REPORTING
Turn data into cost-saving insights
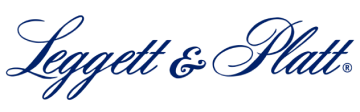
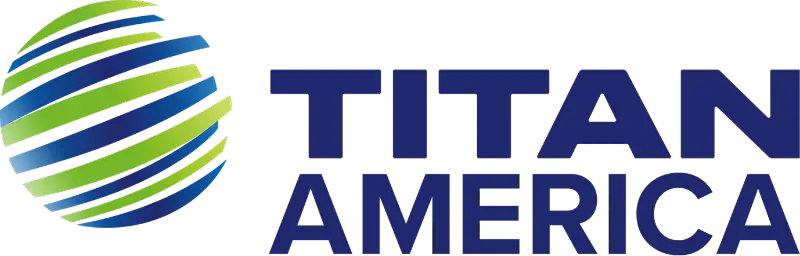
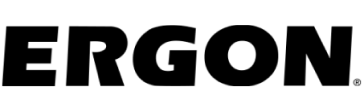

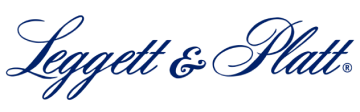
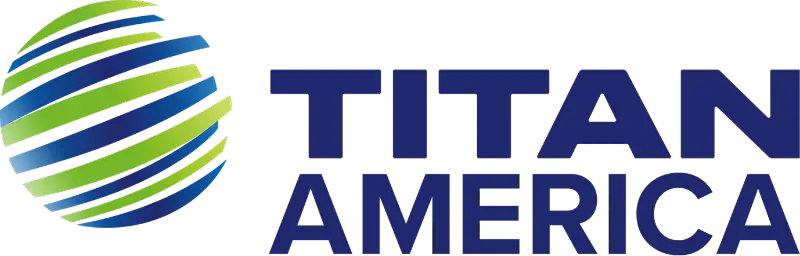
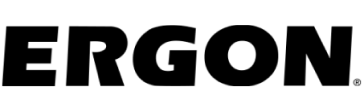

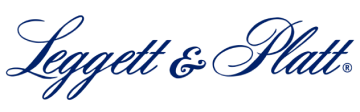
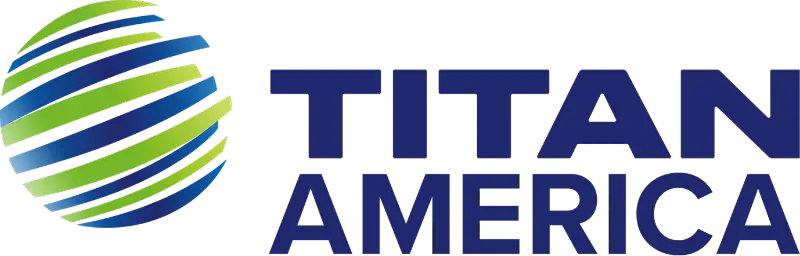
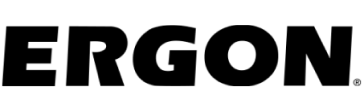

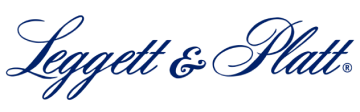
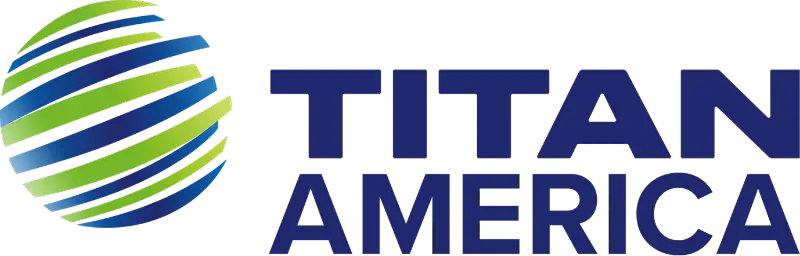
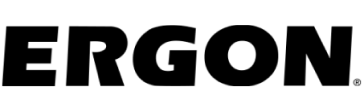

Our clients using MaintainX report
(mean time to repair)
Improve performance against KPIs and goals
Track your resources and optimize operations to hit your most important goals, like reducing MTTR, increasing production capacity, and reducing downtime.
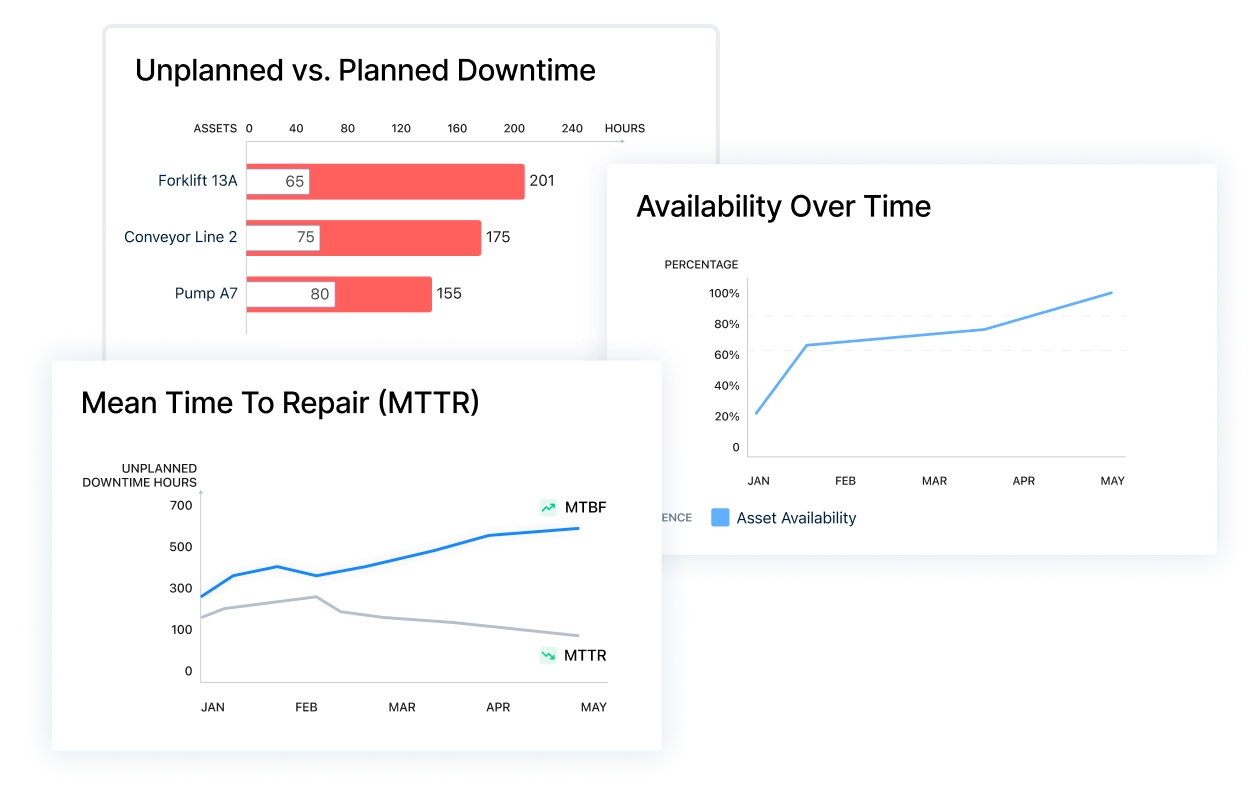
Transition from reactive to preventive maintenance
Track the health of your PM program and quickly spot broken maintenance processes before they hurt your bottom line.
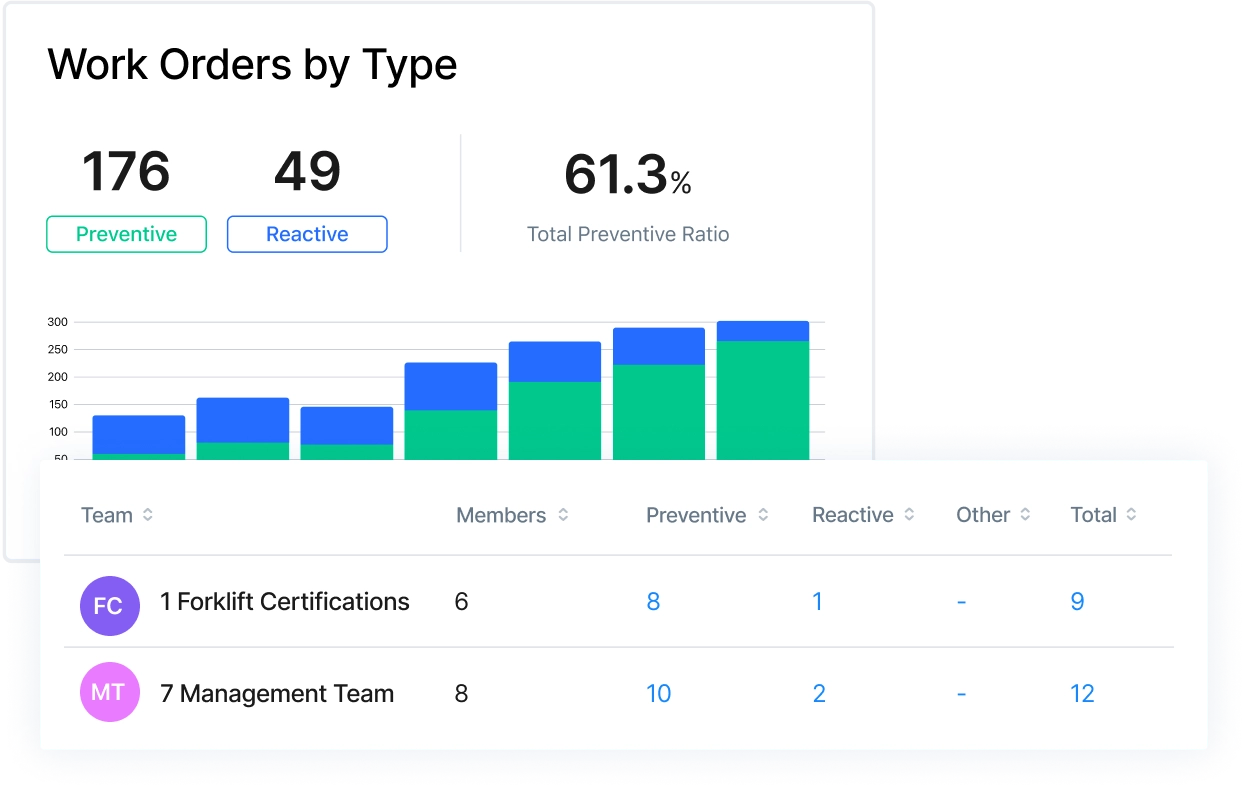
Enforce safety and compliance with detailed audit trails
Simplify your compliance with regulatory bodies like OSHA with real-time records of work order history and maintenance activity.
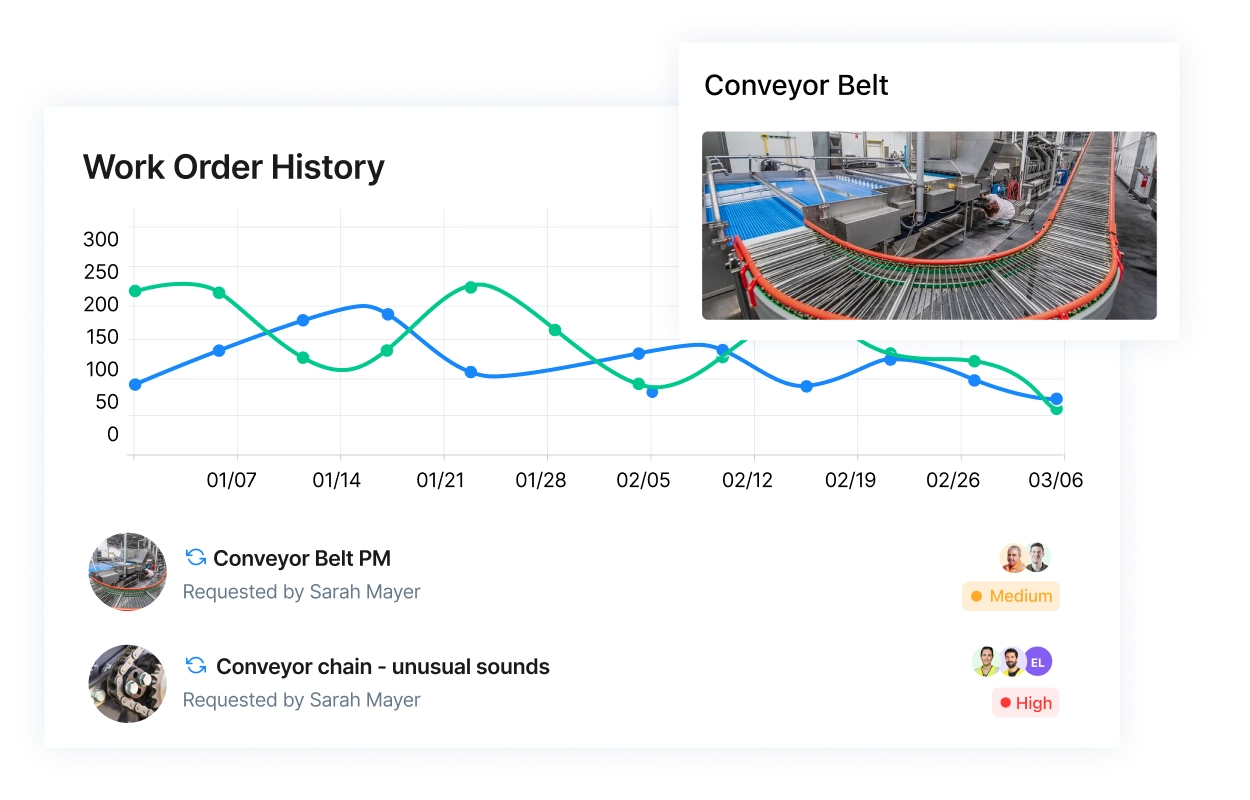
Track asset health and identify problematic assets
Minimize downtime and safeguard revenue with proactive alerts before an asset fails, insights that tell you why assets fail, and which assets are costing you the most.

Get the right insights with filters and custom dashboards
Tailor your insights to fit your needs, whether it’s by comparing performance across sites, building custom dashboards, or filtering reports by team, asset criticality, and so much more.
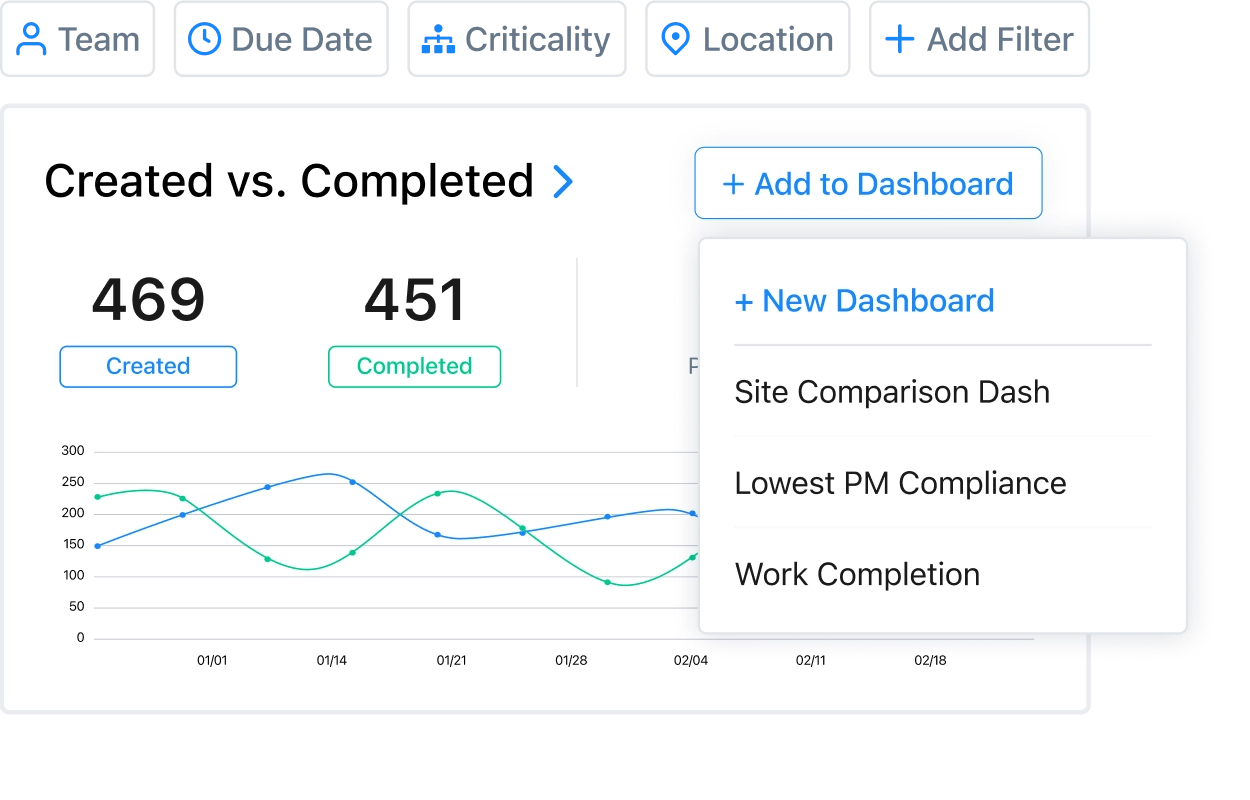
Save time with scheduled reports and exports
Share the right data with stakeholders at the right time with scheduled reports, and export them in your desired formats like PDF or CSV.
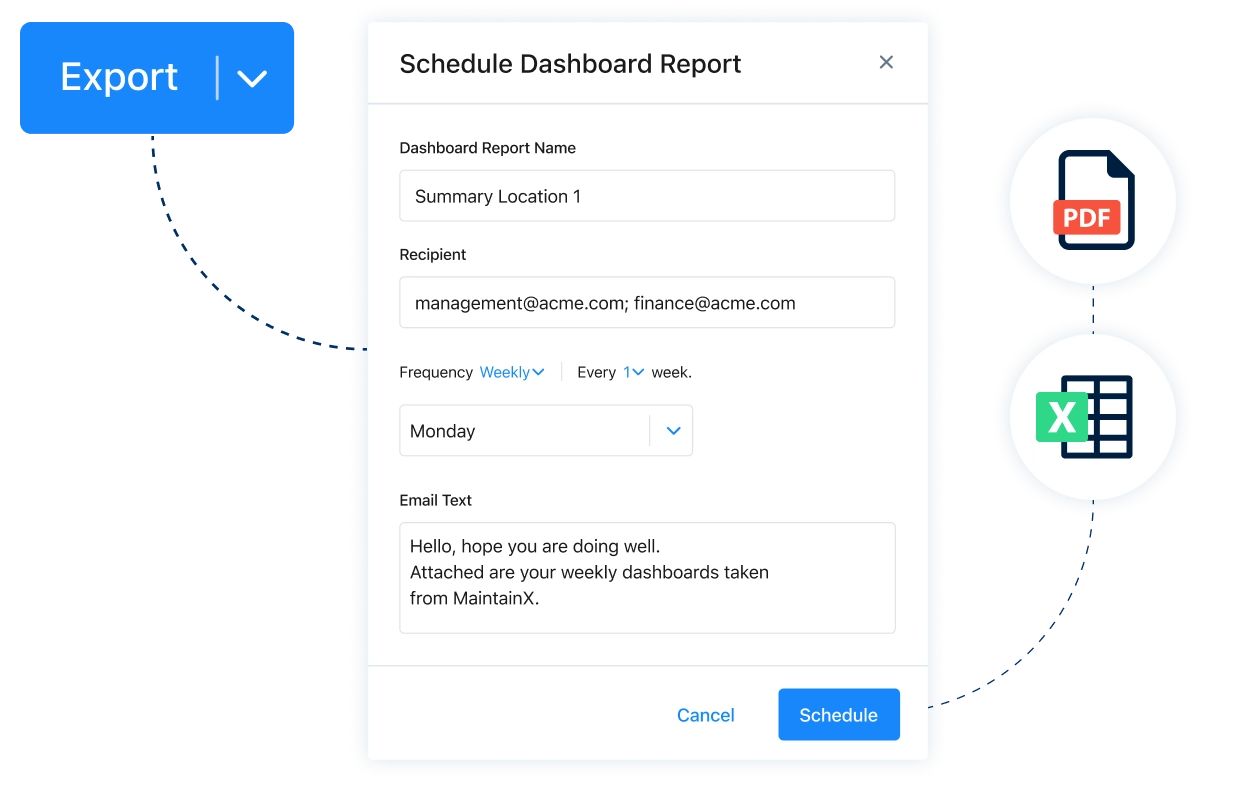
MaintainX is the best software for maintenance and operations across third-party review sites
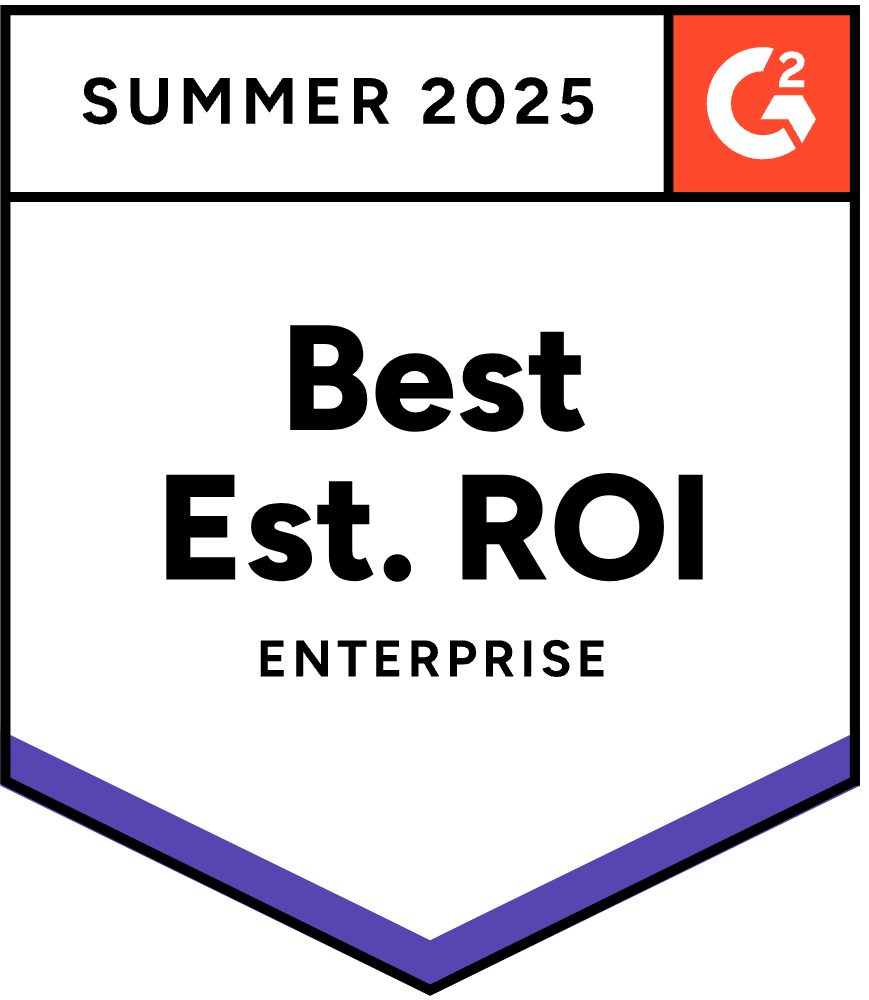
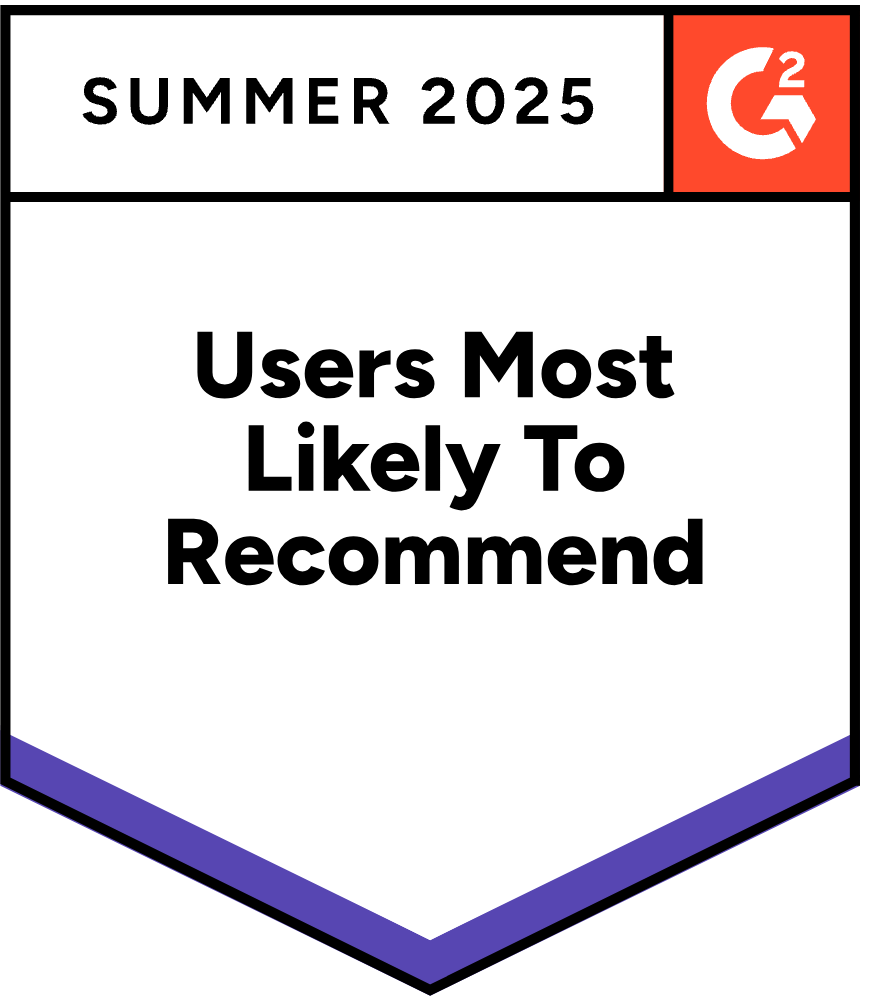
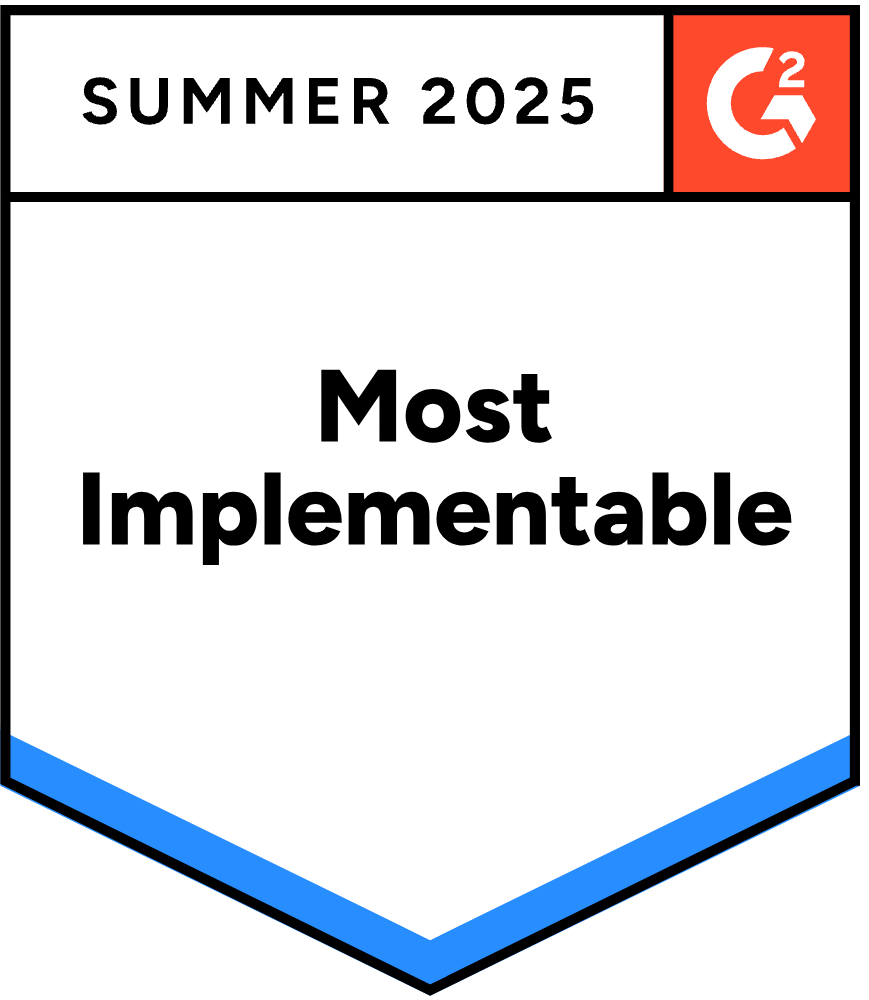
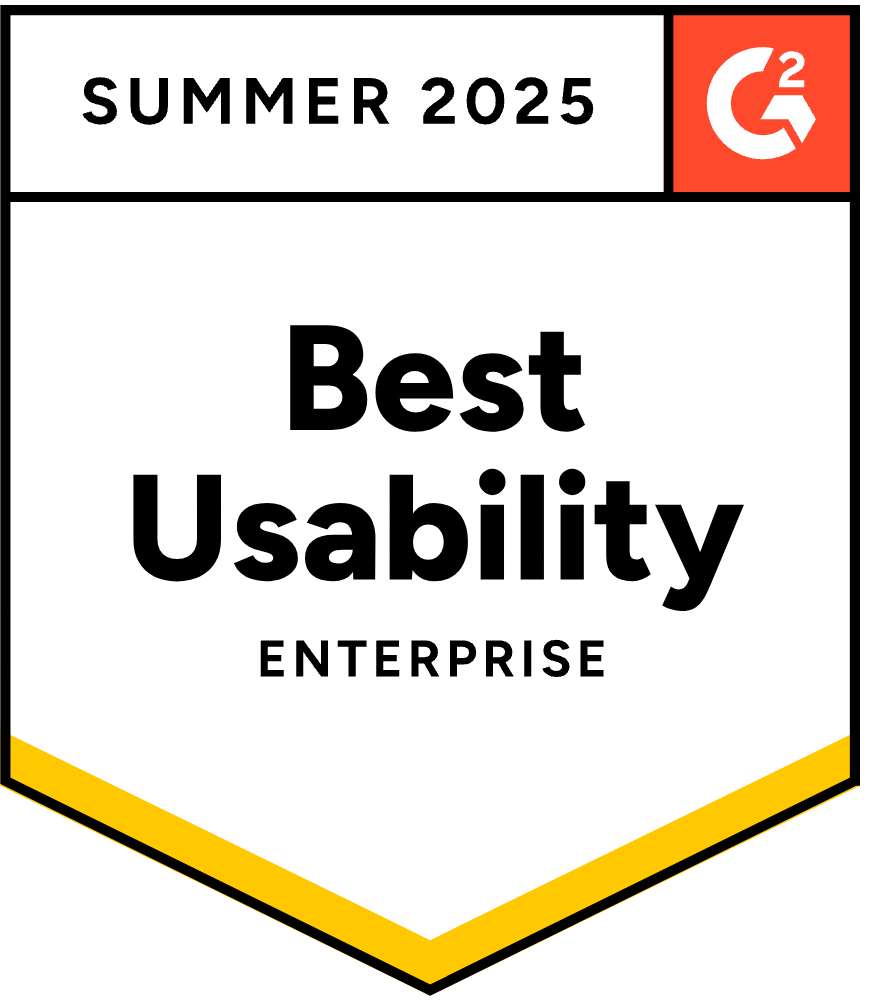
See what customers have to say
Get more done with MaintainX
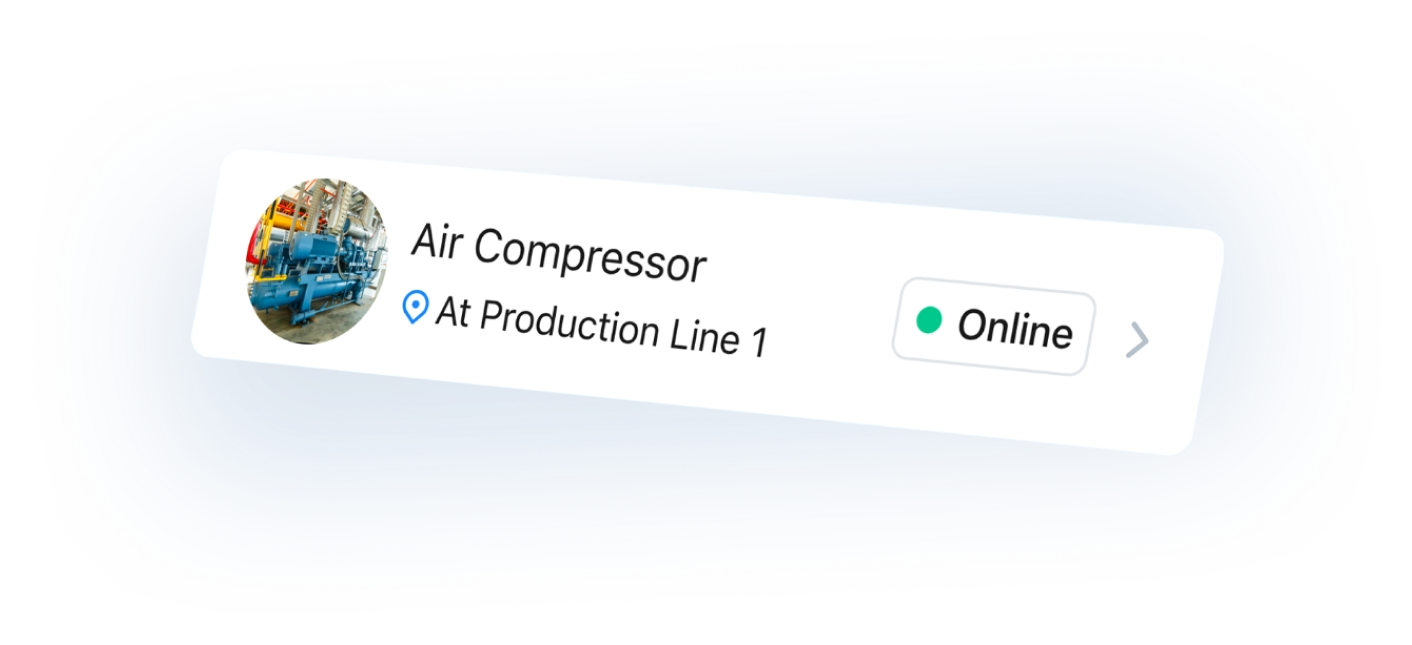
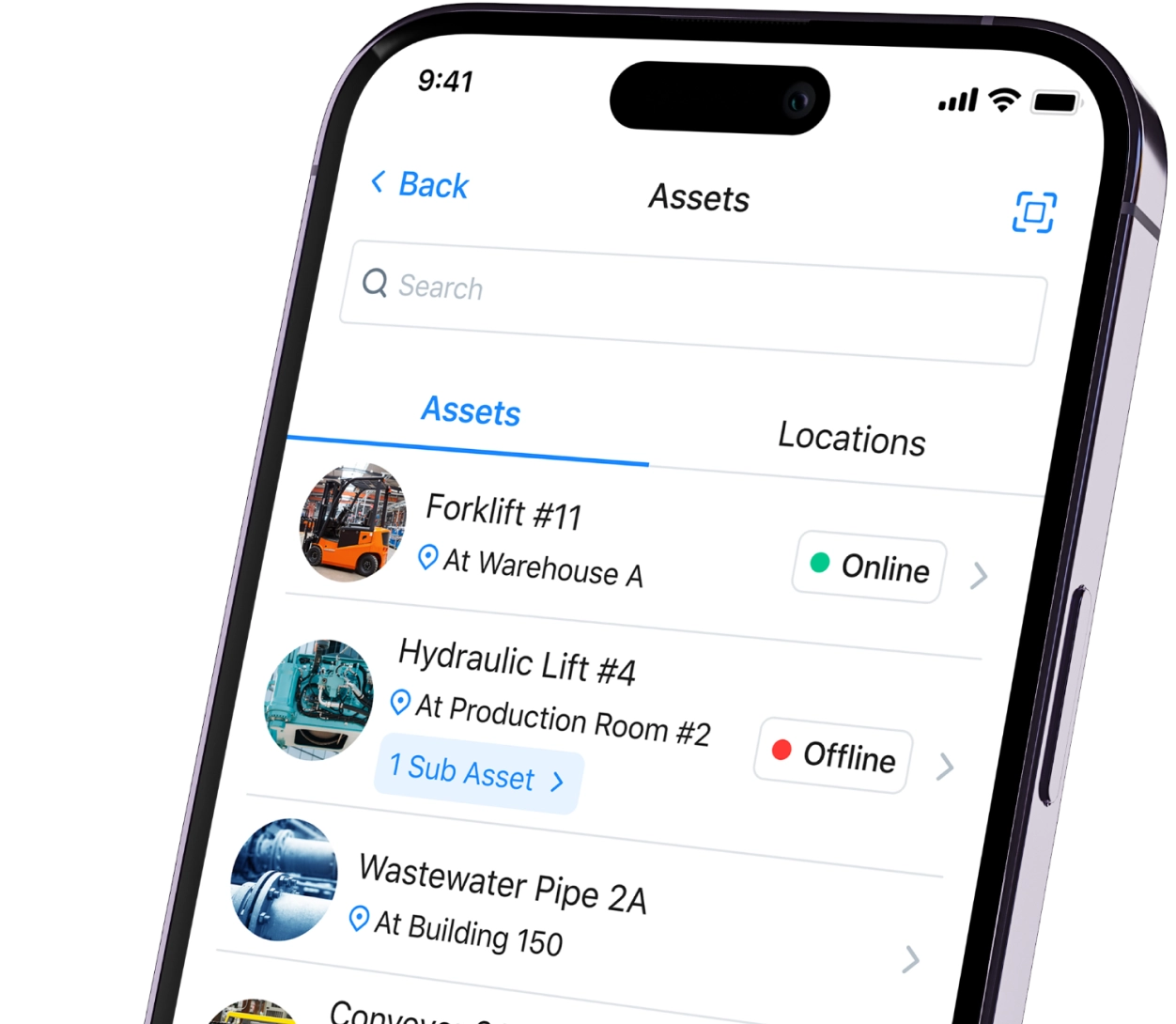