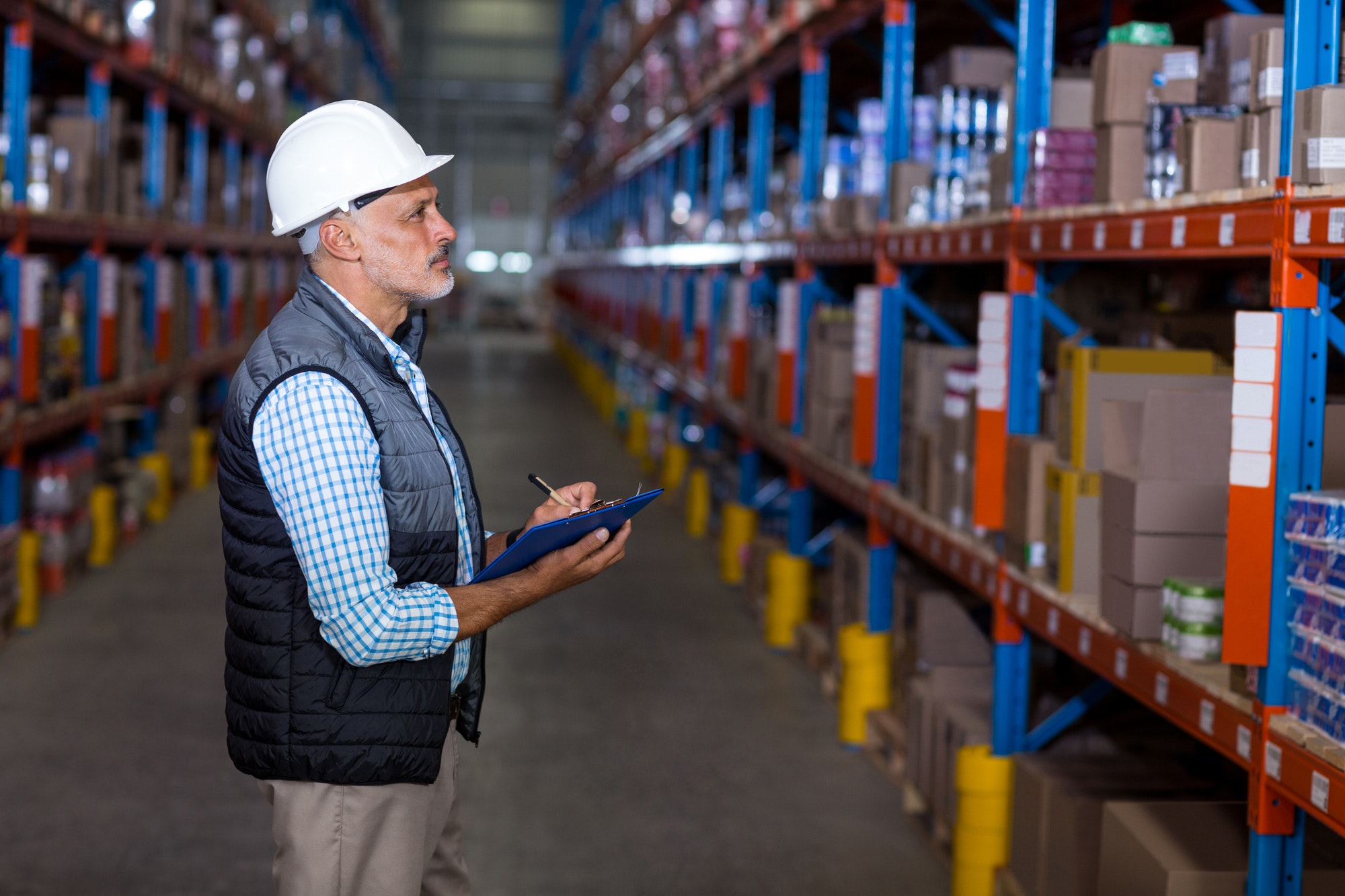
How do you ensure you have what you need when you need it? And how do you make sure you don’t have too much and then have to deal with waste? The tug of war between these two simple ideas is the core of the Just-in-Time vs. Just-in-Case debate.
Optimizing your operations often means optimizing several different processes within those operations. For example, suppose you’re looking to run a successful team. In this case, you’d probably not just be thinking about keeping your production smooth, reducing your downtime, and ensuring your workers stick to their maintenance schedules. You may also be thinking about inventory management.
“We should not forget the original rationale for just-in-time: catch quality problems early before you have a lot of defective parts made, lessen the risk of obsolescence (especially in fast-moving industries), don’t waste space storing and managing all that inventory, lessen the amount of cash tied up.”
Forbes
Just-in-Time vs. Just-in-Case Explained
Just-in-Time and Just-in-Case are two different approaches to inventory management. Most companies aim to have a supply chain that runs smoothly and experiences no delays or wasted effort.
Just-in-Time inventory management is a lean manufacturing strategy that involves purchasing stock based on current conditions. The Just-in-Time (JIT) model means having inventory filled “just in time” to meet orders. If you run this system, you’ll want your stock to arrive no sooner than there is demand for it. That is, for materials to arrive just as you need them. Continual improvement of your Just-in-Time system is crucial to stay lean and not beholden to vendors.
JIT is, in a sense, a pull strategy: you call up inventory on demand. However, instead of a proactive inventory management strategy, JIT is reactive.
Just-in-Case inventory management, meanwhile, involves stocking up before the need arises. It is a proactive system of supply chain management that aims to meet potential consumer demand and avoid shortages.
Compared to the JIT system, the Just-in-Case (JIC) inventory management system can be costly. For example, teams always having material on hand necessitates higher storage costs. Also, you’ll have to find ways to manage potential excess inventory.
However, having inventory on hand means you benefit from potential financial costs due to unreliable suppliers or other disruptions. In addition, with steady inventory levels and raw materials always available, production teams can be sure they can meet customer demand.
“The tangible costs of storing inventory such as storage, handling, and insuring goods are obvious. Less obvious are the intangibles such as the opportunity cost of the money that was used to purchase the inventory, and the cost of deterioration and obsolescence of goods in storage.”
Investopedia
Just-in-Time vs. Just-in-Case: Pros and Cons
As with any system, pros and cons exist for both of these options. But which should you adopt? Well, that depends on your goals and resources. Are you aiming for a lean system? What is more important to you: preventing waste or always meeting customer demand? How much are you willing to spend? Let’s look at how both systems compare in a few key areas.
Waste
Just-in-Time is a feature of Toyota’s lean model of continuous improvement. As a result, waste reduction is part of its design. The system’s impact varies based on your business, but production teams dealing with perishable materials can benefit significantly here. In addition, reducing your stock to only what is needed prevents any excess inventory from going to waste.
Just-in-Case, on the other hand, will likely result in more waste. Ensuring you always have stock on hand to meet production means that any demand shortfalls will result in unused raw materials. This particularly concerns businesses dealing with seasonal goods or products with unsteady demand.
Consumer Demand
Teams running JIT systems run the risk of not meeting consumer demand. So while you’ll reduce wastage by not always having inventory on hand, you could end up not being able to meet orders when they come in.
For a JIT system to work, production teams need reliable suppliers who can deliver raw materials when orders come in. However, having reliable suppliers doesn’t guarantee you can avoid the problem. Demand isn’t always static. Teams can plan for seasonal changes, but customer behavior isn’t always predictable.
Just-in-Case doesn’t have this supply problem. With raw materials always on hand, you can always fulfill orders. Despite seasonal surges or changes in consumer behavior, you’re also not at the mercy of suppliers. Teams have a competitive edge, as they never run out of stock.
Cost
On the surface, Just-in-Time is a much better bet here. You spend far less on buying raw materials and lose less to waste. You also save on warehousing. Meanwhile, Just-in-Case requires spending not only on warehouse space but also labor to handle the higher inventory. In addition, JIC requires more working capital and cash flow for the production process to work.
However, the JIC system offers cost benefits despite its extra carrying costs. For one, buying raw materials in large batches means potential bulk discounts. Also, being fully stocked means being able to fill orders and, therefore, fewer sales lost to competition.
Efficiency
The JIT system benefits from the efficiency boost in lean management. Your workers can focus on remaining productive without downtime waiting on supplies to come in. This reasoning applies to inventory management as well. You can divert your workforce from managing large inventories to the work of production.
However, JIC systems offer efficiency benefits. Having stock on the ground means team members don’t have to worry about racing to fulfill orders. There is also less of a need for accurate forecasting as, whatever the demand is, teams can meet it while avoiding bottlenecks.
Quality Control
A large stock of raw materials makes quality control more manageable. You can be sure of the quality of materials you have in storage in a Just-in-Case system. Preserving your inventory properly ensures the quality of your finished products.
With Just-in-Time systems, quality often depends on suppliers, especially if you have to order quickly. If you are in a time crunch, you can run into problems ordering sub-standard supplies from vendors you don’t know.
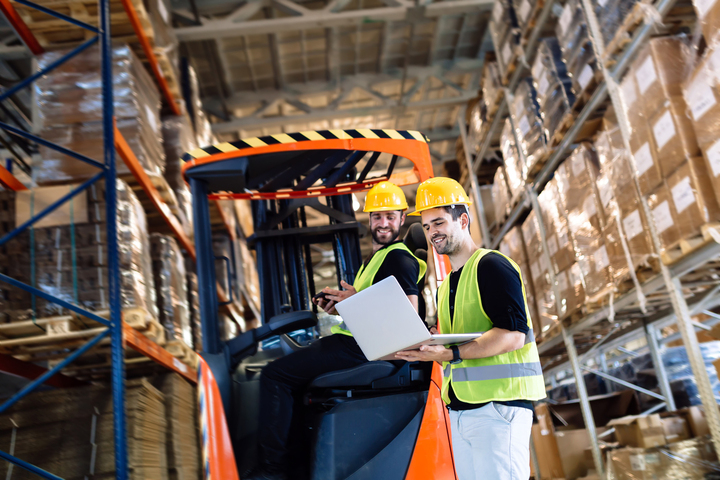
Just-in-Time vs. Just-in-Case: Which System Should You Choose?
As you’ve probably noticed, both systems have their advantages and disadvantages. Your choice depends on your company’s particular goals. Therefore, aiming for a balance between both approaches may be a good bet.
The Covid-19 pandemic underscored the importance of proper supply chain management. As a result, many retailers ran out of inventory. Furthermore, the global economy is still recovering from system-wide shocks.
Businesses should balance Just-in-Time with Just-in-Case to navigate potential stockouts. For example, even if you primarily run a JIT system, you can use JIC for end-products with longer lead times. This is especially important when dealing with raw materials that risk going out of stock.
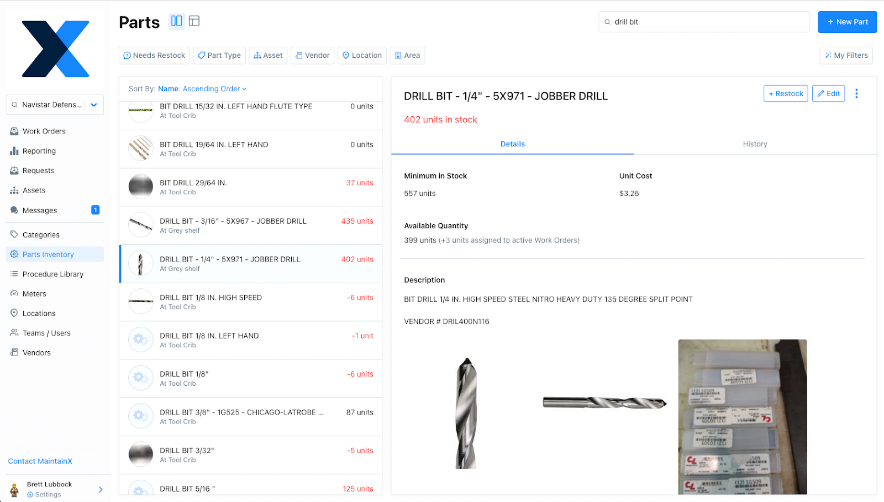
Use a CMMS to Manage Your Inventory
If you’re looking for ways to optimize your inventory management, consider using MaintainX. MaintainX allows you to store details about your current inventory and comes with a Parts Inventory module.
MaintainX’s Parts Inventory allows you to:
- Create automated alerts for when items reach minimum thresholds.
- Create purchase orders to restock low supplies.
- Track usage history and create digital audit trails.
- Store real-time data for all your vendors and service providers.
- Create digital checklists for inventory management.
Try MaintainX today!
FAQs
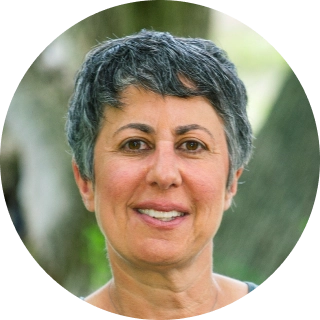
Caroline Eisner is a writer and editor with experience across the profit and nonprofit sectors, government, education, and financial organizations. She has held leadership positions in K16 institutions and has led large-scale digital projects, interactive websites, and a business writing consultancy.