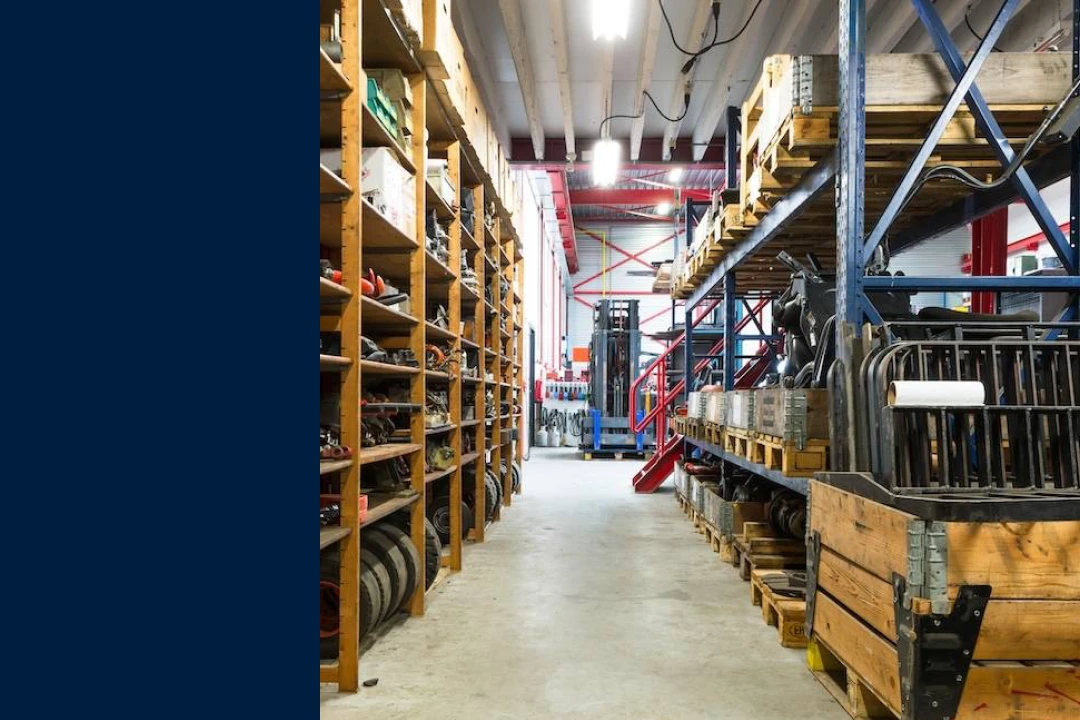
For many maintenance professionals, a trip to the parts garage might come with a sense of dread—and with good reason. It’s frustrating to sift through a surplus of mystery parts, encounter evidence of wasted spending on duplicates, and struggle to find the part you’re actually looking for.
Greg Wortman, operations manager at Redimix Companies, recalls initial visits to his company’s centralized parts storage area with his team: “I remember going through our inventory with a maintenance technician and asking him about a part: ‘What is this? It's not in a box.’ The technician said it came from a plant. But he didn’t know which plant it came from, or if the part worked. He guessed that we pulled it out seven years ago and put it here.”
Messy inventory storage can lead to an array of issues, from unnecessary spending on rush shipping to safety risks. It’s even a leading culprit for rising downtime costs—in fact, for facilities that successfully reduced the cost of unplanned downtime last year, 58.9% of them attributed their savings to improving their parts inventory management.
Yet it’s also a problem many teams tend to ignore. As Greg puts it: “It's the closet where all the skeletons hide out.”
So how do you conquer the clutter while keeping the right parts in stock? And how do you prevent the mess from resurfacing in the future? Here, we’ll break down the 5 “S” pillars of lean manufacturing that Greg used to get his team’s parts inventory under control and help his organization save big on maintenance costs.
1. Sort
The first step in getting your inventory under control is identifying and removing unneeded parts. “Start with a red tag to get rid of the clutter,” Greg says. “You’ve got to rip the bandaid off if you're serious about getting better.”
Prioritize sorting items based on value and criticality, and flag parts that haven't been used in an excessive period of time. Understandably, many maintenance professionals hesitate about scrapping old parts, but Greg cautions against this.
“It's that sunk cost fallacy of, ‘I spent $10 to go to a movie and now I'm going to sit through it even though it's terrible.’ But your time is worth more than that,” Greg explains. “It’s the same thing when you’re trying to put together a maintenance program. You may have a bunch of old parts, but if they're not good or never being used, they should be gone.”
Get the right stakeholders involved to help you evaluate parts disposal decisions. A CMMS or EAM can help expedite this process, too, and set you up for success going forward. These systems can automatically categorize parts by usage frequency and criticality. From there, your team can look at usage patterns for each part to determine the minimum or maximum amount to keep stocked.
2. Set in Order
After the red tag, the next step is developing an effective strategy about where to store each part. Greg’s team streamlined storage at his organization by dividing parts between a centralized location and individual plants.
“We've focused on keeping one central storage spot for major components. For my team, that would be bin gates. Since they're rather large, I don't want to store them at a plant. I need the plant space decluttered so when my team needs to do maintenance, they can do it easily,” Greg says. “When they do have to do maintenance on a bin gate, it's going to be a couple hours, so I have time to transport it up to the plant.”
Meanwhile, the team has reserved space at individual plants for expendable goods. “We keep parts like belts—which may take just 10 minutes to fix—onsite at the plant because I don't want to eat the excessive downtime to transport them.”
The team has also digitized its inventory in a mobile CMMS so technicians can quickly consult their phones about where to find each part. “ We’ve loved that with MaintainX, each plant has a categorized part. So we know that at Bin A101, for example, we can find this part, which belongs to this plant. And we've replicated that at each plant.”
3. Shine
An often overlooked step after sorting the parts is maintaining a clean, easy-to-navigate storage environment. This is essential to keep parts accessible and in top shape so you don’t encounter any unpleasant surprises about a part’s condition when you need it.
Work cleaning time into your team’s routine. Consider scheduling specific times for teams to deep-clean storage areas, and implementing quick, daily end-of-shift cleanups. During these cleanups, make sure to inspect parts for corrosion, damage, or contamination.
We recommend taking a comprehensive approach to the “Shine” step, regularly evaluating both the physical condition of your inventory and the accuracy of your inventory data. Regularly clean up your data to verify that your digital and physical inventories match—a CMMS feature like Cycle Counts can help your team manage this. Also put routines or technologies in place to monitor when parts are approaching shelf-life limitations and track which ones require periodic inspection.
4. Standardize
Without a process everyone can agree to follow, your newly organized inventory won’t stay orderly for long. It’s important to create systems that make it easy for the whole team to keep up with inventory management.
A CMMS that automates certain processes helps Greg’s team stay on track. MaintainX automatically removes parts from the digital inventory after they’ve been tied to a completed work order, for example.
“We've used MaintainX to get all our inventory logged, and we've become really disciplined at tying that inventory to work orders,” says Greg. “Now, once a work order is complete, the software automatically removes the part tied to the work order from the inventory. This way, I always have an accurate inventory.”
Moreover, using CMMS software to trigger automatic notifications when parts reach reorder thresholds has helped Greg’s team avoid downtime and emergency shipping costs. “I've also been able to set safety stocks with the software, so it sends me an email saying, ‘Greg, by the way, you said you're supposed to have four of this part. You need to reorder to make sure you have enough.’”
Standardizing naming conventions across the organization is also critical for keeping an accurate inventory. Make sure you’re creating consistent descriptions to help your team correctly identify and find parts in your system.
5. Sustain
After the inventory is initially organized, how do you prevent your team from slipping back into old ways of doing things?
First, keep your team accountable by tracking who receives and adjusts inventory. Greg sustains an organized inventory by creating a system that helps every technician easily maintain records of parts usage. “We’ve created a step in our weekly PM schedule to include updating inventory counts at the plants,” Greg says. “And then we added another layer of security onto that: As we do our PMs for the plants once a week, the last step on that PM is to make sure the inventory is accurate.”
Easy mobile access to a digitized parts inventory allows teams to keep up with inventory management from anywhere in the facility. This leads to more accurate data, which will ultimately help you identify patterns in parts usage, costs, and availability.
The bottom line? “Make it predictable,” he says. “I want my team to live in the world of preventive maintenance.”
Want to hear more advice from Greg? Check out the recording of his discussion with MaintainX cofounder, Nick Haase. Beyond parts inventory management, they cover strategies maintenance professionals can apply to minimize costs and maximize uptime in their facilities.
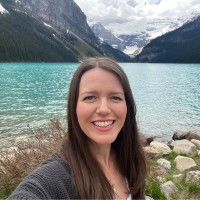
Senior Content Writer, MaintainX