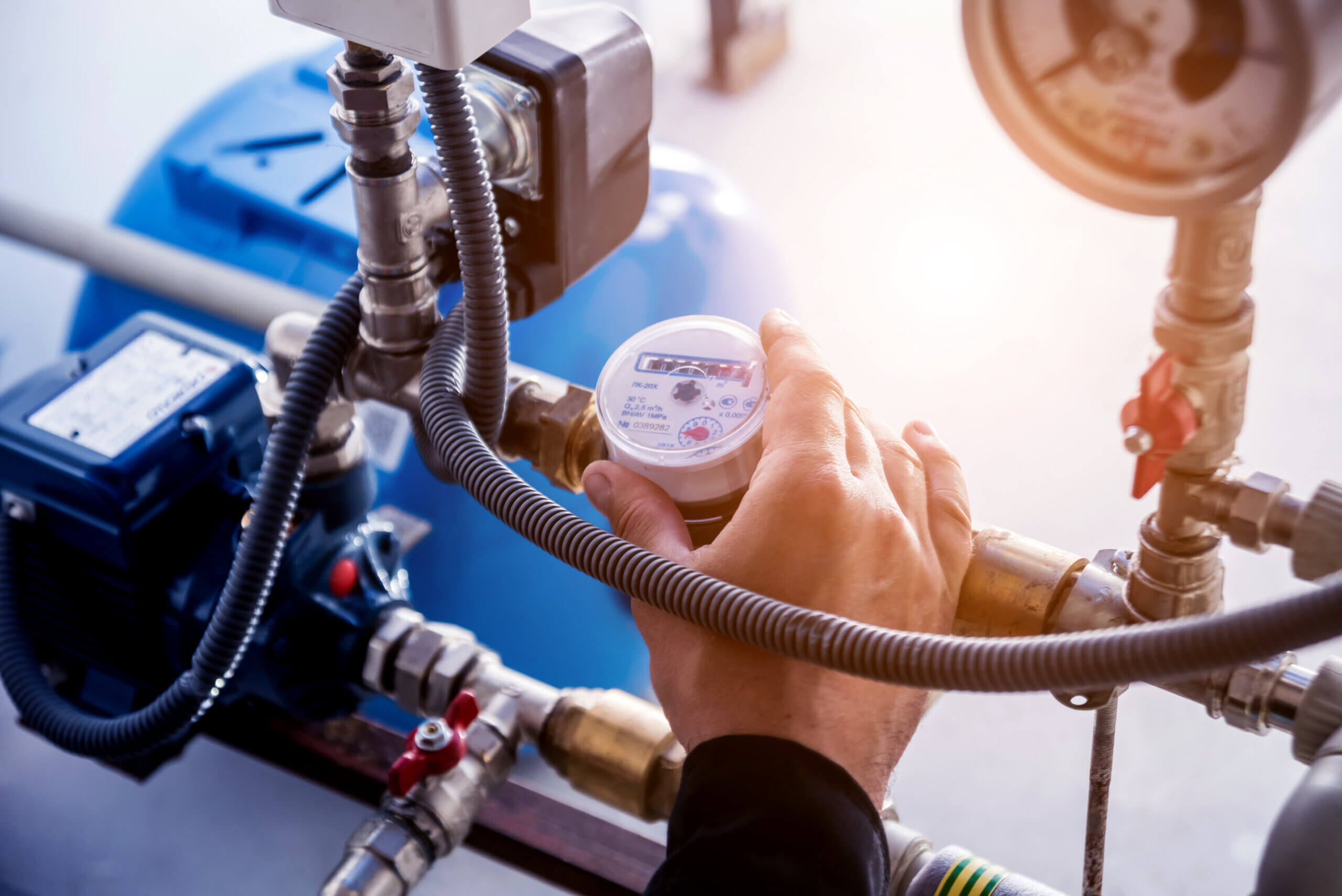
Given the complexity of global production today, organizations have turned to the latest digital solutions to keep pace with today’s swift-moving and changing environments to meet customer demands. Meter-based maintenance is a smart way to integrate manufacturing maintenance efficiency strategies into workflows.
Fortunately, maintenance management and operations software, like MaintainX, provides recurring work order scheduling, automated parts inventory, and in-depth analytics and reporting capabilities to meet these global customer demands.
Customizable dashboards, audit trails, and reports allow management to view completed preventive maintenance plans and regulatory SOPs in real time to keep operations running smoothly and reduce costly downtime.
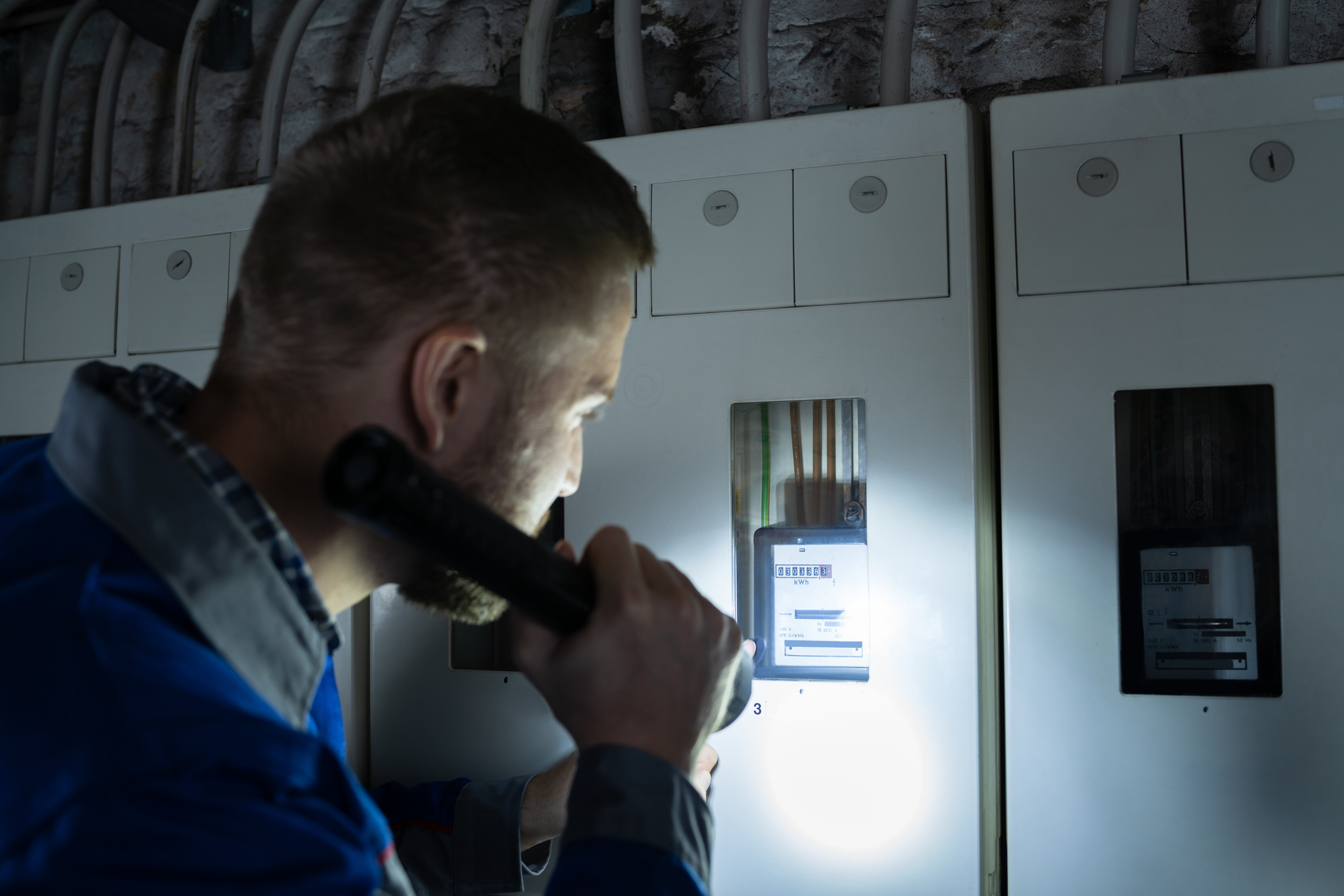
Meter-Based Maintenance Best Practices
Keeping pace with Industry 4.0 solutions, meter-based maintenance—also called performance-based PM and meter-based PM—dictates maintenance based on equipment-usage variables.
High-level maintenance programs, like Asset Condition monitoring, typically mix several different maintenance strategies based on the maintenance needs of individual equipment. The optimal balance between asset performance and repair costs is, therefore, different for each company.
However, we do know that shifting from reactive or corrective maintenance to preventive maintenance can improve the ratio between asset performance and repair costs.
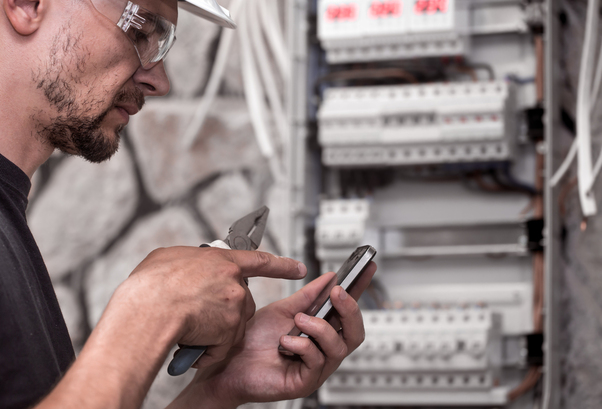
Implementing Preventive Maintenance with CMMS
Preventive maintenance (PM) minimizes equipment downtime, improves asset lifespans, and lowers maintenance costs. It is a simple, direct, and systematic way to improve asset reliability. While launching a preventive maintenance program may seem complicated, it is simple if effectively planned for.
Maintenance teams regularly perform PM tasks to reduce the likelihood of failure throughout an asset’s normal operating conditions. The most common preventive maintenance tasks include equipment inspections, cleaning, lubrication, and adjustments.
Operations and maintenance managers schedule these preventive maintenance tasks according to manufacturer recommendations, average asset life cycles, and historical behavior patterns.
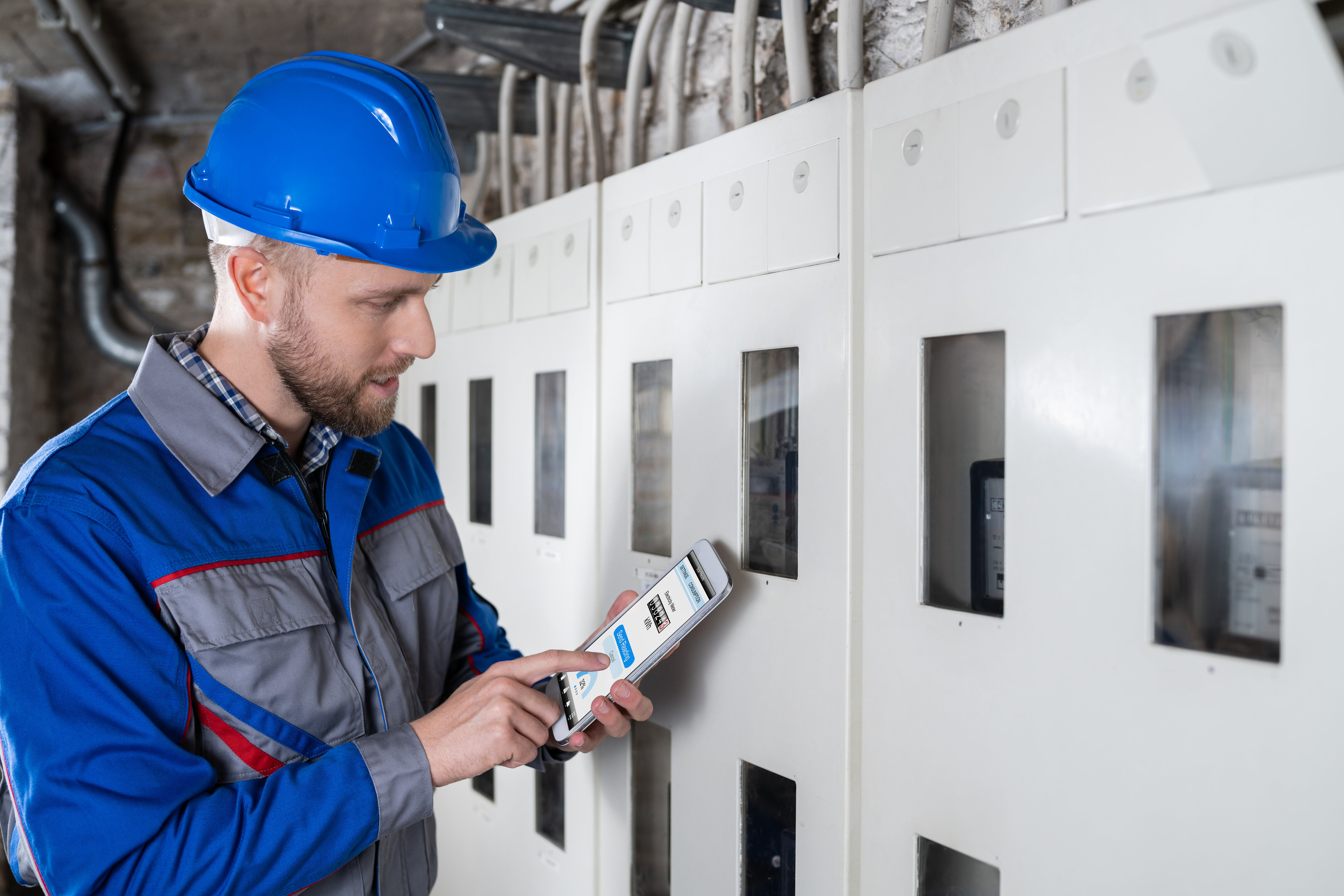
Types of Preventive Maintenance (PM)
Preventive maintenance tasks that promote maintenance efficiency reduce unplanned downtimes. Maintenance tasks generally fall into four broad categories. In this post, our subject is meter-based maintenance, but we will describe the others as well.
Meter-Based Maintenance
Meter-Based maintenance is based on equipment-usage variables. Any piece of equipment that requires usage-based maintenance will come with a meter and/or counter to assess hours running, production milestones, temperature, vibration, etc.
Periodic Maintenance
Periodic maintenance includes preventive maintenance tasks performed at scheduled intervals. Teams can perform maintenance weekly, monthly, quarterly, or annually. Equipment manuals usually contain the recommended maintenance schedules for an asset. Periodic maintenance also is referred to as time-based maintenance.
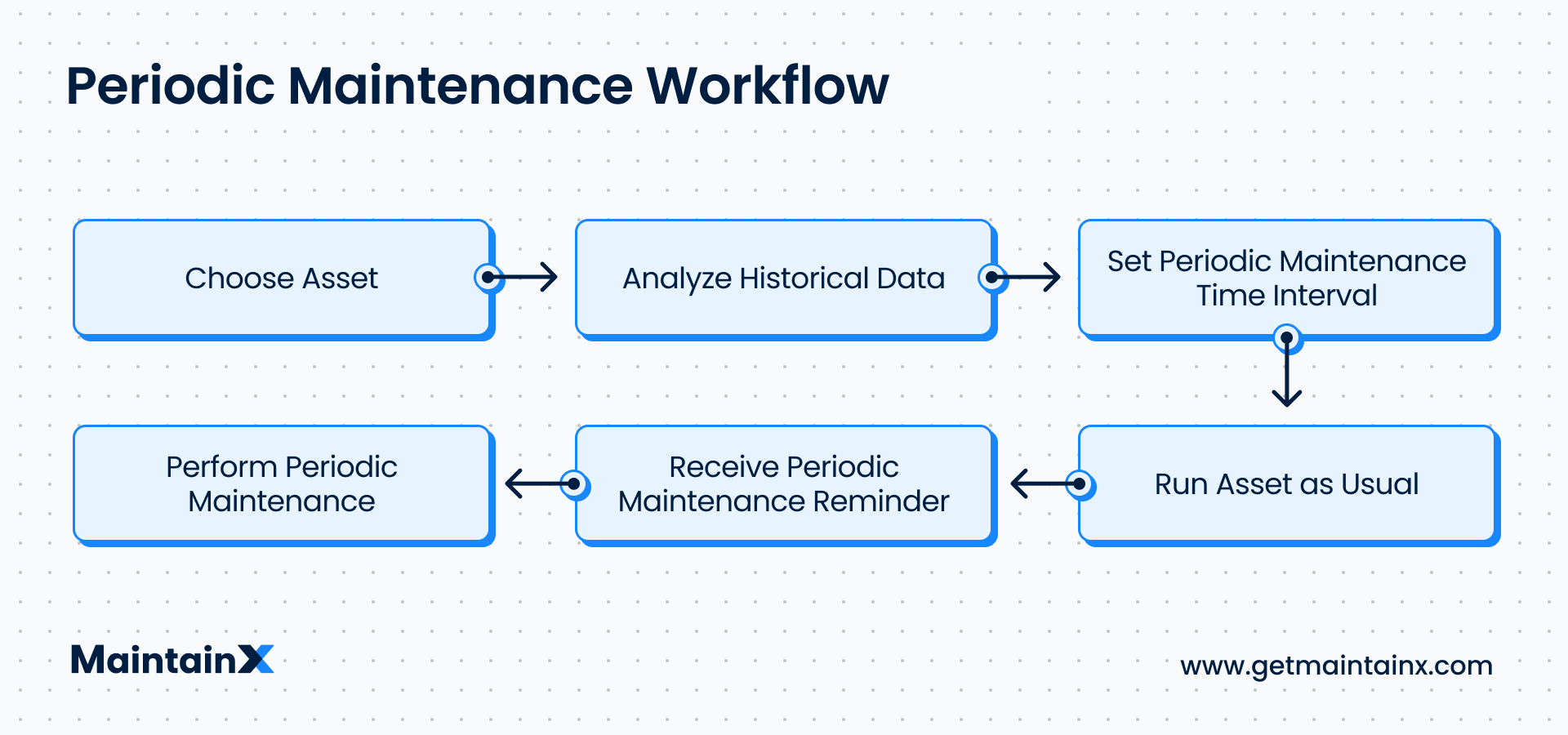
Predictive Maintenance (PdM)
Predictive Maintenance (PdM) is an advanced form of preventive maintenance that uses sensor devices and data analysis tools to predict the optimal time when assets should receive maintenance to prevent failure. The goal of PdM is to perform maintenance just before failure occurs to eliminate the risk of under- or over-maintenance. An example of PdM is using vibrational analysis on high-rotating machinery to detect imbalance, misalignment, or bearing wear. A fluctuation in machine vibrations triggers maintenance work.
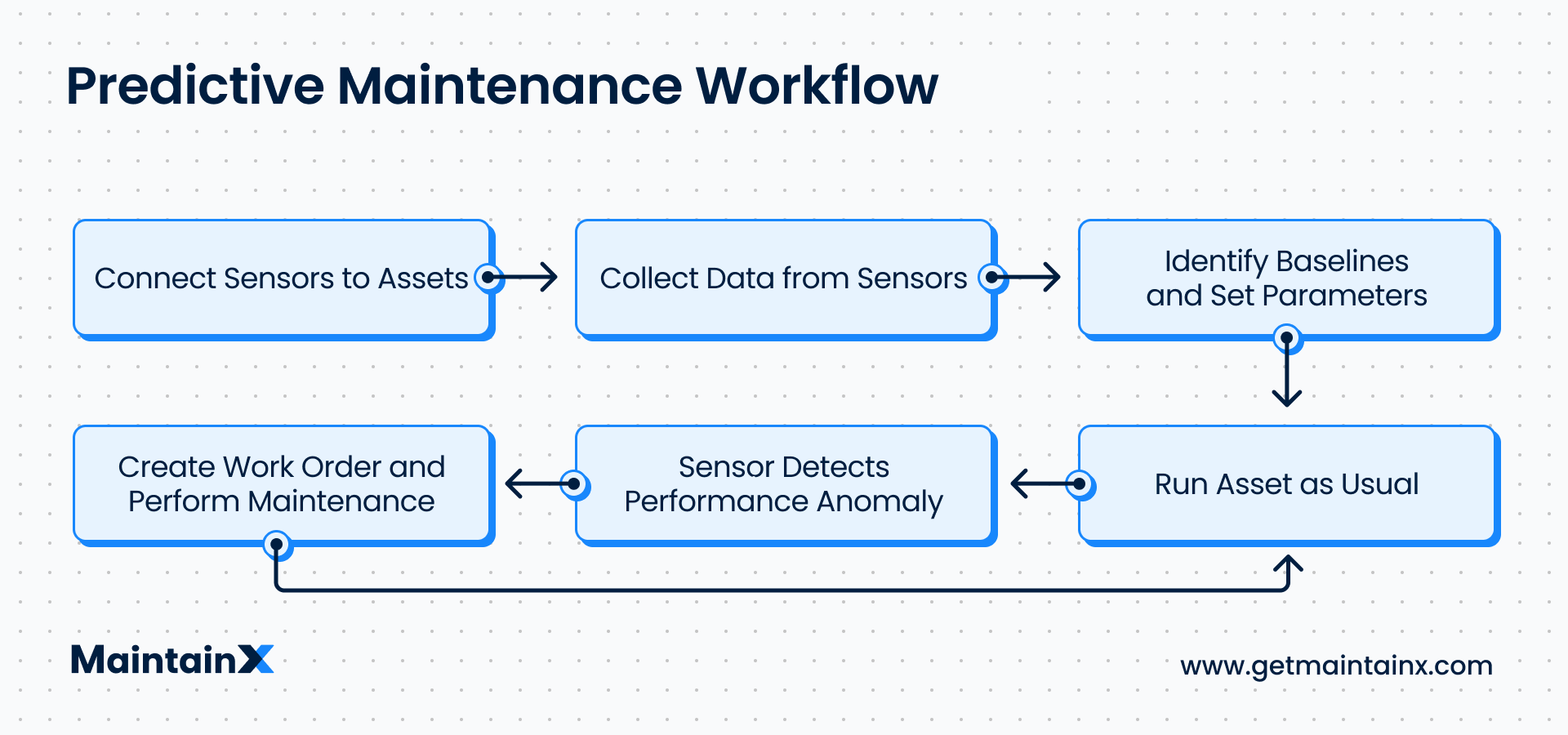
Prescriptive maintenance is like PdM in that they both rely on data to make maintenance decisions. However, with prescriptive maintenance, machine-learning software gathers and analyzes equipment conditions to recommend specific maintenance actions. This helps to minimize operational risks and increase overall operational and maintenance efficiency. For example, sensors or other artificial intelligence (AI) software will recommend adjusting the barometric pressure in a processing tank in the event of a thunderstorm to avoid high pressure in the tank.
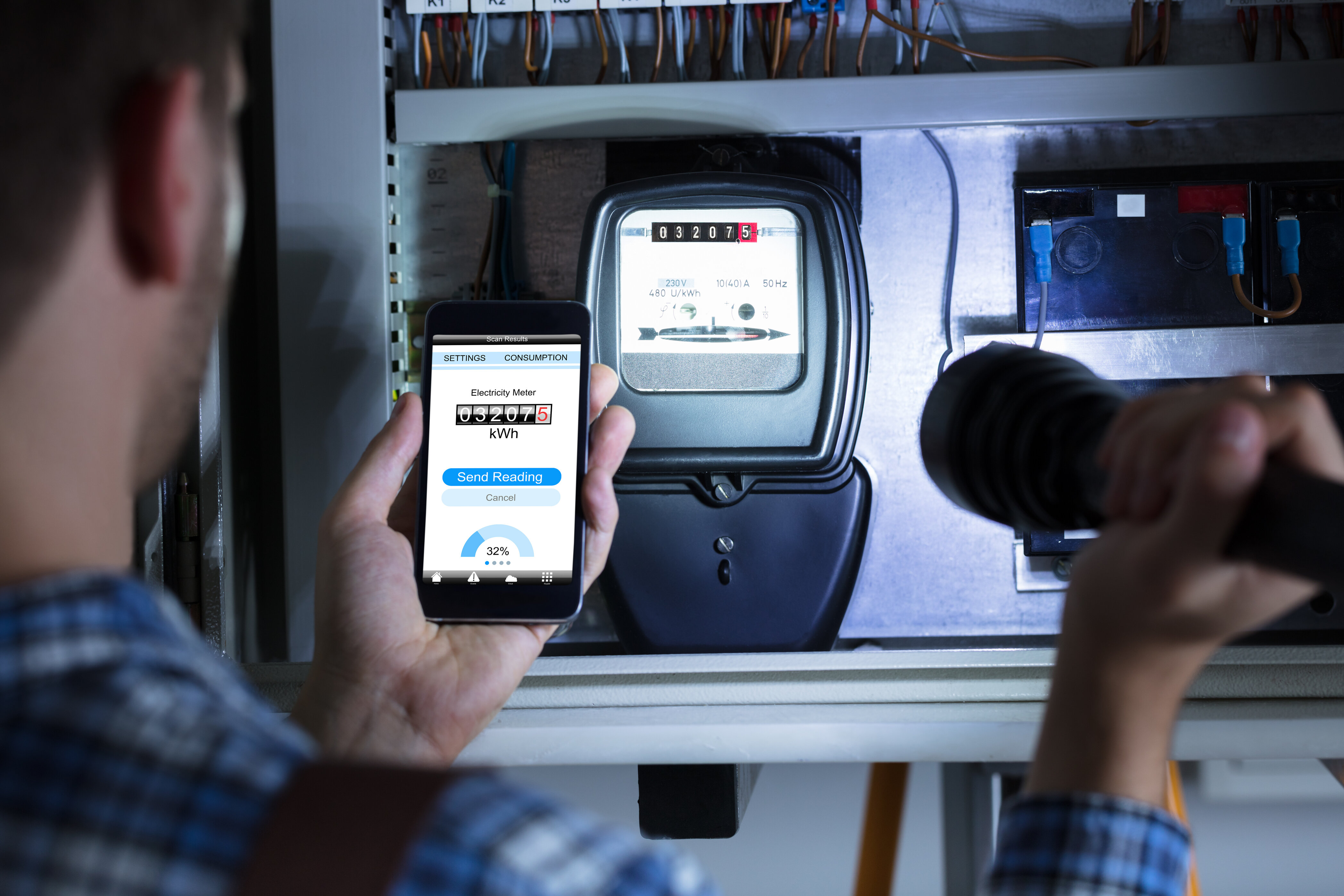
Automating Meter-Based Maintenance
Basing preventative maintenance on meter readings instead of time is better for most PM plans because it is tied to the utilization of the asset instead of an arbitrary date.
Furthermore, scheduling routine maintenance based on usage or time triggers reduces the likelihood of unplanned equipment failures that translate to emergency maintenance expenses. To figure out which assets will run best on a meter-based maintenance plan, we recommend taking three steps.
1. Asset Inventory
Preventive maintenance (PM) is an excellent strategy for keeping critical assets in good working condition. However, the real cost savings comes from finetuning your organization’s PM schedule over time.
Manufacturers’ recommendations do not always provide foolproof guidelines to obtain asset reliability. The industrial environment and machine usage patterns can uniquely impact equipment behavior over time.
As technicians perform routine maintenance, keep track of service dates, labor costs, parts used, and current conditions. Also, note the asset’s criticality to production and safety.
2. Asset Prioritization
Prioritize assets that significantly impact production, have high maintenance costs, require regular maintenance, and/or pose safety hazards. As you begin to realize the return on investment (ROI) of your assets, gradually add more assets to the PM program.
3. Preventive Maintenance Schedule based on Meter Readings
Maintenance triggers that are not calendar-based are called runtime—or condition-based triggers. These are the triggers that meter readings make possible. They also inform maintenance managers and technicians when a specific runtime or condition is met.
Tracking aspects of PM other than those based on time provides a detailed picture of what’s wrong with the equipment and the best method to repair it. Logging meter readings creates asset histories in real time. When a specific meter-reading trigger is met, maintenance is required.
PM schedules depend on a work order system that assigns maintenance teams to track meter readings, such as:
- Odometer readings
- Cycles counts for machinery
- Engine run time
- Temperature readings
- Pressure readings
- Vibration readings
- Electric meter readings
In MaintainX, equipment that requires usage-based maintenance can sync with a meter or counter to assess hours running and production milestones and then trigger work orders as a crucial component of a company’s well-organized maintenance strategies.
Start your meter-based preventive maintenance program today with MaintainX.
FAQs
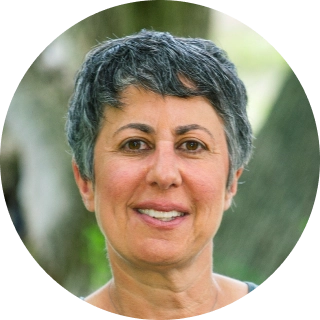
Caroline Eisner is a writer and editor with experience across the profit and nonprofit sectors, government, education, and financial organizations. She has held leadership positions in K16 institutions and has led large-scale digital projects, interactive websites, and a business writing consultancy.