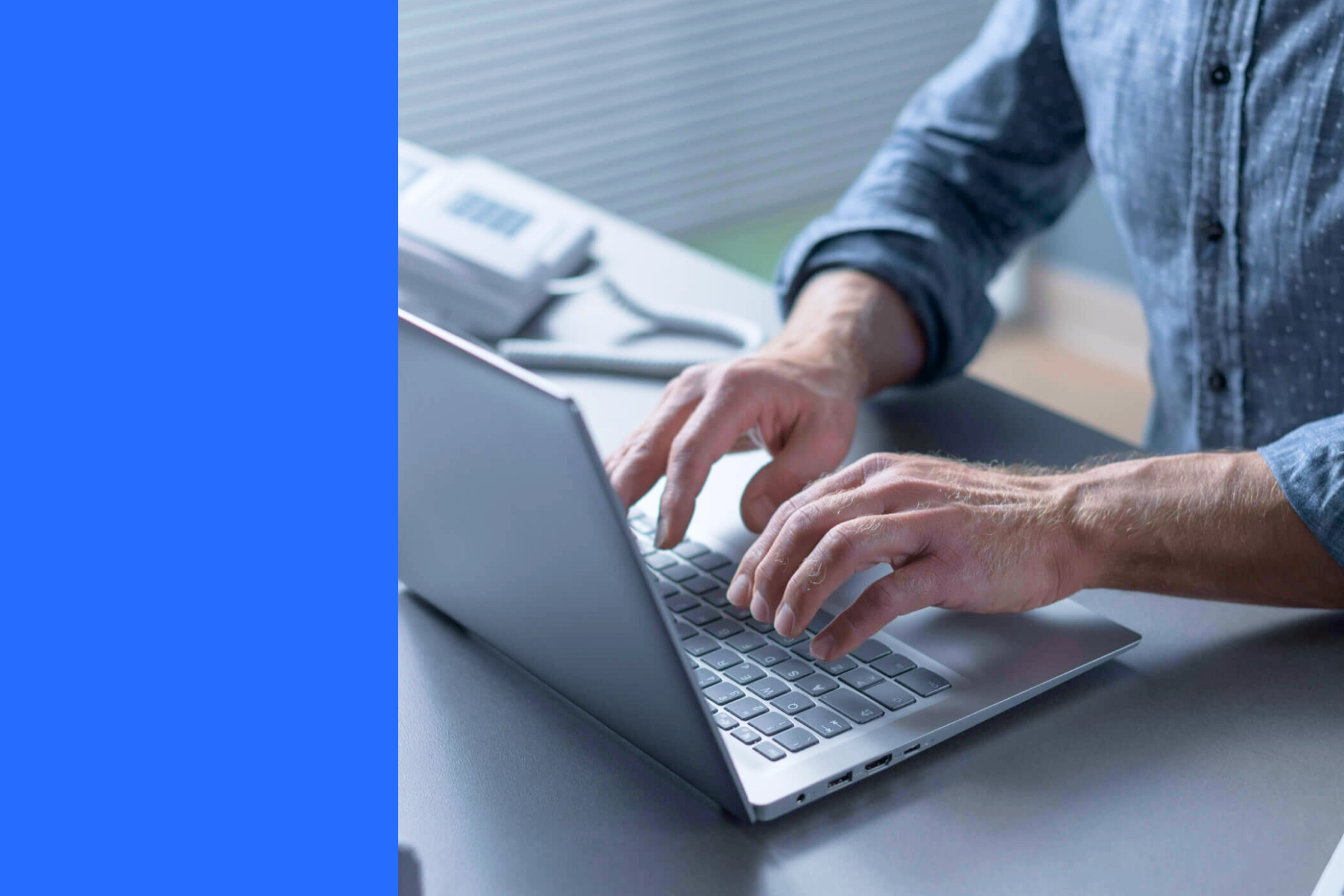
You know that preventive maintenance is essential for keeping your equipment running smoothly, but developing a regular maintenance schedule can feel overwhelming. Without a structured approach, maintenance teams often find themselves constantly reacting to breakdowns rather than preventing them.
A well-designed preventive maintenance schedule helps you transition from costly reactive maintenance to strategic equipment management. By following proven steps to create and implement your PM schedule, you'll reduce downtime, extend asset lifespans, and optimize your maintenance resources.
This guide walks you through the process of building an effective preventive maintenance schedule that works for your specific operational needs, from asset inventory to continuous improvement.
Key takeaways
- Preventive maintenance schedules reduce unplanned downtime by addressing equipment issues before they cause failures.
- Three main schedule types—fixed, floating, and meter-based—offer different advantages depending on your equipment and operational needs.
- Start by inventorying critical assets and determining maintenance priorities through criticality analysis to focus resources where they deliver the most value.
- The right maintenance intervals prevent both equipment failures and excessive maintenance, optimizing both reliability and resource utilization.
- Digital maintenance management solutions like MaintainX can reduce monthly maintenance costs by 30% through better scheduling, resource allocation, and communication.
What is a preventive maintenance schedule?
A preventive maintenance schedule is a plan that details when to perform maintenance tasks before equipment fails. This maintenance schedule serves as the foundation for any maintenance program, helping teams prevent unexpected downtime and extend asset lifespans.
Creating a successful preventive maintenance schedule requires more than just setting dates. You must understand:
- Your piece of equipment’s specifications and maintenance needs
- Available workforce and their skills
- Required materials and tools
- Realistic timeframes for task completion
Maintenance schedulers, supervisors, and planners typically develop these schedules. They balance maintenance requirements with operational demands to minimize operational disruptions due to production cycles.
Note the difference between an effective preventive maintenance schedule and a preventive maintenance plan. Planning determines what work needs to be done and how. Scheduling establishes who performs these tasks and when, ensuring resources are allocated efficiently for maximum uptime.
Why should I have a preventive maintenance schedule?
A preventive maintenance schedule transforms reactive fire-fighting into proactive equipment management. Organizations that implement effective PM schedules experience fewer breakdowns, longer asset lifespans, and more predictable maintenance costs—all directly impacting your bottom line.
The primary benefits of a preventive maintenance schedule include:
- Reduced unplanned downtime by addressing issues before they cause failures
- Extended equipment lifespan through regular care and maintenance
- Lower repair costs by catching small problems before they become major issues
- Improved workplace safety by ensuring equipment operates as designed
- Better resource allocation for maintenance personnel and spare parts
- Enhanced compliance with regulatory requirements and safety standards
- Increased overall equipment effectiveness (OEE) and production reliability
Preventive maintenance schedules are most appropriate for critical equipment where failure would halt production or create safety hazards and high-value assets with significant replacement costs.
Not all equipment needs preventive maintenance. For low-cost, non-critical items where failure has minimal impact, a run-to-failure approach to corrective maintenance might be more cost-effective. The key is to prioritize your assets based on criticality, focusing your PM program on equipment where routine maintenance delivers the greatest value.
Types of preventive maintenance schedules
Selecting the right maintenance schedule type impacts equipment uptime and resource allocation. Three main approaches exist, each with specific benefits for different equipment types.
Fixed PM schedules
Fixed preventive maintenance schedules operate on predetermined time intervals regardless of when equipment usage-based maintenance is due. These schedules run on calendar cycles—daily, weekly, monthly, quarterly, or annually.
With fixed schedules, maintenance tasks occur on set dates whether previous work was completed or not. If HVAC inspections are scheduled every first Monday, they happen that day even if last month's task was delayed.
This approach works best for:
- Equipment requiring inspections due to regulations
- Systems with time-based deterioration
- Facilities with standardized operations
- Assets where calendar time matters more than usage
For example, a data center schedules quarterly electrical system checks for uninterruptible power supplies. Even with minimal power fluctuations since the last inspection, technicians test connections, verify battery capacity, and check cooling systems on the same date each quarter to ensure reliability.
Floating PM schedules
Floating preventive maintenance schedules base each task's timing on when the previous work was completed. These schedules adjust future dates whenever work occurs.
This method ensures consistent intervals between maintenance activities. If a 30-day PM finishes 5 days late, the next PM is scheduled 30 days after completion, not from the original due date.
Floating schedules prevent regular maintenance tasks from creating scheduling conflicts but require tracking task completion dates. They work well for equipment where occasional maintenance delays won't impact operations significantly.
Meter-based PM schedules
Meter-based schedules trigger maintenance based on equipment usage rather than time. These schedules track various condition-based maintenance parameters like runtime hours, cycles, miles, or production units.
This approach matches maintenance to actual equipment wear, preventing both over-maintenance and under-maintenance by aligning work with usage patterns.
Meter-based PM schedules work effectively for:
- Vehicles tracked by mileage or engine hours
- Production machinery measured by cycles
- HVAC systems based on runtime
- Pumps and motors monitored by operating hours
- Equipment with seasonal usage variations
For example, a warehouse might schedule forklift maintenance every 200 hours of operation instead of monthly, optimizing both equipment reliability and maintenance resources during varying workloads.
How to create and execute a preventive maintenance schedule
Creating a preventive maintenance schedule requires systematic planning and ongoing refinement. These six steps will help you develop a proactive maintenance schedule that balances equipment reliability with resource efficiency.
1. Inventory your assets
Begin by listing your organization's equipment assets. Focus on items critical to operations, safety, and productivity.
For each asset, record:
- Make and model
- Serial number
- Location
- Primary users
- Required parts
- Maintenance history
Use a spreadsheet or CMMS to organize this information. This inventory becomes the foundation of your preventive maintenance program.
2. Determine maintenance priorities
Not all equipment needs preventive maintenance. Conducting PM on every asset wastes resources. Use criticality analysis to set priorities for effective preventive maintenance.
Consider these factors when ranking assets:
- Production impact if failure occurs
- Safety risks
- Repair costs
- Maintenance requirements
- Compliance needs
Schedule PM for high-priority assets first. Place non-critical or older items on reactive maintenance programs to optimize resources.
3. Identify ideal preventive maintenance intervals
Finding the right maintenance frequency prevents both unexpected equipment failures and excessive maintenance.
Determine appropriate PM intervals by:
- Checking manufacturer recommendations
- Reviewing past failure patterns
- Analyzing equipment performance data
- Getting input from operators and technicians
- Considering operating environment factors
These inputs help establish maintenance frequencies that match your specific operating conditions and equipment needs.
4. Schedule recurring work orders
Implement a system for scheduling and tracking recurring work orders. Whether using paper, spreadsheets, or CMMS software, your system should:
- Generate work orders based on defined intervals
- Assign qualified technicians to tasks
- Include maintenance procedures
- Track completion status
- Document parts and labor
A CMMS platform offers advantages through automation, real-time notifications, and robust data collection that enables deeper analysis. This collected maintenance data becomes invaluable for identifying optimization opportunities, revealing potential cost savings, and spotting efficiency gaps—all insights that drive the continuous improvement process.
5. Track maintenance KPIs to measure success
Monitor key performance indicators to evaluate your preventive maintenance schedule effectiveness:
- Mean time between failures (MTBF): Uptime ÷ number of failures
- Planned maintenance percentage (PMP): Planned hours ÷ total maintenance hours × 100
- Scheduled maintenance critical percent (SMCP): (Days overdue + maintenance cycle) ÷ maintenance cycle × 100
- Preventive maintenance compliance (PMC): Completed PMs ÷ scheduled PMs × 100
- Overall equipment effectiveness (OEE): Measures productivity, considering availability, performance, and quality
These metrics reveal how well your PM program supports operations and where improvements are needed.
6. Improve your schedule
Use maintenance data to refine your preventive maintenance schedule. Analyze KPI trends to identify:
- Equipment failing despite PM (may need more frequent maintenance)
- Assets showing no improvement from PM (possible over-maintenance)
- Consistently late maintenance tasks (resource allocation issues)
- Early part replacements (incorrect maintenance intervals)
- Seasonal performance patterns (schedule adjustment needed)
Adjust schedules based on these insights. Involve technicians in the improvement process to capture their observations. Their experience helps identify which preventive maintenance tasks and preventive maintenance activities deliver the most benefit.
A CMMS solution streamlines this analysis process by automatically tracking historical performance data, generating trend reports, and providing visualization tools that make patterns immediately apparent—capabilities that would be impractical with manual record-keeping.
4 tips for preventive maintenance scheduling success
Implementing effective PM schedules requires clear processes and proper tools. These four practices ensure consistent results.
1. Set clear procedures
Clear maintenance procedures eliminate guesswork. Create detailed steps in a preventive maintenance checklist for each task with inspection points, required tools, and safety precautions. Digital procedure libraries give technicians immediate field access to important procedures, improving schedule adherence.
2. Leverage software
Digital tools streamline maintenance scheduling and communication. Mobile-first CMMS solutions allow technicians to receive and update work orders instantly from their devices, eliminating paperwork delays and communication breakdowns between shifts. These systems also provide real-time inventory tracking and automatic reordering capabilities that ensure parts availability when needed.
Additionally, comprehensive CMMS analytics generate performance dashboards and trend reports that make monitoring maintenance effectiveness straightforward, helping teams continuously optimize their preventive maintenance program.
3. Optimize inventory
Preventive maintenance schedules fail without available parts. Track inventory usage patterns and set automatic reorder points for critical components. Link parts to specific tasks in your CMMS to forecast needs based on upcoming work orders.
4. Monitor performance
Regular performance tracking identifies issues before they impact your maintenance schedule. Review completion rates, task times, and maintenance technician feedback to spot recurring problems. Use these insights to adjust resource allocation or maintenance frequencies.
Why preventive maintenance schedules fail
Understanding common failure points helps maintenance managers implement successful PM programs.
Unclear or delayed communication
When information about equipment status and maintenance needs isn't shared promptly between teams, PM tasks get delayed or skipped. Implement real-time communication channels to keep everyone informed about maintenance priorities.
A CMMS platform addresses this challenge by providing a centralized communication hub where teams can share updates, document issues with photos, assign tasks, and receive automated notifications about critical maintenance events—all in real time. This visibility ensures everyone, from technicians to operations managers, has access to the same accurate information, eliminating the communication gaps that derail maintenance schedules.
Poor equipment inventory practices
Incomplete equipment records lead to missed maintenance. Maintain comprehensive asset inventories with specifications and maintenance requirements. Regular audits ensure information stays current as equipment changes.
Lack of consistent procedures
Without standardized procedures, work quality varies between technicians. Develop documented standards for all maintenance tasks and train technicians to follow them consistently to ensure PM tasks effectively prevent failures.
Simplify PM scheduling with MaintainX
If you’re wondering how to get around the challenges of preventive maintenance scheduling, you don’t have to do it alone. MaintainX can help you create and implement effective PM schedules. Here are some features that can support you.
Asset health insights
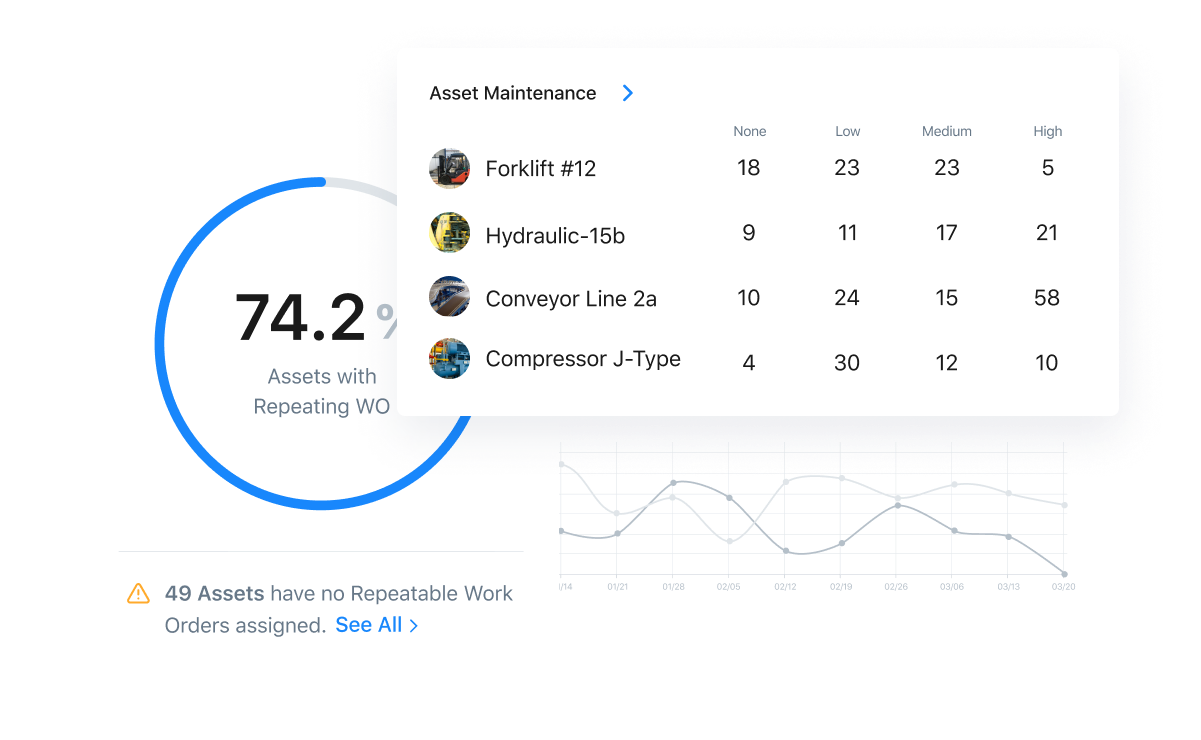
One crucial element for creating an effective preventive maintenance schedule is finding the right balance between too much or too little maintenance. Too little maintenance and the program yields no benefits, but too much maintenance can result in wasted efforts and resources. MaintainX’s in-depth reporting provides actionable insights into metrics like Mean Time Between Failure and Mean Time To Repair. By analyzing this data, MaintainX helps you to optimize your maintenance scheduling. You’ll be able to determine which assets require more frequent maintenance work and the ones that need less attention.
Resource planning with labor insights

Just as striking the right balance for maintenance work is critical, you also need to find optimal ways to apply your human resources. Knowing who to assign maintenance work and when can be difficult for maintenance managers, especially when you have to go over schedules manually to understand people’s historical workloads. MaintainX preventive maintenance software offers work scheduling tool that helps optimize your work management based on labor insights and smart estimates. You’ll get a complete picture of your team’s workload and capacity so you can prioritize, assign work orders, and make real-time adjustments.
Recurring work orders
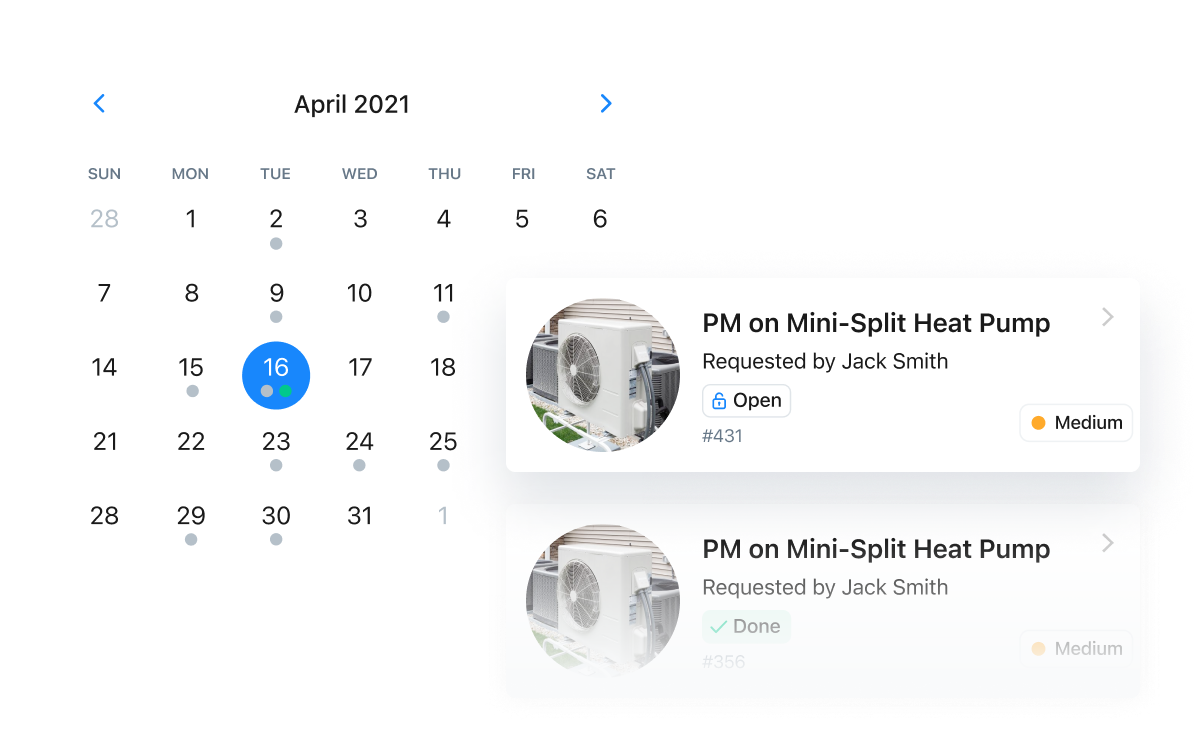
Planning out a maintenance schedule is one thing, but without the right implementation tools, your efforts risk getting wasted. MaintainX helps teams avoid missed schedules and incomplete work by offering tools to automate your maintenance scheduling. Repeatable work orders and mobile notifications help team members ensure they know what to do and when. Checklists, templates, procedures, and work instructions also ensure team members know exactly how to perform their tasks.
Meter-based preventive maintenance
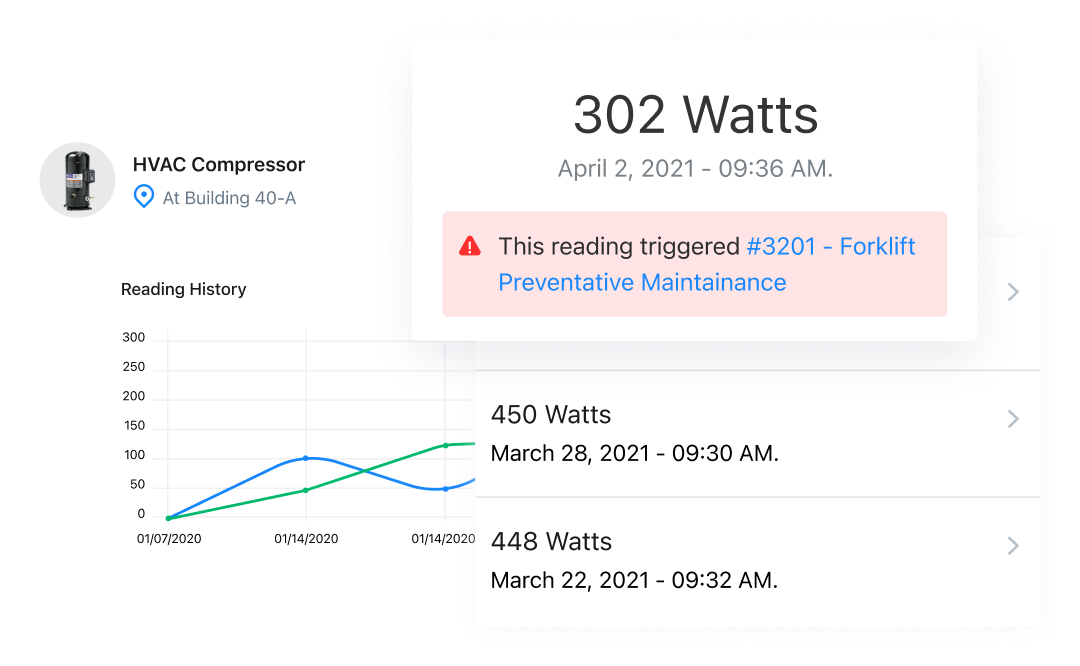
In addition to helping you execute your own preventive maintenance schedule, MaintainX also facilitates preventive maintenance on a meter-based schedule. By using MaintainX, you can automatically trigger preventive maintenance work based on meter readings—technicians can carry out maintenance work after time used, mileage, or any other readings you choose.
Ready to optimize your preventive maintenance scheduling? Get started with MaintainX today!
Preventive Maintenance Schedule FAQs
What is floating preventive maintenance scheduling?
Floating preventive maintenance scheduling bases each task's timing on when the previous task was completed rather than fixed calendar dates. If a 30-day PM is completed five days late, the next PM is scheduled 30 days from completion, not from the original due date.
Which elements belong in an effective preventive maintenance plan?
A complete preventive maintenance schedule should include equipment identifiers, task descriptions, required procedures, parts and tools needed, qualified technicians, estimated completion times, and maintenance frequencies.
How frequently should you review and refresh your preventive maintenance plan?
Review preventive maintenance schedules quarterly, with comprehensive updates annually. Update schedules whenever equipment conditions change significantly, new assets are installed, or other failure modes or patterns emerge.
Why should you implement a preventive maintenance system?
Preventive maintenance software automates work order creation, tracks completion status, and sends notifications about upcoming tasks. Digital platforms improve communication between maintenance and operations teams, centralize maintenance records, and provide insights to optimize maintenance intervals.
What is the best software for creating a preventive maintenance schedule?
MaintainX offers a comprehensive solution for preventive maintenance scheduling with an intuitive mobile interface for recurring maintenance work orders. Its reporting features provide insights into maintenance performance, helping teams optimize their PM programs across multiple locations.
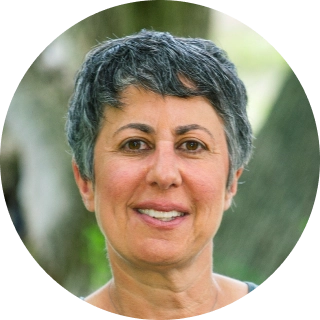
Caroline Eisner is a writer and editor with experience across the profit and nonprofit sectors, government, education, and financial organizations. She has held leadership positions in K16 institutions and has led large-scale digital projects, interactive websites, and a business writing consultancy.