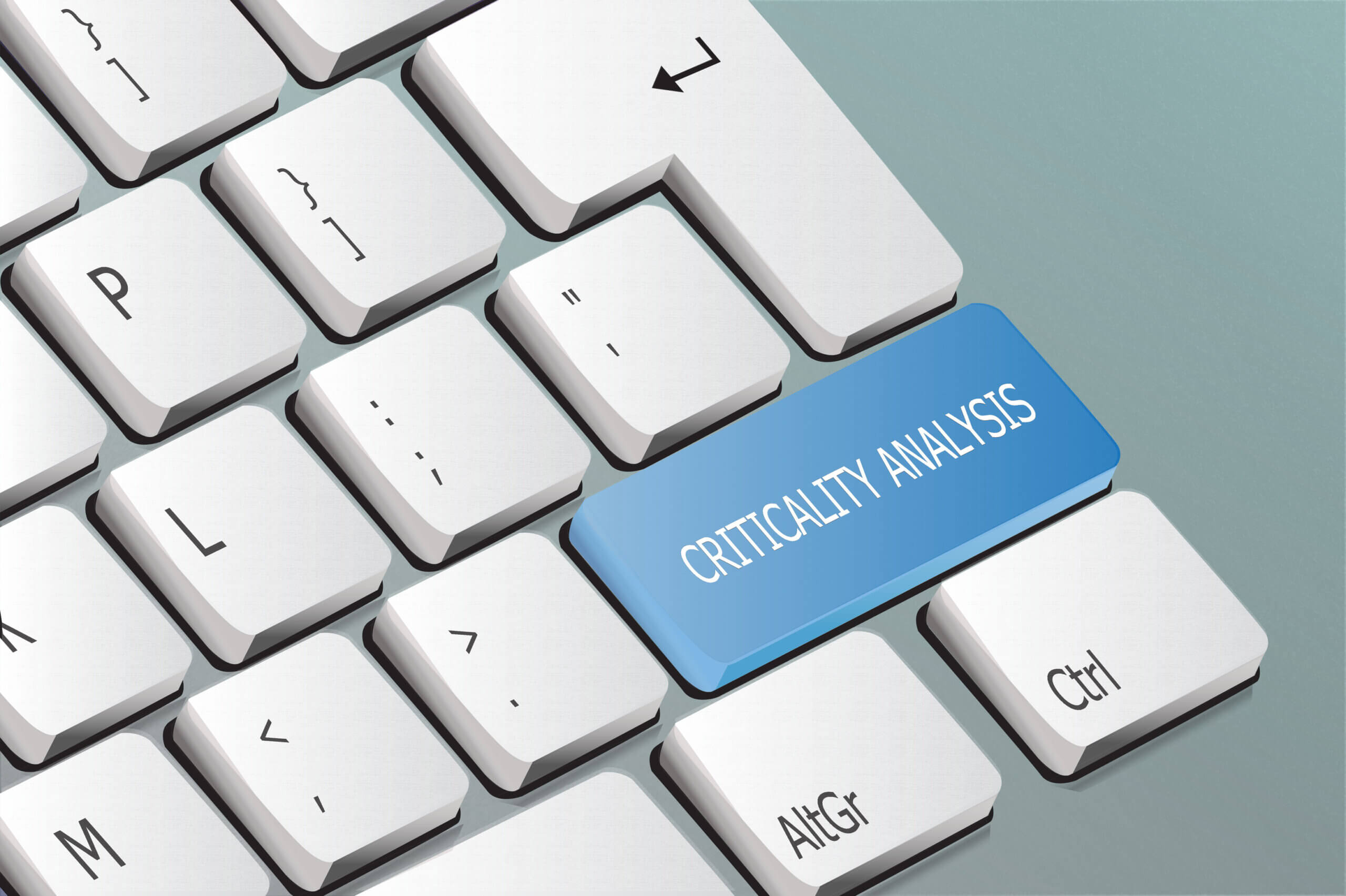
Criticality analysis helps determine the prioritization of each piece of equipment based on various factors. In this guide, we help you understand maintenance criticality analysis, how it can inform your maintenance strategy, and how you assign maintenance teams.
Growth brings multiple challenges. Over time, you’ll need to hire more people and maintain more assets. You’ll struggle to meet your asset’s maintenance needs without a solid proactive maintenance strategy.
What Is Maintenance Criticality Analysis?
Maintenance criticality analysis is a methodology to prioritize equipment maintenance based on various factors, including asset failure frequency and the operational impact of those failures.
Criticality analysis involves assigning a rating to assets based on these factors. It adds objectivity to your maintenance strategy. For example, your most critical assets, more prone to failure and to cause greater operational disruption, have a higher criticality rating and should be prioritized during maintenance.
This helps optimize maintenance spending and increases equipment reliability and uptime. In addition, criticality analysis aligns with the ISO 55000:2014 standard that provides guidelines for establishing a maintenance regime based on criticality.
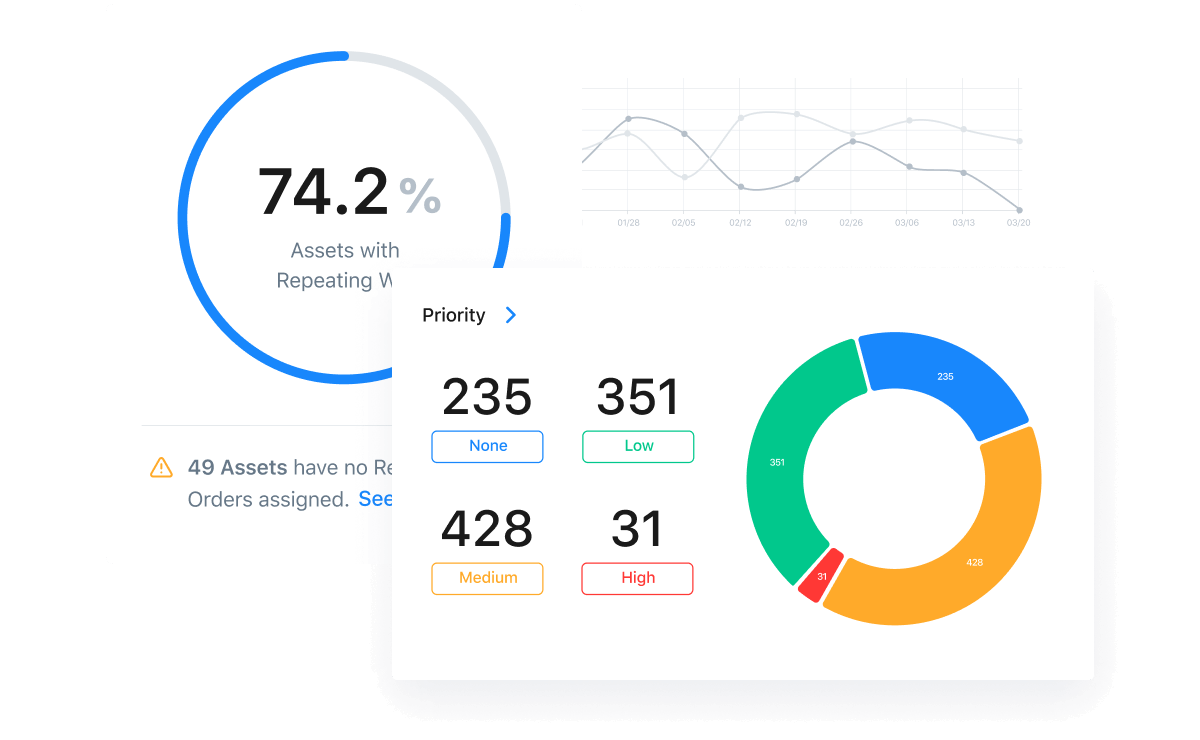
You can think of criticality analysis as part of a more comprehensive approach like failure modes, effects, and criticality analysis (FMECA), FMEA, root cause analysis, or a framework like reliability-centered maintenance (RCM).
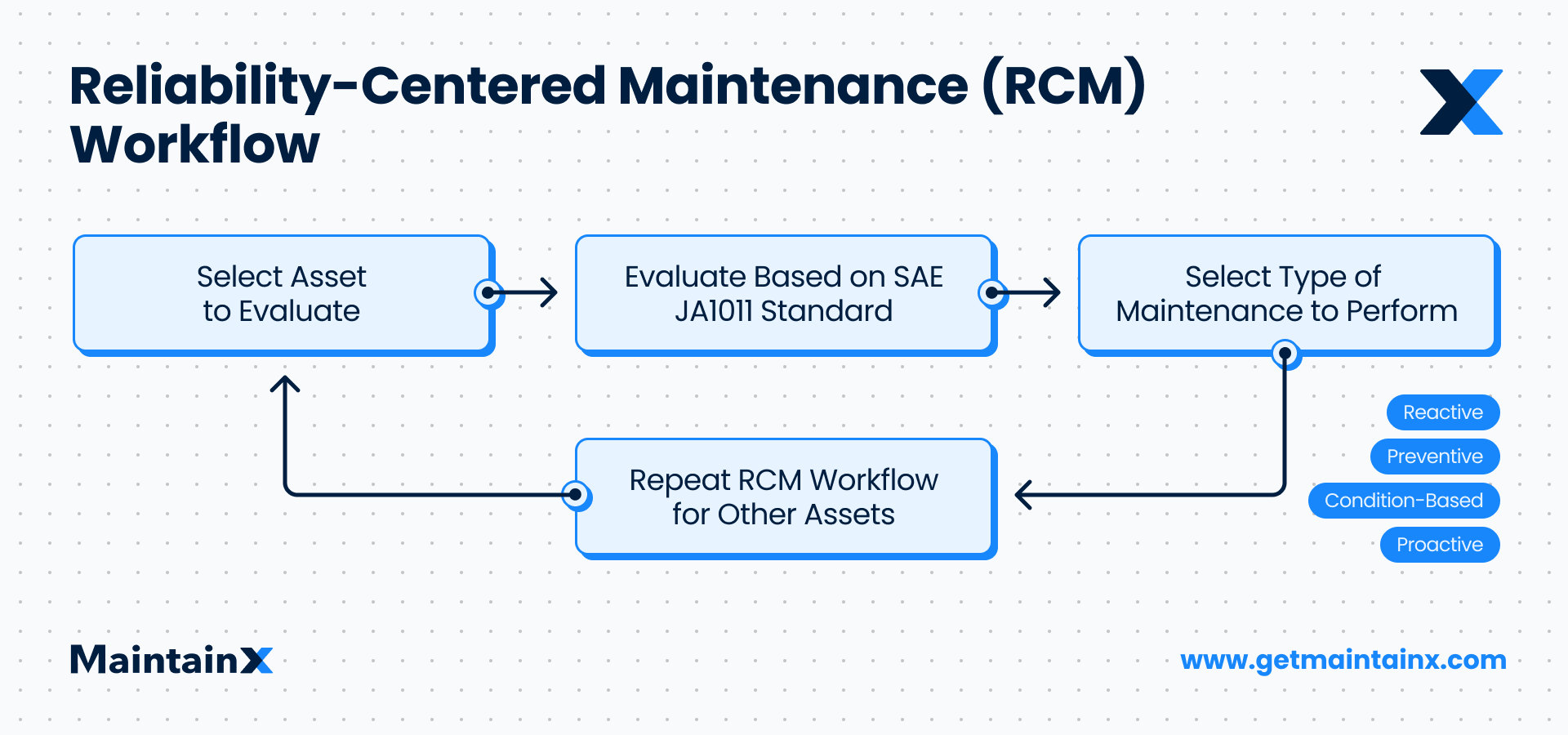
On the other hand, you can focus on criticality analysis to prioritize critical equipment for maintenance tasks. These approaches help reinforce decision-making, such as knowing when to upgrade based on when even effective maintenance no longer increases the asset lifecycle and the asset remains prone to failure. In fact, replacing the risk-based asset may become a high priority.
“An asset criticality assessment is a prioritization methodology intended to establish the most effective maintenance strategies for assets considering their importance and contribution to the plant’s business goals.”
Reliability WEB
How Maintenance Criticality Works
You can take a quantitative or qualitative approach to maintenance criticality.
Quantitative Approach
The quantitative approach uses the risk priority number (RPN) metric. Additionally, the RPN helps determine how the maintenance should be performed on assets.
To use the quantitative approach, you’ll need the following data:
- Severity: The severity of the potential failure on your overall system
- Occurrence: The probability of the failure occurring
- Detection: The likelihood that you’ll detect the failure
RPN = S x O x D
RPN = Severity x Occurrence x Detection
In factg, some industries have their own predefined rating system. However, you can also create your own rating table. For example, you can create a rating table for severity and occurrence probability:
Probability Table
Similarly, you can create a table to rate the detection probability:
Detection Chart
When creating your charts for severity, occurrence, and detection, consider factors like:
- Health and safety hazard: What’s the risk to staff’s health or safety when handling the equipment?
- Operational disruption: How severely will failure disrupt the operations? What’s the lead time for spare parts if the equipment requires emergency maintenance?
- Environment impact: How much can equipment failure adversely impact the environment?
- Cost of failure: What will be the cost of failure for the company?
Once you’ve prepared the charts and calculated the RPN, you’ll be better positioned to create a maintenance plan. Therefore, to categorize assets based on the criticality rating:
Categorize Assets by Criticality Rating
Next, create a spreadsheet list of all assets and their RPNs and sort this list by the RPN. Then, prioritize condition monitoring and preventive maintenance for equipment with high RPN.
“Maintenance criticality analysis allows you to quickly and easily make decisions regarding which preventive maintenance work may be moved in the schedule and which must be done on the date specified. In addition, you will be able to prioritize any issues that occur in order to keep your most critical equipment available, maximizing plant uptime.”
Prometheus Group
Qualitative Approach
The qualitative approach considers only the severity and occurrence probability, ignoring the detection probability. The qualitative approach is popular because it eliminates the complexity of determining the detection probability.
Therefore, the formula to compute criticality is:
Criticality = Severity x Occurrence
Next, create charts similar to the ones shown under the quantitative approach. Once you have the criticality ranking, create a criticality matrix (or a risk matrix) with the probability of occurrence on the vertical axis and severity on the horizontal axis like so:
Criticality Matrix
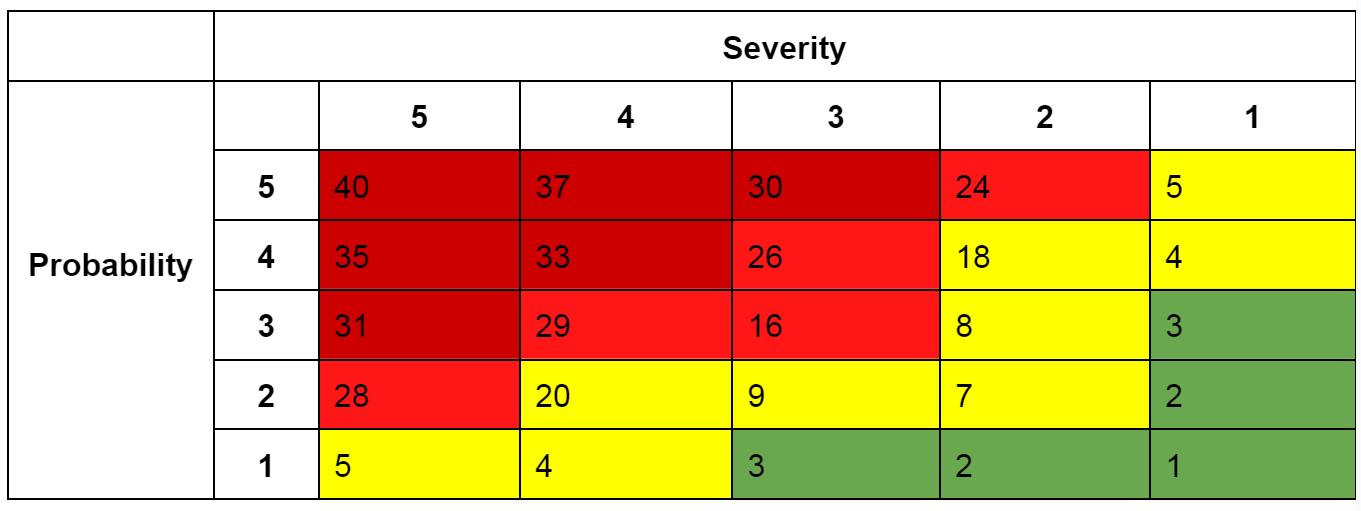
How to Optimize Maintenance Management Based on Asset Criticality Analysis
Maintenance programs are typically some combination of these strategies:
- Corrective maintenance
- Reactive maintenance
- Preventive maintenance
- Condition-based maintenance
- Predictive maintenance
Once you have insights about the impact of equipment failure from your asset criticality assessment, you’ll be able to identify the best strategies to maintain the equipment.
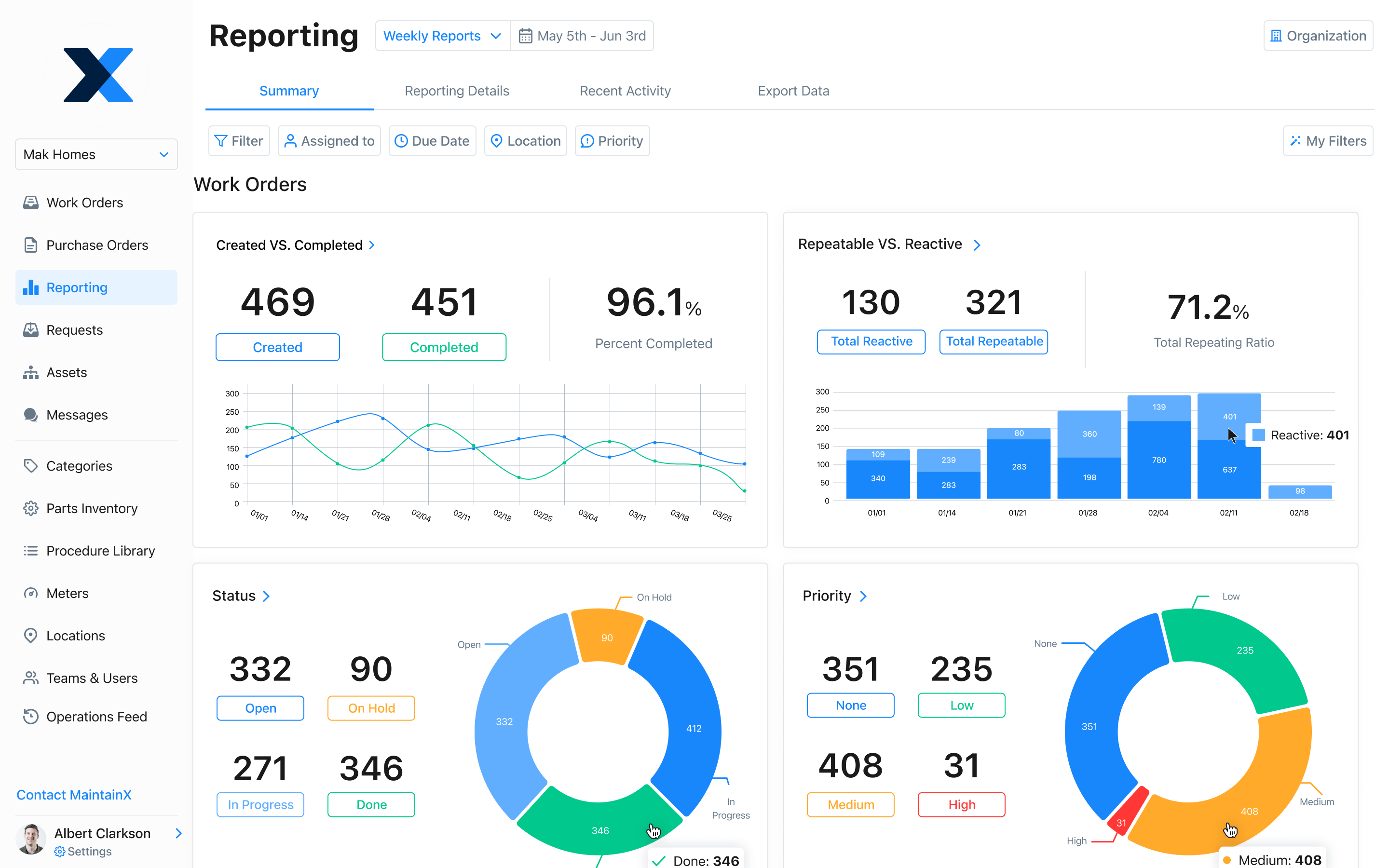
How to Determine the Right Maintenance Strategy Based on Criticality Analysis
In addition, you can determine an asset-wise maintenance strategy based on failure risk and impact.
Suppose you’re dealing with a high-criticality asset like a programmable logic controller (PLC) system. Importantly, PLC failure leads to an inability to monitor critical equipment, which can potentially result in non-compliance and bring operations to a halt.
Since it’s a critical asset, you should schedule preventive maintenance work orders like regularly cleaning debris from the PLC’s surface and changing filters to prevent failure.
However, things are different for low-criticality assets. For example, in some cases, it makes sense to run a low-criticality asset to failure. On the other hand, installing sensors on a low-criticality asset for proactive maintenance can unnecessarily balloon maintenance costs.
Simplify Maintenance Criticality Analysis with a CMMS
Finally, criticality analysis involves multiple steps that a computerized maintenance management system (CMMS) can simplify.
You’ll need asset management data, such as asset performance and downtime history, as inputs for criticality analysis. Next, you’ll need to manage the criticality analysis output (i.e., asset ranking). Finally, you’ll need to take action based on the effects analysis.
Get MaintainX for Your Maintenance Criticality Analysis
A CMMS like MaintainX can help with all of these aspects. MaintainX can provide easy access to historical information on maintenance and repairs. It stores data on the cloud and makes it remotely accessible.
When you need to perform maintenance, you can create work orders (or a complete maintenance schedule) in MaintainX. It helps monitor the effectiveness of your strategy for minimizing failure events. MaintainX summarizes maintenance costs and other asset performance metrics to validate your strategy.
If that sounds interesting, try MaintainX today!
FAQs
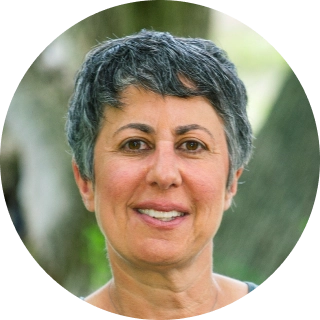
Caroline Eisner is a writer and editor with experience across the profit and nonprofit sectors, government, education, and financial organizations. She has held leadership positions in K16 institutions and has led large-scale digital projects, interactive websites, and a business writing consultancy.