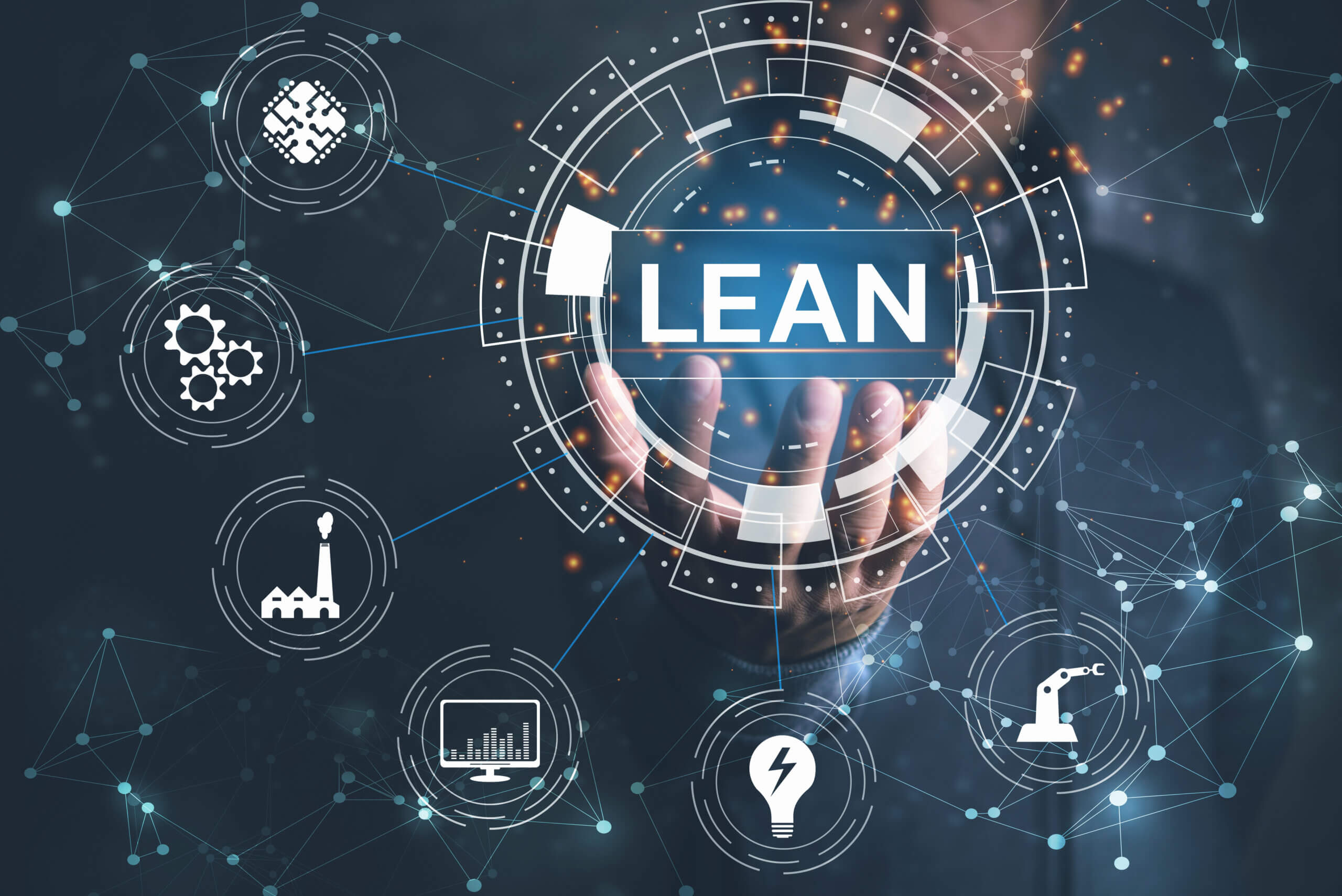
Lean strategies have revolutionized how we write preventive maintenance SOPs, providing a more effective and efficient approach to these tasks.
Your company can save time and money by utilizing a lean strategy while achieving higher performance levels. Lean strategies focus on eliminating wasted time, effort, and resources to maximize the efficiency of operations. When it comes to preventive maintenance SOPs, this means ensuring that all steps are necessary, relevant, and effective at preventing any problems or breakdowns before they occur.
What Is Lean?
Lean strategies are a set of business principles and approaches that aim to minimize cost, time, and resources while optimizing the overall value of outputs. This is done by eliminating unnecessary or redundant, such as overproduction, inventory stockpiling, waiting time, and extra motion.
This approach is based on the concept of “lean manufacturing,” which Toyota established in the late 1980s to streamline its production processes and reduce waste.
Lean strategies focus on identifying and eliminating non-value-adding activities, streamlining processes, and finding ways to add more value with fewer resources. These strategies concentrate on production flow, customer feedback, and system optimization to create a leaner and more efficient operation on the shop floor and in the field.
Well known in manufacturing, lean refers to methods that help to identify and eliminate operational waste; Six Sigma refers to techniques used to improve processes and quality. The Six Sigma methodology includes five key steps: define, measure, analyze, improve and control (DMAIC).
Forbes
An essential element to lean strategies is the “Kaizen” approach, which involves continuous improvement in all areas of your company. This means that teams should constantly assess their processes to identify what can be improved or eliminated altogether. Other Lean tools that operations management may find useful include Gemba walks, lean six sigma, and other management systems that try to reduce waste.
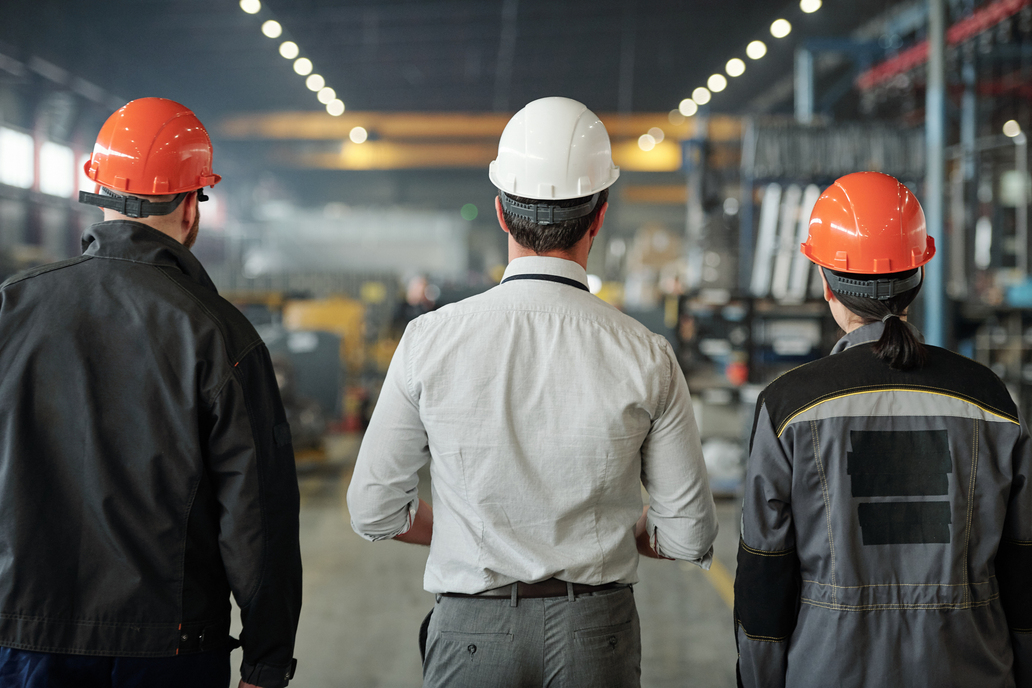
What is DOWNTIME?
In the manufacturing world, the term, downtime, refers to the amount of time production stalls because of non-functioning equipment. However, downtime can also represent wasted time in your company’s production cycle.
Use this methodology to identify opportunities to eliminate these eight types of waste with new processes DOWNTIME is an acronym that names 8 types of waste to eliminate in your drive to become more efficient:
DOWNTIME
- Defects
- Overproduction
- Waiting
- Not utilizing talent
- Transportation
- Inventory excess
- Motion waste
- Excess processing
What Are the Benefits of Lean?
Businesses often use Kaizen approaches such as benchmarking against competitors or industry standards, experimenting with new technologies or processes, conducting root cause analysis for inefficiencies and leveraging data-driven decision-making.
Start by identifying areas of potential improvement in your company’s existing processes or products. You can identify these deficiencies through data analysis techniques such as value stream mapping, which diagram out each step in a process to pinpoint opportunities for optimization or streamlining.
Lean process redesign helps companies streamline processes, eliminate waste, and foster a culture of continuous improvement. This versatile methodology applies well to short-cycle as well as long-cycle processes, transactional as well as judgment-based processes, client-facing as well as internal processes.
McKinsey
Once these areas have been identified, standardization solutions can be implemented to address them, such as introducing automation into repetitive tasks or altering the design of products or services to increase customer satisfaction.
Furthermore, it is essential to create a culture of continuous improvement amongst employees for the benefits of lean strategies to be maximized over time. This involves seeking regular customer feedback regarding their needs and expectations and open communication between different departments within your company about best practices for efficiency and cost savings.
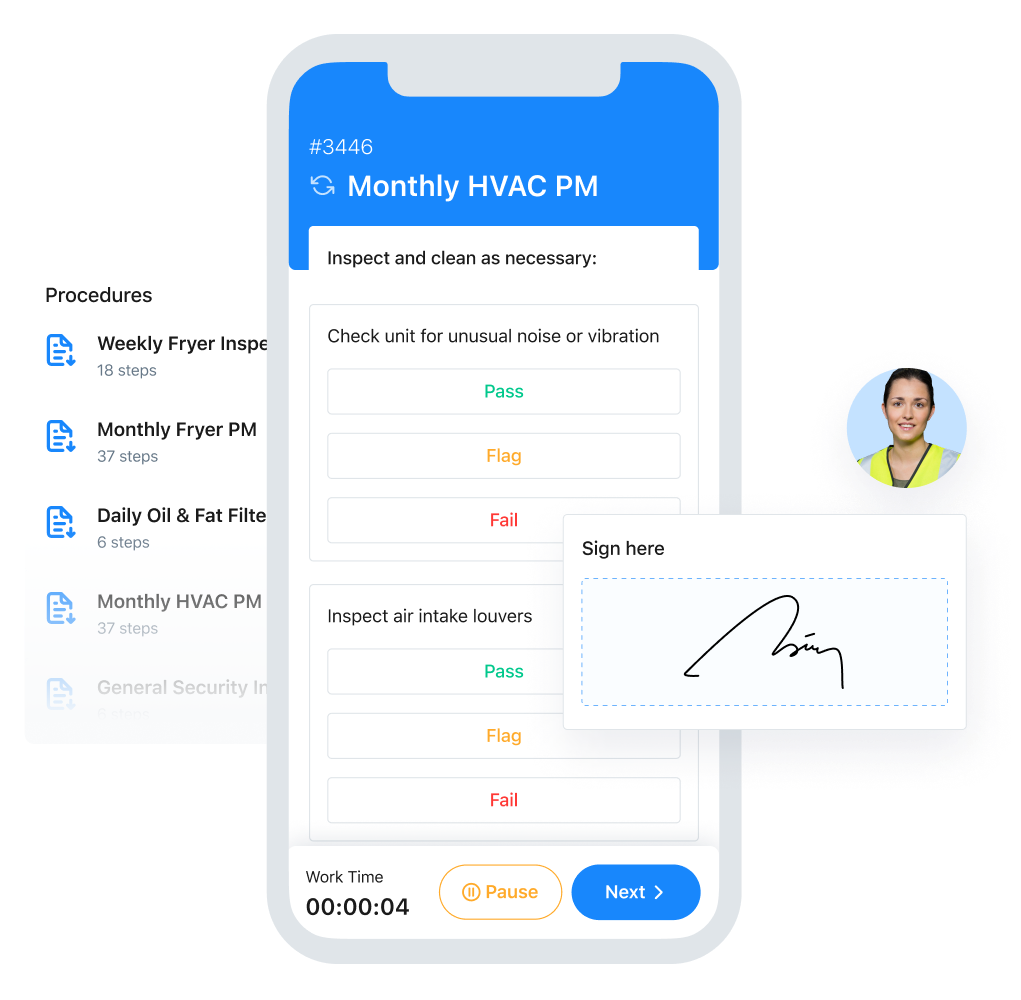
Why Use a Lean Approach to Write SOPs?
Employing lean strategies to write work instructions in the form of Standard Operating Procedures (SOPs), a procedural document that can significantly improve your maintenance team’s effectiveness. To maximize the effectiveness of your preventive maintenance SOPs using a lean strategy, follow these fundamental principles:
- Focus on value-added activities that directly contribute to maintaining peak performance within your company. Lean methodology suggests identifying processes to either improve or eliminate to reduce waste and optimize resource utilization.
- Consider value stream mapping (VSM). This involves creating a visual representation, such as a flowchart, of all the steps involved in completing a task or process, starting from its initiation completion. VSM initiatives help identify areas where duplicated efforts or unnecessary steps may be eliminated or merged to increase efficiency and reduce waste.
- Analyze existing processes thoroughly and identify any areas of inefficiency or waste. Adjust the step-by-step process as much as possible with minimal impact on overall performance levels. This includes examining resources, workflows and hierarchical steps, tools, equipment used, procedures followed, onboarding and training requirements, and more.
- Create checklists and standards for tasks included in your preventive maintenance SOPs so that they are consistently executed correctly and efficiently every time they are performed. This reduces the likelihood of errors occurring across operations. Standard work processes also ensure a consistent level of quality across business processes.
- Strive for continuous improvement in your preventive maintenance SOPs by regularly reviewing them for improvements or changes that could further increase efficiency.
For example, suppose new technology has been introduced to ensure consistency. Incorporating it into existing procedures may offer opportunities for greater efficiency or cost savings that were not available previously.
How to Use a Lean SOP Approach
Overall, utilizing a lean strategy when writing effective preventive maintenance SOPs can provide your company with numerous benefits, including:
- increased productivity due to streamlined workflows
- reduced costs due to optimized resource utilization
- improved accuracy through creation of checklists
- improved quality through regular reviews and updates as required by changing technology or operational conditions.
By following this approach when creating your preventive maintenance SOPs, your company can maximize efficiency while minimizing waste.
Overall, lean strategies can offer your company numerous advantages, from reduced operating costs to increased output quality, without sacrificing customer satisfaction or safety standards. By utilizing these principles successfully, companies can benefit from improved productivity, better customer service experiences, faster turnaround times, reduced inventories, and lower costs associated with producing goods or services while remaining competitive in today’s market.
Finally, establish feedback loops to identify problems quickly and respond appropriately. Your company should continuously seek customer insight through surveys or interviews that allow them to learn about your customers’ needs and wants so you can create products or services that better satisfy those needs. Set up automated systems for tracking customer complaints that alert team members when anything unusual arises to address it before it becomes a more significant issue.
How to Create Lean SOPs
Creating effective preventive maintenance standard operating procedures (SOPs) is vital for businesses that rely on machines, systems, and other equipment.
Implementing a lean strategy when writing these SOPs can help ensure that processes are efficient and comprehensive. To create standard operating procedures, you want your SOP to be digital, integrated, and interactive.
Digital SOPs ensure that all team members have access to all the updates in real time to help save time. In addition, you can include detailed instructions with videos and images. While there is no one SOP format, you can use an SOP template to create and update the defined SOPs much faster when they are digital. A standard template allows users to find the information they need quickly.
An interactive standard operating procedure document provides a checklist or template to employees. The steps come up one by one as the employees work on them. They can check off each step as they go. This is helpful when onboarding new hires. An integrated SOP uses automation to do the work for you. As employees enter data about the task into the template, additional steps are triggered as needed. Reports, even a flowchart, can be created to see performance, downtime, and inventory. Your new SOP looks less like a manual and more like an interactive application.
What Should Your Lean SOPs Include?
Consider the SOP template below to structure your SOPs:
Additional Steps for Writing Lean SOPs
- Use active voice and precise language, and include step-by-step lists wherever possible. Avoid technical jargon whenever possible – this will make it easier for everyone following the procedure to understand precisely what they need to do.
- Break down each step into smaller tasks where possible. This helps ensure that all necessary details are included without making the document overly long or confusing.
- When documenting complex processes, breaking them down into smaller chunks makes them much more accessible for others to follow along with and understand quickly without spending too much time reading through long paragraphs.
- Include relevant information regarding safety protocols.
How to Review Your Lean SOPS
Once your first draft is finished, ask those who do the work to review it for accuracy and completeness. Involving stakeholders is essential. Getting input from those who will use the procedure ensures that its steps make sense from their point of view. It also gives them ownership over its success or failure, which could lead to further improvements if needed. Furthermore, employees are empowered when management recognizes their skills and knowledge. This often leads to increased job satisfaction and lower turnover rates.
- Ask reviewers to check if any of the steps outlined in your SOP cross over to other procedures or conflict with existing regulations.
- Remember to train personnel responsible for these preventive maintenance tasks on an ongoing basis. Providing new training materials alongside any new SOP documents can help ensure that everyone understands their roles and how they should approach each task. This is especially important for new employees who may need help problem solving.
- Consider how these SOPs fit together into a cohesive system overall. Take a holistic view of the entire system rather than just focusing on pieces of machinery or equipment that may be part of it. By doing so, you’ll be able to spot areas where various processes may overlap or create redundancies, leading to even more significant efficiency gains across your entire system when addressed correctly.
- Measure SOP performance through key performance indicators (KPIs) to evaluate progress against goals and identify areas for further improvement.
- Review each section of the document regularly—at least once a year—to ensure accuracy and relevance.
Use a CMMS to Enhance SOPs
A CMMS is an invaluable tool for improving the efficiency and effectiveness of planned maintenance activities. A centralized platform for managing and tracking these activities, a CMMS can help reduce the risk of errors. Likewise, a CMMS improves communication and coordination among team members and optimizes the use of resources.
Automate Scheduling and Track Progress
A key benefit of using a CMMS is that it allows you to schedule and track maintenance and repair activities in real time. A CMMS can also improve your recordkeeping and documentation of maintenance activities. During inspections, this recordkeeping is invaluable for compliance and regulatory purposes. Furthermore, a CMMS like MaintainX offers easy integrations with your EAM, EAP, and other business software solutions across industries.
Improve Communication and Collaboration
A CMMS like MaintainX can help to improve communication and coordination among team members. Everyone involved in a particular task is aware of their responsibilities and the status of the work being performed. MaintainX, by the way, is the only CMMS on the market that offers in-app chat capabilities.
Optimize Resources
A CMMS can optimize the use of resources, including equipment, spare parts, facilities, and personnel. By providing real-time data and analytics on the status of maintenance activities, a CMMS can help reduce costs, manage supply-chain challenges, and integrate lean maintenance strategies.
FAQs
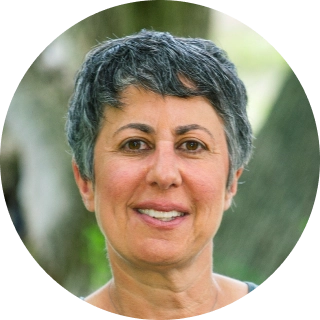
Caroline Eisner is a writer and editor with experience across the profit and nonprofit sectors, government, education, and financial organizations. She has held leadership positions in K16 institutions and has led large-scale digital projects, interactive websites, and a business writing consultancy.