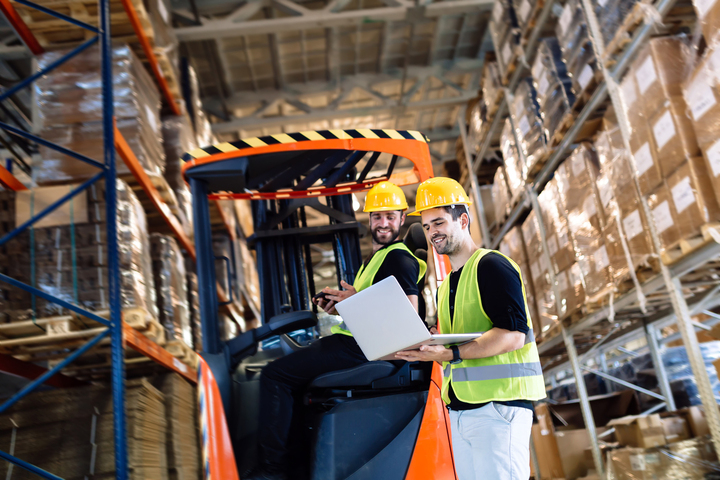
Creating Effective Maintenance Workflow Automation
Creating effective maintenance workflow automation takes time. But the most important part is to launch a successful preventive maintenance program, which includes building asset inventories, conducting criticality analysis, and determining key performance indicators (KPIs) to measure success.
A preventive maintenance schedule is a plan for organizing company resources to ensure maintenance tasks are performed according to specific time or usage triggers. The primary goal of preventive maintenance is to keep assets in optimal working condition.
Creating a preventive maintenance schedule involves coordinating materials, equipment, and timeframes for completing tasks. It also entails determining who should perform which tasks and how they should do them. Dedicated maintenance schedulers, maintenance supervisors, and maintenance planners are the team members most often responsible for developing PM schedules.
Don’t confuse maintenance scheduling with maintenance planning. Though the two processes support one another, they are not always completed by the same individual. Maintenance planning focuses on what needs to be done and how. Maintenance scheduling, on the other hand, details who will perform recommended maintenance tasks and when.
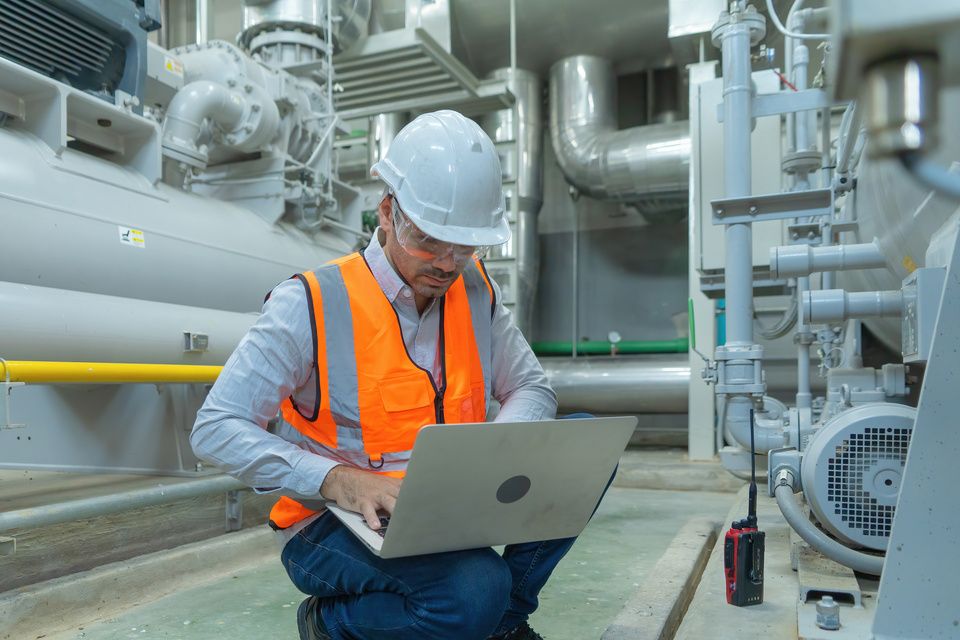
Fixed vs. Floating Preventive Maintenance Workflows
Effective preventive maintenance schedules help facility managers efficiently allocate maintenance resources, effectively maintain assets, and appropriately plan for the year ahead. When making a preventive maintenance schedule, you have two primary options: fixed and floating PM scheduling.
1. Fixed PM Workflows
A fixed preventive maintenance schedule is a routine maintenance plan scheduled according to specific equipment usage or time interval. Fixed PM schedules focus on future planned tasks, regardless of whether previous tasks were completed or not.
For instance, tasks scheduled on Mondays are always performed on Mondays regardless of whether your technician completed last week’s assigned task. Maintenance schedulers also can base recurring PMs on specific usage intervals or triggers.
EX: You schedule your fleet’s vehicles to undergo maintenance every 3,000 miles. Once an odometer reaches 3,000, you create a work order for a routine oil change and performance check. The vehicle’s next oil change will happen in another 3,000 miles. It does not matter how long it takes your driver to reach the mileage. This is a fixed PM schedule based on usage intervals.
2. Floating PM Workflows
A floating preventive maintenance schedule is a maintenance plan based on the timing of previous PM tasks. Floating PM schedules are informed by an asset’s past usage or maintenance history.
For instance, assume you have a 30-day PM schedule for a machine. You will assign the asset’s next PM 30 days from the completion of the last PM activity. In other words, the subsequent work order is not triggered until the previous work order is completed and closed. Floating PM schedules require greater diligence than fixed PM schedules for tracking maintenance task completion.
EX: You schedule an HVAC system for maintenance every 100 hours of operation. You delay maintenance until after the 120th hour. Therefore, your next work order is triggered after 220 hours from the original PM. The system starts counting the 100 hours after the previous work order is closed (at the 120th hour). If the HVAC system were on a fixed schedule, it would still be triggered for maintenance after 200 hours.
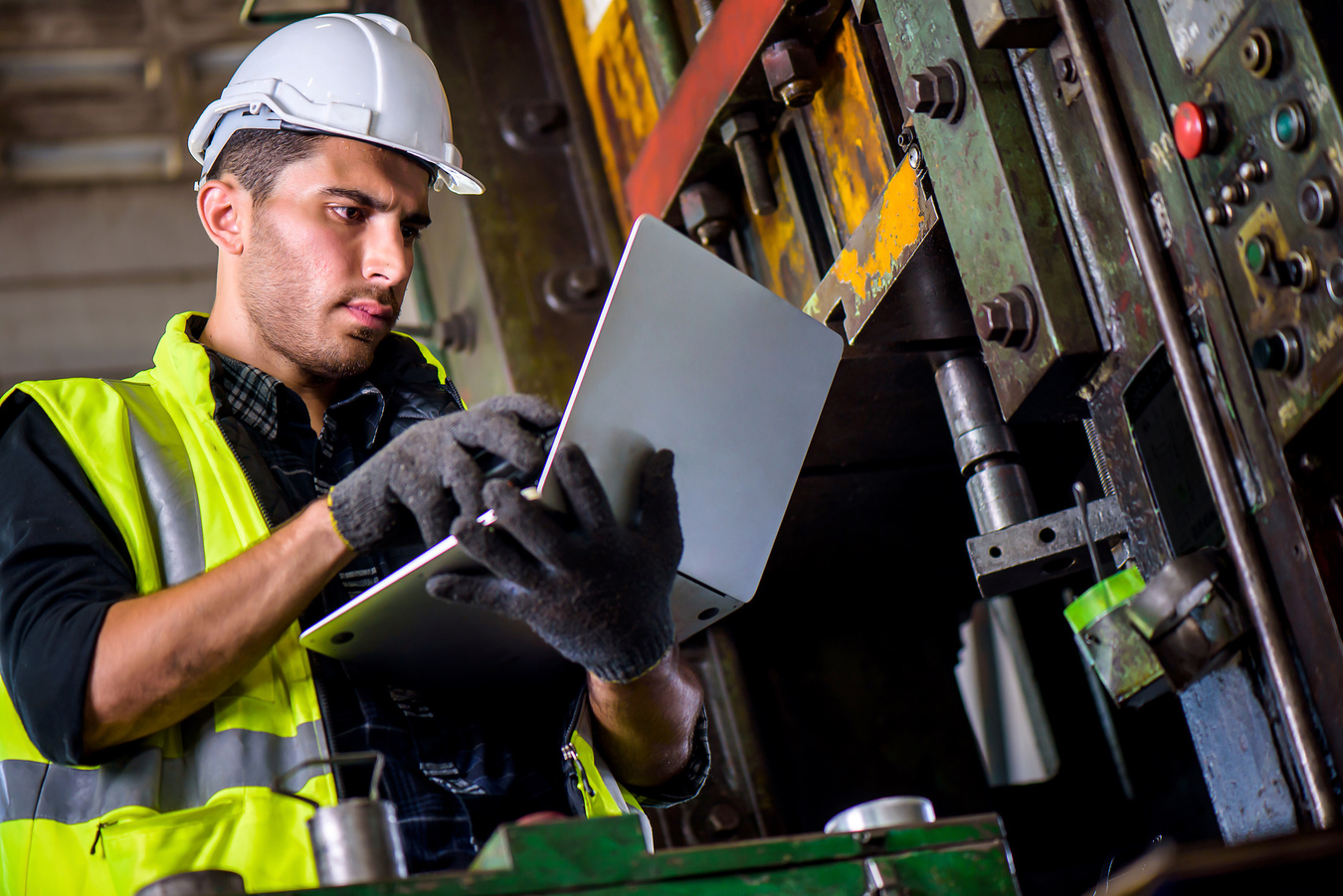
Implementing Maintenance Workflow Automation
The key to creating a successful preventive maintenance schedule is identifying the correct maintenance interval for each asset. This allows you to maximize resources while reducing the chance of unexpected breakdowns.
Tips for Successful Preventive Maintenance Workflows
Preventive maintenance scheduling is not rocket science. However, several challenges can disrupt workflows, reduce schedule compliance, and create bottlenecks if not proactively navigated. Some common factors that disrupt PM schedules are:
- Poor team communication
- Inefficient maintenance inventory management
- Misunderstandings with third-party contractors
- Miscommunication with suppliers
- Lack of in-house skill sets for specialized tasks
Taking the time to develop centralized communication systems, employee continuing education programs, and clear standard operating procedures (SOPs) will set your team up for success.
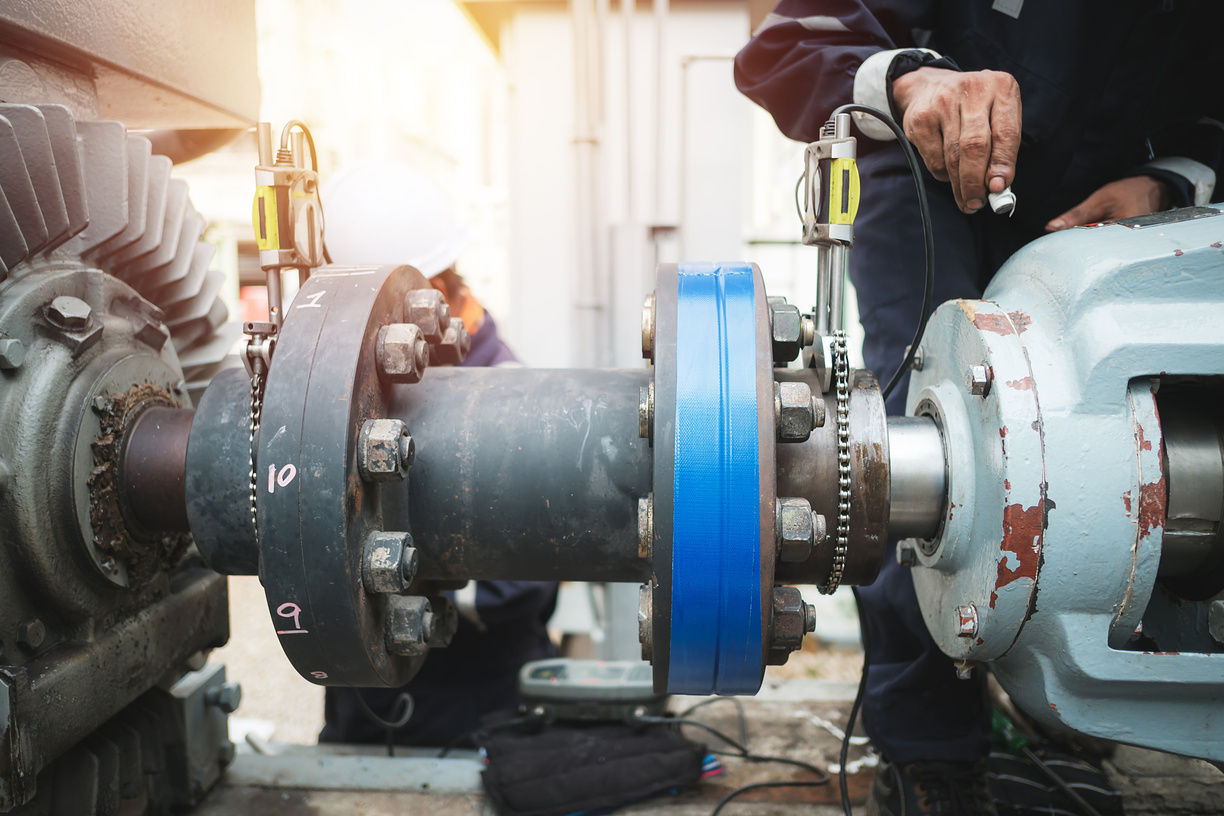
Creating a Preventive Maintenance Program
Effectively planned preventive maintenance (PM) programs deliver substantial savings. For example, studies show preventive maintenance can save facilities as much as 18 percent in maintenance costs.
Scheduling routine maintenance based on usage or time triggers reduces the likelihood of unplanned equipment failures that translate to emergency maintenance expenses.
The expenses of workers’ overtime, outsourced expertise, and expedited parts shipments can add up quickly. However, the most significant financial loss for industrial businesses stems from missing production targets due to downtime.
The key to cutting costs, increasing reliability, and extending equipment life spans is executing a consistent preventive maintenance (PM) program—on the right assets.
Manufacturers that primarily rely on reactive maintenance lose between $10,000 and $250,000 for every hour of downtime. While downtime affects no two businesses exactly alike, the outcome is always the same: lost company resources that you could have better used elsewhere.
While performing scheduled maintenance itself is not complicated, launching a program from scratch can be challenging. Often, maintenance managers know what to do; they just are not sure how to get started and in what order to do things. Follow the steps below for successful maintenance workflow automation.
1. Establish Clear Goals
The three most common obstacles organizations face when initiating preventive maintenance (PM) programs are:
- Lack of available workforce, finances, and time
- Inefficient preventive maintenance management systems
- Uncertainty about which assets should receive PM first
The good news is you do not have to perform scheduled maintenance on every asset. Pieces of equipment critical to production, quality, safety, and service delivery are prime candidates for preventive maintenance programs. Leave everything else for reactive maintenance, as usual.
Furthermore, you do not need a huge budget to develop an organized system that supports consistent results. For these reasons, start the process by outlining clear program goals. Examples of potential program goals include reduced equipment downtime, improved work completion rates, maximized production time, and increased asset reliability.
Ask your organization’s machine operators, maintenance technicians, and other key stakeholders for their input early in the process. Their feedback will be integral to establishing priorities, making future hires, outlining standard operating procedures (SOPs), and setting your preventive maintenance program up for success.
2. Inventory Your Assets
Once you have everyone on board, take an inventory of the assets you want to include in your preventive maintenance program. Tracking asset history regularly will play a crucial role in your PM strategy.
Monitoring asset data will ensure your team does not perform too much preventive maintenance on one asset at the expense of others. As you fine-tune your program, it will also reveal maintenance spending patterns, worker inefficiencies, and optimal timeframes for asset replacements.
Beyond the importance of maintaining detailed asset inventories for accounting records, consistent record keeping can reveal opportunities to optimize spending patterns.
As routine maintenance is performed, keep track of service dates, labor costs, parts used, and current conditions. Also, note the asset’s criticality to production and safety.
Record the following data for each asset:
- Make/Model
- Serial number
- Unit number/brass tag number
- Category (e.g., plumbing or HVAC)
- Location
- Specifications
- Department or team responsible for upkeep
- High-cost parts associated with the asset
Also, consider the asset’s current condition and its priority level in relation to productivity and workplace safety. You can use a spreadsheet or a computerized maintenance management system (CMMS) to catalog your asset entries. We recommend adopting a user-friendly platform like MaintainX to maintain asset records, cross-reference data, and glean cost-saving insights over time.
Create an inventory of your organization’s most crucial assets. This equipment should receive preventive maintenance first. This exercise will help you avoid delaying maintenance on certain assets, especially if using a floating PM schedule.
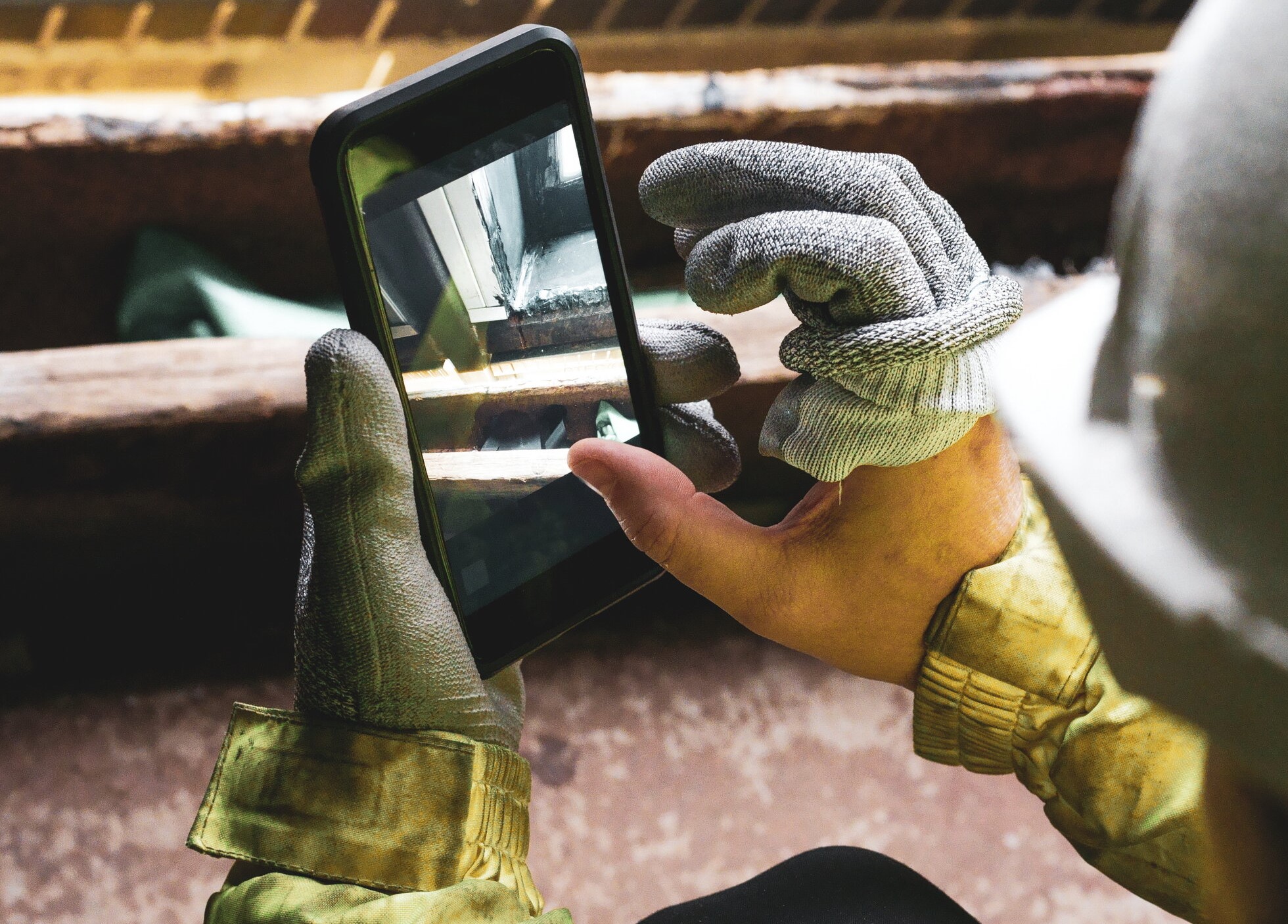
3. Conduct Asset Hierarchy and Criticality Analysis
It is impossible to place all essential assets on initial PM programs. Stay realistic by creating an asset hierarchy for your organization’s most critical assets.
Remember, most of your facility’s assets do not need to be scheduled for preventive maintenance. Therefore, exclusively performing PM on extensive asset inventories is unrealistic for most organizations. Additionally, performing PM on inexpensive, non-critical, and easily repaired items is wasteful. One way to determine PM priorities is to conduct a criticality analysis.
Criticality analysis is an exercise that involves ranking assets according to their risk potential in several categories, including operational, financial, environmental, and safety. This process is beneficial to organizations with several complex assets because it removes personal bias from the equation.
Criticality analyses allow managers to rank, prioritize, and schedule PMs with objectivity. Assets with higher criticality ratings receive top priority. Use the following questions as a launchpad when evaluating asset criticality:
- Which assets are critical to production and safety?
- Which assets require regular maintenance?
- Which assets have high repair and replacement costs?
When making your preventive maintenance schedule, prioritize assets critical to production, require regular maintenance, or have high repair and replacement costs. Remember: it is more cost effective to place non-critical and older assets on reactive maintenance programs because you may need to replace them sooner.
However, if you run or work at an SMB that just needs help with basic maintenance prioritization, follow the steps below to gauge PM priority levels:
List Top Assets
Write down your most important assets. To avoid overwhelm, do not include more than 20 percent of all pieces of equipment. Prioritize assets that significantly impact production, have high maintenance costs, require regular maintenance, or pose safety hazards. As you begin to realize the return on investment (ROI) of your assets, gradually add more assets to the PM program.
Rank Criticality by Financial Impact
Use this formula to determine the financial impact of each asset:
Equipment Criticality = Failure Frequency (per year) x Cost Consequence ($) = Risk ($ per year)
Here, the cost consequence includes the cost of lost production plus repair costs.
Rank Criticality by Safety, Environment, and Health Impact
Consult with your team to determine which equipment breakdowns pose the greatest threat to worker and customer safety. Rank those items from highest safety risk to lowest safety risk.
Assess Likelihood of Failure
Individual assets may pose several unique failure events, each with entirely different associated risks. For this reason, reliability consultants recommend only choosing the failure event that poses the greatest likelihood of occurring for each asset. Therefore, rank your assets from greatest to least likelihood of failure.
Combine Findings
If you use a points system, add your individual RPN categories to generate a total RPN for each asset. Then, divide the total RPN by the total weighted points possible and multiply this number by 100. Finally, analyze your findings to determine the assets most essential to your organization’s goals.
Again, if you work at or run a small organization just getting started, do not feel pressured to conduct an official criticality analysis.
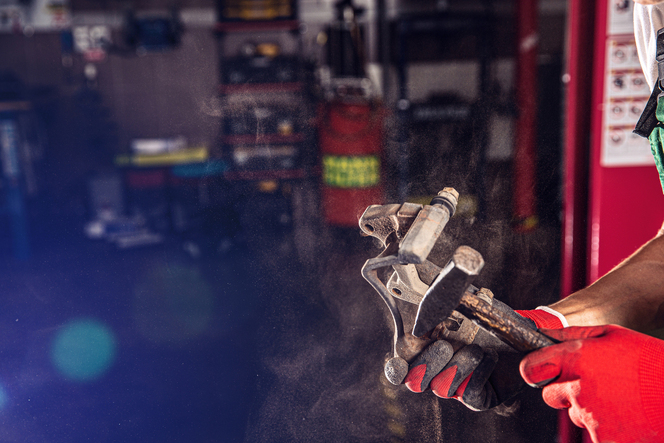
4. Identify Ideal PM Intervals
Of course, preventive maintenance is not without a potential downside. Without proper planning, you risk wasting precious resources on unnecessary inspections and repairs. Over-maintaining assets can be just as wasteful as under-maintaining them! Avoid overdoing it by identifying ideal PM ratios for your individual assets.
The three primary methods to determine PM intervals include:
- Consulting equipment manufacturer’s manuals for recommended maintenance work instructions, manual processes, schedules, and usage of critical spare parts
- Reviewing historical maintenance data for insights into past failure patterns
- Asking machine operators and technicians for their insights into asset behaviors
5. Schedule Your Preventive Maintenance Workflow
At this stage, you are finally ready to schedule your preventive maintenance activities. This is one of the key steps for successful preventive maintenance workflow automation. Word to the wise: do not try to tackle everything at once. Instead, we recommend creating a long-term (yearly) maintenance schedule before breaking high-priority tasks down into a short-term schedule (quarterly, monthly, weekly, and daily).
A PM schedule lays out when to perform maintenance activities on any given piece of equipment. When developing your PM schedule, select a day and time for maintenance that does not disrupt production. Base PM schedules on one of two metrics:
- Time: You can base your PM schedule on time and perform maintenance after a set period. For example, your fleet of vehicles can undergo maintenance every three months.
- Usage: For usage-based PM schedules, track usage metrics such as operating hours and production cycles. Maintenance activities are then performed when certain milestones are met. For example, schedule your fleet of vehicles for maintenance every 1,000 miles instead of every three months.
PM schedules usually depend on a work order management system. A work order is a document that provides details about a maintenance task and outlines the process to complete the task. A work order specifies the scope of the work, the expected timeline to complete the work, who authorized the work order, and an assigned maintenance technician. Work orders help you organize, assign, prioritize, track, and complete maintenance tasks besides capturing asset maintenance history.
A user-friendly Computerized Maintenance Management System (CMMS) like MaintainX will make assigning, overseeing, and adjusting your PM program infinitely easier. In fact, maintenance workflow automation is nearly impossible without a CMMS. MaintainX’s desktop and mobile CMMS allows operational managers to:
- Create, assign, and monitor recurring work orders
- Track historical asset data in the cloud
- Communicate with team members via work order commenting, direct messaging, and group messaging
- Manage inventory supplies with automated alerts
- Glean cost-savings opportunities from advanced reporting capabilities
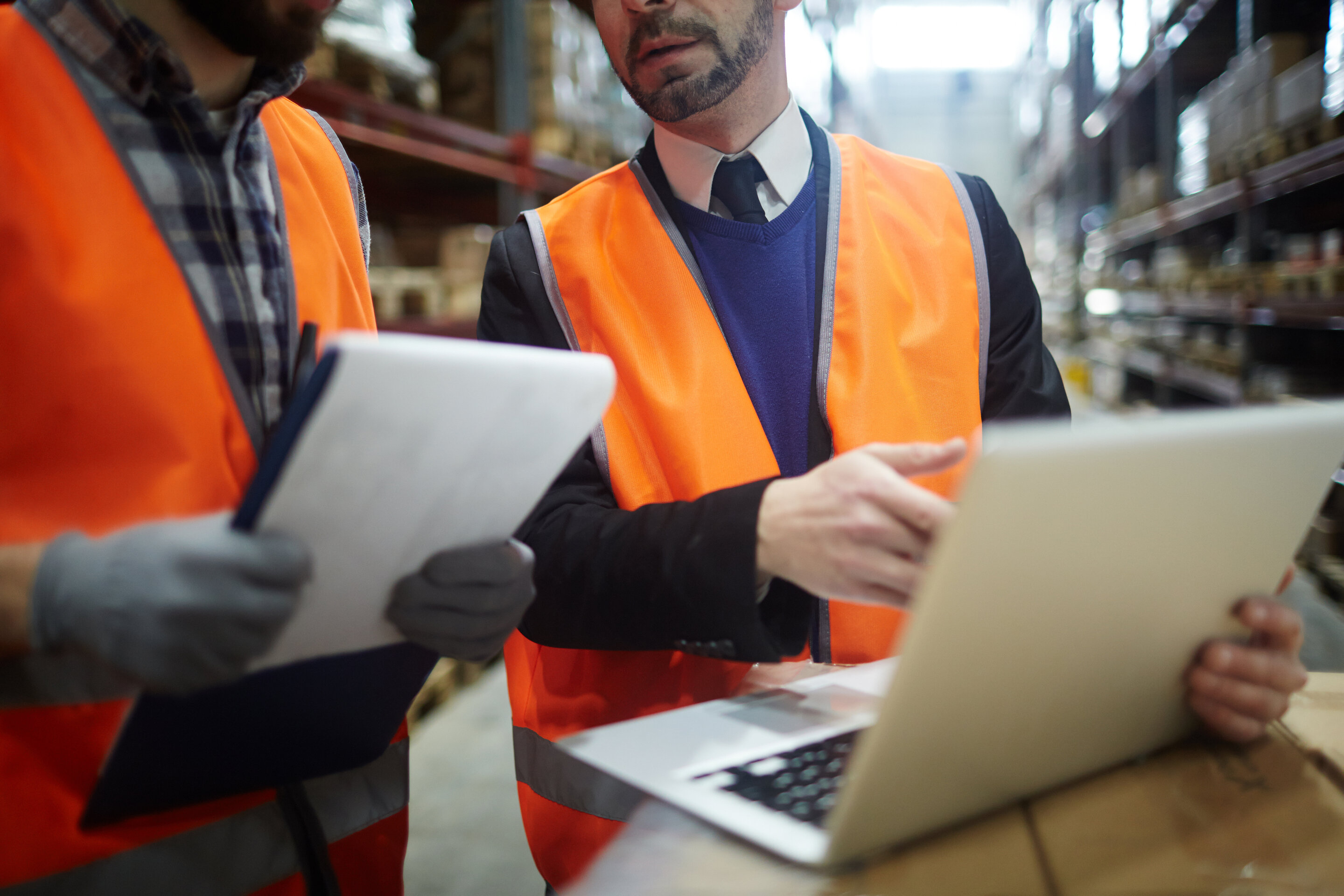
6. Train Your Team
Operator error accounts for up to 12 percent of unplanned downtimes. No matter how carefully you plan your preventive maintenance program, it may fail if you do not spend time onboarding the workers responsible for maintaining your assets.
Organize training sessions for employees who work with the assets to be maintained. Also, be sure to write work instructions in simple, easy-to-understand language. You also should provide employees with additional learning resources for reference. Finally, ensure they understand when and how to perform scheduled maintenance.
Clear and fast communication is essential for an effective PM program. Your team should always be able to communicate with each other efficiently and effectively. Poor communication can lead to:
- Delayed maintenance timelines
- Overlapping work orders and activities
- Inappropriate prioritization of maintenance tasks
- Under- or over-maintenance
- Poor maintenance inventory management
- Prolonged downtimes
Approximately 96 percent of office executives claim poor communication is to blame for workplace failures. Maintenance departments are no exception to everyday communication woes.
According to McKinsey Global Institute, a connected workforce is more likely to post better performance. Using a mobile CMMS with team chat will virtually eliminate important project details falling through the cracks. MaintainX reduces time spent clarifying details, improves access to maintenance records, and speeds up troubleshooting between technicians and managers.
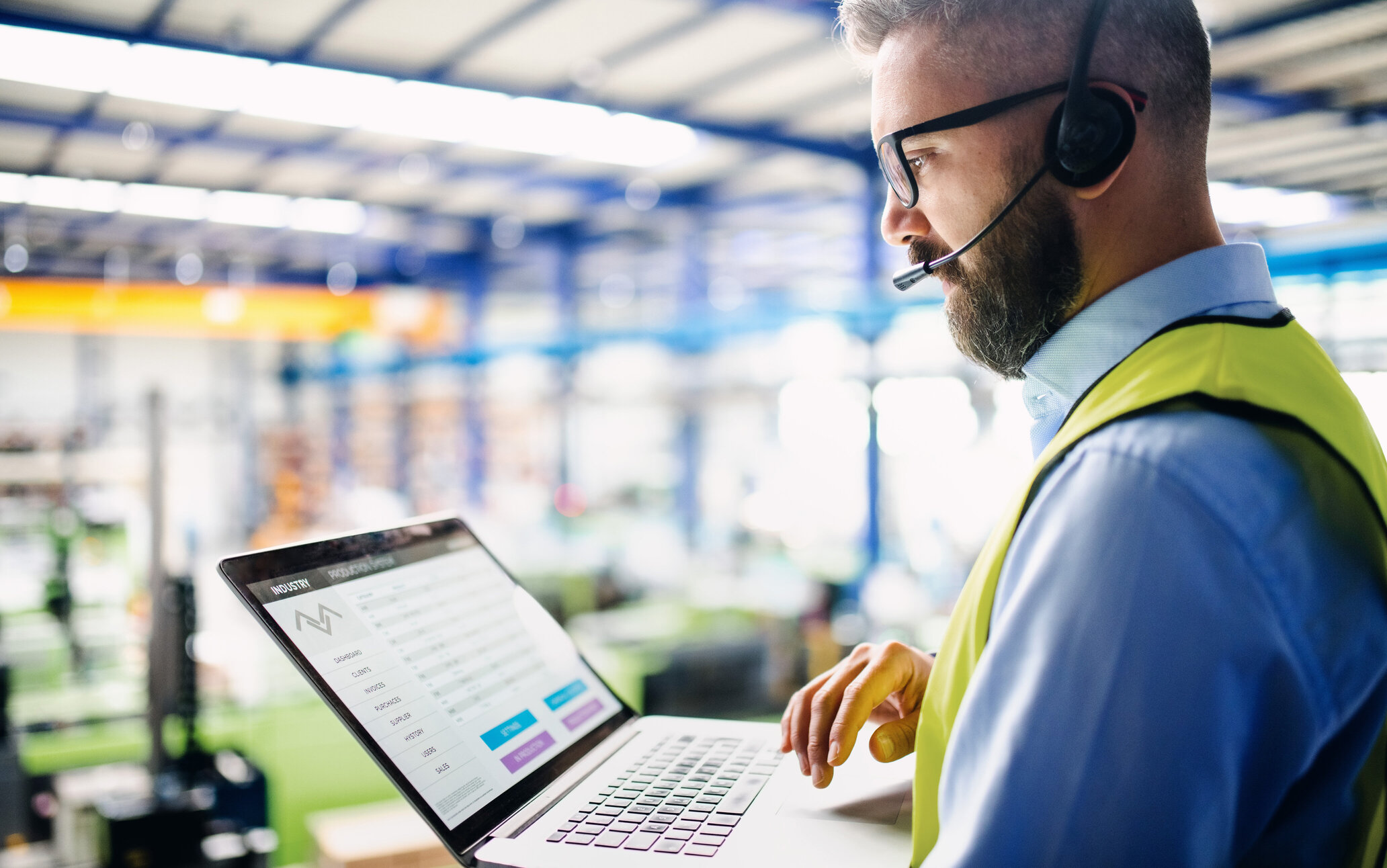
7. Monitor Preventive Maintenance Workflow Success with KPIs
Set SMART goals and key performance indicators (KPIs) to measure progress. SMART is an acronym for Specific, Measurable, Achievable, Relevant, and Time-Bound.
Your maintenance goals should clearly outline what you want to accomplish, by what date, and the metrics you will use to measure success. In addition, your goals should be relevant to your company’s broader business goals.
Common KPIs to measure preventive maintenance plan effectiveness and maintenance workflow automation include:
- Planned Maintenance Percentage (PMP) reports the time spent on planned maintenance compared to unplanned maintenance within a given period
- Preventive Maintenance Compliance (PMC) reports the number of scheduled PM tasks completed within a specific timeframe
- Scheduled Maintenance Critical Percentage (SMCP) determines the impact of delayed planned maintenance activities
- Mean Time To Repair (MTTR) reports the average time it takes to repair and restore an asset to full functionality
- Overall Equipment Effectiveness (OEE) calculates asset efficiency during production by combining asset availability, performance, and production quality
Monitor your chosen key performance indicators (KPIs), ask for team member feedback, and make minor adjustments accordingly. Remember: you will never eliminate all downtime.
Instead, focus on progress by determining how many PMs have been performed on critical assets and how often those assets have failed since the program began. You can determine whether you should reduce or increase your PM activities based on this data. If your team is not meeting its goals, conduct a root cause analysis to locate inefficiencies and correct course.
Establish KPIs that align with your maintenance program and maintenance workflow automation goals. These metrics will help determine whether your PM program is effective along the way. Consistently identifying your maintenance program’s strengths and weaknesses is the only way to experience steady progress and long-term success.
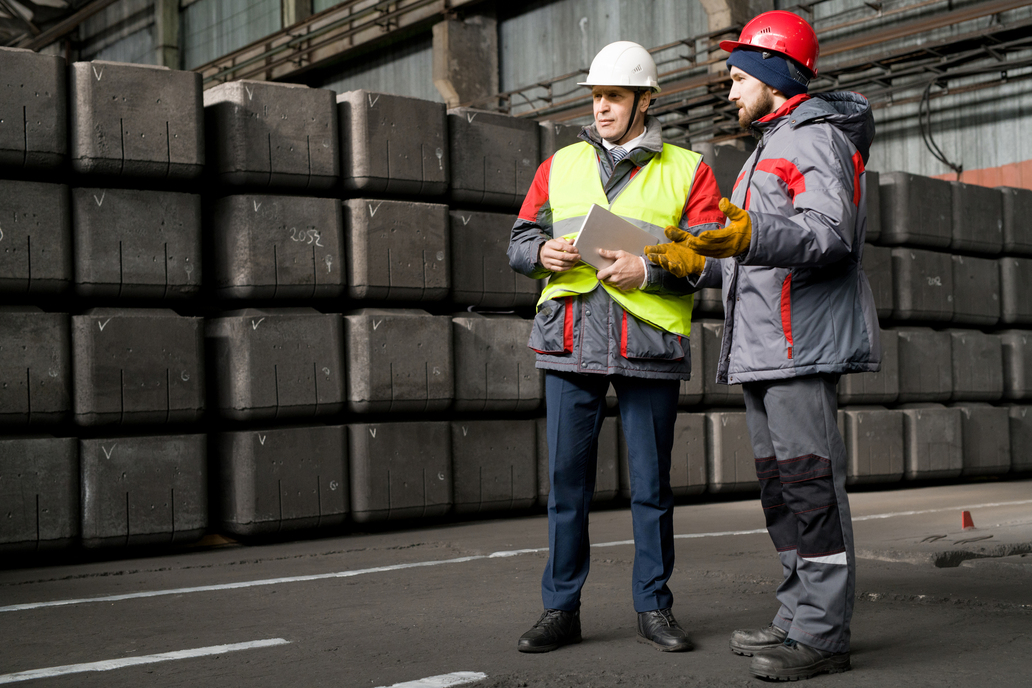
8. Get Upper-Management Support
Finally, you will need the support of your company’s management to implement a PM plan and maintenance workflow automation successfully. Convincing leadership to get on board, and increase O&M budgets, can be a daunting task. Tips to help you to make a case for implementing a PM plan include:
- Estimating Return on Investment (ROI): You need to convince the management how the PM program will improve the company’s bottom line. Select a few critical assets and demonstrate how shifting from corrective to preventive maintenance will reduce maintenance costs and improve profits. For example, say you experience three unplanned downtimes a year., and the cost of restoring full functionality each time is $500. APM program could reduce the downtimes from three to one and save $1000 in maintenance costs.
- Determining Maintenance Goals: Outline your long-term maintenance goals and how they align with the overall organizational goals. Remember to cover the challenges faced by the current (reactive) system and how a PM program would overcome them.
For an effective PM program and maintenance workflow automation, you first need to understand your facility’s maintenance goals and develop maintenance checklists that align with the goals.
9. Use CMMS Software for Maintenance Workflow Automation
Most effective PM programs and maintenance workflow automation have one thing in common: a Computerized Maintenance Management System (CMMS) the entire team feels comfortable using. Maintenance planners can create, implement, and track recurring work orders via workflow automation software and user-friendly dashboards.
Additionally, CMMS simplifies, automates, organizes, and optimizes Operations and Maintenance ( O&M). In fact, 58 percent of facilities management relies on CMMS to manage maintenance operations.
However, up to 80 percent of CMMS implementations fail. Reasons for CMMS failure include:
- Exclusion of users from the selection process
- Complex CMMS software
- Resistance to technology adoption
- Poor implementation of CMMS
Using modern, cloud-based CMMS can help overcome these implementation challenges. Unlike traditional on-premise systems, cloud CMMS is available over the Internet and, therefore, easier to set up, access from anywhere, and manage the database. Modern CMMS like MaintainX also offer regular updates and better database security.
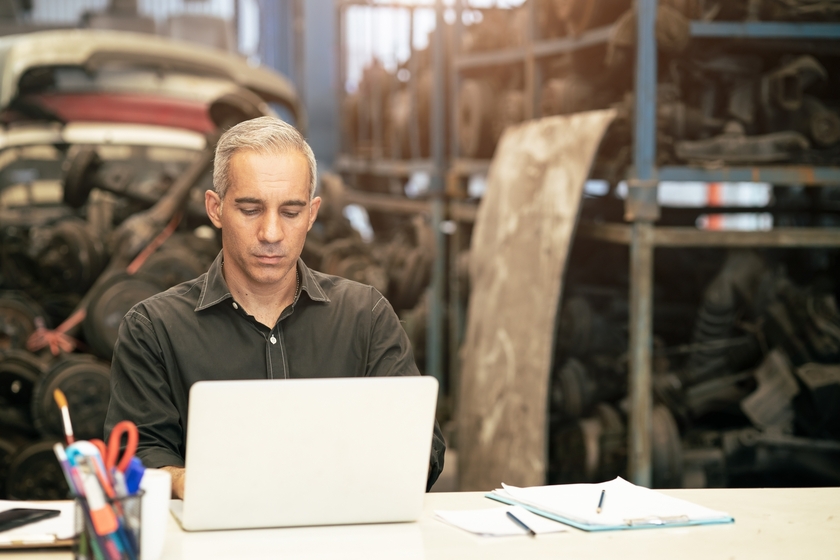
Writing Efficient Work Orders
A work order is a document that outlines instructions for a maintenance job. Generally, work orders include information about who should complete the task, the process involved, and when the task needs to be completed. Operational managers assign work orders to maintenance technicians in both paper and digital formats.
The primary purpose of a work order is to provide precise details of scheduled maintenance tasks. The documents also serve as official authorizations to service equipment. Maintenance technicians often initiate work requests after identifying parts’ problems during routine inspections. In addition, facility users, customers, and other stakeholders can create a work request after noticing a problem at a facility.
Upon receiving such a request, maintenance managers create a work order and assign it to an available technician.
Work Orders
Successful completion of maintenance tasks largely depends on how detailed work orders are. Incomplete information can result in costly errors. Therefore, a standard work order should contain the following pieces of maintenance and facility information:
- Location of asset needing work
- Description of asset
- Description of problem
- Scope of work to be completed
- List of needed tools and replacement parts
- List of safety procedures to be aware of on the job
- Details of person or department that requested it
- Date when it was created and submitted
- Projected date of completion
- Expected hours of work and actual number of hours used for completion
Work orders can also include checklists for completing the assigned tasks and urgency priority levels. Managers can also attach standard operating procedures (SOPs), asset maintenance histories, manuals, and images to help maintenance technicians complete them more efficiently. Some organizations include notes with observations, such as the frequency of the problem and techniques for troubleshooting the given piece of equipment. These notes help technicians complete work orders, and managers review them for verification after assignments.
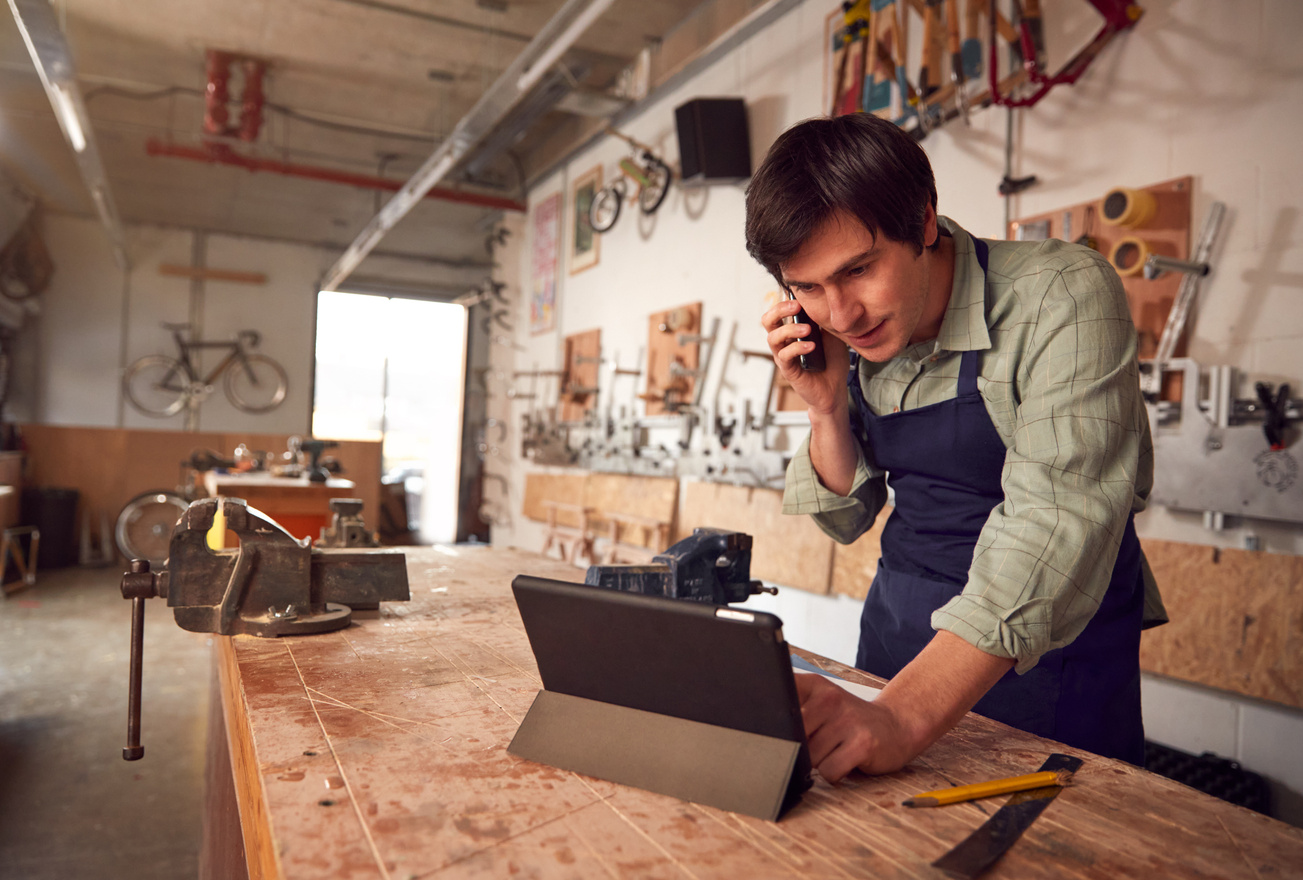
Work Orders Usually Go through a 4-Step Process
Step 1: Submitting Work Requests
Machine operators, equipment inspectors, or employees from other departments can submit work requests that managers turn into work orders. In residential organizations, tenants often submit work and maintenance requests. Work requests are often an essential aspect of customer relationship management (CRM).
Maintenance novices may confuse work requests with work orders. However, there is a distinct difference between the two terms. Work requests are simply a request for maintenance on a given asset. Technically speaking, management can approve or deny that request.
Alternatively, work orders are authorized assignments for maintenance to be completed. Work requests become work orders after their submission and approval. Either maintenance supervisors or maintenance planners approve work requests. Factors they consider before approving appeals include:
- Available maintenance budget
- Severity of the reported issue
- Safety impact of the reported issue
- Planned maintenance activities already in place
- Asset age
Step 2: Creating Work Orders
Maintenance supervisors usually review work requests and, if approved, create a work order. However, not all work requests receive the necessary approval. Managers can deny work requests if a reported problem has already been resolved or the task does not fall under their department. If resources necessary to complete the request are not available, the manager can schedule the task as a “deferred maintenance activity.”
Step 3: Assigning Work Orders to Technicians
Maintenance technicians receive digital or analog instructions on when and how to do the job. Organizations that use CMMS software automatically assign work orders to technicians. Depending on the priority level, technicians complete the job immediately or schedule it for later.
Step 4: Closing Work Orders
Maintenance technicians should close the work order as soon as they have performed the assigned tasks. Ask them to include the following details:
- Amount of time spent on task
- Replacement parts used
- Comments and images
- Completion notes, such as observations beyond assigned task
CMMS software automatically updates the maintenance log on the given asset after a work order is closed. Maintenance supervisors can then review the completed ones and decide on the next course of action.
Notably, work orders are either planned or unplanned. Emergency work orders are an example of unplanned work orders. As mentioned above, they can be initiated within an organization or externally by customers.
Work orders can help maintenance teams efficiently and effectively streamline their activities. Well-planned task assignments increase the efficiency of PM strategies and reduce the need for reactive maintenance. They enable maintenance personnel to define roles, track tasks, track time-consuming activities, document information, and make automated workflows smoother.
Furthermore, they are a great source of an asset’s maintenance history and provide valuable insights for making maintenance decisions. As a result, organizations that use modern CMMS solutions for their work orders have better productivity KPIs than those that still rely on paper records.
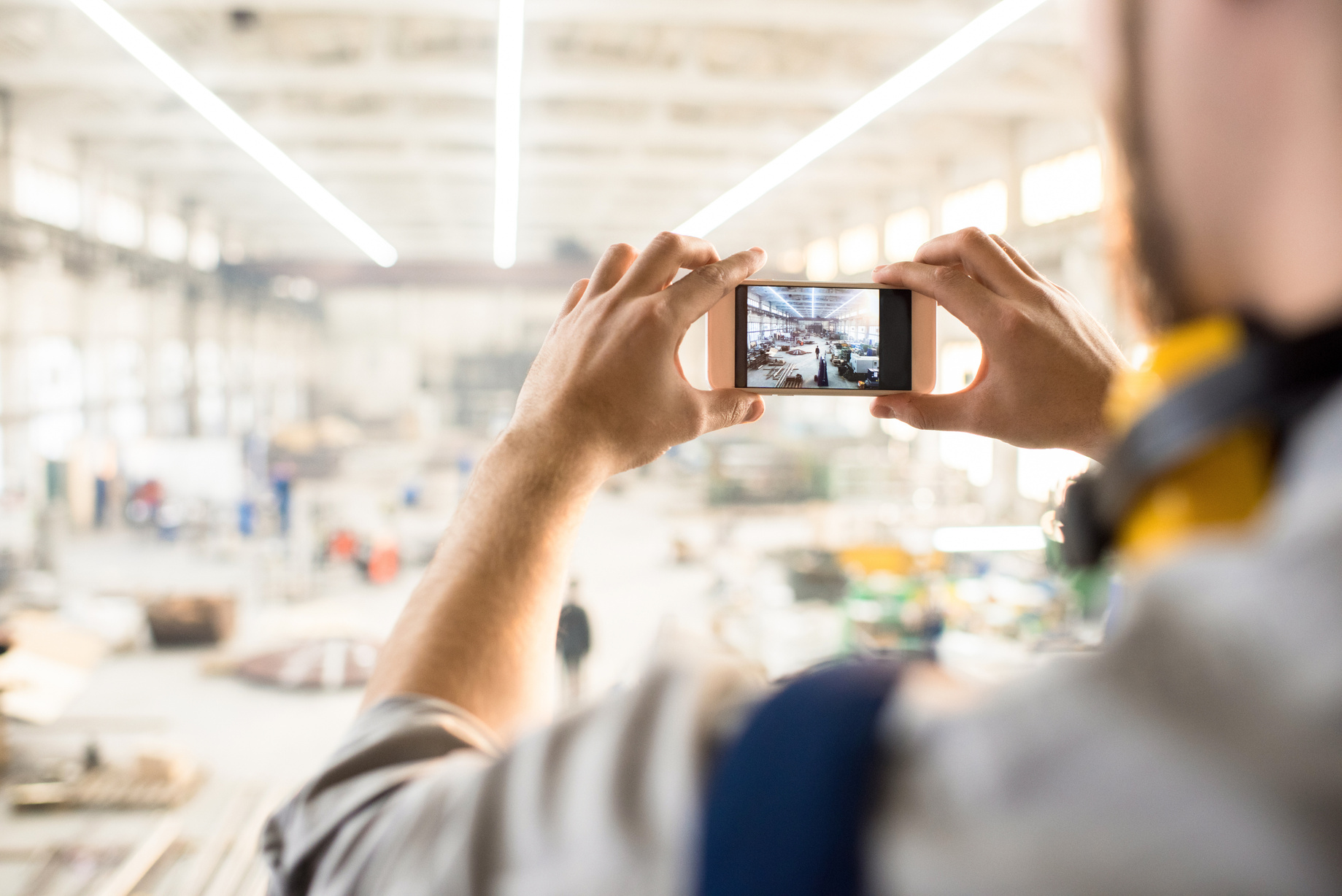
Run Your Maintenance Workflow through CMMS
There are many reasons to adopt computerized maintenance management programs. However, the primary motivating factor—for most companies—is to save money. CMMS features allow operational managers to track maintenance activities, implement maintenance processes, automate workflows, and make cost-effective decisions which are nearly impossible without digital organization.
Indirect maintenance costs add up through reduced asset life cycles, high-energy costs, lost production, late deliveries, inefficient equipment scheduling, and various wasted resources. Direct maintenance costs appear in the form of labor, materials, contracts, and overhead expenses. CMMS services solve these problems by making proactive maintenance a realistic, achievable, and stress-free goal.
Features and Benefits of CMMS Software
With CMMS, you can:
- Streamline Preventive Maintenance: Operational managers can create, assign, and monitor work orders in one place.
- Organize Inventory Management: Maintenance teams can track the movement of spare parts and reorder replacements as needed.
- Reduce Downtime: Technicians can report asset failures on-site from the convenience of their smartphones, reducing the length of equipment downtime.
- Improve Cost-Effectiveness: CMMS analytics provide management with insightful information that allows for better decision-making.
- Enhance Communication: MaintainX is the only provider that offers CMMS instant messaging within individual, group, and work-order chat threads. Translation: Important information arrives in real time and never falls through the cracks.
- Increase Compliance: Digital audit trails allow managers to determine who completed what task and when. Workers designate work orders as open, in progress, or closed, so managers know the progress of assigned work orders.
- Simplify Bookkeeping: Accountants have easy access to asset information that informs capital expenditure decisions and tax reporting.
- Improve Asset Management: CMMS allows managers to catalog and track assets by location, category, serial number, date, and more.
- Support Condition-Based Monitoring: Advanced CMMS platforms sync with sensor technology to provide real-time insights into equipment wear, tear, and potential failures.
Organizations exclusively practicing run-to-failure maintenance are not ideal candidates for legacy CMMS systems. Ideally, an organized preventive maintenance strategy should be implemented before integrating work order software or EAM software.
It takes time to track down manufacturers’ recommendations, evaluate past asset history, create proper workflows and workflow management for large numbers of assets, and train team members. Once everything is in place, the best CMMS will help your maintenance workflow automation run like a well-oiled machine.
MaintainX and Your Maintenance Workflow Automation
CMMS users include business owners, facility and maintenance management, asset planners, and maintenance personnel. Modern CMMS software is also useful for Safety Managers, Quality Control Managers, Directors of Operations, Logistics Coordinators, and more.
For small businesses (SMBs) to stay competitive in the global and local market, businesses must adopt technology that brings immediate efficiencies and impact. Being a small business used to mean that robust software solutions were too expensive or complicated. Now, solutions like CMMS software empower teams with revolutionary tools that can grow with your business and business processes.
MaintainX CMMS maintenance software lets you build, for each asset, an infinite number of calendar and/or meter-based preventive maintenance (PM) tasks. In addition, you can provide a clear description of task procedures, instructions, and other essential details within the PM task record.
Within the CMMS, each PM is recorded and accessible in the future via Asset History. Maintenance scheduled in advance helps keep things from falling behind. In addition, this data supports your reporting insights about where operations need to improve.
Modern, cloud-based CMMS platforms are scalable, affordable, and user-friendly. The software allows you to automate both long-term and short-term maintenance schedules based on quarterly, monthly, weekly, and daily tasks.
CMMS also allows you to capture minor maintenance activities that often fall through the cracks and go unnoticed. This enables teams to maintain backlogs at manageable levels. Additional features like inventory management, advanced asset history, work order commenting, team chat, and advanced reporting make MaintainX a game-changing tool for maintenance teams of all sizes.
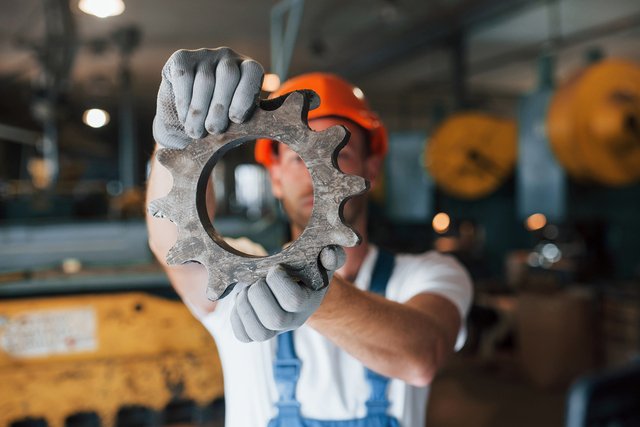
Track Asset History
Every time a technician completes a work order on an asset, the work order is linked to the asset’s history for reference. These completed work orders also help drive reporting insights via the MaintainX dashboard to detail asset maintenance and cost history.
Cloud-based CMMS systems utilize sophisticated data encryption protocols along with routine updates and maintenance. In addition, MaintainX performs frequent security and penetration checks to ensure that client data is not compromised or otherwise unavailable. MaintainX data is stored on encrypted Amazon Web servers because we prioritize data security across the entire system.
Modern CMMS solutions like MaintainX offer parts inventory modules to track parts usage across work orders. When a maintenance team is disorganized, it can be challenging to find parts needed or even know if they are available on site. Our CMMS tracks parts’ usage and restock histories and even sends alerts to reorder when parts quantities are running low.
Increase Transparency and Accountability with MaintainX
MaintainX is the world’s first CMMS platform designed with real-time chat. As a result, operational managers, maintenance technicians, and critical stakeholders can instant message one another directly within the app’s work orders.
MaintainX is also one of the first programs designed specifically for smartphone usage from day one. Comparatively, the majority of CMMS providers adapted their software for mobile devices from complex desktop-based legacy systems. Translation: These adapted CMMS programs are not always user friendly.
With robust CMMS reporting features, leaders can quickly determine, for example, which policies are weak, which machines cause the most problems, and where there is overspending. In addition, efficiently tracking asset health allows project management to fine-tune their strategies toward reducing downtime, cutting costs, and increasing asset longevity.
The best CMMS enhances your understanding of assets and organization through advanced reporting features that track key performance indicators (KPIs), analyze trends, and generate reports for decision-makers. For example, maintenance managers can identify increasing costs, low efficiency, or frequent maintenance using a CMMS to evaluate historical data and patterns.
MaintainX makes it easy to identify outliers in your organization. For example, through reporting, you can quickly identify a forklift that requires 10x more maintenance than any other in your fleet and adjust capital expenditures accordingly.
Modern computer-based management systems are sleek, intuitive, and affordable. With MaintainX, you do not have to sacrifice features for simplicity—you can:
- Create reactive and preventive maintenance work orders.
- Assign recurring work orders to both teams and individuals.
- Monitor progress by maintenance category, priority level, downtime, etc.
- Analyze maintenance costs for greater efficiency and savings.
- Hold text conversations with team members in real time.
Anyone with a smartphone can download MaintainX and get started right away with our basic plan, including unlimited work orders.
FAQs
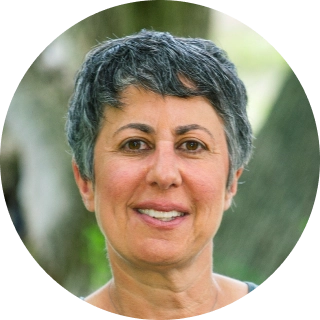
Caroline Eisner is a writer and editor with experience across the profit and nonprofit sectors, government, education, and financial organizations. She has held leadership positions in K16 institutions and has led large-scale digital projects, interactive websites, and a business writing consultancy.