
For many organizations, knowing which assets take priority over another isn’t always clear-cut. This is where a criticality analysis and a CMMS can help.
Criticality measures how integral a piece of equipment is to your business.
Sometimes asset criticality can be obvious. For example, if you run an industrial spray painting company, your compressed air system is vital to getting the job done. As a result, you’d need to address any unplanned compressor downtime immediately. Likewise, you’d need to prioritize any maintenance of your compressor, pipework, air dryer, and filtration systems over maintenance of less critical equipment.
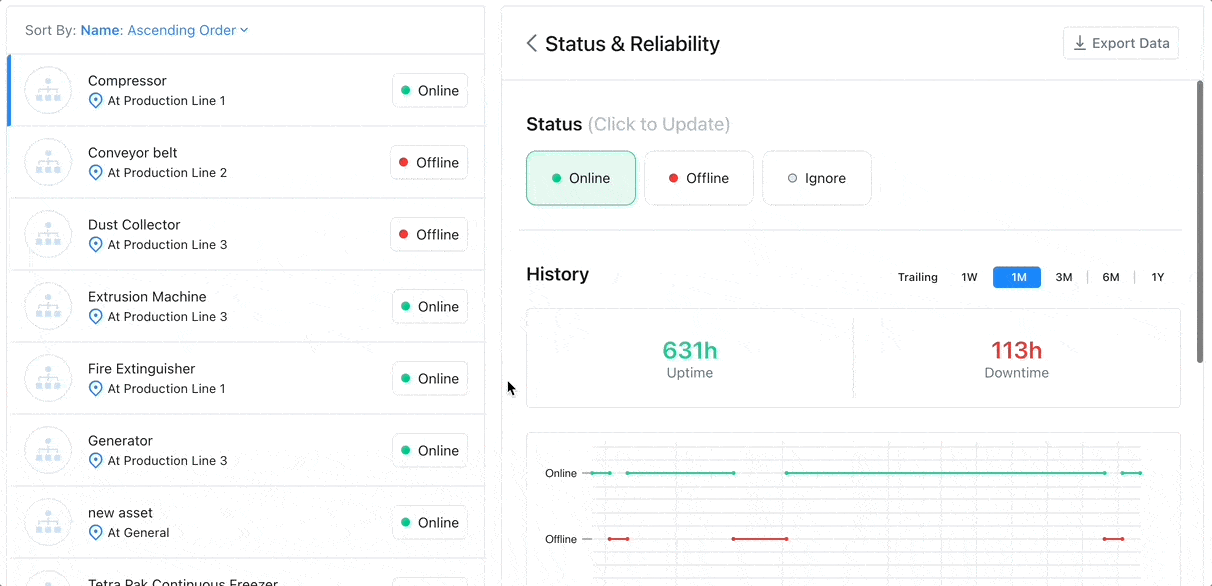
What Is Asset Criticality Analysis?
As your business matures and increases in complexity, the number of assets and equipment to service and maintain grows exponentially.
This can present several new challenges. How do you know what assets impact your ability to fulfill orders for your customers? What gets fixed first? And when budgets are tight, where can you safely reduce maintenance costs? A criticality analysis can help answer these questions.
A criticality analysis is a tool used to prioritize asset management and maintenance. The tool is a quantitative way to approach your maintenance strategy, using numeric values to rate each piece of equipment on factors such as the seriousness of a potential failure.
Why Perform a Criticality Analysis?
With the data you collect from your Computerized Maintenance Management System (CMMS), you can view and analyze historical work orders, preventive maintenance information, and asset failure reports.
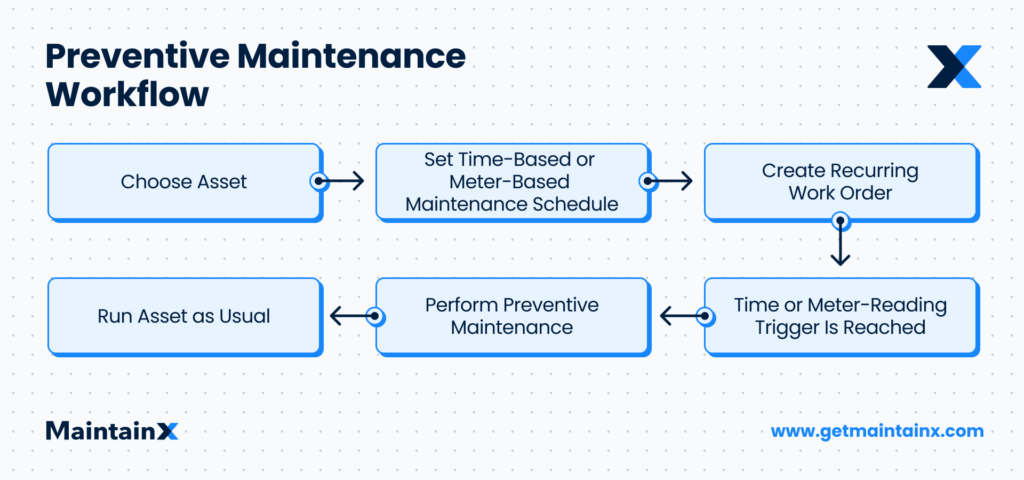
Now, armed with this data and insights from your maintenance team, you can gain clearer and more actionable insights into what assets impact productivity most. You can then confidently allocate funds to essential maintenance management tasks.
These insights also help you optimize spare parts inventory management, use your maintenance resources more effectively, and identify necessary upgrades of aging equipment.
Furthermore, one additional reason to perform criticality analysis is to avoid “cost consequence,” the total business impact of that asset’s failure.
“The cost consequence is not just the cost of lost production and the cost of the repair, but also includes cost related to safety, the environment, quality, the organization’s reputation, etc. The cost consequence is the failure frequency is an estimated number. This is a probability based on history or industry norms for similar situations and updated as new asset knowledge is developed.”
Reliability Web
The Big Picture: Reliability-Centered Maintenance and FMEA
Criticality analysis works best when you apply it as part of a more extensive failure analysis methodology, such as a failure mode and effects analysis (FMEA), and overarching frameworks, such as Reliability-Centered Maintenance (RCM).
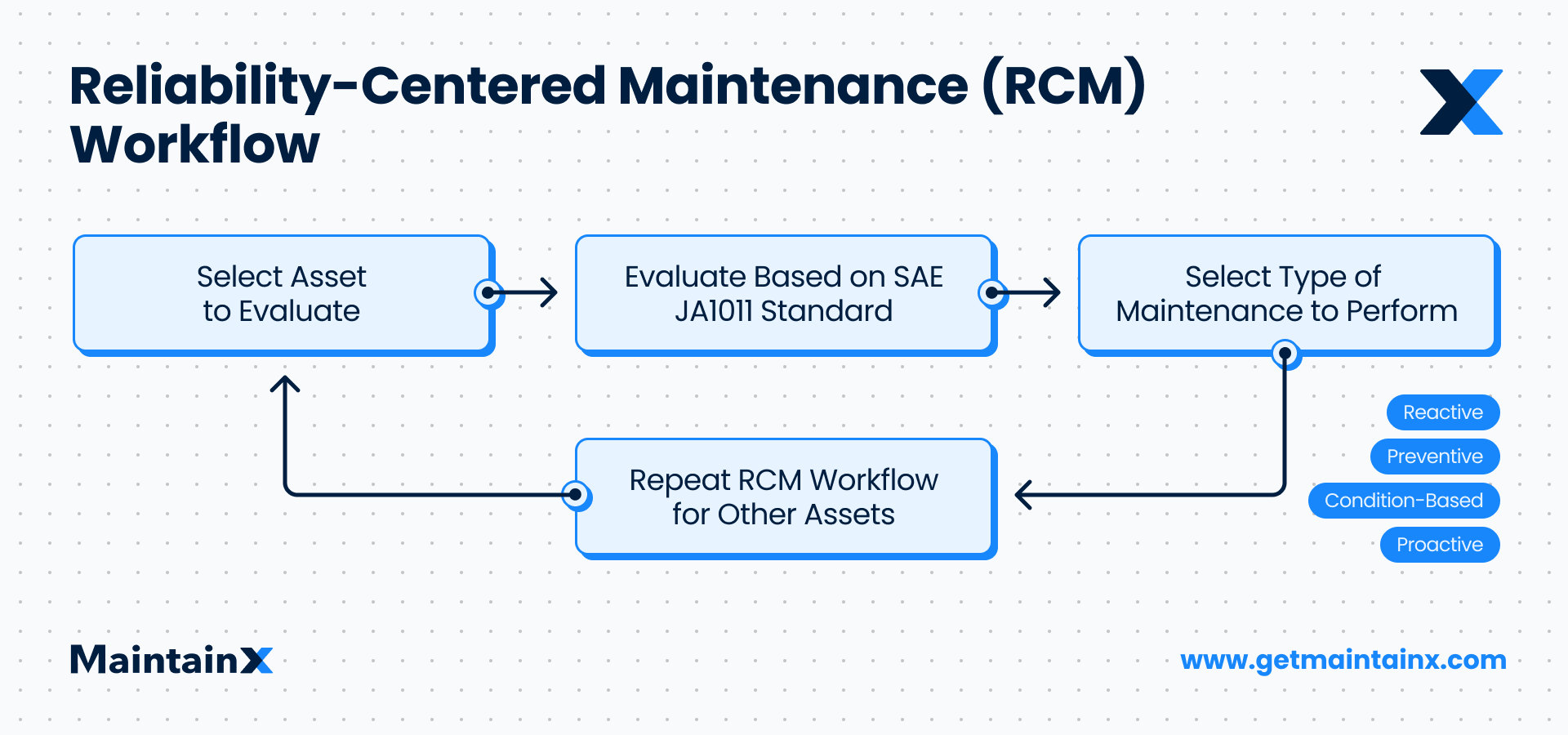
These approaches seek to understand the wide range of influences that impact the operability of an asset–factors like design or maintenance program inefficiencies–and uncover the root causes of why an asset fails.
However, FMECA (including C for Criticality) takes the simple cause-and-effect analysis a step further. Here, you conduct a risk assessment for each failure mode. This is the essence of criticality analysis. You calculate which assets are at high risk of failure. Then, you adjust your asset operations and maintenance program accordingly.
“When looking at your assets, you’ve got to understand the consequence to the business. You could have a pump that’s outside that might pump runoff water for no reason… And you have the same exact pump that’s pumping oil to your food manufacturing process to make a recipe. It could be the same two pumps, but the consequences to the business are completely different.”
Plant Services
How to Perform a Criticality Analysis Using Hard Data
There are several schools of thought on how to approach asset criticality analysis. Some methods take an “all assets are equal” approach. Here you give the same amount of attention (and funds) to vital assets as to less critical pieces of equipment.
However, other approaches are subjective. These are based on your maintenance team’s perceived risk of breakdowns or the difficulty and complexity of previous maintenance tasks.
While you should consider your team’s input, you should combine it with data from your maintenance software to give a more accurate picture of asset performance.
This quantitative approach uses a Risk Priority Number or RPN to indicate which critical equipment you should prioritize.
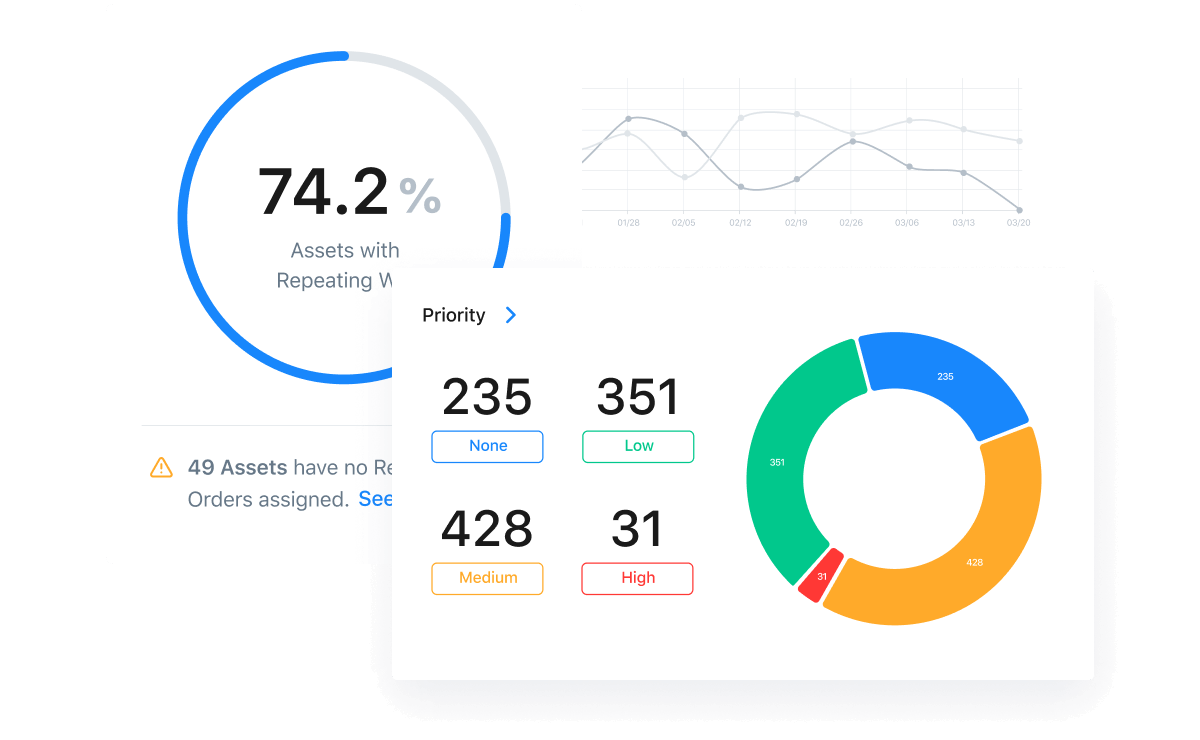
How to Calculate Risk Priority Number (RPN)
To calculate an asset’s risk priority number, follow this formula:
RPN = S × O × D
S = Severity of the impact of failure
O = Likelihood of failure occurring
D = Ease of detecting the failure
Your business can apply its own criticality ranking matrix to each element of this equation, using a scale of 1 to 10. Each number represents a documented and agreed-upon set of criteria.
By the way, this is a great example of where standard operating procedures can assist teams in maintaining consistency in ranking asset maintenance metrics.
Your final RPN receives a level of risk based on a numerical scale. For example, you should prioritize maintenance efforts for an asset with an RPN score of 90 over equipment with an RPN of 20.
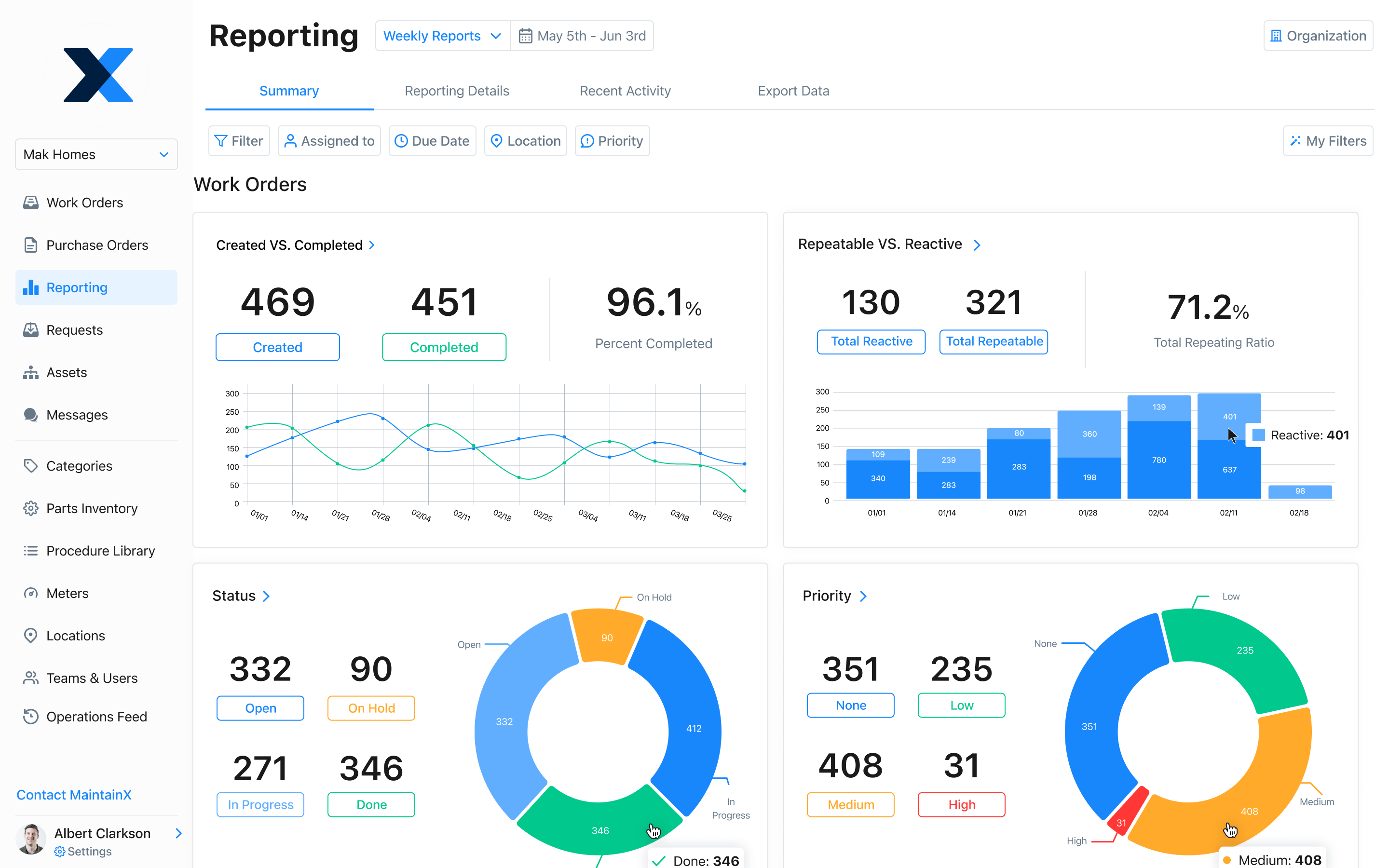
What CMMS Data Should I Analyze?
As you can see, the success and accuracy of your criticality analysis rely heavily on data. This is where you can lean on your CMMS to sense-check anecdotal evidence.
A CMMS can capture data on every asset in your facility. While this is helpful for day-to-day tasks like health and safety checklists and equipment inspections, it also allows you to tap into a huge library of historical data.
When performing an asset criticality assessment, you can consider CMMS metrics such as:
- Spare parts consumption
- Equipment failure records
- Condition monitoring data (uptime vs. downtime)
- Current predictive maintenance schedules
- Results and frequency of prior maintenance work
- Overall equipment effectiveness (OOE)
- Notes attached to work orders
- Quality metrics relating to product QA inspections
Pull It All Together with MaintainX
Asset analysis is more straightforward with MaintainX. You can get accurate real-time data across the whole equipment life cycle. With this data, you and your team can accurately assess the criticality of each piece of equipment, streamline maintenance workflows, reduce costs, and ensure your assets are being proactively managed and maintained.
Schedule a demo, or try MaintainX yourself. It’s free, easy to use, and designed for collaboration.
FAQs
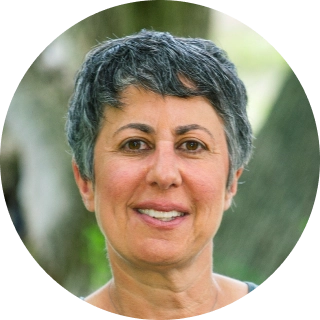
Caroline Eisner is a writer and editor with experience across the profit and nonprofit sectors, government, education, and financial organizations. She has held leadership positions in K16 institutions and has led large-scale digital projects, interactive websites, and a business writing consultancy.