Run-to-failure (RTF) maintenance is a maintenance strategy in which assets are used until they break down or require repair or replacement. Though RTF maintenance is reactive, operational managers sometimes deliberately choose this maintenance plan. When used correctly, the strategy can help reduce costs, streamline maintenance work, and serve as a valuable addition to an organization’s maintenance toolkit.
What Is Run-to-Failure Maintenance?
Run-to-failure maintenance is the best choice for non-critical equipment that is cheap, disposable, or unserviceable. Assets or parts that can easily be replaced upon breakdown are ideal candidates for RTF. This can be both easier and cheaper than servicing it at regular intervals.
There is a popular misconception that run-to-failure maintenance is unplanned. On the contrary, RTF requires careful planning to guarantee sufficient resources—manpower and inventory—are available post-failure.
When using an RTF program, a maintenance team’s standard operating procedures (SOPs) must be accessible, current, and easy to access. The key to consciously running “run to failure” is investing in the training of maintenance staff to quickly and efficiently eliminate failures.
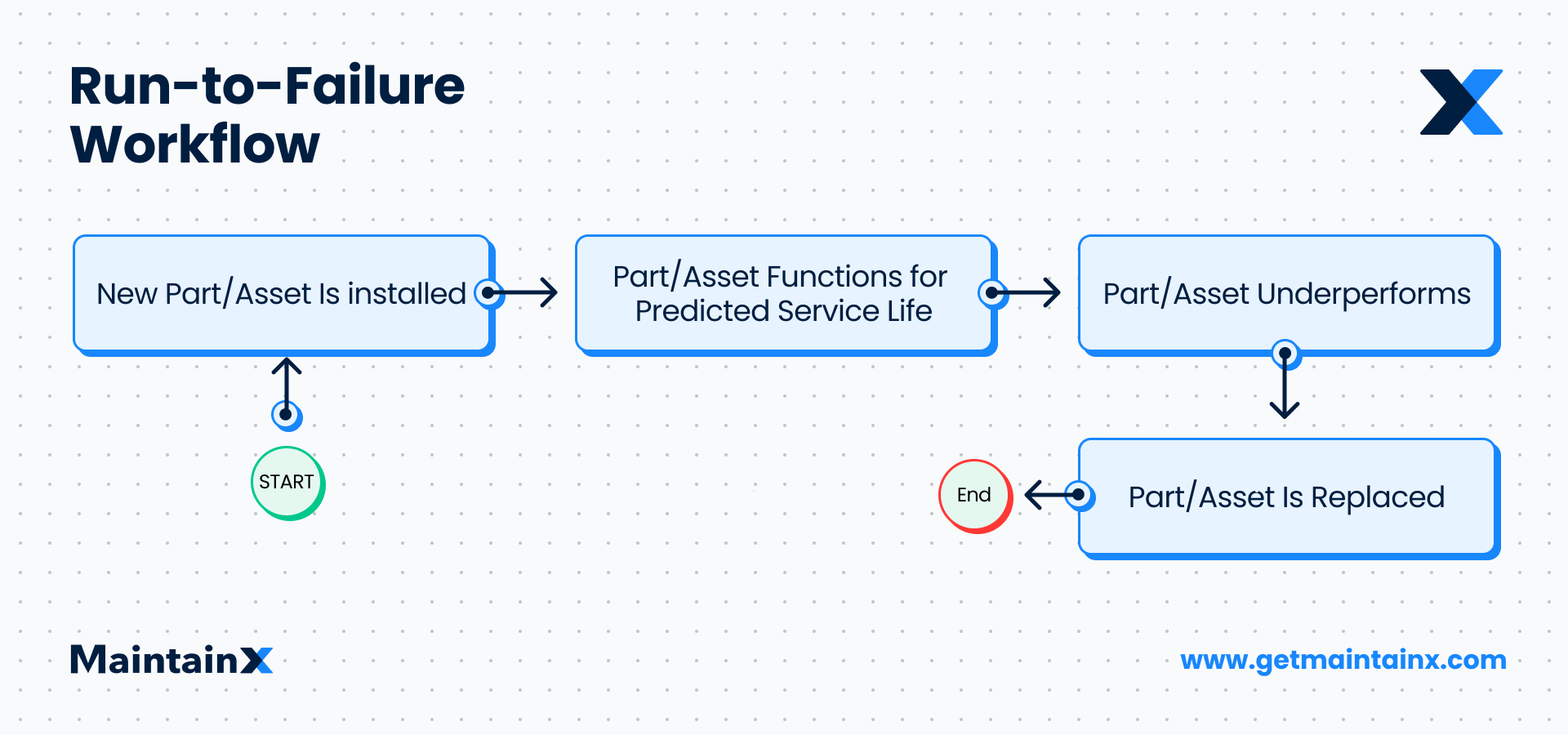
What Are the Benefits of Run-to-Failure Maintenance?
A run-to-failure maintenance program provides the following benefits:
- Low Maintenance Costs: Interrupting production for maintenance tasks can be expensive. Using assets until they break down completely can reduce planned downtime. However, this only makes sense for assets that are quick and easy to replace without bringing operations to a complete halt.
- Time Savings: Maintenance teams only act when replacements or repairs are absolutely necessary. This allows technicians to concentrate on critical tasks, which streamlines operations.
- Ease of Implementation. Due to the program’s overall simplicity, it’s easy to implement with minimal resources. An RTF maintenance program doesn’t require a complex schedule; maintenance technicians fix issues as they arise. In many instances, this is why companies begin with RTF maintenance, before moving toward proactive strategies.
Why and When Does a Run-to-Failure Maintenance Program Make Sense?
Run-to-failure maintenance is ideal if the cost of replacing a piece of equipment is lower than performing preventive maintenance. For example, a general-purpose light bulb doesn’t need to be serviced before it stops working. Once it fails, the bulb can be easily replaced. The same goes for filters, water pumps, carpet flooring, cables, signages, and more.
If the inevitable failure minimally impacts overall performance and productivity, a run-to-failure approach is preferable. Put simply, it’s best used in cases where maintenance managers clearly understand all of the risks associated with failure and feel confident in their team’s ability to quickly address issues.
Run-to-Failure maintenance Scenarios
- Assets with a Short Life Span: Equipment with short life spans can simply be replaced at the end of its life cycle. Examples of such assets include batteries, water heaters, high-traffic doors, and digital controls.
- Disposable Assets: Disposable assets are usually cheap and easy to replace. Often, they cannot be serviced at all. Such parts include printer cartridges, signage, and filters.
- Assets with a Low Risk of Failure: Equipment that is durable and isn’t prone to wear and tear doesn’t typically require periodic servicing. Some assets don’t need any maintenance. For example, a building’s foundations or its internal steel structure doesn’t necessitate preventive maintenance.
- Non-Critical Equipment: Equipment that isn’t vital to production can be replaced or repaired without impacting a facility’s output.
- Difficult to Service Equipment: Some assets have random failure patterns, making regular maintenance difficult or unproductive. Alternatively, other assets may be unmaintainable because they’re impossible to reach.
Additionally, there are less obvious instances where run-to-failure maintenance programs should never be used:
- When a failure could lead to major financial losses,
- When a failure could pose a safety risk to personnel or customers, and/or
- When RTF maintenance costs would be higher than PM costs.
In some instances, run-to-failure maintenance may be more expensive in the long term. A good, cost-efficient maintenance strategy requires finding the right balance between preventive and reactive maintenance.
What Is Needed to Implement a Successful Run-to-Failure Maintenance Program?
A successful RTF program requires careful planning, good judgment, and teamwork. While implementation costs are low, the following resources may be necessary:
- Sufficient Inventory: Obviously, it’s too late to order spare parts or tools once a failure has occurred. For this reason, maintaining sufficient inventory supplies is paramount. An inventory management system can help ensure you have the necessary spare parts on hand when breakdowns happen.
- Available Staff: A well-planned schedule guarantees technicians are available when failures occur. Alternatively, operations managers may sometimes opt for having technicians on call if resources are limited.
Get MaintainX to Guide Your RTF Maintenance
Run-to-failure maintenance is a viable maintenance strategy for specific facility assets. When practiced in combination with a solid preventive maintenance program, RTF can lower costs, extend the lifespan of non-critical equipment, and increase operational efficiency.
A CMMS allows maintenance teams to create work order templates in advance and assign tasks when maintenance needs arise. The software helps busy managers track, plan, and operationalize maintenance activities and analyze failure data.
See MaintainX in action