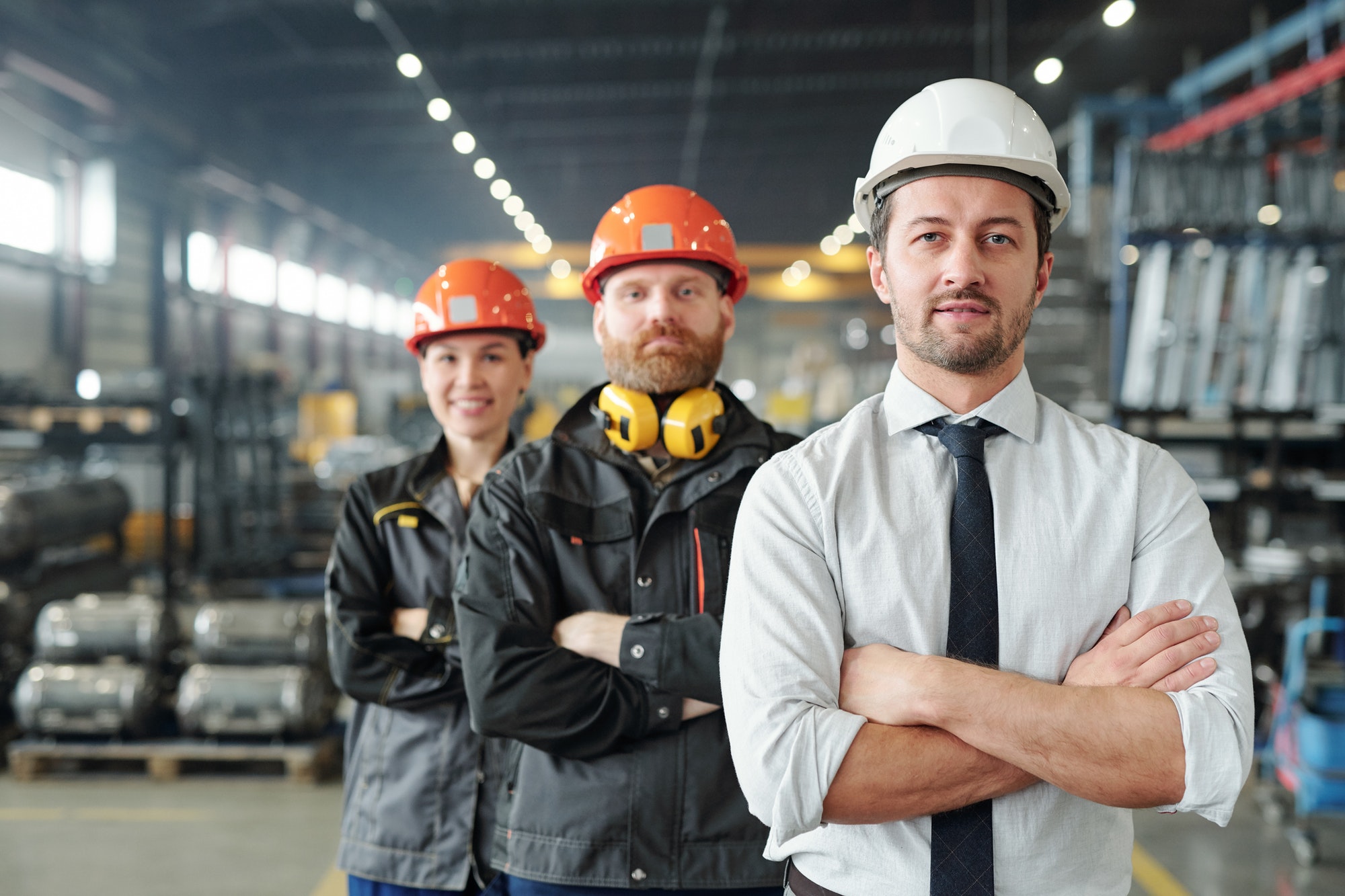
PFMEA helps maintenance departments prioritize preventive maintenance (PM) work orders by providing a method for measuring the varying impacts of equipment breakdowns. Notably, the PFMEA process is a derivative of Failure Mode and Effects Analysis (FMEA).
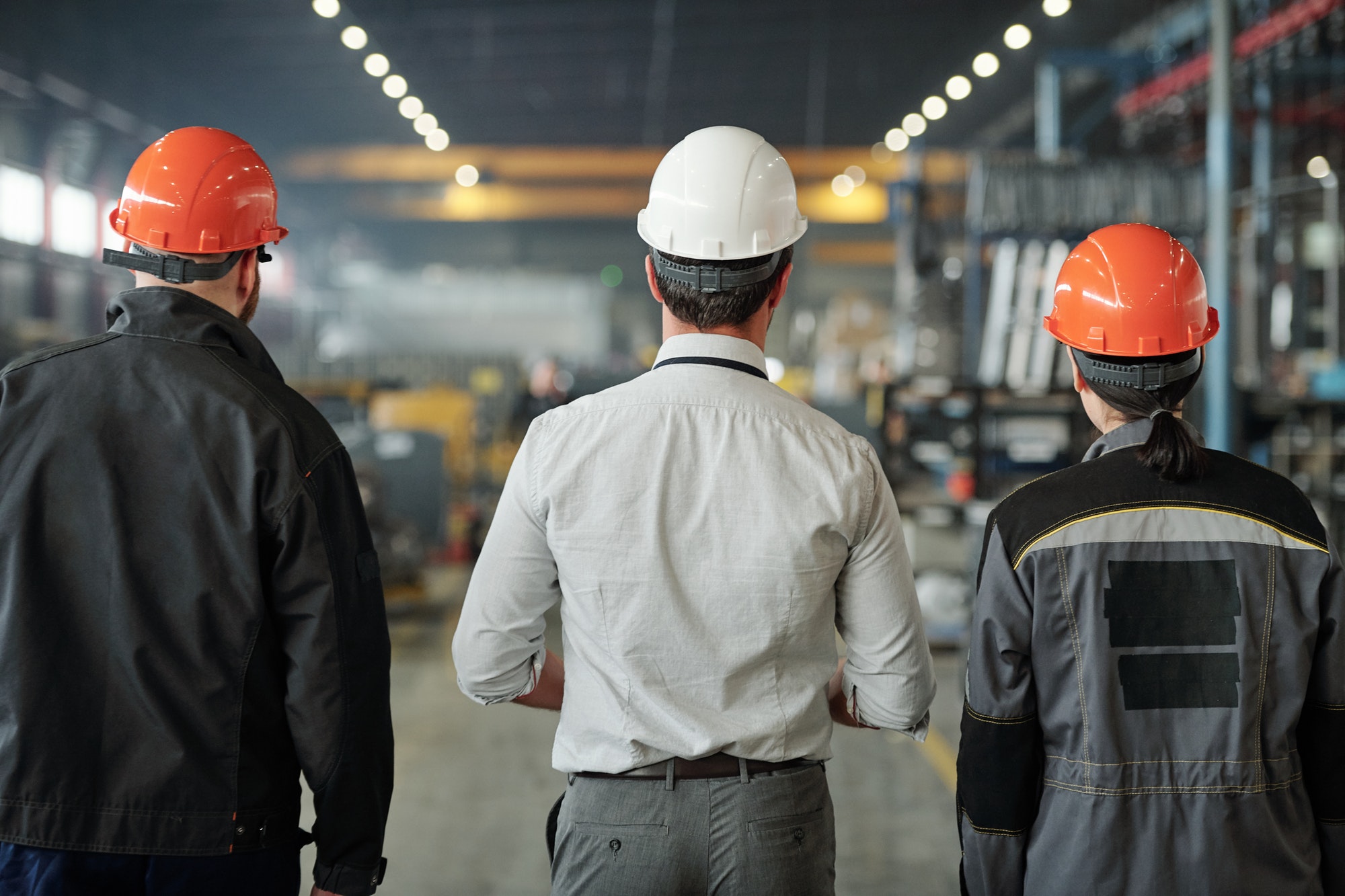
What is PFMEA?
Process Failure Mode and Effects Analysis (PFMEA) is an analytical tool used to evaluate and identify potential failures related to operational processes. Possible failure modes refer to vulnerabilities resulting in productivity, quality control, and safety setbacks. The “big picture” goal of Process FMEA (PFMEA) is continuous improvement.
While PFMEA can be helpful for fine tuning all kinds of operational processes, it is particularly common within industrial manufacturing. Manufacturers rely on dozens, if not hundreds, of pieces of equipment to meet their production quotas every day, and PFMEA helps O&M leaders identify, address, and eliminate the root causes of manufacturing process failure modes.
Facilities that implement mistake-proofing measures can feel good about producing high-quality deliverables most safely, efficiently, and cost- effectively.
How PFMEA works
PFMEA entails analyzing routine process steps to identify all potential production errors. Potential risks in the production process come from several factors, including:
- Poor standard operating procedures
- Manufacturing material bottlenecks
- Inefficient assembly processes
- Unreliable production machinery
- Communication roadblocks
- Unskilled team members
In PFMEA, cross-functional teams put a magnifying glass to processes, looking for potential setbacks. They assign each setback, or failure mode, a severity, occurrence, and detection score. The severity score indicates the estimated impact of a potential setback, while the occurrence score assesses the chance of it happening.
The detection score points to the likelihood of workers uncovering a failure mode—through preventive maintenance, quality control measures, and safety SOPs—before it happens. PFMEA scores are ranked on a scale of one to 10.
The team then multiples the three scores to generate a Risk Priority Number (RPN). This final calculation provides insight into the level of attention a process needs. Generally, the higher the RPN, the higher prioritization the taskforce will give the objective.
What is the difference between FMEA and PFMEA?
ASQ defines Failure Mode and Effects Analysis (FMEA) as a process analysis tool that takes a “step-by-step approach for identifying all possible failures in a design, a manufacturing or assembly process, or a product or service.”
The goal of FMEA is to ensure organizations consistently release high-quality products to market. Initially developed by the U.S. Armed Forces during the 1940s, FMEA allowed troop leaders to identify failures impacting mission safety.

As mentioned above, PFMEA is a subtype of FMEA with a focus on process improvement. PFMEA is one of three types of FMEA; the other types of analyses are:
- System FMEA: System FMEA identifies and assesses failure modes that impact systems and subsystems. Also known as functional FMEA, it’s based on the assumption that a system failure is rarely an isolated event. It can occur between multiple assets and processes.
- Design FMEA: This type of FMEA focuses on the design of deliverables. Managers use it to assess failure modes that can result in product malfunctions, impacting quality standardization, consumer/worker safety, and regulatory compliance. Essentially, designing FMEA ensures that customers receive reliable products and services.
Basically, FMEA takes a broader look at failure modes, while PFMEA restricts itself to failure modes related to operational processes.
Read “What Is FMEA? Failure Mode and Effects Analysis for Beginners.”
Industries that use PFMEA
Since its original adoption by the U.S. military, PFMEA has brought success to large organizations worldwide. After civil aviation initially followed suit, additional industries have recognized the value of the practice, including:
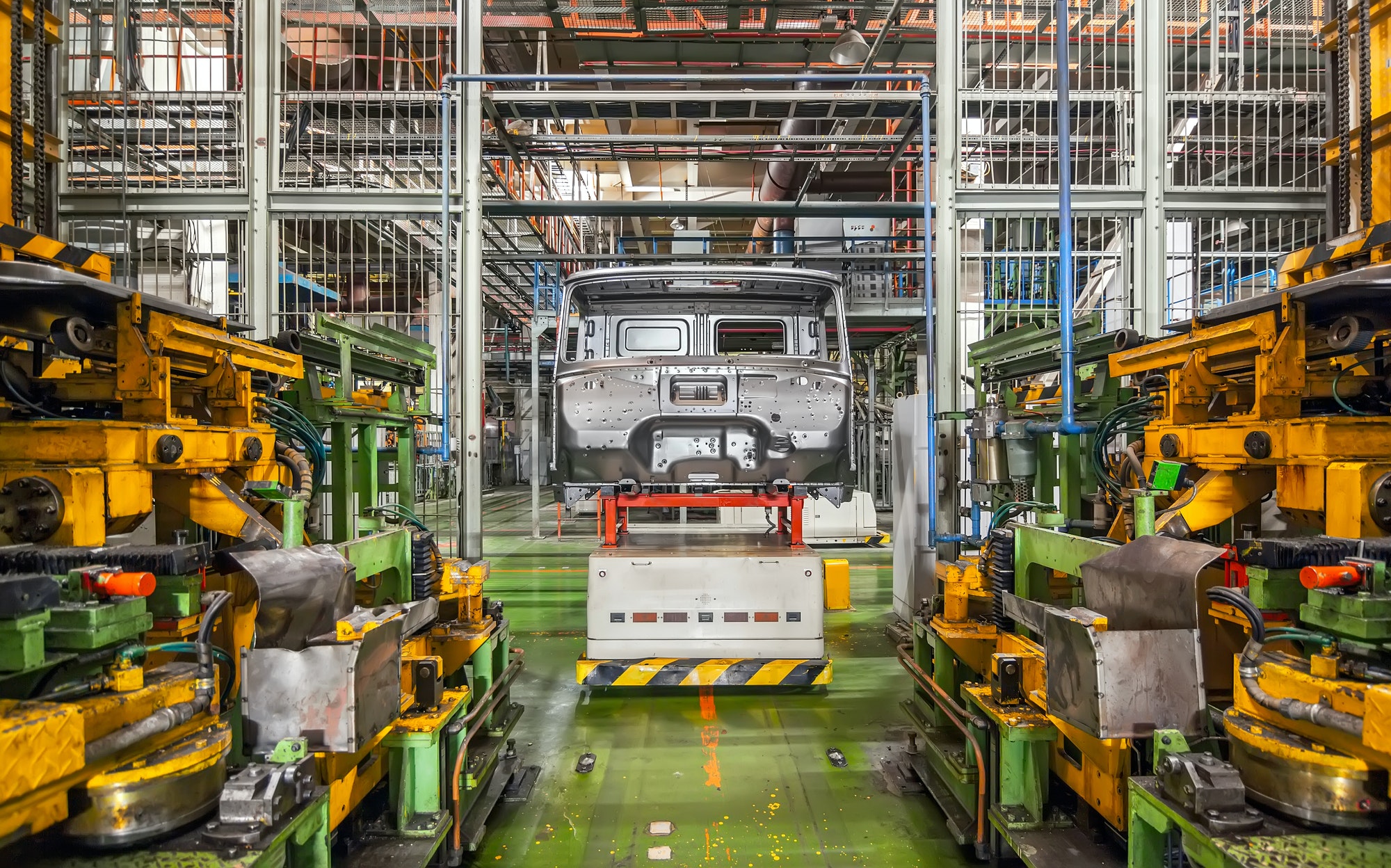
Automotive
PFMEA has helped automotive manufacturers to avoid high-risk failures resulting in mass recalls. Automakers also have relied on PFMEA to make safety improvements to their vehicles. For example, proximity parking sensors now help prevent crashes and unnecessary expenses on repairs. Other safety features that have been improved through PFMEA include airbag deployment and the inability to remove ignition keys while in Park mode.
Manufacturing
As mentioned above, the manufacturing industry is a significant user of PFMEA. Manufacturers rely on the methodology to deal with potential process failures before costly repairs down the line. As reported by Oden, manufacturers routinely lose millions of dollars in revenue because of unplanned downtime. In addition, the mistake-mitigating methodology safeguards quality controls and deliverables.
Healthcare
Accident prevention hasn’t historically played a significant role in medical practices. For whatever reason, many hospital systems weren’t designed to safeguard doctors, nurses, and administrative workers from making tragic errors. But that began to change when the industry adopted healthcare PFMEA to reduce the likelihood of facility power failures, MRI machinery malfunctions, and numerous other risks.
Software development
Software FMEA focuses on eliminating engineering deficiencies that lead to wonky software programs, unreliable user experiences, and costly mistakes that developers must later correct. The methodology guides engineers through a sequential process for identifying missing program requirements, analyzing software system responses to external requests, uncovering hardware malfunctions, and preventing single-point failures from becoming catastrophic failures.
Transport and logistics
The transportation and logistics industry has come a long way since coining the term “supply chain” during the 1980s. During this time, increased global planning, loading, and turning over of goods motivated industry leaders to seek new process improvement systems. Today logistics players use PFMEA to evaluate logistics bottlenecks, optimize routes, and improve customer service delivery.
Agriculture
Lastly, the agricultural industry has been known to use PFMEA. Farmers assess environmental, equipment, and production risks that could impact product quality. Not only are such systems essential for productivity, but they also provide a layer of protection against ethical, legal, and environmental ramifications.
Other industries that benefit from performing PFMEA are electrical component production, oil and mining, and chemical processing. Regardless of industry or size, businesses need to determine process risks as early as possible. Proactive diligence makes it easier to brainstorm risk mitigation plans, identify and inspect required materials, and minimize the impact of failure modes on both production and safety.
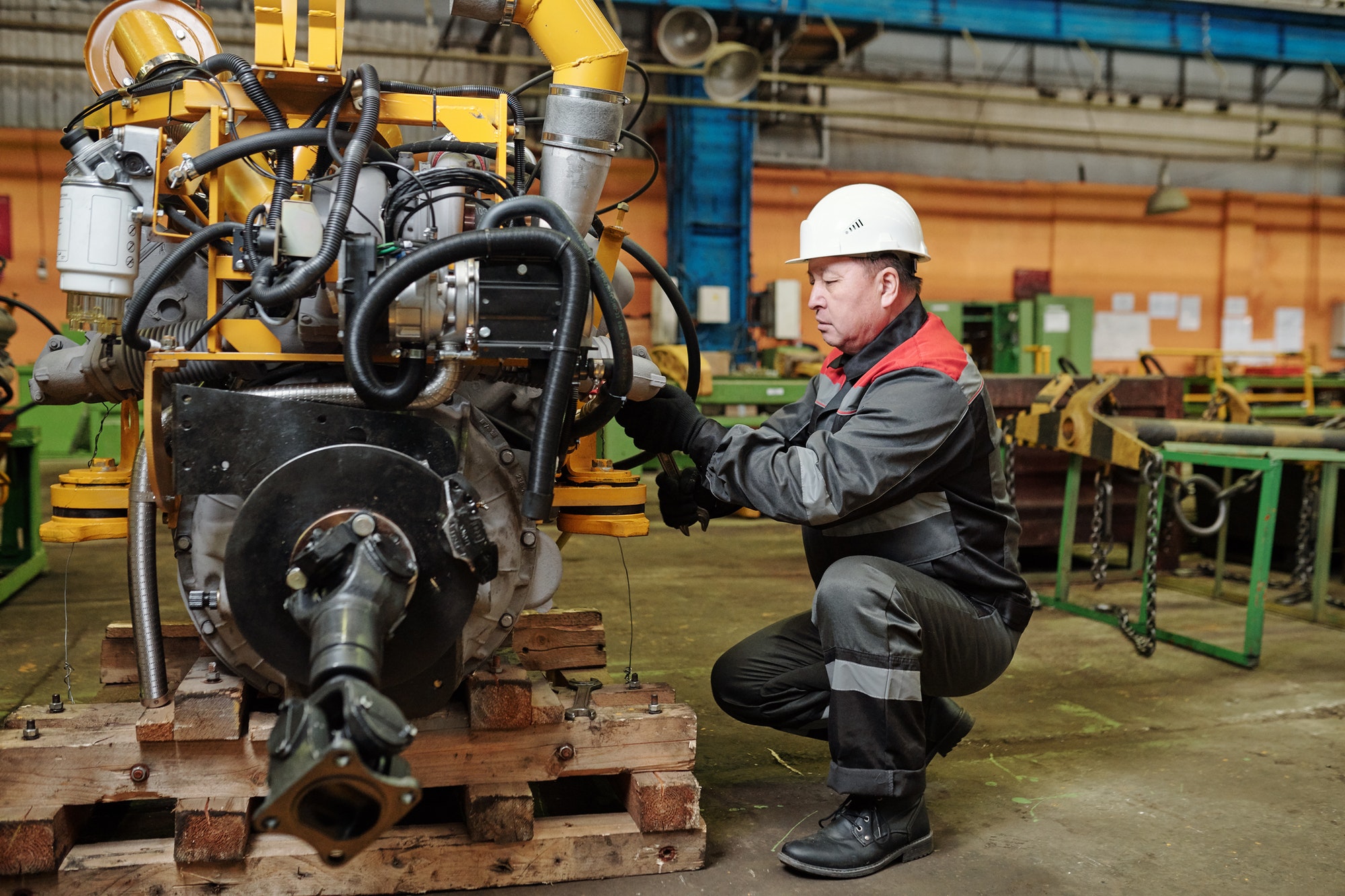
Benefits of PFMEA
At its core, PFMEA is an analytical tool to reduce risk. Here are some of the benefits that coincide with minimizing the various risks associated with production processes:
1. Prevent costly failures
Failure is inevitable, and staying on top of failure modes won’t guarantee their absence. But performing PFMEA can significantly reduce the likelihood of costly setbacks due to process malfunctions. The process helps leaders better understand how workflows, procedures, and machines might fail. And, as the saying goes: knowledge is power.
2. Promote process correction, prevention, or redesign
PFMEA enables organizations to monitor critical process parameters and develop effective process control plans. You can rank potential failure modes according to how difficult it is to detect a failure mode, how severe the failure would be, and how frequently it would occur.
You can also measure how different failure modes impact both internal and external customers and prioritize maintenance actions.
3. Reduce development and production costs
As a business, it’s essential to continually seek new ways to reduce product development and production costs. However, the challenge is how we accomplish this without sacrificing quality, performance, or safety standards.
PFMEA helps managers find those sweet spots between doing too little and doing too much when it comes to production optimization.
4. Limit customer exposure to failure risks
The average rate of warranty claims for U.S. manufacturers is 1.5 percent. However, computer, automotive, and medical equipment manufacturers have higher warranty claim rates than the national average. Warranty claims can leave a significant dent in profits.
PFMEA enables organizations to identify process variables and eliminate defects that may result in warranty claims. The process helps inform detection guidelines to allow workers to identify product defects before shipping items to customers.
5. Improve safety
Last but not least, businesses use PFMEA to identify safety concerns. This mitigates work environment hazards and protects consumers from harmful interactions with products and services. All employers have an obligation under OSHA standards to provide a safe working environment for their employees.
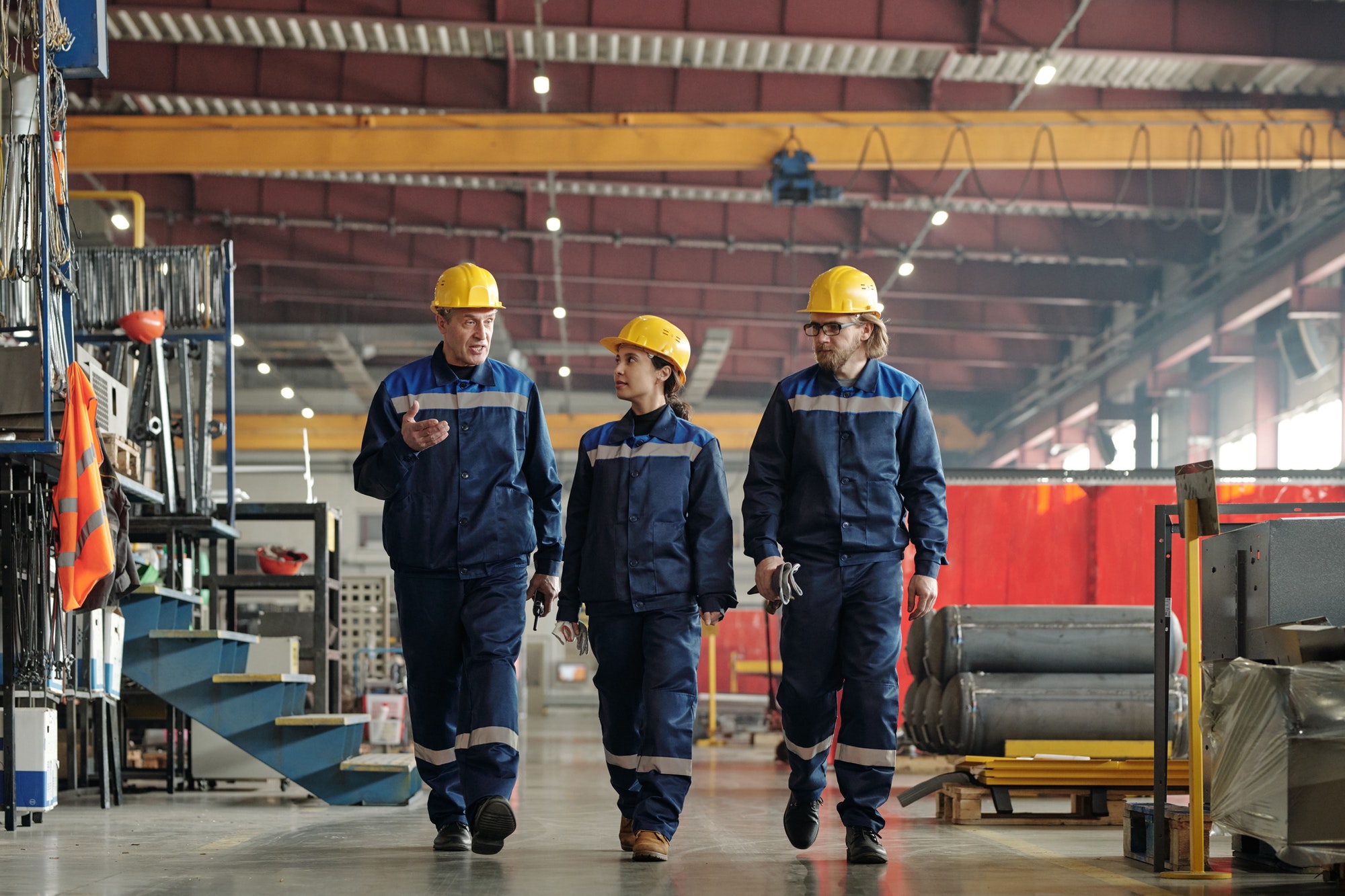
When to perform PFMEA
As previously mentioned, PFMEA is a risk assessment tool for evaluating potential failures in operational processes that harm products and services. Though organizations use the methodology within several contexts, they most often use it during:
- New process introductions: Perform PFMEA when introducing new procedures to departmental teams. Ideally, leadership uses the analysis before implementing new processes to identify proper equipment care, tools, and production needs.
- Process adaptations: Engage PFMEA when modifying existing processes. Any changes to production methods, types of machinery, and transportation can negatively impact multiple factors that cause chain reactions.
- Quality risk assessments: If you suspect a scenario in which quality is or could be compromised, use PFMEA to help create corrective actions. Process failures can result in defective products and customer returns that, in turn, decrease bottom lines.
- Business relocations: Has your facility recently moved to a new location? If so, it’s an ideal time to conduct a failure analysis to assess potential production risks in the new environment. Taking such precautions is essential regardless of whether current process controls remain the same.
In summary, conduct a Failure Mode and Effects Analysis anytime there’s a change in “business as usual.” Regardless of how small the difference is within your production department, it’s vital to evaluate how it may affect related processes in unsuspecting ways.
While it’s impossible to eliminate failure modes, manufacturers can benefit from minimizing them with routine analysis systems.
PFMEA helps organizations achieve operational excellence and receive all the benefits of decreased downtime, increased profitability, and enhanced customer satisfaction. Put simply, it’s not something you do once and forget about it!
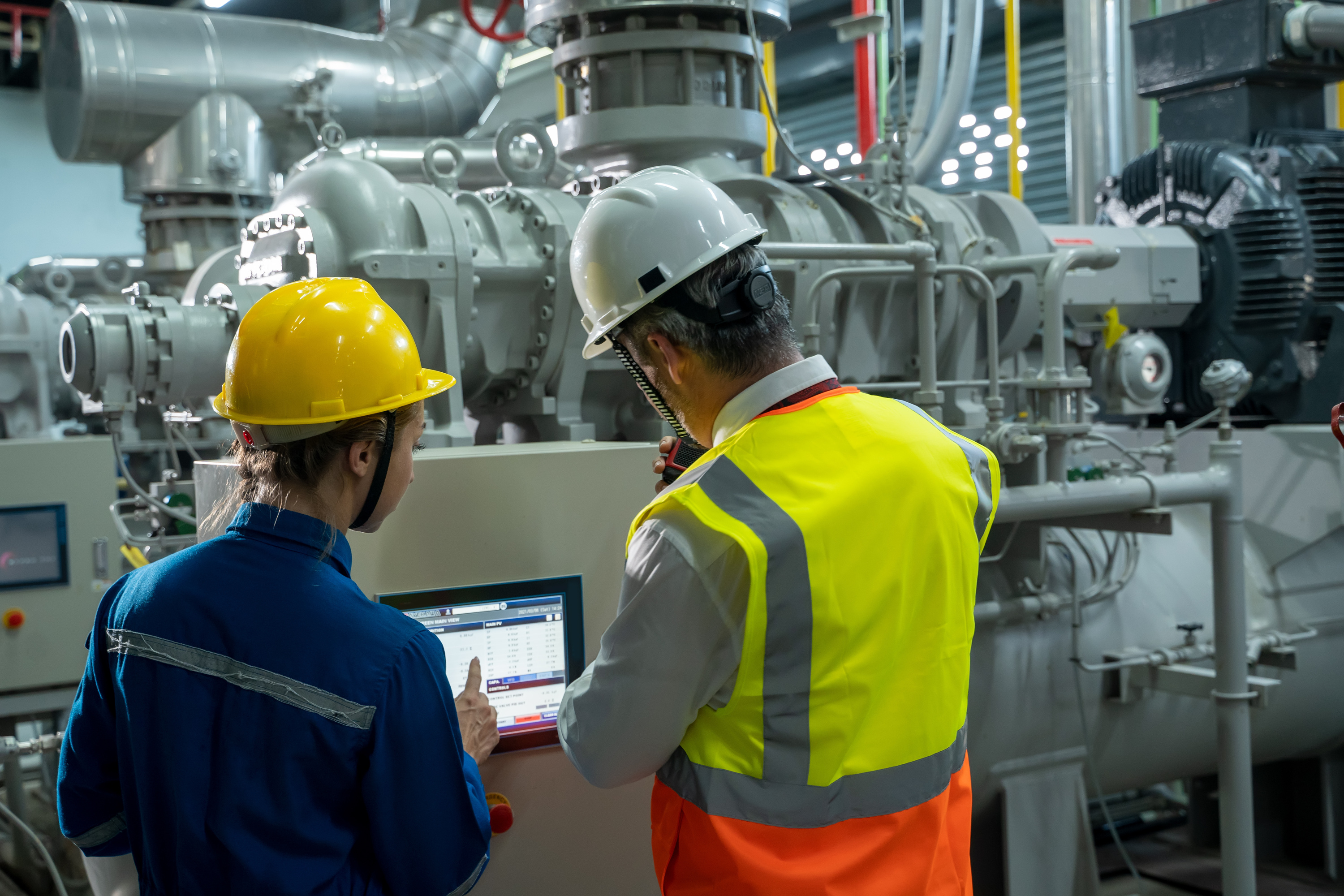
How to run process failure mode and effects analysis (PFMEA)
Obviously, most organizations aim to develop efficient processes that deliver optimal results from the beginning. However, unforeseen design flaws, quality issues, and bottlenecks can sometimes cause processes not to work as originally intended.
One of the easiest places to start fine-tuning your facilities’ processes is the maintenance department. Here’s a step-by-step guide on how to get started:
Step 1: Perform a process review
Start with the processes most integral to your operational functionality. Use flowcharts to illustrate all process tasks—from input to output—and gather historical data to inform the review. Process reviews serve three primary purposes:
- They ensure every PFMEA team member, especially those who don’t interact with the processes daily, is familiar with process components.
- They enable team members to identify the procedures involved.
- They reduce the likelihood of forgotten process components.
In addition, you should review all the requirements for the process under review. Ask yourself: What are the inputs needed for each one? Who is involved? And what role does each worker play?
Step 2: Identify potential failure modes
When identifying potential process failure modes, analyze historical documentation and maintenance data for clues. This will enable you to do a thorough analysis and identify all of the ways processes can falter. The five types of failure modes include:
- Full failures: Completely broken down; equipment possibly needs replacement.
- Partial failures: Still functional, but some components aren’t running correctly.
- Intermittent failures: Occur irregularly with no discernible pattern of occurrence.
- Degraded failures: Weakened parts cause fatigue over time.
- Unintentional failures: External process components are at fault.
Note: processes and their components can have multiple potential failure modes. Factors such as operating conditions, process deployment, and service operations can all cause setbacks. Work together to brainstorm and document all conceivable causes of failure.
Step 3: List potential effects of each failure mode
At this stage, determine the potential effects of failure modes documented in the previous step. What would be the impact of a failure mode if it were to happen? Failure modes can impact the process itself, process end-users, other business operations, internal and external customers, and the environment.
The effect should directly impact the ability of the process in question, or its components, to perform intended functions optimally. It’s essential to recognize that a single failure mode can have multiple effects. When documenting potential outcomes, you should be detailed and descriptive to avoid ambiguity.
Step 4: Assign severity rankings
Severity rankings help you to determine how critical the effects of each failure mode would be. The question to ask at this point is how severe the consequences of failure would be. Answering this question is key to prioritizing maintenance actions based on the severity of the setback.
The rankings are usually done on a scale of 1 to 10. A high score means that the consequences of failure are very severe, and the failure mode shouldn’t be overlooked under any circumstances. Alternatively, failure modes with low severity rankings may not necessarily impact process functionality.
Step 5: Assign occurrence rankings
Use occurrence rankings to determine the frequency in which a given failure mode is likely to occur. To assign occurrence rankings, first determine the potential causes of process failure.
Consider using the 5-Whys Technique to identify the causes of the identified failure modes. The occurrence ranking will be influenced by the likelihood and frequency of the cause happening.
Also, look at existing process controls that could help prevent the failure from occurring. Just like severity rankings, high occurrence rankings mean the likelihood of failure is very high.
Step 6: Assign detection rankings
Next, determine the ease of detecting the failure mode before it occurs and assign it a detection ranking. To do this, evaluate process controls currently in place for each failure mode and determine how effective each control is in identifying failure before it occurs.
Process control can be for the failure mode itself, its causes, or the impact of failure. A detection ranking of 10 means it’s nearly impossible to identify failure before it occurs. It means you have no controls in place to identify the failure mode. A lower detection means that you’re confident in your ability to identify and mitigate the threat.
Step 7: Calculate the risk priority number (RPN)
At this point, you’re ready to calculate the failure mode’s risk priority number (RPN).
RPNs help rank your failure modes from most urgent to least urgent. This, in turn, can help inform preventive maintenance scheduling priorities. As noted above, to calculate the RPN, simply multiply the three rankings (severity, occurrence, and detection). Focus your maintenance efforts on failure modes with high RPNs and find ways to lower the number.
Step 8: Develop an action plan
At this point, you have all the information about the concerned process, its various failure modes, and the impact of each failure mode. This includes how often the failure modes are likely to occur, the severity of the effects, and controls to detect each failure mode.
You have also calculated the RPN and know which failure modes to prioritize. The next step is to develop an action plan to keep them from happening.
As a team, determine the process improvements and who will be responsible for completing them. Also, clearly define the timelines for initiating and completing the assigned actions.
Step 9: Execute the plan
At this stage, implement the improvements and actions as outlined in your plan. Put in place standard operating procedures (SOPs) for implementing the action plan.
This will help ensure everyone stays on track. We recommend assigning digital SOP checklists via CMMS maintenance software that detail compliance in real-time, provide digital audit trails for review, and include work order commenting functionality for enhanced team communication.
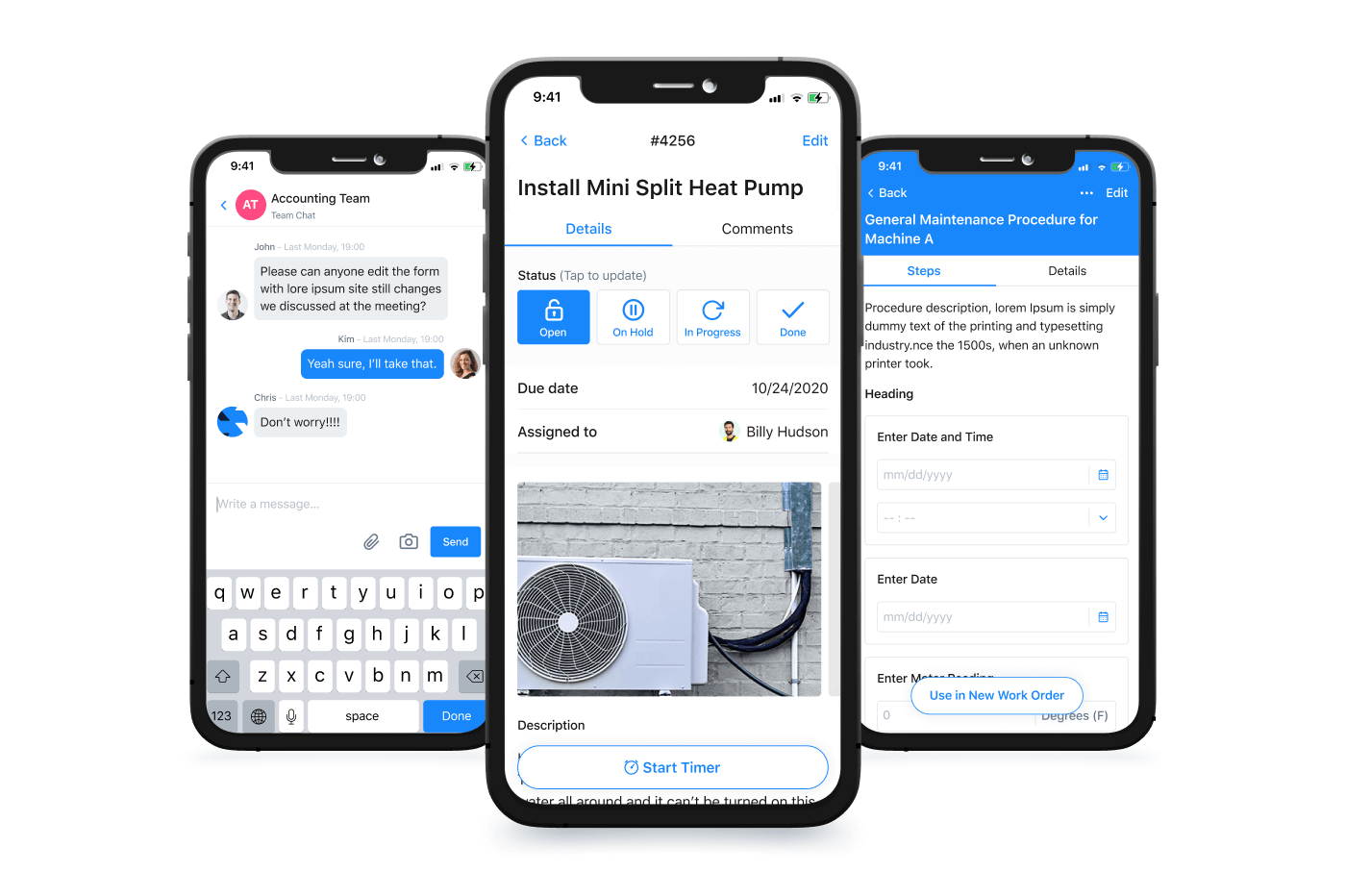
Step 10: Recalculate your RPN
After the recommended improvements have been implemented, determine how effective they are in practice. Reevaluate each failure mode and reassess its occurrence, severity, and detection rankings after improvements have been made.
Recalculate the RPN for each failure mode to assess if progress has been made.
Streamline asset management with MaintainX
PFMEA isn’t a magic bullet for perfecting business processes. But it’s still an invaluable risk assessment method that can increase bottom lines, enhance safety, and improve quality management.
Before initiating an effective PFMEA program, provide your FMEA task force with meaningful historical data related to failure mode objectives. One of the most efficient ways to organize equipment-related information is with a CMMS (computerized maintenance management software) like MaintainX.
Our mobile-friendly platform allows PFMEA teams to catalog, analyze, and act on maintenance-related metrics. It also makes creating, assigning, and monitoring work orders in real-time a breeze!
FAQs
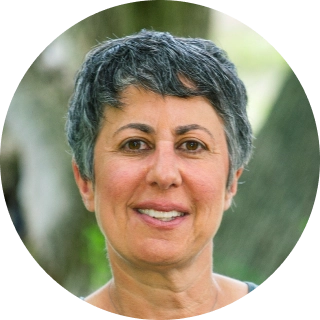
Caroline Eisner is a writer and editor with experience across the profit and nonprofit sectors, government, education, and financial organizations. She has held leadership positions in K16 institutions and has led large-scale digital projects, interactive websites, and a business writing consultancy.