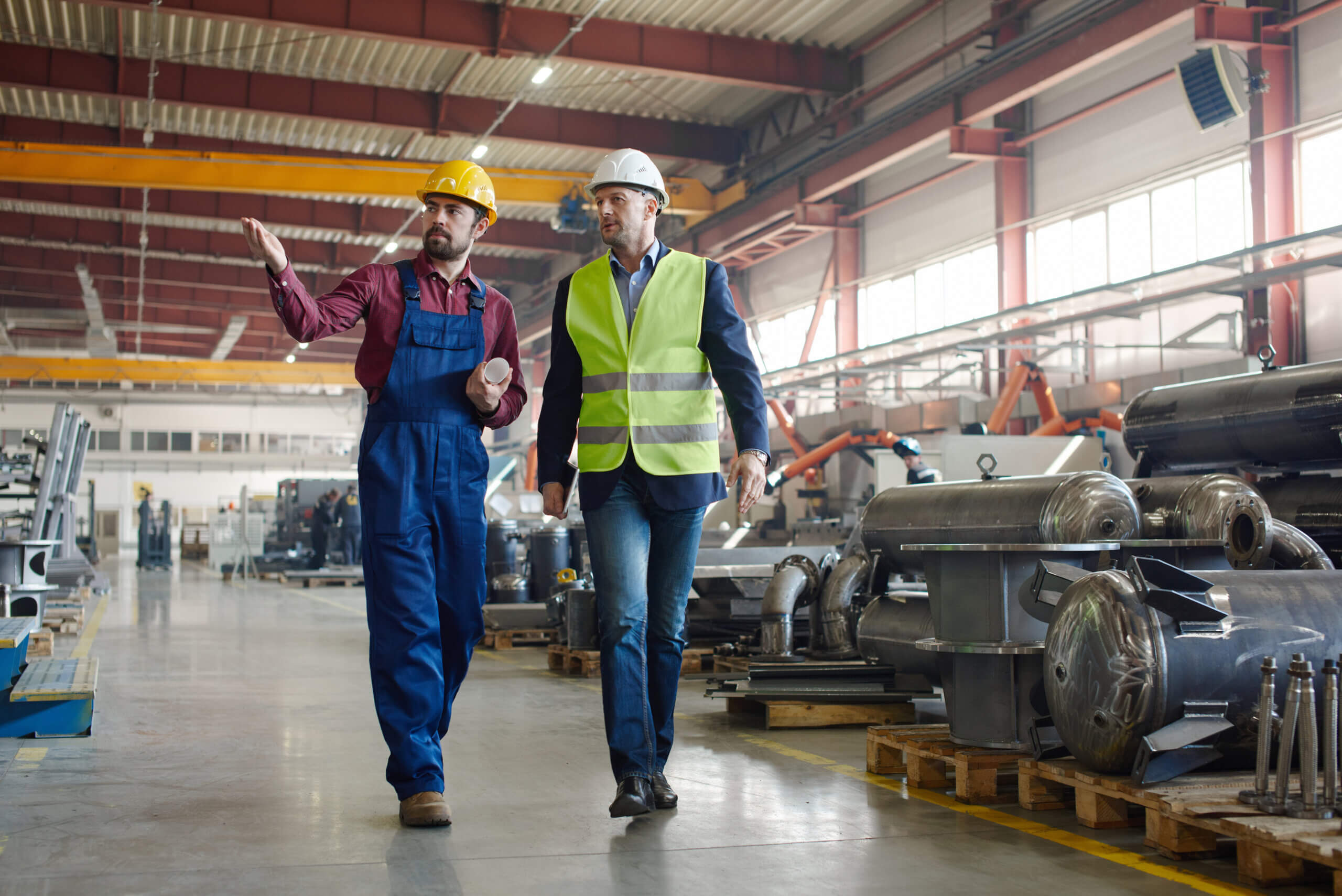
Maintenance management, broadly, is the process of ensuring assets and resources are in optimum working order. In this post, we discuss how to optimize maintenance management to keep assets working effectively, thus maximizing efficiency and lifespan, reducing costs, and increasing profitability.
From scheduling tune-ups to repairing faulty equipment to tracking downtimes, planned maintenance management involves everything from prioritizing maintenance activities to delegating maintenance tasks.
Benefits of Maintenance Management
On some level, it must look like a no-brainer. But, given a choice between keeping your equipment in good working order or not, the answer seems quite clear. And indeed, minimizing asset failure and extracting maximum value from equipment is a boon to any organization.
But beyond this, maintenance management has even more potential benefits that can be useful when deciding on a maintenance management strategy.
Improve Asset Performance
This is perhaps the greatest benefit of a proactive approach to maintenance management. With a structured process in place, particularly with planned and preventive maintenance schedules, you can prevent severe breakdowns by regularly addressing issues before they cripple assets.
You can reduce unplanned downtimes, reduce production losses, extend the useful life of equipment, and save on maintenance costs. Proper asset management also improves production efficiency as a whole. When your processes aren’t impeded by unexpected breakdowns, you can direct time and money toward other tasks.
Improve Output Quality
Top-performing assets yield fewer errors in production output. This has many resulting benefits, from increased customer satisfaction to fewer faulty products needing to be scrapped, leading to more cost-effective operations overall.
Meet Compliance and Safety Regulations
Depending on your industry, you will likely need to follow industry and state/federal regulations. Occupational Safety and Health Administration (OSHA), for example, maintains strict regulations regarding workplace safety and risk management. In addition, a top-notch maintenance schedule will help ensure equipment remains in good condition. Equipment in good condition reduces the risk of malfunction or accidents compromising employee safety and helps your maintenance team keep regulatory compliance.
Budget Efficiently
Efficient maintenance management can offer insights into exactly where your resources are going. Instead of feeling your way through the dark, an optimal maintenance system allows you to identify where your money and employees’ time are going. For example, what assets require the highest costs and labor to maintain?
When breakdowns happen, assets need to get back up and running no matter what, which often means unexpected costs. But, whether it’s money spent on emergency orders of spare parts or needing to hire special maintenance technicians for a particular piece of faulty equipment, proper maintenance planning reduces emergency spending.
With a robust CMMS, detailed reporting and real-time KPIs allow you to work out beforehand what assets require regular maintenance and what the financial costs may be, which you can then account for when making budgetary considerations.
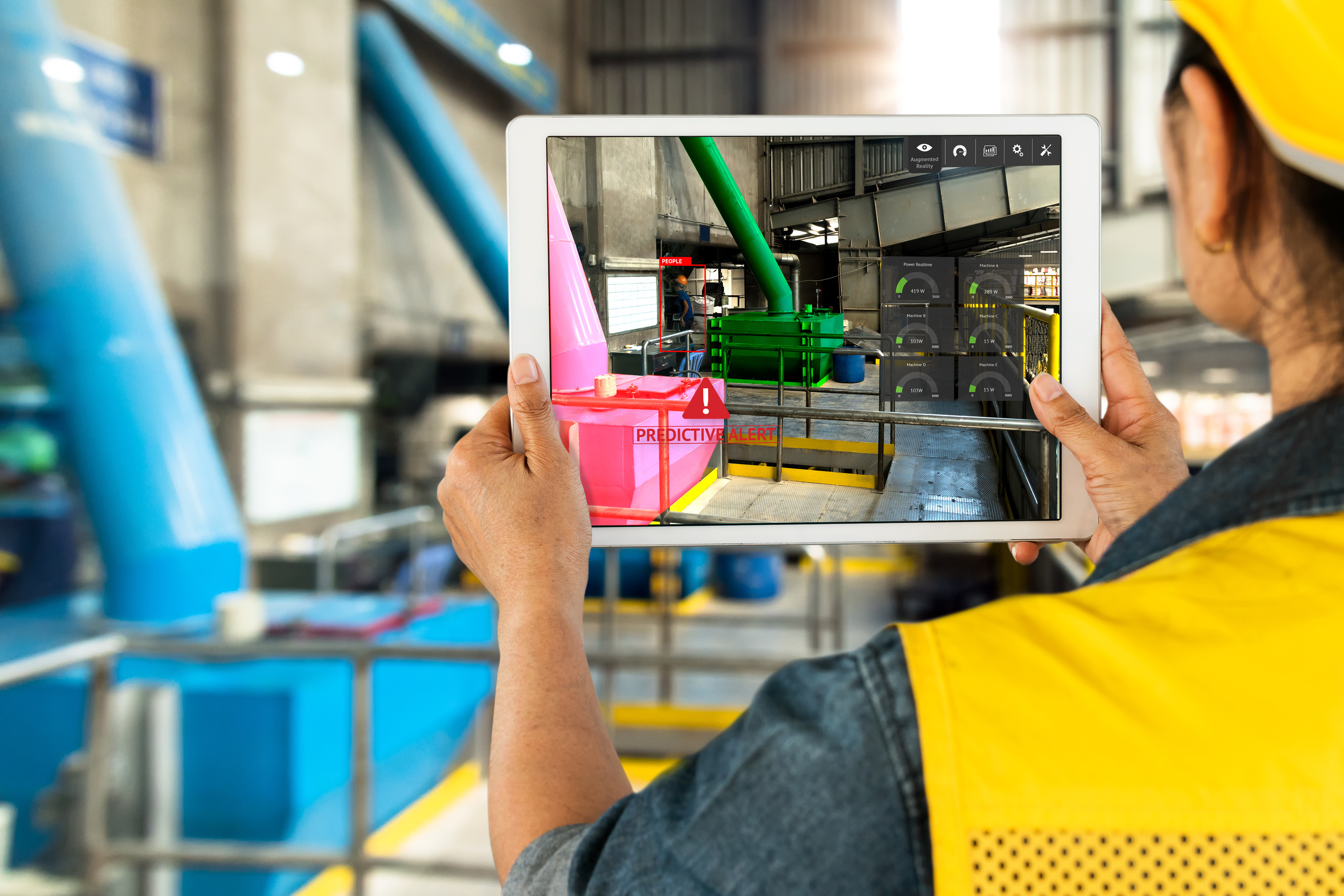
Optimize Your Processes
Over time, as you carry out your maintenance operations, you should begin to notice equipment performance trends. With maintenance management software that allows for recording and tracking data, you’ll be able to create a clear picture of what assets are failing, when, and why. This will enable you to extract useful insights regarding your current processes. You can then make necessary adjustments to optimize performance and reduce downtime.
“Once an organization understands where digital work management can add value, the first task is to ensure processes are set up to capture that value. This process-optimization step is essential to prevent non-value-adding activities becoming embedded into the new system, and to ensure that maintenance planners and supervisors are able to make full use of its capabilities.”
MCKINSEY
Maintenance Management Strategies
A maintenance strategy refers to an organization’s specific approach to its maintenance management processes. It involves the company’s plans and strategy regarding time management and maintenance scheduling, as well as other elements like what kind of maintenance checks and analyses maintenance teams carry out and the requirements of their reporting, among others.
There are various strategies out there, and, as with most elements of maintenance, there’s no one-size-fits-all approach. However, most effective strategies will involve a mix of the following:
Preventive Maintenance Management
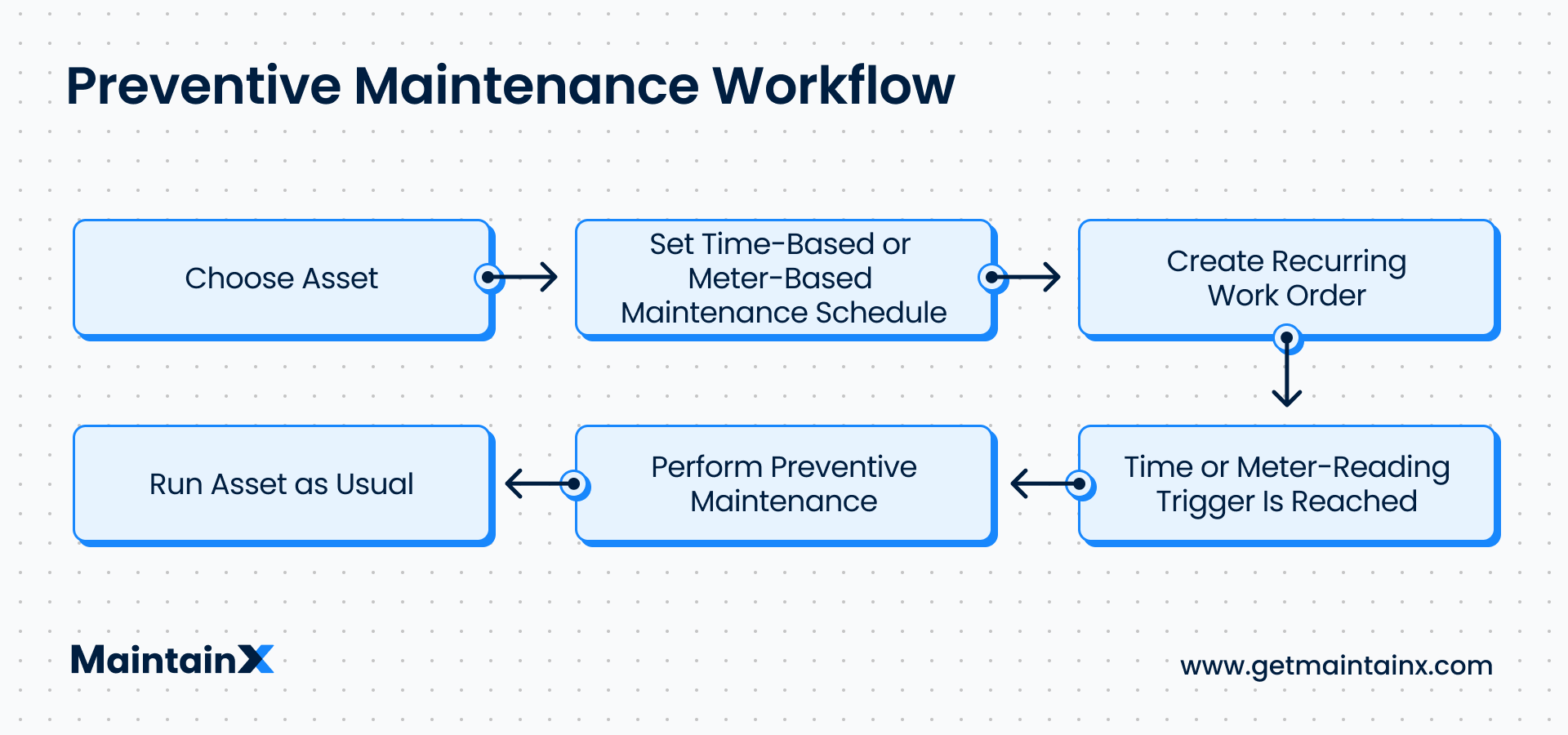
Preventive maintenance involves scheduled asset maintenance to identify and solve problems before they lead to serious breakdowns. This can be performed based on the period of time when maintenance activities are carried out according to certain calendar intervals.
It can also be carried out based on equipment usage or meter usage. For example, you can create SOPs to check equipment parts for every fixed amount of hours they have run. Apart from helping with proper planning and executing production activities, you can reduce unplanned costs with this approach.
Predictive Maintenance Management
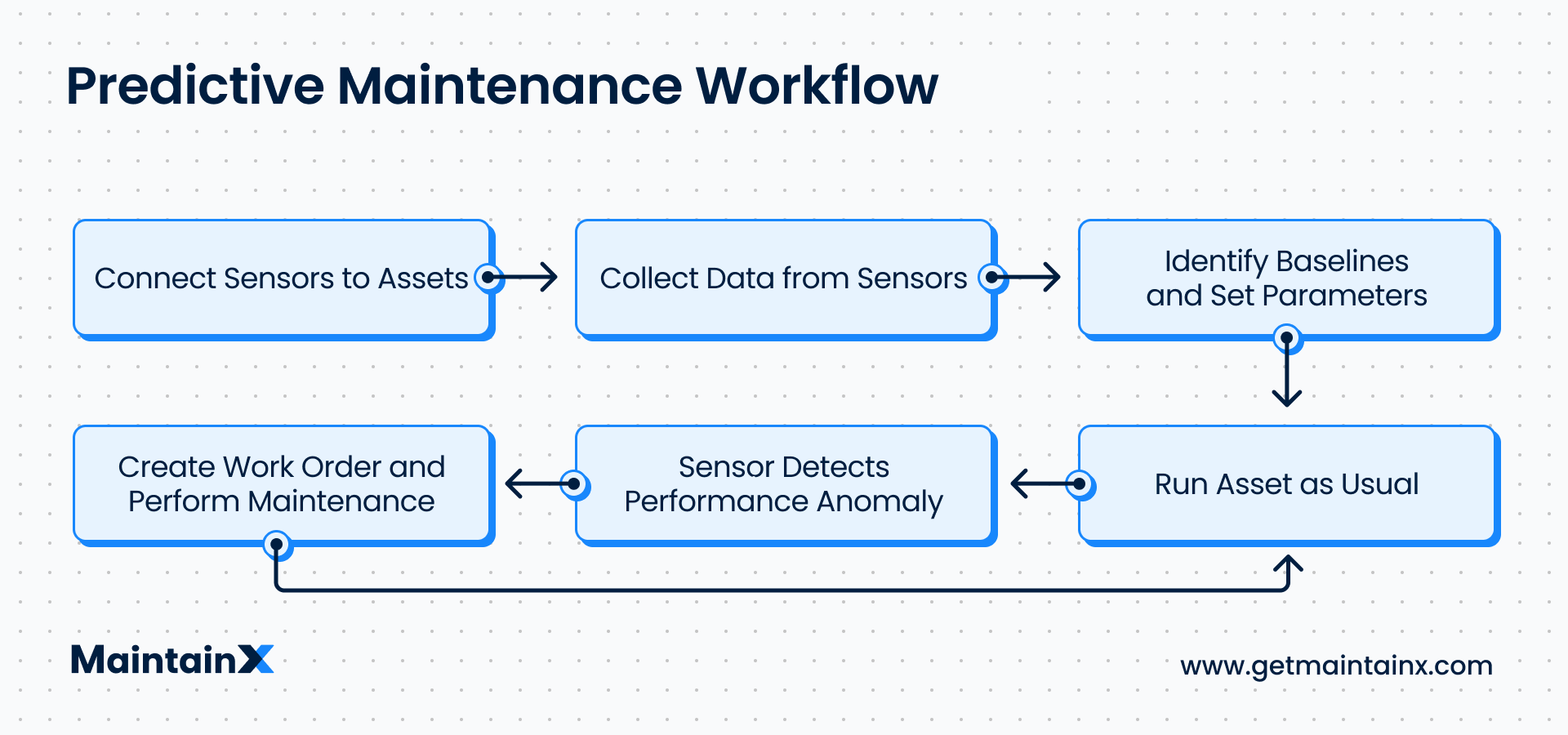
This form of preventive maintenance aims to reduce unnecessary scheduled maintenance processes. Predictive maintenance tracks equipment conditions and isolates specific problems beforehand.
With regular preventive maintenance, you might run scheduled checks on an asset every month, going six months without having to fix anything. While this is a good plan, it can quickly start to feel like wasted effort. Predictive maintenance, on the other hand, aims to redirect that effort on the part of maintenance workers by analyzing the conditions of the equipment.
With predictive maintenance, you only run checks when failures are imminent. This could be via vibration analysis, thermal sensor analysis which monitors equipment temperature, oil analysis to assess the oil particle size, and other metrics. This strategy is most beneficial for assets with intermittent or erratic failure periods.
Reliability-Centered Maintenance Management
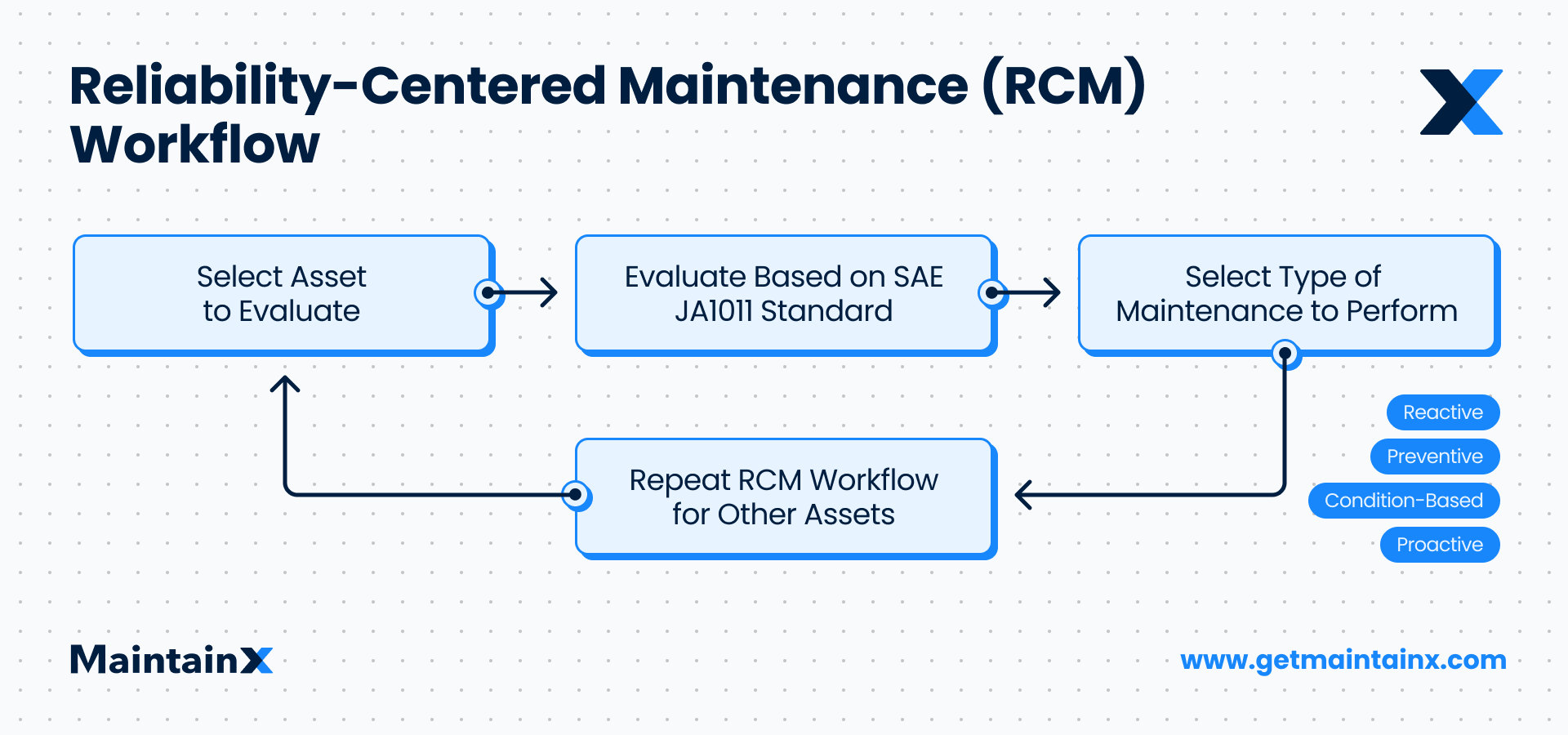
Reliability-centered maintenance is a more equipment-based approach in which maintenance activities are carried out on a case-by-case basis. Assets are evaluated individually to determine what maintenance activities they require, when, and how frequently. This maintenance plan often follows equipment manufacturer guidelines.
Condition-Based Maintenance Management
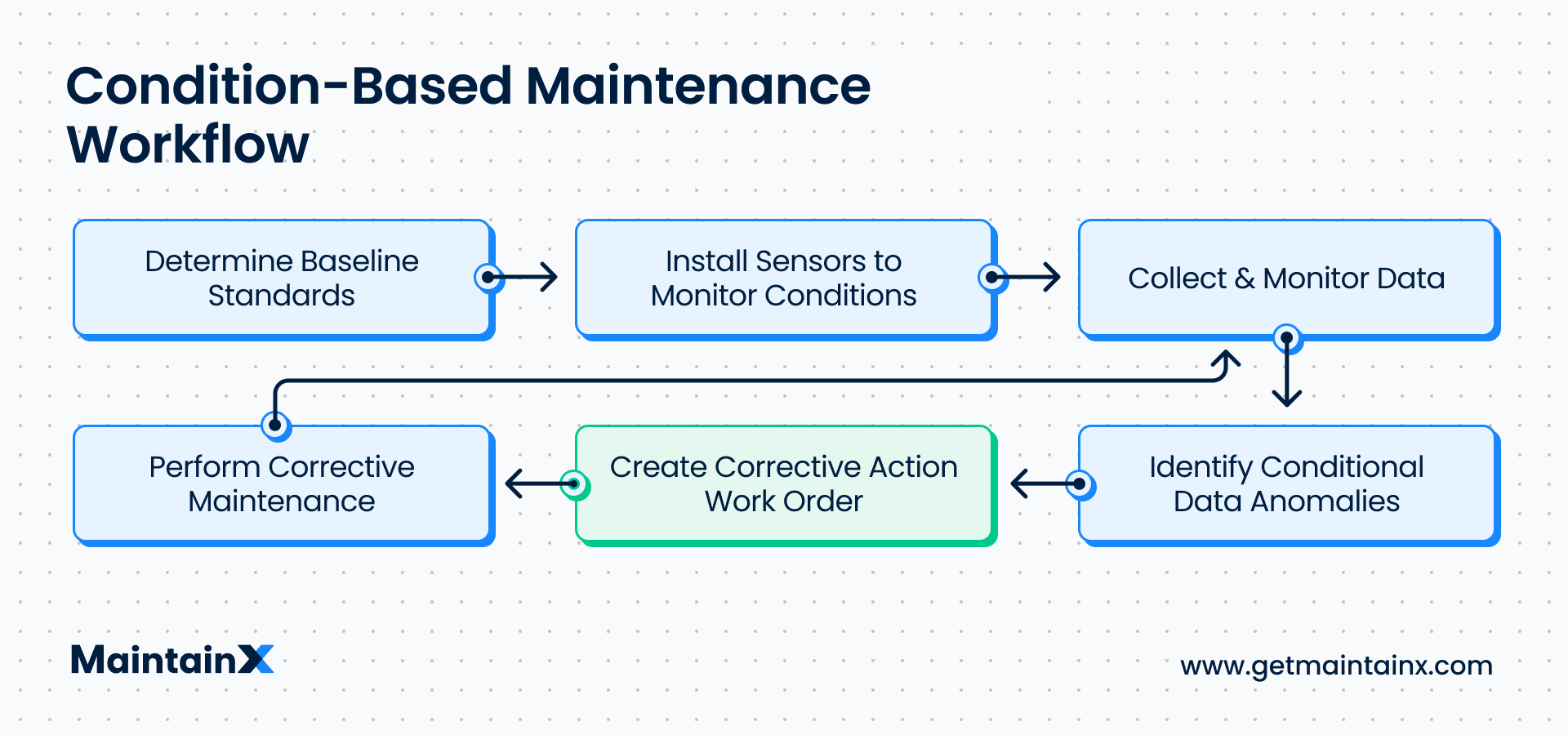
Condition-based maintenance sits somewhere between reactive and preventive maintenance. Instead of a maintenance program involving regular checks and servicing, this approach relies on implementing maintenance actions based on equipment performance. For example, applying lubrication to a conveyor belt when it displays increased friction.
Reactive Maintenance Management
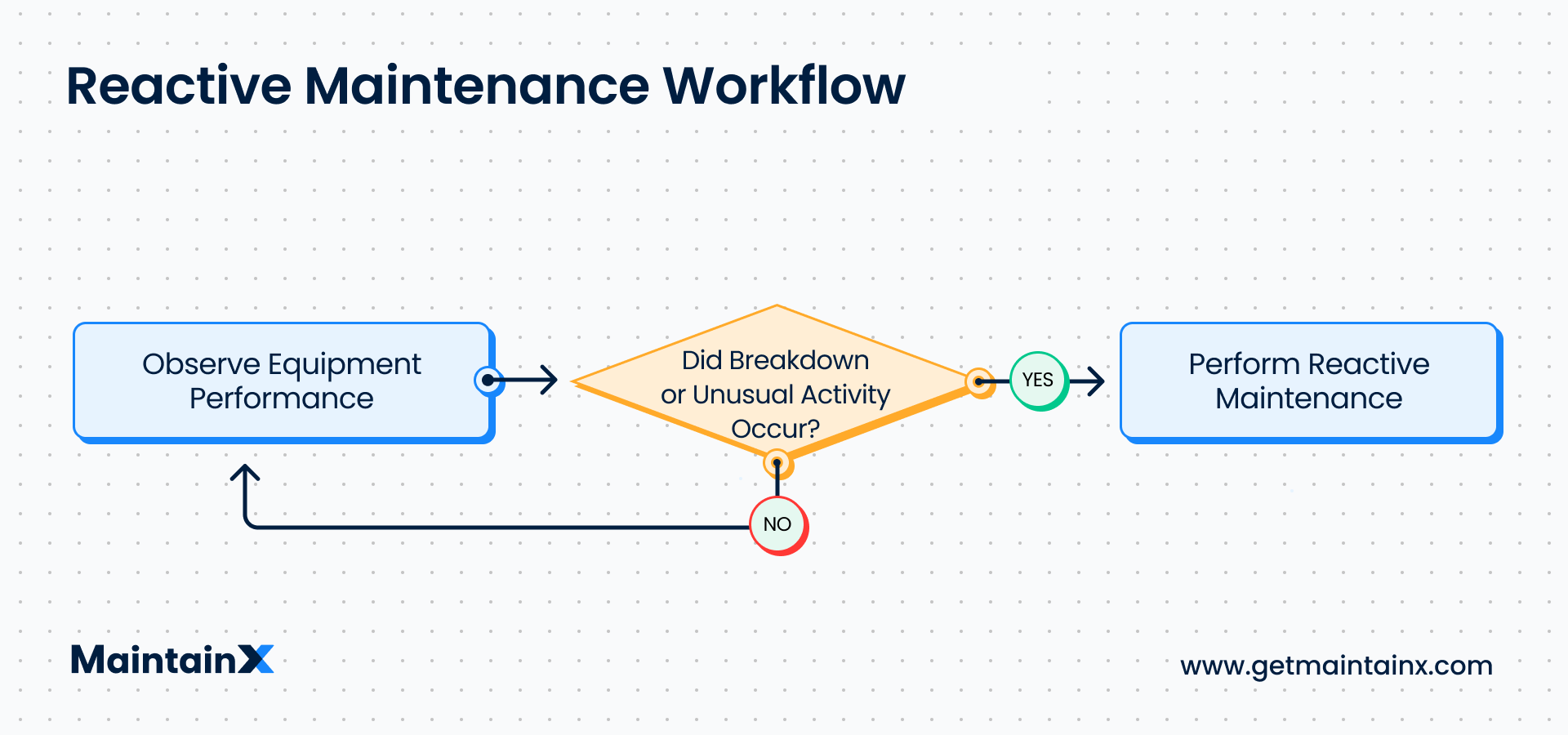
Reactive or corrective maintenance involves, as the name implies, maintenance activities undertaken after an asset or piece of equipment has failed in some capacity. This is often unplanned but also can be planned, as in cases in which the assets are deliberately run to failure.
Unplanned failures often result in unplanned costs in terms of spending on repairs and potential revenue lost to downtime.
That said, reactive maintenance can sometimes be cheaper in the short term. For example, fixing or replacing a faulty part in a large machine may result in more cost savings in terms of time and resources than regularly planned maintenance work. In addition, knowing what to do in an emergency helps prevent confusion when it happens.
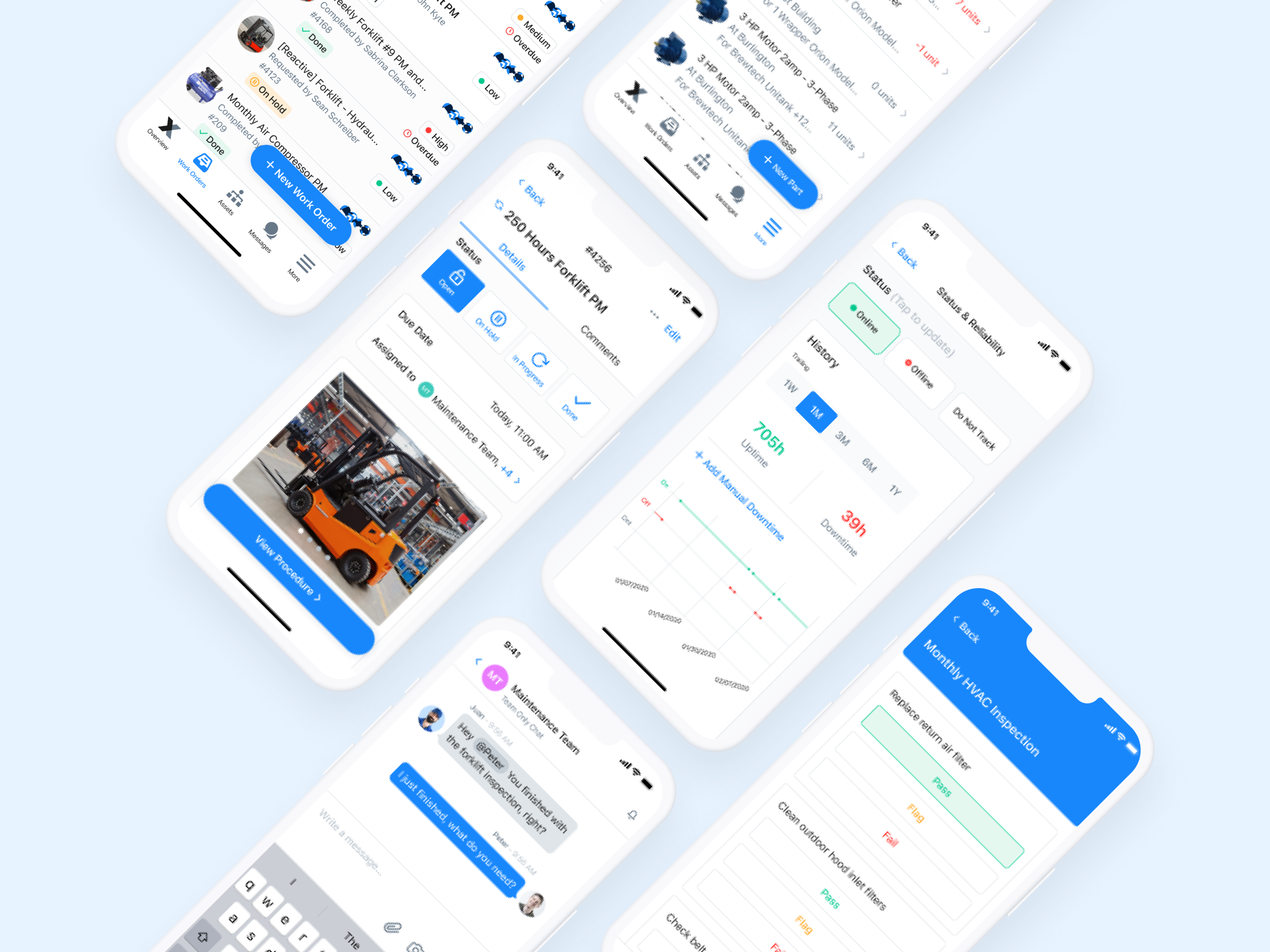
Managing Maintenance with a CMMS
Working out your approach to maintenance management will depend on the particular circumstances of your team and organization. However, whichever type of maintenance management you choose, you likely manage multiple assets at once. Keeping track of various pieces of equipment and the specific reviews and services they require can be an arduous process, even for the most efficient teams.
A Computerized Maintenance Management System (CMMS) can go a long way to streamlining this process and your overall workflows. For example, a user-friendly CMMS system like MaintainX has real-time functionality that allows for optimized work order management and standardized operating procedures (SOPs).
With functionalities like instant communication and workflow optimization, the software allows you to create work orders on the go, delegate tasks, oversee inventory management, receive real-time notifications and updates, and record information for long-term tracking and analysis.
Ready to optimize your maintenance management?
FAQs
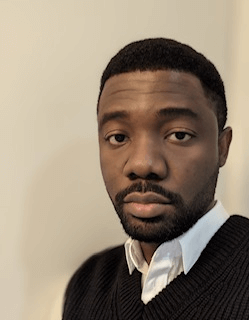
Lekan Olanrewaju is a content writer with years of experience in media and content creation. He has held positions at various media organizations, working with and leading teams at print magazines, digital publications, and television productions.