The paper-on-glass approach allows manufacturers to move paper-based batch records to a digital environment. Paper-on-glass systems can help validate entries as your staff enters them. Simultaneously, it also creates an audit trail.
However, paper-on-glass systems operate in digital silos. Therefore, you can’t integrate them vertically with other systems like enterprise resource planning (ERP) or manufacturing execution systems (MES).
This post explains the meaning of paper on glass, how to use it, and why you might consider using a CMMS instead.
What Is Paper on Glass?
Paper on glass is a data recording approach similar to paper-based recording but in a digital environment.
A paper-on-glass system’s interface includes predefined fields into which employees enter data. For example, you might have fields for a batch number, time taken to process the batch or process-specific details like temperature and weight of material used as input.
The system validates the data as the employees enter it, reducing the human error associated with paper-based systems. For example, the system won’t accept an entry if the employee enters 2000°C as the temperature instead of 20°C.
These systems also ensure that records don’t have missing entries. For example, you can define the production sequence. In fact, the system knows the workflow and the data. If an employee misses information, the system won’t allow the employee to move to the next step.
Note that these details are also valid for advanced paper on glass applications from companies like COPA-DATA. More traditional systems don’t allow data validation or other advanced options. Older applications merely used an existing paper-based record and duplicated it into a digital environment.
“Digitization and automation will also ensure better quality and compliance by reducing manual errors and variability, as well as allowing faster and effective resolution of problems.”
McKinsey
Why Manufacturers Use Paper on Glass
When the digital transformation began, the paper-on-glass approach was the best option for manufacturers (especially pharma companies) with high volumes of batch records. Here are reasons why manufacturers may still use paper on glass:
Electronic Records and Instant Batch Reports and Analysis
Manufacturers in highly regulated industries like pharma must comply with FDA regulations and follow Good Manufacturing Practices (GMP). Furthermore, the traceability requirements in FDA 21 CFR Part 11 require manufacturers to store records electronically.
In addition to compliance, paper on glass can help get a quick overview of all batches without much manual effort. In addition, most advanced applications can auto-generate batch reports, allowing for faster batch analysis.
Increased Batch Execution Accuracy
Paper on glass systems force entry into each data field and validate the entry in real time. The data is verified and queried at the point of entry, and each entry is automatically timestamped. These factors improve batch control, increase batch consistency, and ensure high-quality production.
Automated Data Processing
Pharmaceutical production generates a lot of data. As a result, you must process data after collection and maintain data integrity. Paper-on-glass systems process this large volume of data at scale through automation. Such processing can identify violations, record all data processes in an electronic logbook, and create an audit trail to prove traceability.
Cost Reduction
Paper-on-glass systems help reduce the costs associated with recordkeeping. For example, you don’t need to invest in storage space for large volumes of paper and paper rolls. Because there’s no need to use paper, you don’t have to print or track each document manually. More importantly, you’ll save time by not needing to transfer data manually.
“While investments already made represent huge opportunities, too often, they are impeded by manual and disconnected processes and documentation, especially if paper-based.”
Deloitte
But You Need an Alternative to Paper on Glass
Paper on glass isn’t fit for modern facilities. Here are two reasons why you should move away from paper on glass:
Potential for Human Error
Human error can still creep into paper on glass, especially when using an older application that doesn’t offer data validation or other advanced features. Any error committed on the paper-based record will find its way into the digital document, compromising data integrity.
Difficult to Transfer Data
Managing paper-on-glass documentation requires significant human resources. In addition, paper on glass is incredibly prohibitive in some cases. An example is when a pharma company needs to move data from paper on glass to other systems for R&D. The cost and extensive process of manually transferring data from paper on glass to other systems make paper on glass a prohibitive approach.
You face a similar problem when using multiple digital systems that don’t integrate vertically. When you pull data from multiple systems, it’s generally translated into a PDF (or paper on glass)—this process is often commercially unviable.
Here’s why: think of the COVID vaccine development as an example. Pfizer dedicated a significant workforce to completing the tech transfer for its vaccine, which had a 50,000-step development process. So when you hand over this enormous volume of information to the manufacturing operations, they’ll need to reverse engineer that data to input it into the ERP and MES.
Lacks Additional Features
Paper-on-glass applications typically don’t include additional functionalities. However, other software solutions—such as a computerized maintenance management system (CMMS)—allow creating of batch records and offer additional functionalities such as creating standard operating procedures (SOPs), assigning work orders, and executing a maintenance schedule.
A CMMS like MaintainX also enables you to use batch records more contextually. For example, say one of your machines malfunctioned. You’ve created a work order for one of the technicians to fix the machine. The technician receives the request and refers to the SOP in MaintainX to complete the work order.
However, the technician needs more context. The technician uses MaintainX’s built-in chat option to request information about the asset’s task when the malfunction occurred. You can share the batch records with the technicians internally in real time without any back and forth over email or phone to speed up the process.
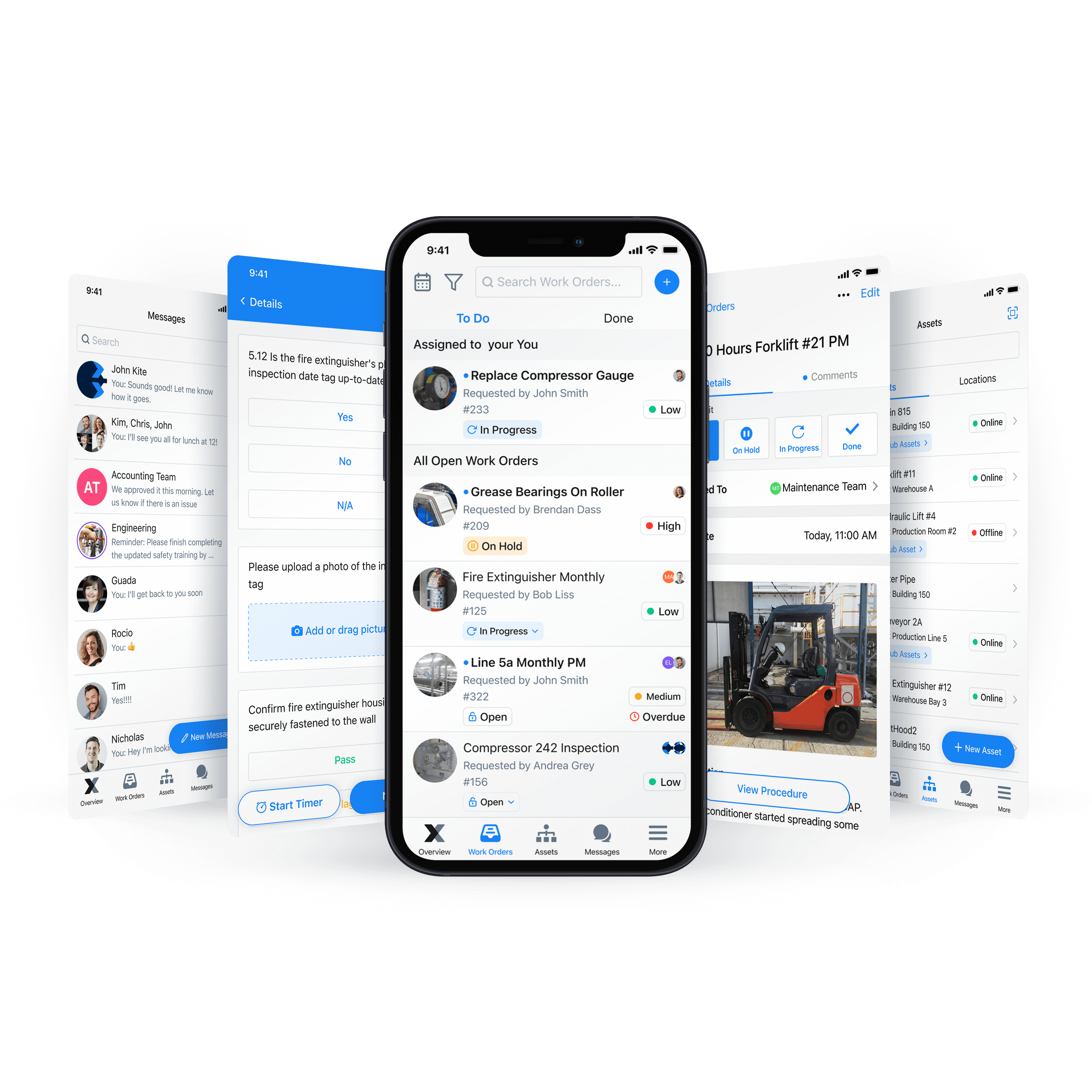
MaintainX: The Smarter Way to Maintain Electronic Batch Records
A CMMS makes maintaining and organizing batch records simpler. It can auto-generate reports for real-time insights. In addition, a CMMS like MaintainX stores your data in the cloud, allowing your team remote access to data on almost any device with an Internet connection and ensuring data security.
Once again, by the way, we earned SOC 2 Type 2 compliance renewal and ISO 27001 certification.
Don’t forget that MaintainX also integrates with ERP and MES. Vertical integration eliminates the need to convert digital data into PDFs or any other file type because MaintainX directly exchanges information with the integrated systems.
Even better, you can use a CMMS for purposes beyond managing electronic batch records. For example, you can use the MaintainX procedure templates to ensure compliance or create a digital checklist to execute your maintenance program digitally.
If that sounds interesting, try MaintainX yourself to see how it can address the shortcomings of paper on glass and automate various parts of your production and maintenance workflow.
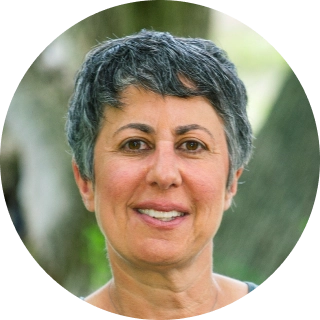
Caroline Eisner
Caroline Eisner is a writer and editor with experience across the profit and nonprofit sectors, government, education, and financial organizations. She has held leadership positions in K16 institutions and has led large-scale digital projects, interactive websites, and a business writing consultancy.
See MaintainX in action