_%20Ranking%20the%20Top%20Vendors-1080x720.webp)
The hardest part about searching for a CMMS (computerized maintenance management system) is knowing what information you can trust. It can also be overwhelming to digest opinions from dozens of vendors, industry analysts, and ranking sites.
But the biggest problem is none of these sources rely on insights from people who use the software.
That’s what makes this comparison guide different—its primary source of data is the words of maintenance and asset management professionals who have stood where you are now.
This guide compares nine CMMS software vendors with the help of thousands of reviews about the strengths, gaps, and capabilities of each solution to help you find the right maintenance software for your team.
Key Takeaways
- This guide compares nine leading CMMS platforms using 100% user-generated feedback from maintenance management and asset management professionals.
- MaintainX ranks as the top overall CMMS software, praised for mobile-first design, scalability, and ease of use.
Who is this guide for?
This guide is a fit if the following sound like you:
- By role
- Maintenance leaders: Maintenance managers, directors, supervisors, and others that manage maintenance operations.
- Plant and facilities leaders: Plant, facility, and operations managers.
- By industry
- Manufacturing: Automotive, building materials, chemicals, food and beverage, heavy machinery, plastics, and other manufacturing segments.
- Warehousing and logistics: Retail distribution centers, logistics providers, and fleet management.
- Facilities: Property management, universities, hospitals, and resorts.
- By team size
- Maintenance teams with 10 or more people operating at a single site or across multiple sites
- By current solution
- Replacing a CMMS: Maintenance teams that have CMMS software, but are looking to replace it.
- No CMMS: Maintenance teams transitioning to a CMMS from spreadsheets, paper work orders, or nothing at all.
While you’ll still find helpful information for your CMMS search, this guide is not geared toward:
- Buyers seeking ERP platforms, broader operational software, or other enterprise systems for tasks beyond managing maintenance processes.
- Companies committed to custom-built or on-premise tools to manage maintenance operations.
- Those looking to manage maintenance tasks for residential property management or small-scale building maintenance.
How we assessed CMMS software solutions for this guide
Each CMMS software was assessed based on direct customer insights from the following sources:
Each CMMS needed to have a minimum volume of reviews on each platform to ensure well-rounded feedback from users.
Best overall CMMS software: MaintainX
What makes MaintainX the best overall CMMS software
Ease of use: Reviewers consistently praised its intuitive, user friendly interface, calling it simple enough for technicians with limited tech experience to pick up on day one.
Mobile functionality: The mobile app was a standout feature, with many users highlighting how easy it was to schedule preventive maintenance, complete work orders, upload images, and stay updated on the go.
Scalability and support: Maintenance leaders managing multiple sites appreciated how easily MaintainX scaled, with responsive customer support guiding them through rollouts and changes.
Reporting and visibility: Reviewers valued the clear, built-in reports for tracking KPIs, asset histories, and task completion, crediting it with helping them stay audit-ready and data-informed.
Customization without complexity: Users loved how they could tailor workflows, forms, and permissions to match their needs without needing IT involvement or expensive consultants.
How the Top CMMS Software Compare: Key Features, Fit, and Feedback
MaintainX
What customers like
- A mobile-first experience: The technician-friendly mobile application allows teams to see preventive maintenance tasks, execute work quickly, and track resources more accurately.
- Fast, easy adoption: Reviewers say even non-technical users can learn the platform in minutes, making it ideal for cross-functional teams.
- Multi-site coordination: Teams praise how easily MaintainX scales across facilities to standardize maintenance processes and communication.
What to watch out for
- Not built for ultra-regulated industries: While built for broad use cases, it’s not currently designed for organizations and maintenance operations that are constrained by strict regulations.
- Advanced workflows require support: Some complex use cases require involvement from support to configure.
What customers think of MaintainX
“The user interface is great and so is the mobile app. There is plenty of customization for us to grow without major limitations. Customer support has been top notch. Very easy to integrate.” - Ben B., Senior Maintenance Lead
“This system is very user-friendly and intuitive. Creating work orders and loading information is as easy as it comes, and has saved us so many hours of data entry.” - Neal G., Plant Manager
“We've used MaintainX to streamline our maintenance operations, and the results have been outstanding. The platform is intuitive, user-friendly, and packed with features that simplify work order management, asset tracking, and team communication.” - Craig M., Operations Manager
“Using MaintainX has been a game changer. The interface is the best I have come across. Ordering parts and creating work requests are just a few simple clicks. With an open API, it is a few moments to set up an integration with PowerBI to customize any report you see fit.” - Gartner Peer Reviews Reviewer
“MaintainX has streamlined the management of our facility and equipment and allowed our organization to become more efficient in resolving equipment issues.” - Gartner Peer Reviews Reviewer
Limble
Key features
- Solid core functionality: Reviewers like the feature depth across preventive maintenance, parts, analytics, and asset tracking.
- Onboarding with guidance: Teams appreciated how fast they got up and running with onboarding and training support.
- Technician usability: Technicians find the mobile app intuitive for completing maintenance tasks, even in offline or multi-language environments.
What to watch out for
- Complex reporting setup: Users say it takes lots of effort and/or support to set up custom dashboards. “The least liked item for me is the dashboards. There are no standard reports. Everything must be custom built.” - Mark H.
Manual setup without clean data: Teams without pre-organized asset data reported longer implementation timelines. - Limited user controls: Some users wanted more detailed permissions or configuration options. “Can be slow at times which causes challenges for my team. Part search is still an issue. Reporting to those outside of Limble is not as easy as I would hope”. - Ed. P.
- Disconnect between mobile and desktop apps: Customers mentioned that some capabilities available on the web version of the software weren’t available on mobile. “While the mobile app provides core functionality, it lacks advanced features only available on the web platform.” - Bon V.
Fiix
Key features
- Integrations: Reviewers noted the native connectivity with SAP, Microsoft, and Power BI.
- Reporting and compliance tools: Users regularly mention Fiix’s dashboards, audit trails, and KPI tracking as differentiators.
- Modular for scaling: Teams appreciate how Fiix scales across sites, with advanced asset structuring and role-based access.
What to watch out for
- Long onboarding: Complex setups or custom workflows can take longer to create and learn. “The part that I have never liked is the inventory module. To me, it seems clunky and should be simpler to use and implement.” - Cris R., Maintenance & IT Supervisor
- Support quality varies: Users on lower tiers occasionally mention longer response times.
- Requires upfront planning: Users report slow implementation and adoption without clear data and workflow goals. “Not the best for planning and scheduling work orders. Unable to do retroactive corrections. Unable to sort Work orders based on multiple criteria.” - Rey G., Facilities Operations Coordinator
- Lacks advanced workflow options: Some customers were disappointed by their inability to create more complex workflows and execute them in the mobile app. “There is no option for advanced creation of scheduled maintenance work orders. The app does not meet expectations. - Guilherme C., Materials Planning and Control Analyst
UpKeep
Key features
- Mobile-first functionality: Technicians use the mobile app for simplifying work orders, asset tracking, and photo uploads in the field.
- Quick onboarding: Reviewers say setup and adoption are fast, with teams completing maintenance tasks in the software up within days.
- Solid integration options: Users say that integrations with ERPs and IoT platforms are easy and helpful.
What to watch out for
- Reporting limitations: Users say advanced reporting is difficult to set up and often inaccurate. “Building reports could be more intuitive. Stability issues can be annoying. Slow loading, or not loading pages at all, occurs more frequently than one would expect.” - Brad B.
- Customization complexity: Configuring custom fields and workflows can take time without support. “Notification settings haven't worked consistently. Custom statuses aren't automatically selected on page views. There's often glitches on things like saving a quick filter.” - Tobin S., Industrial Automation Engineer
- Variable support experience: While many praise support, others mention slow response times. “I have been a little surprised at the number of bugs that I have found. The purchase order functionality could use lots of improvement. Cycle counts as well.” - Doug L., Process Safety / Automation Manager
eMaint
Key features
- Flexible and scalable: Reviewers noted its ability to grow with the organization.
- Reporting capabilities: Many users rely on its built-in reports and dashboards for KPIs and compliance.
- Multi-site friendly: Teams managing multiple plants like its structured hierarchy and asset segmentation.
What to watch out for
- Interface feels dated: Customers mention that the UX isn’t as modern or intuitive as newer platforms. “Searching for assets can be a bit of a hassle. Our parts area of Emaint took almost a year to get fixed after issues occurred during implementation.” - Verified G2 Reviewer
- Steep learning curve: New users often require more training to fully leverage the system. “It has been a steep learning curve for someone who is not familiar with databases and SQL server language.” - Melissa R., Maintenance Technician
- Pricing scales quickly: Teams say the price for the software jumped quickly in higher tiers.
Brightly (Asset Essentials)
Key features
- Customer support: Users cite Brightly’s hands-on implementation and training as a major benefit.
- Facility-focused features: Reviewers love its asset hierarchy, preventive maintenance scheduling, and reporting capabilities.
- Public sector alignment: Schools, governments, and healthcare facilities highlight its fit for their needs.
What to watch out for
- Not very flexible: Users say the system lacks deep customization for unique workflows. “Way too vast. Too many things that can be customized. Not intuitive. Too many layers to get to simple things.” - Verified G2 Reviewer
- UI can feel outdated: A few reviewers describe the interface as clunky or dated. “We have had a difficult time communicating the value of this program to our mechanics. The user interface makes it somewhat daunting to learn.” - Verified G2 Reviewer
- Reporting can be complex: Users find dashboards hard to configure without training. “The view is cluttered. The reports are not easy to use and are not customizable enough.” - Verified G2 Reviewer
Fracttal
Key features
- Mobile interface: Technicians found the app easy to use for on-the-floor updates.
- Maintenance KPI tracking: Users saw improved visibility into maintenance spend and KPIs.
- User interface: The intuitive design was highlighted as a plus.
What to watch out for
- Limited integrations: Some reviews indicated challenges connecting with other systems. “If for some reason we lose signal, the program becomes completely out of service, unable to manage.” - Matias C.
- Customer support: A few users experienced delays in support response times. “Managing it depends a lot on the training provided. Without it, understanding it becomes very difficult.” - Jaime G.
- Reporting depth: While easy to use, reporting was sometimes seen as less flexible. “Charts and visualizations are formatted with pre-made templates that do not provide business intelligence, only basic statistics.” - Marcelo M.
IFS Ultimo
Key features
- EAM functionality: Users noted the breadth of features across maintenance, and safety, and asset management.
- Modular design: Many appreciated the flexibility to scale asset management features based on business needs.
- Enterprise capabilities: Reviews highlighted the handling of complex organizational structures and teams.
What to watch out for
- Complex setup: Initial implementation may require IT involvement and planning. “User-friendliness can be improved and the software is complex to implement and set up.” - Joel, Director
- Outdated design: Users say the UI lacks modern polish compared to newer systems. “It’s not always flexible, and there’s a need for a mobile solution that’s much better than the current app.” - Erich, Business IT Manager
- Training required: Full feature adoption often requires formal training. “Every time an update is done it takes a few days for a consultant to get the system to work without errors.” - Erik, Maintenance Manager
Maximo
Key features
- Configurable: Reviewers cited its flexibility and broad asset management feature set.
- Industry-specific modules: Tailored solutions for sectors like utilities and transportation.
- Scalability: Handles global, multi-site environments well.
What to watch out for
- Steep learning curve: Many noted that Maximo requires extensive training. “Maximo is not user friendly. Most of the screens have fields which are all not used. It requires many training sessions to start using Maximo.” - Priya M., QA Lead
- Cost: As a premium maintenance management system, it’s on the higher end of the pricing scale.
- Slow updates: Some users felt innovation lagged compared to newer asset management platforms. “There is a major learning curve - it's clearly designed by people who aren't experienced in the roles it's designed for.” - Verified G2 Reviewer
Evaluation Checklist: How to Find a CMMS Software that Fits your Team
Choosing the right CMMS can be a high-stakes decision that impacts your team for years. This section will help you dial down that pressure and evaluate CMMS software with confidence. Use it as a guide to avoid common pitfalls, build internal alignment, and pick the maintenance management solution that’s right for you.
Key takeaways from this section
- Use structured evaluation criteria, like feature fit, reporting capabilities, and integration ease, to simplify your vendor comparison process.
- Form a cross-functional evaluation team to identify key needs, test maintenance management platforms, and build buy-in across departments.
- Prioritize maintenance management solutions that solve real-world problems for your team, not just those with long feature lists.
CMMS Evaluation Criteria: What You Should Look for in a CMMS Vendor
Use these criteria to compare maintenance management vendors on areas that matter most to you and your team:
How to Structure Your Evaluation Process for CMMS Software
Step 1: Build an evaluation team
Pick a group of people that can help you:
- Outline challenges, goals, and use cases for CMMS software
- Create and prioritize a list of must-have capabilities
- Create a plan, budget, and timeline for adoption
- Establish champions and help you get buy-in
- Test, assess, and score maintenance management software
When building your evaluation think about including:
- Maintenance leads
- Technicians and other daily users of the software
- Operations and facilities management leaders
- IT, procurement, and finance
Step 2: Create an evaluation framework
Design a set of requirements to help you identify a maintenance management solution that fits your organization best and disqualifies vendors quickly.
To create your evaluation framework, list the following:
- Your biggest challenges and goals
- Your KPIs and targets
- The workflows and processes to address
- Who will use the software
- The most important features and functionality for your team
- Your budget
- Expectations for implementation and vendor support
Step 3: Create a shortlist of CMMS software
Use this comparison guide to identify 3-5 vendors that meet your needs and budget. Include your evaluation team in this process so they can give feedback, raise concerns, and test software.
Step 4: Evaluate your shortlist vendors
Here’s are 10 must-ask questions for CMMS vendors as you assess software:
- How will the software help me solve my challenges, reach my primary goals, and hit KPIs?
- How long does implementation typically take for a team like ours?
- Can you walk me through a real-life technician workflow on a mobile device?
- What does standard reporting look like?
- How does your system manage users and data across multiple sites?
- What can I customize without needing IT support?
- What kind of onboarding and support do we get?
- Which other enterprise systems do you integrate with? How long does this take? How much work does it require from my team?
- How much does it cost? What’s the pricing structure? What is the typical time to value?
- Are we able to test or pilot the software to make sure it works for our team?
CMMS Software Evaluation Checklist
The final word: The best CMMS is the one that’s right for your team
There are dozens of factors that make your team different from any other, from industry and size to its level of digital maturity. At the end of the day, the best maintenance software is the one your team will actually use to execute its maintenance strategies while solving the biggest challenges of the job.
This is why it’s so important to make your CMMS evaluation a team effort. Include multiple stakeholders. Consider a wide range of criteria. Have different roles test the software. When combined with other factors, like price and integrations, team fit can guide you to the perfect CMMS software. Hopefully, this guide has helped you create a shortlist you can take to your team and propel your search for maintenance software forward.
Frequently Asked Questions
How do I choose the right CMMS (computerized maintenance management system) for my organization?
Here are three steps to guide your CMMS software evaluation:
- Create an evaluation team to establish goals, budget, use cases, must-haves, and timelines. For example, you may need a CMMS with robust features for scheduling recurring maintenance tasks and mobile accessibility, but you don't care as much about tracking asset lifespan or inventory management tools.
- Do your research. Chat with peers. Look at websites. Talk to vendors. Collect as much information as possible to create a shortlist that matches your criteria.
- Demo 3-5 CMMS platforms. Try different options with your team to understand which one fits your workflows, maintenance strategies, and team abilities best.
How long does it take to implement CMMS software?
Most CMMS implementations take 30 to 90 days. Small teams with simple preventive maintenance setups can be up and running in 2-3 weeks. Large or multi-site teams with complex requirements may take longer due to data migration, user training, and system integrations.
How much does CMMS software cost? How do I calculate the total cost of ownership for CMMS software?
The cost of cloud-based CMMS software varies widely depending on several factors, including the size of your team and the complexity of your operation. Free versions of maintenance software are common, although the feature set is limited.
Subscription fees are a primary part of the total cost of ownership (TCO) for a CMMS, but other factors include:
- Implementation and training costs
- Integrations
- Time spent managing the system.
To calculate TCO, factor in license fees, onboarding, IT resources, and long-term support.
What’s the difference between CMMS software and EAM (Enterprise Asset Management) software?
CMMS software typically focuses on managing day-to-day maintenance tasks, like preventive maintenance work orders, asset tracking, and parts. EAM software adds broader asset management tools like financial tracking, lifecycle costing, inventory management, and capital planning. If you manage maintenance only, a CMMS software solution works well. If you're responsible for enterprise-wide asset strategy, consider an EAM.
Can CMMS software integrate with other systems like ERP or IoT sensors?
Yes, most modern CMMS and asset management platforms offer APIs or pre-built connectors for ERP systems and IoT sensors. Integrations let you sync real-time equipment data, preventive maintenance schedules, inventory levels, asset performance, and purchase orders. This enables you to improve data accuracy and automate preventive maintenance scheduling while allowing you to adopt advanced maintenance strategies, like predictive maintenance. It also helps you optimize your enterprise systems and the rest of your existing tech stack.
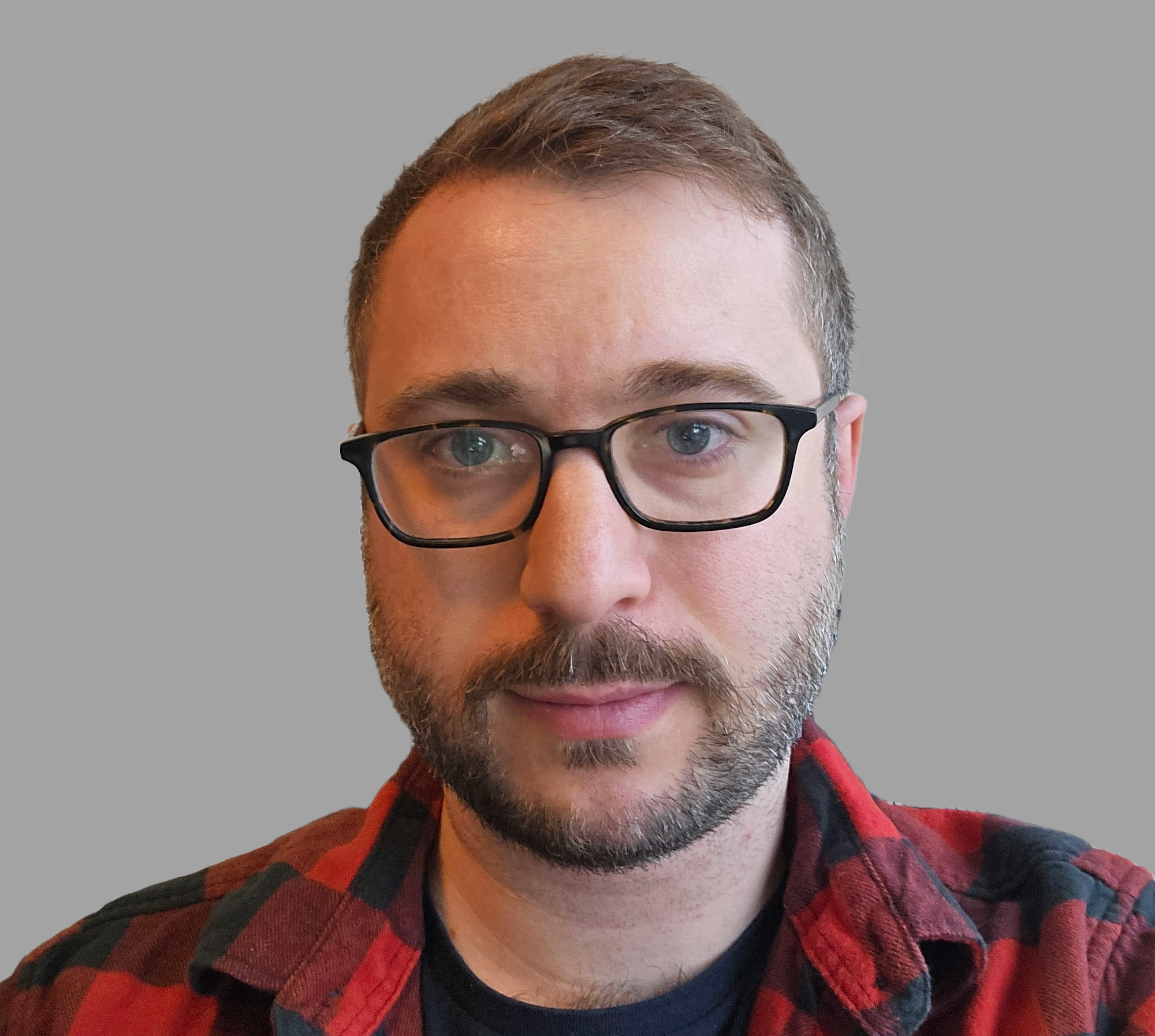
Marc Cousineau is the Senior Content Marketing Manager at MaintainX. Marc has over a decade of experience telling stories for technology brands, including more than five years writing about the maintenance and asset management industry.