Maintenance work order forms outline the maintenance tasks a technician needs to perform. Standardized forms brief technicians about problems so they can deal with asset-related issues quickly. In such cases, maintenance work order forms are part of reactive maintenance when addressing a particular issue. Work orders are also essential because they can list and identify safety issues, OSHA regulations, and priority levels.
NOTE: A work order form is the same as a work order.
However, work order forms are also vital for preventive maintenance. Preventive maintenance is a maintenance approach that aims to keep assets in good working condition through routine upkeep activities. These routine activities should identify and address minor problems before they become major ones.
Maintenance departments can prevent breakdowns and reduce unplanned downtime by ensuring equipment remains in good shape. In preventive maintenance, work order forms outline the necessary activities that form part of an organization’s maintenance routine.
This post explains what you need to know about a maintenance work order form and how to use one.
What Is a Work Order Form?
Work order forms inform maintenance technicians about an asset that needs attention. A maintenance work order form is also known as a maintenance job order, maintenance service request, and maintenance ticket.
The form includes details about the problem and other information a technician needs to start maintenance work. Work orders help elicit faster responses from technicians and minimize the mean time to repair. As a result, you’ll be able to reduce equipment downtime and improve productivity.
Most modern businesses use work order software like computerized maintenance management systems (CMMS) to create work orders. A CMMS can streamline the entire workflow. Creating work orders with a CMMS allows you to provide all the necessary information to ensure technicians carry out tasks properly. In addition, assigning, scheduling, and prioritizing work orders is easier with a CMMS. Automating work orders on a robust CMMS like MaintainX also facilitates technician collaboration. MaintainX is the only CMMS with in-app chat, allowing techs to comment on work orders in progress.
What to Include in a Maintenance Work Order Form
Maintenance work order forms should provide technicians with all the necessary details to perform a maintenance task. In fact, the right work order management software requires specific fields to be populated so that techs have all the information and instructions necessary to complete tasks on time. The work order should contain at least the following information.
Work Order Requestor
The person working on the maintenance task may have questions or need additional information. Therefore, the technician should know who made the work order request.
Was it the maintenance manager, floor manager, or another technician? Knowing who made the request and having access to their contact information helps the tech get in touch and save time tracking down the right person.
This is especially useful when using digital work orders in chat-enabled CMMS apps. Employees can tag other colleagues, comment on the work order, and chat directly to seek necessary clarifications.
Maintenance Problem
The technician needs to know the problem, when and how the problem occurred (if known), and possible causal factors. The person filling out the work order form can add notes linking to similar issues with the asset in the past and how the asset was fixed to reduce troubleshooting time.
With a CMMS, you can simply look up an asset’s maintenance history. Maintenance teams can further simplify this process by scanning QR and bar codes. A CMMS with the right functionality allows users to scan these to look up useful asset information like maintenance history, service instructions, etc.
With a robust CMMS, you can also add a picture of the problem requiring maintenance. You can also attach a PDF of the manufacturer guidelines to provide more context about the type of maintenance or repair work and the tools and parts needed.
Asset Requiring Maintenance
When it comes to maintenance workflows, if you have multiple similar assets across the shop floor and even at other locations, technicians need to know exactly which asset at what location needs work.
Digital codes play a useful role here. With bar codes placed on equipment, you can simply scan the code on your mobile device, and your CMMS will automatically find the equipment’s location. Think about how helpful this is for property management, with lighting and plumbing across buildings, floors, offices, etc. However, for fleet maintenance, you may need GPS or similar asset-tracking devices for your vehicles.
Managing Maintenance Work Orders and Requests
Digital work order forms can replace hardcopy documents, maintenance work order books, and generic paper work order slips.
We recommend integrating a computerized maintenance management system to manage work order request forms and work orders effectively. This is especially true if you have many assets and frequently assign maintenance and other work orders.
To organize repair work orders, we recommend the following:
Creating a Work Order Form Template
MaintainX offers ready-to-use work order templates for all types of work orders. Using a well-done work order template makes it easy for technicians to find the information needed to execute and complete maintenance tasks.
However, many companies download free templates to create printable MS Excel or MS Word work order templates. However, maintaining paper maintenance records takes a lot of work and makes audits difficult. They can get lost or unfiled, making them fairly useless for recordkeeping.
Think about it: no matter your industry or use case, you can create plumbing work order templates, shop work order templates, and any other job work order forms all set and ready to go when maintenance requests come in. MaintainX users create repair work order forms, maintenance work order forms, service work order forms, business work order forms, and general job work order forms, all based on one of our sample work order form templates.
Using a CMMS like MaintainX to issue real-time work orders can streamline your workflow. MaintainX automatically centralizes work orders, so you don’t have to deal with bulky paperwork or manually sift through piles of paper during an audit.
Making Collaboration Easier
Technicians often need additional information or have questions. Providing them with the necessary information helps them complete tasks faster. Traditional companies rely on phone and text messages, but you won’t need them when you use MaintainX.
MaintainX is the world’s first CMMS to offer a built-in chat. When technicians have questions, the technician can use their mobile devices to chat with others directly from the work order in MaintainX. This way, the technician doesn’t waste time returning to the office to ask questions or find a team member.
Using a Digital Solution
No matter your industry—from manufacturing to facility management to automotive—using a digital solution helps ensure your technicians don’t commit mechanical errors. For example, you can issue work orders with the tap of a button using a CMMS. When you issue a work order form, technicians are notified immediately. You can include procedures, graphics, and notes along with the work order. Technicians can mark completed tasks as they move through a procedure. You’ll have complete visibility over the work order’s progress.
Standard operating procedures (SOPs) also provide robust guidance for technicians to complete tasks more efficiently and effectively. Seek out a CMMS app that provides templates to simplify the SOP process. MaintainX CMMS features a global procedure library, housing procedures, manuals, and templates across industries and equipment to improve user maintenance, safety, and operations.
Why You Need a CMMS
A CMMS with maintenance work order templates helps ensure your preventive maintenance tasks run effectively and efficiently. MaintainX templates help you collect and share all the necessary details about work requests, including a description of the work, maintenance history, due date, completion date, and any other additional information.
By automating your preventive maintenance, your teams know exactly which equipment needs maintenance and why. When you use a CMMS, you won’t need someone to constantly monitor each preventive maintenance program step. All data is automatically logged in the CMMS for accurate real-time KPI and metric analysis.
Automate Your Work Order Forms with MaintainX
With MaintainX’s reporting features, you can gain insight into your past activities, identify areas for improvement, and streamline your work order management. As a result, you’ll save money on asset repairs and minimize downtime. The ROI of those benefits alone justifies your investment in a CMMS.
MaintainX offers third-party vendor integration, allowing staff members to order from vendors directly within our app. This feature helps ensure maintenance teams always have the necessary tools and parts for preventive and corrective actions.
Ready to automate your maintenance workflows? Try MaintainX today.
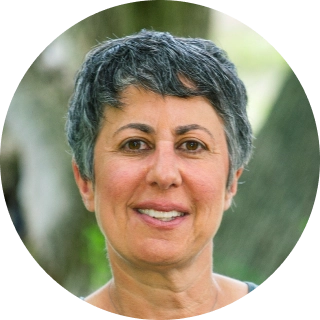
Caroline Eisner
Caroline Eisner is a writer and editor with experience across the profit and nonprofit sectors, government, education, and financial organizations. She has held leadership positions in K16 institutions and has led large-scale digital projects, interactive websites, and a business writing consultancy.
See MaintainX in action