For most products, the parts you see are only a small part of the story. Behind every item on a shelf lies a long list of behind-the-scenes essentials: cleaning supplies, spare parts, tools, and maintenance work. These items may not appear in the bill of materials, but without them, nothing gets built or shipped.
This behind-the-scenes ecosystem is known as maintenance, repair, and overhaul (MRO). While not widely recognized outside of operations teams, the workflow plays a crucial role in keeping supply chains safe and productive.
Think of this guide as MRO 101. We’ll cover what MRO consists of and how to make it work best in your organization.
Key takeaways
- MRO (maintenance, repair, and overhaul) is everything that keeps your equipment, tools, and facilities up and running behind the scenes.
- The right MRO interventions Whether it’s preventive, predictive, or corrective, the right MRO interventions can make or break your uptime.
- Good MRO inventory management means fewer delays, fewer surprises, and better control over operational costs.
- Tools like CMMS and EAM software make it easier to stay on top of all maintenance activities and MRO-related considerations.
What is maintenance, repair, and overhaul (MRO)?
MRO is a wide category. It includes everything needed to make a product that doesn’t end up in the final item. That includes industrial equipment (pumps, motors, belts), consumables (cleaning and office supplies), and maintenance supplies (lubricant, gaskets, repair tools).
These supplies and equipment are used in three types of activities:
- Maintenance covers the routine maintenance work that prevents problems in the first place and increases lifespan. Scheduled inspections and proactive equipment calibration reduce the risk of unexpected breakdowns.
- Repair kicks in when something goes wrong. These disruptions could mean anything from fixing a jammed conveyor belt to replacing a worn-out motor.
- Overhaul is a full reset. This is when maintenance and repair aren’t enough, and you need to fully tear down and rebuild equipment or systems. Repair and overhaul situations tend to be expensive and involved, like revamping an entire production line.
Why MRO matters for operations and supply chains
Anyone who oversees operations or supply chains needs to be well-versed in MRO best practices. In these environments, even a small issue, like a snapped conveyor belt or missed safety inspection, can halt production and disrupt the entire operational lifecycle. Effective MRO is about minimizing these kinds of risks.
What are MRO products and materials?
MRO products and materials are essential items and supplies that are used in the day-to-day maintenance, repair, and operations of industrial or manufacturing facilities. Examples include spare parts, safety equipment, or cleaning supplies. These products are not directly involved in the production process, but they are crucial for keeping operations running smoothly and maintaining the physical assets of a business.
MRO products are critical for maintaining a safe, efficient, and compliant work environment. They are typically managed through an organized inventory system to ensure that they are readily available when needed for maintenance, repair, or operational tasks.
What are the types of MRO?
Industry experts typically divide MRO into four categories:
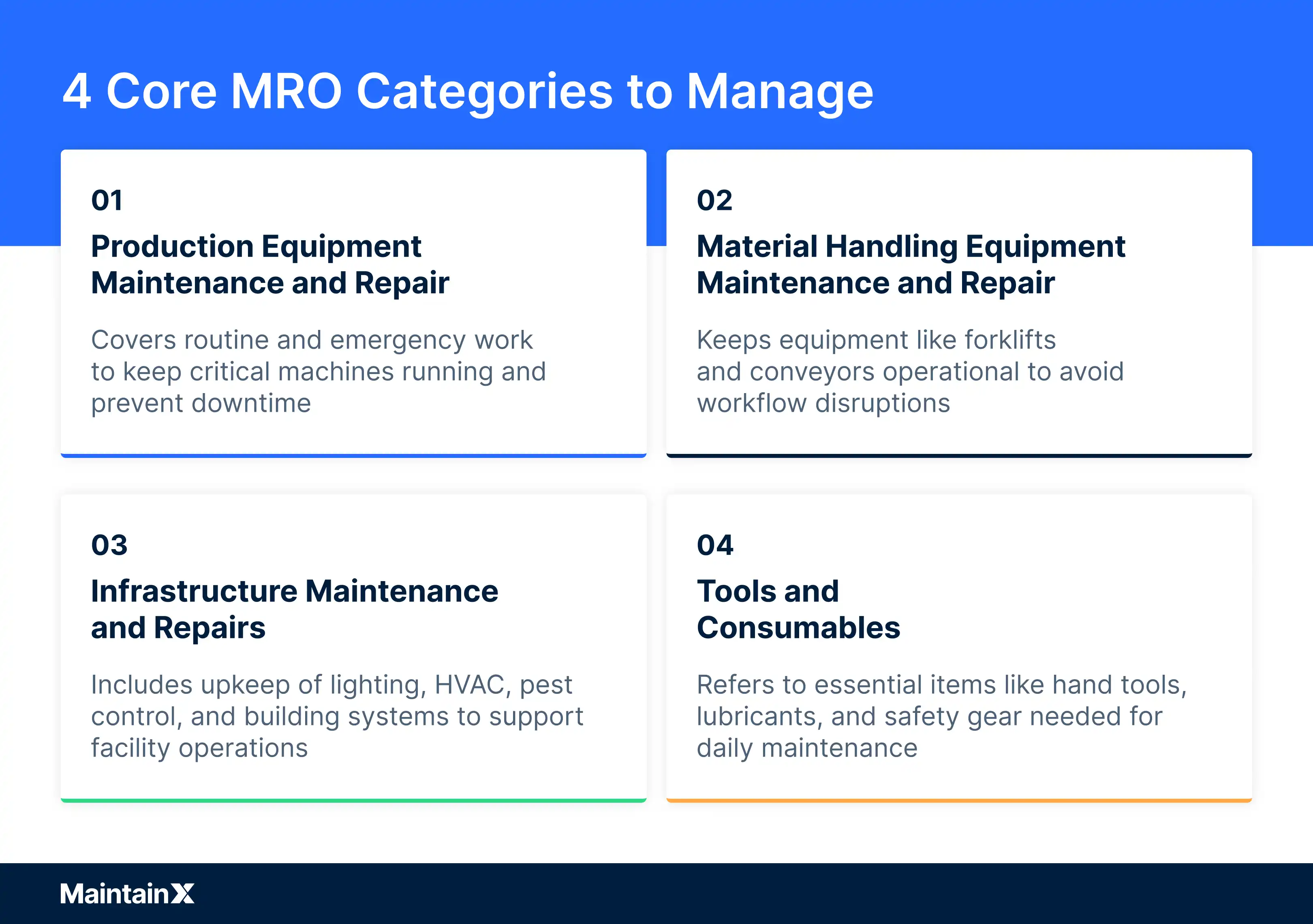
1. Production equipment maintenance and repair
This category of MRO focuses on the maintenance of critical assets and systems so that production isn’t disrupted. Over time, frequently used machines experience wear and tear, necessitating more frequent upkeep over time.
MRO activities related to production equipment include routine and emergency maintenance, the purchase of condition-monitoring equipment, replacement parts inventory management, and supplier management. Switching to proactive maintenance strategies such as predictive and preventive maintenance helps production facilities stay on top of maintenance and improve asset uptime, availability, and reliability.
2. Material handling equipment maintenance and repair
Material handling equipment includes different types of machinery, such as forklifts, storage systems, bulk containers, conveyor systems, robotic arms, and pallet positioners.
These items are essential for moving raw materials and components through production lines. They also help transport finished products to loading bays, where workers can ship them to customers. It’s crucial to ensure that material handling equipment remains operable to avoid idle time.
3. Infrastructure maintenance and repairs
Though not as immediately pressing, management must prioritize the upkeep of facility infrastructure. This type of maintenance includes cleaning services, lighting and HVAC systems servicing, pest control, grounds maintenance, and building maintenance.
Though not as immediately pressing, management must prioritize the upkeep of facility infrastructure. This type of maintenance includes cleaning services, lighting and HVAC systems servicing, pest control, grounds maintenance, and building maintenance. Regular attention to these areas helps optimize overall facility performance and longevity.
4. Tools and consumables
Finally, MRO includes hand tools and limited-use items needed to carry out maintenance and repairs. Examples of MRO tools and consumables include items like electric saws, pliers, safety gear, lubricants, adhesives, welding supplies, and even basic office materials. These items are usually small and can easily get lost in a large facility, so they need proper management, too.
What do MRO professionals do?
Different types of organizations have different MRO needs. Small businesses with relatively low MRO expenses, such as restaurants, resorts, and private practices, typically rely on a general manager to oversee all aspects of MRO.
Alternatively, large organizations like warehouses, manufacturers, and oil and gas companies often divide responsibilities amongst a team of professionals to ensure operations run smoothly. Essential roles within high-volume MRO facilities include:
Procurement officers
MRO departments often require dedicated MRO procurement personnel who have experience working with organizational items. They are responsible for assessing the suitability of suppliers, products, and services and negotiating contracts with suppliers. They also ensure businesses purchase high-quality and cost-effective MRO products.
Supplier relationship managers
Large organizations often require a specific manager to maintain relationships with suppliers. Considering that businesses need raw materials to produce deliverables for customers, maintaining reliable supply chains is paramount to success.
Though some suppliers are undoubtedly more important than others, most businesses source supplies from various sources. Supplier relationship managers identify “mission-critical” MRO items and secure iron-clad purchase order arrangements to ensure their organizations always have the materials they need to stay in business.
Inventory managers
Inventory managers are responsible for adequately stocking MRO items at all times. A large part of their responsibilities is overseeing the quantity levels of spare parts necessary for performing both preventive maintenance and corrective maintenance, as needed.
MRO inventory management is crucial to reducing unnecessary downtimes, delayed deliveries, and expedited shipping costs associated with emergency inventory orders.
Standards/compliance officer
Without proper controls, there’s always a risk of purchasing defective MRO items. In addition, companies must stay vigilant against procuring items from unauthorized suppliers who can’t guarantee quality control.
This is where a compliance officer steps in. This person can ensure that all MRO items are secured following compliance regulations and that no illegal items are purchased.
How to use technology to streamline MRO
Modern maintenance operations teams have a lot more software tools at their disposal than even a decade ago. Here's how you can incorporate technology to improve your performance.
Use a CMMS or EAM system
A Computerized Maintenance Management System (CMMS) or Enterprise Asset Management (EAM) platform centralizes all your maintenance data. Think of these systems as your one-stop-shops for all things MRO where you can schedule preventive maintenance, track work orders, monitor inventory, and see how operational costs are trending over time.
Increase real-time tracking and work order visibility
New tech tools are making it easier than ever to stay on top of all aspects of MRO. Real-time monitoring, for instance, helps maintenance teams pinpoint and resolve issues faster than they otherwise could with a manual approach. And with a platform like a CMMS, you can view open work orders, task progress, and team activity all in one place.
Improve data reporting, forecasting, and cost control
Along with helping you keep track of all MRO-related moving parts, modern tools also produce lots of valuable data. The best teams don't let it go to waste. They use it to analyze spending patterns, forecast upcoming inventory needs, and flag areas where maintenance costs are creeping up. Feeding that data into predictive analytics tools also helps spot early warning signs of equipment failure, so teams can act before anything breaks.
Keep your MRO program moving forward
The whole point of MRO is to keep production moving swiftly and efficiently. But too many teams pay little attention to the systems they use to manage MRO. They rely on paper checklists and disparate spreadsheets to keep track of dozens of interconnected processes, which inevitably leads to confusion and missed steps.
A CMMS provides all the functionality MRO teams need to keep production moving, including predictive maintenance tools. But not all providers and platforms are created equal. But not all platforms are created equal. Check out our guide to learn more about how these systems work.
Not quite. Repair usually involves fixing specific faults or replacing broken parts. Overhaul is more comprehensive, often involving disassembly, inspection, and rebuilding to restore the equipment to like-new condition.
A factory worker replacing worn-out bearings on a conveyor belt is an example of MRO in action. Those bearings don't make it into the final product, but they're necessary for the product to actually be made.
The aviation business is packed with routine inspections, and for good reason. All the equipment, supplies, and activities required to ensure aircraft are safe and working properly fall under the MRO umbrella. That includes swapping out brake pads, checking fluid levels, replacing hydraulic lines, and making sure ground crew support gear is ready to go.
See MaintainX in action