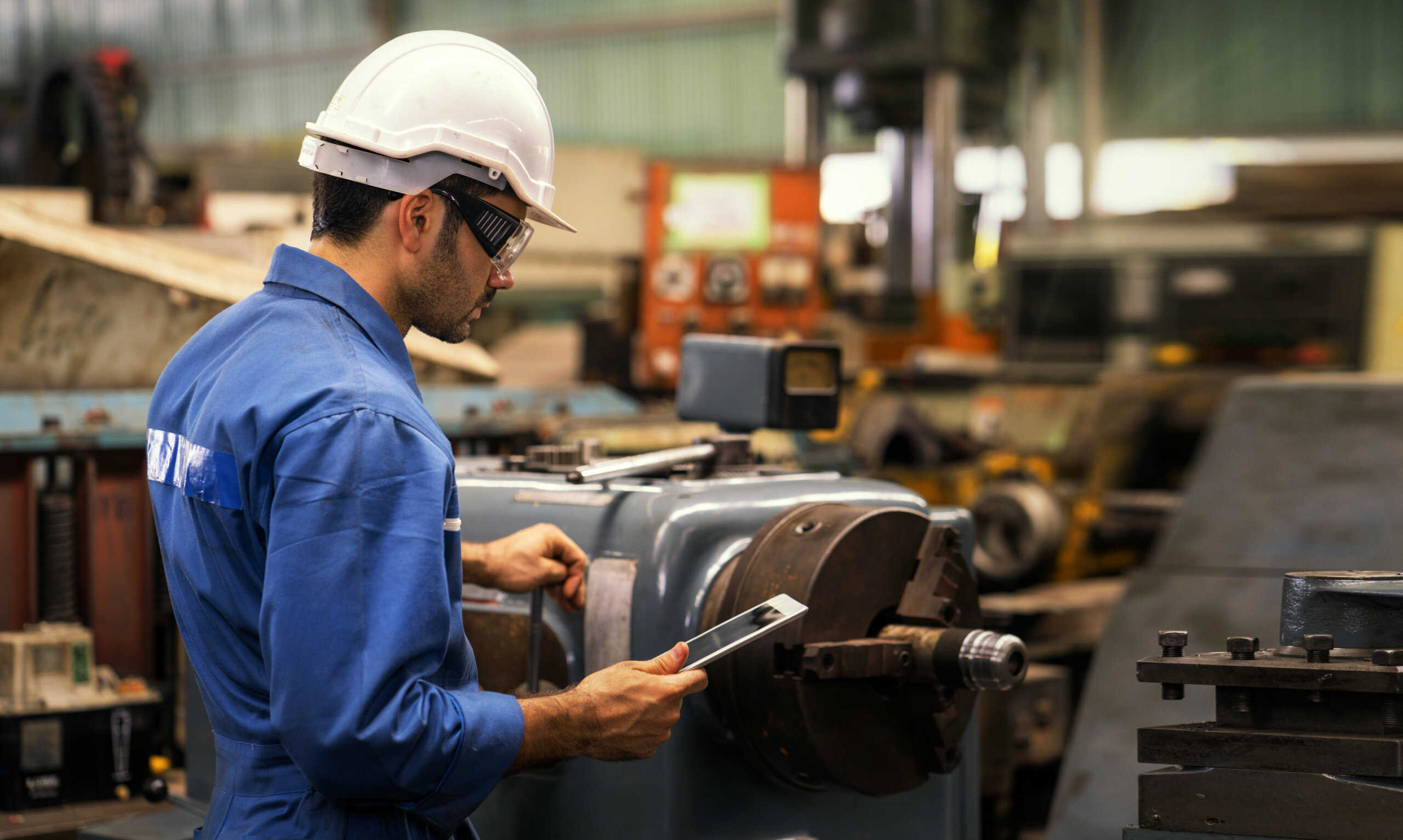
Mobile CMMS applications are the starting point for managers wanting to uplevel their facilities maintenance departments. Cloud-based CMMS apps allow company leaders to build more cost-effective, cross-connected, and productive workforces.
These days there’s a lot of talk about leadership. We hear about empowering employees, being transparent, and leading through change.
Move Your Maintenance into the Cloud
There’s no doubt that excellent leadership yields organizational success, but it’s not just about being a great leader. It’s about the operational systems great leaders put into place; especially, in light of recent shutdowns, slowdowns, and uncertainty worldwide.
With that said, even the best systems can fall flat without employee buy-in. However, workers who understand “the why” behind standard operating procedures and have the right tools for the job—like mobile CMMS— are a force to be reckoned with.
This article will delve into a new wave of computerized maintenance management systems (CMMS). After reading, you will understand why mobile CMMS revolutionizes O&M systems in industries from manufacturing to hospitality.
What Is a Mobile CMMS?
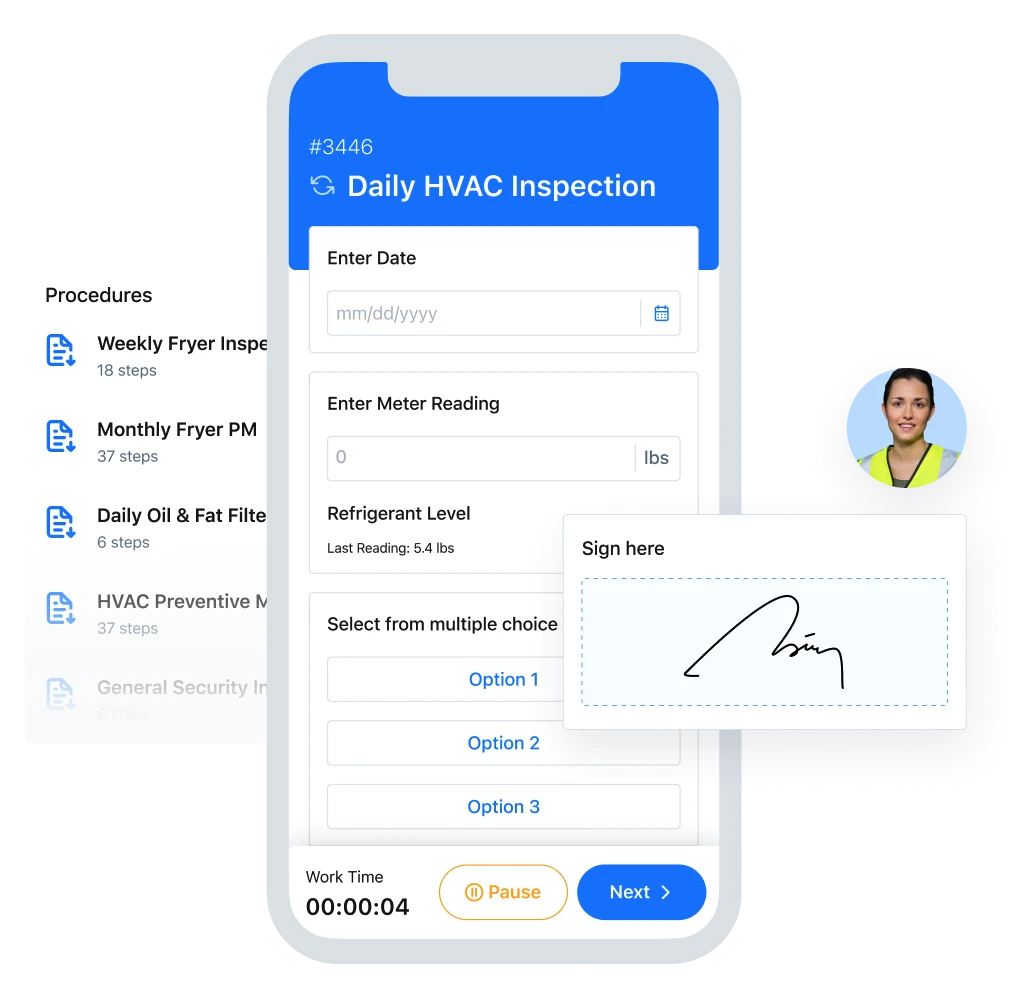
Mobile CMMS software allows managers to create, assign, and monitor work orders; organize data on facility assets, spare parts, and cost/time metrics; and message team members directly within digital work orders from their smartphones.
These cloud-based CMMS maintain a database of integrated systems that centralize maintenance department initiatives in one convenient location. Essentially, it’s a new kind of work order management system that empowers maintenance teams to become more self-sufficient.
When maintenance technicians have access to historical maintenance data at their fingertips, they are free to move forward with accurate information. Consequently, these mobile apps translate into managers receiving fewer emails, phone calls, and text messages from confused workers.
How Do Mobile CMMS Apps Work?
Mobile maintenance management software is built onto what app developers call “cloud-based servers.”
They then automate these servers over the Internet for shared usage. One of the best parts about cloud-based mobile applications is their scalability and affordability. In the past, maintenance departments wanting to take advantage of CMMS were limited by their ability to afford, house, and maintain on-premise hardware.
Not only did the work order software cost hundreds of thousands of dollars, but its interface often proved too difficult for the average worker to navigate. Consequently, it’s not hard to find manufacturing facilities that consider CMMS as a “sunk cost!”
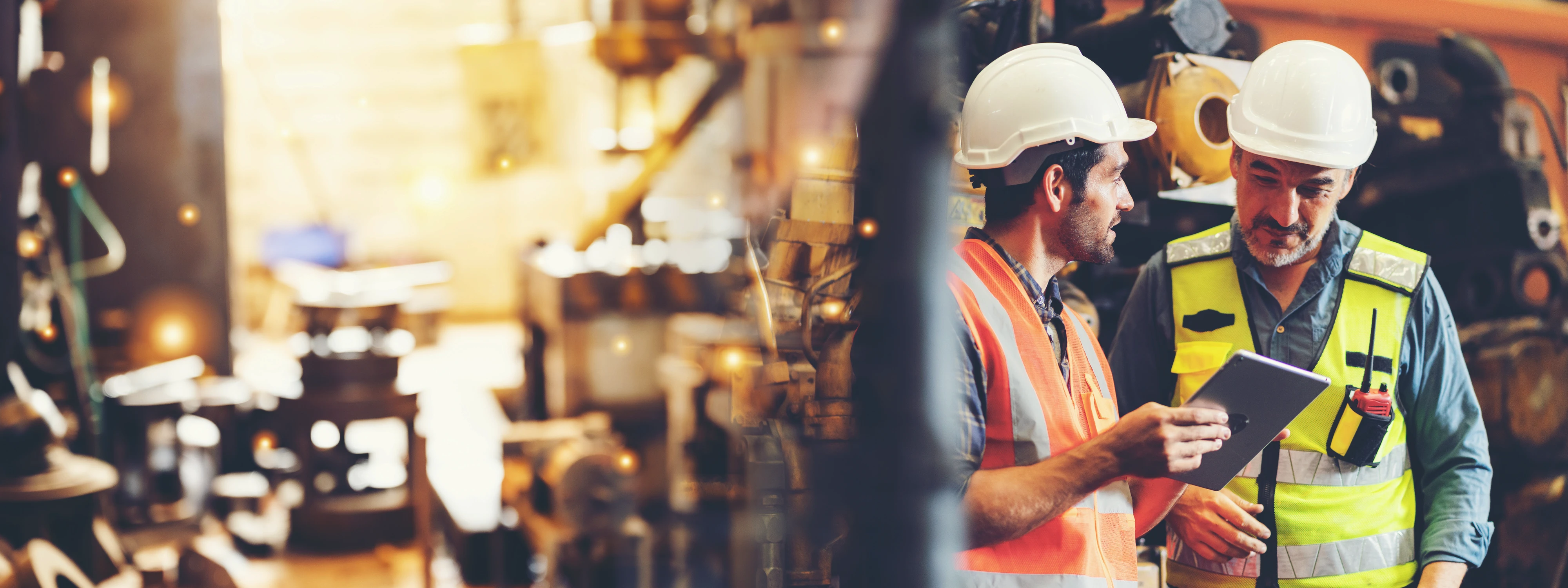
What’s the Difference between CMMS and EAM?
If you’re entirely new to computerized maintenance management systems (CMMS), you may have seen the term used interchangeably with enterprise asset management (EAM). In recent years, some providers have misleadingly marketed themselves as “EAM systems” despite not having a full range of EAM functionality.
Though both software systems embody similar traits—supporting maintenance task management, inventory management, and asset tracking—they aren’t the same. Maintenance and MRO (Maintenance, Repair, and Operations) management are CMMS’s core, while EAM facilitates tracking assets throughout their entire life cycles.
For example, with EAM, you can oversee MRO procurement, engineering, accounting, and business intelligence. Additionally, typical EAM solutions provide integration options that connect the software to supervisory control and data acquisition (SCADA) systems and building automation systems (BAS).
A robust CMMS is the best option for most small businesses (SMBs). Alternatively, larger enterprises can use a singular EMA or combine it with a streamlined mobile CMMS for greater versatility. With that said, both cloud-based apps can guarantee crucial information is always available in real time via desktop, tablet, or mobile devices.
What Are the Advantages of Mobile Maintenance Software?
Organizing workflows and mobile work orders is a breeze with the right CMMS. Beyond increased convenience, mobile maintenance software provides users with several advantages compared to analog O&M management methods.
Mobile CMMS allows maintenance teams to:
- Access digital work orders both online and offline.
- Monitor scheduled and unscheduled maintenance activities.
- Track work order history by asset, location, user, and category.
- Pull up real-time reports of maintenance data to track progress.
- Set low-quantity alerts for crucial inventory and supply reordering.
- Create SOP checklists that are easier to track than paper checklists.
- Document technical procedures, policies, and manuals in the cloud.
- Communicate with team members via individual and group messages.
Having the right tool translates to improved maintenance operations with fewer surprises for workers. At the end of the day, strong leadership means a) equipping technicians with everything they need to fulfill work orders without hesitation and b) maintaining open lines of communication across departmental roles.
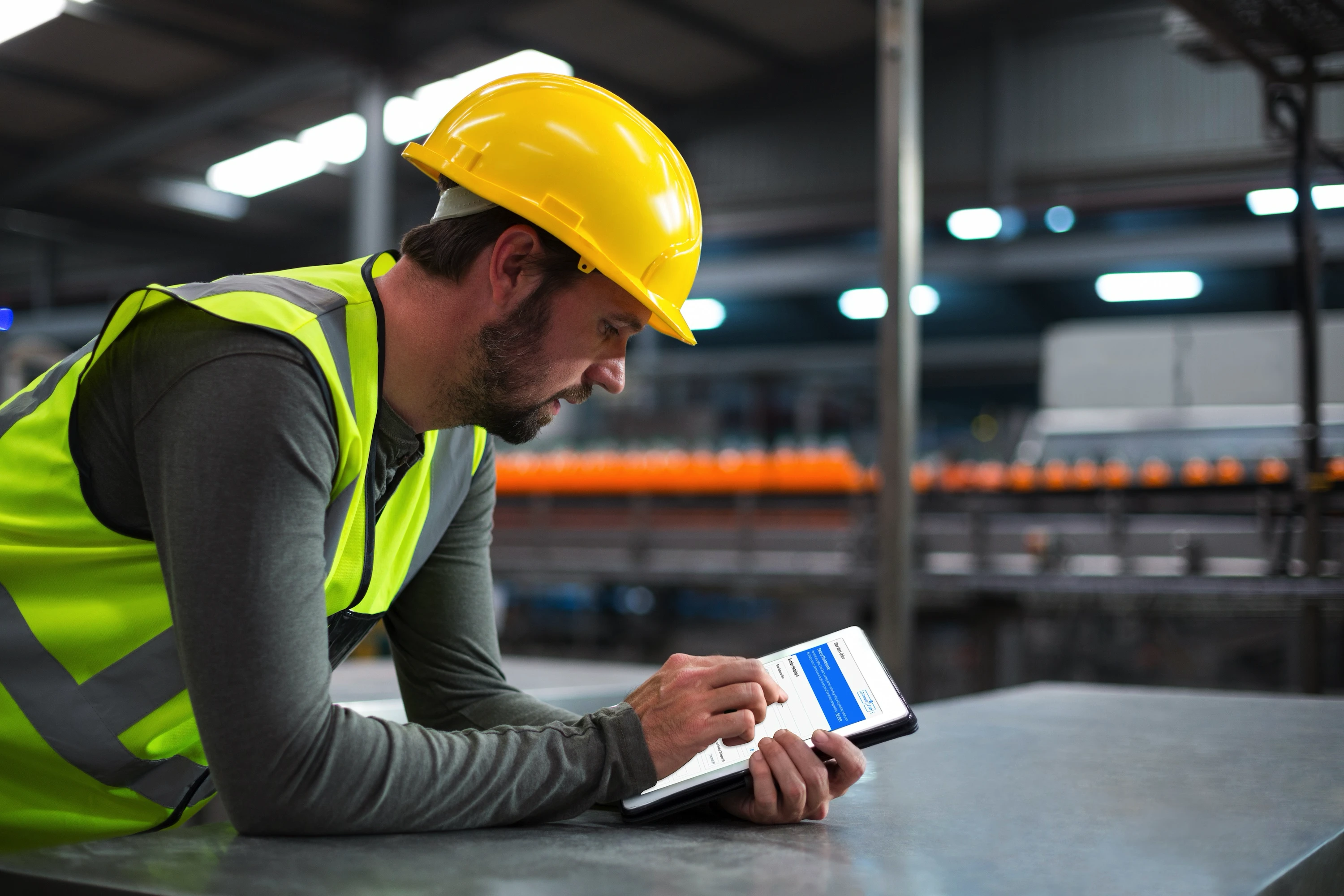
Transitioning from Reactive to Preventive Maintenance
If you’ve never used any type of CMMS software, there’s a good chance your department predominantly operates in “reactive mode.” Reactive maintenance, or run-to-failure maintenance, involves waiting to repair assets until they break.
According to Plant Engineering’s Facilities Maintenance Report, most organizations still exclusively practice reactive maintenance. Running a consistent preventive maintenance (PM) program is nearly impossible without a robust CMMS system.
Depending on the size of your asset inventory, you could be maintaining dozens, if not hundreds, of complex pieces of machinery. As mentioned above, securing a CMMS was cost-prohibitive until recently. Mobile CMMS providers have widened the playing field with low monthly pricing plans.
However, switching from reactive maintenance to PM doesn’t happen overnight. To be successful, leadership can take the following steps:
- Establish clear, realistic, and KPI-driven goals.
- Record an accurate inventory of asset information in a spreadsheet.
- Conduct a criticality analysis to establish an equipment PM hierarchy.
- Document standard operating procedures for completing PM assignments.
Click here to read “How to Start a Preventive Maintenance Program from Scratch.”
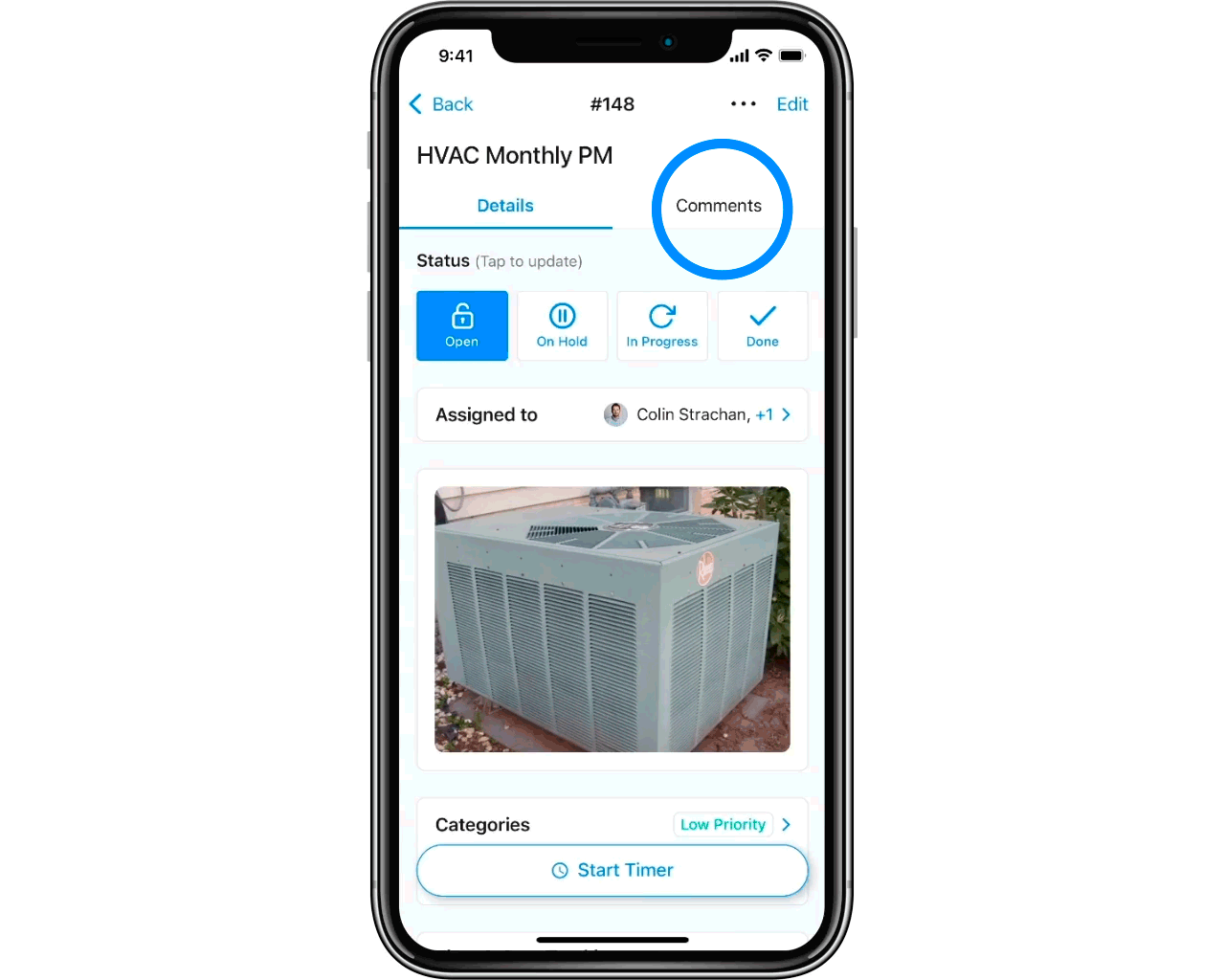
Get Your Work On with Mobile CMMS
Cloud-based CMMS systems are essential to building productive, efficient, and profitable modern maintenance departments. Our web-based CMMS software, as well as our mobile CMMS software, provide real-time access across our features.
The right CMMS will help reduce downtime, increase profit margins, extend equipment lifecycles, and support consistent supply chain control. Are you an operational leader who would love to hit some hefty maintenance KPIs within the next six months?
If so, we invite you to check out MaintainX. Our mobile CMMS is available for download on both iOS and Android devices. Click the button below to get a free 30-day trial of MaintainX Premium (no credit card required).
FAQs
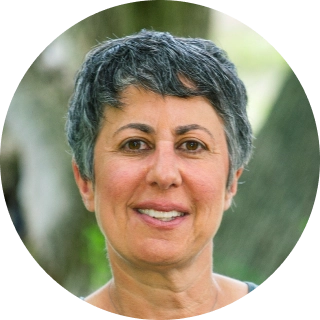
Caroline Eisner is a writer and editor with experience across the profit and nonprofit sectors, government, education, and financial organizations. She has held leadership positions in K16 institutions and has led large-scale digital projects, interactive websites, and a business writing consultancy.