Maintaining accurate manufacturing data is critical for compliance, especially if you’re in the life-sciences industry. As a result, the U.S. Food and Drug Administration (FDA) established ALCOA principles for collecting data and maintaining data integrity.
This post explains the meaning of ALCOA and what your company should consider implementing to comply with these guidelines.
No matter what, we always recommend developing good documentation practices at your company. A CMMS will help you complete compliance work by automating and digitizing your company’s ALCOA-required data collection.
What Is ALCOA?
ALCOA is a set of principles that governs data integrity (see 21 CFR Part 11), published by the FDA in December 2018. ALCOA stands for Attributable, Legible, Contemporaneous, Original, and Accurate.
Abiding by these principles when setting up and monitoring your data management system ensures that the data it collects is accurate. These principles also ensure you correctly follow the guidelines required to stay GMP compliant.
The FDA has extended the ALCOA principles over the past few years in response to the evolving manufacturing landscape. In 2010, the FDA added Complete, Consistent, Enduring, and Available (CCEA) to ALCOA. These days, ALCOA-CCEA is more commonly known as ALCOA-C or ALCOA+.
What Are the Nine ALCOA+ Principles?
Just knowing what the acronym ALCOA means and the principles it includes doesn’t tell you much about how to ensure your company’s data integrity. So, here’s what each of the ALCOA principles means:
1. Attributable
The data must be attributable to a date, time, and source. The source can be a person, device, or system that collected or generated the data. Attributable data points provide manufacturers and regulators context during analysis or an audit.
While attribution is a normal part of most digital tools, your internal standard operating procedures could lead to inconsistencies. For example, say you have one account for your entire testing team to log test data. Your digital tool will attribute all the data to that single account. This means it won’t attribute the data to any one person on the team, which ALCOA principles require
2. Legible
Manufacturers traditionally maintained data on paper. Even today, some small manufacturers use paper as a primary method for maintaining records. Unfortunately, physical records are prone to several risks, including illegible handwriting, being filed incorrectly, and, worst of all, getting lost or tossed.
Modern manufacturers maintain electronic data. They use tools like a computerized maintenance management system (CMMS) to digitize and automate data collection to ensure accuracy.
However, even digital records can still have a legibility issue. Avoid using uncommon words or language, which may make interpreting the data difficult for a person in the future. Instead, consistently use simple language across data.
3. Contemporaneous
Recording should occur contemporaneously with actions that generate data. Time stamping is built into most data management systems, but you still need to take care of a few loose ends.
For example, ensure tasks don’t queue up when the system is trying to record tasks for accurate time stamping. Also, check that you’ve set the clock in your systems to the correct time standard and in the correct time zone. Time stamping is one of the most important ALCOA principles.
4. Original
Keep the original records, not copies. Maintaining original information is primarily a concern for manual recording. For example, an employee may copy down data on a clipboard with plans to copy it to the primary record later. But that information never makes it to the original record. Obviously, the original record, whether paper or digital, is incomplete.
5. Accurate
The data needs to be accurate and error-free. The original data should exist in an unmodified condition to avoid any loss of accuracy. If changes are needed, take steps to document them. Avoid deleting data permanently.
Of course, this is easier with a digital system than with manual recording. Select a digital data management system with built-in accuracy and verification controls.
6. Complete
Recorded data should always have an audit trail that verifies no data was deleted or lost. Also, the audit trail needs to include records of modifications and all relevant timestamps.
7. Consistent
Consistency refers to logging data sequentially. Data should be in chronological order, along with dates and timestamps. Also, any data modifications need timestamps to show your company logged changes chronologically and with timestamps.
8. Enduring
ALCOA+ strongly emphasizes the need to maintain records for the long term. A cloud-based digital system is the best way to preserve data for years.
As a result, you need a system with excellent security to prevent data breaches. Moreover, you also need a data backup system, a disaster recovery plan, and a power backup to protect your data for the long haul.
9. Available
You need to make sure your data is easily accessible. A CMMS, like MaintainX, makes finding data easy. Indeed, it won’t matter if you have followed all the other ALCOA principles if you can’t find
MaintainX, for example, provides robust search and filtering features. Searching for data on paper-based records can be a nightmare, especially when the volume of data is large. Digitized records make data more accessible.
Use a CMMS to Maintain ALCOA Data Integrity
If you’re still using paper records, following ALCOA+ guidelines will be tedious. Also, you may find fat finger errors or missing data points. Using inaccurate data sets leads to poor insights and penalties for not complying with GMP and other regulatory requirements.
Automating data collection with a CMMS like MaintainX enables you to streamline data collection and management. Only choose a CMMS that date and time stamps all data entry. You’ll spend less time on data-related tasks and eliminate the risk of human error. If automated data collection sounds interesting, try MaintainX today!
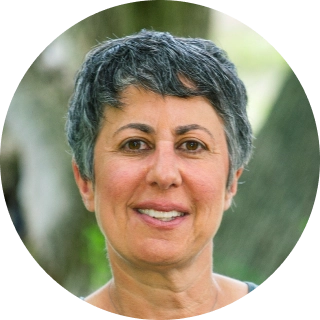
Caroline Eisner
Caroline Eisner is a writer and editor with experience across the profit and nonprofit sectors, government, education, and financial organizations. She has held leadership positions in K16 institutions and has led large-scale digital projects, interactive websites, and a business writing consultancy.
See MaintainX in action