Testing your equipment’s components, design, and materials helps identify defects in your equipment. Non-destructive testing (NTD) also provides valuable insight into your quality control and preventive maintenance program.
There’s a wide range of available testing techniques based on your use case, equipment, and industry, according to industry codes and standards. Testing methods are classified as destructive and non-destructive based on the state of the components after testing.
As the names suggest, non-destructive testing includes techniques that don’t physically damage the parts you’re testing. In this article, we discuss the meaning and methods of non-destructive testing.
Non-Destructive Testing (NDT)
Non-destructive testing (NDT) is a group of testing methods that allows technicians to evaluate a component or system without damaging it. It’s also commonly referred to as non-destructive inspection (NDI) or non-destructive evaluation (NDE).
NDT is most commonly discussed in the context of industrial use, but it also has extensive applications in other areas like medicine. In medicine, X-rays and MRI (Magnetic Resonance Imaging) are the best examples of NDT’s use cases.
However, unlike MRI scans, not all non-destructive examination methods require specialized testing equipment. For example, technicians often inspect an asset visually—such as inspecting the exterior of a vacuum system—without specialized tools.
9 Commonly Used Non-Destructive Testing Methods
Over the years, many NDT methods have evolved along with technological advancements and industry-specific needs. Below, we discuss some of the most commonly used NDT inspection methods.
1. Visual Testing
Visual testing, or visual inspection, is one of the most commonly used NDT methods. Technicians visually inspect assets to detect defects, damage, cracks, corrosion, and other problems, often using tools like a magnifying glass, remote cameras, and drones.
2. Vibration Analysis
Vibration analysis involves using accelerometers and velocity sensors (among other types of sensors) to register an asset’s vibrations. Then, technicians can use this vibration data to identify changes in the machine’s behavior.
3. Ultrasonic Testing
To use ultrasonic testing, the inspector transmits sound waves through an asset using a transducer. The asset’s material isn’t defective if the sound waves pass through to the other end. However, if the material property has defects, the sound waves reflect off those defects. The inspector then uses 3D visualization to determine the distance of the defect in the asset.
Several ultrasonic testing techniques have emerged over time. Here are examples of ultrasound techniques:
- Pulse-Echo (PE) Testing
- Through Transmission (TT) Testing
- Time of Flight Diffraction (ToFD) Testing
- Electromagnetic Acoustic Transducer (EMAT) Testing (also called Electromagnetic Testing)
- Air Coupled Testing
- Phased Array Ultrasonic Testing (PAUT)
- Full Matrix Capture (FMC)
- Guide Wave (GW) Testing
4. Liquid Penetrant Testing
Liquid penetrant testing involves applying a low-viscosity penetrant liquid over the tested asset. The liquid is allowed to seep in through cracks and pores. Once the liquid seeps in, the inspector cleans the surface and applies a developer liquid on the same surface. Applying this developer causes the penetrant liquid to rise to the surface, revealing the flaw.
5. Radiographic Testing
Radiography testing requires passing X-rays (for thin or low-density materials) or gamma rays (for thick or high-density materials) through the test asset. The radiation will reduce as it penetrates through the asset, and this reduction is measured on a film to detect the flaw.
Technicians use various imaging methods to process the results of industrial radiography. For example, they can use Computed Tomography (CT), Computed Radiography (CR), Real-Time Radiography (RTR), and Digital Radiography (DR).
6. Magnetic Particle Testing
Magnetic particle testing relies on the effect of a magnetic field to identify defects in ferromagnetic materials. The test material or asset is placed between electromagnets, and magnetic particles are poured over the test material. The magnetic flux lines reveal the leakage because the magnetic particles cluster near the defect.
7. Eddy Current Testing
Eddy current testing is one of several electromagnetic testing methods in which the test material is brought in the proximity of an excitation coil. The coil’s magnetic field and current oscillate at the same frequency. Bringing a conductive material in its proximity can induce currents opposed to the coil’s currents (known as eddy currents).
If the material has a discontinuity, it will disturb the eddy current’s path and create a local magnetic field, changing the system’s balance. A receiver coil monitors the change magnitude of eddy currents by measuring changes in the current flowing through the excitation coil. The changes appear on a monitor, helping the inspector identify the defect.
8. Leak Testing
Leak testing helps find leaks on a test asset and pipelines. The least expensive of all leak tests is the bubble leak test. You’ve probably seen a bubble leak test yourself when an automotive mechanic tries to find the punctured spot on a tire.
Bubble leak tests involve immersing the test asset in a liquid container or applying soap solution (if the asset is large) to find gas leaks. Bubbles appear in the water or soap solution at the spot where the air is leaking. Other leak testing methods include pressure change, halogen diode, and mass spectrometer testing.
9. Acoustic Emission Testing
Acoustic emission testing is a passive NDT method that relies on bursts of acoustic emissions from a crack in the test asset. Before the test, the inspector places sensors across the structure’s surface to register these acoustic emissions. Alternatively, the inspector can plasticize stressed areas to detect acoustic emissions before cracks emerge.
ISO 19.100: Non-Destructive Testing
Finally, the International Organization for Standardization’s ISO 19.100 provides guidelines and specifications for non-destructive testing. The standard includes information about “testing equipment: industrial apparatus for X-ray and gamma radiography, penetrant flaw detectors, etc.”
Who is Responsible for Non-Destructive Testing?
The person or team responsible for NDT depends on the technique(s) you want to use. For example, radiographic testing requires someone with experience working with radiology equipment.
Other techniques, like visual testing, don’t require specialized knowledge. In most cases where technical knowledge is not a prerequisite, the maintenance team is responsible for NDT. If you want to help your maintenance team hone their NDT skills, enroll them in the American Society for Nondestructive Testing (ASNT) NDT training courses.
Regardless of who performs NDT, you need to record testing data in one place. However, recording data manually results in messy records and time wasted on a task you can automate. This is where a computerized maintenance management system (CMMS) comes in.
A CMMS helps record testing data and schedule testing digitally for each asset. For some NDT techniques, a CMMS also can automate data collection. For example, a CMMS can receive real-time data from meters and sensors mounted on your machines to notify you about potential defects automatically.
Ultrasonic Testing Is the Future of Non-Destructive Testing Techniques
Across industries, NDT techniques like visual inspection continue to be used widely. Traditional methods offer advantages like low-cost testing and time efficiency. However, modern techniques can help with more complex testing needs.
Ultrasonic testing techniques are becoming increasingly popular. According to Fortune Business Insider, in the aerospace industry, ToFD’s market share will grow significantly by 2027 because of its increasing popularity as a method to test welds for in-service aircraft inspection.
Non-Destructive Testing and CMMS
Using a mobile-friendly CMMS like MaintainX ensures that your maintenance team always has work order forms with the required information at its fingertips. In addition, following ToFD (time-of-flight diffraction), other ultrasonic testing techniques like phased array, immersion, and guided wave testing are gaining popularity.
As you start using these more advanced NDT techniques, be sure to have the best tools to collect, store, analyze, and act on the test data.
With MaintainX, you also can create preventive maintenance checklists and SOPs to help beginner-level technicians use more straightforward NDT techniques like visual inspections.
If you need more control over testing processes and automate test data collection, try MaintainX for free.
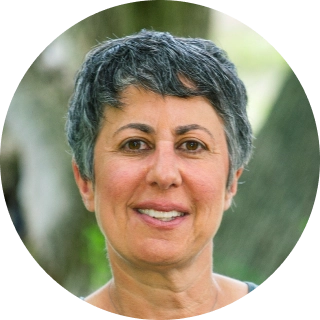
Caroline Eisner
Caroline Eisner is a writer and editor with experience across the profit and nonprofit sectors, government, education, and financial organizations. She has held leadership positions in K16 institutions and has led large-scale digital projects, interactive websites, and a business writing consultancy.
See MaintainX in action