
Computer-Aided Facilities Management uses software and digital solutions to manage facilities and physical space. Computer-Aided Facilities Management (CAFM) solutions leverage information technology to help organizations plan, execute, and streamline all facility activities. From asset management to reactive and preventive maintenance, CAFM software helps oversee the management of the physical workspace.
To be clear, using Computer-Aided Facility Management software is not the only way to manage the physical workspace. CAFM systems are only one type of facility management system. Other types of software solutions include:
- Integrated Workplace Management Systems (IWMS)
- Enterprise Asset Management Systems (EAM)
- Computerized Maintenance Management Systems (CMMS)
Let’s take a closer look at these options now.
Facility Management Software Solutions
Integrated Workplace Management Systems
Integrated Workplace Management Systems (IWMS) focus on managing physical spaces. In this way, they aren’t too different from CAFM solutions. However, IWMS solutions are more focused on large-scale property management.
Facility managers overseeing multiple locations would benefit more from an IWMS, while a CAFM is more helpful in managing one location. IWMS platforms allow for control of functions like creating floor plans, managing real estate portfolios, and implementing maintenance programs.
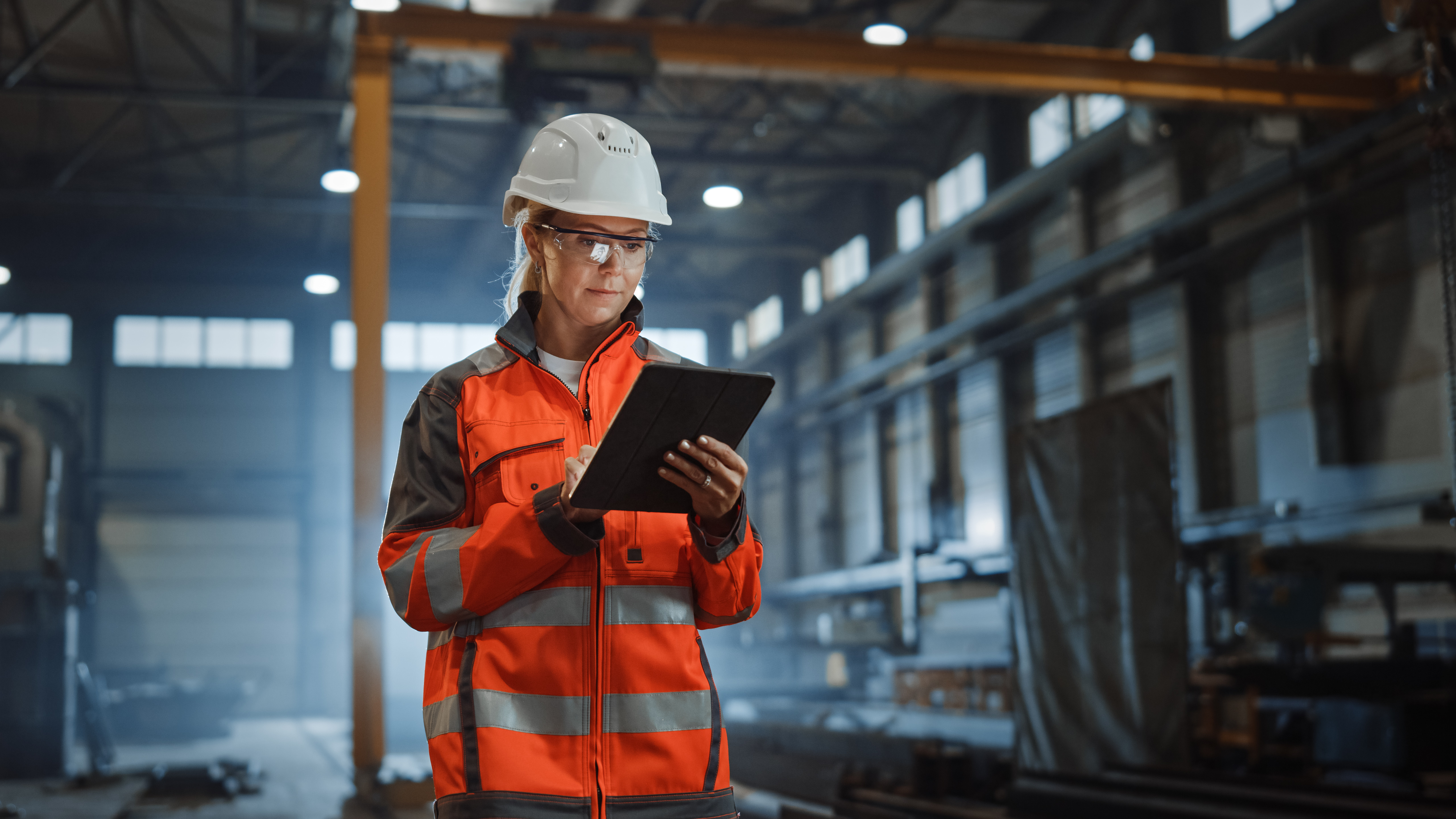
Enterprise Asset Management Systems
Unlike other facility management systems, Enterprise Asset Management (EAM) systems focus entirely on physical assets, not physical spaces or building management.
EAM software can help you manage inventory levels, plan preventive maintenance, and more. They provide access to real-time data and help ensure optimal asset management workflows.
Computerized Maintenance Management Systems
Many Computerized Maintenance Management Systems (CMMS) focus solely on maintenance management. However, some CMMS solutions in today’s market offer greater functionality.
While the app can help organize maintenance tasks, MaintainX is an example of a solution offering long-term asset tracking. With work order management and a user-friendly mobile application, the software allows you to simplify your maintenance operations with real-time data.
For example, you can use cloud-based storage for your digital Standard Operating Procedures (SOPs) and reduce your maintenance costs and downtime with preventive maintenance work orders. You can take your facility operations to the next level with dashboards that help you generate actionable insights for data-driven decision-making.
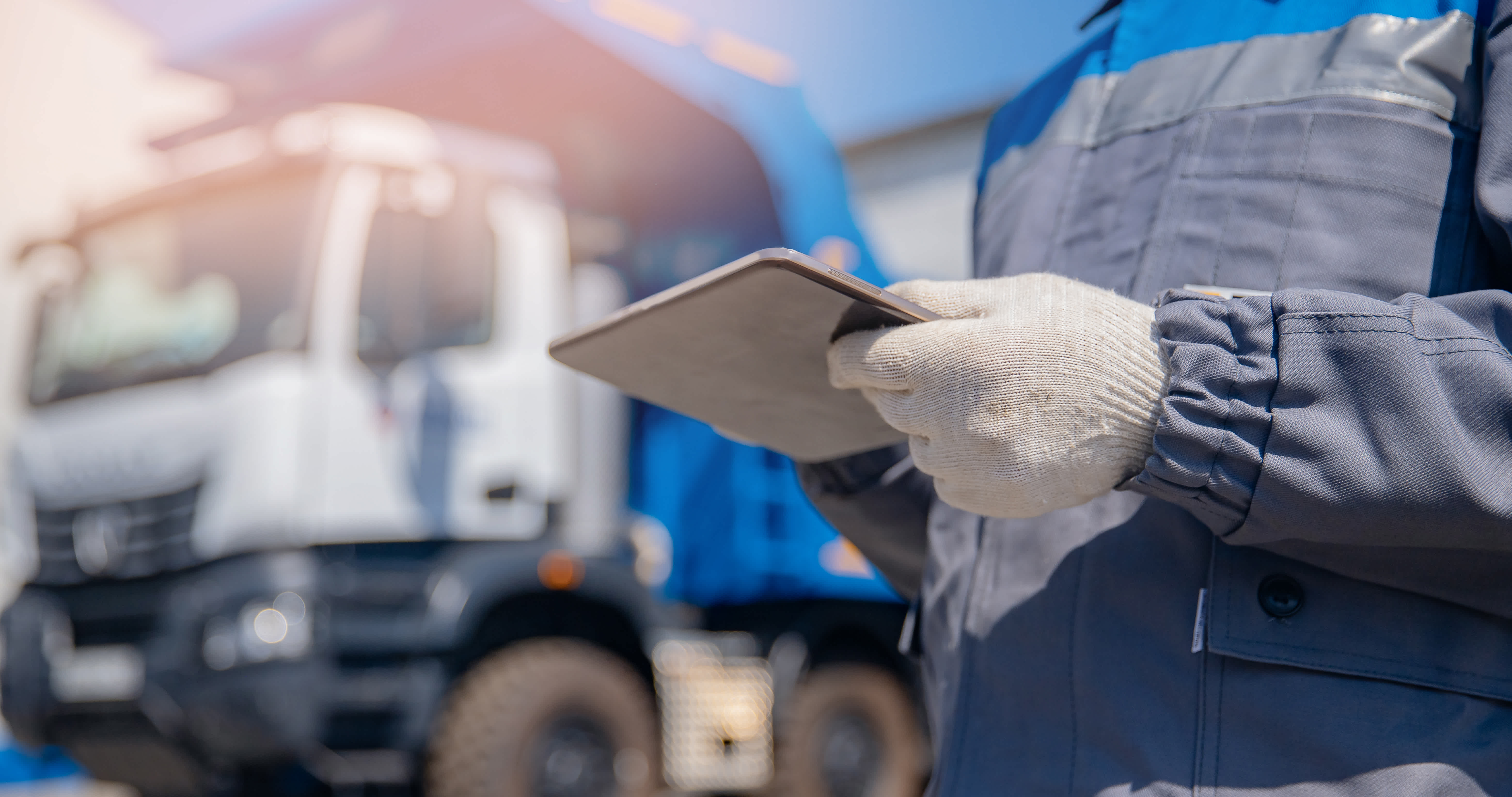
Uses of CAFM
Some of the features, uses, and benefits of CAFM are:
Computer-Aided Design (CAD)
Computer-aided design is one of the main benefits of using a CAFM. With this feature, you can create visual representations of your physical workspace before setting it up ultimately. This process allows you to visualize your layout more effectively and in more detail.
As such, you’ll have greater insight into your planning. While using this feature means spending a bit more time on planning before diving right into space management, it can also save you time later. Using these visualizations to uncover problems before you organize your space helps you avoid the extra time and money you would require if fixing these problems later.
Space Management
As mentioned, Computer-aided design assists in organizing a physical workspace. You’ll be able to determine where to place assets, storage rooms, safety materials, etc. One key benefit of using CAFM to generate and manage visual representations of a workspace is locating items.
Visual representations can help you search through your workspace much quicker than doing it physically. This can also lead to cost savings in terms of time workers can spend on more productive activities.
Apart from space planning, access is a critical aspect of managing your physical space. For example, when handling room reservations. With a CAFM, staff can see real-time information about the status of locations. Your CAFM will offer staff a centralized location for making requests and allow you to approve them in real time.
Real Estate Management
In addition to managing your physical space, a CAFM can help you handle the business side of facility management. For example, a CAFM with the proper functionality can help you with lease management. Other uses include managing tenant service requests and organizing viewings for potential renters.
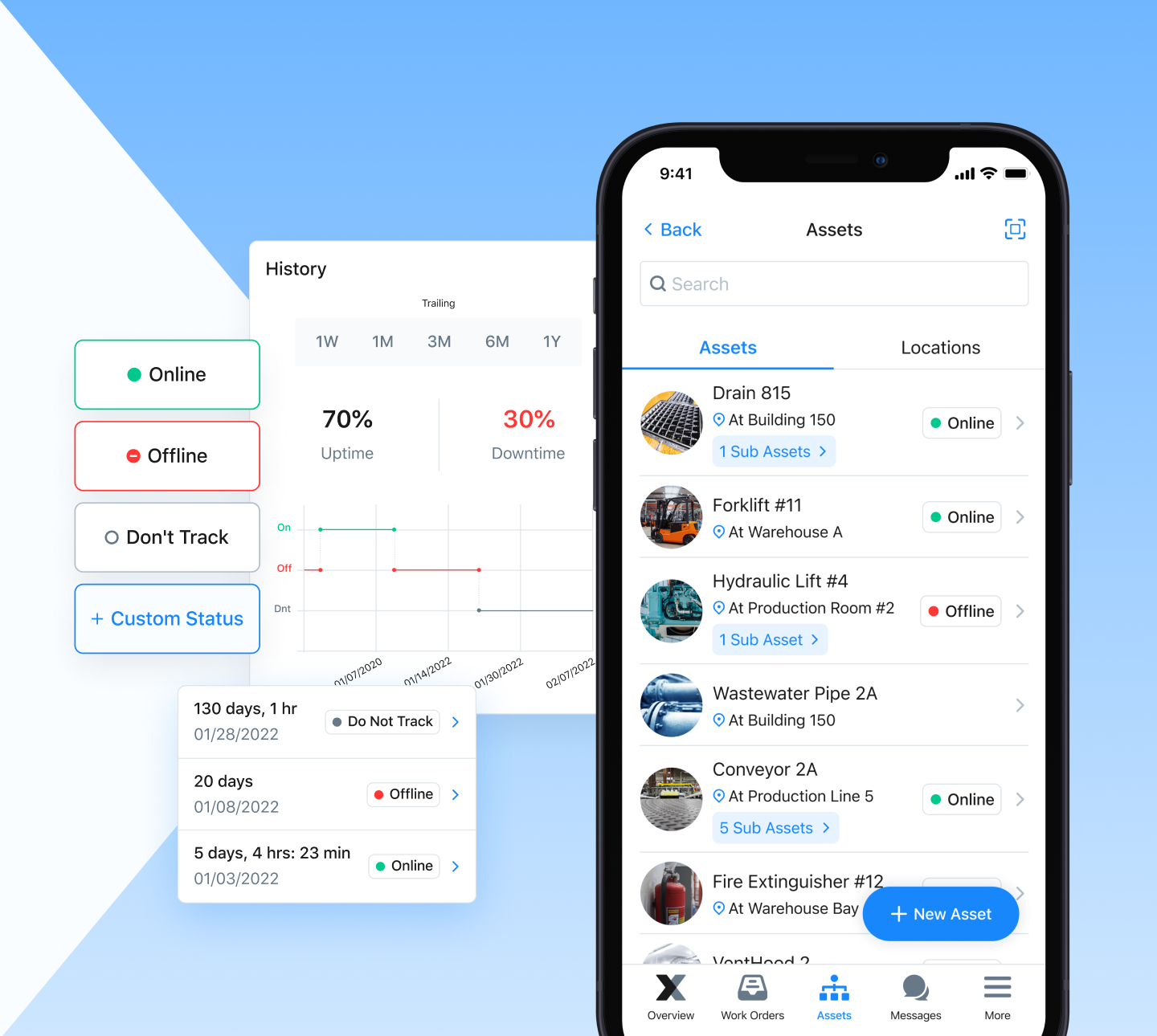
Asset Management
CAFM helps you keep an eye on your assets within your facility. Such assets include everything from machines and equipment to spare parts and other minor forms of inventory.
In addition to letting you know the precise location of assets within a facility, CAFM solutions also help you ensure you use your assets cost-effectively. You can keep track of asset performance over time and analyze the data to generate insights. You can also track metrics like energy usage, downtime, and any other KPIs you need to make decisions about your operations.
Maintenance Management
By monitoring your assets closely, you can create more robust approaches to your maintenance. For example, paying attention to how assets behave between maintenance cycles can inform whether or not you need to adjust those cycles. Also, you can use CAFM to automate maintenance requests, send notifications to shop floor workers, and disseminate work instructions.
Lifecycle Management
When working towards sustainability, you want to ensure you’re using your assets in the most cost-effective way throughout their lifecycle. Helping to facilitate this is one significant benefit of CAFM.
The tracking features in a proper CAFM will help you identify trends and determine where to improve. This approach ensures that you have data to back up any improvement efforts you make, which in turn increases the likelihood of a positive outcome.
Get MaintainX to Take Your Facility Management to the Next Level
If you’re considering leveraging facility management software to optimize your operations, consider MaintainX. Despite being a CMMS, MaintainX is uniquely adaptable to a range of facility management and enterprise asset management functions.
Implementing a robust CMMS solution like MaintainX will allow your facility access to real-time data and automate your maintenance activities. You can monitor your location status, track your assets, digitize information, and maintain audit trails. MaintainX’s reporting module also allows you to analyze your data, generate insightful reports, and monitor equipment status.
Implementing MaintainX CMMS software will enable your facility maintenance teams to:
- Collaborate across departments.
- Communicate via instant messaging.
- Collect real-time operations data to improve work order management.
- Digitize information.
- Monitor KPI and metrics, which you can then analyze to identify trends and drive continuous improvement.
- Decrease reactive equipment maintenance, improve efficiencies, and increase profits.
FAQs
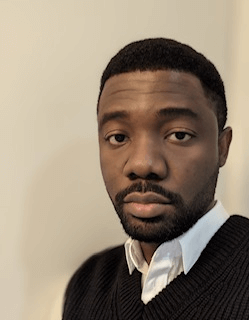
Lekan Olanrewaju is a content writer with years of experience in media and content creation. He has held positions at various media organizations, working with and leading teams at print magazines, digital publications, and television productions.