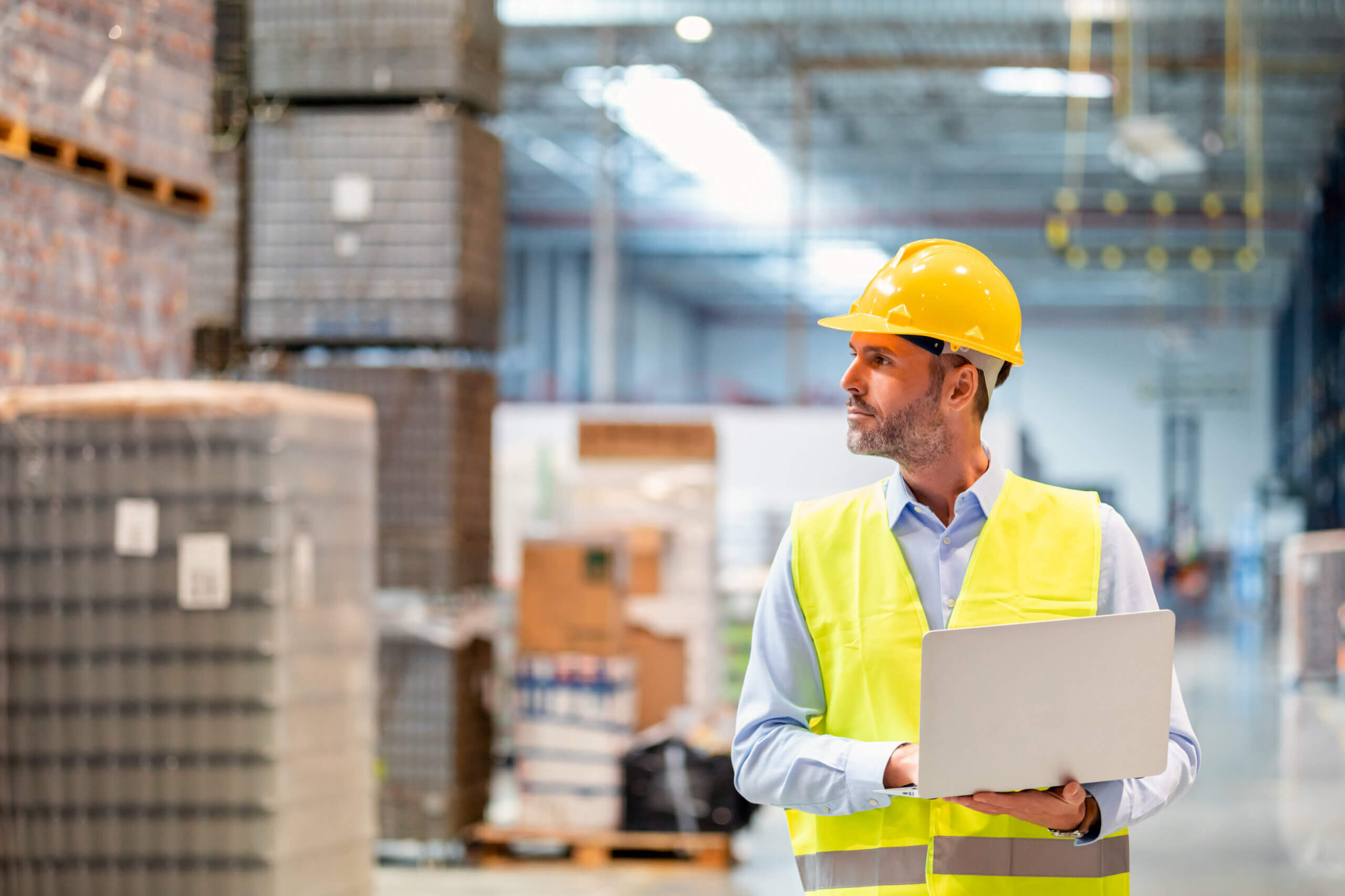
Managing spare part inventory has never been more crucial.
Post-pandemic, we are still reeling from supply-chain vulnerabilities in companies worldwide. As reported by Deloitte, businesses must cast wider partnership nets to meet increasing consumer demands for quick deliveries moving forward.
Supply managers can’t always expect to receive what they need when they need it and from a single supplier without delays. But spare part inventory management has recently come to the forefront of manufacturing conversations for another reason.
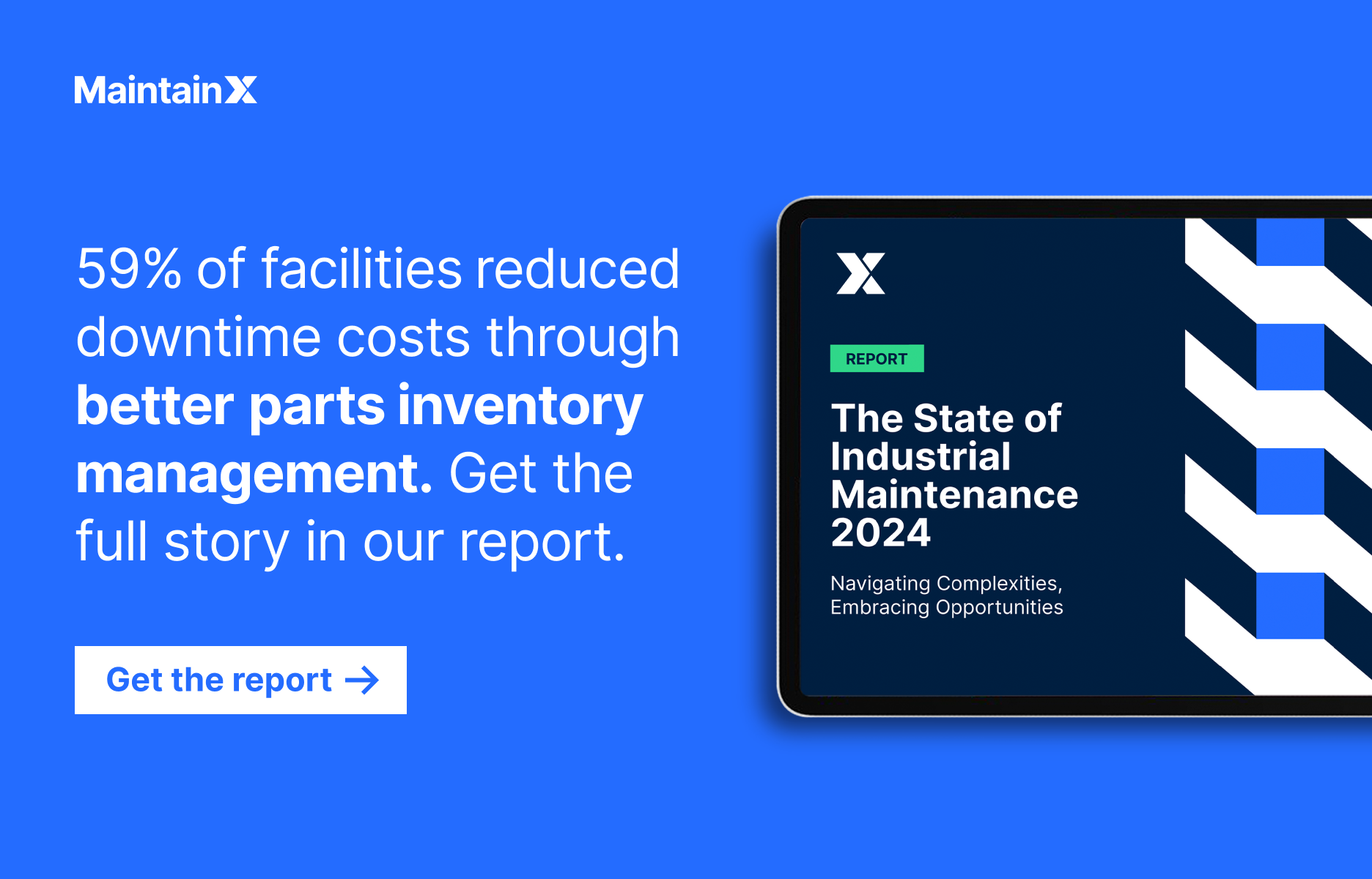
How to Improve Spare Part Inventory Management (and Supply Chains)
U.S. and European lawmakers are increasingly pressuring manufacturers to simplify their product repair processes. As reported by The New York Times, the “right to repair” movement would “require companies to make their parts, tools, and information available to consumers and repair shops to keep devices from ending up in the scrap heap.”
Spare parts inventory management is crucial because replacing parts accounts for a significant component of product life-cycle costs. According to Spare Parts Inventory Management: A Literature Review, the value of spare parts annually consumed by a piece of equipment amounts to nearly 2.5 percent of its original purchasing price.
For these reasons, we’re sharing our best tips for streamlining spare parts inventory management. We’ll also discuss how spare parts inventory management software simplifies the process.
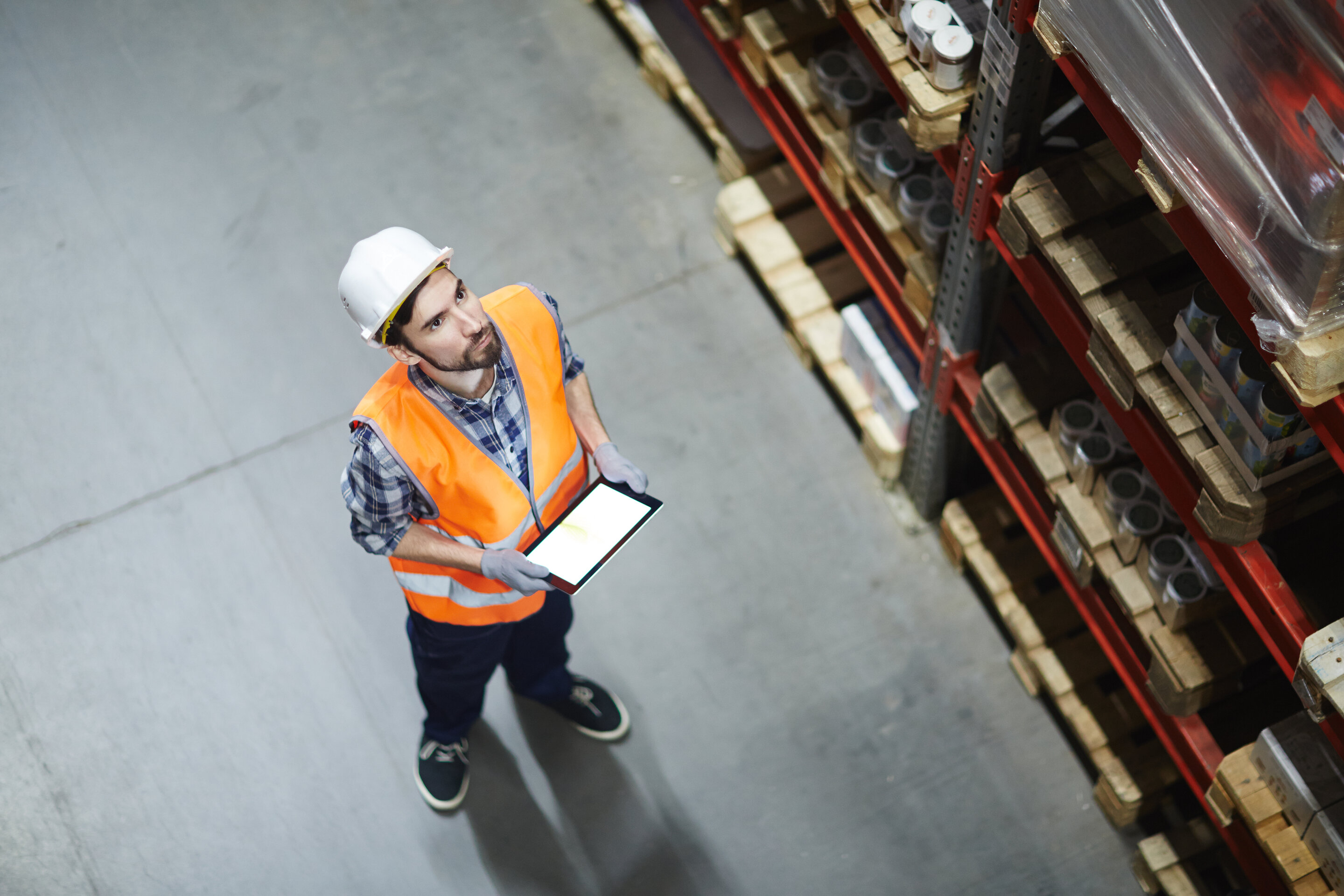
Introduction to Running Spare Part Inventory Programs
Even before the pandemic and the “right to repair,” businesses sought new ways to reduce operating expenses. Global events have made it more difficult for organizations to stock up on spare parts, making it harder to cut costs.
With this in mind, maintenance managers need to set up systems to effectively monitor parts’ usage, optimize parts’ spending, and develop maintenance repair hierarchies. Before we delve into that, let’s make sure we’re on the same page about what we mean by “spare part inventory.”
“The key to automated, predictive, and prescriptive operations . . . lies in the interconnectivity of digital tools, physical infrastructure, and their underlying data streams.”
Deloitte
What Is Spare Part Inventory?
Spare part inventory refers to a list of stock items that maintenance technicians use to replace failed equipment parts. Manufacturing facilities keep spare part supplies—like belts, motors, gears, and grease—on hand so they can fix equipment failures in minutes as opposed to days, weeks, or months.
However, spare part inventory also can include small items like printer cartridges, batteries, and light bulbs. Maintenance departments or general operational departments typically store spare parts in stockrooms on location.
Before we move on, let’s address a common source of confusion: do the terms stock parts and spare parts refer to the same thing? Well, not exactly.
The Difference between a Spare Part and a Stock Part
A spare part refers to an extra part of a machine kept for replacement or use in an emergency. Notably, businesses use spare parts solely for maintenance and repair.
A stock part refers to items kept to produce deliverables for sale. In other words, stock parts eventually leave facilities in the form of finished products.
In addition to product materials, stock parts can include personal protective equipment (PPE), packaging materials, and office supplies. While spare parts depend on maintenance activities, stock parts are contingent on planned production output.
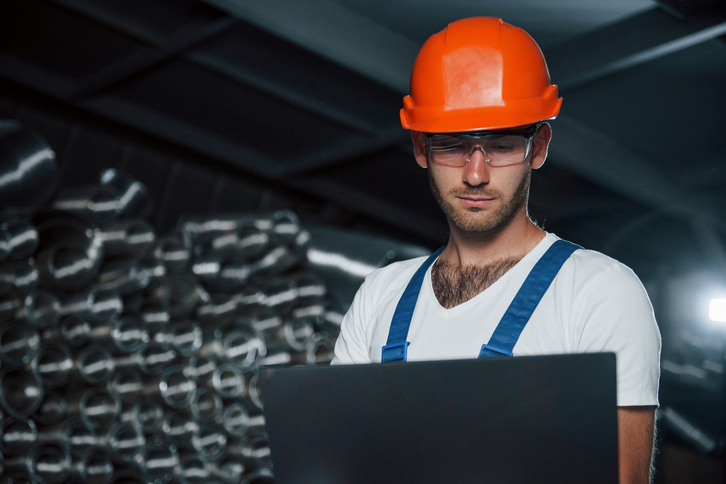
Benefits of Spare Parts Inventory
Unfortunately, feeling torn between minimizing operating costs and keeping plentiful inventory items on hand is normal.
When faced with pressure from upper management to increase bottom lines, it’s not unusual for maintenance managers to go against their better judgment and keep inventory levels low across the board. But this is a bad move for several reasons.
The non-availability of spare parts can cause significant financial losses in equipment downtime, unmet production targets, expedited shipment costs, and unhappy customers. Alternatively, following inventory management best practices yields several benefits, including:
- Quick Responses to Emergency Repairs: No matter how intensive a preventive maintenance (PM) program a manager runs, unplanned downtime is inevitable. For this reason, organizations must prioritize always having spare parts for critical machinery on hand. Any asset integral to production goals, expensive to repurchase, or essential to safety falls into the “critical equipment” category. The quicker that maintenance technicians can restore functionality, the fewer downtime losses the business will occur.
- Improve Metric Assessments: If you’re looking to improve your wrench time stats and your department’s overall efficiency, spare parts inventory control is vital. Having critical replacement parts on hand reduces employee idle time, which later contributes to inaccurate wrench time assessments.
- Reduce Repeat Repairs Have you ever performed a “patch job” on a broken asset? Essentially, you were forced to haphazardly fix something, knowing you would soon receive another work request to fix the asset properly. If you want to “do it right” the first time, so you don’t have to do it again for a long time, you need sufficient stock levels.
- Lower Expenses: While it’s possible to overstock a storeroom, effective spare parts management helps teams minimize their expenses. As previously mentioned, the cost of downtime can be catastrophic to manufacturers. Stocking spare parts for your facility’s most essential bill of materials eliminates rushed shipping for specialized parts, stalled production, and worker idle time.
Additional benefits of spare parts inventory include improved equipment uptime, enhanced part visibility, and improved brand reputation. In the next section, we’ll highlight tips for running an adequate spare parts inventory management system.
Maintaining a Spare Parts Inventory Management Program
Here are six steps to optimizing inventory accuracy while keeping costs low:
Step 1: Embrace Proactive Maintenance
First, if you haven’t already, transition your organization from an overall reactive maintenance strategy to a proactive maintenance strategy. It’s not possible to completely eliminate reactive maintenance—machines aren’t made to last forever.
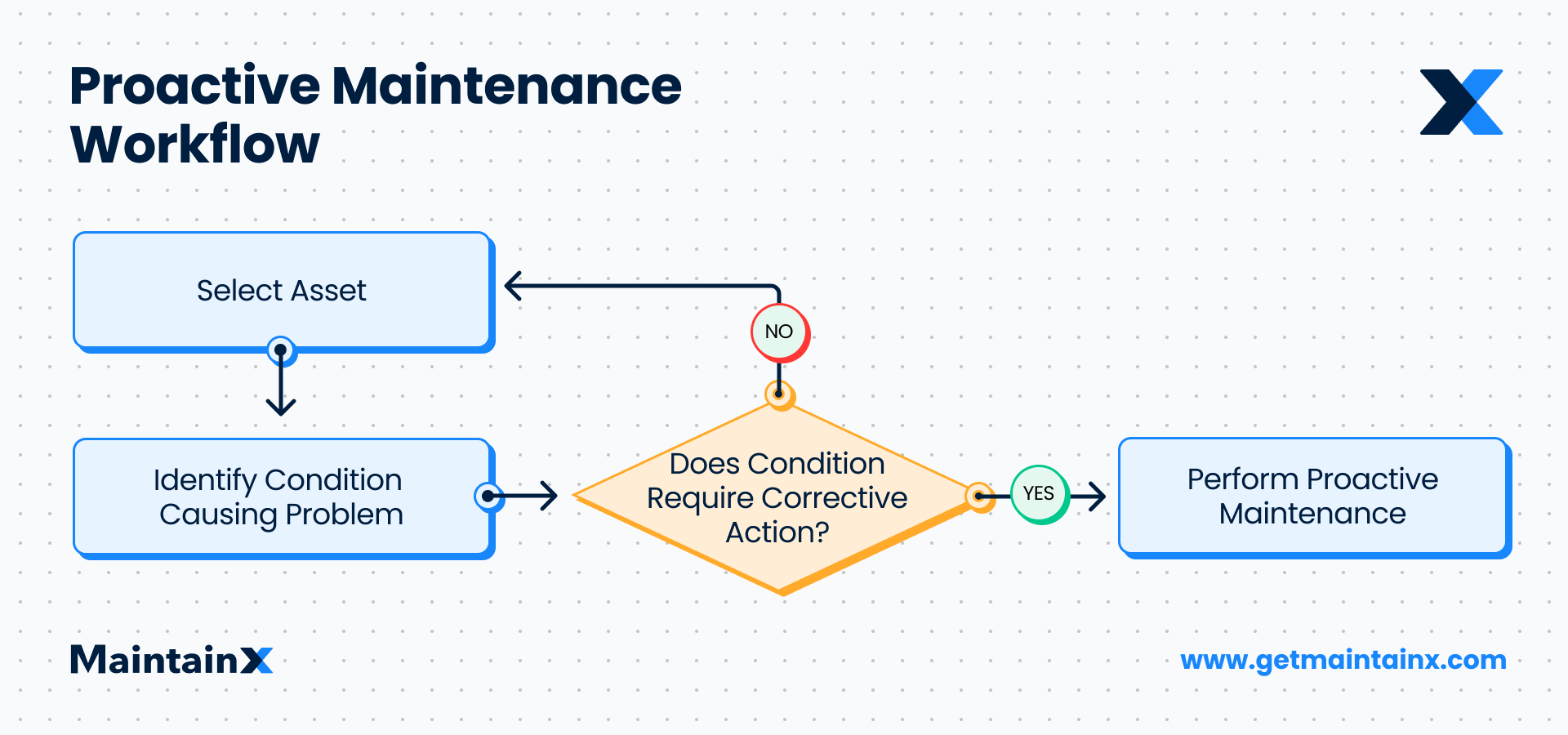
But reactive maintenance shouldn’t be the core aspect of your maintenance tasks if you seek financial optimization. The success of your spare part inventory management program depends on your ability to prevent problems before they happen.
Step 2: Develop Standard Operating Procedures
Standard operating procedures (SOPs) help ensure workers know exactly how to repair assets according to company standards. As a maintenance manager, it’s your job to identify the most efficient way to fix standard equipment issues and maintain critical machinery.
Digital SOP checklists partner well with inventory control systems, making it easier to track when spare parts move from the stockroom to the shop floor.
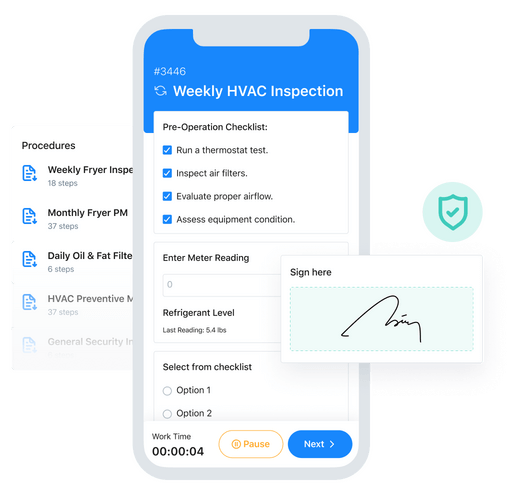
We recommend using a mobile computerized maintenance management system (CMMS) that includes parts inventory software capabilities to streamline department initiatives. The best platforms allow maintenance technicians to catalog exactly what parts they are using to fulfill assigned work orders in real time.
Step 3: Adopt Proper Inventory Control Measures
Your spare parts inventory management program doesn’t have to be all-inclusive to be effective. It’s almost impossible to keep an inventory of all the spare parts you need without breaking the bank! As a manager, your goal is to stock the parts most essential to operations.
That means updating records whenever you take parts out of the stockroom and logging new purchase orders. Clearly define and categorize all spare parts according to their manufacturers, costs, and dates of purchase.
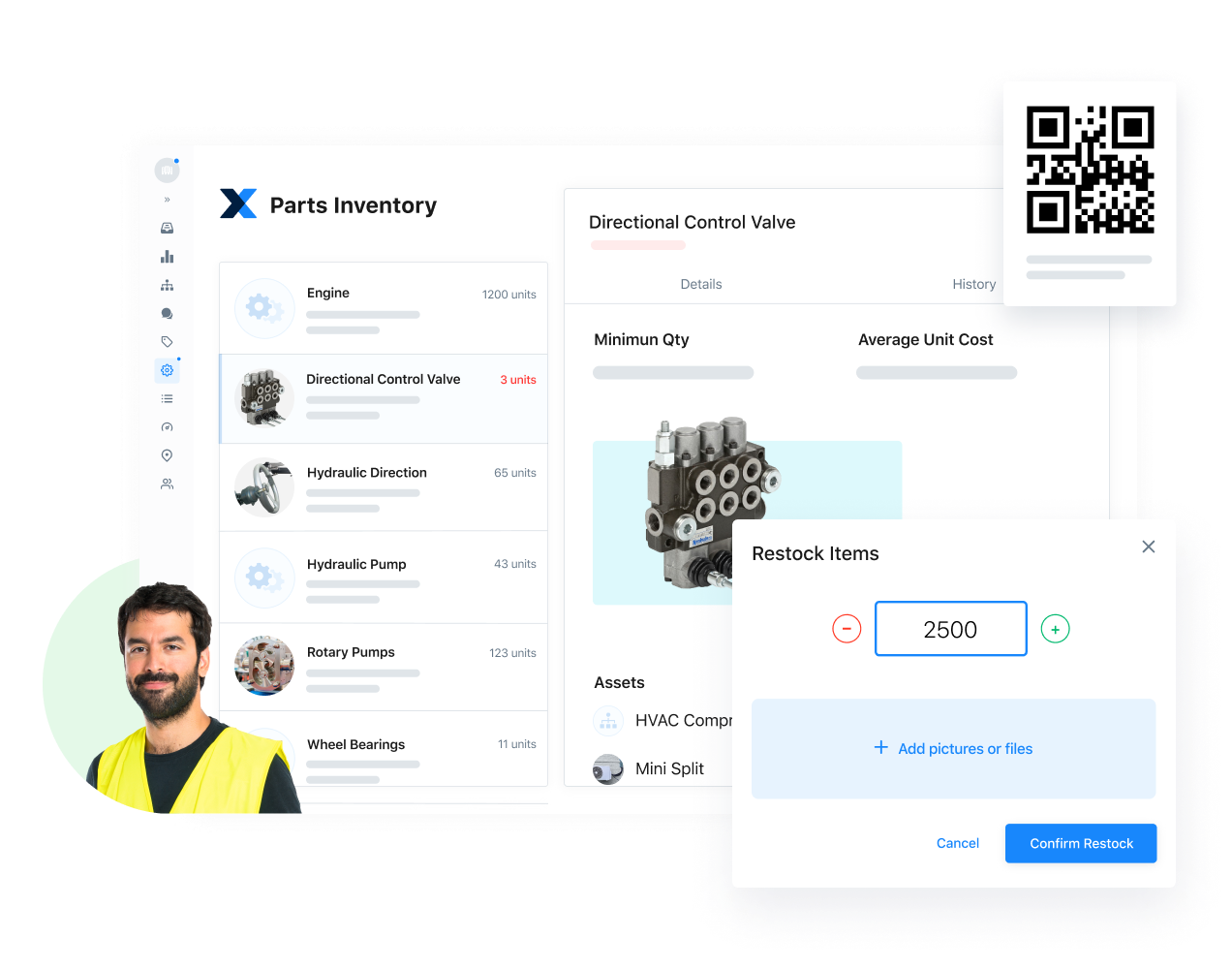
Regularly review your inventory to check for parts due to expire or excess stock. Again, user-friendly spare parts inventory management software, as shown above, can help simplify this process.
Step 4: Understand Your Lead Times
Next, get a clear understanding of lead times for ordering and receiving different parts. This can help determine which ones to stock and in what quantities.
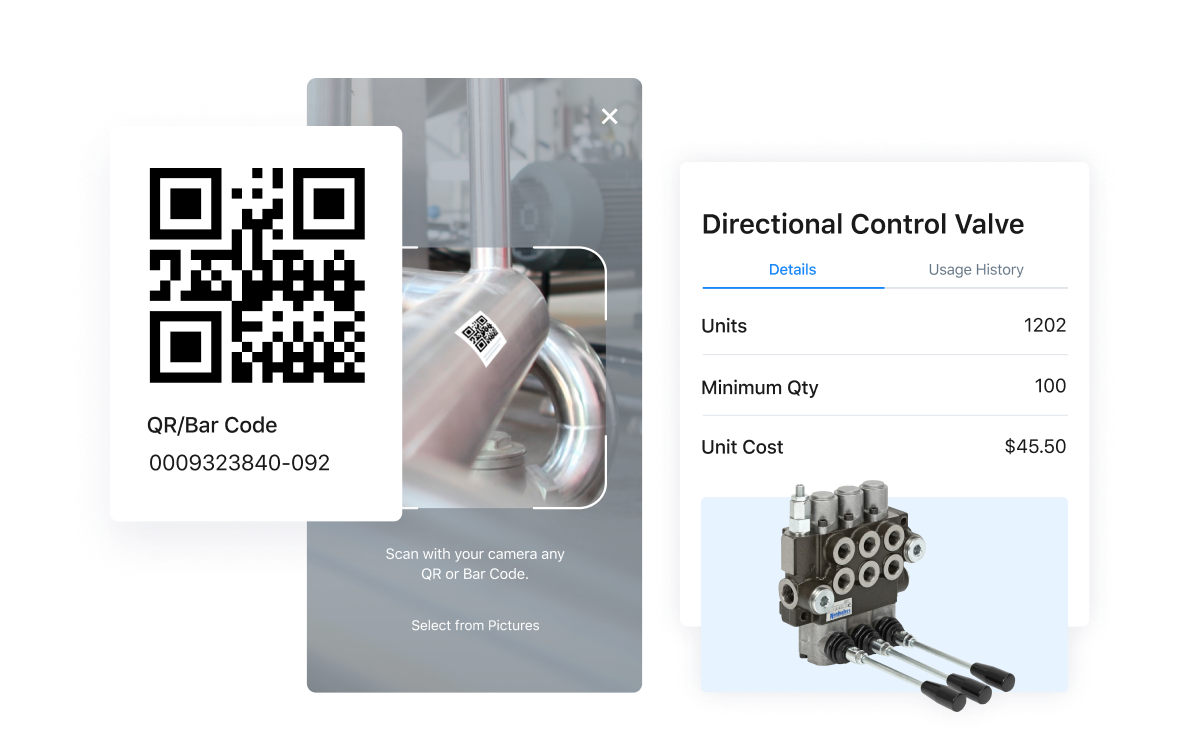
Prioritize spare parts for critical assets instead of non-critical assets. Order parts with long lead times—those that take longer to ship and may force you to incur extra costs for expedited delivery—first.
Step 5: Calculate Risk
Any realistic maintenance manager will admit that it’s impossible to avoid asset failures altogether. After all, old age is the leading cause of unplanned breakdowns.
But you can calculate the risk of downtime for each asset and adequately stock up for those that are high risk. The most accurate way to assess risk is to conduct a Failure Mode and Effects Analysis (FMEA).
Step 6: Enforce Security Measures
Limit access to your spare parts inventory store. Only authorized personnel should have access to the warehouse. This will enable you to effectively monitor and track the movement of spare parts in and out of the warehouse. In addition, you may want to install security cameras at facility entry and exit points.
Lastly, make sure to train relevant personnel on properly receiving purchase orders and counting incoming inventory. This will reduce the likelihood of inaccuracies that can contribute to a false sense of security when you’re running low down the line!
Use MaintainX Spare Part Inventory Management Software
If you haven’t been paying attention to your spare parts, now is the time. As recent global events have demonstrated, organizations that want to remain competitive can no longer ignore spare part inventory management.
As previously mentioned, spare part inventory management software streamlines maintenance management in a centralized location. Benefits of using CMMS inventory management software include:
- Automated low-quantity alerts save time, energy, and resources.
- Digital reporting allows for analyzing asset breakdown patterns.
- Connected workforce capabilities help manage multiple remote locations.
- Vendor data management keeps contact information at your fingertips.
- Asset data management allows for cataloging barcodes, serial numbers, and more.
- Digital checklists support standardization and reduce worker errors.
- Timestamps provide digital audit trails and proof of compliance.
With that said, the most significant advantage of using a solution such as MaintainX CMMS is the integration! Having everything you need to manage an effective, responsible, and cost-optimized maintenance department from your smartphone is a game-changer.
Get started on spare parts inventory management for free.
FAQs
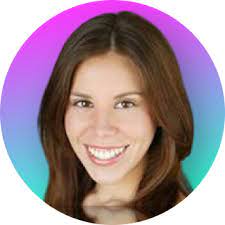