
Maintaining optimal inventory levels is tricky. The type of system you choose will depend on your unique business model. Inventory management systems range from surprisingly simple to exceedingly complex. In this article, we’ll delve deeper into the world of maintenance inventory management before sharing the most important information you need to know when evaluating software options.
Overstock, and you risk tying up precious capital that you could reinvest elsewhere. Understock, and you risk losing money on equipment downtime, delayed shipments, and customer dissatisfaction. Either way, mismanaging inventory erodes a company’s bottom line.
For these reasons, developing a foolproof inventory management system is essential to long-term operational success. What’s the best way to accurately track, control, and optimize your supplies?
With maintenance inventory software, of course! Modern inventory management systems combine cloud-based software with standard operating procedures (SOPs) to monitor tangible business assets in a digitized central location. Inventory items can include raw materials, parts, and deliverables ready for customers.
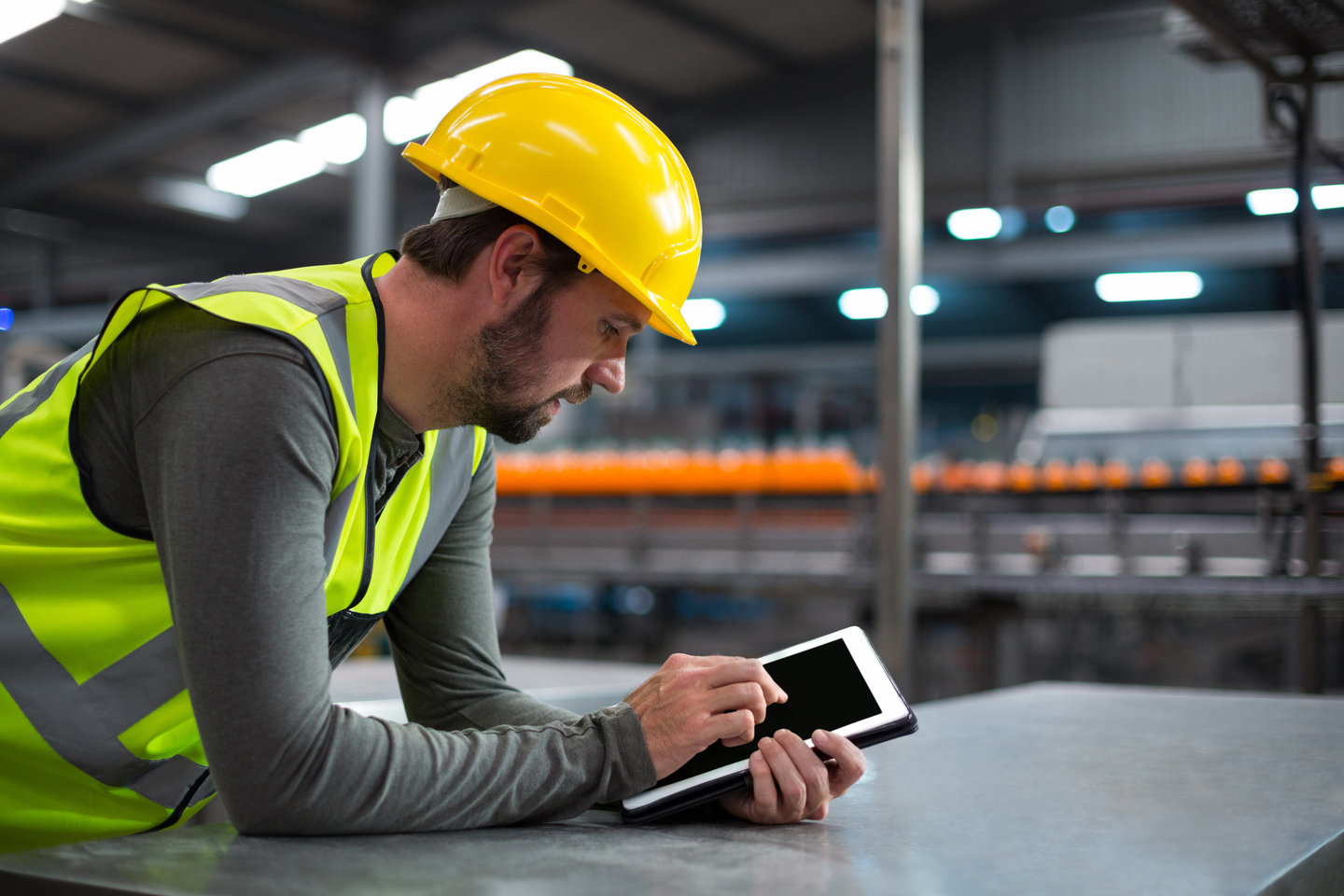
Streamline O&M with Maintenance Inventory Software
Inventory mismanagement is widespread across multiple industries.
Case in point: a Management Science analysis of nearly 370,000 inventory records from 37 retail stores found 65 percent of stores to have inaccurate inventory records. In many cases, such gross inaccuracies negatively impact an organization’s ability to meet customer demand.
Inaccurate inventory records also lead to stock-outs, market changes, and over-purchasing. According to Granite Bay consulting, reducing inventory inefficiencies by 50 to 80 percent can significantly increase market shares and profitability.
Of course, most company executives initially associate inventory with the supplies needed to make products and perform services. However, upon closer examination, maintenance storeroom shelves hold equally valuable forms of inventory.
Efficiently stocked parts, materials, and tools provide maintenance technicians with everything they need to keep critical machinery running smoothly.
Depending on the business, delayed equipment downtime due to parts unavailability can dramatically affect profitability. In the auto industry, downtime can cost up to $50,000 per minute, which translates to a whopping $3 million per hour.
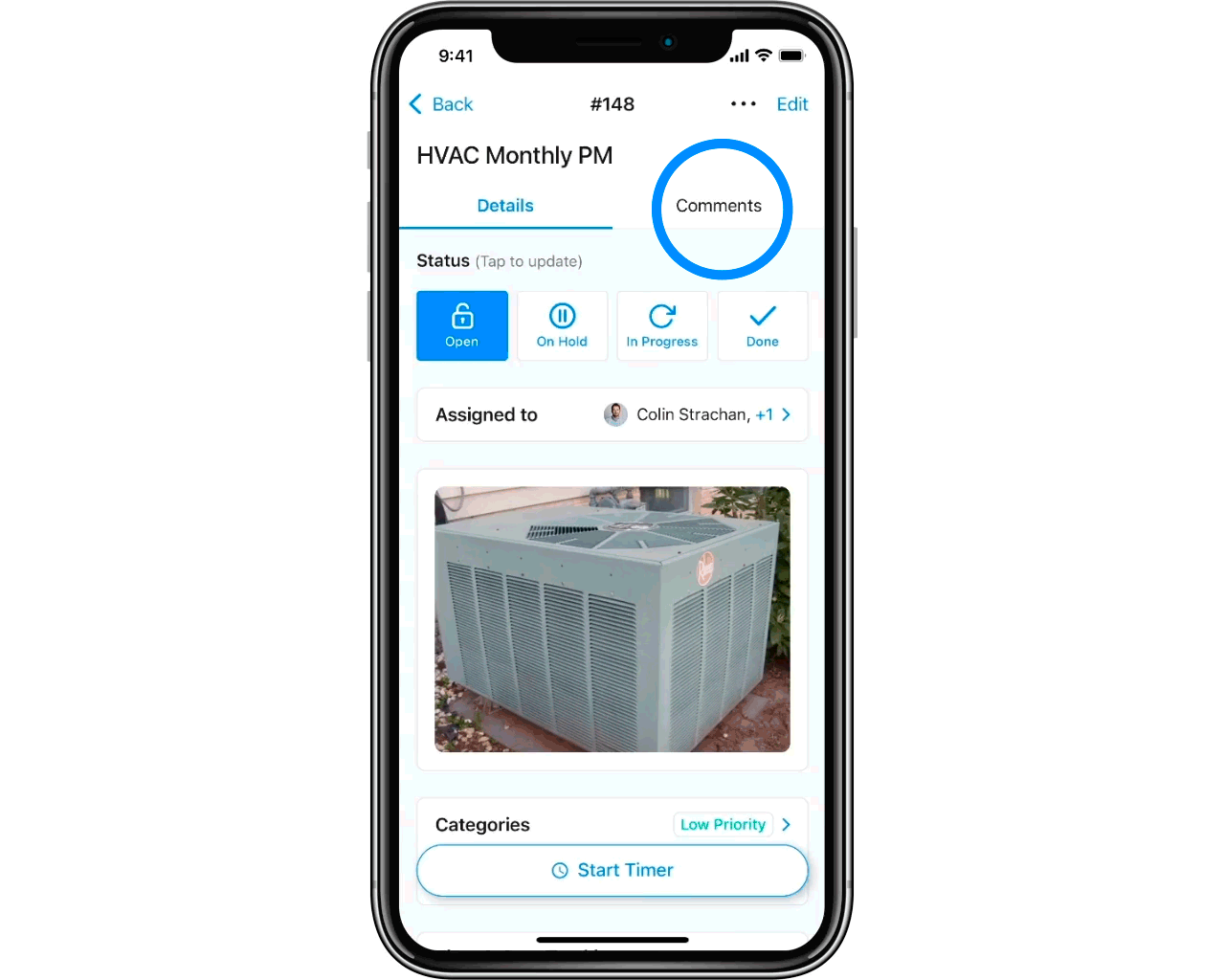
Benefits of Maintenance Inventory Software
Just as inventory management software provides a bird’s eye view of company supplies, maintenance inventory software streamlines the management of equipment parts.
Also known as spare parts inventory, maintenance inventory solutions allow operational leaders to proactively maintain a pulse on supply levels. Notably, they maintain accurate counts of the number of materials/replacement parts available, their location, and their association with specific work orders.
It’s worth mentioning that most maintenance inventory platforms are built directly within computerized maintenance management systems (CMMS)—a centralized platform that allows managers to create, assign, and monitor PMs; digitize SOPs; centralize team communication; and track key performance indicators (KPIs) to evaluate program success. Benefits of using CMMS and maintenance inventory software include:
Minimized Storage Costs
Maintenance inventory management software assists its users in making more economic order quantity calculations. This is essential to identifying the most cost-efficient method for ordering maintenance material and replacement parts. In some cases, you also may shave off additional warehousing fees.
Minimized Losses
The software provides insights to help departments avoid over-investing in rarely used materials. It can also track and calculate predetermined numbers of units to order upon quantity triggers, thus recommending ideal times to order parts.
Management of Multiple Locations
CMMS inventory management also comes in handy when overseeing multiple locations. You can easily track spare parts’ levels for different facilities in a central place. You also can order products for your locations in bulk, hence not paying multiple shipment fees.
Improved Customer Satisfaction
As previously mentioned, unplanned downtime majorly disrupts production. Several studies have shown the availability of spare parts significantly impacts efforts to restore production. Of course, disrupted production leads to limited product supplies that fail to meet customer demand. Maintenance inventory management software ensures necessary parts are always on hand so critical machinery is restored ASAP.
Reduced Record Inaccuracies
Manually calculating stock levels often results in costly human errors. Analog record-keeping also hogs employee hours that could otherwise be put toward productive maintenance work. Maintenance inventory management software helps eliminate inaccuracies such as duplicate data, thus reducing time-consuming errors.
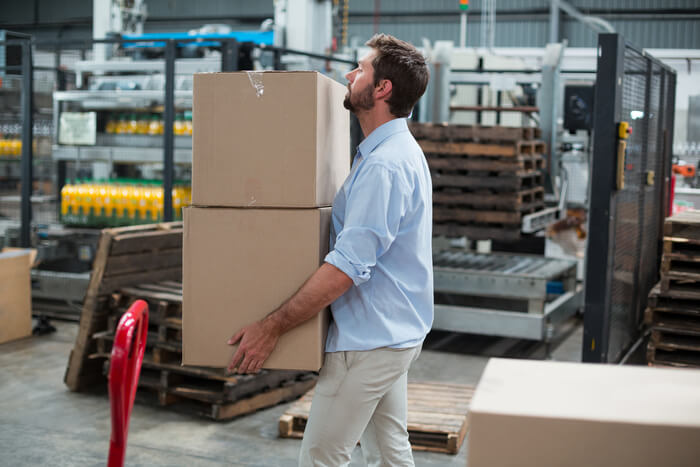
How Do You Manage Maintenance Inventory?
Overall, maintenance inventory management software allows you to enhance productivity in maintenance, save costs, and improve bottom lines. Now that you know the benefits of the software, let’s take a closer look at how to use it effectively. We can break down managing maintenance inventory into seven simple steps:
1. Identify All Parts Systematically
Identify every part needed for each facility maintenance activity. It’s essential to figure out which machines periodically require replacement parts so you’re never left empty-handed in the event of an emergency. Identifying parts also includes inventorying unused parts purchased for one-time use. This preliminary assessment will provide a baseline to build initial inventory counts.
2. Leverage Bill of Materials (BOM)
A bill of materials (BOM) refers to a detailed list of parts and their respective quantities that make up a specific component or asset. BOMs simplify the process of ordering replacement parts and assigning work orders. Update your BOMs regularly to avoid inaccuracies resulting from changed, removed, or new supplies. Maintaining accurate lists reduces the time needed to create both planned and unplanned work orders.
3. Streamline the Work Order Process
Maintenance technicians should always document any parts used after completing an assigned work order. That way, the maintenance department can maintain an accurate inventory count of available parts. Taking this step is especially important to ensure necessary parts are available for emergency maintenance situations.
4. Implement Effective Security Measures
This often-overlooked step may be crucial to maintaining secure and accurate inventory counts. If necessary, limit inventory warehouse access to authorized staff. Spare parts should only be issued in line with approved work orders and strictly monitored. You also may want to install security cameras to monitor entry and exit points for added protection.
5. Consolidate and Centralize Spare Parts
As mentioned above, one of the benefits of CMMS inventory management software is the streamlined management of multiple locations from a centralized platform. Whenever you can, take advantage of parts’ consolidation capabilities. It not only improves inventory security but also makes it easier to maintain and control extensive lists.
6. Utilize a User-Friendly Inventory Control System
Approximately 45 percent of facilities still rely on spreadsheets for maintenance management. If you’re reading this article, you’re probably already seeking a more effective inventory control method. With that said, choosing a user-friendly option is paramount to long-term success. We absolutely recommend MaintainX mobile CMMS for organizations prioritizing extreme usability in a platform.
7. Assign Locations to Parts
Lastly, make it easy for team members to locate parts on the fly. Take the time to match every stock with its corresponding locations. Further, include even the smallest details, such as bin and slot locations. Though it may seem cumbersome upfront, cataloging parts information with such precision will make it easier for technicians to fulfill future work orders.
Again, the easiest way to follow these steps is with the help of a robust inventory management system. Now, let’s look at what we believe is the best CMMS software for inventory management.
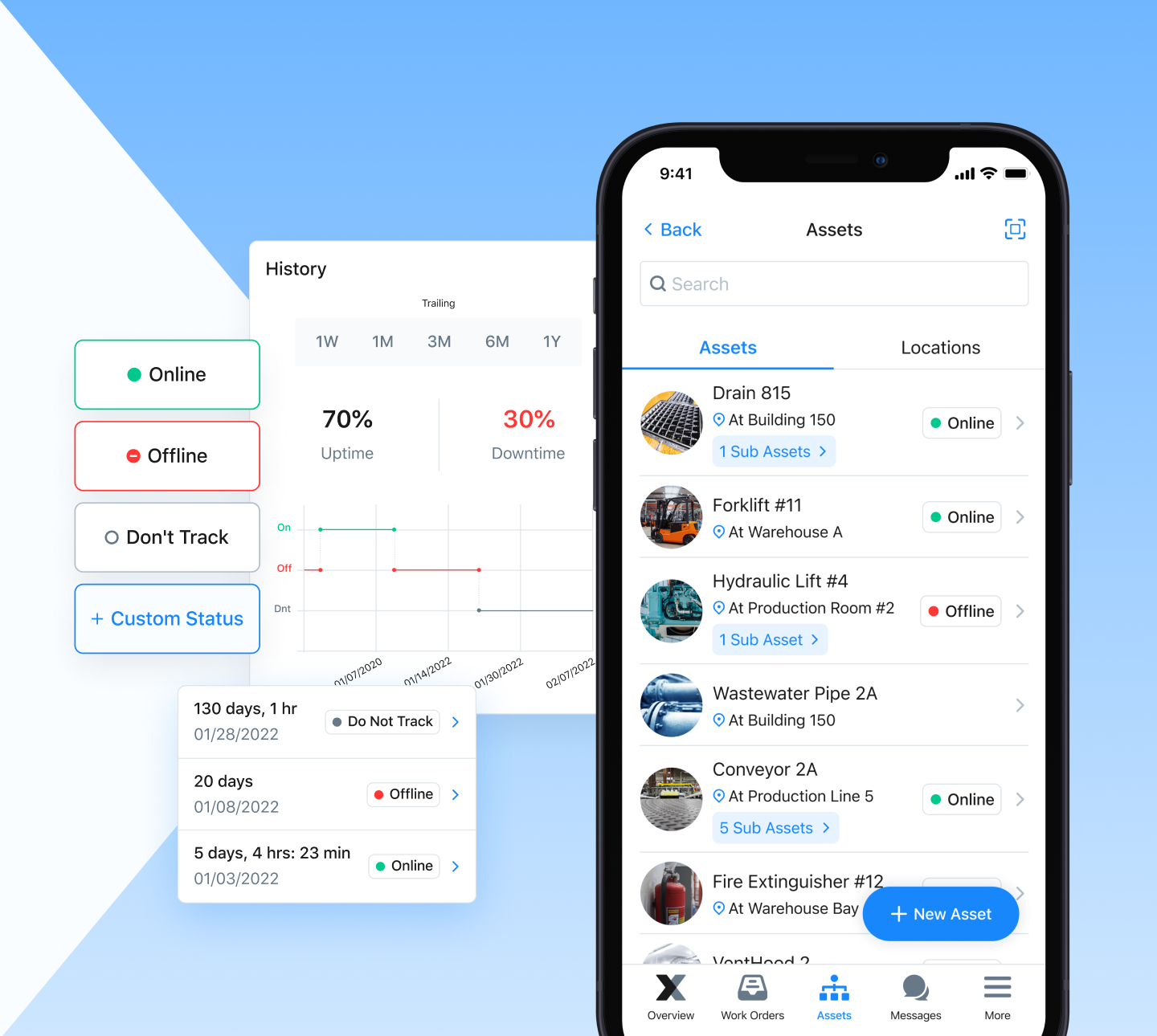
MaintainX: The Best CMMS Software for Inventory Management
Are you ready to save money, increase efficiency, and improve inventory management? If so, it’s time to invest in user-friendly maintenance inventory management software.
MaintainX is the world’s first CMMS designed with inventory management, asset management, work order creation, and team chat on a mobile app. Our user-friendly platform provides several benefits to operational managers seeking streamlined O&M systems, including:
- Low-Inventory Alerts: Set notifications to alert your team when critical spare parts are running low. Customize purchase limits based on your department’s unique needs.
- Cost Tracking and Reporting: Generate reports based on costs of used parts, asset downtime, and Mean-Time-to-Repair (MTTR) to inform capital decision-making.
- Barcode Scanning: Instead of searching for SKUs, quickly add parts to work orders with barcode scanning functionality.
- Digital Audit Trails: Increase team accountability with digitized work orders saved in the cloud for quick accessibility with cloud inventory management.
Find out why global organizations like McDonald’s, Marriott, and Hilton manage their maintenance inventory with MaintainX.
Click here to download the app for free.
FAQ: Maintenance Inventory Software
What Is MRO Inventory?
MRO inventory simply refers to maintenance, repair, and operation supplies. They are supplies, materials, and equipment used in production but don’t make up part of the finished products. Without well-managed MRO products, businesses may face delays in maintenance and repairs, which can lead to costly disruptions in production and operations.
How Does Maintenance Inventory Software Support Preventive Maintenance?
Maintenance inventory software helps maintenance teams keep track of available spare parts to schedule work orders according to parts’ availability. It eliminates inaccuracies caused by human error when calculating stock levels. This makes PM programs more efficient and effective.
Inventory Management Software vs. Maintenance Inventory Management Software
Inventory management software is for general inventory tracking. Anyone who runs a business, large or small, that needs supplies to make products may use it. Maintenance inventory management software, on the other hand, is essentially one part of a CMMS. Operational and maintenance managers use it focused on running preventive maintenance programs and managing equipment parts and inventory.
In most cases, maintenance inventory management software does not directly contribute to revenue generation as inventory management software would. The latter only keeps track of products that are now sold to customers. Maintenance inventory management software keeps track of operational and maintenance items such as:
- Computers
- Laboratory equipment
- Office supplies
- Repair tools
- Cleaning or janitorial supplies
- Valves, compressors, and other industrial equipment
- Gloves, masks, and other safety equipment
Many organizations ignore the importance of good maintenance inventory management software since maintenance inventory doesn’t directly contribute to revenue generation. But if you want to improve your preventive maintenance strategy, then you need one. We recommend MaintainX.
FAQs
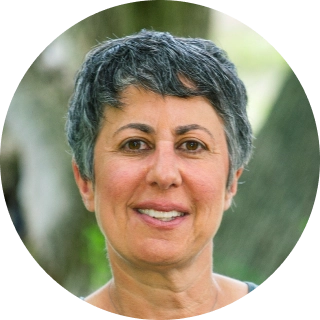
Caroline Eisner is a writer and editor with experience across the profit and nonprofit sectors, government, education, and financial organizations. She has held leadership positions in K16 institutions and has led large-scale digital projects, interactive websites, and a business writing consultancy.