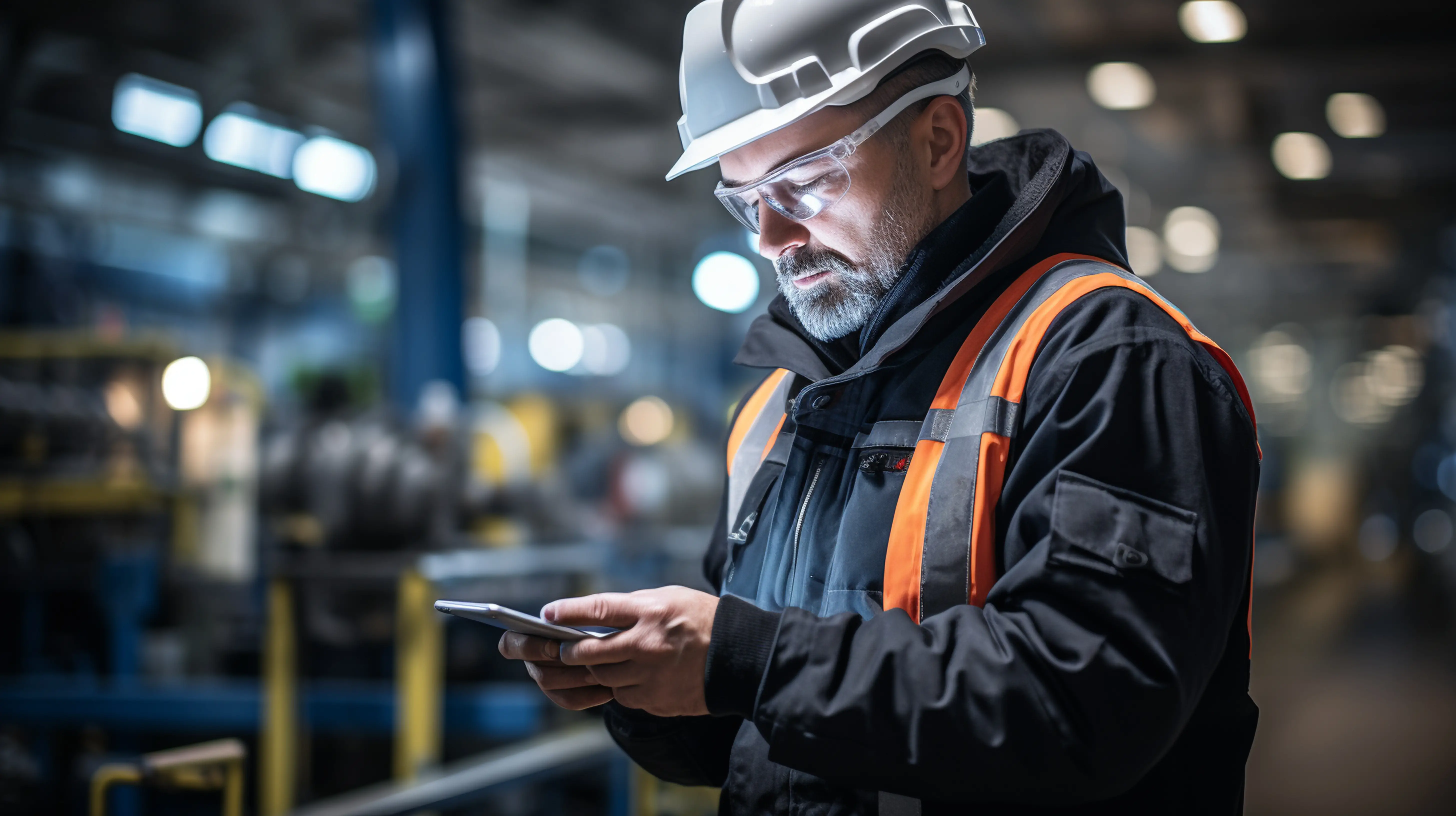
Mean Time Between Failure (MTBF) measures the average time between failures for an asset. It is a maintenance metric that measures how well a particular asset performs under normal operational usage.
For example, operating a piece of equipment at five times its standard capacity will likely lead to problems. So, its performance metrics tell you little about your preventive maintenance efforts except that you overloaded that particular asset at that time.
When thinking about MTBF, it’s essential to keep the following factors in mind:
- The assets in question need to be repairable: i.e., one-off assets are irrelevant for MTBF, and teams should only count failures from which they can recover their assets.
- Maintenance teams need to properly define what counts as an equipment failure. Some teams only consider complete breakdowns, while others consider any malfunction a failure. Similarly, while periods spent deliberately shutting down a machine for routine maintenance count as planned downtime, they don’t necessarily count as assets failing.
Regarding these factors, the right tools are necessary for getting maintenance teams on board with an organization’s approved parameters. For example, using digital standard operating procedures (SOPs) is a great way for teams to establish their failure reporting protocol.
Teams can use work order software like Computerized Maintenance Management Systems (CMMS) to create procedures that allow team members to identify what counts as a failure and record these failures in real time, ensuring they have accurate data for measuring their metrics.
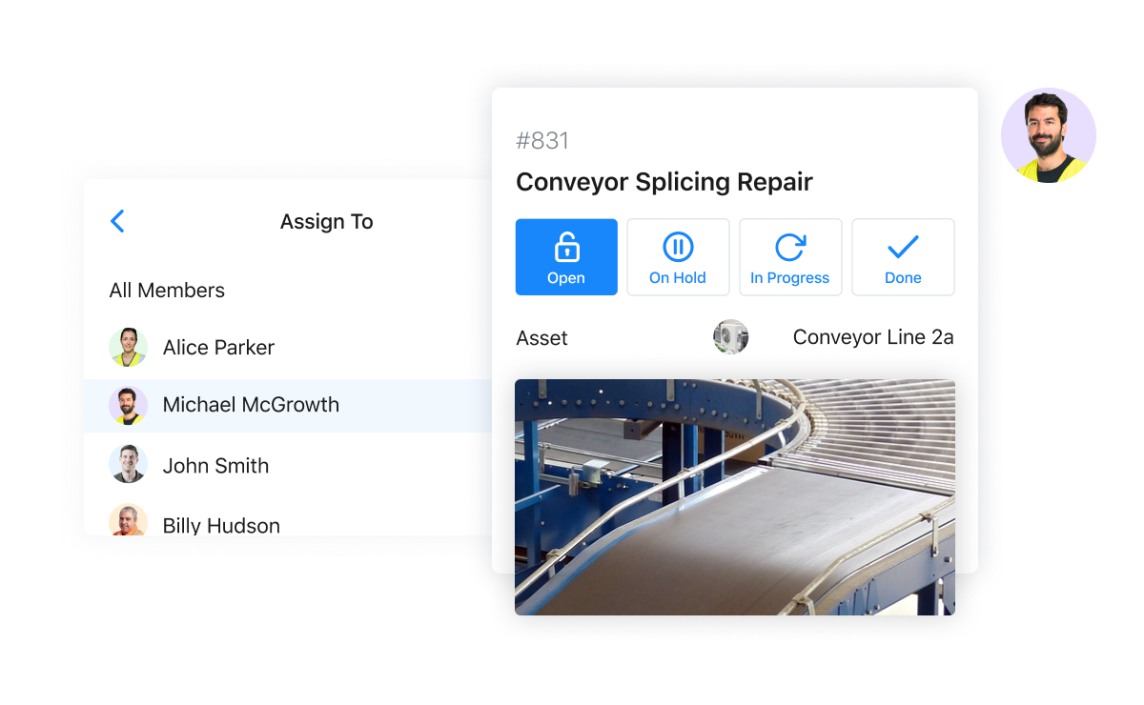
How to Calculate MTBF
To calculate MTBF, sum up the total amount of uptime for a repairable asset during a given period and divide that figure by the total number of failures within the period.
MTBF = Total Uptime of Repairable Asset/# of Failures within given period
For example,
A printer runs for 100 hours and breaks down 20 times. MTBF for this asset in this situation would be 100/20 = 5 hours.
This example illustrates the usefulness of MTBF. You only have to look at the number to notice a problem. Only 5 hours of uptime between each failure isn’t exactly a fantastic performance and likely indicates issues with the machine that teams should address beyond regular repairs.
In such a situation, a root cause analysis would help determine what is wrong with the asset and why the team’s maintenance efforts aren’t yielding lasting results.
“A CMMS is among the best ways to track maintenance KPIs because it lets users create baselines to measure against and reveals opportunities for improvement. If you already use a CMMS, you can likely transform your existing data into measurable insights that help empower data-based decisions and ultimately improve reliability.”
Efficient Plant
Benefits of Calculating MTBF
Optimizes Maintenance
High MTBF figures, despite regular maintenance activities, are a clear sign that a team needs to rethink its maintenance approach. Continuing routine maintenance tasks is counterintuitive when the assets don’t last very long between failure states. MTBF offers an excellent way to identify when a team might need to vary its approach.
Knowing your MTBF also helps to know if these varied approaches are working. For example, imagine a team starts with an MTBF of 5, then conducts a root cause analysis, and then modifies its asset management and maintenance strategy. If the team sees its MTBF increase to 20 hours after this, they have a clear sign that their new maintenance activities are working.
A Computerized Maintenance Management System (CMMS) with a robust reporting module simplifies this process by giving teams access to dashboards with data visualizations and detailed insights.
In addition, MTBF allows teams to schedule condition-based maintenance according to predicted failure states. If an asset regularly breaks down after 10 weeks of routine work, teams must schedule maintenance activities before that time approaches to prevent downtime.
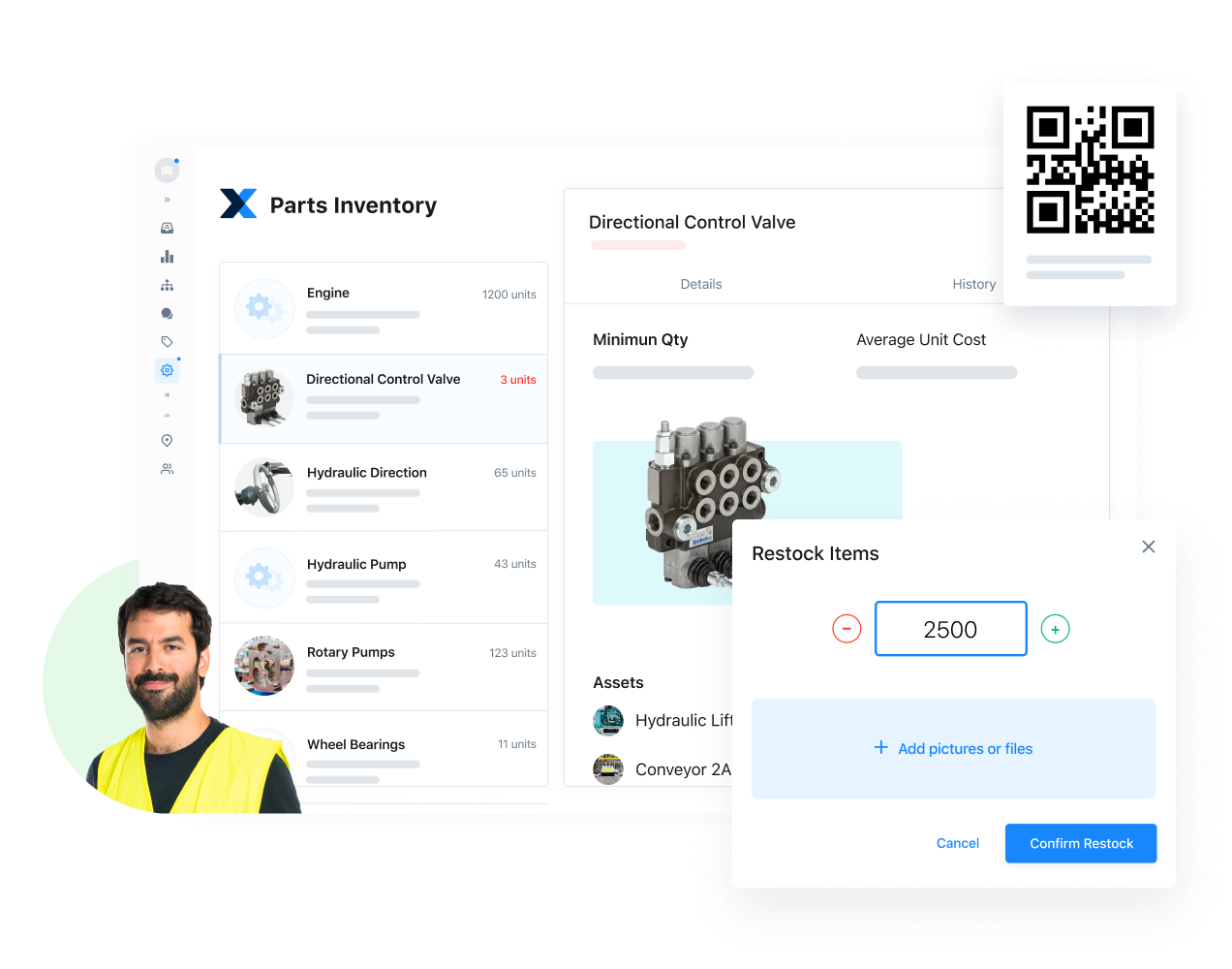
Optimizes Inventory Management
Because teams know, based on past performance, when assets are likely to fail, they can prepare for maintenance work by ensuring they have the necessary spare parts on hand. Instead of stocking these parts and spending more on inventory and storage, they can schedule purchases based on their MTBF calculation and predicted failure states. With the right CMMS solution, teams can automate and schedule their purchases in advance and create automated purchase orders.
Also, not all assets can be saved, and sometimes it costs more money to try to fix something than it would to simply accept it’s come to the end of its lifecycle and replace it. MTBF offers a way to track whether or not assets are improving in performance or deteriorating beyond the point of repair.
Maintenance managers can calculate estimated maintenance costs over projected time periods and weigh these against the cost of replacing the asset entirely.
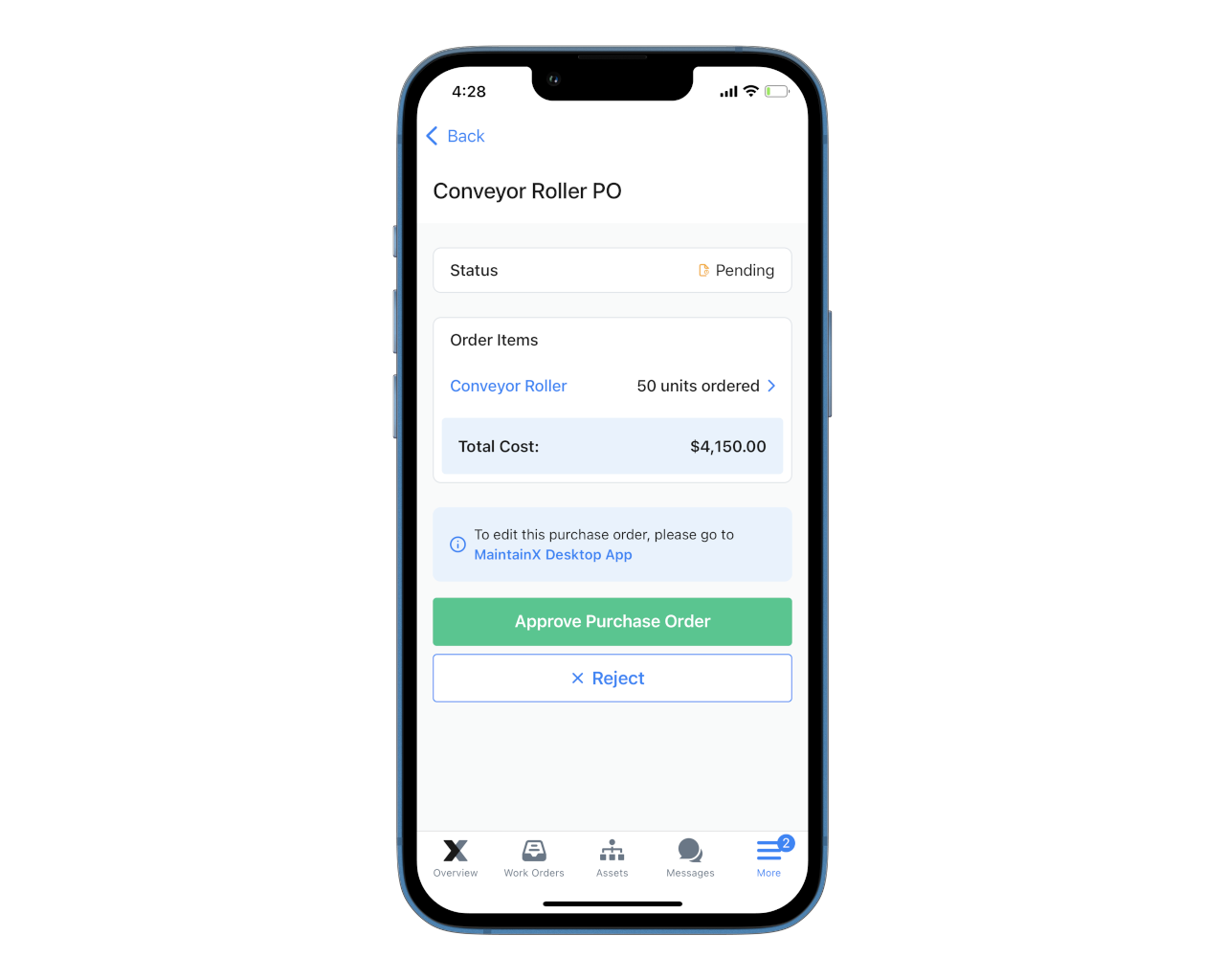
Improve MTBF with a CMMS
If you’re looking to improve not just your MTBF but other metrics and Key Performance Indicators (KPIs) like Mean Time To Repair (MTTR), Overall Equipment Effectiveness (OEE), and downtime, CMMS software is your best bet. Here are a few crucial benefits of using CMMS programs in your maintenance management.
Streamline Data Management
The first step in getting accurate figures for MTBF or any other maintenance metric is collecting data. A CMMS can streamline this process by providing teams with an easy way to record and access data.
With a mobile CMMS, teams can report failures and record real-time failure data right from the shop floor. CMMS software like MaintainX, for example, offers digital standard operating procedures (SOPs) that teams can use to establish standard reporting methods for team members, as well as cloud-based storage, allowing users to store this data and access it from anywhere within the network area.
Schedule Maintenance
Preventive maintenance strategies rely on proper task scheduling. With the information gleaned from MTBF and asset tracking over time, teams can better understand how to organize their maintenance planning. A CMMS system helps teams create and schedule maintenance in advance.
Using CMMS like MaintainX, for example, teams can optimize their maintenance operations with scheduled work orders that notify the assigned technicians once the time approaches. The software also allows teams to store a robust record of their maintenance history, creating digital audit trails that simplify compliance events.
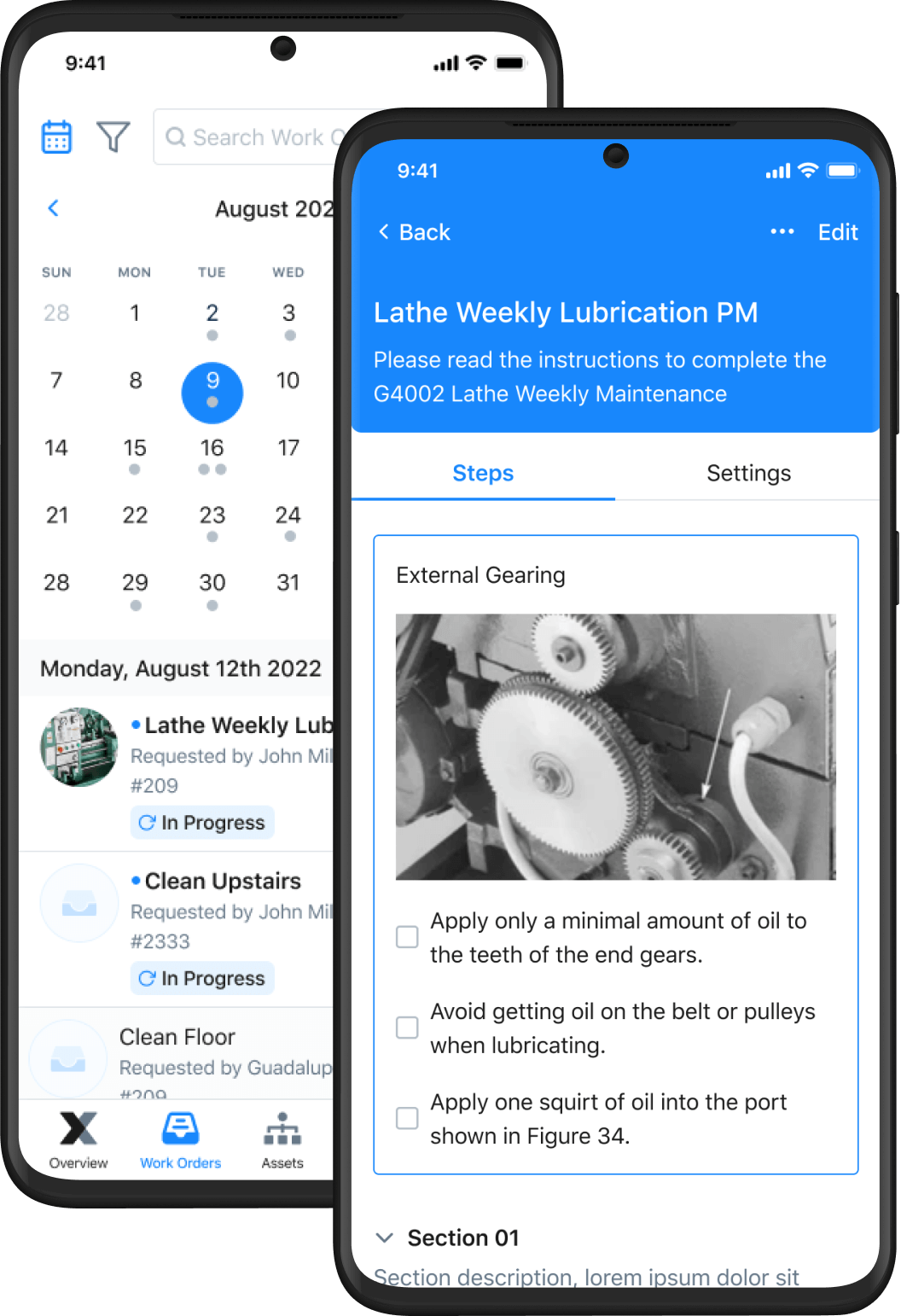
Carry Out Root Cause Analysis
When teams see worsening asset performance despite regular preventive maintenance, it’s a clear sign that they need to change something. Root cause analysis is a method for optimizing maintenance processes by getting to the heart of a problem instead of simply focusing on getting an asset back up and running.
Computerized Maintenance Management Software optimizes root cause analysis by offering robust reporting features, allowing data-driven decision-making. Track your key performance indicators with custom dashboards and data visualizations that provide instant insight into your asset performance.
Track and Improve Maintenance Metrics with MaintainX
If you’ve been thinking about ditching the pen-and-paper and spreadsheet work orders, there’s no better time than now. MaintainX CMMS offers a robust work order management module that streamlines your workflows, optimizes your preventive maintenance, and helps reduce downtime.
FAQs
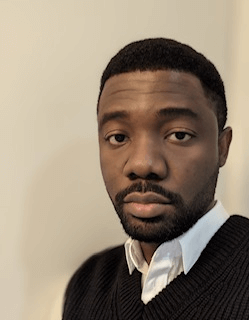
Lekan Olanrewaju is a content writer with years of experience in media and content creation. He has held positions at various media organizations, working with and leading teams at print magazines, digital publications, and television productions.