Of the many metrics by which you’ll judge your manufacturing processes, your bottom line is probably the most important to you, and optimizing this requires understanding your manufacturing overhead costs. Increasing or improving your profitability depends on how much you spend on manufacturing.
Of course, manufacturing involves all kinds of costs, from costs incurred during the manufacturing process to transportation costs, among others. Manufacturing overhead refers to indirect costs a company or manufacturer incurs during production. These manufacturing overhead costs are called indirect costs because it’s hard to trace them to each product.
Direct costs are, as the name suggests, directly incurred as a result of production. These include the cost of labor and raw materials that go into the actual production.
On the other hand, indirect costs are due to elements not actively used during production but necessary for production anyway. They include spending on utilities and facilities and depreciation. These are manufacturing overhead costs. Other indirect costs exist, like administrative costs and legal fees, but are not considered manufacturing overhead expenses.
Examples of Manufacturing Overhead Costs
This is far from an exhaustive list, but a few common overhead expenses in manufacturing include:
Maintenance Costs: Spending on regular maintenance activities. These could be repairs, machine work, or even cleaning and janitorial activities for the manufacturing facility.
Materials Costs: Specifically indirect materials. Materials that aren’t used directly when manufacturing but are part of regular maintenance activities (such as cleaning materials, lubricants, etc.) fall into this category. Spending on direct materials, such as raw materials, that change based on the production volume does not count as overhead.
Property Fees: Fees spent on the manufacturing facility, such as rent, mortgage, and property taxes.
Utilities: This includes the cost of electricity, water, gas, and other utilities that power the manufacturing process.
Wages and Salaries: These include indirect labor costs for employees not directly involved in the production process. They include facility managers, production managers, janitors, quality control officers, and so on. Direct labor costs do not factor in here.
Manufacturing overhead is also known as factory overheads or manufacturing support costs. Overhead costs such as general administrative and marketing costs are not included in manufacturing overhead costs.
Types of Overhead Costs
In general, costs can be direct or indirect, and overhead costs are indirect costs. But even these indirect costs fall into three subcategories: fixed overhead costs, variable overhead costs, and semi-variable overhead costs.
Fixed Overhead Costs
These fixed costs remain the same regardless of the company’s scale of production. Whatever quantity of goods the company produces, these overhead costs do not change.
Examples of fixed overhead costs include rent and property taxes. Whether two goods are produced within a year inside a factory or a hundred goods are produced, the rent is static. Routine maintenance costs would also fall under this category.
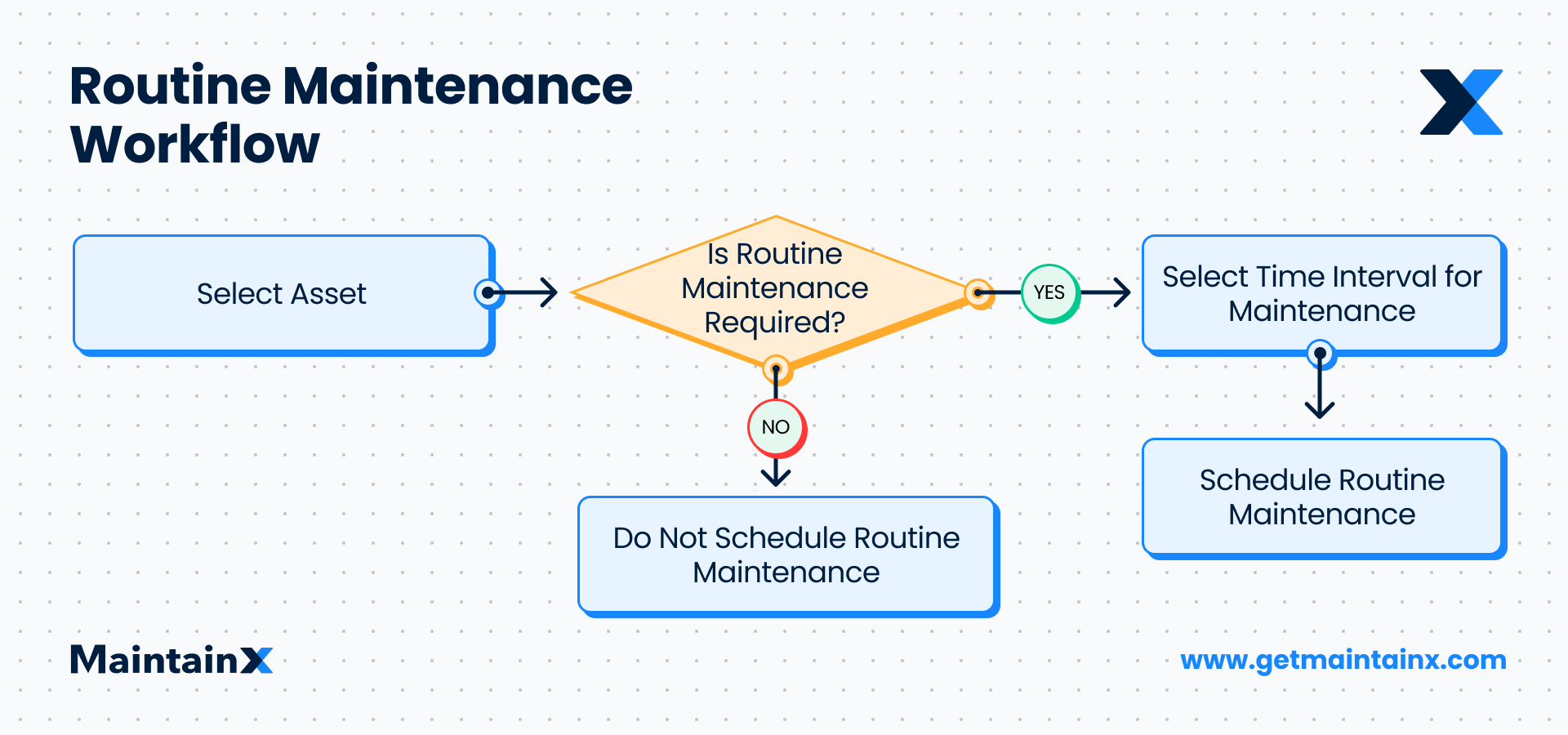
Variable Overhead Costs
Unlike fixed overhead costs, variable manufacturing overhead costs depend upon the scale and size of production. Therefore, a higher output volume leads to a higher amount of variable overhead costs.
Producing more goods means running manufacturing equipment for a longer amount of time, which often means increased utility costs. Electricity, water, and fuel costs all fall in the variable category.
Semi-Variable Overhead Costs
These costs are sometimes fixed and sometimes variable. They remain the same at certain stages but increase based on production output. So, for example, insurance rates will typically include a base rate, with premiums then based on factors like performance.
Why Does Manufacturing Overhead Matter?
As we’ve stated, manufacturing overhead is a fundamental factor when calculating or working toward profitability. As a manufacturer, you can calculate this overhead for every product. This helps you determine the unit price for the finished goods to ensure you see the returns you want.
In addition to determining the cost of goods sold, manufacturing overhead helps companies manage their spending. It’s easy to make the mistake of focusing only on the direct manufacturing costs like materials and labor. Understanding your overhead will give you a clearer view of how much money you’re spending. This will also help determine your budget allocation and schedule your operations.
Generally Accepted Accounting Principles (GAAP) indicate that manufacturing overhead should be added to the cost of direct materials and labor when determining the Cost of Goods Sold (COGS) and the inventory value. Therefore, each of these figures must be reported on both the balance sheet and income statement.
To achieve full GAAP compliance, you must allocate a portion of overhead to every item produced by an organization.
How to Calculate Manufacturing Overhead
The first step is to figure out all your costs. First, make an extensive list of all your spending, big and small. Then, from this list, identify your direct and indirect costs. Once you do this, you can sum up the total costs and then calculate your overhead. There are multiple formulas for calculating the overhead, depending on whether you want to look at your total overhead or your manufacturing unit overhead.
The formulas are:
- Manufacturing overhead = Total manufacturing overhead / Total number of units produced
- Manufacturing overhead = Fixed manufacturing overhead + Variable manufacturing overhead / Number of units produced
How to Calculate Your Manufacturing Overhead Rate
Manufacturing overhead percentage is your manufacturing overhead cost expressed as a percentage of your company’s total revenue. The percentage gives you a sense of how much of your income you spend on overhead over set time intervals or accounting periods. To calculate the overhead rate in, say, a month, divide your total overhead costs for one month by your total monthly sales and multiply it by 100.
MOR Formula:
Manufacturing Overhead Rate = Overhead Costs / Sales x 100
For example, if your total manufacturing overhead is $10,000 and your total sales in a month amount to $50,000, then your overhead rate will be: (10,000/50,000)x100 = 20.
This means 20% of your income goes towards overhead. With this, you have a good picture of your margins and can better organize your manufacturing to get closer to your financial goals. Remember that manufacturing overhead expenses must also be included in your cost of goods sold (COGS) that is listed on the income statement.
Get a CMMS to Help Calculate Manufacturing Overhead?
Keep Track of Your Financial Health
A CMMS can help you get a clear picture when organizing your financial statements by keeping track of your data. In addition, a Computerized Maintenance Management System helps you maintain a broad view of your entire operations. As such, you can always turn to your CMMS tool for records regarding your spending over an accounting period. Forget needing to add additional pages to your Excel balance sheet.
If your team is using your chosen CMMS right, you’ll be able to see all your purchase orders, inventory spending, and any other financial costs involved in running the facility. In addition, knowing the costs of production and your factory overhead will help you get an accurate picture of your overall financial costs.
Establish and Automate SOPs for Your Manufacturing Unit
As there are many ways to calculate manufacturing overhead, you’ll need to keep track of different kinds of data. Whatever formula you decide is best for you and your facility, use a CMMS to establish and automate standard operating procedures for which data to track and store.
Monitor Data over Time
With a CMMS, you can monitor your facility’s performance over time. For example, you can track machine hours, labor hours (direct and indirect labor hours), and spending on direct and indirect expenses. If you’re trying to improve your manufacturing overhead rate, for example, keeping a close eye on this data will help you identify what efforts are working.
Track Your Manufacturing Overhead with MaintainX
MaintainX is a CMMS system that helps centralize your documents and data. For example, with MaintainX, you can keep track of purchase and work orders in your facility, establish SOPs for calculating overhead, and track historical data regarding your overhead rates. Try MaintainX today!
See MaintainX in action