Routine maintenance (RM) refers to maintenance work performed on a regular or ongoing basis to find and address problems before they lead to equipment failure. Routine maintenance tasks can be performed daily, weekly, monthly, or annually and typically consist of small, simple tasks that don’t require specialized skills. For example, checking and topping up the oil in a machine every week is routine maintenance. This quick task helps keep the equipment running smoothly and prevents failure or breakdowns due to poor lubrication.
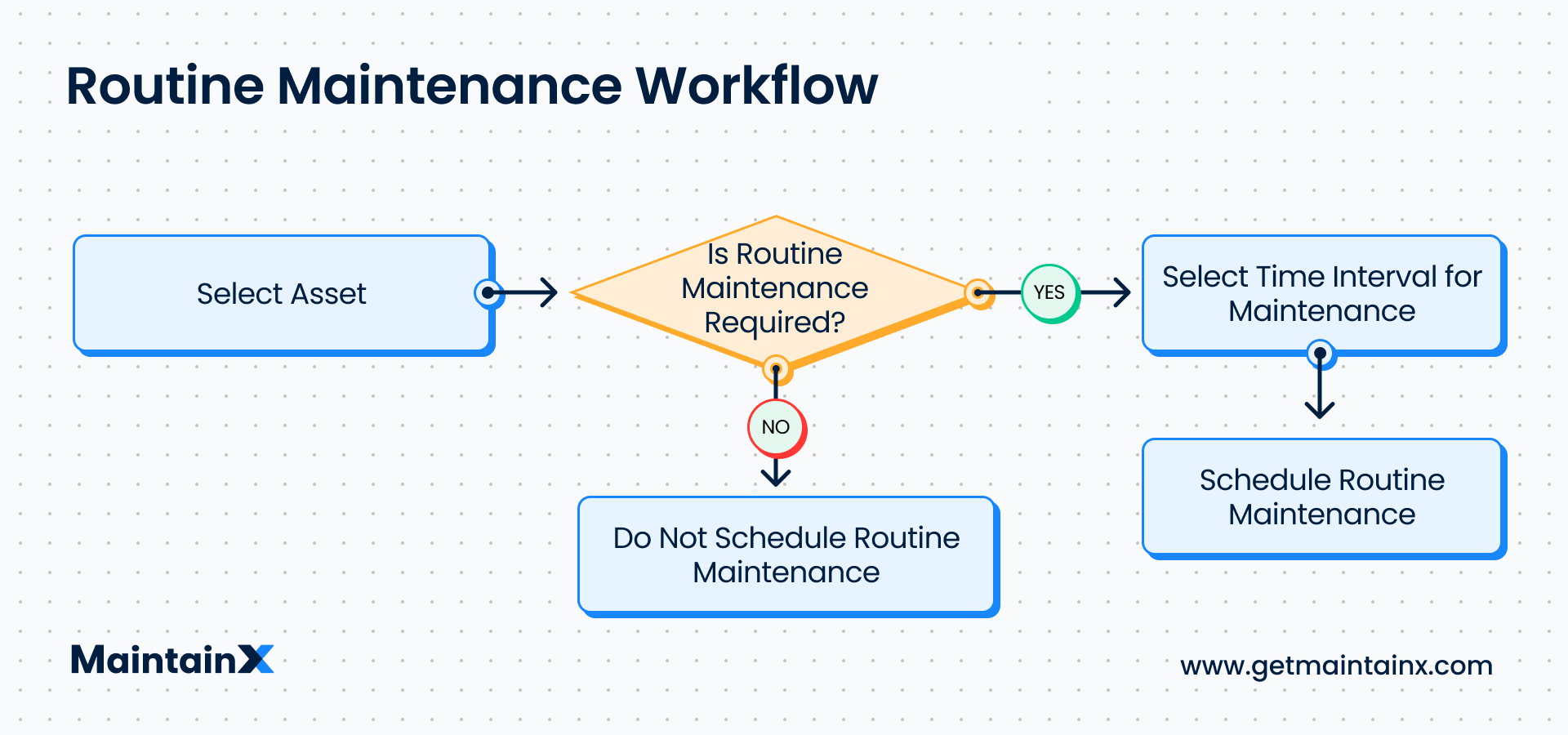
When workers complete these routine work orders—usually inspections and machine servicing—they can reduce the need for emergency maintenance. In addition, routine maintenance reduces wear and tear and, as a result, increases the useful life of assets.
Effective maintenance is not simply upholding the status quo. Because technology is evolving so quickly, maintenance processes must continuously become faster, more accurate, and more efficient. Engineering and innovating these processes means businesses can use maintenance to grow and scale production.—Forbes
Examples of routine maintenance
Examples of routine maintenance include:
- Property management teams that clean and sanitize surfaces and water plants daily.
- Factory workers who lubricate and adjust a specific machine every six months.
- Maintenance technicians and machine operators who inspect high-risk assets for unseen issues every month.
- Car owners who get their motor oil changed every 5,000 miles.
Types of routine maintenance
Routine maintenance falls into several key categories, with each aiming to keep equipment in optimal working condition, prevent unexpected failures, and prolong equipment lifespan. By understanding the different types of routine maintenance, organizations can tailor their maintenance strategies to address specific needs, ensuring equipment runs efficiently and reliably. The four primary types of routine maintenance are:
Time-based maintenance (TBM)
TMB emphasizes replacing parts at fixed intervals, times, or usage markers regardless of condition. It’s mostly used for assets with clear service lines where failure is age-related, such as such as vehicle parts. For example, replacing the timing belt in a car every 60,000 miles to prevent engine damage, regardless of whether the belt shows visible wear, falls under TBM.
Maintenance teams can streamline their processes by scheduling routine tasks in advance. For example, if you follow a monthly schedule for a piece of equipment, you can use a CMMS like MaintainX to create the preventive maintenance work order in advance and have it repeat at the same time every month.
Failure-finding maintenance (FFM)
The goal of Failure Finding Maintenance (FFM) is to detect hidden failures in equipment that are not immediately apparent during regular operation. It’s mostly used on assets that perform protective functions, like safety valves, which are designed to open only when pressure reaches a critical level. Since these components often sit idle, routine checks and tests are necessary to ensure they will function correctly in emergency situations.
Risk-based maintenance (RBM)
RBM prioritizes performing preventive maintenance on high-risk assets. Technicians determine risk levels by analyzing the likelihood of equipment failure and the severity of its associated consequences. Effective RBM relies on risk assessment and maintenance planning, neither of which can successfully proceed without the right tools. Risk assessment, for example, requires teams to collect and analyze robust asset data. Both of these tasks are made easier with software solutions like MaintainX. MaintainX Asset Health Insights, for example, helps you to quickly identify your most problematic assets based on past failures, downtime hours, and more. Similarly, maintenance planning relies on robust and reliable scheduling.
Condition-based maintenance (CBM)
CBM involves monitoring assets for signs of impending breakdowns and taking appropriate actions to maintain uptime. It relies on monitoring and analyzing equipment conditions. By doing so, teams can identify deviations that suggest potential failure. Such diagnostic tools and techniques include vibration analysis, ultrasonic testing, thermography, and much more. Teams can schedule maintenance work orders based on observations about these conditions or use a CMMS to automatically trigger maintenance work based on predetermined thresholds. MaintainX, for example, enables condition-based maintenance triggers that help you keep your assets online.
Advantages of routine maintenance
Routine maintenance offers several advantages that go beyond simply keeping equipment running; it plays a crucial role in optimizing performance, reducing downtime, and extending the lifespan of assets. Here are some of the advantages:
- Reduces downtimes: Assets that are regularly inspected and maintained perform consistently better than those that aren’t. Reduced downtimes translate to increased equipment lifespans, decreased inconveniences, and increased efficiency.
- Minimizes reactive maintenance: Taking a proactive approach to maintenance reduces the chances of dealing with expensive, time-consuming, and sometimes hazardous failures after they occur.
- Increases equipment lifespan: Routine maintenance helps prolong the lifespan of machinery and equipment by preventing wear and tear through regular inspections and servicing. By addressing minor issues early, organizations can avoid costly replacements and ensure that assets operate efficiently for a longer period.
- Improves productivity: Well-maintained equipment operates more efficiently, which can lead to improved production quality and reduced energy consumption. Regular upkeep helps keep machinery running at optimal levels, ensuring that teams meet production targets consistently.
- Improves safety: Regular maintenance checks help ensure that safety equipment, such as emergency shut-off valves and alarms, function correctly. This enhances workplace safety and minimizes the risk of accidents, protecting employees and reducing liability for the organization.
How MaintainX supports routine maintenance
The key to a well-run maintenance program is to develop a schedule and track maintenance performance. While 55 percent of facilities still rely on in-house spreadsheets and schedules to manage maintenance activities, a user-friendly CMMS system like MaintainX can revolutionize any routine maintenance program. MaintainX supports routine maintenance in the following ways:
- Scheduling and managing maintenance activities: MaintainX simplifies work order management in several ways. The system enables you to schedule maintenance work, assign tasks to specific team members, indicate due dates, and set priority levels. Take advantage of our resource planning features to carry out workload-based scheduling. Instead of assigning work orders randomly, you can access labor insights, ensuring that you make assignments based on actual technician capacity. In addition, you can track your work orders in real-time and share and receive updates directly to and from the floor.
- Controlling spare parts inventory: Digitizing your parts inventory with a CMMS like MaintainX ensures that you never stock out again and always have the right parts to complete routine maintenance. Centralized inventory data gives you an easy way to track down critical assets using a system that works for you, which could be barcodes or unique IDs. You can also make smarter decisions to avoid overstocking or understocking and avoid expensive rush orders.
- Storing maintenance data: MaintainX CMMS helps you collect, store, and analyze your maintenance data to optimize your routine maintenance schedules better. Determine if you should be performing maintenance more or less frequently by tracking key KPIs such as mean time to repair (MTTR) and mean time between failure (MTBF). MaintainX’s reporting module offers out-of-the-box reports that generate actionable insights and enable data-driven decision-making.
Routine maintenance FAQs
Routine maintenance is a broader term that encompasses all regular maintenance activities. Preventative Maintenance is a specific type of Routine Maintenance that is performed proactively to prevent equipment failures and extend its life.
To create an effective plan, you could follow this routine maintenance checklist:
- Identify all equipment and assets that require maintenance.
- Determine the manufacturer’s recommendations for maintenance tasks and intervals for each asset.
- Develop detailed procedures for each routine maintenance task.
- Assign responsibilities to specific individuals or teams.
- Establish a schedule for performing routine maintenance activities.
- Implement a system for tracking and documenting routine maintenance.
Routine maintenance helps ensure that each piece of equipment is in good operating condition, reducing the likelihood of accidents or incidents caused by equipment failure. Regular inspections can identify potential safety hazards, and maintenance tasks can address these issues proactively.
A routine maintenance checklist for HVAC systems should include tasks for inspecting and cleaning air filters, thermostats, and compressors. Other tasks should include checking electrical connections, checking operating pressures, and cleaning drains. For a robust HVAC preventive maintenance checklist, check out the procedures in MaintainX’s Global Procedure Library.
See MaintainX in action