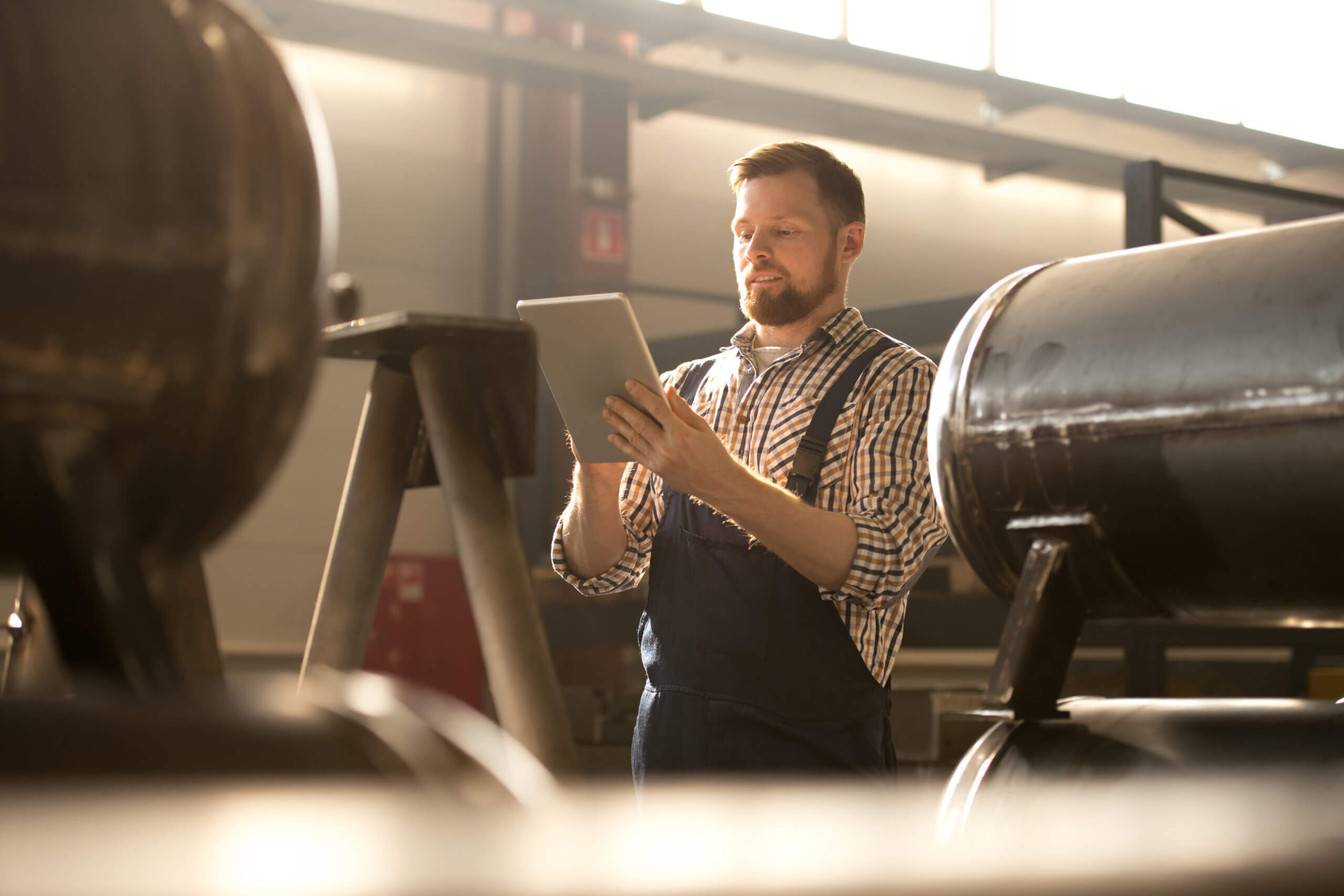
Implementing a systematic way to carry out maintenance and perform tasks is more important than you may initially think. Standardization of maintenance processes can keep equipment online, improve products and services, and help a firm avoid costly unplanned downtime. In addition, there are plenty of other benefits of standardization for your company’s bottom line and overall business success.
In this post, we dig deeper into standardization and discuss what it is, why it’s essential, and how to improve it across your maintenance teams.
“Over the past seventy years, [the] focus on the reduction of waste and process variability through rigorous standardization and continuous improvement has transformed operational performance in many industries. More recently, the growth of Industry 4.0 and related digital technologies has brought a new methodology onto the scene.”
McKinsey
Importance of Standardization
Let’s start by discussing the definition of standardization. Simply put, it’s the process of making something conform to a standard or implementing a systematic way of doing things.
Look around, and you’ll see plenty of examples of standardization. There are global standards, such as those from the International Organization for Standardization (ISO). ISO product standards are de jure (which means “according to the law”) international standards agreed upon by experts. Other industry standards include the American National Standards Institute, or ANSI, which facilitates and coordinates voluntary standards and conformity assessments in the United States. The International Electrotechnical Commission (IEC) is another standards organization that publishes international standards for electrical-related technologies. You can see more location- and industry-specific standards, such as telecommunications and operating system standards—you name it.
Standards are everywhere—and not all are governed or established by any organization, interest group, or institution. As a result, companies can establish and implement standard operating procedures (SOPs) to streamline pricing, metrics, and other business processes—and the benefits of doing so can be far-reaching.
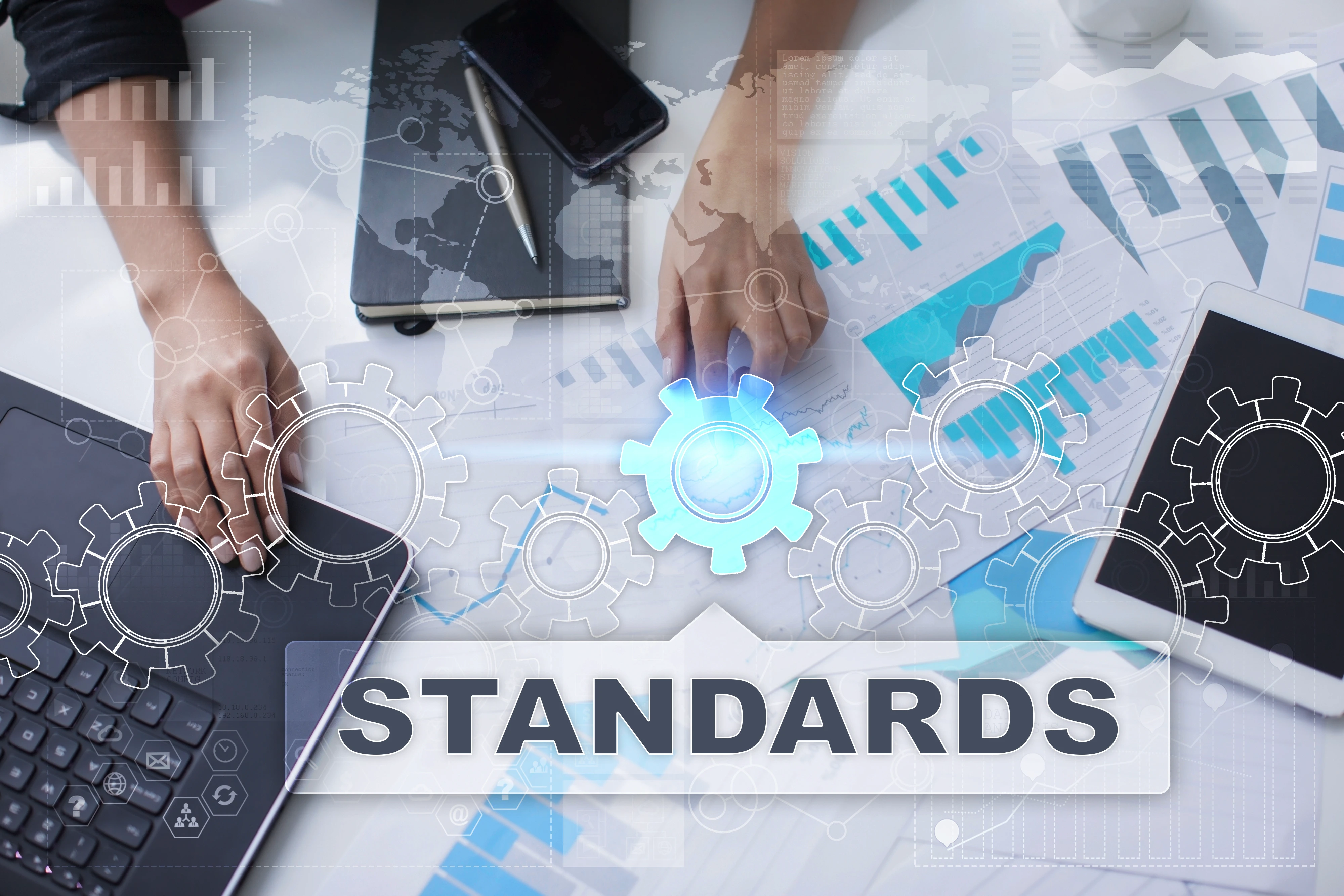
Benefits of Standardization
What are some of the benefits of standardization? As we just noted, they can be far-reaching and include the following:
Creates Lean Operations
Standardization can help eliminate inefficiencies and lead to a leaner overall work environment. For example, it can help eliminate wasted time searching for tools or materials or time spent adjusting equipment out of standard settings. What’s more, when a company standardizes equipment maintenance, it’s likely to lead to sustainability benefits and equipment that runs more consistently and predictably.
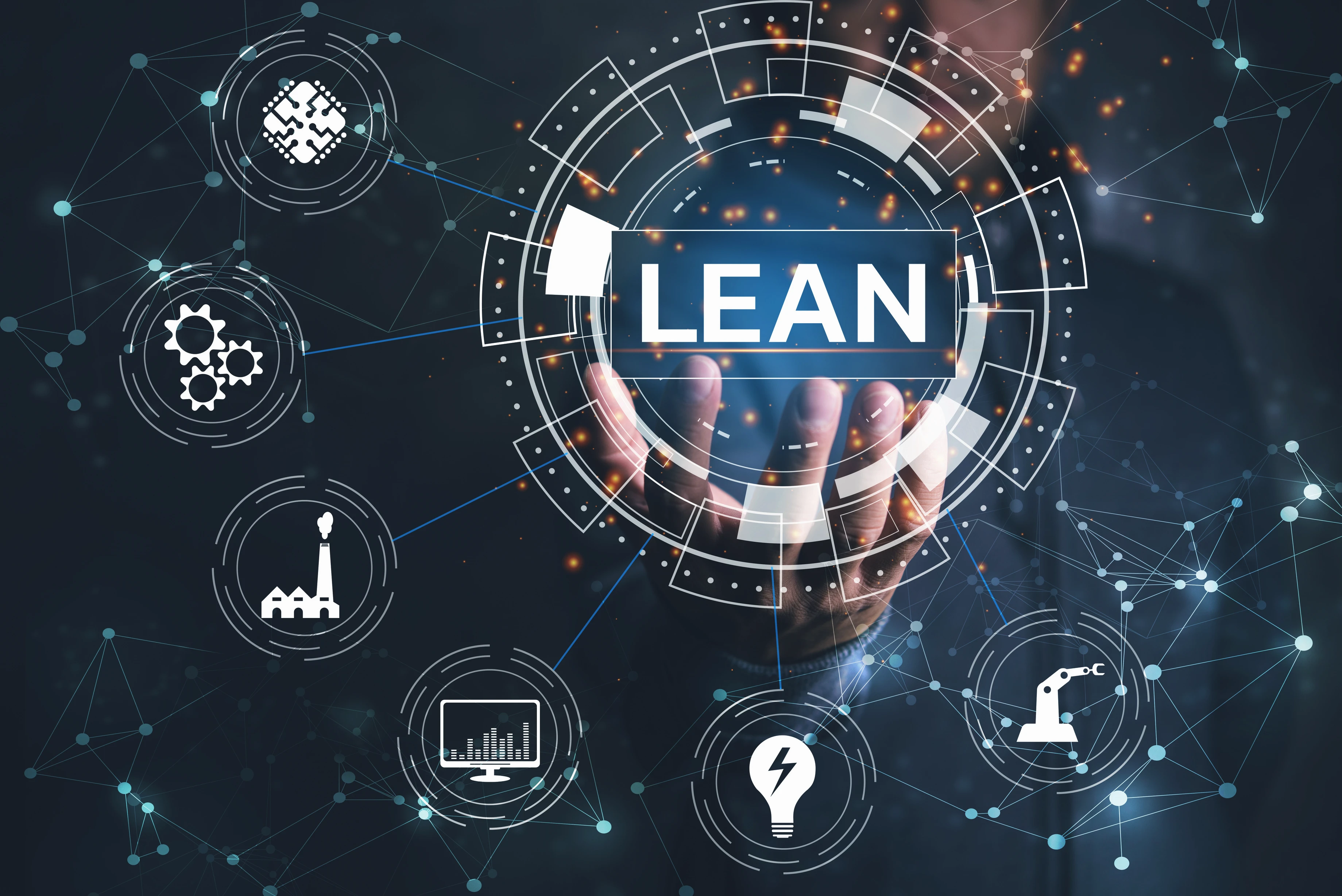
Improves Moral
Studies show that a happier overall workforce is often a more productive workforce. Managers can implement new ways of working by eliminating the more frustrating tasks. A happy workforce isn’t often just more productive, but also more content with its work and less likely to look for other opportunities, minimizing turnover.
Reduces Costs
Beyond better equipment maintenance and streamlined processes, standardization can improve purchasing decisions and inventory stocking. Creating uniform packaging and enhancing storage options make a difference. But, often, it’s not a significant change that makes a difference.
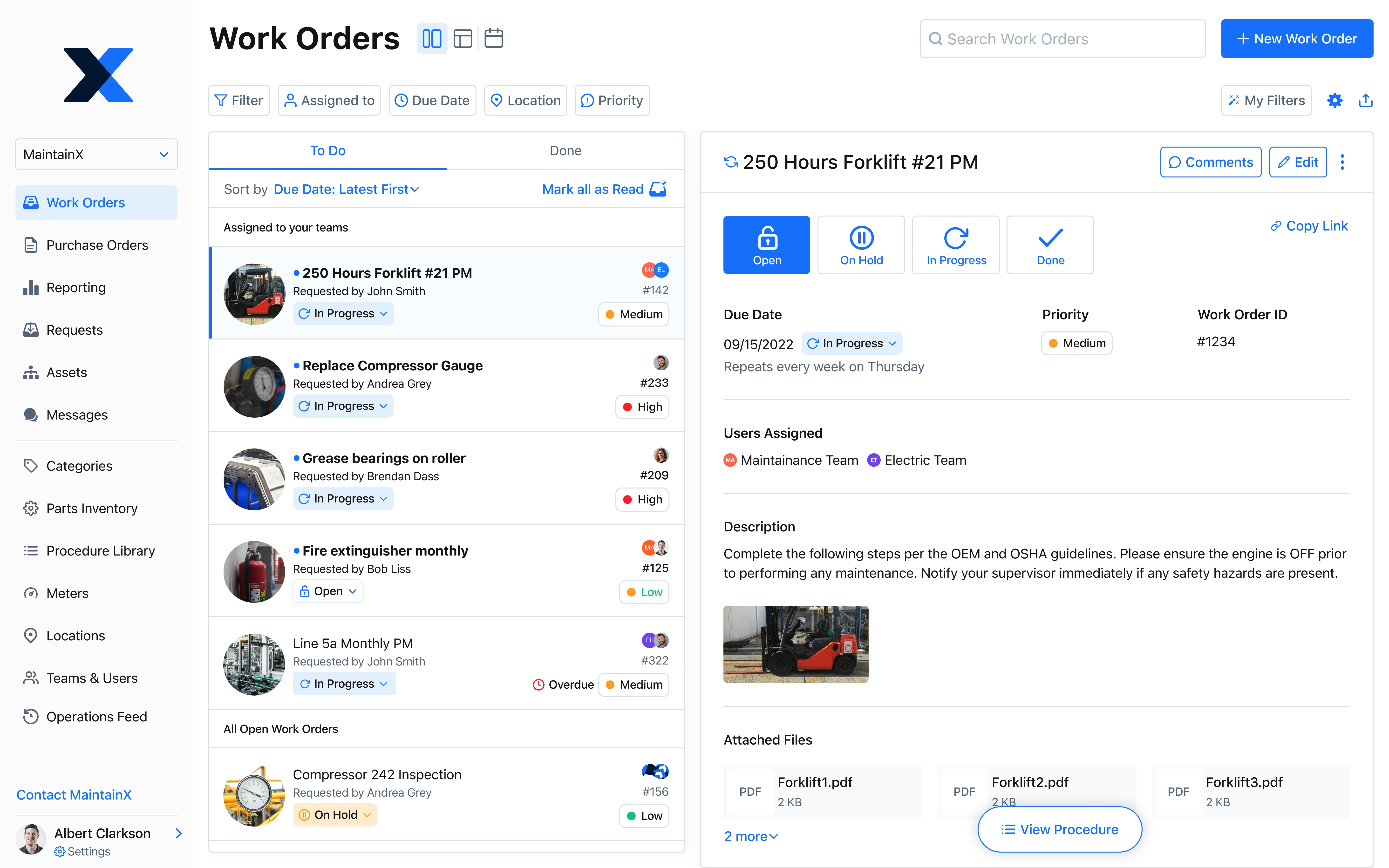
How to Standardize Business Processes
A lack of standardization can hurt a business—and it might not even realize it. So how can a firm improve standardization processes? First, let’s look at a few generally accepted ways to standardize a company’s productivity, efficiency, and profitability.
Adopt a Robust CMMS Program
A computerized maintenance management system, or CMMS, can streamline standardization processes regarding equipment maintenance, ensuring equipment runs better for longer. In addition, adopting a planned maintenance program, complete with digital standard operating procedures, allows companies to avoid costly unplanned downtime.
In today’s ever-evolving world of Industry 4.0, a robust CMMS program, like MaintainX, captures data on equipment performance and tracks work orders. Using a CMMS to manage maintenance makes it easy to use approved procedure checklists and hold workers accountable. MaintainX captures real-time data and reports KPIs (such as MTBF and MTTR) via cloud-based reporting features. As a result, compatibility and interoperability are maximized.
Using the best CMMS isn’t just an effective way to help with standard normalization but is also affordable. For example, preventative equipment maintenance, spare parts inventory management, and work order standards save money by reducing costly downtime and increasing employee and customer satisfaction. And being that CMMS programs are cloud-based, data can be accessed from anywhere there’s an internet connection.
Double Down on Equipment Maintenance Workflow
A CMMS program helps organize equipment maintenance workflows. Various equipment maintenance strategies, such as condition-based maintenance, predictive maintenance, and reactive maintenance, can be implemented. Most experts believe that the best equipment maintenance strategy includes elements from all industrial maintenance workflows.
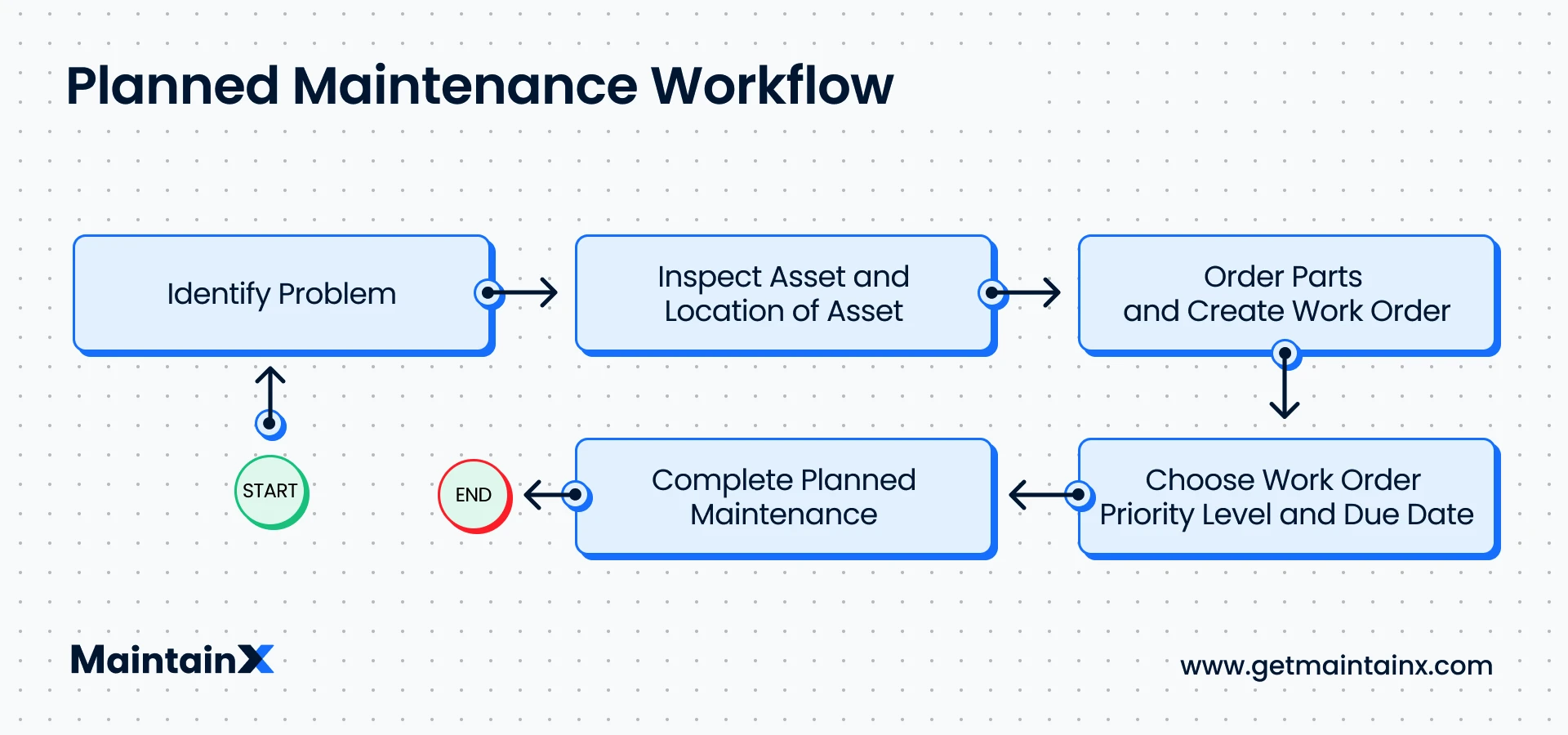
Focus on Improving
Finally, a company should never establish or adopt standards only to let them slide. Instead, establish key performance indicators (KPIs) and focus on continuous improvement. If continuous improvement is not a priority, the company will likely struggle to establish competitive advantages in the market.
Implement a CMMS to Standardize
Standardization helps companies increase productivity and improve efficiency. In today’s competitive marketplace, an essential cog in any industrial maintenance machine is a nimble CMMS.
Book a tour to learn more about how MaintainX can help.
FAQs
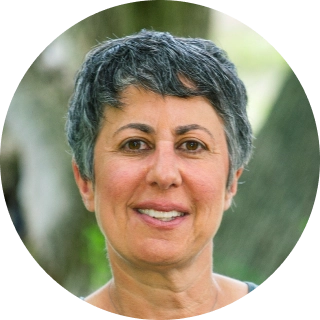
Caroline Eisner is a writer and editor with experience across the profit and nonprofit sectors, government, education, and financial organizations. She has held leadership positions in K16 institutions and has led large-scale digital projects, interactive websites, and a business writing consultancy.