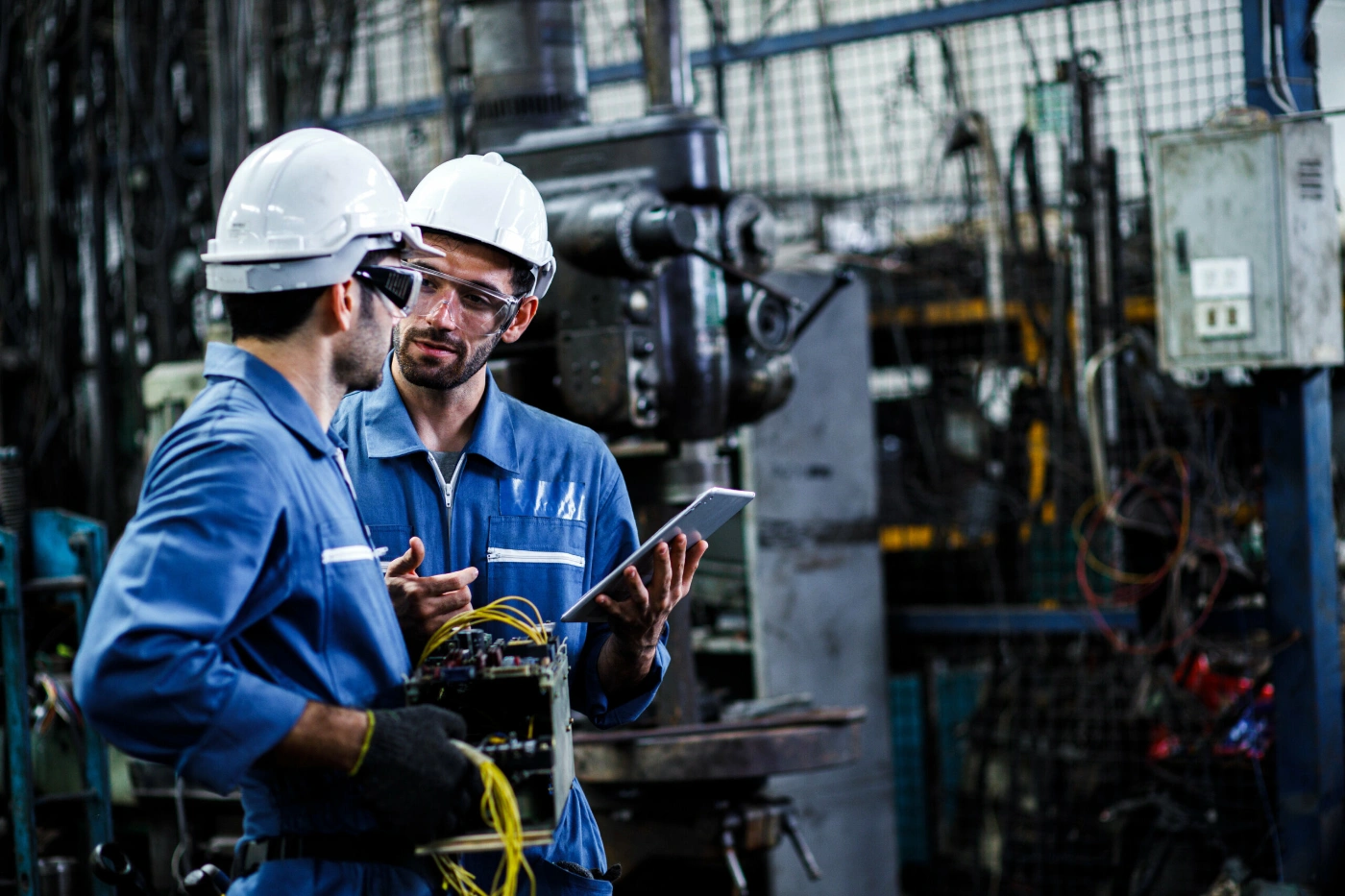
What Is Root Cause Analysis?
Root Cause Analysis (RCA) is a structured process of identifying, understanding, and solving production-related problems. According to the American Society for Quality (ASQ), RCA involves a range of tools, approaches, and techniques to drill down and identify the actual root causes of specific problems. As a result, RCA helps you go from panicked firefighting to rooting out problems and preventing future interruptions and unplanned downtime.
Imagine carrying out routine maintenance when you notice a blown fuse. Or even worse, a fuse blows in the middle of a production cycle. There’s nothing worse than getting knocked off schedule.
But, luckily, you’ve anticipated all kinds of mishaps and prepared for them.
For example, you take a quick look and realize an insufficiently lubricated bearing caused the sequence of events leading to the blown fuse. All you have to do is change the parts. Cause and effect repaired.
No big deal, right? You remember changing the same parts just two weeks ago after a similar incident. The last thing you want is to find yourself in the same place next month.
Here, we will discuss RCA’s various steps and methods to identify the root, solve the issues, and prevent their reoccurrence. RCA treats the underlying causes of a problem instead of the surface-level symptoms of the problem itself.
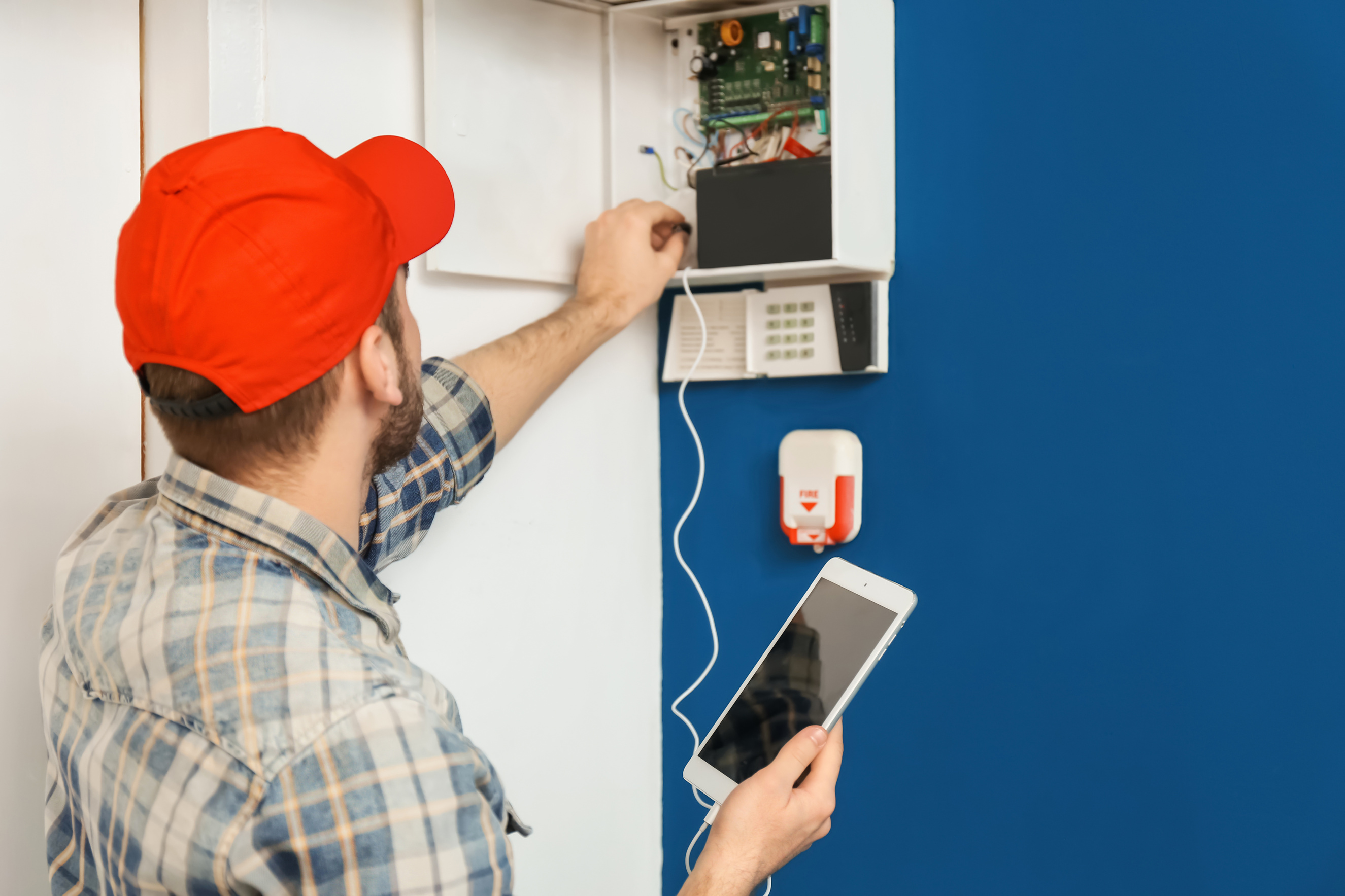
Other Types of Root Cause Analysis
You may already know about Failure Mode and Effects Analysis (FMEA), the process of assessing the potential root causes and impacts of equipment failures. Troubleshooting technicians often use a cause-and-effect diagram, known as an Ishikawa diagram (it looks like a fish), to work through FMEA.
It’s a proactive, data-driven, and team-oriented method for identifying the relative effect of various failure modes on productivity goals.
Pareto analysis is a statistical technique. Technicians analyze a select number of tasks depending on their impact on the overall effect. It’s based on the idea that 80 percent of problems result from 20 percent of causes. You may have seen a Pareto chart before. It contains both bars and a line graph, where individual values are represented in descending order.
How Can CMMS Help?
Computerized maintenance management systems (CMMS) provide a framework for a standardized approach to maintenance practices.
While RCA is a critical component of the international Total Quality Management (TQM) movement, there is no unified approach or methodology to problem solving.
RCA can be carried out using a wide range of processes, tools, and philosophies on just as wide a range of problems. You can apply it to procedural, material, equipment, personnel, and business processes, as well as to environmental factors. Using CMMS software allows professionals to customize RCA procedures to the specific needs of their equipment and facility. For example, you can create checklists, schedules, and problem statements for these purposes.
A CMMS also allows for the easy allocation of tasks to team members.
CMMS software provides professionals with tools for tracking malfunctions and maintenance. Think about the blown fuse. If nobody was present when the malfunction and parts replacement occurred, they would have to locate physical logs and records to review past incidents to see if the problem existed previously.
A CMMS app offers easy access to this information all in one place. In addition, you can track historical incidents and changes or maintenance steps taken in real time.
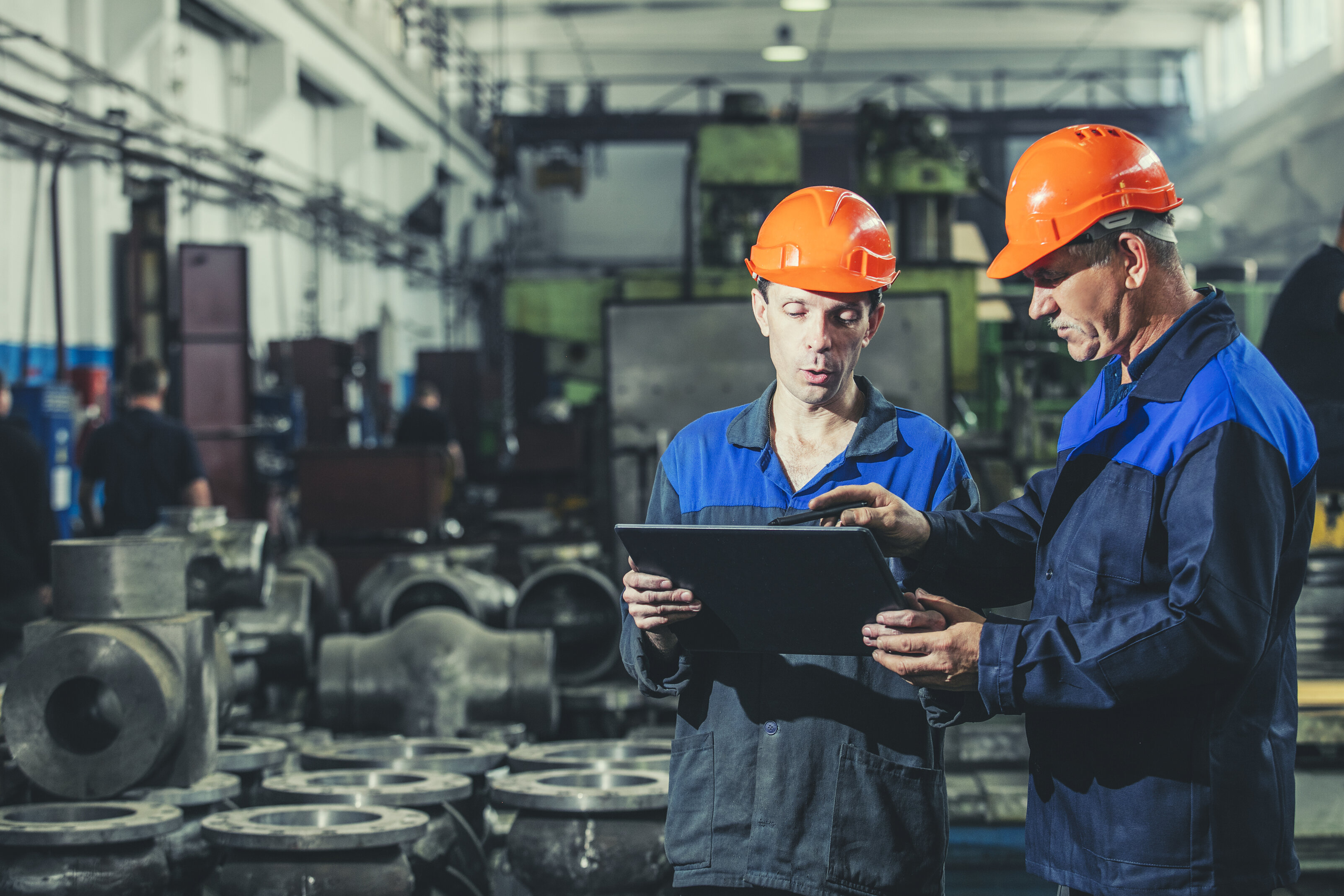
Benefits of Using a CMMS
Helps You Meet Regulations
OSHA prescribes strict regulations for workplace safety and risk management. Root Cause Analysis tools, such as fishbone diagrams, help organizations improve the safety and reliability of their working environments. Workplace injuries and illnesses have been reported per OSHA regulations since 2018. A CMMS like MaintainX will facilitate the quick and easy reporting of this data, ensuring organizations comply with OSHA reporting standards as they address root causes and take corrective action.
Helps You Delegate Tasks
The main components of effective root cause analysis include:
- defining the problem,
- performing the analysis to find the underlying cause, and
- implementing the solution.
Break these components into six phases:
- noting all the possible causes of a problem,
- collecting data and evidence,
- identifying contributing factors,
- analyzing data,
- developing a plan to prevent future occurrences, and
- implementing the process improvement (and maybe a quality control) plan.
Each phase also contains various steps and processes that can be adapted—for example, into an RCA template—as individual organizations see fit. A goal of RCA is continuous improvement that leads management to implement solutions.
A well-developed CMMS like MaintainX helps assign tasks and stages in the process to specific personnel. In addition, it stores details of what tasks have been performed and when, helping everyone keep track of where they are in the process and what they need to do.
Helps Staff Understand RCA Processes
Given the broad nature of RCA, staff members may be challenged to keep track of the various procedures, especially when a problem occurs. But, we know it’s faster and better than brainstorming possible causes and effects without a straightforward process.
Apart from processes such as “the Three Rs,” organizations also use methods such as the “5 Whys,” “Lean Six Sigma” technique, and “Fault Tree Analysis.” Rather than having staff commit all these to memory and risk forgetting critical steps while on the job, organizations can use a CMMS to collate various sources of information that staff can then access to find the causal factor and root cause of a problem.
MaintainX’s Learning Center and Global Procedure Library house various RCA knowledge resources.
Help You Communicate with Your Team
A robust CMMS software facilitates team communication through real-time messaging. MaintainX provides mobile and desktop messaging as well as commenting functionality directly within digital work orders. In addition, MaintainX provides users with both private and team messaging threads, helping team members collaborate from the field.
RCA Examples Using CMMS
- At-your-fingertips asset data, including information about a problem’s first occurrence, past repairs, and its impact on the organization.
- Manufacturer manuals, machine operating characteristics, and similar critical information are easily accessible to technicians in work orders and procedures at all times.
- Available parts inventory and onsite purchase ordering.
- Checklists and standard operating procedures for implementing RCA in reactive maintenance situations.
Which Is the Best CMMS Software for RCA?
Several CMMS software solutions are available on the market. However, as of July 2022, MaintainX is the highest ranked, with an overall rating of 4.8 on Capterra, 4.6 on Google Play, and 4.9 on the Apple App Store. MaintainX offers unlimited work order creation and asset cataloging. It also offers parts inventory and facilitates team communication through unlimited team messaging. The paid version provides advanced functionality and costs $10 per user/monthly, the lowest entry-level price in the marketplace.
There is no one-size-fits-all approach to Root Cause Analysis, but MaintainX offers the knowledge and tools to adapt existing processes to your organization’s needs. The platform is also easy to use and requires little-to-no training. Simply download the app to your desktop or mobile device and get started.
FAQs
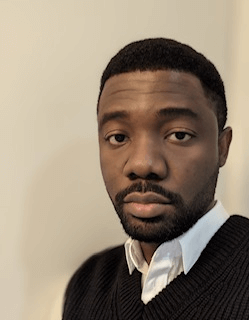
Lekan Olanrewaju is a content writer with years of experience in media and content creation. He has held positions at various media organizations, working with and leading teams at print magazines, digital publications, and television productions.