Periodic maintenance is a proactive approach to equipment care that provides numerous benefits, including increased safety, reliability, and maintenance cost savings. It's an essential practice for any organization that relies on machinery or equipment for its operations.
What is Periodic Maintenance?
Periodic maintenance, also known as scheduled maintenance, refers to a planned and recurring set of tasks performed on equipment, machinery, or systems at predetermined intervals to ensure their continued operational efficiency, reliability, and safety.
All equipment is prone to wear and tear—even more so when used often. Periodic maintenance involves checking an asset’s condition at pre-defined regular intervals so that maintenance technicians can detect small anomalies before they become big problems.
Periodic Maintenance
Periodic maintenance, or time-based maintenance (TBM), is maintenance performed on equipment at set intervals. Maintenance managers define the optimal intervals for maintenance tasks and schedule them.
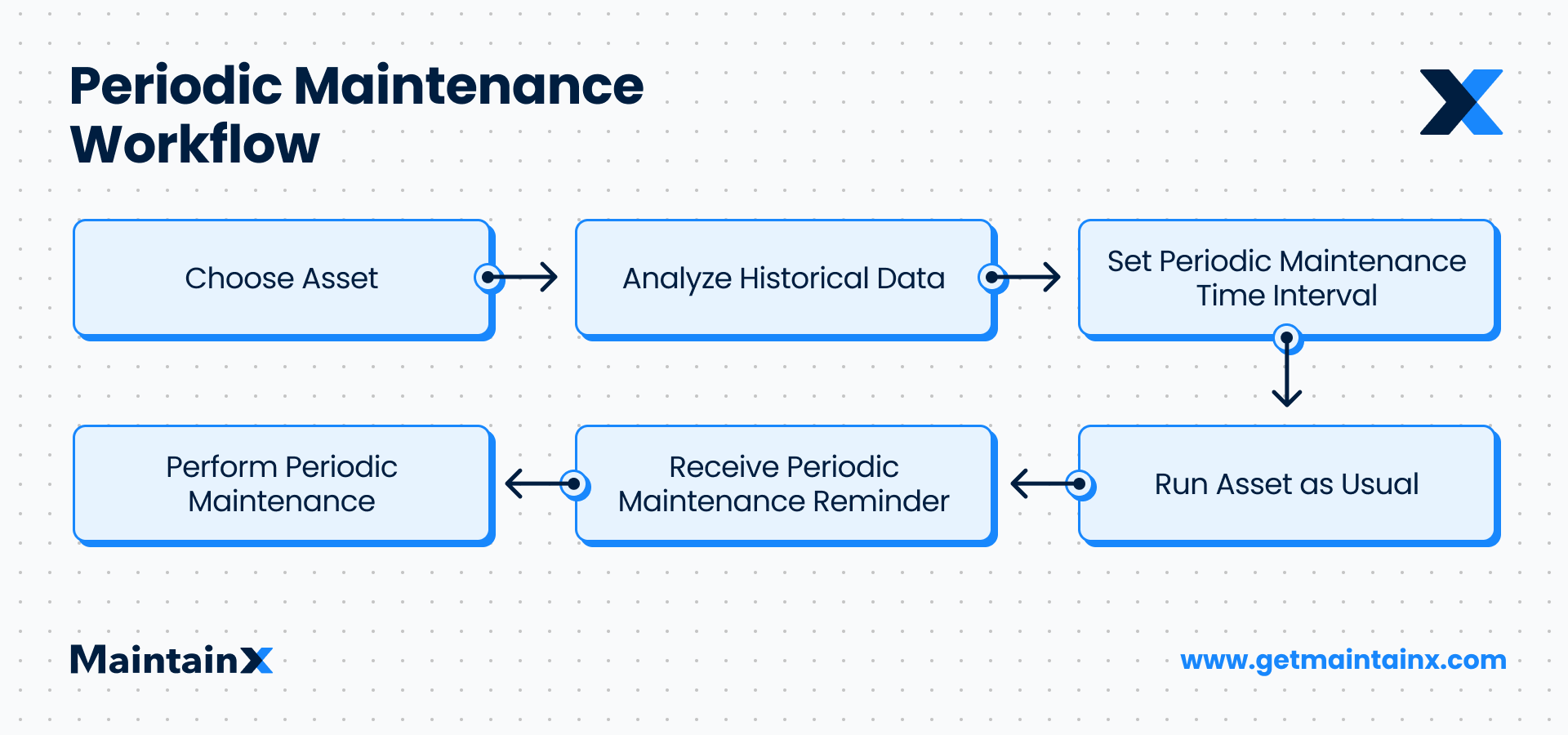
The main goals of periodic maintenance are:
- Extended equipment lifespan,
- Enhanced reliability, and
- Reduced unplanned downtime.
This is the most commonly practiced type of preventive maintenance.
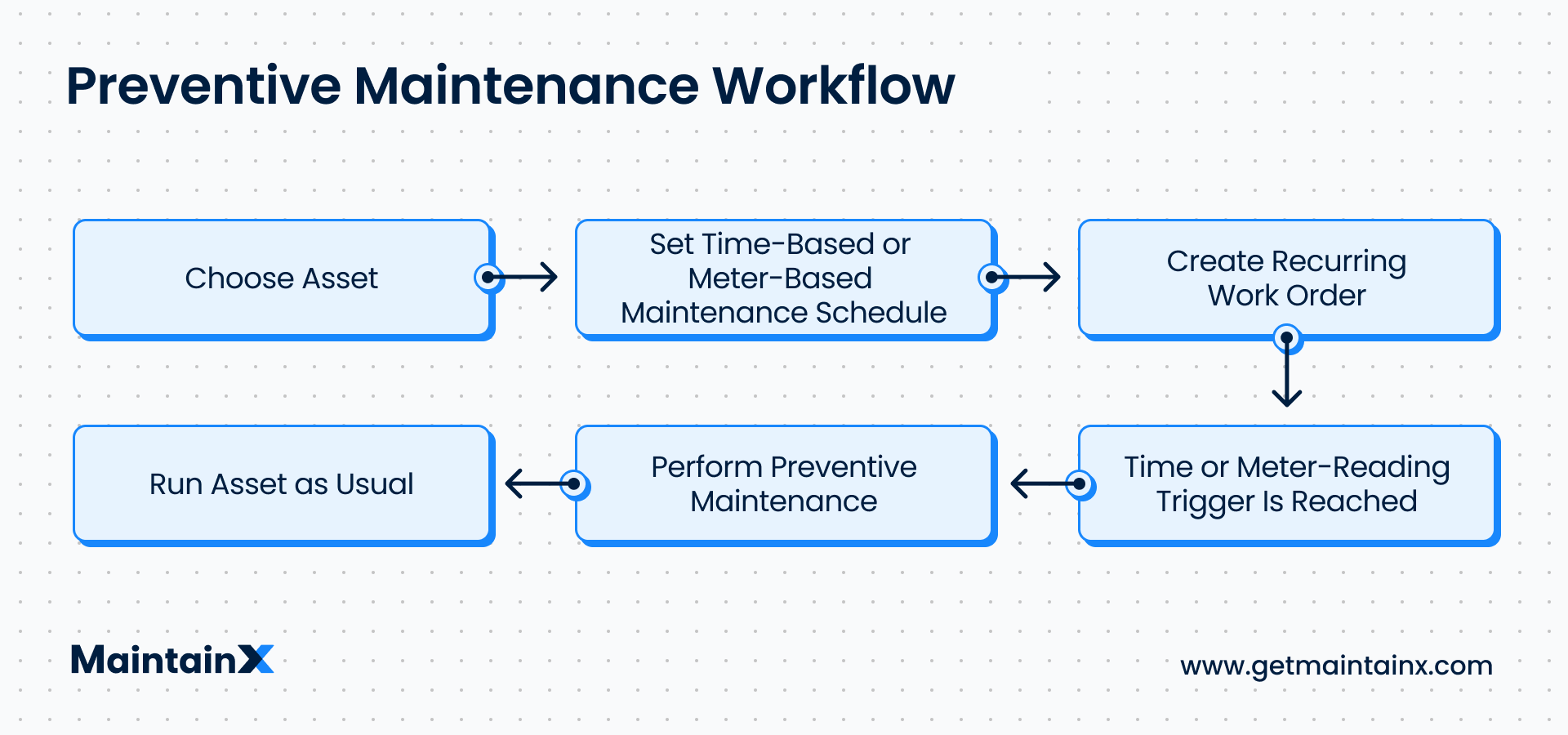
Periodic Maintenance Tasks
Maintenance tasks follow a schedule set intervals throughout the year. CMMS maintenance software is particularly useful for planning and scheduling periodic maintenance work orders. CMMS allows for accurate tracking and analysis of maintenance data, such as failure rates, uptime, downtime, and past work performed on any asset.
Software users can define intervals for time-based maintenance (TBM), schedule recurring work orders, and keep tabs on the ever-evolving state of facility equipment. Alternatively, companies can use Excel spreadsheets, Word templates, and other paper-based systems to schedule periodic maintenance.
How to Implement a Periodic Maintenance Program
A workflow to implement TBM programs includes:
1. Choosing an asset for performing periodic maintenance. Begin with your most valuable piece of equipment in terms of meeting production goals. You can incorporate more assets into your periodic maintenance program as time goes on.
2. Analyzing manufacturer’s guidelines and available real-time data and metrics. Look up the manufacturer’s Mean Time Before Failure (MTBF) and servicing guidelines for your piece of equipment. Also, analyze any available internal historical data for the asset.
3. Defining your ideal interval for performing periodic maintenance. You may schedule periodic maintenance yearly, quarterly, monthly, or weekly.
4. Scheduling recurring maintenance tasks. As previously mentioned, CMMS is ideal for scheduling multiple tasks at regular intervals, monitoring work order progress, and storing equipment servicing data. You may also use a combination of spreadsheets, digital calendars, and paper work orders to get the job done.
5. Performing as scheduled. The assigned technician should determine if the asset is performing as expected while performing recommended upkeep procedures.
Defining Ideal Intervals for Periodic Maintenance
Scheduled maintenance intervals will vary depending on an asset’s model, type, age, and maintenance history. A machine’s manufacturer’s guidelines are your best starting point for creating a TBM program.
Most manufacturers provide information on Mean Time Between Failure (MTBF)—estimated performance timelines before needing servicing/replacement. However, these recommendations are never 100 percent reliable. Newer equipment models may not have been tested in enough scenarios to determine consistent behavior. The unique environment of your facility may also affect equipment needs.
Thus, your most trustworthy periodic maintenance intervals will always come from internally gathered historical data. Many maintenance departments use a CMMS to track asset MTBFs for this reason. Monitoring individual KPIs is the key to continually finetuning your time-based maintenance program for increased efficiency.
Examples of Periodic Maintenance
This type of maintenance addresses the smaller, less costly issues before they impact performance or safety. Common examples are:
- Replacing Filters: HVAC unit filters must be replaced regularly to remain functional and maintain ideal equipment lifespans.
- Changing Lubricating Oils: Proper lubrication is essential for equipment with rotating parts. Inspecting and changing lubricating oils at regular intervals guarantees optimal performance.
- Maintaining Vehicles: Vehicles must undergo periodic car maintenance for optimal performance and safety. Cars are designed to run smoothly for significant periods of time. However, specific components prone to wear and tear must be serviced at regular intervals to guarantee safety, maintain value, and extend longevity; these aspects include brakes, lights, tires, windshield washer fluid, and more.
- Maintaining Residential Property: Property managers annually check electrical, heating, and plumbing systems; rooftops; grounds; HVAC units; and more for issues.
The Pros and Cons of Periodic Maintenance
Let’s now look at the advantages, along with the downsides:
Pros
- Increased Asset Lifespan: Periodic maintenance allows technicians to detect and address issues before they become major problems or lead to asset failure. This, in turn, helps increase equipment lifespans.
- Enhanced Performance: Time-based maintenance helps make the most out of equipment, ensuring it’s always performing at optimum levels. Adequate lubrication, for example, can significantly impact both the output and energy use of an asset.
- Easy Implementation: Setting up the program is simple. Organizations need nothing more than their manufacturers’ guidelines and historical maintenance data. Additionally, periodic maintenance is highly predictable and easy to plan.
- Reduced Downtime: When scheduled and performed correctly, time-based maintenance can reduce unplanned downtime to a minimum. Regular inspections yield accurate overviews of asset reliability.
Cons
- Excessive maintenance of some assets: It may sometimes be overdone, leading to wasted resources. Not all assets need servicing as often as planned; adjust your maintenance schedule as you gather more information about your organization’s equipment needs.
- Unplanned events: Unplanned breakdowns always happen. Your company should still allocate resources for unexpected equipment failures.
What Is a Periodic Maintenance Schedule?
Periodic maintenance programs require scheduling recommended maintenance tasks based on manufacturers’ guidelines and historical equipment data. Operational managers assign recurring work orders using calendars, templates, or CMMS platforms.
A good periodic maintenance schedule provides instant visibility of the entire maintenance team's workload. It allows managers to get ahead of equipment failures, ensures they have necessary parts on hand, and strategically utilizes existing company resources.
Here’s an example of the CMMS calendar our clients are using to track time-based periodic maintenance:
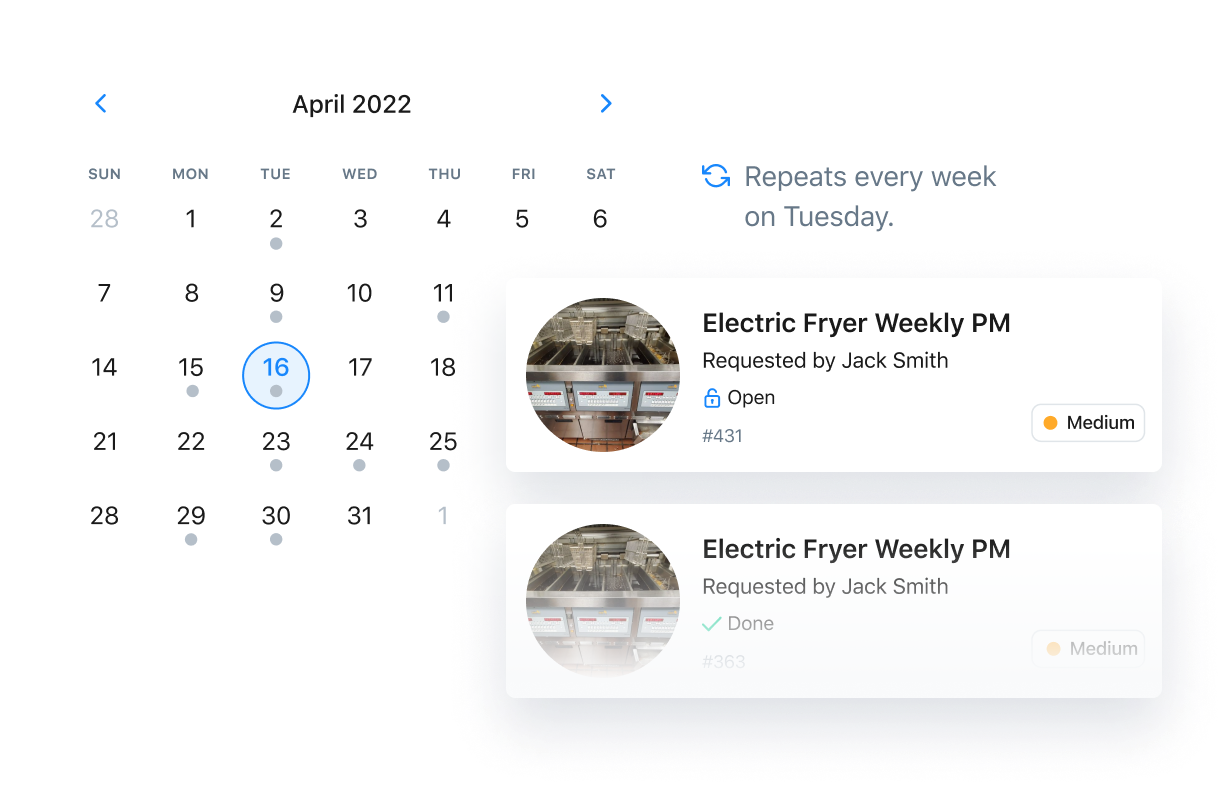
Periodic maintenance increases equipment lifespan and reliability and is very easy to plan and implement. It does come with its limitations, though. For example, it may lead to unnecessary costs associated with over-maintaining assets. For this reason, many facilities use both time-based and condition-based maintenance programs.
Periodic Maintenance FAQs
How Often Should Periodic Maintenance Be Performed?
The frequency of periodic regular maintenance depends on factors like the type of equipment, its usage, manufacturer recommendations, and industry standards. It can range between various time intervals from daily, weekly, monthly, to annually.
Can I Perform Periodic Maintenance In-House or Should I Hire a Professional Maintenance Service?
Depending on the complexity of the maintenance strategy and the asset management expertise of your team, you may choose to perform periodic maintenance in-house. However, for specialized equipment life cycles or tasks, it may be advisable to hire qualified professionals to keep equipment in good condition.
How Can I Track and Manage Periodic Maintenance Tasks Effectively?
Utilize a Computerized Maintenance Management System (CMMS) or maintenance checklist to schedule, track, and manage periodic maintenance processes. These systems provide tools for planning, recording, and analyzing maintenance activities to avoid costly repairs.
See MaintainX in action