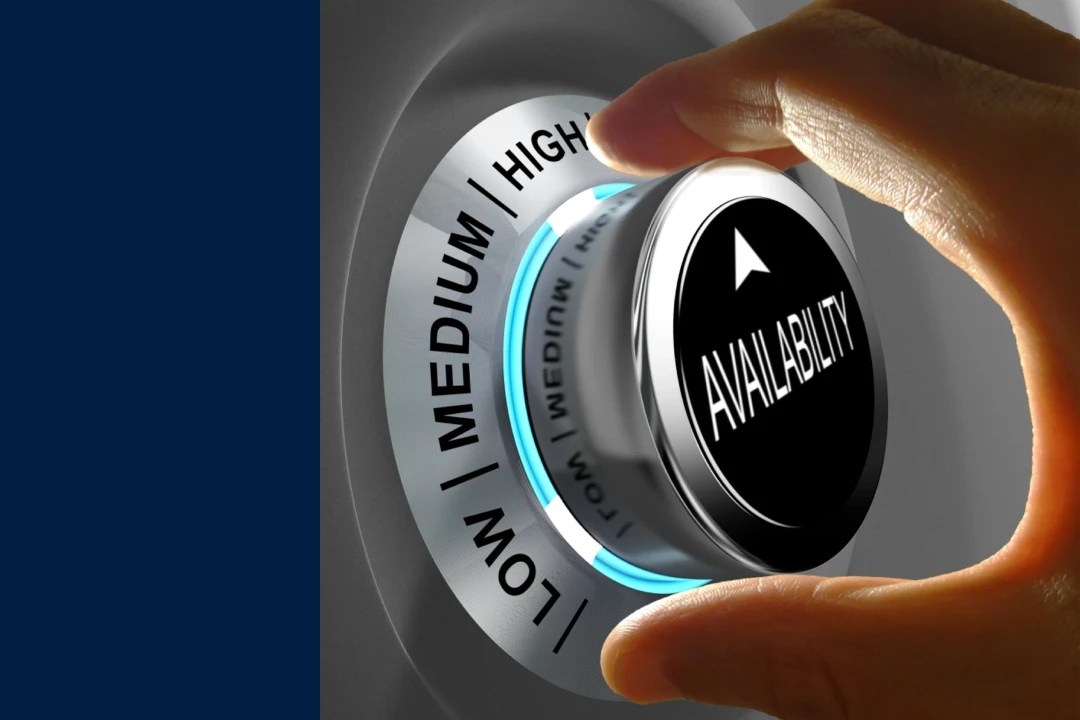
When it comes to maintaining equipment, MTBF (Mean Time Between Failure) and MTTR (Mean Time to Repair) are essential failure metrics to track.
Failure metrics are an excellent tool to gain insights into your maintenance strategy’s effectiveness. They are critical to understanding equipment health and efficiency.
Being able to predict downtime, the time it will take between failures, and the time your team will need to repair failures can help create a strategy that maximizes uptime.
Maintenance metrics frequently monitored include:
- MTBF (the average duration before a failure occurs),
- MTTR (the average time required for recovery, repair, response, or resolution),
- MTTF (the average time until a failure happens), and
- MTTA (the average time taken to acknowledge an issue).
These measures are designed to assist technology teams in determining the frequency of incidents and the speed of their recovery from these incidents.
In this post, we will help you understand how to calculate and improve MTBF and MTTR.
The Difference Between MTBF and MTTR
There are various points of difference between the two, as we explain below.
1. Meaning
The fundamental difference between MTBF and MTTR is that the former measures uptime while the latter measures downtime.
MTBF
MTBF measures the average time between two instances of fixable failures. It factors in the time spent on unscheduled maintenance. Time spent on routine maintenance tasks like inspection and recalibration is considered part of the total life of the asset.
MTBF essentially measures equipment and system availability (or total uptime). It gives you an idea about the equipment’s efficiency, reliability, and failure rate. It’s calculated as the total lifespan of equipment divided by the total failures. The total lifespan excludes time spent repairing the asset, calculated as unscheduled downtime. While you should aim to maximize MTBF, a high MTBF doesn’t mean your equipment won’t break down.
“A high MTBF doesn’t mean that breakdowns will never occur, only that they are less likely to occur. All systems and components have a finite lifecycle, and failures can occur due to a variety of factors, including wear and tear, environmental conditions and manufacturing defects.”
IBM
MTTR
On the other hand, MTTR measures downtime. It gives insights into the average time spent troubleshooting and fixing failures.
If you hear someone talk about mean time to recovery, mean time to resolution, mean time to restore, or mean time to reply—they are all just variations on MTTR, also representing downtime. There are also several incident management metrics that are a subset of MTTR. Examples include:
- Mean time to acknowledge (MTTA): the average time between a failure alert and initiation of action (like creating a service ticket)
- Mean time to detect (MTTD): the average time it takes the team to identify an issue as one that requires corrective action
In this post, we focus on mean time to repair.
MTTR is a crucial indicator of your repairing efficiency and the ability to maintain the business’s systems, equipment, and infrastructure. High MTTR indicates a potential risk of a machine breaking down and impacting your operational workflow.
MTTR is calculated as the total time spent repairing failures divided by the number of repairs.
2. Calculating MTBF Vs. MTTR
Here’s the formula for calculating MTBF and MTTR:
- Mean Time to Failure = (Total lifespan of the asset had it not failed - Unscheduled downtime) ÷ Total number of failures
- Mean Time to Repair = Total time spent repairing ÷ Total number of failures
MTBF and MTTR Calculation Example
Suppose a machine runs 24 hours a day for 10 years. It has four outages per year. The repair time on each of these outages is 10, 15, 20, and 25 hours, respectively.
- Total lifespan = 87,600 hours (24 hours x 365 days x 10 years)
- Unscheduled downtime = 700 hours [(10 + 15 + 20 + 25) hours per year x 10 years]
- Number of failures = 40
The MTBF calculation is: [(87,600 hours - 700 hours) ÷ 40] = 2,172.5 hours
The MTTR calculation is: [700 hours ÷ 40 failures] = 17.25 hours
3. Strategies to Improve MTBF and MTTR
Increasing MTBF and minimizing MTTR can translate to increased productivity and improved efficiency KPIs (key performance indicators). Below are some ways to improve your MTBF and MTTR metrics.
How to Increase MTBF
The MTBF isn’t consistent throughout the asset’s life. As time passes and the asset depreciates, MTBF will start to fall. However, a few tactics can help minimize this reduction in MTBF. Here are some examples:
Use High-Quality Parts
Use the manufacturer’s recommended replacement parts whenever possible during repairs. Alternatively, you can source high-quality replacement parts from third-party vendors. Poor-quality parts can often wear out quickly and, in some cases, cause further damage.
Stick to Your Maintenance Schedule
Consistently being on time with your predictive or preventive maintenance techniques can help minimize unscheduled downtime. Maintenance teams might even detect problems when performing routine maintenance that can lead to failure in the near future.
Study the Root Cause of Failure
Study the root cause after troubleshooting equipment or system failure. Over a period of time, you’ll have a playbook that can inform your maintenance schedule and help prevent these root causes from occurring.
Handle the Equipment Well
Train employees on how to operate the equipment. Rough handling can shorten the equipment’s lifespan. Using the equipment as intended goes a long way in increasing its MTBF and useful life.
How to Decrease MTTR
Restoring equipment or IT systems when they fail directly impacts productivity and revenue. A well-thought-out plan can help restore operations quickly and effectively and reduce your MTTR.
Here’s what you can do to reduce MTTR:
- Monitoring equipment performance: Measuring equipment performance in real-time can shorten the time you need to troubleshoot and assess the problem. The maintenance team can quickly determine the issue based on collected data and directly jump into fixing the problem.
- Create a repairs checklist: Trim unnecessary tasks out of the repair process. Your focus is to get the piece of equipment running again, so streamlining the repair process is critical. Use a repairs checklist to create a standard operating procedure. This will streamline the process for known causes of failure. Checklists can also help assign roles to each technician for the repairing process.
- Train employees: Train employees to use the most efficient repair methods. Practice can help employees gain confidence and perform repairs faster.
- Use asset management and maintenance tools: Asset management and maintenance tools help collect asset data from which you can draw insights. Maintenance applications can collect data on each failure event—how many hours of downtime did it result in? How much time did it take to fix the problem?
CMMS: The Best Way to Manage MTBF and MTTR
Failure metrics enable you to understand the asset’s availability and reliability.
MTBF gives you an idea of the hours of operation you can expect to use the asset for. MTTR tells you the length of time the team needs to repair an asset during which it can’t be used. To increase MTBF and reduce MTTR, you need data.
A computerized maintenance management system (CMMS) can help log and store data on asset performance and work orders throughout the asset’s lifecycle. They can automatically calculate metrics like MTBF + MTTR using the collected data.
MaintainX is a mobile-friendly CMMS designed to improve maintenance efficiency. You can use MaintainX as a central control system to manage maintenance processes. It auto-collects data you can use to optimize your maintenance and repair processes, which in turn helps improve asset reliability.
FAQs
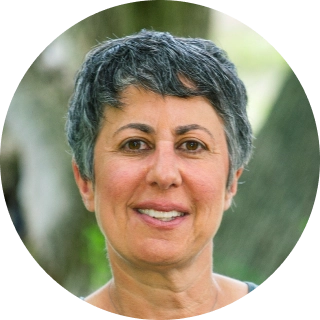
Caroline Eisner is a writer and editor with experience across the profit and nonprofit sectors, government, education, and financial organizations. She has held leadership positions in K16 institutions and has led large-scale digital projects, interactive websites, and a business writing consultancy.