Verification and validation are two crucial components of ensuring the quality of a manufacturing process. However, they aren’t as interchangeable as their names suggest. Instead, crucial differences exist between them. To start, let’s consider what both of these concepts mean.
Process Validation
According to the Food and Drug Agency (FDA), process validation is “the collection and evaluation of data, from the process design stage through commercial production, which establishes scientific evidence that a process is capable of consistently delivering quality products.”
The point is to ensure that a process that leads to one quality product can be repeated consistently at the same level. Sure, you might be able to produce a high-quality finished product under one set of circumstances, but what if you need to make changes at some point?
For example, change the assets you use or scale up your production. How do you ensure you don’t compromise quality? First, you need to have collected and evaluated data through all stages of the manufacturing process. And then apply it throughout the product lifecycle.
Process validation uses objective evidence to establish that the process is repeatable and, importantly, to figure out how it is repeatable. The process helps test variability to ensure that varied inputs will continue to yield consistent product quality.
Process Verification
Process verification is the process of confirming that your teams have fulfilled specific requirements during manufacturing. It involves examining and evaluating processes and products to ensure that they fit with specific outlined parameters. These parameters may be regulatory specifications. Like process validation, it also involves a lifecycle approach: from design to product development to production. Whether you’re producing a remote control or a medical device, you likely have regulatory requirements to meet. (Check out the FDA requirement for Process validation: FDA QSR 21 CFR part 820.75.) If these requirements include product specs and quality attributes, then process verification helps ensure that you’re producing your product correctly.
Stages of Process Validation
To dig a little deeper into the differences between the two, let’s consider the three stages of process validation.
- Process Design
- Process Qualification
- Continued Process Verification
1. Process Design
As the name suggests, you have already laid out and designed the manufacturing process before you start manufacturing. You need to have defined exactly how you intend to approach your manufacturing. In this stage, you might be using already existing processes and flows or designing new ones from scratch. Process design moves from process development to production. It involves:
- Risk assessment
- Experiments and/or demonstrations
- All other product development processes
You’ll also be creating process design documents like:
- Block Flow Diagrams (BFD)
- Process Flow Diagrams
- Piping and Instrumentation Diagrams
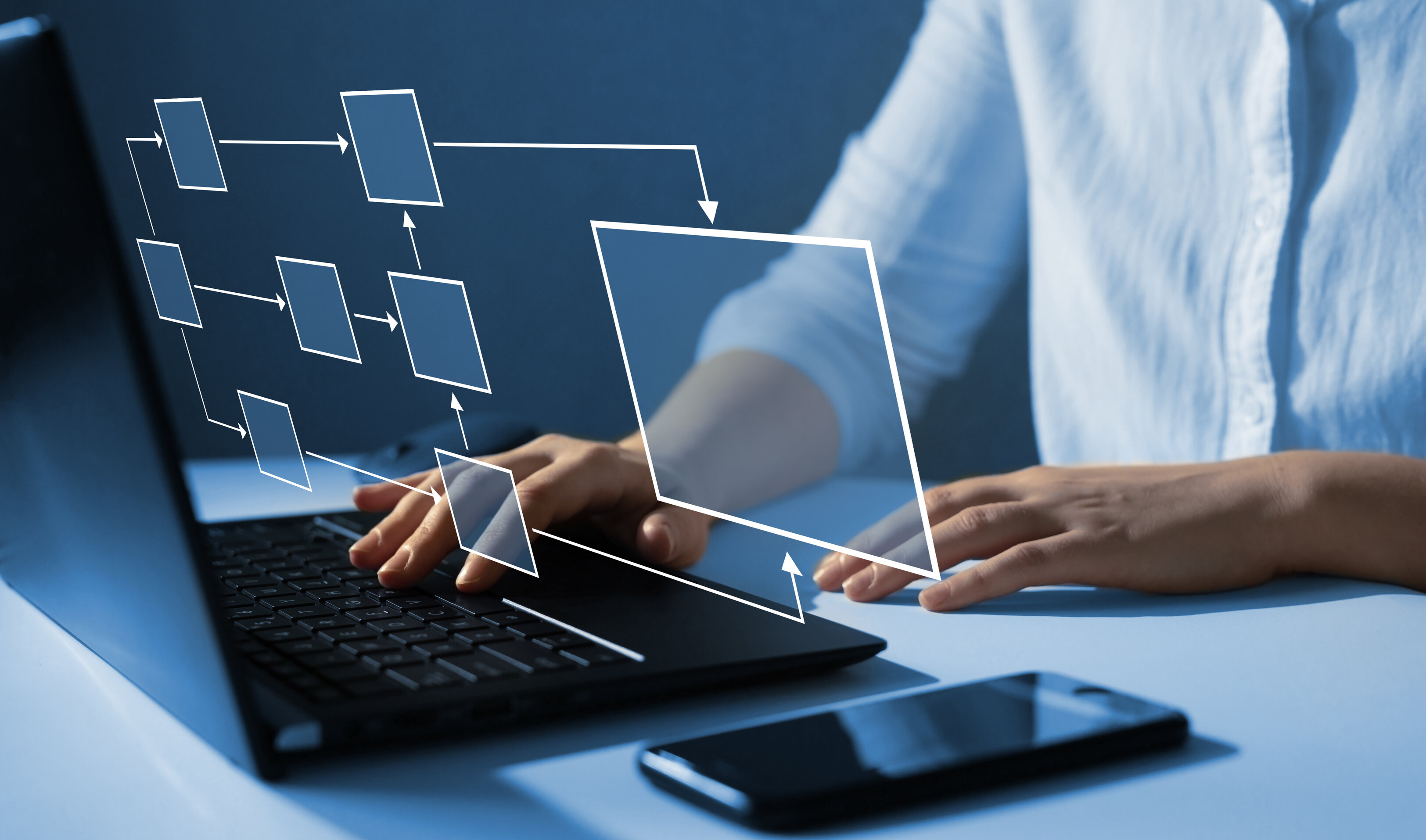
2. Process Qualification
This stage involves reviewing your design from the previous stage. Does it fit the goals of your entire process? Is it repeatable and reproducible? Can you maintain this level of quality management? Here, you’ll be verifying and evaluating all your processes and manufacturing equipment to ensure the quality of the potential output, especially for commercial manufacturing. In essence, you need a detailed approach that you can standardize.
First, you’ll want to ensure your manufacturing facility is built in line with current good manufacturing practices. Then you’ll want to carry out installation qualification: making sure you have installed your manufacturing assets in alignment with those specifications.
Installation Qualification: “Establishing confidence that process equipment and ancillary systems are compliant with appropriate codes and approved design intentions, and that manufacturer recommendation is suitably considered.”
CIQA
Then, you’ll carry out process performance qualification. Here you’ll want to consider critical quality attributes and process parameters. To maintain solid process control throughout, you need to document details such as:
- Sampling plans
- Data collection metrics
- Product testing plans and methods
- Specifications for production batches
3. Continued Process Verification
Once you’ve completed the qualification process, you can begin production. Continued process verification takes place throughout the production process. It is an ongoing quality assurance system to ensure all processes remain in control and involve maintenance practices.
As you’ve probably realized, process verification in practice is part of an overall process validation system. Pharmaceutical manufacturing and medical device manufacturing use this practice extensively. They are recommended (and, in some cases, mandatory) processes according to the guidelines of the FDA and the International Medical Device Regulators Forum (IMDRF).
Types of Process Validation
Process validation can be classified according to when teams carry out checks and what their purpose is. The types include:
1. Prospective Validation: This refers to validation activities carried out before commencing routine production. You should do this before you manufacture the product with a new formula or in a new factory.
2. Retrospective Validation: As the name suggests, this is the kind you carry out after manufacturing. It’s done when the manufacturing process is complete without undergoing a documented validation.
3. Concurrent Validation: Manufacturing teams carry this out during regular production. The goal is to make sure the level at which the manufacturing process begins is maintained throughout.
4. Revalidation: This is usually carried out on medical devices. It is necessary when prospective validation has been carried out, and the results suggest quality might need to be maintained consistently.
5. Periodic Validation: Teams regularly evaluate the process to check it is working according to the original design.
Validation, Verification, and Maintenance
A robust maintenance plan is a vital part of the verification and, by extension, validation processes_._ For continued process verification to work, companies must carry out preventive maintenance on assets and facilities. In addition, you need to ensure that your team has set all required specifications and calibrations to maintain consistency.
Try MaintainX to Ensure Validation and Verification
We think you should consider implementing Computerized Maintenance Management Software (CMMS) to ensure process validation and verification run smoothly. A robust CMMS like MaintainX can help streamline your validation activities by:
- Standardizing your validation process
- Guiding workers through validation activities
- Automating validation data collection
- Analyzing data from production batches
- Tracking quality system consistency over time
- Communicating regulatory requirements
See MaintainX in action