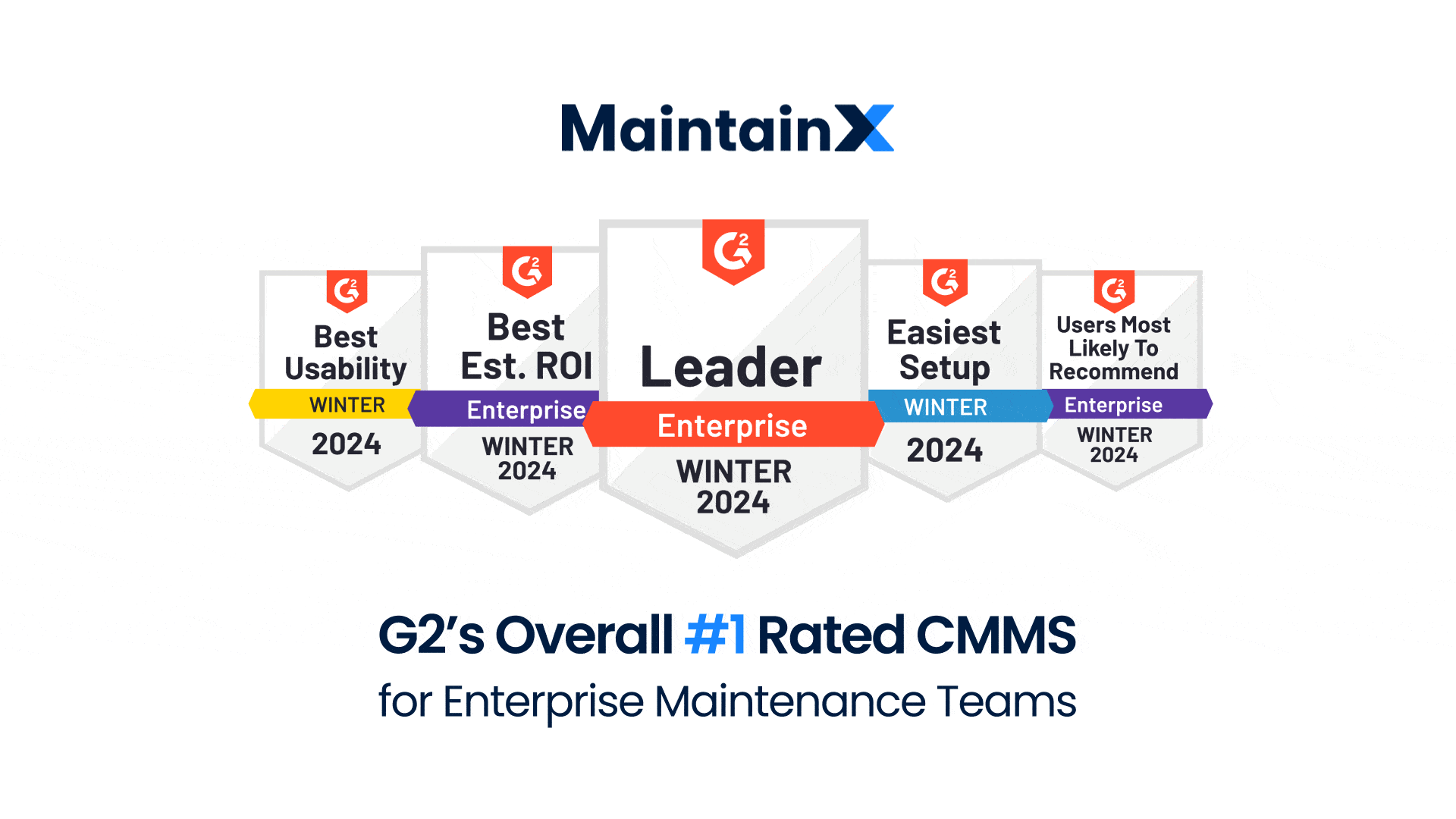
Change Your Mindset from Reactive to Proactive
We hope these facility management tips have inspired you to begin implementing preventive maintenance, asset life-cycle analysis, CMMS software usage, and team training within your organization.
While the right software can do amazing things for your facilities, your mindset will play the largest role in determining whether these measures are successful in reducing facility maintenance costs. Choose a smartphone-friendly facility management system that requires little to no training for usage. Commit to shifting your thinking from reactive to proactive maintenance. And you are well on your way to becoming an in-demand facility manager.
FAQs
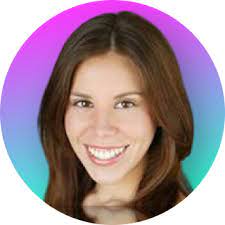