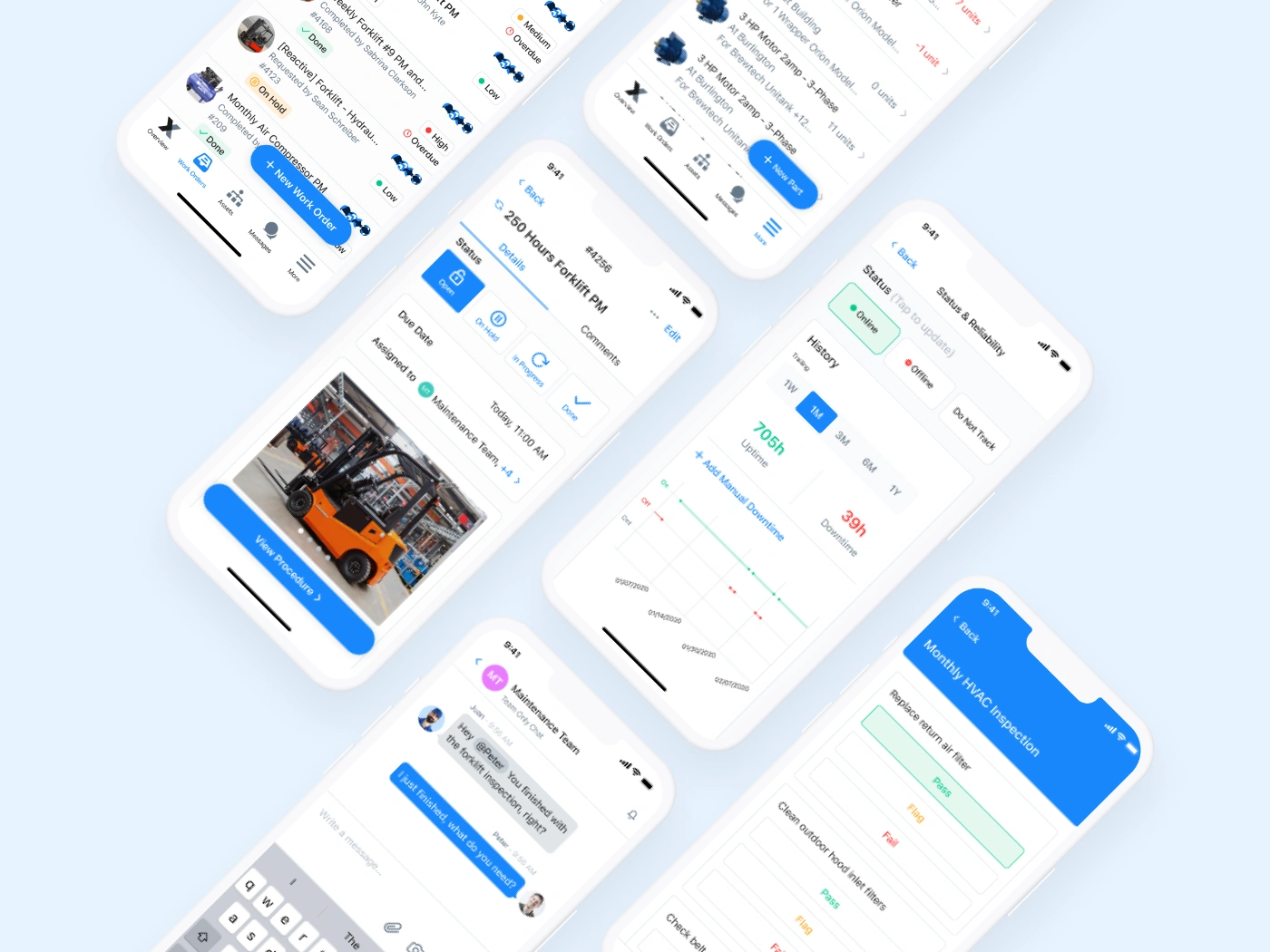
Maintenance teams worldwide are looking for digital solutions to improve cost, efficiency, and safety ratings. Looks like you've also realized you can't effectively improve your teams’ metrics with only unwieldy spreadsheets, legacy software, and stacks of paper. For many, the solution is a CMMS, a computerized maintenance management system. But what is a CMMS, and is it the right tool for your team? We'll cover what a CMMS is, how to effectively implement one, and how to showcase real results for your business.
What is a CMMS?
A Computerized Maintenance Management System (CMMS) is a software-based solution designed to help organizations efficiently manage and maintain their equipment, assets, and facilities by automating and optimizing maintenance processes.
A CMMS organizes a company’s maintenance operations, streamlines procedures, eliminates paper stacks, enhances team communication, and supports cost-effective managerial decision-making.
Often referred to as EAM software (we'll talk more about how they're different soon), CMMS platforms are robust tools that can be used on desktops, tablets, and smartphones.
How do CMMS Systems Work?
Most CMMS platforms include four primary elements:
- Operator Interfaces are the core of the CMMS experience. Essentially, they are the smartphone and desktop screens that allow you to navigate features for recording equipment information; creating, assigning, and tracking maintenance tasks; monitoring inventory; messaging maintenance technicians, and tracking asset history.
- Reporting Dashboards synthesize your collected information into KPI-driven reports that can provide insight into process inefficiencies. For example, you might generate a report comparing the time and cost spent repairing an asset in 2019 versus 2020 before making a capital purchase decision.
- Administrative Settings allow CMMS administrators to customize user-based permissions for various team members. Users can limit user rights, create work order templates, and search filter specifications.
- Databases for modern online maintenance systems are typically “in the cloud.” However, some older systems are still configured for in-house servers. The advantage of cloud storage is unlimited scalability, accessibility, and data security/redundancy.
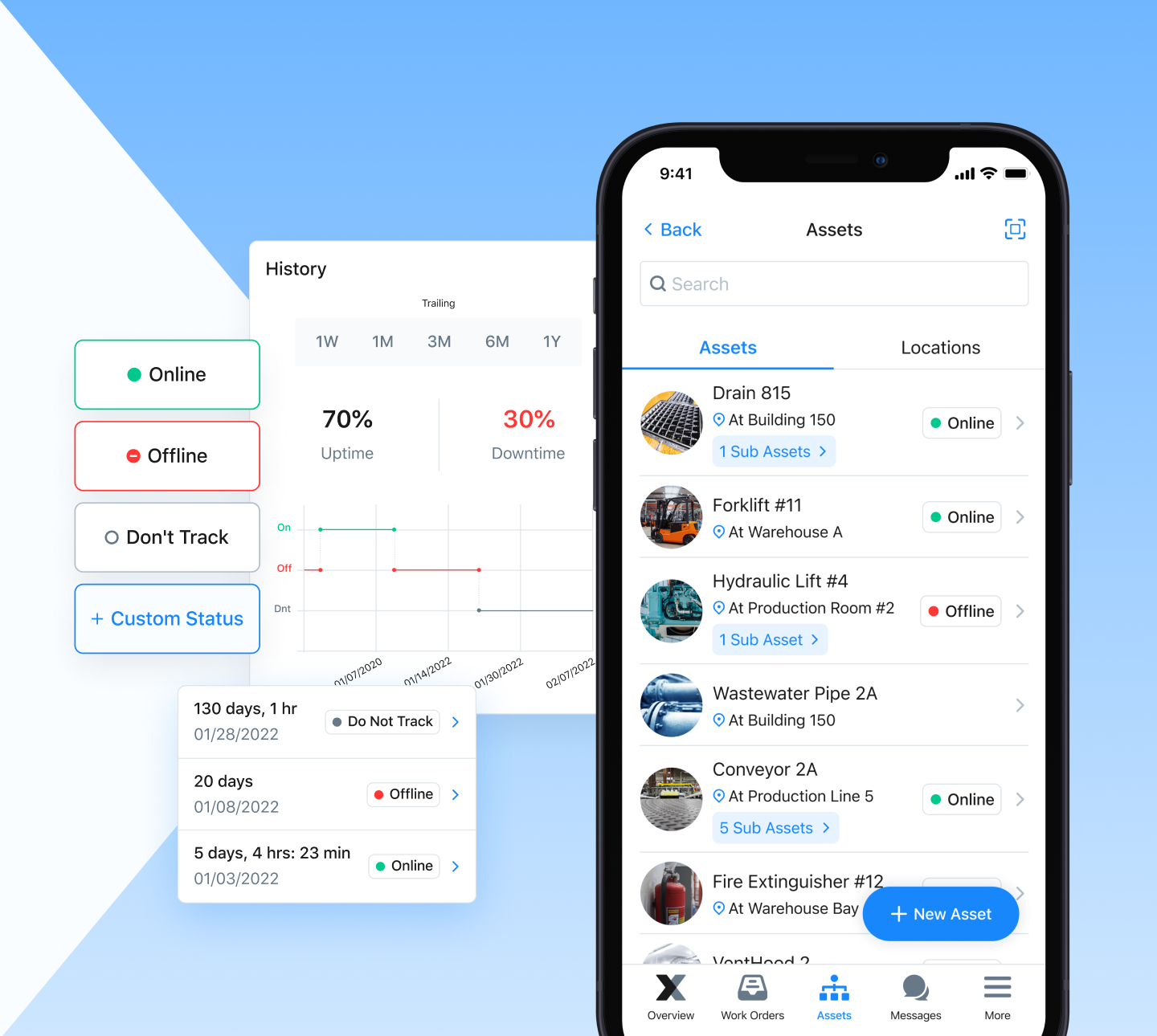
Why Use CMMS With Your Organization
For most companies, it comes down to saving money. With razor-thin margins, it's easy to understand why that's a primary motivation. But, there are many reasons to adopt a CMMS to make your team work more efficiently together.
These days, the primary motivating factor—for most companies—is to save money. CMMS features allow operational managers to track maintenance activities, implement advanced maintenance processes, automate workflows, and make cost-effective decisions in a manner that is nearly impossible without digital organization.
Reduce Downtime
Due to extraordinary global economic growth, many operational managers are now under pressure to maintain intense production schedules and reduce asset downtime with proactive maintenance strategies. Factor in the responsibility of managing hundreds of assets, and is it any wonder companies are increasingly looking toward CMMS digital management solutions?
While running a successful maintenance program with clipboards and Excel spreadsheets is possible, it isn’t easy. Without a proper asset management solution, maintenance teams often find themselves in a “reactive mode” rather than a proactive mode.
Eliminate Indirect Costs
Indirect maintenance costs lurk underneath the surface in the form of reduced asset lifecycles, high energy costs, lost production, late deliveries, inefficient equipment scheduling, and various wasted resources. And direct maintenance costs appear in the form of labor, materials, contracts, and overhead expenses. These are the problems CMMS services seek to solve by making proactive maintenance a realistic, achievable, and stress-free goal.
Increase Transparency and Accountability
Another benefit for many organizational leaders using CMMS is increased transparency. For better or worse, maintenance management software emphasizes the areas where departments are already excelling and the areas that need improvement.
With robust CMMS reporting features, leaders can quickly determine, for example, policy compliance by team, which machines cause the most problems, and where there is overspending. Tracking asset health in an organized manner allows management to fine-tune their strategies toward reducing downtime, cutting costs, and increasing asset longevity.
Unfortunately, CMMS software providers don’t consistently deliver these hyped-up results, and companies don’t always meet their goals. In section five, we’ll look at the most common reasons electronic maintenance management system launches fail. But first, here’s what happens when CMMS goes right:
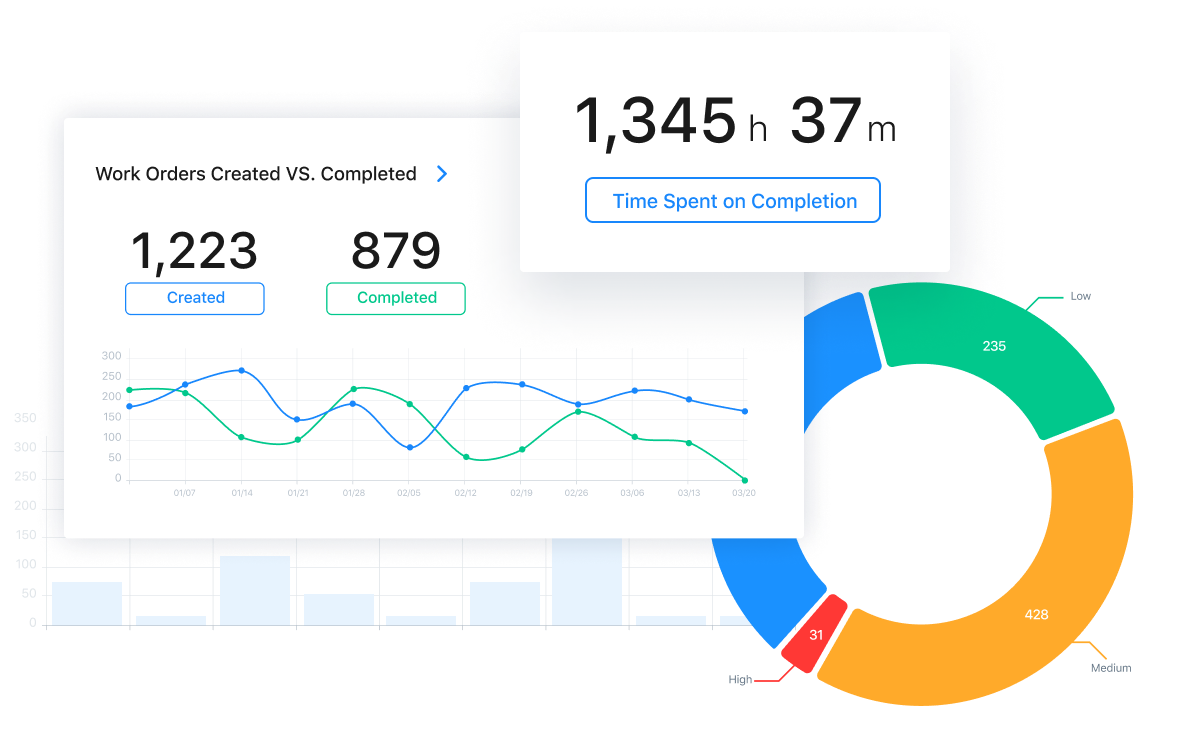
Features and Benefits of CMMS Software
CMMS is designed to be a central component of your maintenance department, providing operational support in several ways. With CMMS, you can:
- Streamline Preventive Maintenance: Operational managers can create, assign, and monitor work orders in one place.
- Organize Inventory Management: Maintenance teams can track the movement of spare parts and reorder replacements as needed.
- Reduce Downtime: Technicians can report asset failures on-site from the convenience of their smartphones, reducing the length of equipment downtime.
- Improve Cost-Effectiveness: CMMS analytics provide management with insightful information that allows for better decision-making.
- Enhance Communication: MaintainX is the only provider that offers CMMS instant messaging within individual, group, and work-order chat threads. Translation: Important information arrives in real time and never falls through the cracks.
- Increase Compliance: Digital audit trails allow managers to determine who completed what task and when. Workers can digitally designate work orders as open, in progress, or closed, so managers always know what’s up.
- Simplify Bookkeeping: Accounting and finance leaders can easily access asset information that informs capital expenditure decisions and tax reporting.
- Improve Asset Management: CMMS allows managers to catalog and track assets by location, category, serial number, date, and more.
- Support Condition-Based Monitoring: Advanced CMMS platforms sync with sensor technology to provide real-time insights into equipment wear, tear, and potential failures.
Industry reports show that using a CMMS can deliver real bottom-line benefits by increasing production capacity and reducing maintenance costs.
- Maintenance productivity increase of 28.3% (A.T. Kearney)
- Downtime reduction of 20.1% (A.T. Kearney)
- Maintenance, repairs, and operational (MRO) inventory cost reduction of 17.8% (A.T. Kearney)
- Equipment life increase of 10 to 15% (CompareSoft)
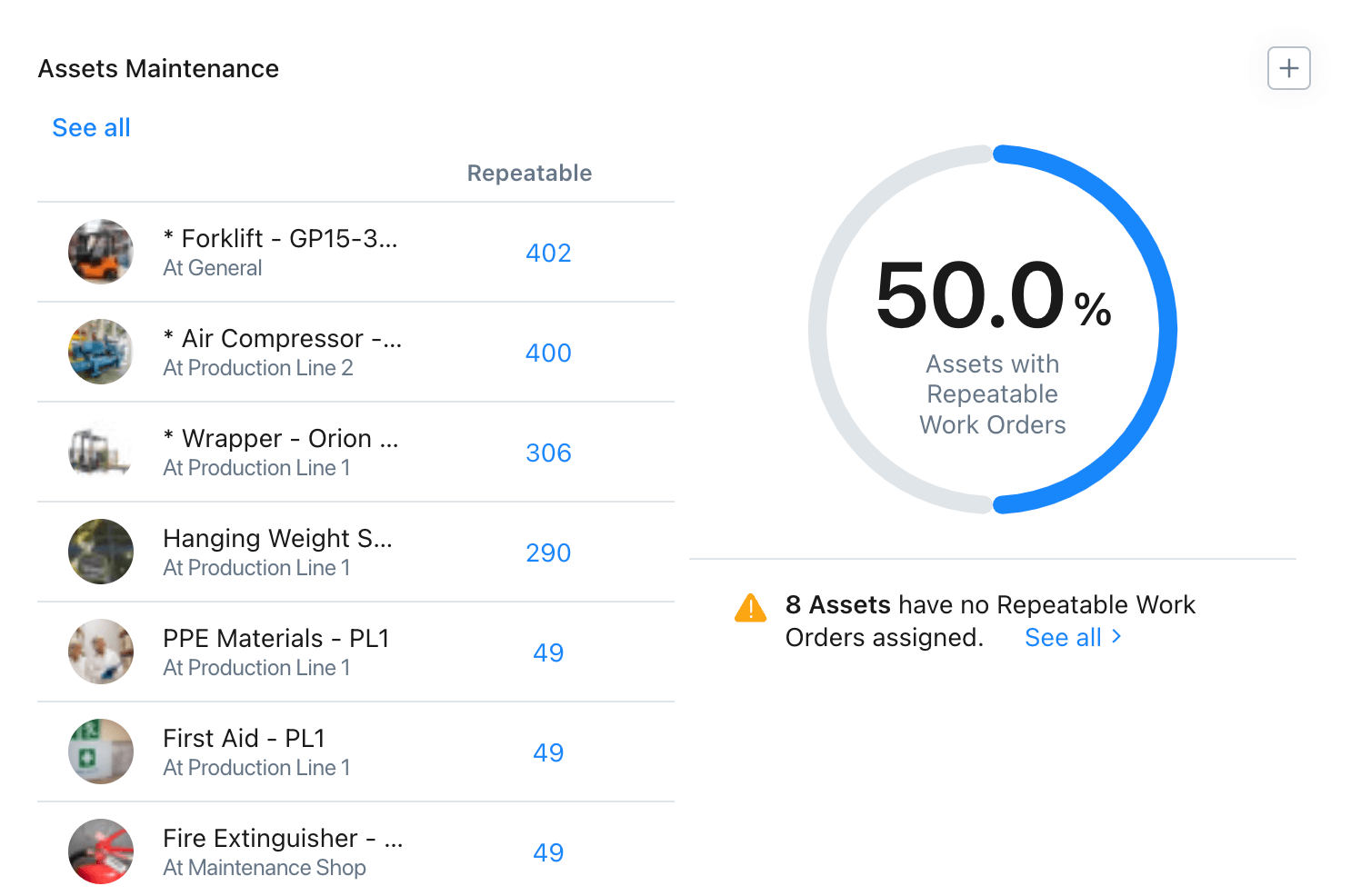
Common Objections to CMMS
1. My Team Won’t Use It
Fears of low adoption put many organizations off introducing a CMMS. Rolling out new software is always an investment of time and cost. If people don’t use the software, then it will not deliver a return. That’s why it’s critical to choose a solution that is built specifically for frontline teams and proven to be quickly adopted on the shop floor.
2. My Data Won’t Be Secure
You can lock paper work orders in a filing cabinet, but what if someone hacks into your CMMS and steals valuable data, or an employee goes rogue and deletes all of your asset history? This is understandably a concern for many CMMS buyers, but it needn’t be. Modern CMMS is protected by custom user permissions, cloud security, and data backups. Just make sure you select a CMMS that takes security seriously and has security certifications, like SOC2 and ISO27001.
3. The IT Department Won’t Allow It
At larger organizations, in particular, IT folks can meet new software with great skepticism. In addition to data security concerns, IT departments often manage an array of software solutions and worry that introducing another one will create a data silo. These fears can be alleviated by selecting a CMMS that can integrate with their existing technology stack, such as IoT devices, ERP systems, and business intelligence tools. Most importantly, look for CMMS solutions that adhere to the latest enterprise security protocols, such as SOC2 compliance and ISO27001 standards.
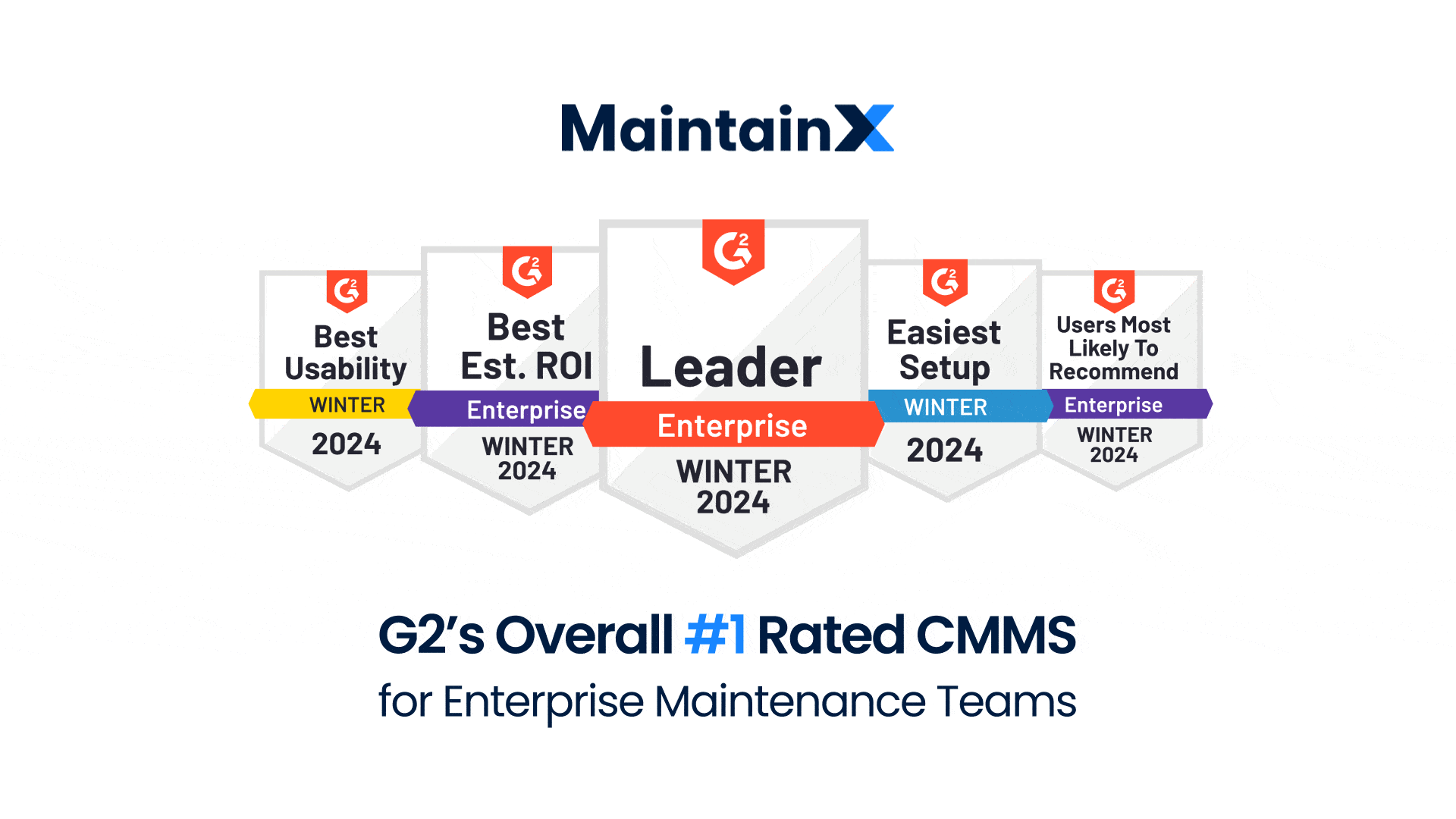
How to Ensure a Successful Implementation
Many executives are hesitant to invest in CMMS programs, and for good reason. Some experts estimate 80 percent of plant maintenance management system implementations fail (more on that in a moment).
While the statistic isn’t nearly as high for other industries, operational managers should understand these common reasons for failure before investing:
1. Executive Leadership Doesn’t Support It
One of the most crucial components of a successful software launch is setting realistic expectations. Projects with unrealistically short milestones inevitably lead to timeline extensions, which yields the unfair impression of failure.
Understandably, executives sometimes become suspicious of projects that take longer than expected. For this reason, CMMS advocates must ensure organizational leadership fully understands the realistic requirements, and time involved, in setting up new maintenance programs for success. Those who entirely sell leadership on the features, benefits, and projected ROI of implementation will garner sustained support for implementation. The most successful champions educate executives on the criticality of reliability in managing predictable organizational growth.
2. Management Views the Software as a “Strategy”
CMMS isn’t a maintenance strategy—it’s a tool that makes it easier to practice preventive maintenance, predictive maintenance, reliability-centered maintenance, and other standard operational methodologies.
Unfortunately, some executives mistakenly purchase automated maintenance management platforms under the false assumption the software will fix their upkeep woes. While we all love tales of magic beans, this couldn’t be further from the truth. Operational managers must still take the time to conduct asset audits, identify appropriate maintenance strategies, and learn to use the software to address their maintenance needs.
3. Organization Isn’t Ready
Sometimes, CMMS launches fail because the maintenance team does not take advantage of the software. You can avoid this dilemma by asking yourself: Which stage of maintenance evolution is our team in right now?
Organizations exclusively practicing run-to-failure maintenance aren’t the best candidates for legacy CMMS systems. Ideally, an organized preventive maintenance strategy should be in place before integrating work order software or EAM software. This is because it takes time to track down manufacturers’ recommendations, evaluate past asset history, create proper workflows for large numbers of assets, and train team members.
4. Workers Find the CMMS System Too Complicated
Approximately 90 percent of plant maintenance managers say they are not using their CMMS at maximum capability, according to a Reliable Plant survey conducted by educator Kris Bagadia. Ease of use is one of the leading factors of successful CMMS implementation.
“I knew that it was going to be a high percentage, but I didn’t know it was going to be that high,” he says. Bagadia surveyed 299 industrial maintenance professionals, who oversaw 938 plant assets on average, to learn more about the obstacles large-scale plant managers face when implementing CMMS programs.
Unfortunately, it’s not uncommon for organizations to underestimate the hours of training required to implement plant maintenance management systems. Bagadia also found that nearly three out of 10 respondents took one to three years to implement their CMMS systems!
Additionally, more than one in four respondents said their employees spent between 100 and 200 hours collecting asset data for implementation. This is unacceptable from our standpoint—CMMS should be intuitive.
However, organizations of any size and stage can use intuitive, freemium CMMS smartphone apps like MaintainX.
Click here to read CMMS Software: Being Tech Savvy Shouldn’t Be a Usage Requirement
How to Evaluate CMMS System Solutions
Conducting due diligence when reviewing computerized maintenance management systems is time well spent. The right platform can help reduce costs, increase productivity, enhance compliance, and simplify daily tasks for everyone within a department.
Here are our best tips for assessing software options:
1. Know What You Need (and What You Don’t)
What works for one company may not work for another. Before shopping, write down all of your maintenance, compliance, and asset management challenges. You can then compare your requirement list against the features listed on CMMS provider websites without being swayed by unnecessary capabilities. Do you need meter readings? Do you need to integrate regulatory compliance procedures?
Moreover, effective work order management is the starting point for making informed decisions about your assets and equipment. Management features that empower asset tracking and reporting are fundamental. Maintenance history should be easily accessible to monitor asset performance and uptime over time.
As previously mentioned, many industries with various needs use CMMS systems. While an industry-specific solution may sometimes be the obvious best choice, don’t overlook versatile applications. For example, cloud-based software programs often come with API integrations that allow users to share data with other management systems. You can tailor these CMMS solutions to meet your needs. While it's important to consider your immediate needs, it's helpful to imagine what the 'end-state' might look like and validate that your solution of choice can help you reach those goals as well.
2. Prioritize Programs with High User-Adoption and Usage Rates
User Adoption is the measurement of how frequently, quickly, and efficiently technicians use new software. User Adoption is also a component of Time to Value, which addresses how fast an organization realizes the value gained.
Unfortunately, you won’t typically find this information on CMMS provider websites. But you can request these statistics from sales reps during the evaluation process. Here are some questions worth asking:
- What percentage of users within my industry stick with your app?
- How often do technicians complete work orders using the app?
- Do technicians and supervisors experience greater autonomy?
- How have MTTR and MTBR improved for your clients?
Indeed, don’t be afraid to ask for industry-specific case studies or client contact information to obtain the information you need. Furthermore, try the software for free with your team members before making a purchase decision.
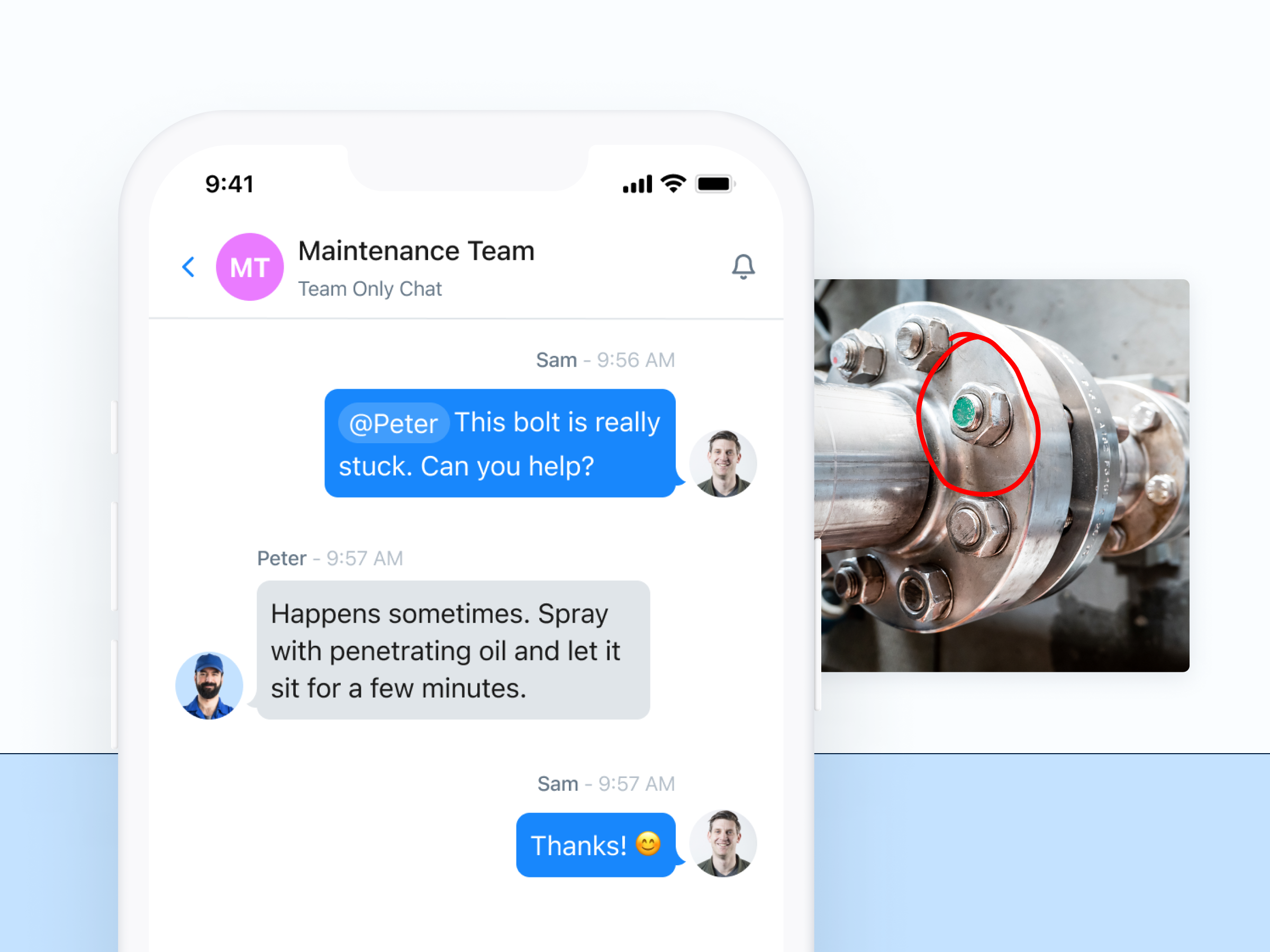
3. Consider Mobile-First Apps with Chat Functionality
Does your team work in a large-square-footage facility? Do your technicians regularly leave headquarters for offsite work? Do they simultaneously communicate with you through walkie-talkies, text messages, and emails?
Moreover, consider prioritizing a CMMS platform designed for smartphone usage. Exchanging information via multiple devices works until essential pieces of information fall through the cracks, and everyone points fingers at one another when the proverbial sh%t hits the fan.
Put simply, scatter-shot communication systems aren’t conducive to organizing complicated instructions for individual work orders. Not surprisingly, MaintainX is the only maintenance work order software platform with native chat functionality. As reported in our 2019 Year-in-Review survey, “work order commenting” was voted the app’s most popular feature. Additionally, we designed MaintainX specifically for mobile usage.
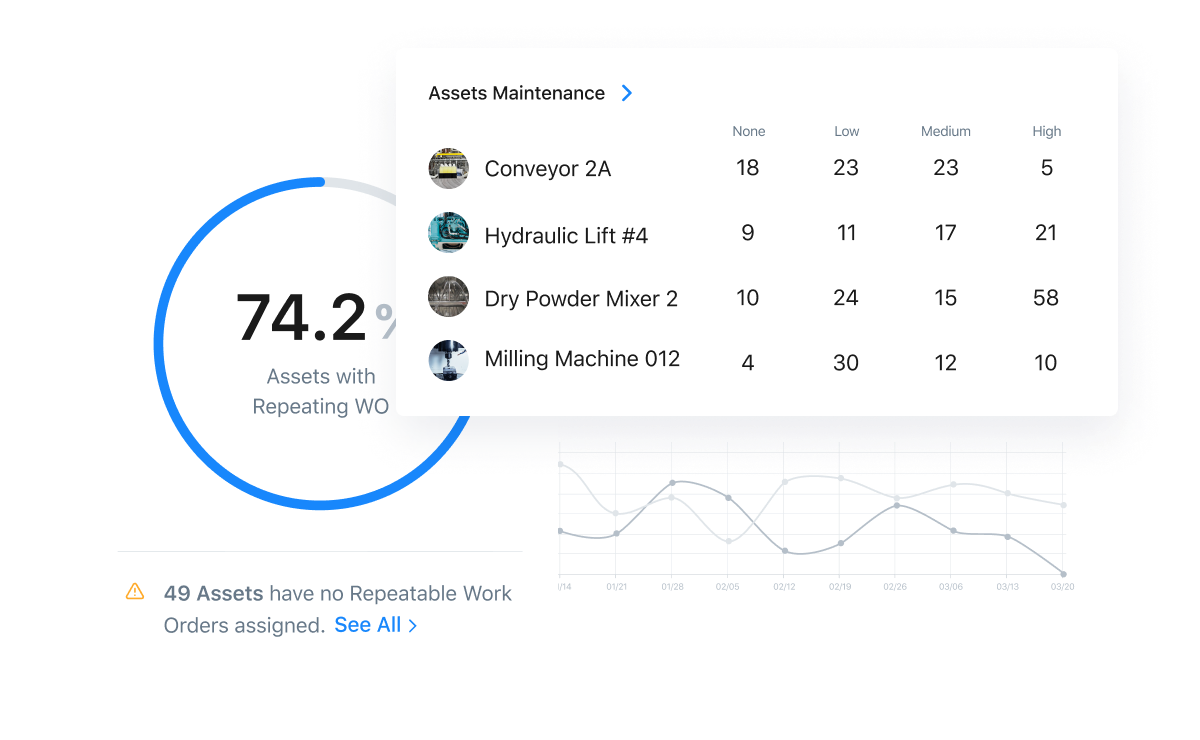
4. Choose Meaningful Data Reporting (Avoid Black Holes)
Choose a CMMS that not only compiles equipment data but translates it into useful and familiar industry metrics. To emphasize, Ashraf Labib, a research scientist at the University of Manchester Institute of Science and Technology, describes most off-the-shelf software—especially computer-aided maintenance management solutions and enterprise resource planning (ERP) systems— as “black holes greedy for data input that seldom provide any output in terms of decision support.”
“This lack of decision support is a definite problem because the key to systematic and effective maintenance is managerial decision-taking that is appropriate to the particular circumstance of the machine, plant, or organization,” Labib says. “This decision-making process is all the more difficult if a CMMS can only offer an analysis of recorded data.”
Dating Reporting Example
Say you create a monthly recurring work order to change an oil filter. This scheduled reminder is a good starting point if you’re an SMB transitioning away from reactive maintenance.
However, a more advanced maintenance department may need value data metrics that illustrate how to fine-tune maintenance schedules beyond a manufacturer’s recommendations. Organizations in this category should prioritize CMMS data collection software that simplifies complex metrics into user-friendly charts, graphs, and KPIs (e.g., MTBF, MTTR, and MTTF). Your reports should illustrate answers to questions like:
- How much time did Carl spend on safety audits last month?
- What percentage of our preventive maintenance tasks did we complete?
- Should we continue maintaining our HVAC or purchase a new one?
- Are we understaffed or overstaffed (and inefficient)?
Furthermore, your CMMS should cross-reference work order data by assigned technician, asset type, priority status, time to complete, and more to integrate into meaningful reports that support sound decision-making.
5. Know Your Projected ROI and Key Metrics
Before handing over your company credit card information, it’s essential to calculate the expected ROI of your CMMS work order system. Of course, your boss will want to know: How long will it take to get our money back?
While it’s impossible to have absolute certainty—with many unknown variables in the mix— you can make an educated guess using an ROI model.
Calculating ROI with MaintainX
By analyzing work orders created and resolved in a specific department, across a facility, within a team, or completed by an individual, you will get both real-time snapshots and deep dives into how the work is getting done. With MaintainX, you can:
- Navigate real-time performance data for KPIs
- Identify insights that allow you to highlight organizational bottlenecks and take action
- Track assets to manage asset downtime and capital equipment allocations
- Monitor team performance to identify top performers and employee performance efficiency
- Monitor metrics to calculate KPIs across assets, teams, and locations
Dashboard metrics are evidence of the success or failure of workflows throughout a company or a team, with an individual, or even with a particular piece of equipment.
Return on Investment (ROI) Formula
The projected value of your CMMS investment is the total expected reduction in maintenance costs due to program implementation. You can calculate your ROI based on a one-year, three-year, or five-year interval.
Here’s the formula:
CMMS ROI = (CMMS Value – CMMS Cost)
CMMS Value is based on the following five categories of unnecessary costs:
1. Asset Life
- Estimate the number of years the manufacturer expects asset life extension by executing preventive maintenance.
- Translate the longevity improvement into a dollar amount by comparing it against a brand-new asset’s purchase prices.
- Repeat the process for every organizational asset.
- Add your assets’ potential savings for a longevity grand total.
2. Downtime
- Determine how often unscheduled downtime occurs per year.
- Compare daily, weekly, and monthly revenue reports to determine how asset downtime impacted revenue loss.
- Calculate a total downtime loss for your chosen ROI parameter (e.g., one year, three years, or five years).
3. Parts Inventory / Material Waste
- Estimate how much time your organization has lost responding to emergency purchase orders.
- Estimate how much overstock inventory has cost your organization in terms of carrying costs and obsolete parts.
- Add the numbers for the total parts/inventory value.
4. Labor Costs and Efficiency
- Determine an average hourly labor amount wasted.
- Estimate how much your organization spends and can avoid on overtime hours and contract labor.
5. Safety and Compliance
- Estimate the average cost of a safety or compliance incident in your workplace
- Average your historical safety incident rate with that cost
Once you’ve finished calculating your estimated value totals, it’s time to evaluate your projected platform costs.
CMMS Costs vary by user number total, feature package, and vendor. Modern platforms like MaintainX require zero to little training for mastery, while most legacy programs necessitate paid training modules. Evaluate all potential CMMS fees before plugging your total CMMS Cost into our formula:
CMMS ROI = (CMMS Value – CMMS Cost)
Not surprisingly, most MaintainX clients experience a first-year ROI ranging from 25 to 300 percent. Your results will vary depending on your organization’s starting point, maintenance strategy, and consistent use of the CMMS.
EAM vs. CMMS: What’s the Difference?
If you’ve heard about computerized maintenance management software (CMMS) and Enterprise Asset Management (EAM) tools, you might assume they perform the same role. And you wouldn’t be one hundred percent wrong. However, currently, there is one difference between the two.
Enterprise Asset Management software collects, houses, and analyzes data from early asset procurement to end-of-life asset disposal (decommissioning expired, obsolete, and unusable assets).
What separates EAM software from basic CMMS solutions is an emphasis on complete tracking from asset acquisition to disposal AND integration with financial data from other company departments to reduce long-term, asset-related expenses. Conversely, traditional CMMS solutions almost exclusively focus on monitoring asset conditions to help improve asset servicing decisions. However, many modern CMMS platforms like MaintainX provide the same functionality as an EAM.
Consequently, a CMMS focuses primarily on planned and preventive maintenance scheduling; work order management; standard operating procedures, inspections and audits, and other aspects of using, fixing, and optimizing physical assets.
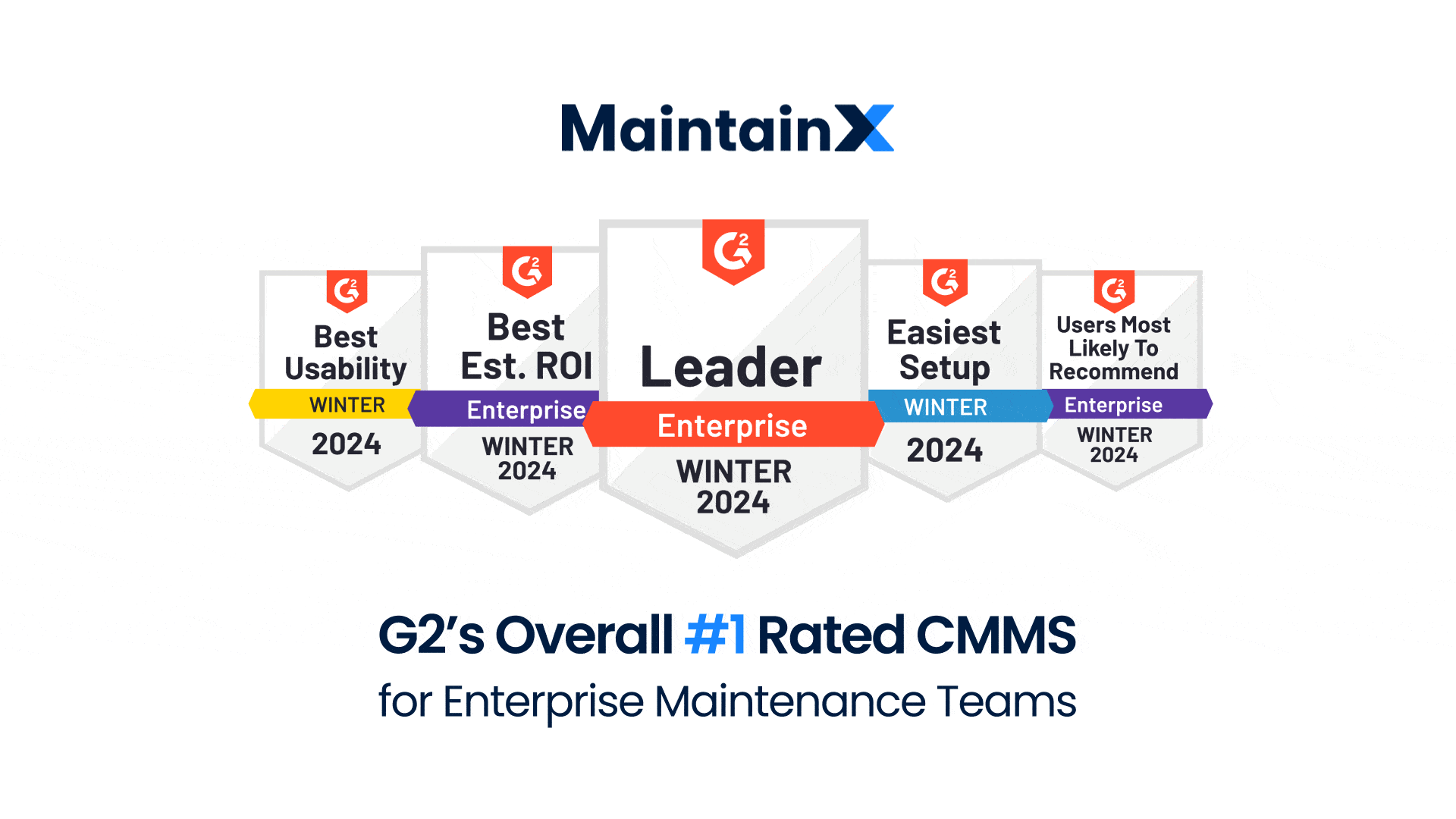
The Best CMMS Software
What is the best CMMS software available? Obviously, we’re biased when we name MaintainX as the top CMMS platform. However, we would be remiss to say other vendors aren’t worth exploring.
Below is a quick CMMS comparison review of the top three options. Why not summarize the top 10 CMMS software options or even just the top five work order software programs?
Put simply, most CMMS options are antiquated. The following options are your best bet in terms of usability, modernity, and depth of features. Most of these platforms include everything you need to create, assign, and track work orders and maintenance; execute preventive maintenance programs; document Standard Operating Procedures (SOPs); manage inventory; maintain asset logs; track work requests and maintenance requests; create invoices; configure API integrations, and report KPIs. So what is the best CMMS Software?
1. MaintainX

Not surprisingly, MaintainX is the world’s first CMMS platform designed with real-time chat. In other words, operational managers, maintenance technicians, and key stakeholders can instant message one another directly within the app’s work orders.
From day one, we designed MaintainX specifically for smartphone use. Comparatively, the majority of CMMS providers adapted their software for mobile devices from complex desktop-based legacy systems. Translation: These adapted CMMS programs aren’t always user-friendly.
However, the most compelling draw for MaintainX is the abundance of features included within the app’s freemium plan, making the software accessible for SMBs and large corporations. We’ve proudly garnered hundreds of positive reviews from customers in both the Apple App and Google Play stores.
Noteworthy Features:
- Generous Free Plan: Includes unlimited work orders, team messages, assets/locations, and Web/mobile access; five work orders with photos per month; two work orders with forms per month; and one month’s worth of reporting analytics (ability to test with your team to decide if it’s useful enough to upgrade).
- Instant Messaging: Segment chat conversations by individuals, groups, departments, topics, and more.
- Work Order Commenting: Chat with technicians directly within individual work orders to troubleshoot in real time.
- Photo Uploading: Upload (and mark up) photos of equipment failures, parts issues, or maintenance quandaries to better illustrate what’s happening.
- User-Friendly Interface: The interface is sleek, quick, and easy to navigate (designed specifically for smartphones, tablets, and desktops).
- PDF Uploading: Upload important PDFs, manufacturer’s guidelines, training manuals, and company policies directly within individual work procedures.
- E-Signatures: Technicians can sign off on completed jobs for additional accountability and the app’s time stamp feature.
2. UpKeep
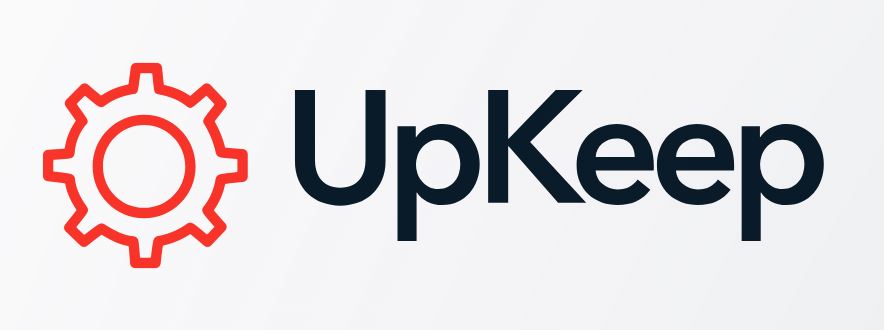
The maintenance software app, UpKeep, also receives high rankings for usability, features, and customer support. Founded in 2014 and developed specifically for mobile usage, the mobile app allows maintenance teams to create and manage recurring work orders, track inventory, run billing/invoicing, manage calibrations, control keys/locks, and more.
In addition, we’ve heard tons of positive feedback from property managers regarding UpKeep’s requester portal! Also, it’s worth mentioning that UpKeep’s freemium version was created with the goal of allowing users to “try before they buy” and isn’t meant to be a complete CMMS solution.
Noteworthy Features:
- Trilingual: Available in English, French, German, and Spanish.
- Photo Uploading: Upload (and mark up) photos of equipment failures, parts issues, or maintenance difficulties to better illustrate what’s happening.
- PDF Uploading: Upload important PDFs, manufacturer’s guidelines, training manuals, and company policies directly within individual work procedures.
- E-Signatures: Technicians can sign off on completed jobs for additional accountability and the app’s time stamp feature.
Potential Drawbacks:
- No work order chat feature.
- Free plan doesn’t provide a complete CMMS management system.
3. Fiix
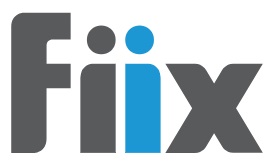
Founded in 2008, Fiix CMMS offers an open integration network, mobile maintenance management, and AI-powered insights. The app has received high user rankings for usability and customer support and offers a free plan with no end date.
Users can access work order management features, schedule preventive maintenance tasks, and build asset hierarchies.
On specific plans, the platform allows for multi-location asset management, custom analytics and reports, custom API integrations, and more.
Noteworthy Features:
- Reporting: Users can track maintenance metrics with reports and customizable dashboards.
- AI-driven analysis: The CMMS can deploy AI to analyze data, find trends, and help users act on the data.
- Third-party integrations: Fiix users can connect the app to other software and hardware that their businesses already use so they can share data and trigger work across systems.
- Parts/Inventory Management: The software provides an overview of stock across locations.
Potential Drawbacks:
- No work order chat feature.
- Customers report needing help to understand analytics.
4.eMaint
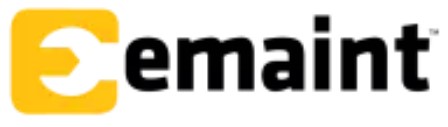
As part of the Fluke Corporation, eMaint aims to “unlock the power of connected reliability.” Like MaintainX, the organization seeks to streamline workers’ workflows by eliminating pen-and-paper processes.
To this end, eMaint offers a system for work order management, PM scheduling, condition monitoring, asset management, and inventory management. The platform also provides mobile functionality for simplified fieldwork and an offline module for work outside the network area.
It’s worth noting that while eMaint offers a free trial on request, there is no free version of the app. Once out of the trial period, users need a paid subscription to continue accessing the program’s features.
Noteworthy Features:
- Condition Monitoring: eMaint connects to Fluke’s testing and calibration sensors to conduct vibration analysis, monitor asset health, and get AI-driven recommendations.
- WO Scheduling: The CMMS app features a scheduler tool that allows users to drag and drop work orders into the calendar and view work order details from the scheduler.
- Multilingual: CMMS settings accommodate several common languages.
- Currency Conversion: The software features a currency feature that allows users to track costs and financial data in local currencies, with standard and customizable conversions available.
Potential Drawbacks:
- No free plan.
- Users report difficulty in reaching technical support.
- No work order chat feature.
Note: Each of the above CMMS solutions is scalable, cloud-based, and priced per user/per month. However, MaintainX is the only provider offering a complete CMMS solution at the freemium level. The three platforms are also Windows, Mac, Tablet, iOS, and Android compatible.
Looking for a free CMMS software option? Click here to read Free CMMS Software Programs: Do They Really Provide Value?
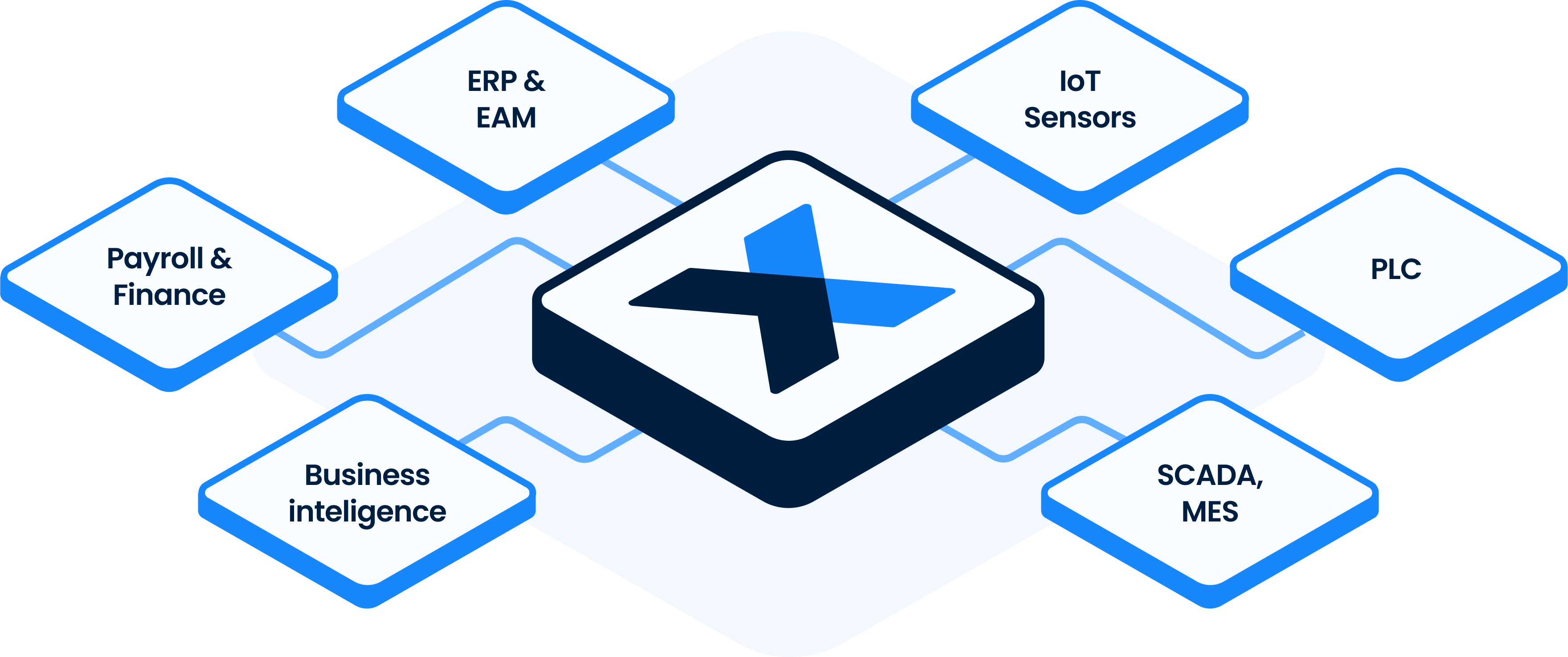
Get started with MaintainX
Modern computer-based maintenance management systems are sleek, intuitive, and affordable. With MaintainX, you don’t have to sacrifice features for simplicity—you can:
- Create reactive and preventive maintenance work orders.
- Assign recurring work orders to both teams and individuals.
- Monitor progress by maintenance category, priority level, downtime, etc.
- Analyze maintenance costs for greater efficiency and savings.
- Hold text conversations with team members in real-time.
Anyone with a smartphone can download the app and get started for free with our basic plan, which includes unlimited work orders, right away.
CMMS FAQ
What does CMMS stand for?
A CMMS (Computerized Maintenance Management System) is a specialized software designed to enhance an organization's maintenance management and asset handling. It provides an effective platform for maintenance managers to efficiently plan, monitor, and evaluate work orders, inventory management, and maintenance tasks. Using a CMMS can help an organization minimize system downtime, prolong the lifespan of assets, effectively allocate labor resources, and improve the efficiency of maintenance activities overall.
Who uses CMMS?
CMMS users include business owners, facility and maintenance management, asset planners, and maintenance personnel. Modern CMMS software is also helpful for safety managers, quality control managers, operations directors, logistics coordinators, and more.
Is a CMMS system necessary for small businesses (SMBs)?
For SMBs to stay competitive in the global, and even local, market, businesses must adopt technology that brings immediate efficiencies and impact. Being a small business used to mean that powerful software solutions were too expensive or complicated. Now, solutions like CMMS software empower teams with revolutionary tools that can grow with your business.
How does CMMS support preventive maintenance?
MaintainX CMMS maintenance software lets you build, for each asset, an infinite number of calendar and meter-based preventive maintenance (PM) tasks. You can provide a clear description of task procedures, instructions, and other essential details within the PM task record.
The CMMS records each PM and makes it accessible via Asset History. Maintenance scheduled in advance helps from things falling behind. This data supports your reporting insights about where operations need to improve.
How does CMMS track asset history?
Every time a technician completes a work order on an asset, the CMMS links the work order to the asset’s history for reference. These completed work orders also help drive reporting insights via the MaintainX dashboard to detail asset maintenance and cost history.
How much do CMMS platforms cost?
Not surprisingly, CMMS platforms range widely in cost across the market. MaintainX offers a 100 percent free CMMS solution while also offering solutions with additional functionality through our paid plans. MaintainX’s paid plans charge per user, with our Essential plan set at $8 per user per month on our annual plan. New users start with a free trial of our Premium plan.
Other CMMS solutions, like Hippo CMMS, can cost hundreds of dollars per user per month.
Do all CMMS solutions include chat functionality?
No. Most CMMS solutions do not offer chat or communication of any kind within the product. Some CMMS solutions allow for comments or notes on a work order, but MaintainX is one of the only solutions that provides direct chat throughout the app.
Where does the CMMS store data?
Cloud-based CMMS systems utilize sophisticated data encryption protocols along with routine updates and maintenance. In addition, MaintainX performs frequent security and penetration checks to ensure that client data is not compromised or otherwise unavailable. MaintainX stores data on encrypted Amazon Web servers because we prioritize data security across the entire system.
How does CMMS help manage spare parts?
Modern CMMS solutions like MaintainX offer parts inventory modules to track parts usage across work orders. When a maintenance team is disorganized, it can be difficult to find parts needed or even know if they are available on site. Our CMMS tracks parts usage and restock histories and even sends alerts to reorder when parts quantities are running low.
What are the advantages of CMMS reporting?
Well-implemented CMMS enhances your understanding of assets and organization by using the Reporting Dashboard feature to track key performance indicators ( KPIs), analyze trends, and generate reports for decision-makers. Maintenance managers can identify concerns such as increasing costs, low efficiency, or frequent maintenance using a CMMS to evaluate historical data and patterns.
Not surprisingly, MaintainX makes it easy to identify outliers in your organization. For example, through reporting, you can quickly identify a forklift that requires 10x more maintenance than any other in your fleet and adjust capital expenditures accordingly.
Do CMMS solutions provide technical support?
Support should be an important factor when evaluating CMMS solutions. Be sure to test support chat response times and ask about their Support Policy. Salespeople can promise you support, but if a solution you're evaluating lacks a support policy, those promises won't mean much should your team need assistance. MaintainX offers an industry-leading Support Policy with guaranteed response times with clear expectations around time to resolution.
What’s the difference between facility management software and CMMS?
Computer-aided facility management (CAFM) and computerized maintenance management systems (CMMS) are primarily differentiated by core functionality and unique user needs. CAFM software helps facilities managers simplify different areas of facilities management, particularly in managing real estate.
On the other hand, some variation of a CMMS is typically part of a CAFM. Many organizations use a CAFM to manage real estate operations and integrate a native CMMS like MaintainX to assist with maintenance and operational tasks.
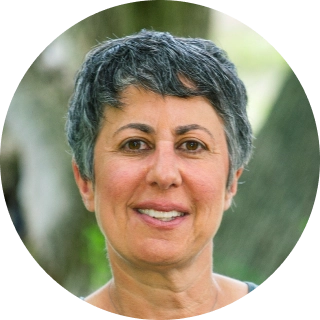
Caroline Eisner is a writer and editor with experience across the profit and nonprofit sectors, government, education, and financial organizations. She has held leadership positions in K16 institutions and has led large-scale digital projects, interactive websites, and a business writing consultancy.