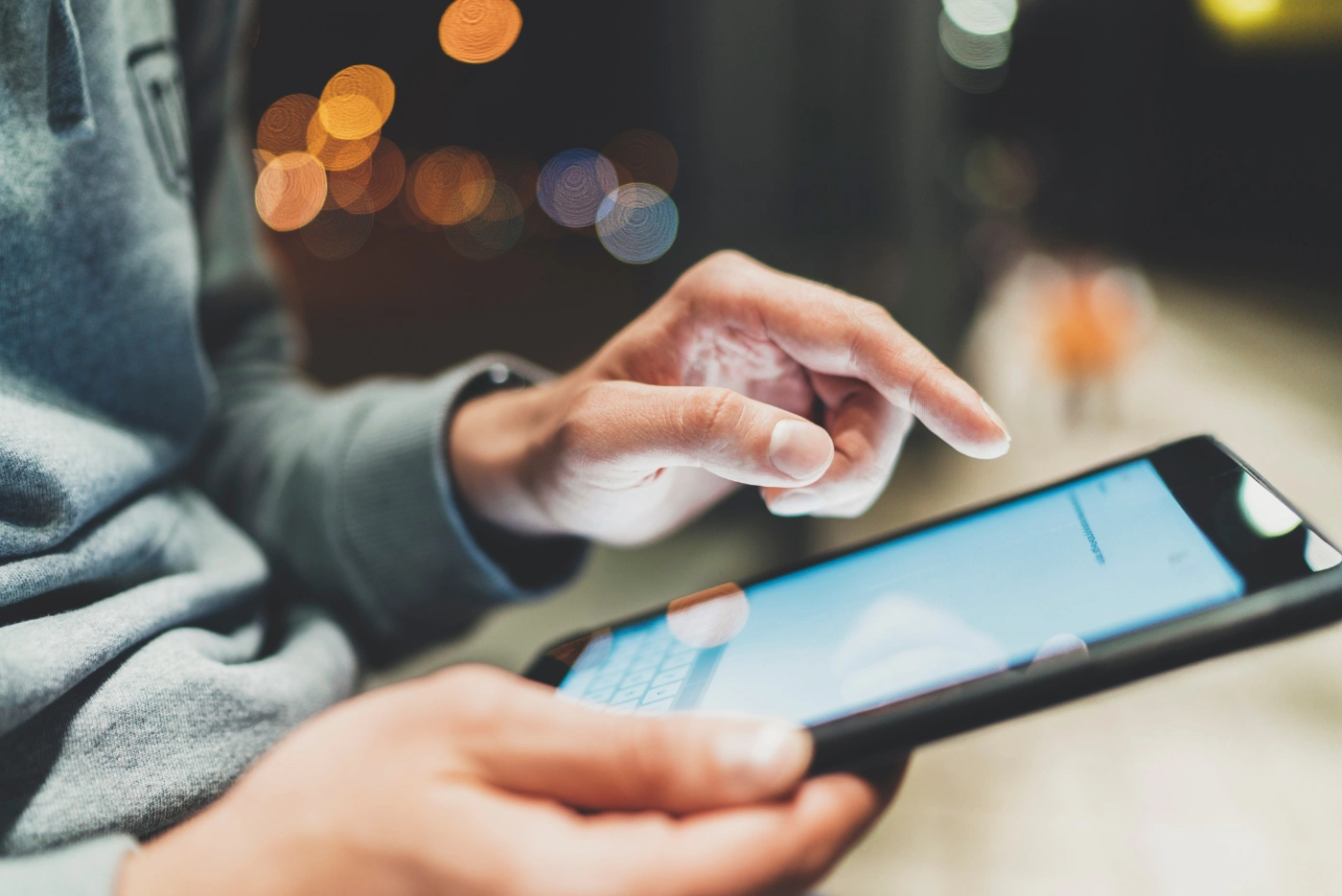
General maintenance in your manufacturing plant can be a never-ending battle. A general maintenance task list is the simplest way to approach this aspect of your maintenance program to get a handle on things.
The bigger your facility and the more equipment and assets you have on site, the harder it can be to remain on top of preventive maintenance work. This more often than not leads to a build-up of mechanical issues or unforeseen breakdowns.
Without applying some structure to your maintenance activities, minor problems can quickly snowball into major situations. Therefore, it’s worth developing a robust maintenance strategy considering all the equipment and structures in your facility that require regular upkeep.
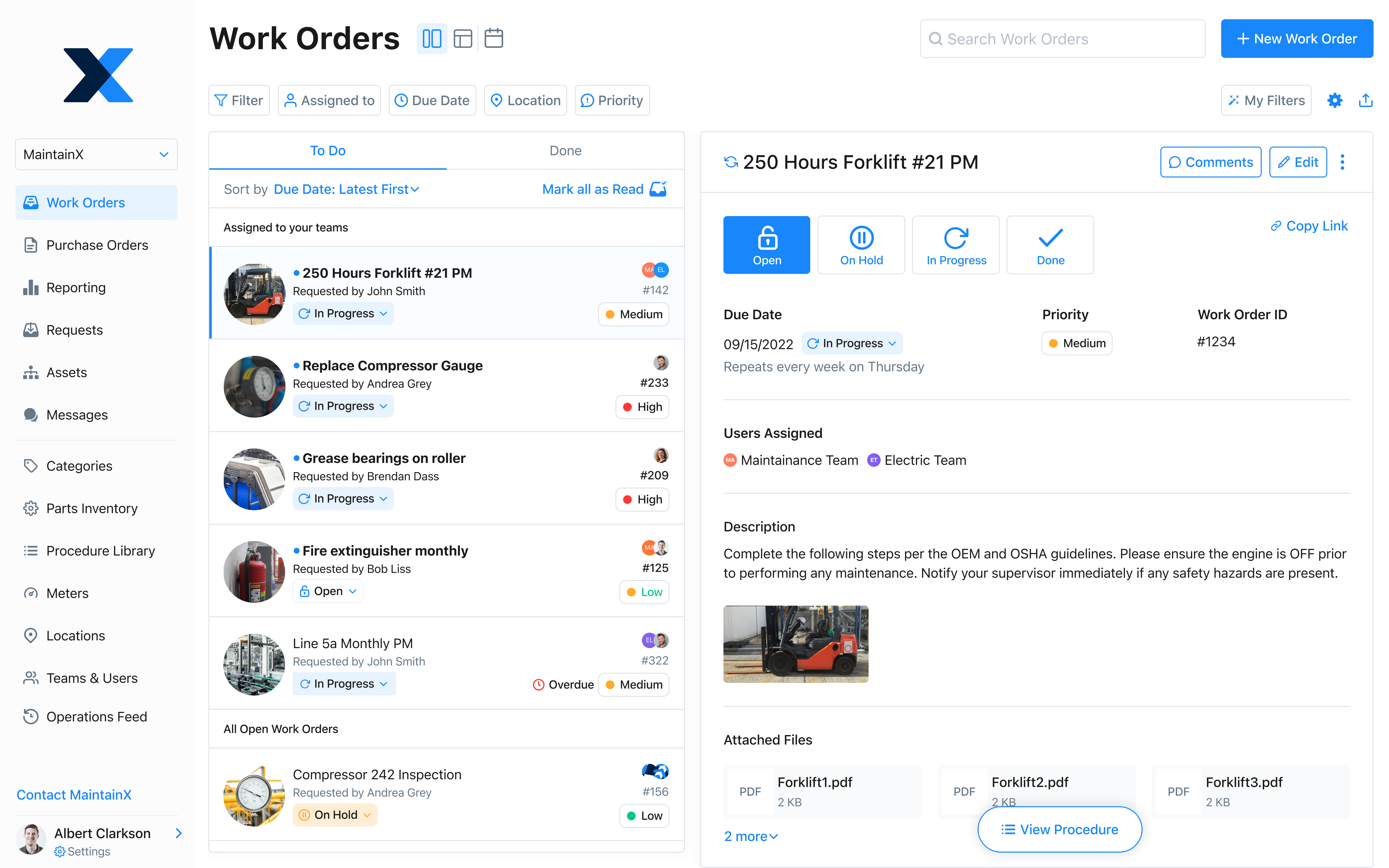
Why Use a Preventive Maintenance Checklist?
Developing a template that lists all the maintenance items for each piece of equipment will make your maintenance crew’s role vastly easier. A checklist also allows technicians to systematically tick off each task as they move through the list.
The primary rationale behind any planned maintenance program is to reduce downtime and eliminate expensive callouts to rectify emergency breakdowns. This helps plant maintenance technicians keep an eye on the right things at the right time.
Developing a general checklist of maintenance tasks keeps your maintenance personnel on task. In addition, it helps managers organize the necessary resources, parts, tools, and consumables required for each work order.
How to Create a General Task List
Decide How to Categorize Tasks
You can break down task lists used in preventive maintenance operations in several ways, depending on your business. Both ongoing and ad-hoc maintenance work can be managed using different lists for different purposes.
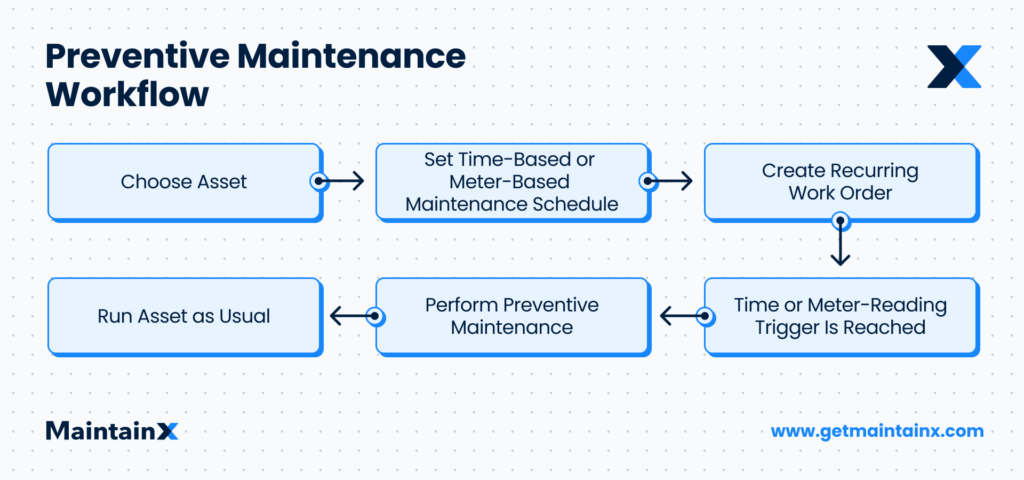
Some maintenance software use three separate task lists:
- General Maintenance Task List
- Equipment Task List
- Functional Location Task List
While this provides some organization, it can still be hard for businesses to manage and administer on an ongoing basis.
For most businesses, starting in the most uncomplicated way is the key to getting all stakeholders on board with a new way of managing maintenance tasks.
Therefore, a simpler solution is to begin with general checklists focusing on each item of equipment or a specific area of your facility.
For example, you can streamline maintenance on areas such as driveways, walkways, and fences under a general exterior maintenance list. Then, as your team becomes accustomed to your checklist procedures, you can break your lists into more detail.
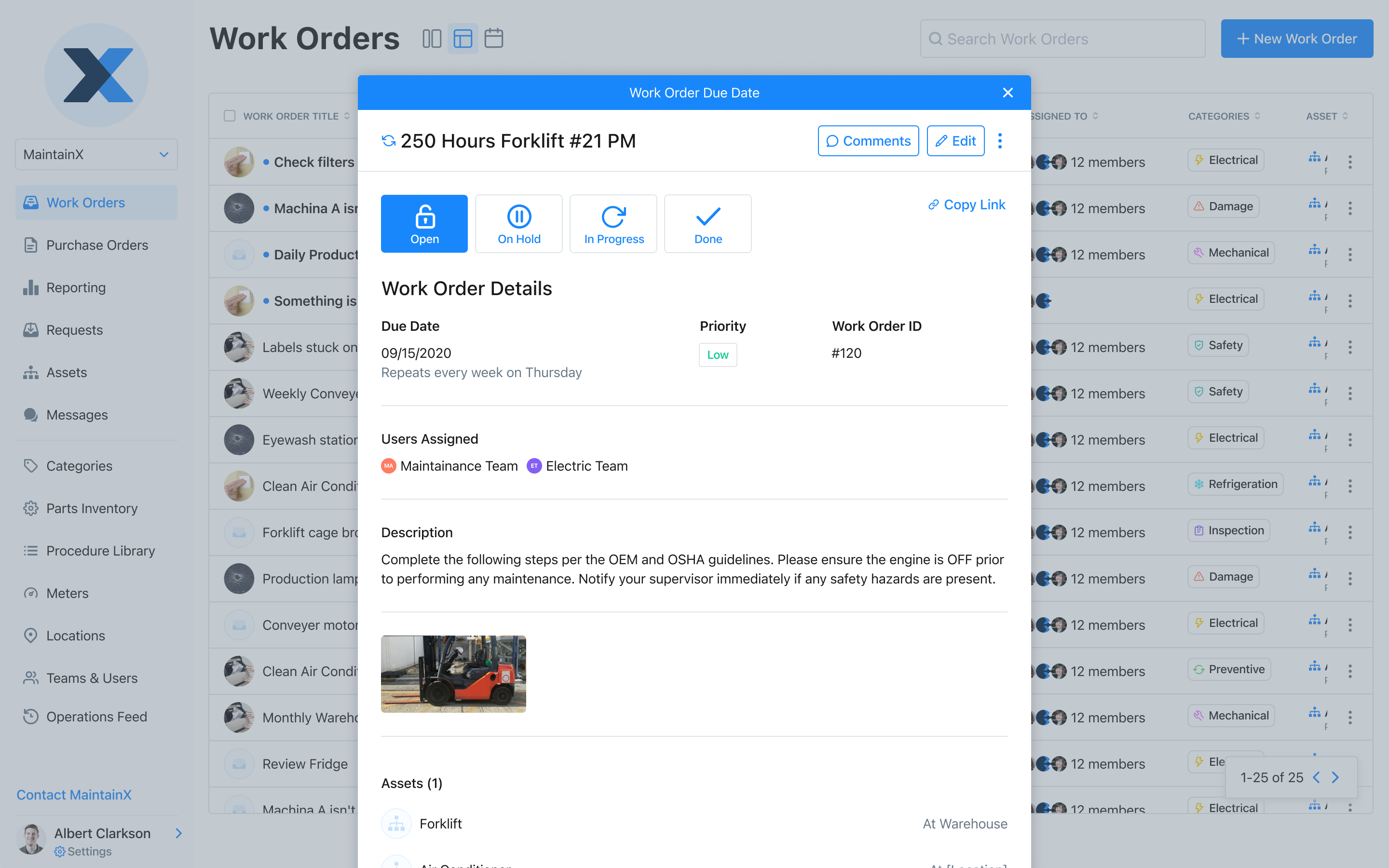
Create a Checklist for Each Asset or Machine
No matter which system of categorization you use, it’s likely that you will have many pieces of equipment that require regular checks and periodic preventive maintenance. For example:
- Items such as HVAC systems need their air filters changed at specific intervals
- Gutters and downspouts need to be kept free of leaves and debris to avoid blocked drains or heightened fire risk
- Boilers, water heaters, and pipes need to be monitored for corrosion. And, thermostats need to be in good condition and calibrated at specific intervals
- Fire extinguishers and carbon monoxide detectors all need to be checked at regular intervals by approved technicians
You can develop a maintenance or inspection task list for each asset. This gives your maintenance team a replicable, structured process to follow.
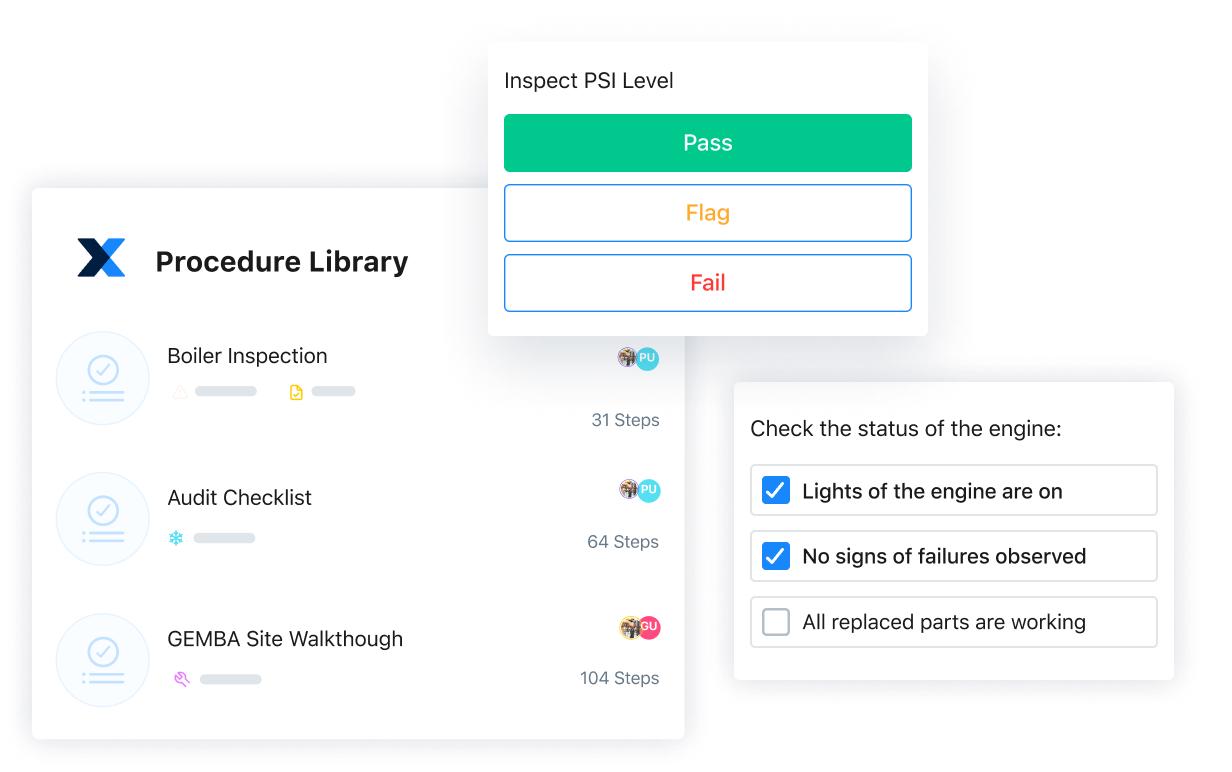
Tie Your Maintenance Task List to a Standard Operating Procedure
Add your checklist to a standard operating procedure (SOP). This will close the loop on your maintenance plan and ensure teams use checklists at the right time.
A PM task list can provide the “what.” But, your SOPs fill in the rest of the picture with the “who,” “when,” and “where.”
Developing a thorough compilation of SOPs is central to running a productive, efficient business. Adding work orders to the mix means your maintenance department will help your maintenance team run like clockwork in no time.
“With the industry evolving faster than ever to meet the growing demands of its customers, it’s important to have an exceptional checks system in place to guarantee the quality of both the work being completed and the final product being produced.”
ReliablePlant
Get a CMMS to Automate Your Maintenance Task List
Regardless of the size of your manufacturing facility, implementing a general maintenance task list can deliver numerous benefits. This seemingly straightforward tool can revolutionize your operations, boosting efficiency, increasing productivity, and augmenting safety levels.
One of the primary benefits of a general maintenance task list is its role in facilitating preventive maintenance. In addition, PM allows for scheduled inspections and machinery servicing, ensuring optimal performance at all times.
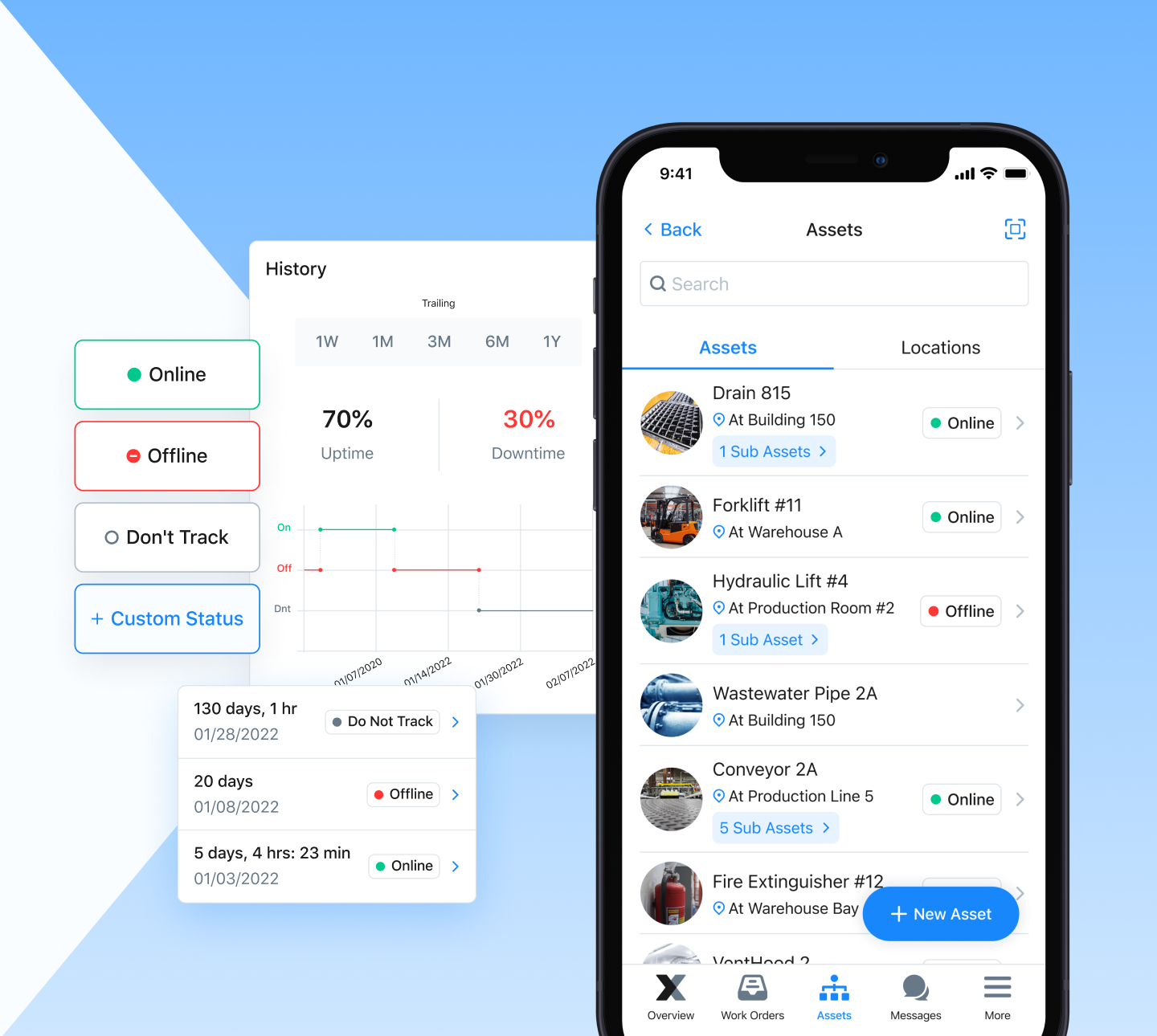
This also prolongs the useful life of your equipment, resulting in substantial cost savings over time. In addition, with a CMMS, you can automate preventive maintenance tasks, providing alerts for scheduled maintenance, thus minimizing the risk of human error and oversight.
Implementing a general maintenance task list, particularly with a CMMS, improves workflow and organizational and team coordination. Clear delineation of tasks ensures that everyone on the team understands their responsibilities, timelines, and the people accountable for each job.
This clarity helps reduce misunderstandings, overlapping tasks, and neglected maintenance responsibilities. Furthermore, a CMMS provides a systematic and easy-to-understand platform for onboarding new staff. A well-designed maintenance task list can enhance your team’s efficiency. In turn, this creates a more fluid and productive operation.
Set Up Your First Maintenance Task Checklist with MaintainX
Facility managers can take advantage of digital maintenance and work order software to keep maintenance crews accountable and focused on the right equipment. There are plenty of options on the market, ranging from older, resource-heavy applications to the newer generation of user-friendly apps like MaintainX.
Designed to automate traditional paper-based processes, today’s modern CMMS (Computerized Maintenance Management Software) allows you to schedule regular maintenance tasks and inspections, log repair requests, raise work orders, and plan for labor and inventory requirements.
With everything in one place and visible to all levels of the organization, a CMMS helps you democratize information and ensure diverse teams stay on top of your facility’s maintenance needs.
Schedule a tour of MaintainX or download the app for free and start creating maintenance task lists today.
FAQs
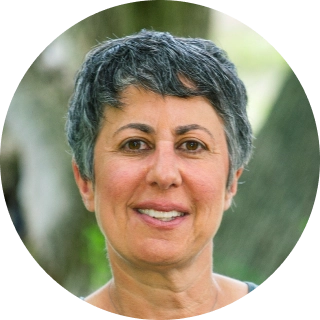
Caroline Eisner is a writer and editor with experience across the profit and nonprofit sectors, government, education, and financial organizations. She has held leadership positions in K16 institutions and has led large-scale digital projects, interactive websites, and a business writing consultancy.