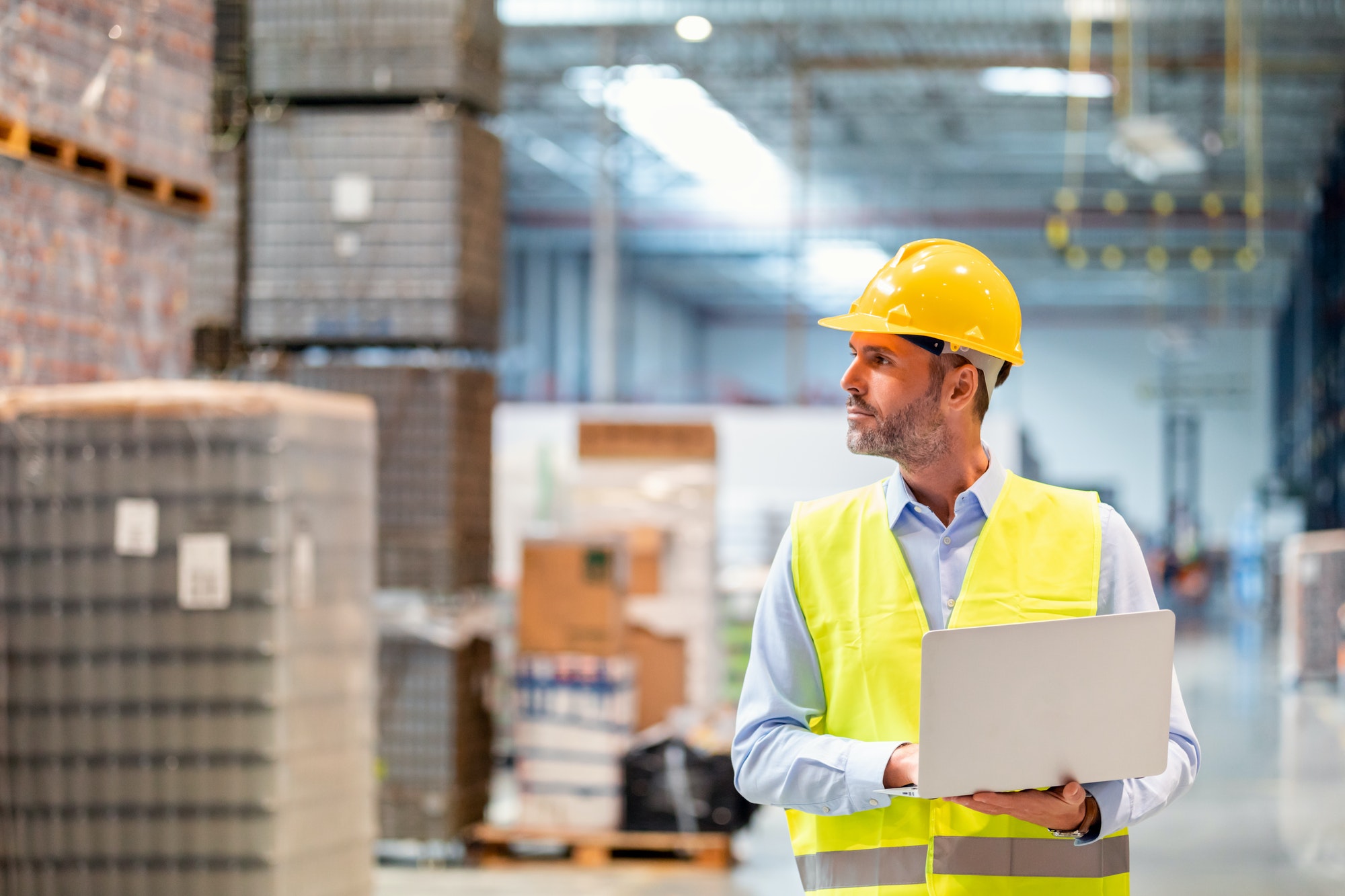
Work order management is important for organizing the workflows in your organization. From physical asset management to facility management and maintenance tasks, figuring out the right work order process flow is crucial for streamlining your operations. Defining the right work order process is beneficial because:
- Work orders allow you to standardize your operational and maintenance processes, which makes implementing preventive maintenance much easier. Preventive maintenance is crucial to prevent breakdowns, reduce downtime, and save costs.
- The work order process allows you to get real-time updates and insight into the process from your maintenance department.
- Real-time feedback via work orders can help with maintenance management and inventory management, which can also trigger purchase orders for falling inventory.
- Work orders help you track the maintenance process and lifecycle, which allows you to monitor maintenance metrics and KPIs like downtime, uptime, maintenance costs, etc.
Let’s look at creating the best work order management system for your team.
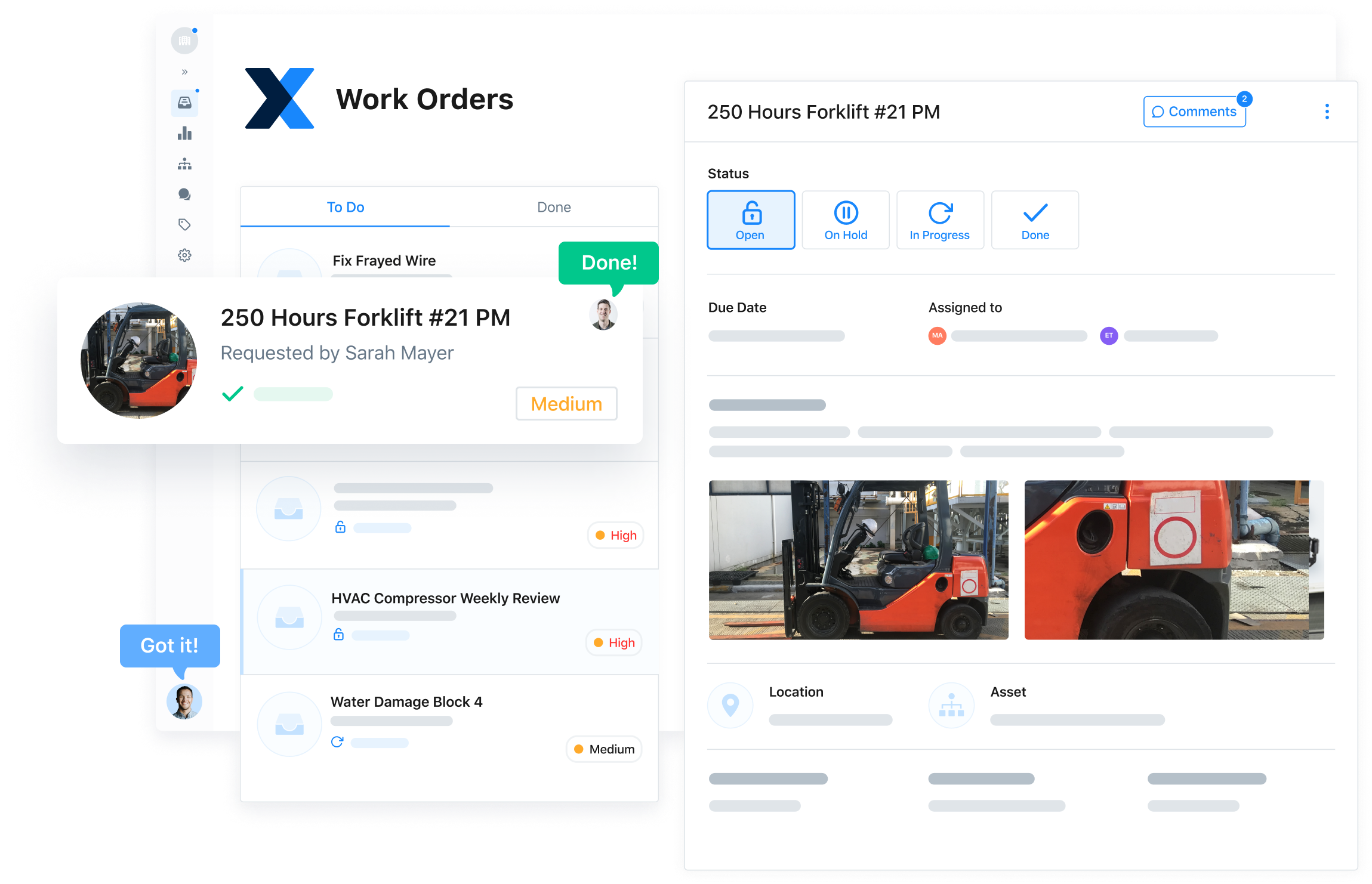
The Work Order Planning Process
You can modify the process to suit your needs, but the right workflow for a work order should include the following steps in some form.
Creating a Work Request
The work order management process usually begins with a work request. This involves someone identifying a task and then submitting the request. In general, work requests should contain information such as the nature of the potential task and the assets involved.
Other information, like the location of the assets within the facility, the task’s priority level, and deadlines, can also be included. To ensure success and a smooth workflow, create a standardized approach to submitting work requests. It helps when workers know that they need to, for example, include pictures in their work requests.
One way to standardize the process is to create a work order template with preset fields that staff must fill. Doing this ensures that, when you create a work order, whoever you assign the task to gets all the information they need to do a successful job. To make the process even smoother, consider using CMMS software instead of pen-and-paper forms.
McKinsey reports that using digital work management software helps companies improve their maintenance labor productivity by between 15 and 30 percent.
Creating the Work Order
The next stage in the procedure involves the work request becoming a new work order. In some cases, this is automatic. Use work order management software like a computerized maintenance management system (CMMS) to automate the process for your staff. An automated process makes it easier for people to create work orders.
Sometimes, a manager might need to approve a work request before it becomes an order. While there are benefits to automatic work orders, an approval phase helps avoid some problems. For example, a manager might know that the maintenance team is already working on a piece of equipment while the entire team might not. In such a case, someone should block the work order and prevent duplicate service requests.
This stage can also ensure that work orders get assigned to the correct team or staff members. In addition, you can decide now if this should be a one-off work order or a repeatable one. Similarly, you can determine if you want the work order done now or schedule work for later. You should typically create work orders in advance and have them follow a set preventive maintenance schedule.
Carrying Out the Task
If you use a CMMS to assign a work order, staff will receive work order assignments instantly, along with all the necessary information. This can be via email or even mobile devices in the case of mobile CMMS mobile apps. This phase also illustrates the value of using software. For example, if you need detailed information about the work order after, you can refer to the app. You can see when the technician got the work order, began work on it, and finished work.
Tracking this information is vital for performing analysis as part of your facility asset management. However, using this information depends on ensuring that workers meticulously log details about their work every step of the way.
This tracking helps you in the long run as you can study past work orders and identify any trends that can provide insights. For example, if specific work orders tend to take significantly longer than others, you might want to ensure the process is as streamlined as possible.
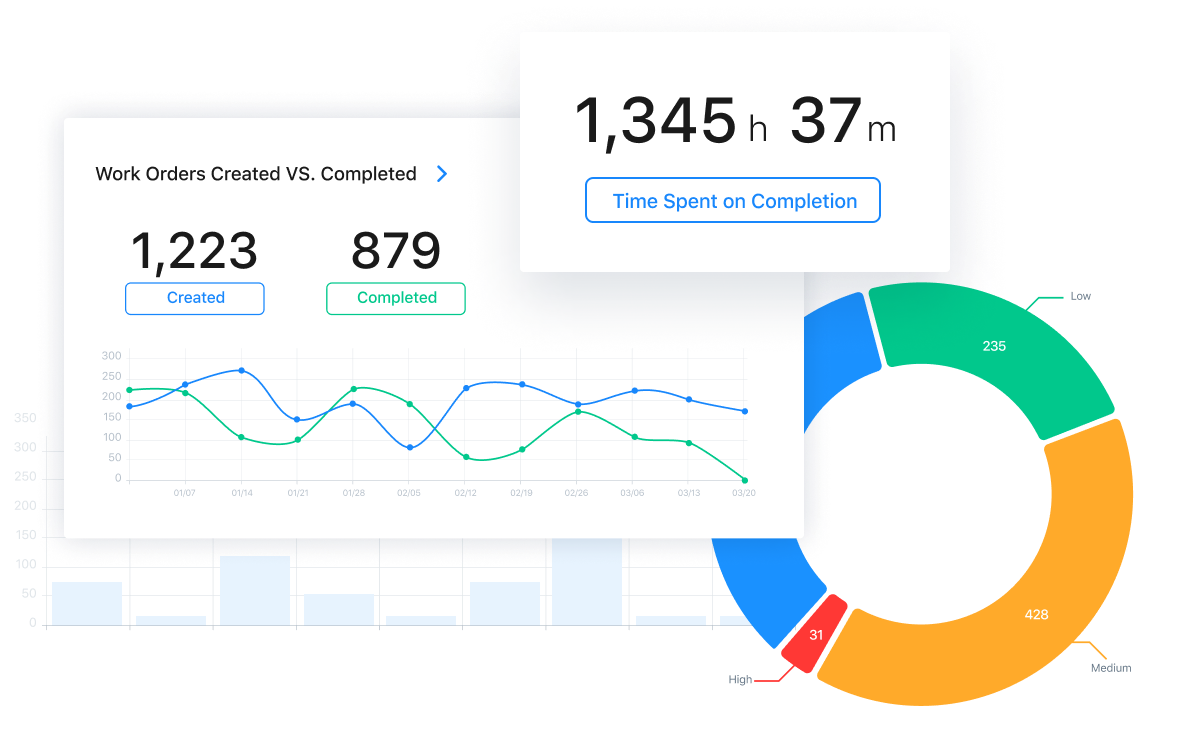
Completing the Work Order
Once the technician has completed their task, they can complete and close out the work order. They should log details of their work and any necessary information according to your standard processes.
Reviewing the Process
At this point, you want to review not just the work order but the actual asset under maintenance. For corrective procedures, you want to ensure that all team members carry out all repairs according to standards, follow all safety protocols, and that equipment runs as it should.
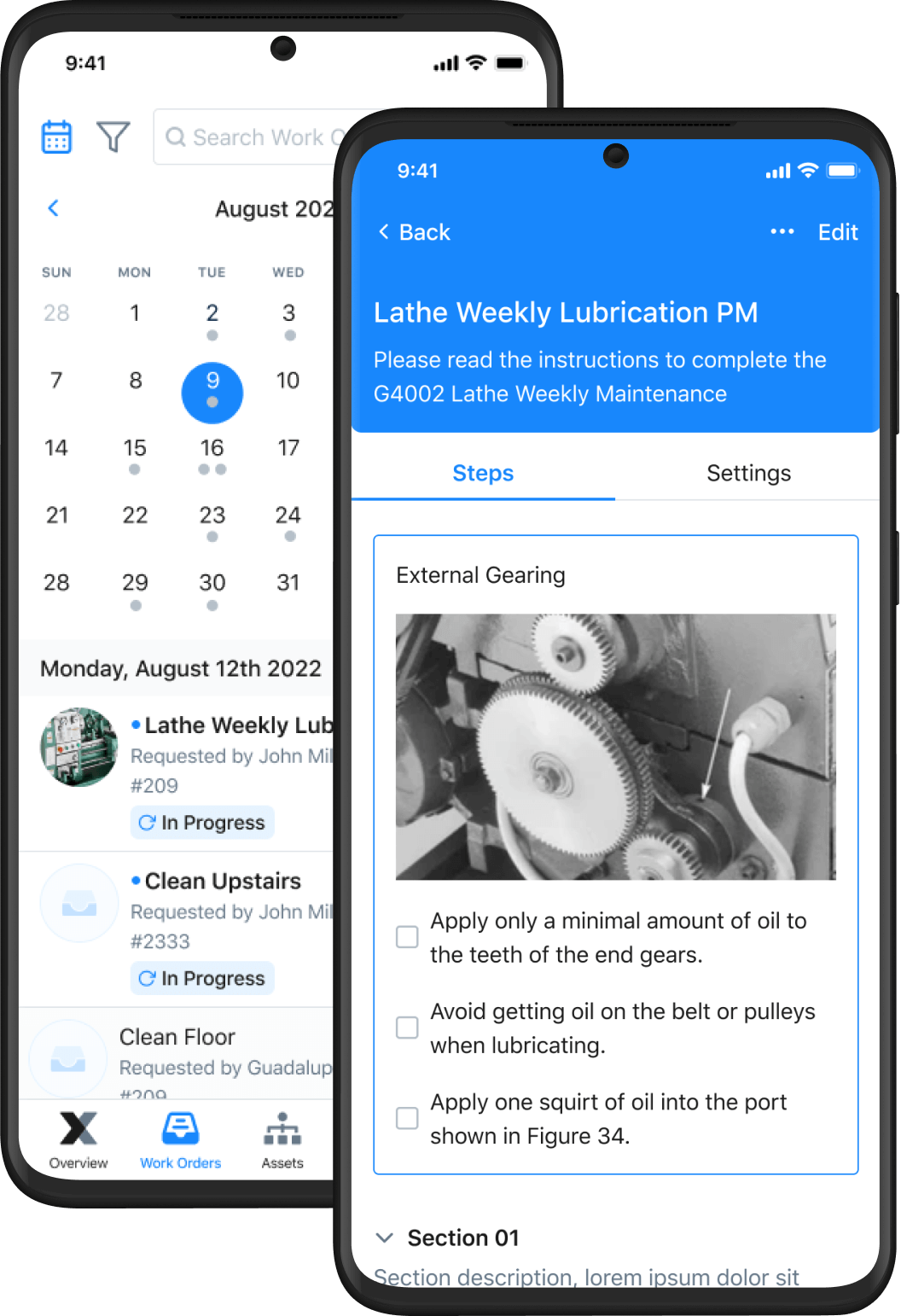
Scheduling Work Orders
Follow these steps to create the ideal schedule for your preventive maintenance work orders.
1. Decide on a Scheduling System
There are two primary ways you can organize your preventive maintenance work orders: according to a fixed schedule or a floating schedule.
Fixed maintenance schedules follow specific time or equipment usage intervals, regardless of previous tasks. For example, a weekly fixed schedule for conveyor belt lubrication means technicians will lubricate the conveyor belt every week regardless of whether or not the person responsible completed the task last week.
Floating schedules, on the other hand, focus on time intervals tied to the completion of a previous task. Work orders will only get triggered once the previous work orders are completed and closed, as opposed to a particular day, regardless of the outcome.
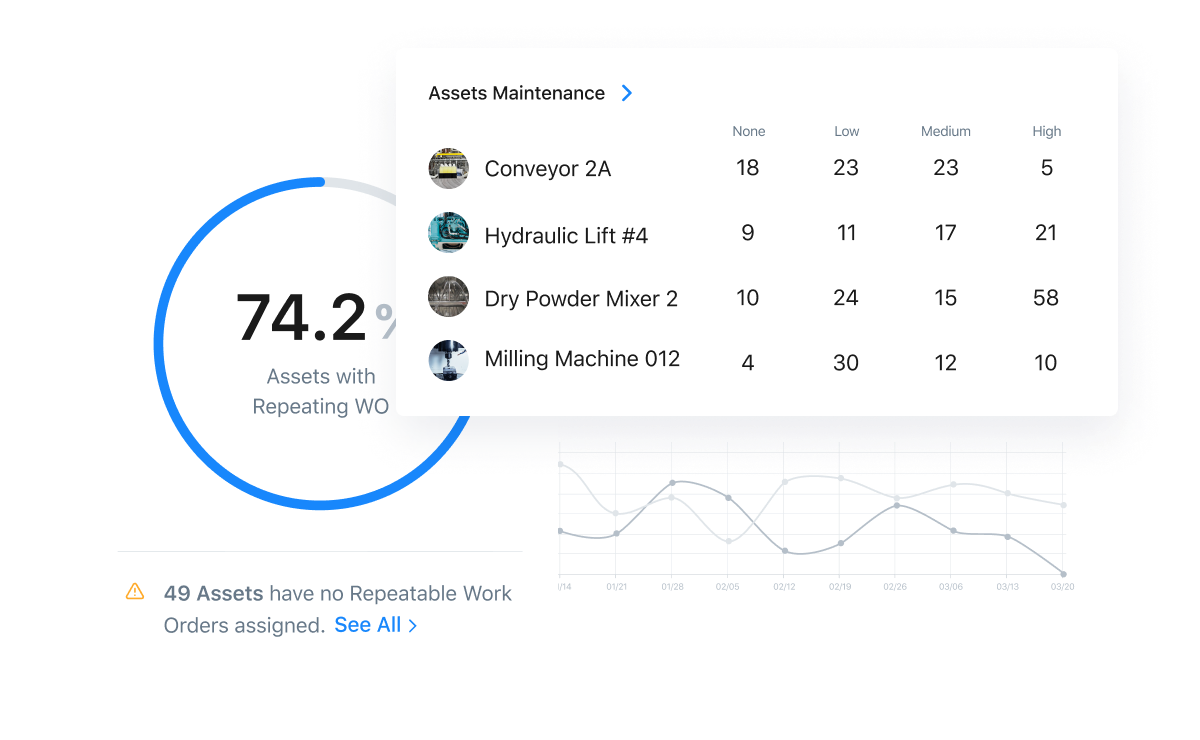
2. Inventory Assets
Maintenance managers must maintain a robust record of their organization’s most critical assets. A CMMS with asset tracking functionality helps ensure teams have a clear view of their assets and their continued usage.
By doing this, teams can ensure they keep track of what assets need maintenance and when and never miss a preventive maintenance task. CMMS solutions like MaintainX also offer useful asset tracking tools like barcodes and QR codes, which, when scanned, provide users insight into equipment data like usage history, maintenance history, and more.
3. Decide on Priorities
The next step in your scheduling process is prioritization. Successfully executing maintenance with limited staff and spare parts requires knowing how to rank equipment in order of importance. You don’t want to find yourself performing costly and time-consuming PM tasks on non-critical assets at the expense of critical assets.
Conducting a criticality analysis is a good way to determine priorities. A criticality analysis involves ranking assets according to their risk potential in categories like financial, operational, environmental, and health and safety.
4. Determine Ideal Intervals
To avoid over-maintaining and under-maintaining assets, determine the optimal intervals for running PMs on each asset. To do this, consult manufacturer instructions and equipment manuals for recommended schedules.
Also, pay close attention to your asset usage and historical data to identify failure patterns. For example, manufacturers might recommend a weekly schedule based on estimated usage, but if you use the asset more frequently or intensely, you might need a modified schedule. Technicians and operators can also offer insight into asset performance patterns. In addition, you should consider any regulatory requirements. Altogether, you want intervals that run smoothly and avoid a backlog of tasks.
5. Schedule Recurring Work Orders
Finally, use a CMMS to ensure no preventive maintenance task falls through the cracks. Schedule maintenance work in advance, assign tasks to technicians, and create repeating schedules according to your predetermined intervals. Create detailed work plans here, including all necessary details like work instructions, estimated work hours, locations, assets, and other relevant information. Also, feel free to use checklists and templates to simplify your maintenance work orders.
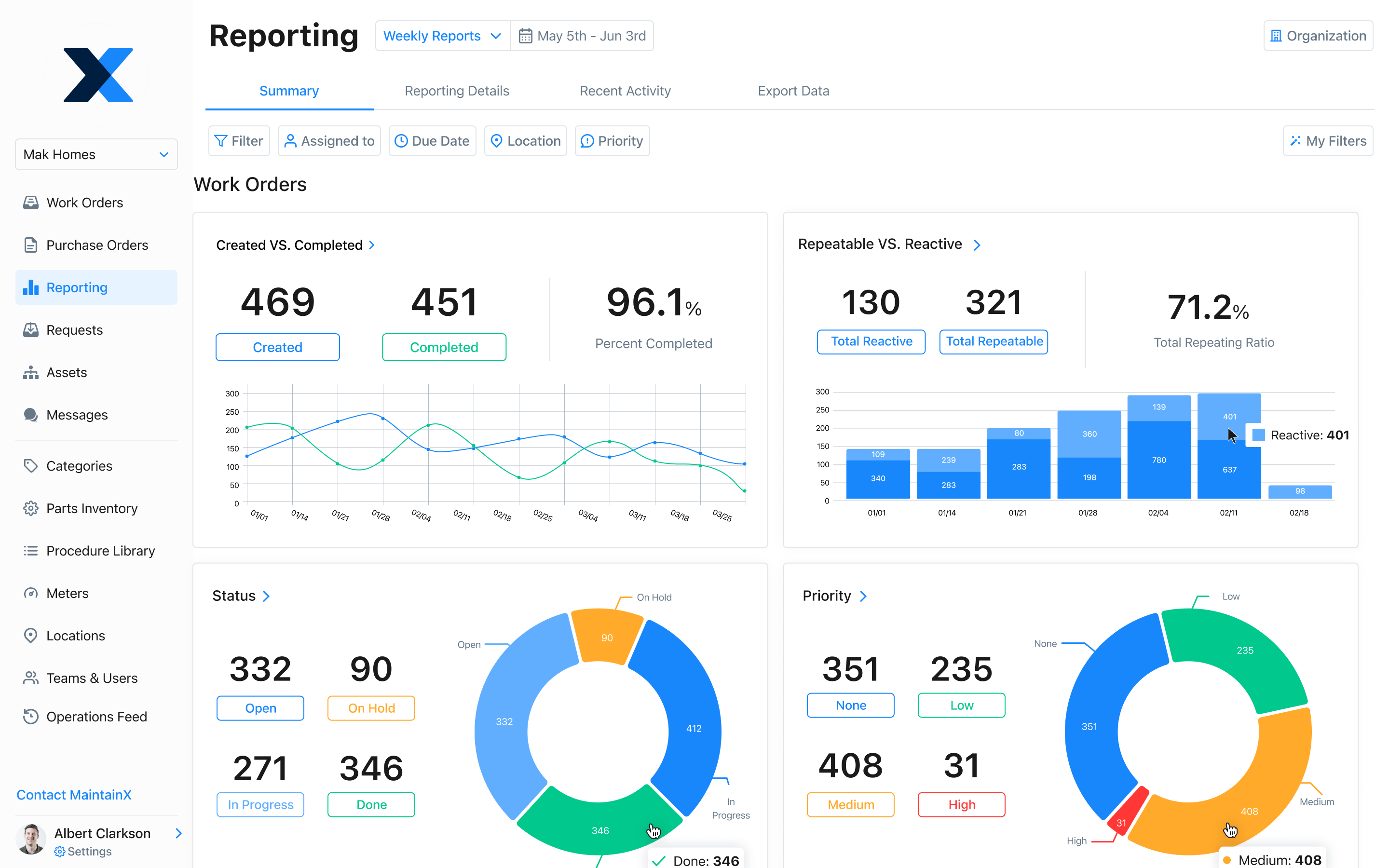
Leveraging a CMMS to Manage Your Work Orders
Build SOPs and Checklists
You need to create standard operating procedures to ensure your team executes work orders effectively, you need to develop standard operating procedures. A good CMMS will allow you to design and store SOPs in whatever form is best for you. This could be as a document stored in the cloud or a template your team just needs to follow.
Automate Work Requests
Move beyond pen-and-paper, text, or email requests to streamline your work request process. With a CMMS, you have an all-in-one platform that allows your staff to submit work requests and allows you to assess and approve them. You can also automate approved work orders and have them repeat at set intervals, essential for routine maintenance activities. As you ramp up your automated workflows, consider adding predictive maintenance workflows, along with sensors and meters that trigger work requests and work orders.
Monitor Your Work Order Lifecycle
CMMS platforms also allow you to keep detailed records of all your work orders. Staff can log all their activities, from when they start the process to any tasks involved and the eventual outcomes. This information comes in handy when you’re carrying out audits or trying to verify compliance efforts, and can help you optimize your future maintenance planning.
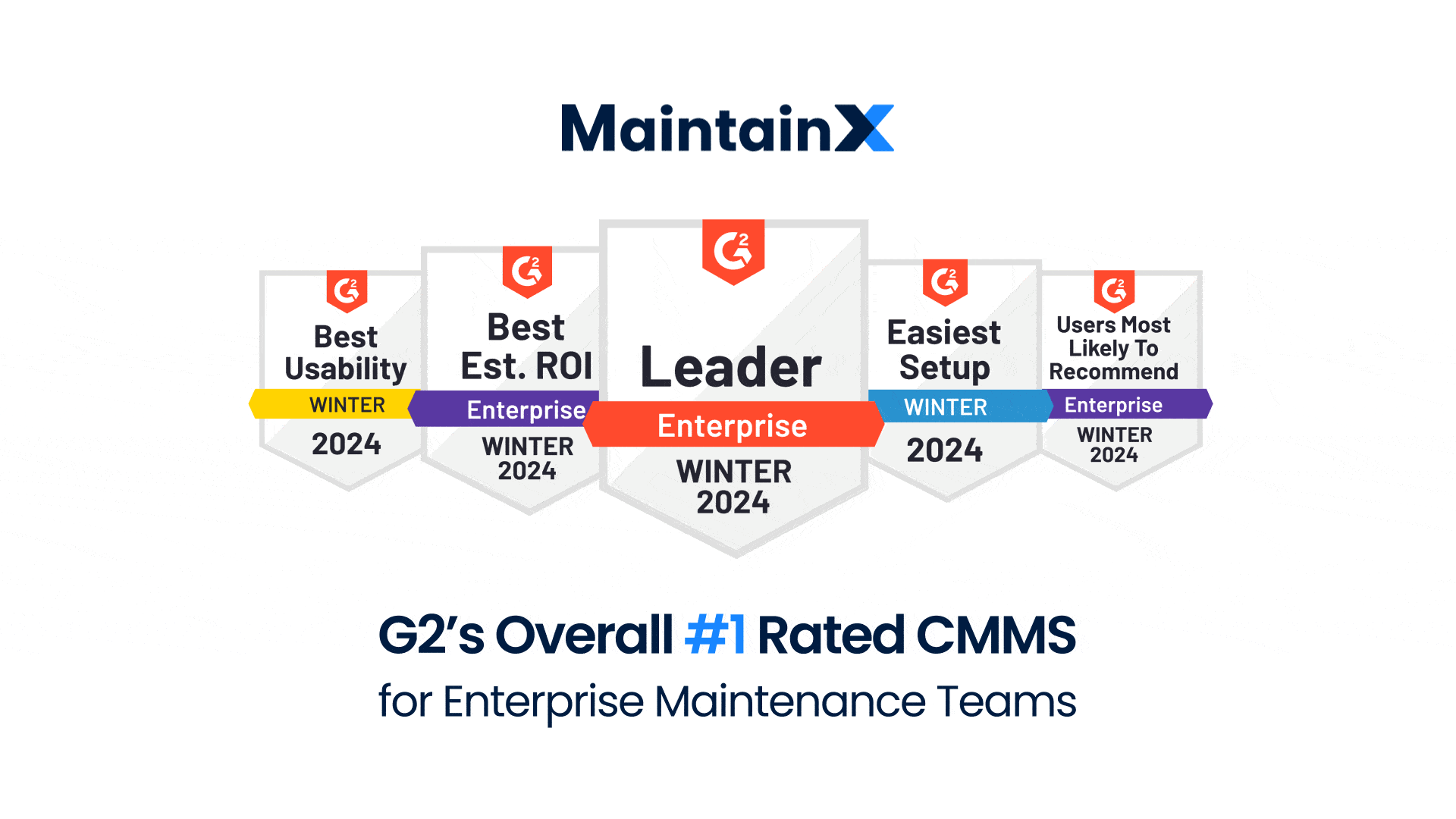
MaintainX Work Order Software
MaintainX is a mobile-first CMMS platform that can help you optimize your work order planning process and execution. Use MaintainX to execute a proactive maintenance plan and schedule work orders, get real-time updates from the shop floor, and gain insights into your performance over time.
If you’re looking to streamline not only your work orders but your work processes, try MaintainX today.
FAQs
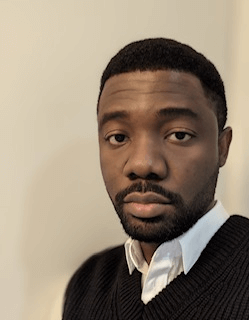
Lekan Olanrewaju is a content writer with years of experience in media and content creation. He has held positions at various media organizations, working with and leading teams at print magazines, digital publications, and television productions.