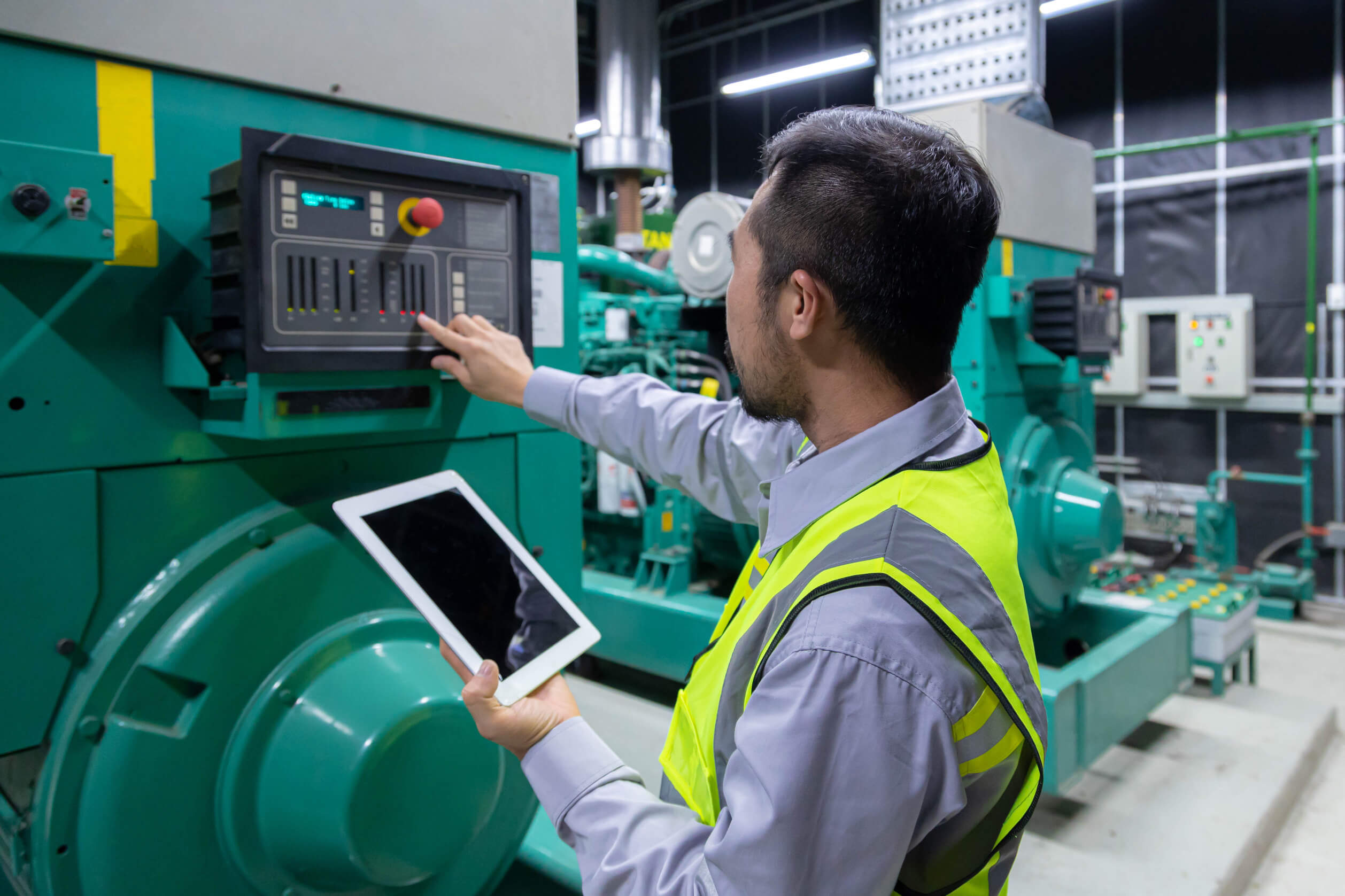
Predictive Maintenance can significantly impact an organization’s operations by improving equipment reliability, reducing downtime, and extending the useful life of assets. Several types of maintenance exist, but predictive maintenance aims to proactively identify and address potential equipment failures before they occur.
When executed properly, predictive maintenance can help reduce the frequency and duration of equipment failures. This can lead to improved equipment availability and increased production efficiency. Further benefits include improved customer satisfaction by reducing delays and disruptions. Additionally, by extending the useful life of equipment, predictive maintenance can help organizations reduce the costs of replacing and maintaining equipment, leading to long-term cost savings.
We’ll talk a bit more about cost savings shortly, but first, let’s take a closer look at how to create a predictive maintenance program.
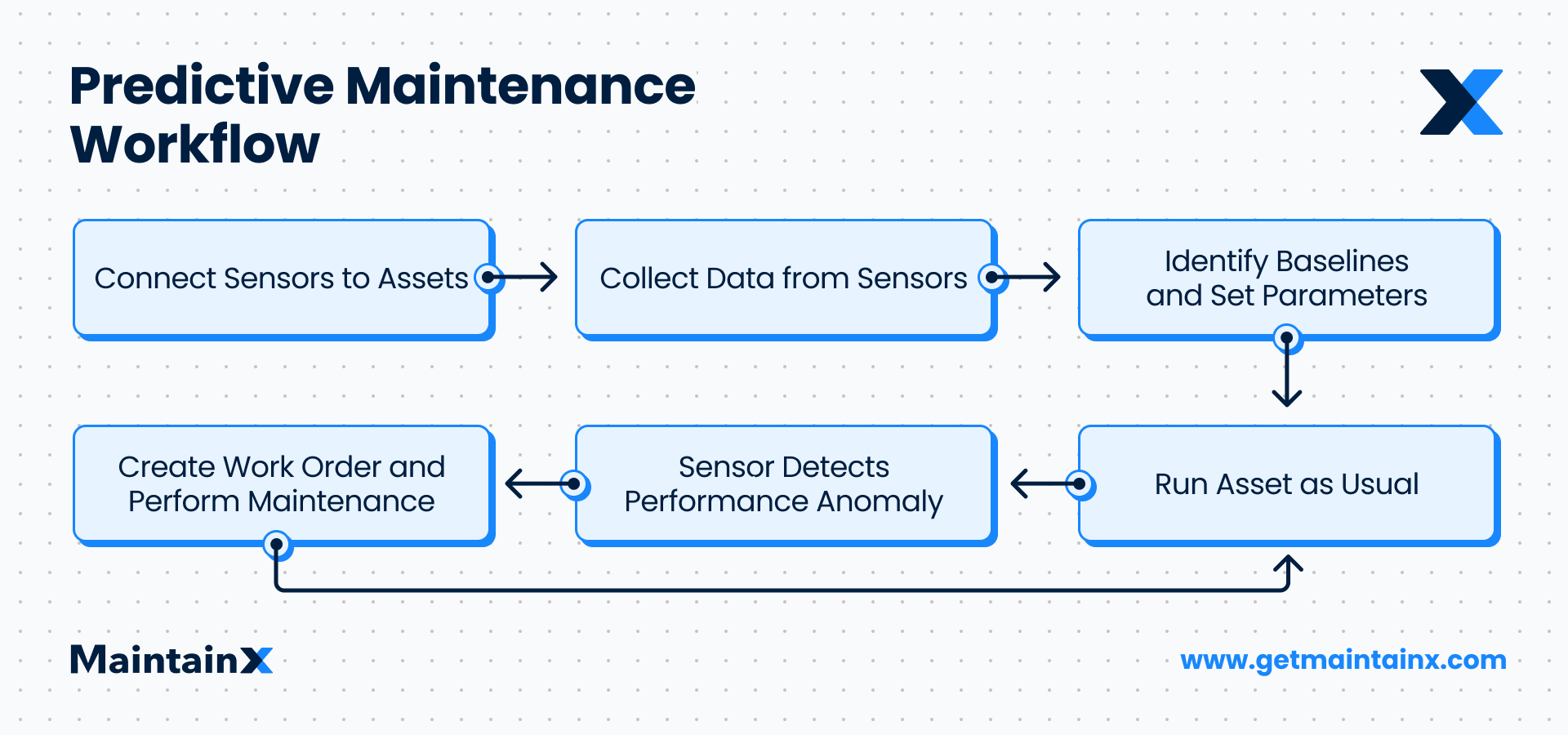
When to Use Predictive Maintenance
Choosing a predictive maintenance plan depends on the following:
- the specific characteristics of the equipment
- the nature of the organization’s operations, and
- the costs associated with equipment failures and maintenance.
We recommend PdM for equipment critical to the operation of your company and that experiences frequent failures or has a high cost of downtime. It also works for equipment that is expensive to maintain or replace or that is difficult to access for maintenance.
“When a manufacturing organization intends to roll out a strategy to address its uptime challenges and optimize its external service opportunities, improving the preventive maintenance capabilities is a great means to start.”
IoT Business
Predictive Maintenance Improves KPIs
Predictive maintenance can improve a variety of key performance indicators (KPIs) related to equipment reliability and maintenance. Some of these specific KPIs include:
1. Equipment Downtime
For asset-intensive industries, such as manufacturing, unplanned downtimes are costly. The International Society of Automation (ISA) estimates that factories lose between 5 and 20 percent of productive capacity during each downtime incident. Periodically tracking downtime is a crucial aspect of establishing a baseline for the effectiveness of all maintenance department activities.
The best way to reduce downtime is to place all critical pieces of equipment on PM maintenance schedules in accordance with the manufacturer’s guidelines. Not only will routine maintenance reduce costly breakdowns, but it will also extend asset life cycles.
2. Maintenance Backlogs and Overtime
Maintenance backlogs can play a significant role in the recruitment of maintenance technicians. Consistently tracking maintenance time and cost data will reveal whether a department is overstaffed or understaffed at any given time.
Too many outstanding worker orders suggest the need to hire additional staff. Alternatively, no backlogs could indicate an unnecessarily large team that could be trimmed.
Managers can also measure overtime to determine if the department is relying too heavily on reactive maintenance. An over-reliance on reactive maintenance leads to technician burnout, unnecessarily high maintenance costs, costly downtime, and reduced productivity.
3. Asset Performance Metrics
Asset performance metrics allow you to track the effectiveness of your maintenance programs. The most revealing metrics to track include the following:
- Mean Time Between Failure (MTBF): MTBF refers to the amount of time it takes before asset failure occurs. It measures the amount of time between failures. MTBF is only measured for repairable assets. Increasing your MTBF for critical assets can help optimize your overall maintenance strategy and improve productivity.
- Mean Time to Repair (MTTR): MTTR measures the average amount of time it takes your maintenance team to repair a broken-down asset. This maintenance performance metric includes diagnosis, repair, and recovery time. MTTR is key to identifying and eliminating inefficiencies in maintenance processes.
- Overall Equipment Effectiveness (OEE): OEE is a metric used to gauge overall facility performance. It measures the productivity of facilities, machinery, and processes. When measuring OEE, it’s essential to factor in equipment availability, performance efficiency, and product quality. OEE helps identify departmental waste and inform improvements to SOPs.
Always seek to identify the root cause of poor performance metrics. This requires investigating SOPs for problematic bottlenecks, gathering input from maintenance personnel, and evaluating existing communication systems.
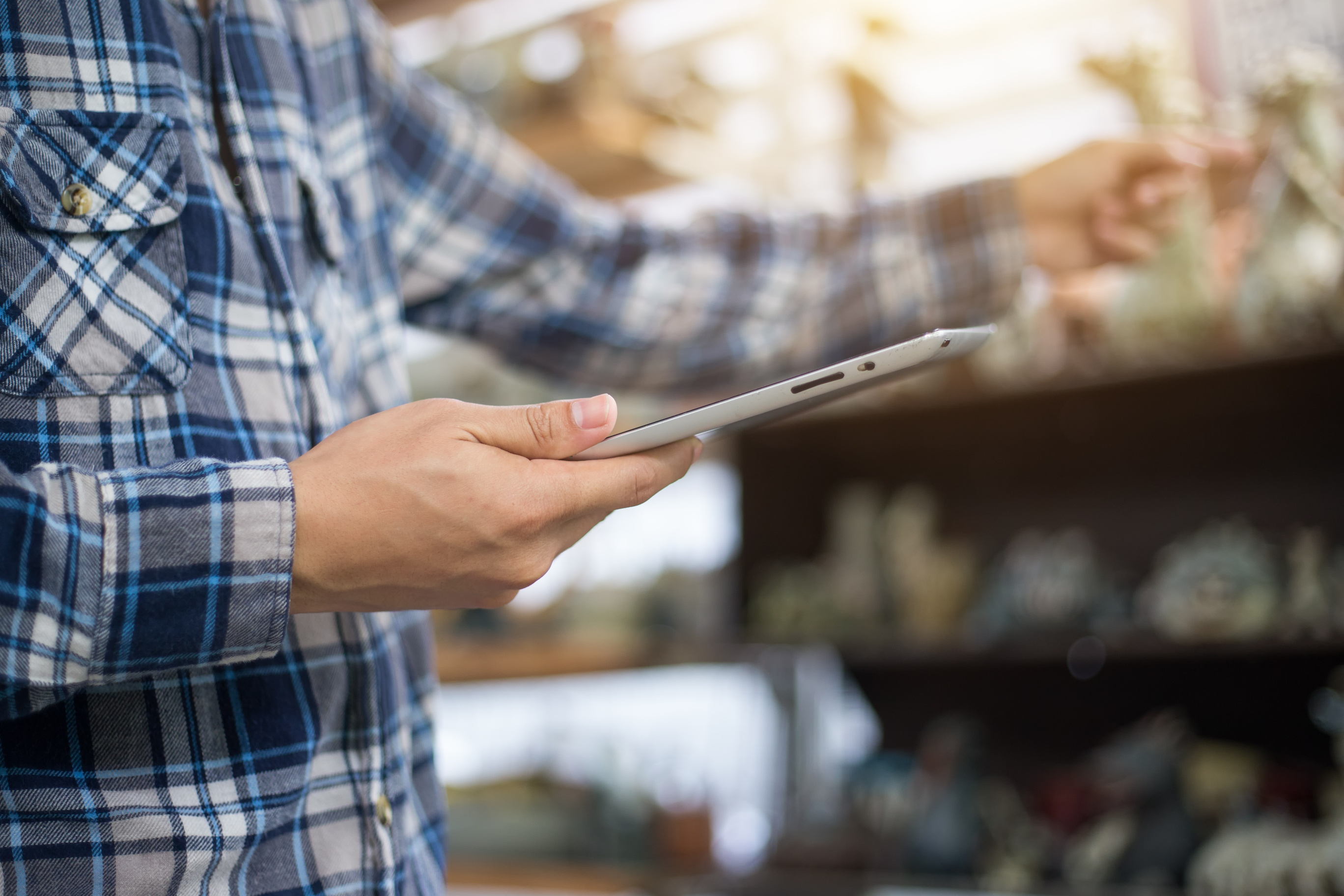
4. Operational Metrics
Operational metrics such as Planned Maintenance Percentage (PMP) and Schedule Compliance are also worth keeping an eye on.
PMP measures the percentage of your overall maintenance time that’s dedicated to planned maintenance. Higher PMPs suggest that your maintenance plans are effective and your team isn’t overly reliant on reactive maintenance.
Schedule compliance, also referred to as preventive maintenance compliance, is a metric used to measure the percentage of PM activities completed as scheduled. Just like PMP, higher schedule compliance suggests that PM planning and scheduling are effective.
5. Predictive Maintenance Cost as Percent of RAV
Lastly, track your replacement asset value (RAV) if you’re trying to determine the cost-effectiveness of your maintenance operations.
RAV refers to the amount of money it would cost to replace a production plant along with its existing assets at the current moment. When calculating RAV, include the facility itself and all of the physical assets within it that require routine maintenance.
However, don’t include working capital such as raw materials. Other maintenance metrics worth tracking include replacement parts inventory management, asset uptime, and availability, the number of workplace incidents and accidents, and the number of requests for rework. So the question now is how can we optimize for cost savings? That’s where a CMMS comes in.
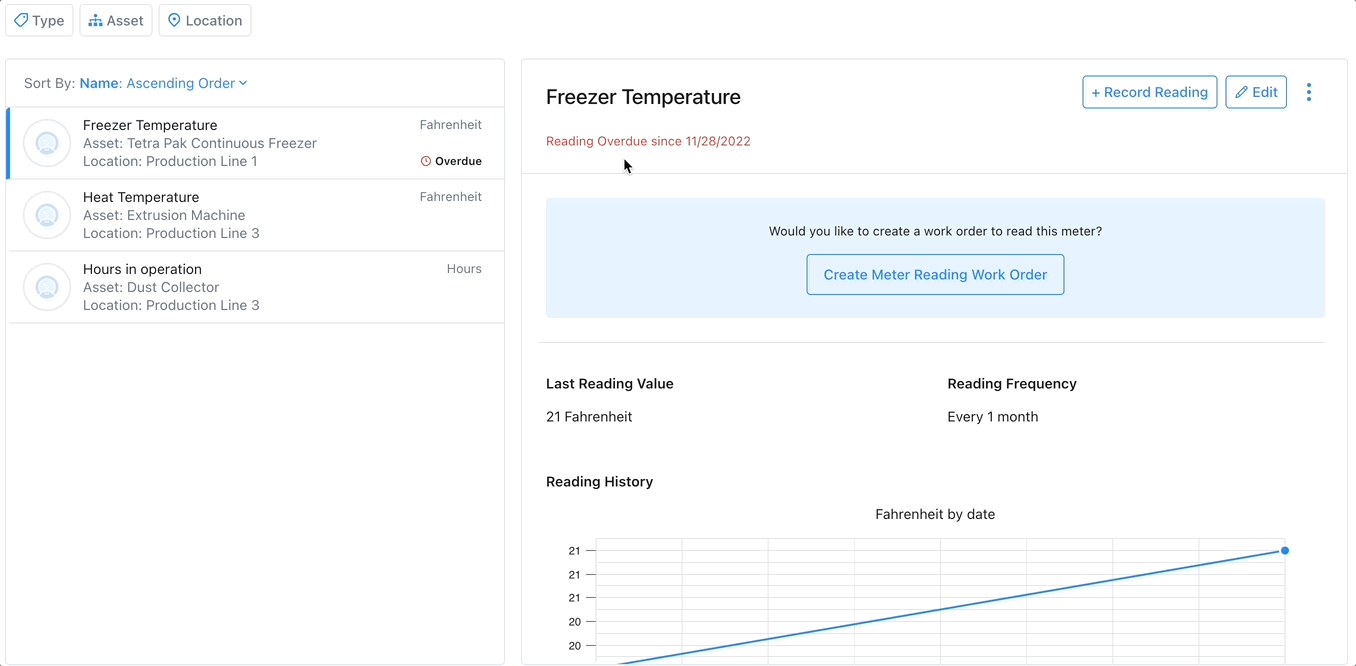
How Predictive Maintenance with a CMMS Saves You Money
A well-designed Computerized Maintenance Management System (CMMS) is a software tool for managing your maintenance activities. If you’re thinking of implementing a predictive maintenance strategy, you should consider using a CMMS.
As reported in the Agility Effect, “Based on our observations of digital maintenance and reliability transformations in heavy industries, we see the potential for companies to increase asset availability by 5 to 15 percent and reduce maintenance costs by 18 to 25 percent” (McKinsey). A CMMS can achieve several specific cost savings with a predictive maintenance strategy.
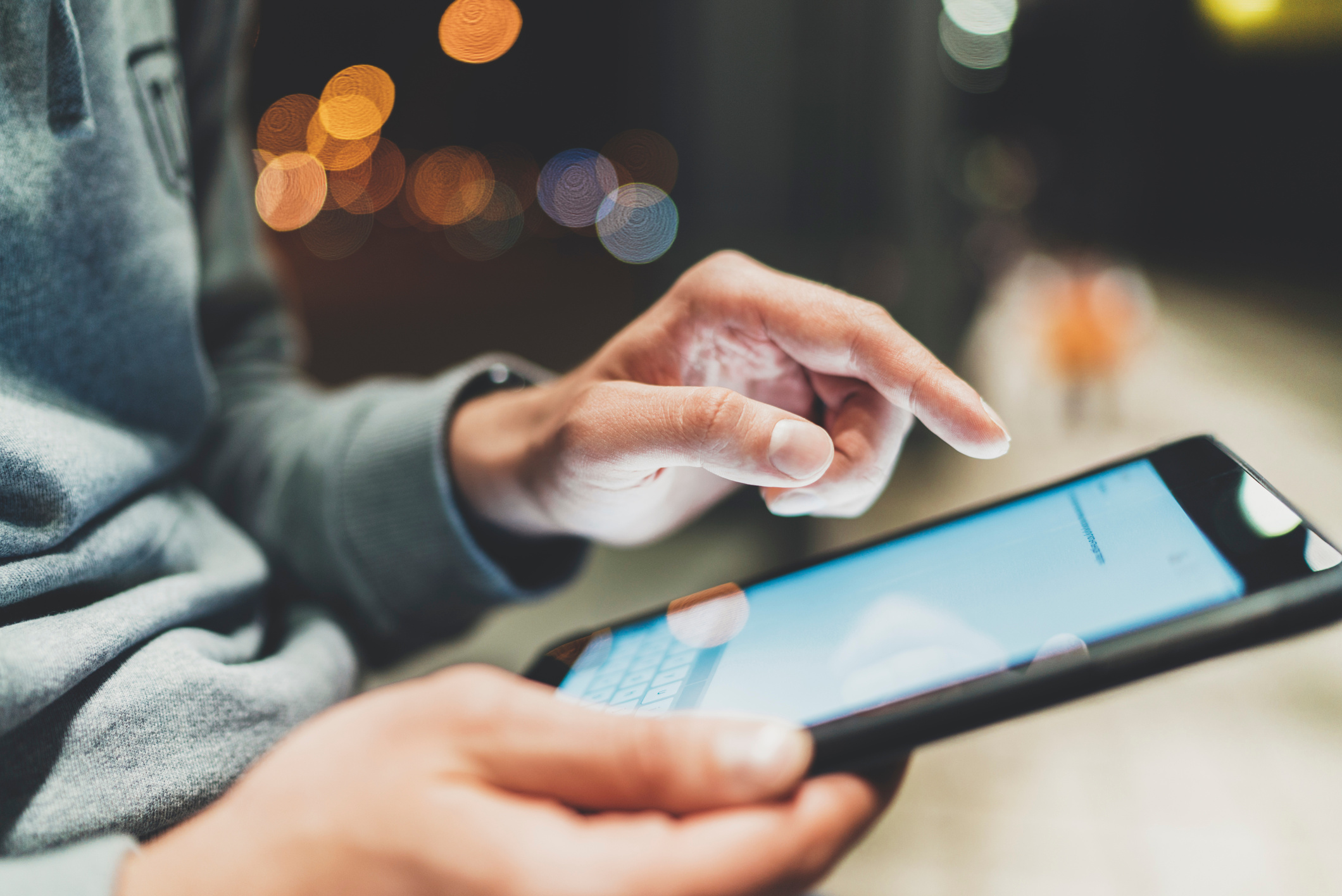
Here are a few of the ways predictive maintenance cuts costs:
Companies can use predictive maintenance to monitor a range of equipment, including mechanical, electrical, and electronic systems and industrial and consumer equipment. By identifying and addressing potential equipment failures before they occur, organizations can:
- reduce downtime: By identifying potential equipment failures and scheduling maintenance activities in advance, a CMMS can help reduce the need for reactive maintenance. Emergency repairs can be costly and disruptive. Predictive maintenance reduces costly shutdowns.
- improve equipment reliability: A CMMS can help improve the efficiency of maintenance activities by automating maintenance scheduling, tracking, and reporting. Instead of having to figure out how to organize these things whenever the need arises, you can lean on your automated work orders in a CMMS.
- optimize overall equipment effectiveness (OEE): Instead of having to figure out how to organize your maintenance activities, you can lean on your automated work orders in a CMMS. And along with OEE comes operational efficiency.
- extend the useful lifespan of your equipment: Fixed assets—pieces of equipment, machinery, and building components—depreciate over time. Useful life is a critical component of effectively managing assets to obtain their maximum value. Companies rely on the length-of-time metric to determine the tipping point at which investment in repairing the equipment becomes more expensive than replacing it.
- reduce O&M budgets and increase profits: A CMMS can help reduce inventory costs by providing real-time data on inventory levels and automating the ordering and replenishment of spare parts.
This proactive maintenance strategy is sometimes referred to as condition-based maintenance.
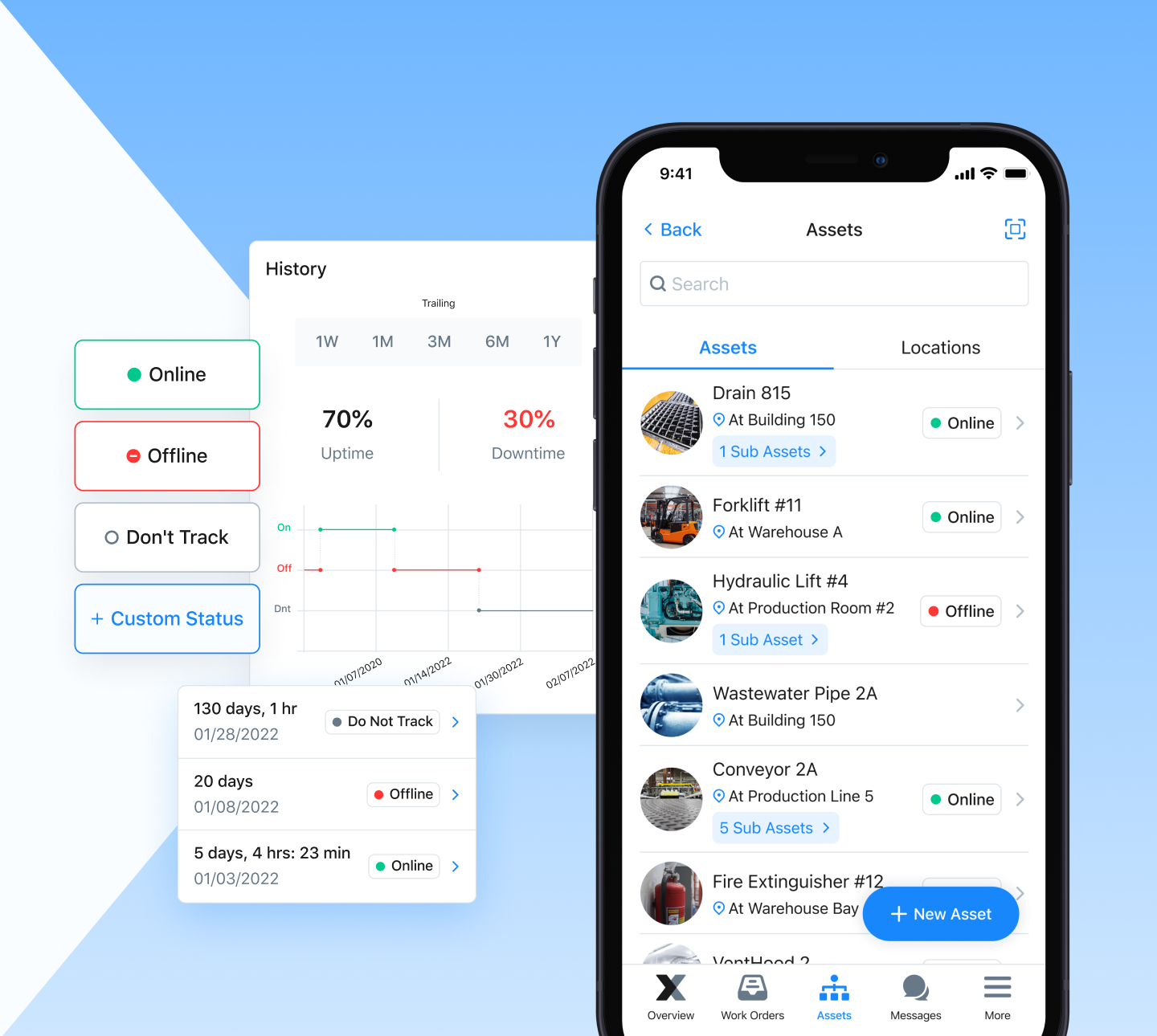
Use MaintainX to Achieve Your Predictive Maintenance Goals
Predictive maintenance works best when guided by 3 major pillars:
1. Data Management
MaintainX can help manage data analytics and collection by predictive maintenance sensors and monitoring equipment, including storing, organizing, and analyzing both the big data, as well as the everyday KPIs and metrics you set.
By centralizing the data in a single system, teams can more easily access the data when needed. This makes it easier for teams to carry out predictive analytics, identify patterns and trends concerning equipment condition, and act if need be.
MaintainX can generate reports on maintenance activities, including data on equipment failures, maintenance tasks, and maintenance costs. This can help teams better understand the maintenance needs of their equipment and identify opportunities for improvement.
2. Maintenance Scheduling
MaintainX can help schedule proactive maintenance activities in advance based on the data collected by IoT sensors. By using MaintainX to schedule maintenance activities, teams can more easily track and prioritize tasks, ensuring that maintenance activities are completed on time and that equipment is properly maintained.
3. Maintenance Tracking
MaintainX can help track maintenance activities, including the tasks that were completed, the personnel involved, and the equipment that was maintained. This can help teams ensure that maintenance activities are being properly completed and that equipment is being properly maintained.
Get MaintainX for Your PDM
Using a CMMS like MaintainX with a predictive maintenance program will help you achieve significant cost savings. MaintainX can help improve maintenance efficiency and reduce unplanned downtime, emergency repairs, and inventory costs. PdM, balanced with other forms of maintenance, implemented on MaintainX can seriously help improve your maintenance key performance indicators. Let us be the start of your digital transformation.
FAQs
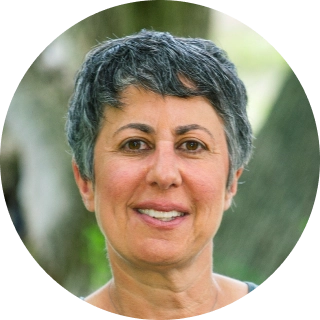
Caroline Eisner is a writer and editor with experience across the profit and nonprofit sectors, government, education, and financial organizations. She has held leadership positions in K16 institutions and has led large-scale digital projects, interactive websites, and a business writing consultancy.