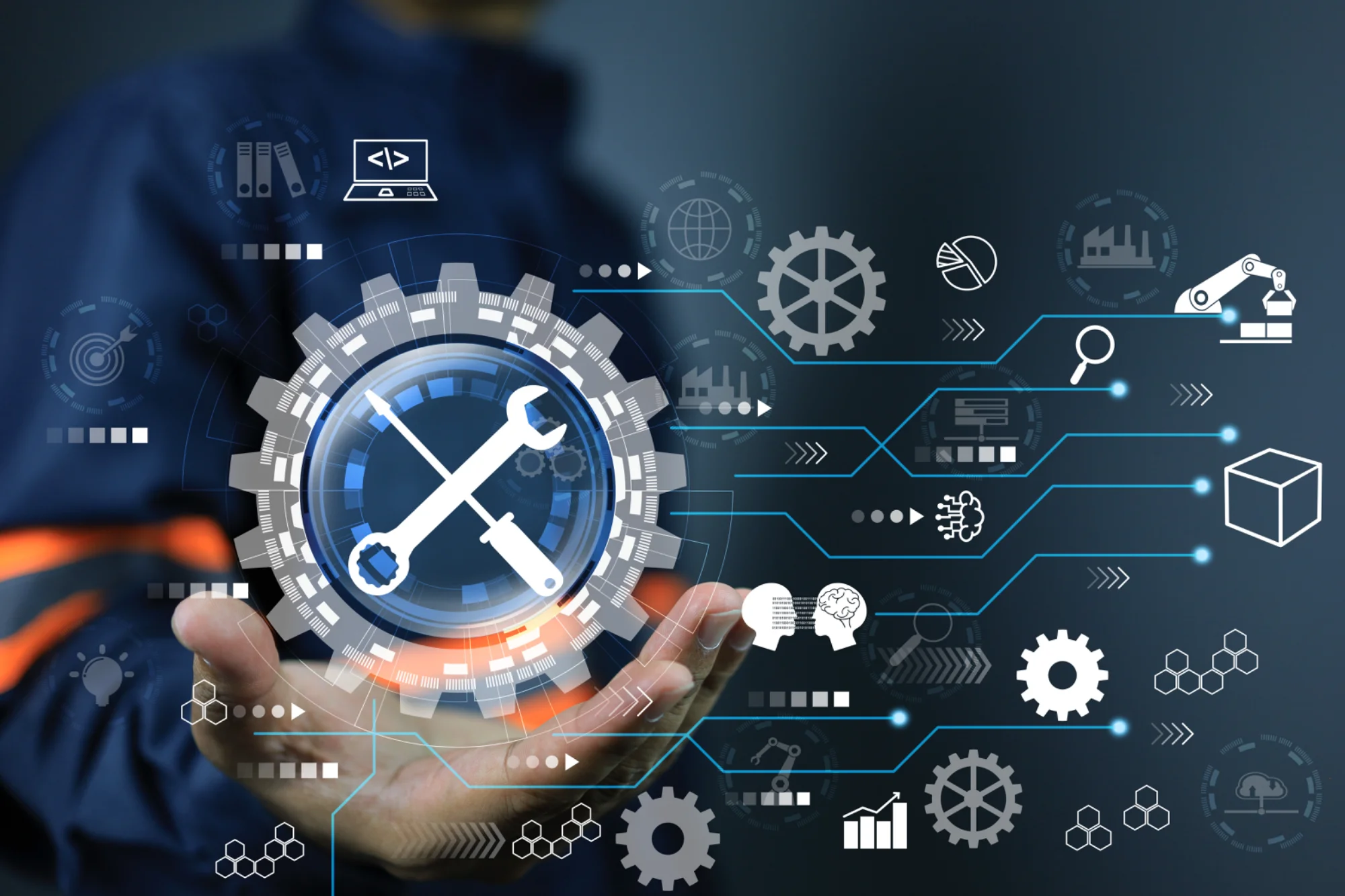
Implementing FRACAS and work order management software together helps achieve a balance between preventive and reactive maintenance. Preventive maintenance programs are often overly conservative. You might be performing more tasks than necessary as part of your maintenance schedule. On the other hand, reactive maintenance can lead to increased downtime.
The FRACAS approach helps optimize your preventive maintenance process by eliminating unnecessary tasks in the schedule. In this post, we explain the concept of FRACAS and how it helps optimize your maintenance management process.
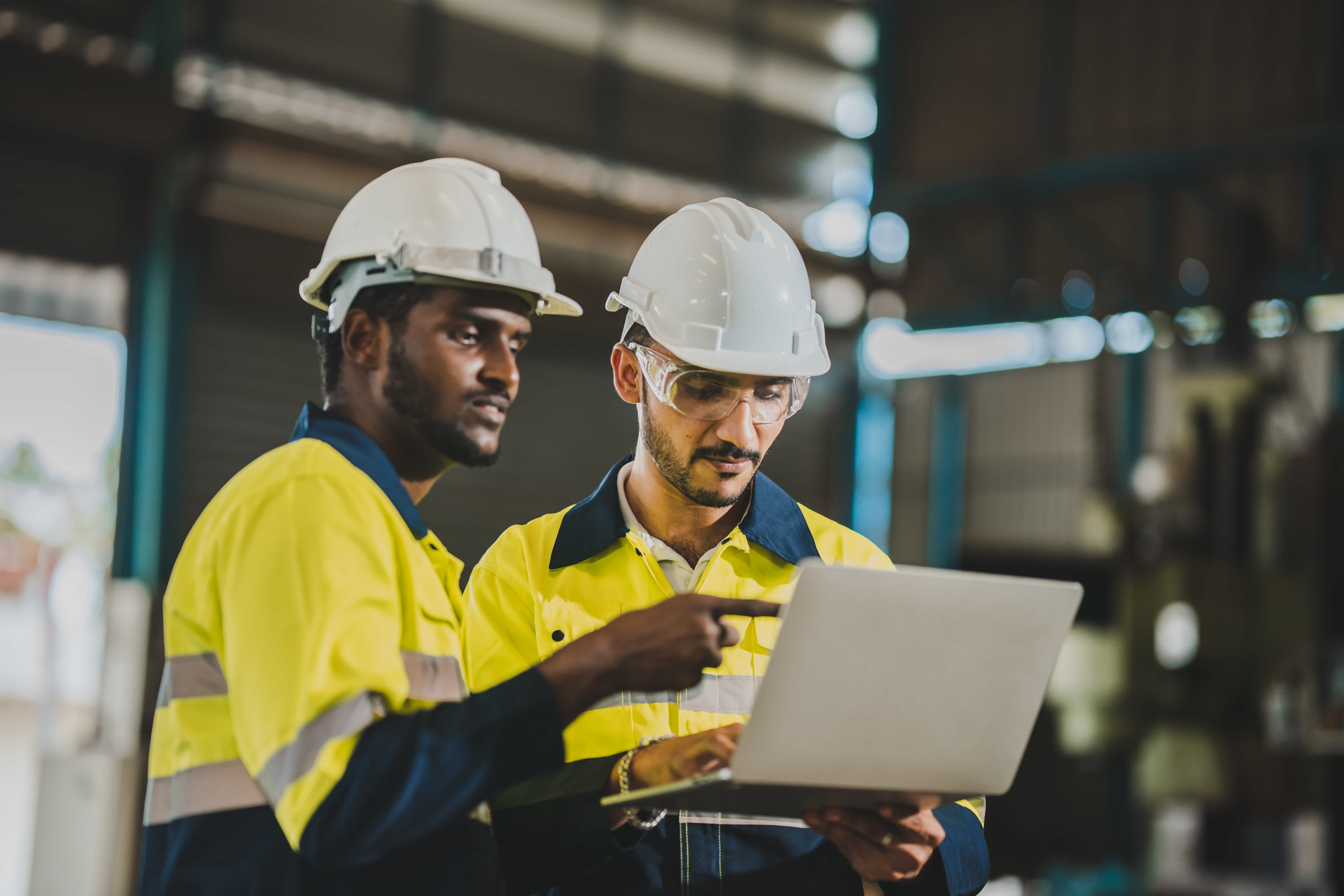
What Is FRACAS?
FRACAS is an acronym for Failure Reporting, Analysis, and Corrective Action System. It was initially used to improve the reliability and maintainability of military equipment systems. The Department of Defense first used the term as military standard MIL-STD-2155. Over time, the closed-loop process has evolved to meet the needs of various industries.
The FRACAS method involves three steps: creating a database of failure events, identifying and analyzing the causes, and finding corrective action. Below, we explain the entire process:
1. Failure Events and Reporting
The first step is to collect all the information you can about a specific failure or issue. The details you include here might vary based on the severity of its impact on operations and your industry.
In most cases, you should include information such as the date and time of the asset failure, as well as the technician who identified the failure or issue, the events leading up to the failure incident, any corrective action that the technician performed, and preventive measures.
The challenge? You might not have enough data. That’s why you need a CMMS (computerized maintenance management system).
A CMMS is an advanced work order management solution. CMMS solutions help automate data collection. It collects and stores data in real time as technicians perform maintenance tasks. When you need failure data for reporting, you’ll have it easily accessible in your CMMS.
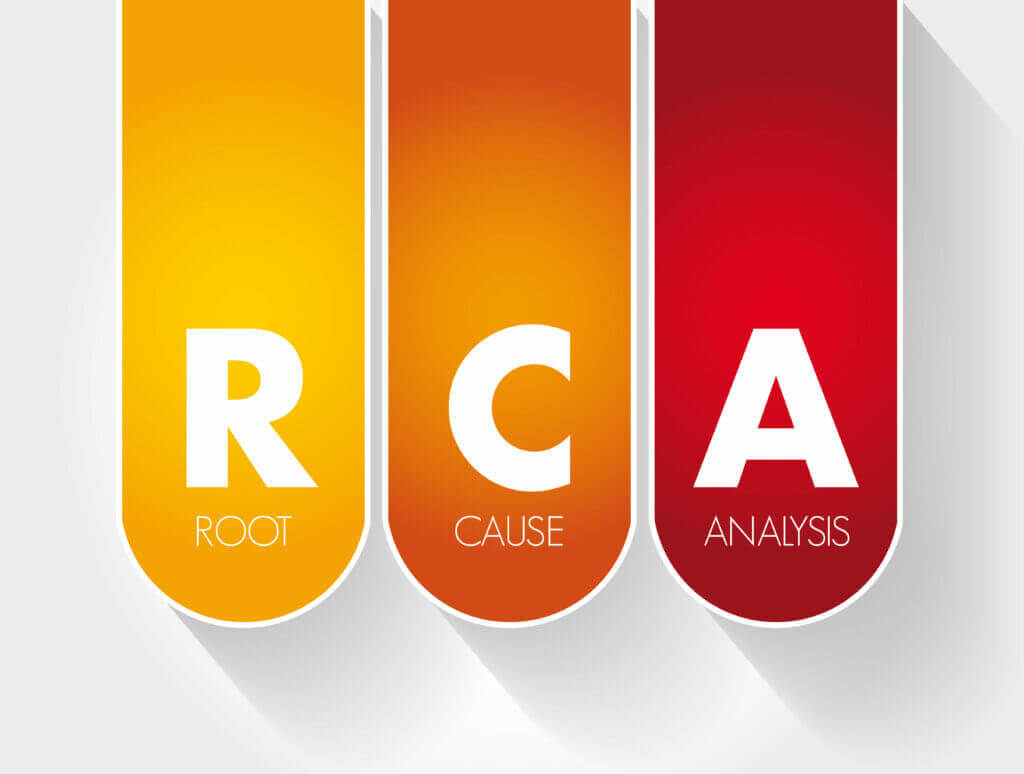
2. Identifying and Analyzing Causes
Once you have all the data, find the root cause of the failure. Finding the root cause is vital to ensuring you’ve fixed the issue. It’s also essential to determine preventive measures so the problem doesn’t recur in the future.
3. Performing Corrective Action
After you find the root cause, take corrective action. The maintenance team leader might consider creating a standard operating procedure (SOP) for fixing such issues.
You can create an SOP on a CMMS like MaintainX. If the problem resurfaces in the future, you can create a work order using the SOP you created in MaintainX without much manual work. Taking corrective action closes the FRACAS loop.
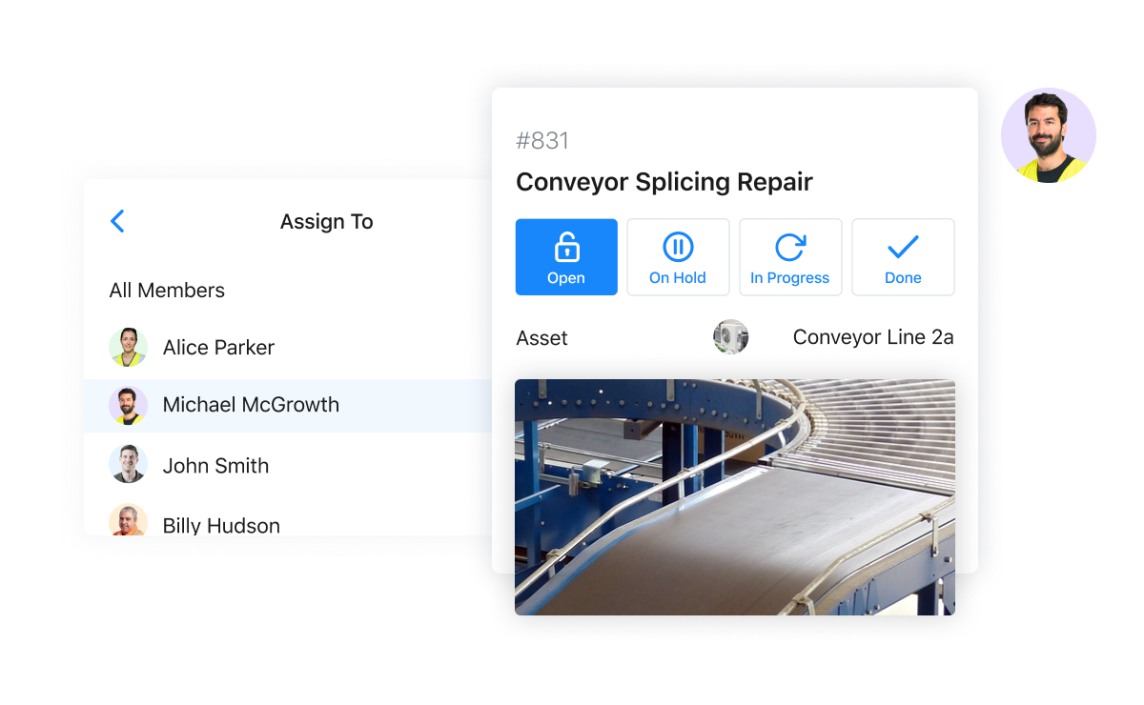
How to Implement FRACAS
FRACAS is a generic methodology, so you don’t use templates to implement it. You must implement a FRACAS system that aligns with your business’s needs.
However, there are a few industry-specific FRACAS programs you can refer to for inspiration. ISO 14224:2016, used in the petroleum and natural gas industries to standardize failure data collection and failure modes, is a great example.
Data is a preliminary requirement to implement FRACAS. You need structured data to draw conclusions and identify patterns. Once you have the data, follow each step in the FRACAS process to ensure you get all the vital information.
Here is how to implement FRACAS:
Discovery Phase
The discovery phase involves identifying tasks you need to perform, establishing accountability, and designing approval processes.
For example, you must determine what counts as a failure event, identify failure modes, and outline root cause analysis (RCA) procedures.
Create a business wiki using a collection of standard operating procedures so all processes are well documented and easily accessible to all team members.
Design Phase
The design phase involves designing a system based on the failure modes, RCA procedures, and other information from the discovery phase. Plan each task within your system based on whether it is manual or document-based.
Human tasks require human involvement. A human must be physically present for these maintenance activities. Document-based tasks are analytical tasks. Humans need to read and analyze software-generated reports, but physical presence isn’t necessary.
Enactment Phase
The enactment phase is about execution. Once you’ve designed a system, inform the team members about the tasks and the overall system. You can execute FRACAS tasks using a CMMS software like MaintainX.
A CMMS helps track the status of each task in real time, so you can intervene when necessary and minimize inefficiencies. You can also use CMMS to define failure codes and run failure mode and effect analysis (FMEA). CMMS is also an excellent alternative for enterprise asset management (EAM) systems.
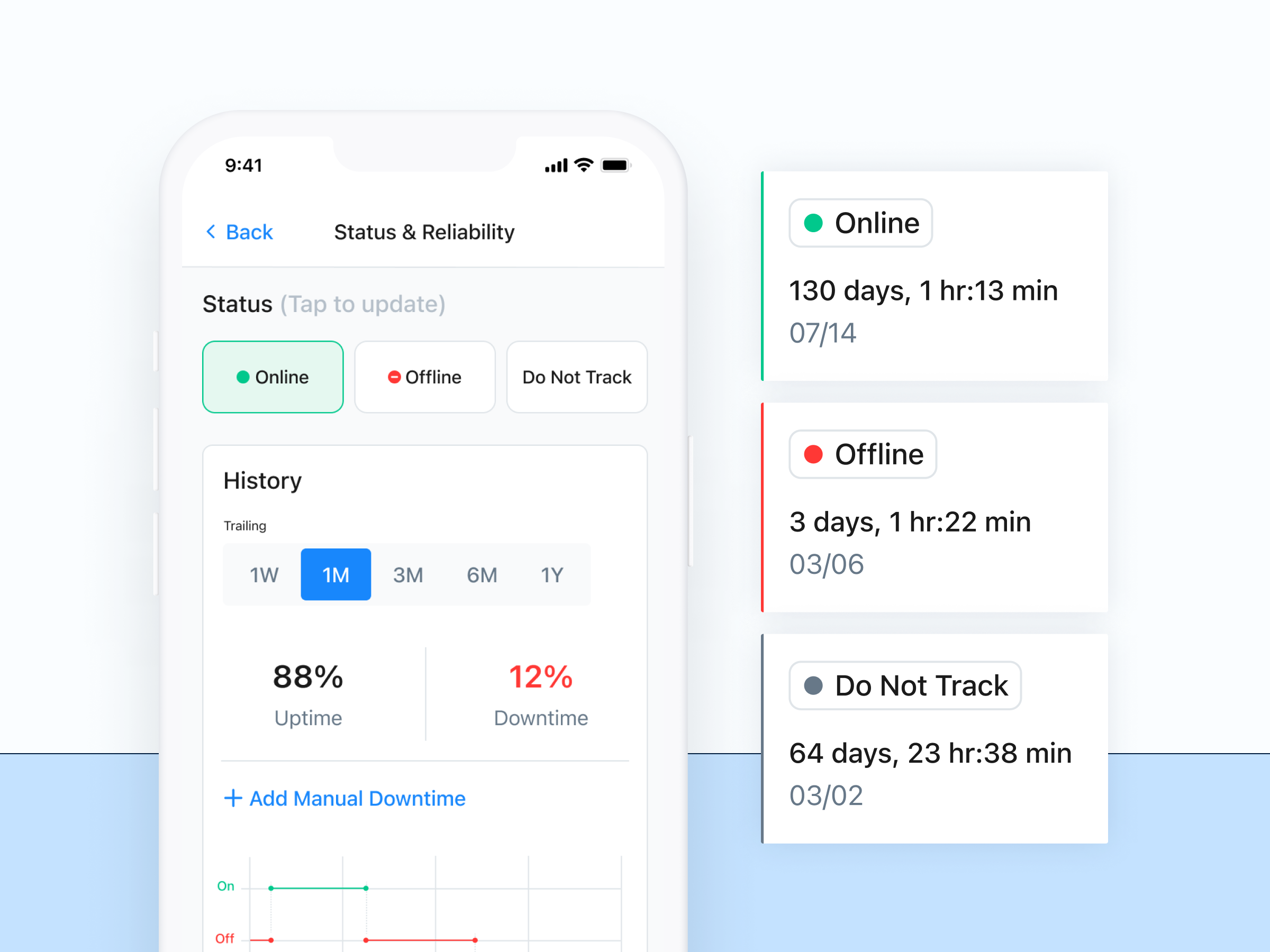
FRACAS in Action
Among various other things, FRACAS helps minimize the Mean Time Between Failure (MTBF) and the Mean Time to Repair (MTTR).
Suppose your electrical breakers are failing. FRACAS can help identify the exact circuit breakers that no longer detect overloaded circuits.
Check the route compliance, and you’ll see a sharp reduction in percentage, signaling that previous inspections were non-compliant.
Benefits of FRACAS
For little additional cost, FRACAS offers multiple advantages. Here are the benefits of FRACAS:
- Increased uptime: Increased availability translates to more revenue by increasing your manufacturing capacity. Monitoring asset status and proactively performing the actions necessary to maximize uptime helps increase the reliability and availability of a piece of equipment.
- Lower costs: It also reduces your per-unit cost by allowing you to manufacture more units. Implementing FRACAS for corrective maintenance also minimizes the need to rework units.
- Better compliance: Equipment failures can sometimes lead to non-compliance with safety or environmental requirements. FRACAS allows for planning for breakdowns and performing corrective actions in a controlled environment instead of a knee-jerk response to failure.
- Lower lifecycle costs: When equipment experiences fewer problems or failures, you save a ton of money. You spend less on spare parts and repairs and increase the asset’s useful life.

Common Mistakes to Avoid When Implementing FRACAS
It’s easy to make mistakes the first time you implement FRACAS. Here are things to keep in mind:
Not Prioritizing Your Goals
Prioritizing goals is vital to deriving the full benefits of FRACAS. For example, if you have a limited budget, start implementing FRACAS to solve the most pressing challenges. Spreading your budget thin leads to issues like inadequate data and improper analysis.
Data Gaps
Data forms the basis of your analysis when implementing FRACAS. Old data is no good, no matter how large the data set is. You need constantly updated, real-time data.
However, collecting real-time data from multiple assets running on the shop floor can take time and effort. CMMS makes data collection easier. It automatically collects data and stores it in the cloud, so your team can access it from anywhere.
CMMS solutions can also automate much of the FRACAS workflow, including data analysis, tracking key metrics, dashboard creation, and failure alerts when a threshold is breached.
Bloated Maintenance Programs
Adding too many maintenance tasks can bloat your maintenance and reliability program. Instead of defaulting to corrective action, prioritize eliminating problems with smarter design, new equipment, and changes in the production process.
Complex System
Complex processes require investment in training and take too much time. Complexity may discourage employees from learning the system. Create an easy-to-use system that your team will view as a way to make their job easier.
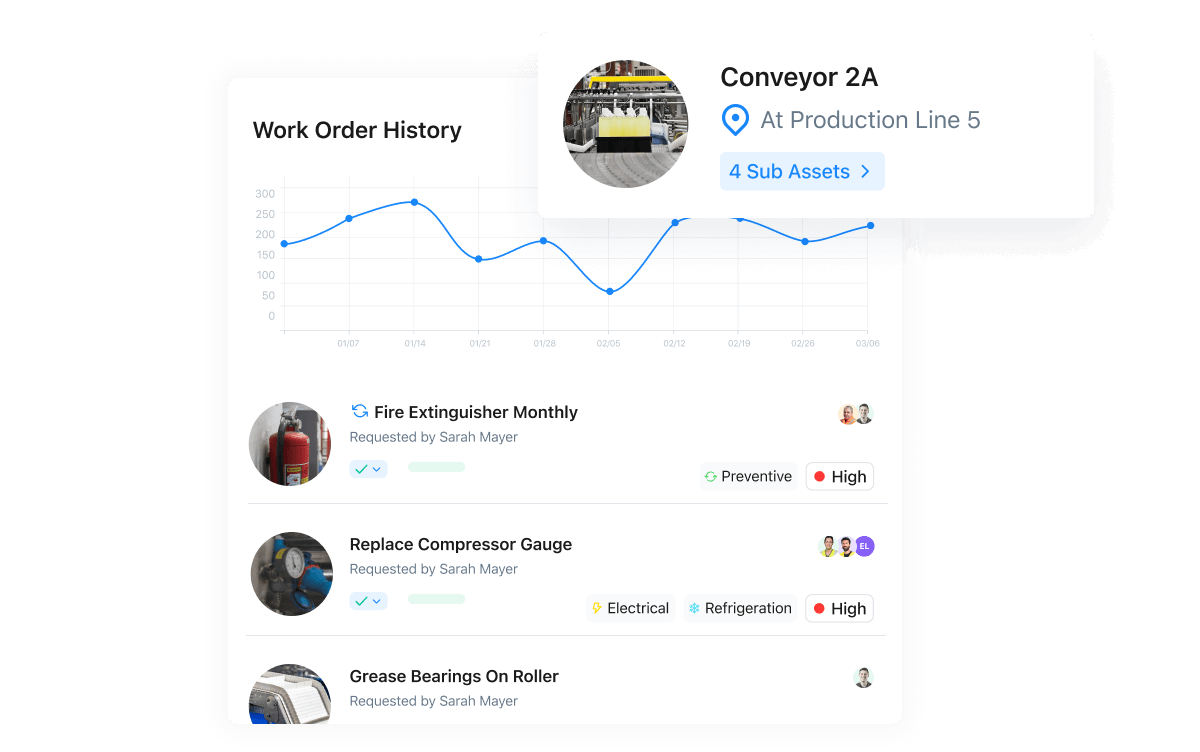
Achieve Peak Reliability with MaintainX
Optimizing preventive maintenance with the FRACAS approach is a big step toward improving system availability. Data collection is a crucial barrier to implementing FRACAS. That’s where MaintainX helps.
MaintainX is a mobile-friendly CMMS that can auto-collect data and automate a large part of the FRACAS process.
If you want continuous improvement, robust asset management, and streamlined maintenance, try MaintainX today!
FAQs
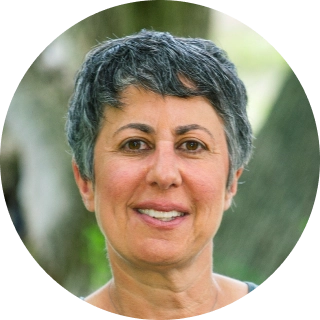
Caroline Eisner is a writer and editor with experience across the profit and nonprofit sectors, government, education, and financial organizations. She has held leadership positions in K16 institutions and has led large-scale digital projects, interactive websites, and a business writing consultancy.