If you run a business, you may have heard about a quality management system (QMS) and asked if you should invest in QMS software. Do you remember those occasional headlines you read about major recalls costing companies billions? A QMS can help avoid those mistakes.
Of course, suppose you want to control quality. In that case, you need a robust manufacturing process, sound decision making, well-trained workers, and the right equipment to avoid recalls and other quality mishaps. The American Society for Quality (ASQ) estimates that an average company spends 10% to 15% of its operational expenses on maintaining quality.
So let’s look at what a QMS is and how it can help you steer clear of quality disasters.
What Is a QMS?
A QMS system includes documents, standard operating procedures (SOPs), and policies your business needs to manufacture and deliver excellent quality products and services.
Gartner defines a QMS as “The business information management system that manages quality policies and standard operating procedures (SOPs).”
The information you store in the QMS may include a quality manual and documents, customer requirements, auditing controls, industry-specific regulations, and ISO requirements.
While you need to configure a QMS specifically for your needs, the system must include essential elements from the start. The International Organization for Standardization’s Quality Management System Requirements, ISO 9001:2015, provides the guidelines to standardize QMS design.
How to Design a QMS?
Designing a QMS involves documenting the policies and procedures of your quality system. You need an overall direction and sustainable workflows to achieve your company’s quality system. You will need to set goals, quality processes, and procedures to help you achieve your quality goals and standards.
Quality Policy
The quality policy is a top-level QMS document that drives the rest of the system toward your quality goals. It keeps your procedures in line with your goals. For example, if you want to build a reputation as a brand with high-quality standards, you should be working on exceeding customers’ expectations. Creating a robust policy is the first step to implementing quality assurance.
Quality Procedures
Quality procedures provide the framework to achieve the goals of your quality policy. For example, you should establish an extensive quality control procedure if your goal is to exceed customer expectations. You may also need to create a preventive maintenance plan to ensure your equipment runs smoothly and at peak performance.
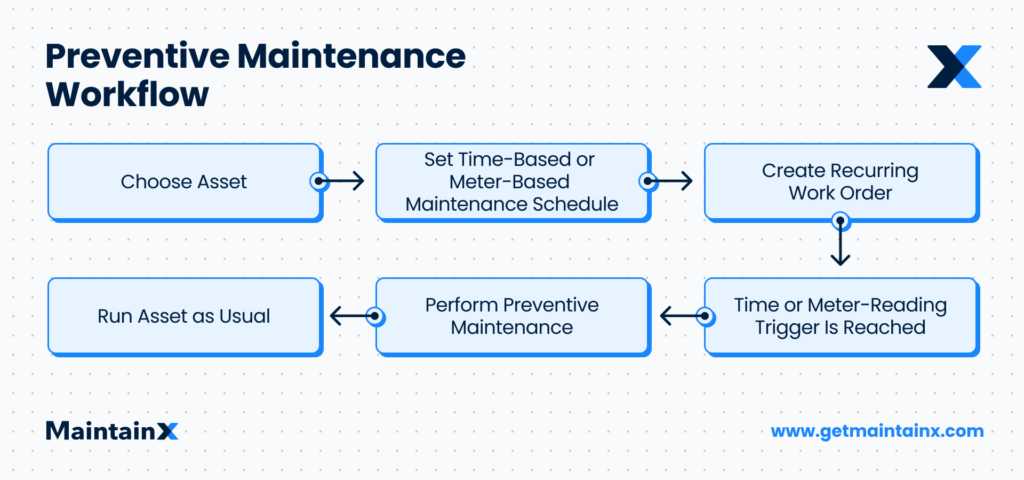
Procedural Guidelines
Procedural guidelines are a set of instructions for employees. You’ll need to create SOPs for each task that influences product quality. The SOPs should be accessible to employees at all times. Instead of using physical documents or an Excel sheet, use a CMMS like MaintainX. By the way, MaintainX’s Global Procedure Library houses adaptable standard operating procedures that you can integrate into your QMS.
A CMMS enables operational managers to digitize SOPs. Automating SOPs goes a long way to streamlining document management. For example, managers can issue work orders from within the CMMS with SOPs attached, and workers from the factory floor or in the field can access the work orders in real time from their mobile devices. The digital work orders can also include guidelines and additional context by adding checklists, notes, safety guidelines, and photographs.
Audit Trail
You need to log data for all quality control procedures for internal (and external) audits. Auditing helps you find room for improvement and things you need to achieve your quality goals. However, recordkeeping is resource-heavy when you input data manually. A CMMS, however, can automate recordkeeping and improve data management. For example, as your teams complete work, the CMMS automatically logs details about each quality-related task performed under a specific work order. This CMMS audit trail can also show regulatory compliance during an inspection.
How to Implement a QMS?
On the one hand, using quality management software can go a long way. On the other hand, you need to design your own QMS based on your specific business processes, objectives, product, and services. Regardless, you’ll need to identify and manage factors and processes influencing customer satisfaction. The four stages of implementing a QMS include the following:
1. Design
In this stage, you develop your QMS by creating an overarching policy and quality objectives. Here, you establish your SOPs, guidelines, and a recordkeeping mechanism.
2. Execute
Train your teams about best practices, efficient ways to use the QMS, and QMS metrics to track. At this step, you must emphasize how crucial it is that employees adhere to the QMS policies and procedures.
3. Audit
Over time, you’ll want to see how your QMS performs. Is it helping improve customer satisfaction? Are you reducing defective production? Are you increasing asset lifecycles? The specific metrics to track may differ among organizations. Remember that with data reporting, the strength of your data collection determines the accuracy of the metrics (KPIs) you receive back.
4. Improve
If you need better quality or nonconformance with your QMS goals, take steps to improve. For example, consider providing additional training to team members to help them better understand the QMS policies and procedures.
“Continuous improvement can support a business’s strategy in many different contexts. In our Organizational Health Index (OHI) of almost 2,000 companies, 38 percent of companies pursuing a continuous improvement culture were doing so in a turnaround context. But the other 62 percent were pursuing continuous improvement as a means of moving from good to great.”
McKinsey
Four Approaches to a QMS
You can manage quality in the following four ways:
1. ISO Certifications
You can meet one or more quality standards to improve your product’s credibility. These certifications are also a regulatory requirement in some industries—for example, FDA regulations for manufacturers of medical devices. Because ISO certifications involve extensive audits, your QMS will indicate the procedures you put in place to ensure excellent product quality. Examples of ISO standards include ISO 9000/9001, ISO 13485, and ISO 17025.
2. Total Quality Management (TQM)
TQM involves identifying and eliminating manufacturing errors, optimizing the supply chain and customer satisfaction, and providing employees the training to maintain high quality and standards. The TQM approach encourages all employees at your company to participate in improving the quality of its processes, products, and services.
3. Continuous Quality Improvement (CQI)
CQI is often used along with another QMS approach. It’s based on the Japanese concept of kaizen, which encourages minor, incremental improvements. CQI encourages teams to strive for small improvements, quality, and customer satisfaction over time.
4. Six Sigma
Six Sigma is a data-driven approach that involves five actions: define, measure, analyze, improve, and control. Major companies like General Electric use Six Sigma to ensure product quality.
Let MaintainX Simplify Your QMS
MaiintainX is a CMMS system that helps centralize QMS documents and data. As the only work order software with chat, you can collaborate on quality procedures from your desk, the factory floor, and the field. The person performing the quality procedure can contact the manager and get clarification within seconds.
Using MaintainX for quality management ensures you are creating an audit trail as you work. QMS on a CMMS also makes it easier for continuous improvement, better document control, and sustained risk management easier. If that sounds interesting, try MaintainX today. Our goal is to make work smarter, not harder.
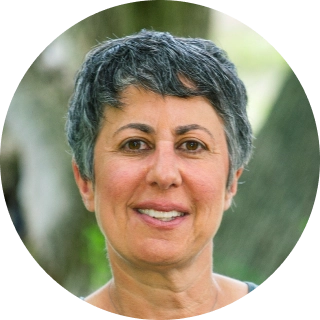
Caroline Eisner
Caroline Eisner is a writer and editor with experience across the profit and nonprofit sectors, government, education, and financial organizations. She has held leadership positions in K16 institutions and has led large-scale digital projects, interactive websites, and a business writing consultancy.
See MaintainX in action