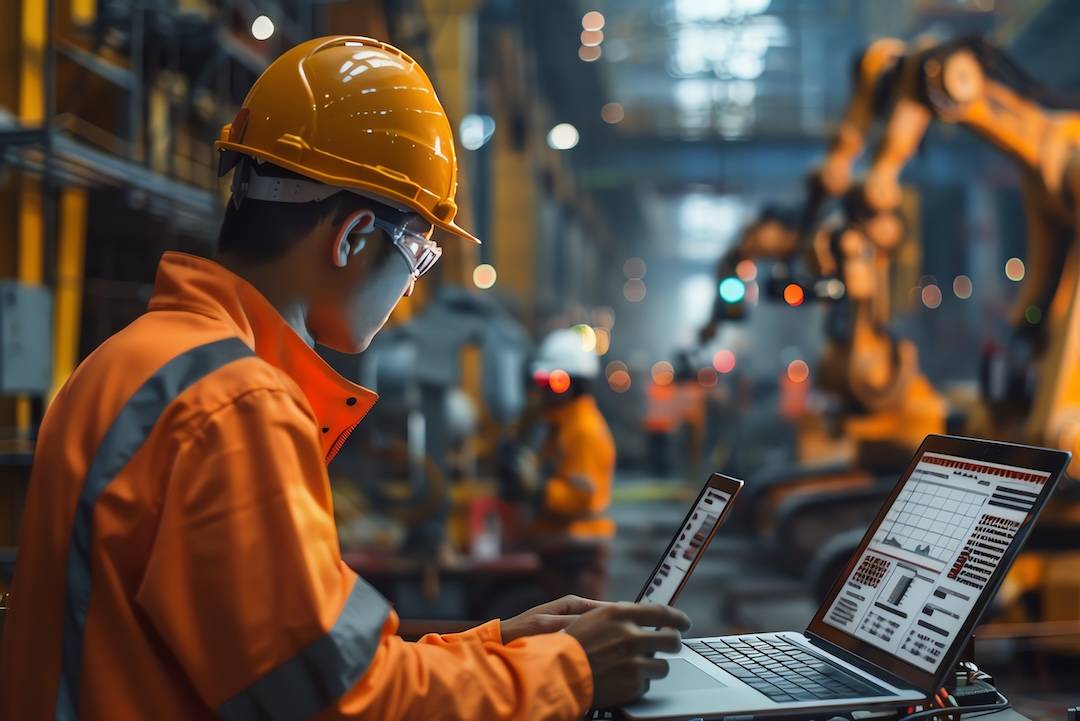
You just left a monthly meeting with your manager and their manager. Everything seemed to go well. You presented the usual reports. Everyone nodded.
A few questions were asked, but nothing out of the ordinary. After all, your team is doing well. Uptime has increased. So has wrench time. You even found a few ways to cut inventory costs.
But something isn’t quite right. It seemed like everyone was only half listening and offered routine criticism before moving on. It’s hard to shake the feeling that maintenance isn’t valued the same way other departments are, no matter how well the team is doing.
Proving the high-level impact of the maintenance program is one of the biggest challenges for asset management leaders.
This article is a guide to translating everyday maintenance KPIs and metrics into insights that make an impression in the boardroom so you can get more support for your team’s goals.
Why it’s so Difficult to Communicate the Impact of Maintenance
Maintenance reporting is an hourly habit at most facilities. There’s no shortage of numbers, dashboards, and trends to look at. But why is it so difficult to get leadership to value these insights the same way they value data from other departments?
There are a few reasons:
- A lot of maintenance work has a long-term impact, while senior leaders focus on short and medium-term results. Your strategy might pay off five years from now, but VPs and executives are thinking about solving a problem in 12 to 18 months.
- It’s hard to directly connect maintenance to improvements in production, capacity, and other revenue-generating activities. Senior leaders don’t just look for results—they want repeatable ways to operate.
- You might lack visibility into higher-level priorities and goals. If you don’t know how higher-ups measure success, there’s no way to connect your KPIs to that definition.
- Senior leaders often see maintenance as a cost center. This seeps through to their views on maintenance metrics.
Let’s explore how to get around these roadblocks with reporting that gets your team the validation and investment it deserves.
A framework for translating maintenance metrics into business outcomes
Linking maintenance metrics and KPIs to financial impact is the quickest way to elevate your reporting and get the attention of more senior leaders and executives. Here are a few ways to translate common maintenance metrics into business outcomes:
Four Practical Steps for Reducing Maintenance Costs: Get your copy of the guide
How to Talk About Maintenance ROI Like a Business Leader
The words you use to communicate your strategy also shape how maintenance is viewed at your company. Here are some prompts to transform floor-level wins into programs worthy of extra resources.
Building a Maintenance Impact Score to Show the Value of Maintenance
A Maintenance Impact Score is a structured way to measure the value of your maintenance program and communicate it to senior leaders and executives. The Maintenance Impact Score analyzes the work done in five key areas:
Here’s an example of what a Maintenance Impact Score might look like:
Use data to elevate the impact of maintenance at your company
You likely have all the information you need to communicate the value of maintenance at the highest levels of your organization. Elevating that data requires you to put it into language that connects to the main priorities of senior leaders.
Understand your leaders’ primary objectives, then work backwards to tie your maintenance activities to them. Go beyond accomplishments to show what led to those gains and how they can be scaled.
You might spend a few more hours working on dashboards, spreadsheets, and presentation decks, but the return on this investment will be well worth it.
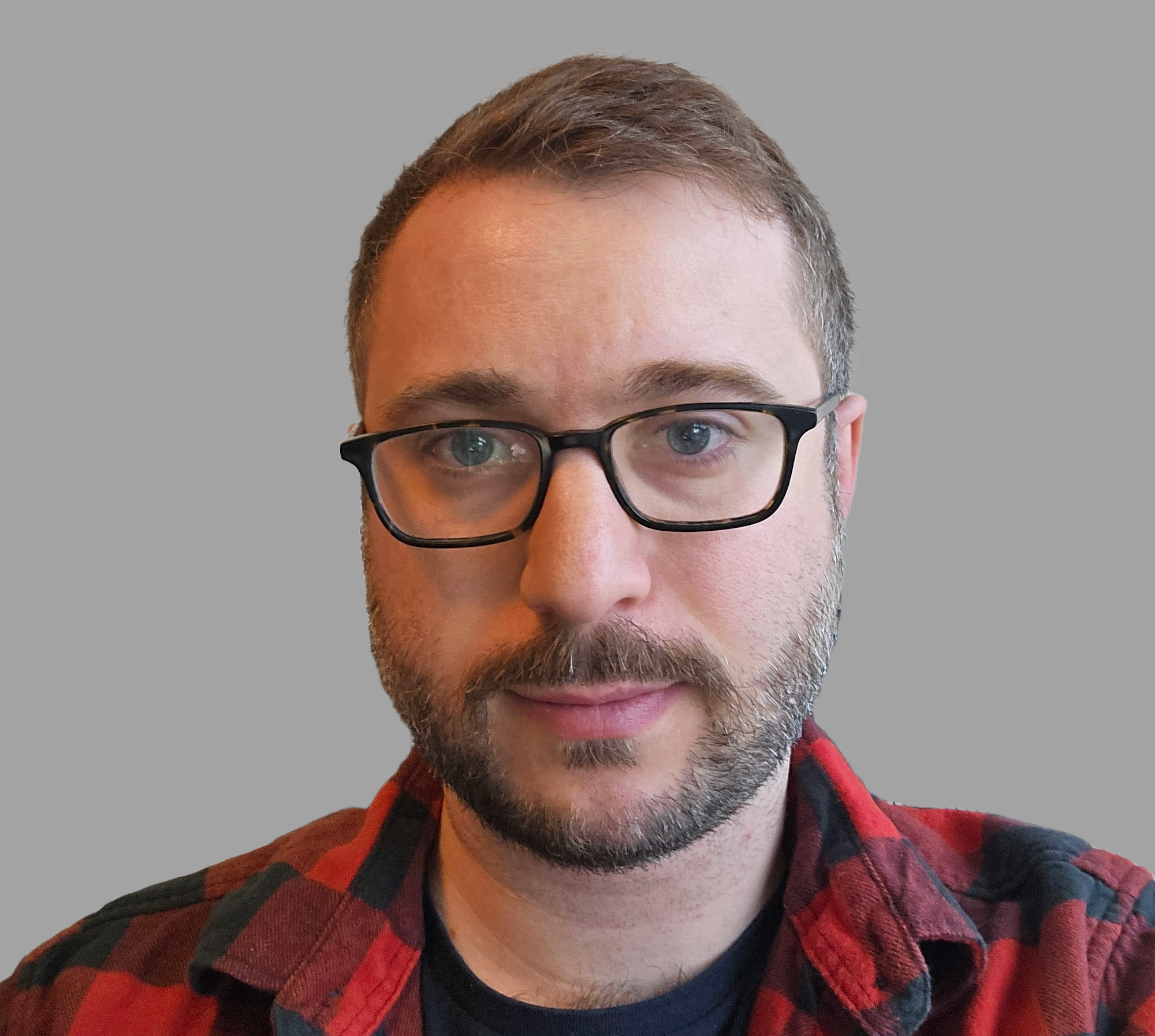
Marc Cousineau is the Senior Content Marketing Manager at MaintainX. Marc has over a decade of experience telling stories for technology brands, including more than five years writing about the maintenance and asset management industry.