This post explains the meaning of ISO 9001, what an ISO 9001 QMS means, the seven quality management principles outlined in the ISO 9001, and how you can implement the ISO 9001 quality standard.
The ISO (International Organization for Standardization) 9001 standard describes how to perform a task—manufacture a product, render a service, or work on any specific process—while ensuring high-quality output.
What Is ISO 9001?
ISO 9001:2015 is the latest ISO standard that outlines quality management standards. This international standard is the most popular ISO 9000 standard and the only standard for which you can get a certification. The standard prescribes requirements for manufacturers to create a consistent, process-driven approach to quality management and improvement.
The ISO quality management system standards are helpful when a business:
- Needs to comply: Some industries are compliance-heavy. In these industries, manufacturers need to meet regulatory requirements for products and services through effective quality management.
- Wants to improve customer satisfaction: You might implement the ISO 9001:2015 standards to exceed customer expectations and increase brand value.
ISO 9001:2015 requirements are generic. The requirements don’t focus on the product directly. Instead, they outline good management practices that help ensure high quality. For example, ISO 9001 doesn’t prescribe the raw materials you should use but rather the process of using the raw materials.
Implementing ISO 9001:2015 requires careful planning. Instead of implementing it using a paper-based system, we recommend you use a quality management system (QMS). The American Society for Quality (ASQ) estimates that an average company spends 10% to 15% of its operational expenses on maintaining quality.
What Is an ISO 9001 QMS?
A QMS helps businesses comply with the ISO 9001 requirements. Modern quality management systems (QMS) use the ISO 9001:2015 standard as a benchmark for quality management. To implement a QMS, you should create a planned workflow where you design each process to meet your quality assurance objectives.
Quality management software solutions help you create and manage these processes. You can conceptualize and outline the processes according to the ISO requirements within the QMS. For example, when you define the process to manage annual revenues, use your QMS to put that process in place.
While a QMS uses the ISO 9001 standard as a basis, it can do a lot more. For example, QMS solutions can assist in meeting and exceeding customer expectations and implementing continuous improvements. The software also helps you comply with other ISO standards and regulations, including ISO 14001 (Environmental Management Systems), ISO 13485 (Quality Assurance for Medical Devices), ISO 27001 (Information Security Management), GMP, GxP, and GLP.
The 7 ISO 9001 Quality Management Principles
The ISO 9001:2015 standard is based on seven fundamental principles. Below, we explain how you can follow these principles to comply with the requirements of ISO 9001 and implement an effective quality management system.
Customer Focus
Quality management’s ultimate goal is to offer your customers more value. Therefore, you need to focus on the customers’ needs and requirements to deliver more value.
- Connect your current quality objectives with future customer expectations.
- Manage customer relationships for long-term success by monitoring customer satisfaction and proactively resolving their issues.
- Enable customers to provide direct feedback.
Proactively matching your customers’ quality requirements ensures you’re putting efforts in the right direction.
Leadership
As a leader, you should align strategies and processes across departments. Set up effective communication processes between departments for frictionless collaboration to make achieving quality objectives easier.
- Communicate your goals, objectives, policy, and processes to ensure excellent quality.
- Recognize and reward team members that contribute towards the company’s quality objectives.
- Build a culture where quality is the norm.
Focus on creating a conducive environment where all team members are inspired to achieve quality objectives, making quality the norm.
People Engagement
Let your team know that their contributions to achieving quality objectives positively impact your business. Reward team members that commit to quality objectives and encourage them to promote their commitment to delivering high-quality products or services.
- Educate your team about the value and importance of their contributions to quality management.
- Empower and inspire your team to promote the company’s quality culture.
- Recognize team members when they fix a quality issue or suggest ways to improve quality.
- Assess employee satisfaction regularly and collect feedback.
Collect feedback regularly to understand how employees feel about your approach to quality management. Consider inviting suggestions from team members to improve current business processes and quality policy to increase employee buy-in.
Process Approach
Start by analyzing your current processes. Then, measure your processes’ current performance and try to find room for improvement.
- Design processes with a focus on achieving quality objectives.
- Analyze process dependencies and consider how a change in one process can impact other processes and the overall workflow.
- Focus on risk-based thinking for better control over quality management.
- Seek inputs from internal stakeholders and external parties such as suppliers when defining a process.
Using a QMS can help you create interrelated processes, enabling stakeholders to better understand how they can change processes to improve quality.
Continuous Improvement
Quality management isn’t a one-off task. Once you’ve implemented a QMS, monitor your processes and performance.
- Train your team to use your quality management toolkit and educate them about best practices.
- Measure the results of your quality management efforts.
- Monitor changes in the market and evolving customer requirements and adapt to those changes quickly.
Conduct regular internal audits to look for nonconformities and opportunities for further improvement. Then, assess the viability of changing processes and implement the changes if necessary.
Beyond earning ISO 9001, consider using a PDCA cycle for continuous improvement. The four-step approach stands for Plan, Do, Check, Act. It is an approach widely used in manufacturing businesses to introduce incremental changes to processes, services, and products. By approaching new initiatives within a plan-do-check-act framework, your organization can try out new processes or maintenance procedures, assess the results, and implement the approach that best suits your requirements.
“Just as a circle has no end, the PDCA cycle should be repeated again and again for continuous improvement. The PDCA cycle is considered a project planning tool.”
ASQ
Evidence-Based Decision Making
Take the guesswork out of decision-making by relying on data-backed evidence.
- Centralize data using software solutions.
- Store data in the cloud to allow technicians, top management, and other stakeholders to access the data in real time.
- Deploy modern methods to analyze collected data.
Robust real-time data can provide excellent insights into your customers’ needs, workflow and process efficiency, and other aspects of your business. These insights help you make objective decisions and review or change them over time.
In fact, it’s best to log data for all quality control procedures for external (and internal) audits. Auditing helps you find room for improvement and things you need to achieve your quality goals. However, recordkeeping is resource-heavy when you input data manually. MaintainX automates recordkeeping and improve data management. For example, as your teams complete work, the CMMS automatically logs details about each quality-related task performed under a specific work order. This CMMS audit trail can also show regulatory compliance during an inspection.
Relationship Management
Managing and expanding relationships with vendors and partners helps build an efficient supply chain.
- Determine KPIs (key performance indicators) and metrics for your relationships.
- Prioritize building and managing relationships with suppliers and stakeholders based on quality impact.
How to Implement ISO 9001
Implementing ISO 9001 involves the following steps:
- Define a quality policy and quality objectives based on customer requirements and your vision of management.
- Create workflow processes and standard operating procedures to deliver your products and services. Prepare documented information, including policies, procedures, and process checklists, that you’ll need later during the audit.
- Fill out the four mandatory documents and any other documents you find necessary. The four required documents are:
- Scope of the QMS (clause 4.3)
- Quality policy (clause 5.2)
- Quality objectives (clause 6.2)
- Procedure for the control of externally supplied products, services, and materials (clause 8.4.1)
- Operate the QMS to collect the records necessary to audit your system. An audit is required to get the ISO 9001 certification.
Quality procedures provide the framework to achieve the goals of your quality policy. For example, you should establish an extensive quality control procedure if your goal is to exceed customer expectations. You may also need to create a preventive maintenance plan to ensure your equipment runs smoothly and at peak performance.
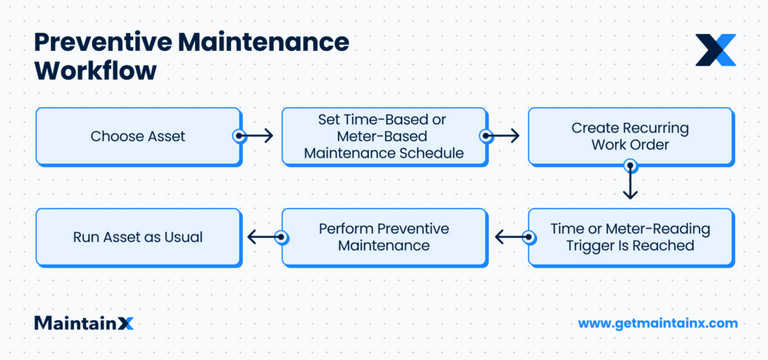
Do You Need an ISO Certification?
ISO certification isn’t necessary according to the standard itself. However, your customers may choose to only work with an ISO 9001:2015-certified business. The reason is that there’s no way for your customers to check nonconformities against the standard. You need the certification to back up your claims.
You’ll need to go through the ISO certification process and apply to a certification body to get certified. ISO develops the standards but does not issue certificates. You can find certification companies online.
Next, the certification body (a registrar or certification body) will audit your QMS to confirm that all processes meet the standard’s requirements.
Once you’ve implemented the QMS and finished the documentation, you’ll need to complete five steps to get certified:
- Internal audit
- Management review
- Corrective actions
- Documentation review
- Main audit
MaintainX: The Best Way to Implement ISO 9001 QMS
MaintainX is a CMMS that helps centralize data and the documents needed to perform quality procedures and make data-driven decisions. We have a built-in chat feature to help you collaborate remotely via computer or mobile, wherever you are.
Using a CMMS like MaintainX automatically creates an audit trail as you go about your day-to-day work. You can focus on continuous improvement, gain more control over documents, and manage data more efficiently. Try MaintainX today to see for yourself how it can simplify your QMS implementation.
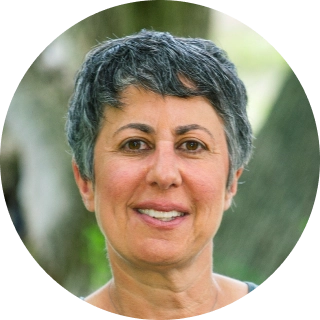
Caroline Eisner
Caroline Eisner is a writer and editor with experience across the profit and nonprofit sectors, government, education, and financial organizations. She has held leadership positions in K16 institutions and has led large-scale digital projects, interactive websites, and a business writing consultancy.
See MaintainX in action