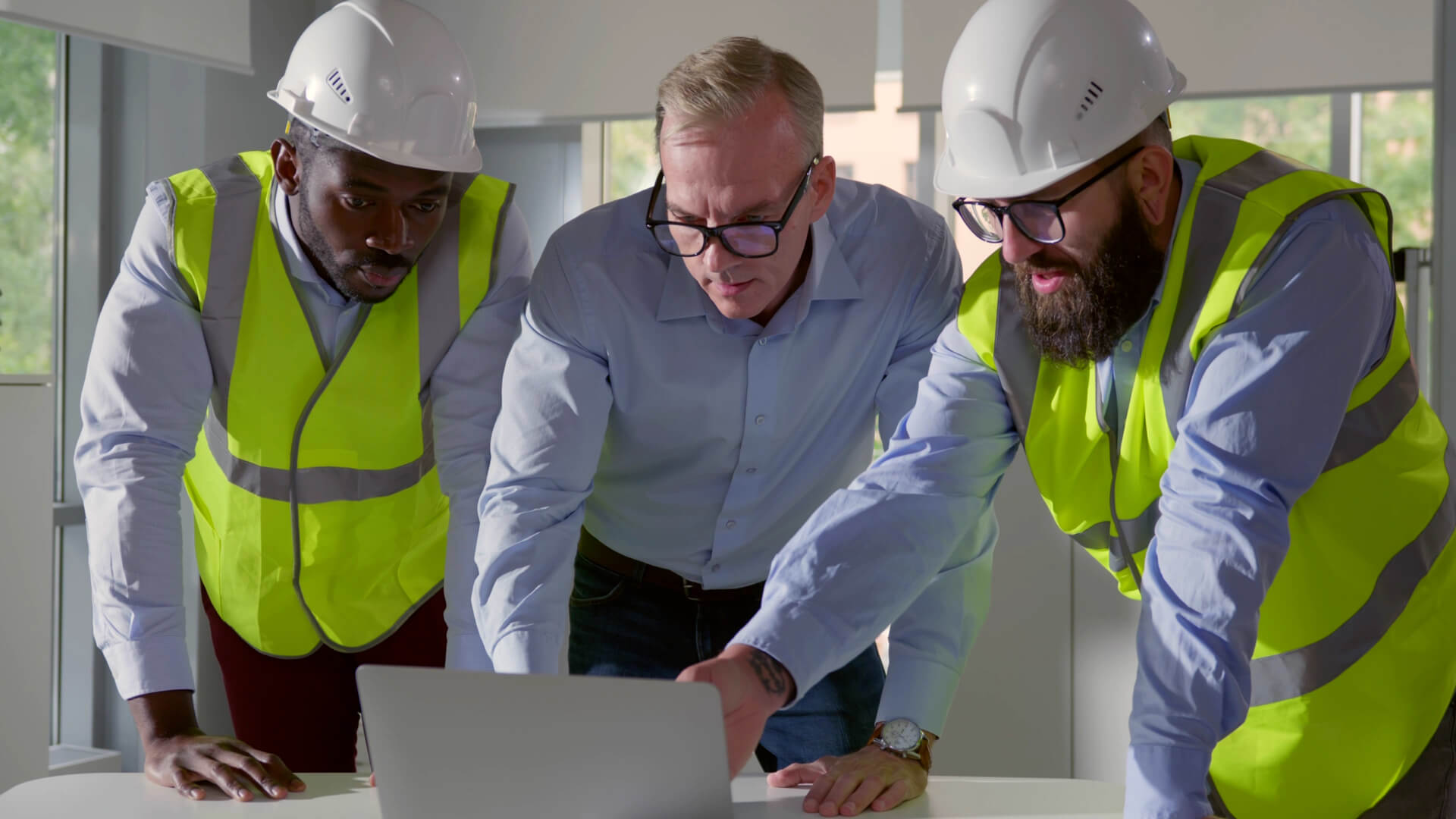
Equipment management in manufacturing plays a crucial role in ensuring the efficiency and profitability of a manufacturing unit. They involve the entire useful life of your manufacturing equipment. What maintenance strategy do you adopt? How do you manage your physical assets? How do you ensure asset performance? The answer to these questions and more will depend on equipment management.
Equipment management helps companies optimize their equipment utilization and reduce downtime. In addition, they help align your equipment management with your organizational objectives. But before we explain, let’s take a closer look at what equipment management means.
“One of the most important things that enterprises today need to understand about asset management—as both a concept and a practice—is that it’s about more than simply maintaining and caring for physical assets. In fact, the scope of asset management is in many ways closely aligned with an organization’s central purpose.”
C. Phillips
What Is Equipment Management in Manufacturing?
Equipment management in manufacturing refers to the processes, systems, and strategies a company uses to effectively and efficiently manage its manufacturing equipment. As a result, companies can utilize these fundamental principles to achieve their operational goals and stay ahead in the market.
Equipment management in manufacturing typically includes:
- Equipment Maintenance: Regularly check and repair equipment to ensure optimal performance and equipment lifecycle costs.
- Equipment Monitoring: Continuously monitor equipment performance to identify potential issues and take corrective action.
- Equipment Management: Track equipment use, location, and performance for decision-making about its deployment, replacement, or disposal.
- Equipment Optimization: Improve the utilization and performance of equipment to maximize value and minimize downtime.
IIot Equipment Management
Maintenance management processes in the Industrial Internet of Things (IIoT) is all about using connected devices, sensors, and analytics to improve equipment management in manufacturing and other industrial settings. The IIoT allows companies to collect real-time measurable data on equipment performance and condition and use it to improve the efficiency and effectiveness of their maintenance operations.
With the IIoT, companies can monitor equipment in real-time, carry out predictive maintenance, improve asset utilization, and enhance safety.
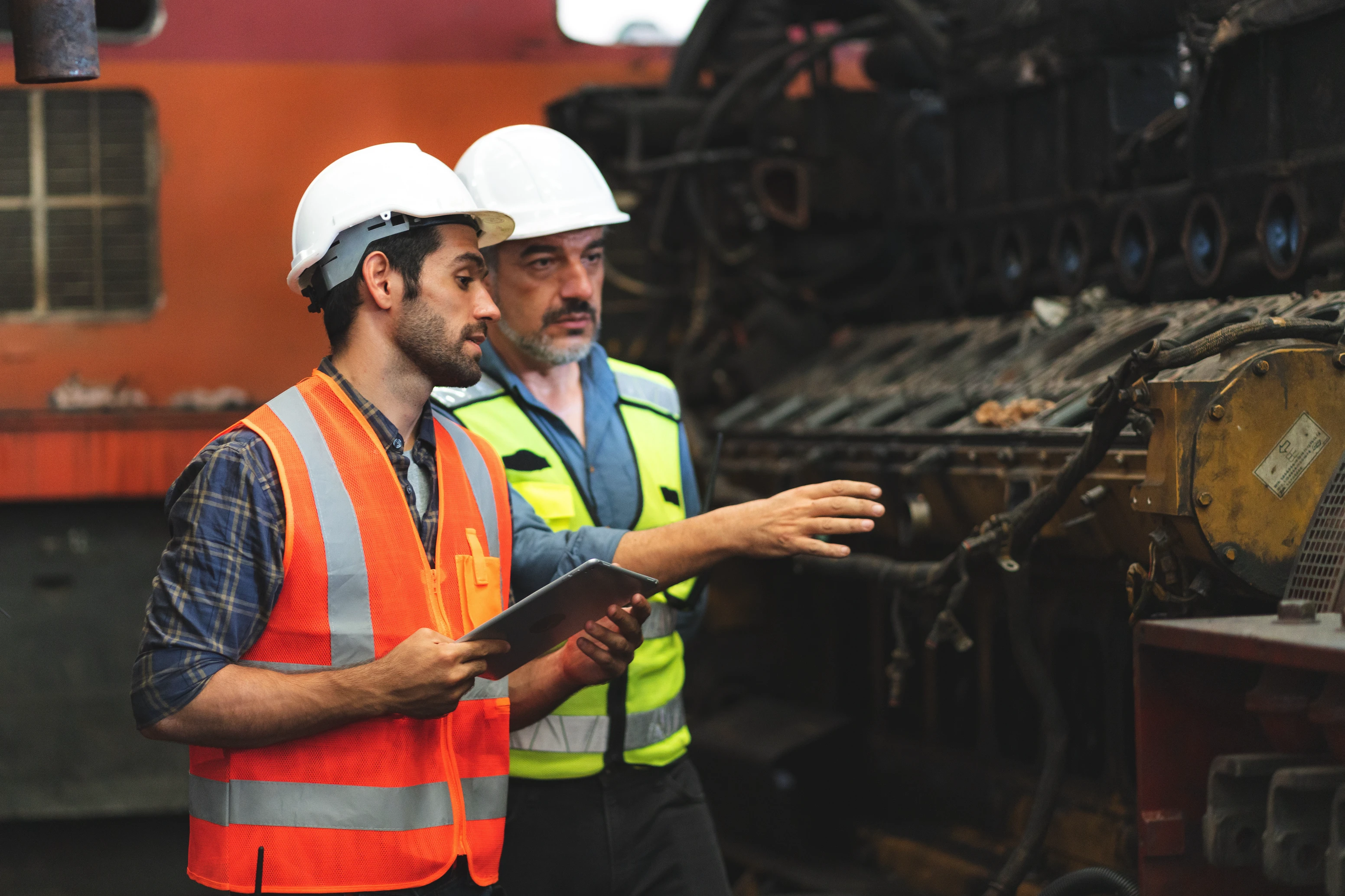
Equipment Management Strategies
We’ve looked at equipment management in manufacturing and the IIot, but what underlying plan guides these operations?
The four equipment management plans are Reliability-Centered Maintenance, Predictive Maintenance, Total Productive Maintenance, and Condition-Based Maintenance. As you can already tell, they center on maintenance.
Maintenance is paramount for every manufacturer. You’ll have to consider factors such as your business, asset types, and industry standards. Consider these plans and how they can help with effective asset management.
Reliability-Centered Maintenance
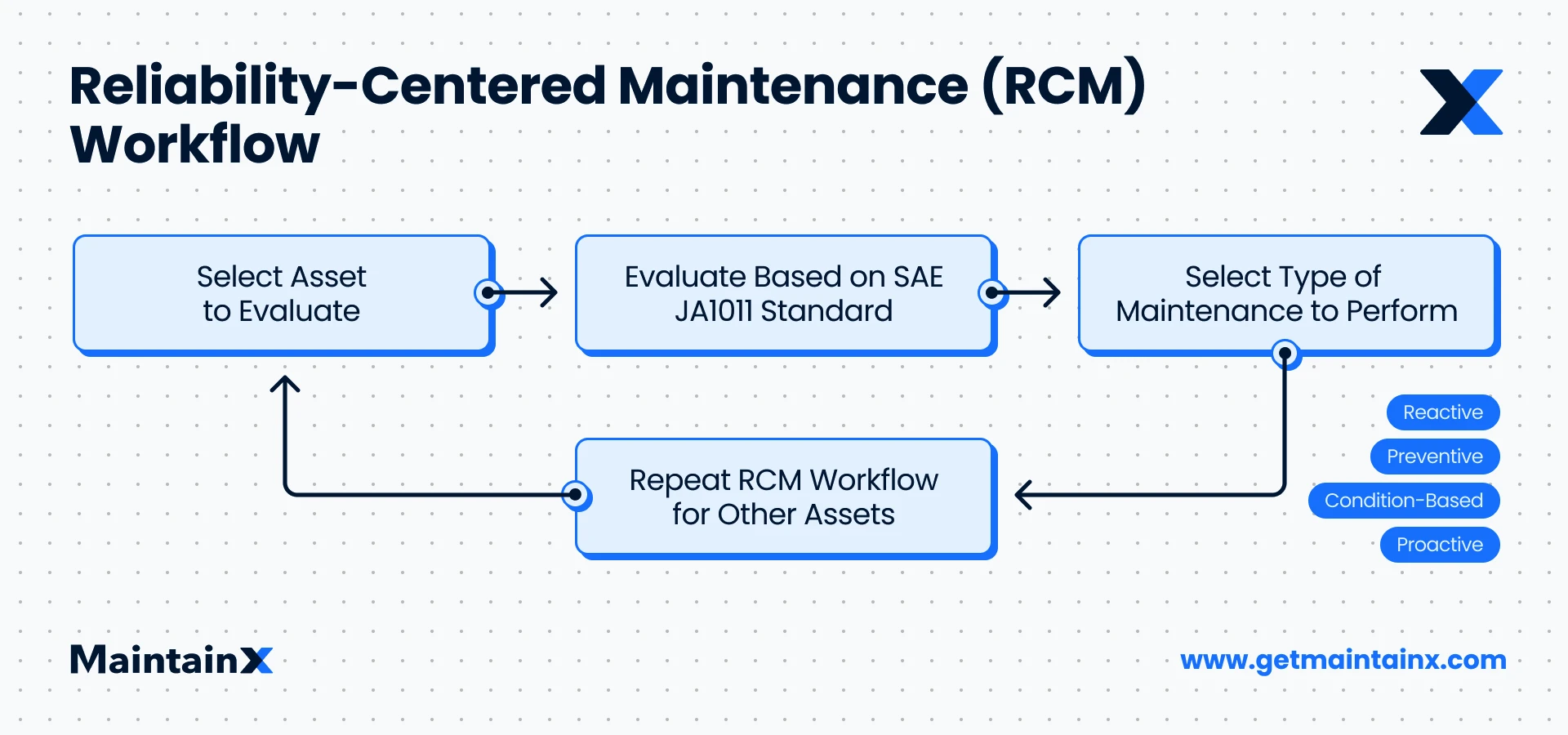
Reliability-Centered Maintenance (RCM) is a maintenance strategy that maximizes the reliability and availability of equipment. It focuses on productivity, minimizing the likelihood of unexpected equipment failure. Using risk-based management analysis, you can apply this plan in the manufacturing sector by identifying critical equipment, determining their potential failure modes, and creating maintenance plans.
Predictive Maintenance
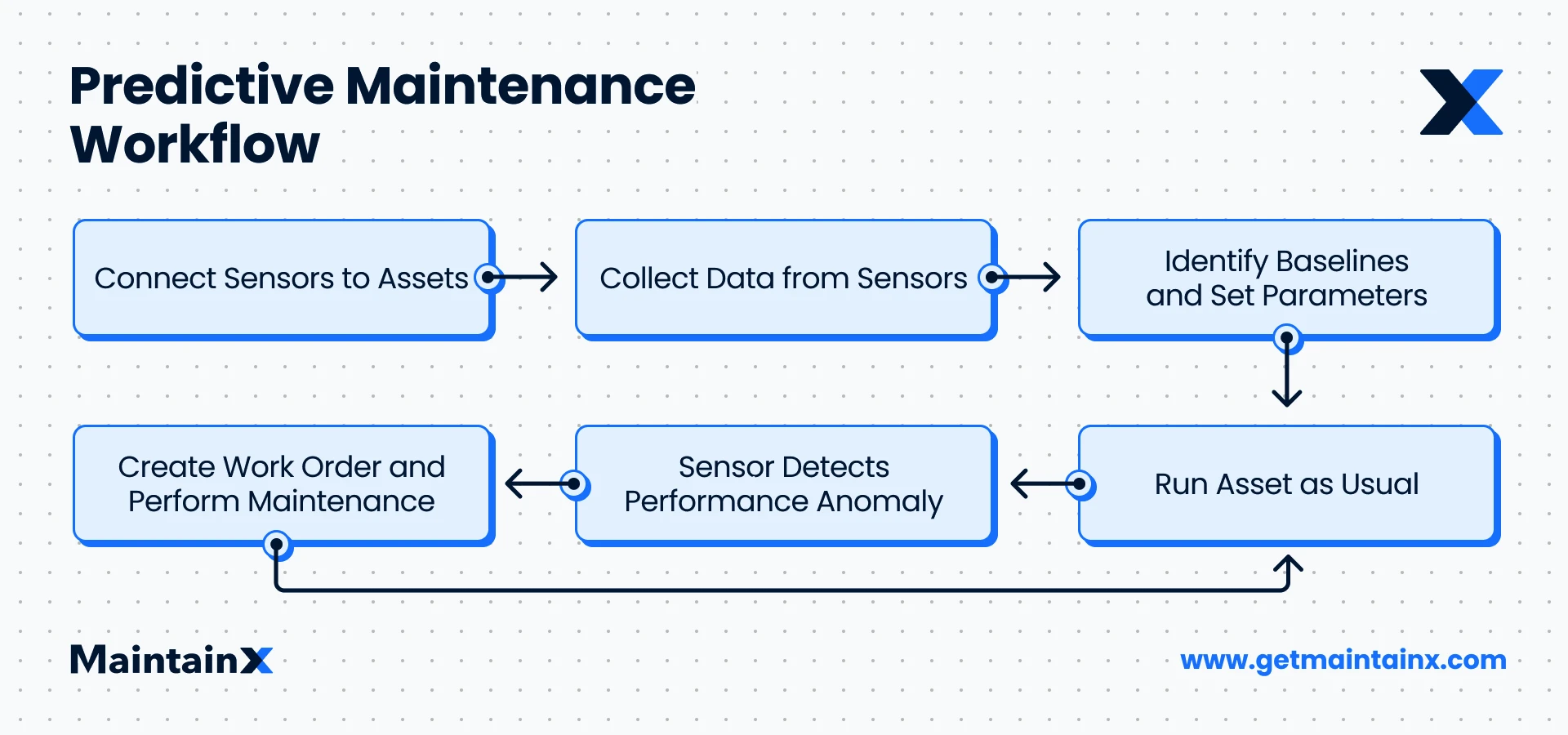
Predictive maintenance (PdM), a type of risk management, is a proactive maintenance strategy that uses data and analytics to predict when an asset is likely to fail. The data enables maintenance teams to schedule maintenance activities in advance, reducing the likelihood of unexpected downtime. For example, in the manufacturing sector, teams can use sensors and other technologies to collect data on the performance of assets. Then, these teams can analyze this data, identify trends, and predict when maintenance is needed.
Total Productive Maintenance
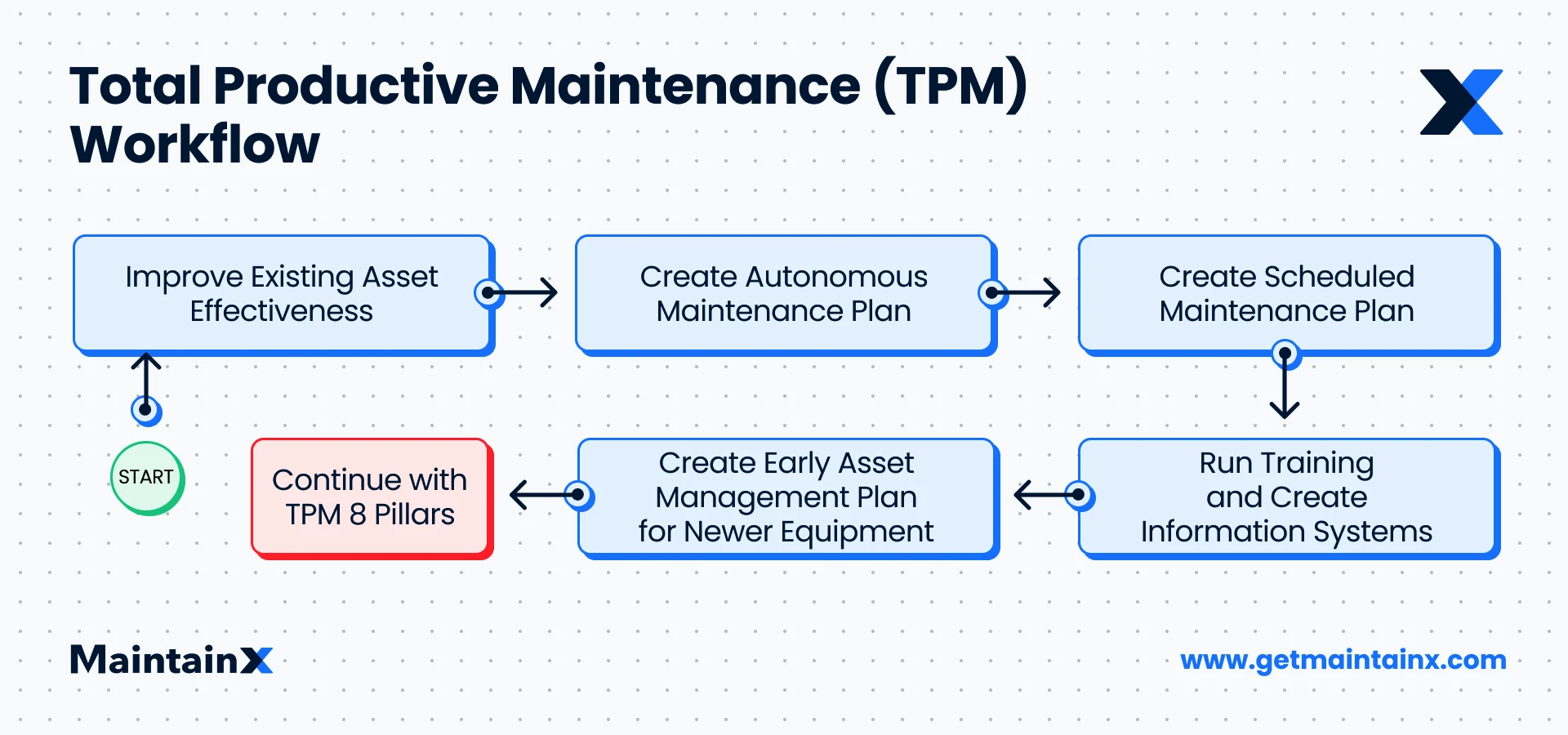
Total Productive Maintenance (TPM) is a maintenance strategy that involves all employees in the maintenance process. This approach focuses on improving an organization’s Overall Equipment Effectiveness (OEE). Companies can apply this plan in the manufacturing sector by training employees in maintenance best practices, encouraging them to be proactive in identifying potential issues, and providing them with the tools and resources they need to perform maintenance activities.
Condition-Based Maintenance
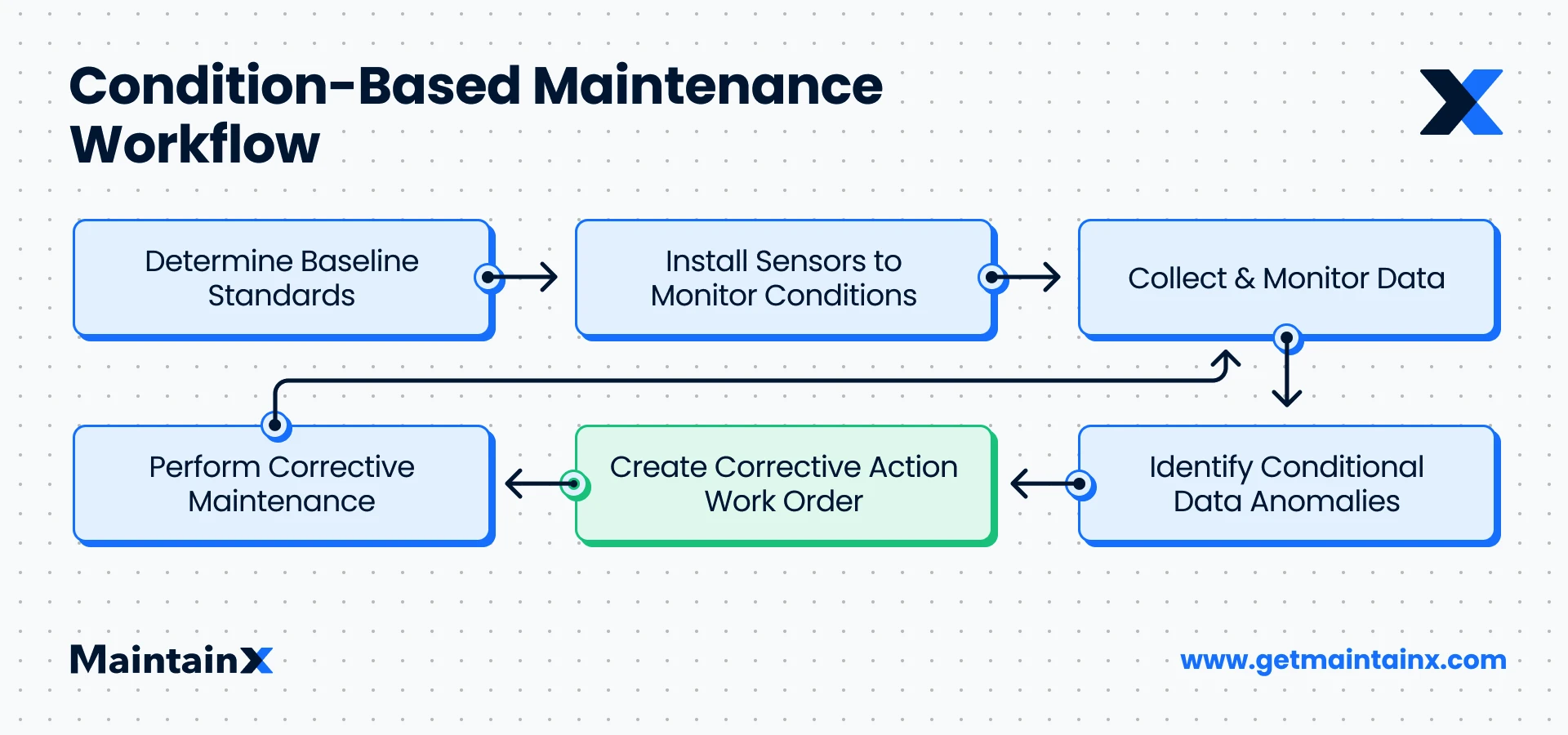
Condition-Based Maintenance (CBM) is a strategy that monitors equipment conditions to perform maintenance activities only when needed. This helps reduce maintenance costs and downtime. For example, in the manufacturing sector, companies can install sensors and other IIoT technologies to detect changes in equipment conditions and determine when maintenance is required.
CMMS and Equipment Management Strategies
Computerized Maintenance Management Systems (CMMS) are software tools that help companies manage their maintenance operations, including asset management. A CMMS can assist in the implementation of various equipment management in the following four ways:
- Equipment Management and RCM: A CMMS can help your organization implement RCM by storing historical data on asset performance and maintenance activities. You can then analyze this data to identify critical equipment and potential failure modes, which can inform the development of a maintenance plan.
- Equipment Management and PdM: A CMMS can collect and analyze data from sensors and other technologies to predict when an asset is likely to fail. Manufacturing teams can then use this information to schedule maintenance activities in advance, reducing the likelihood of unexpected downtime.
- Equipment Management and TPM: A CMMS can support TPM by providing employees with access to maintenance best practices and training materials. The software can also provide tools and resources to help employees perform maintenance activities more effectively.
- Equipment Management CBM: A CMMS can help companies implement CBM by monitoring the condition of assets and triggering maintenance activities based on data collected from sensors and other technologies. Acting on this data will help reduce the cost of maintenance and minimize downtime.
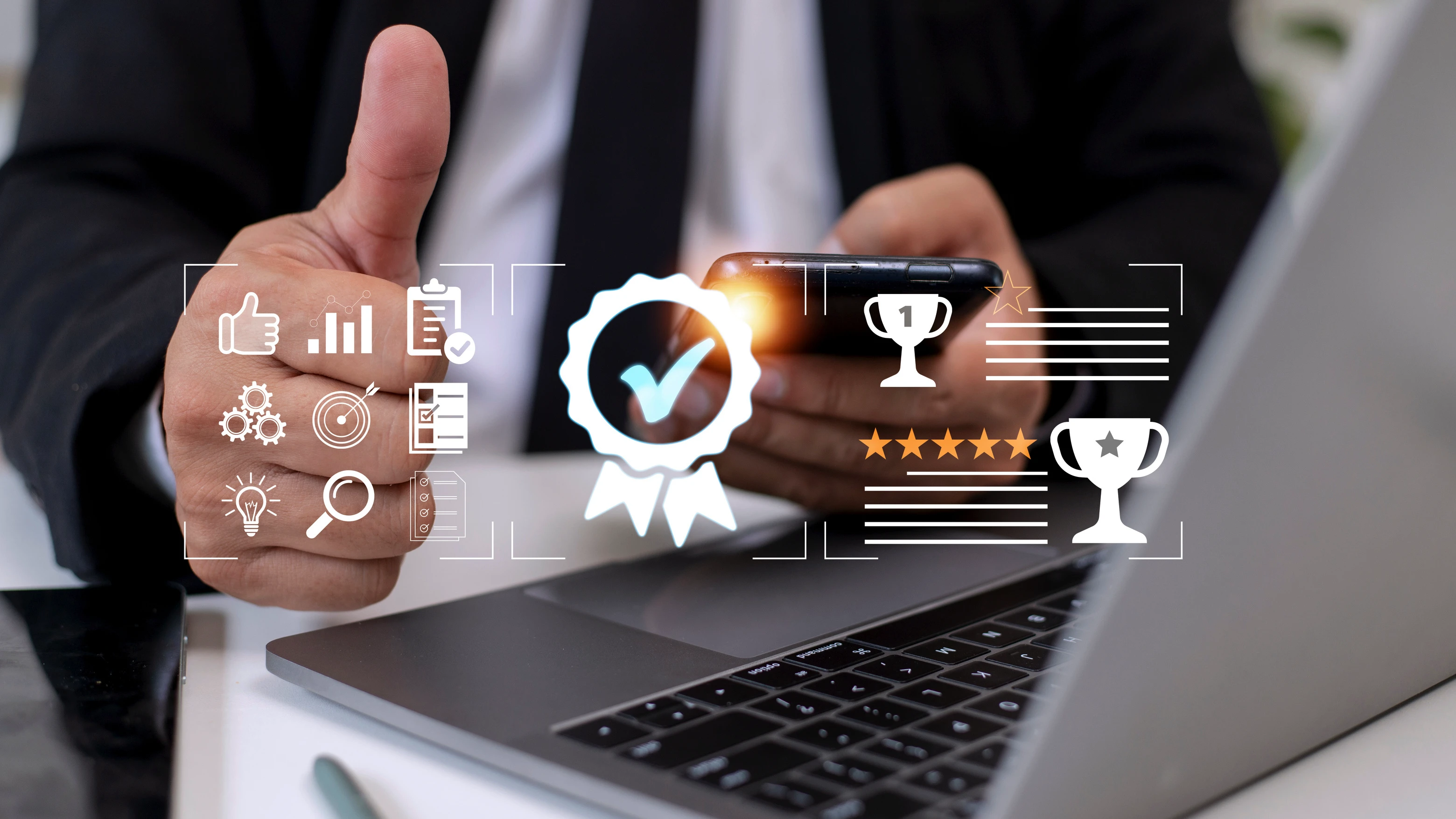
Benefits of CMMS Equipment Management
We’ve seen how a CMMS can help with executing your asset management strategy and key principles, but let’s consider the potential benefits of these asset management principles to your business.
Improved Asset Utilization
A CMMS can provide real-time data on the performance and condition of equipment, allowing companies to optimize their utilization and reduce downtime. This can help improve production and profitability.
Predictive Maintenance
CMMS solutions can use predictive analytics to forecast when an asset will fail. With this knowledge, you can schedule maintenance activities in advance. This helps to reduce the likelihood of unexpected downtime and improve the efficiency of maintenance operations.
Better Maintenance Planning
A CMMS can help companies plan and schedule maintenance activities more effectively, reducing the likelihood of unexpected downtime and improving the efficiency of maintenance operations. Furthermore, equipment management allows you to optimize lean techniques, such as reducing waste and DOWNTIME, while increasing useful life cycles and sustainability of resources.
Improved Inventory Management
A CMMS can help companies manage their inventory more effectively, reducing the likelihood of stockouts and ensuring that the correct parts are available when needed. For example, you can create inventory work orders and set them to repeat at intervals. You can also automate your procurement and purchase orders.
Better Data Management
A CMMS, like MaintainX, provides a central repository for all maintenance-related data, making accessing and analyzing key performance indicators easier. In addition, MaintainX works as both a web and native-first mobile app. As a result, workers and stakeholders can make real-time informed decisions about asset management processes and your levels of service.
Compliance with Industry Regulations
A CMMS can help companies meet industry regulations by providing real-time data on the condition and performance of equipment. In the event of compliance checks, this data is necessary for audits and independent verification.
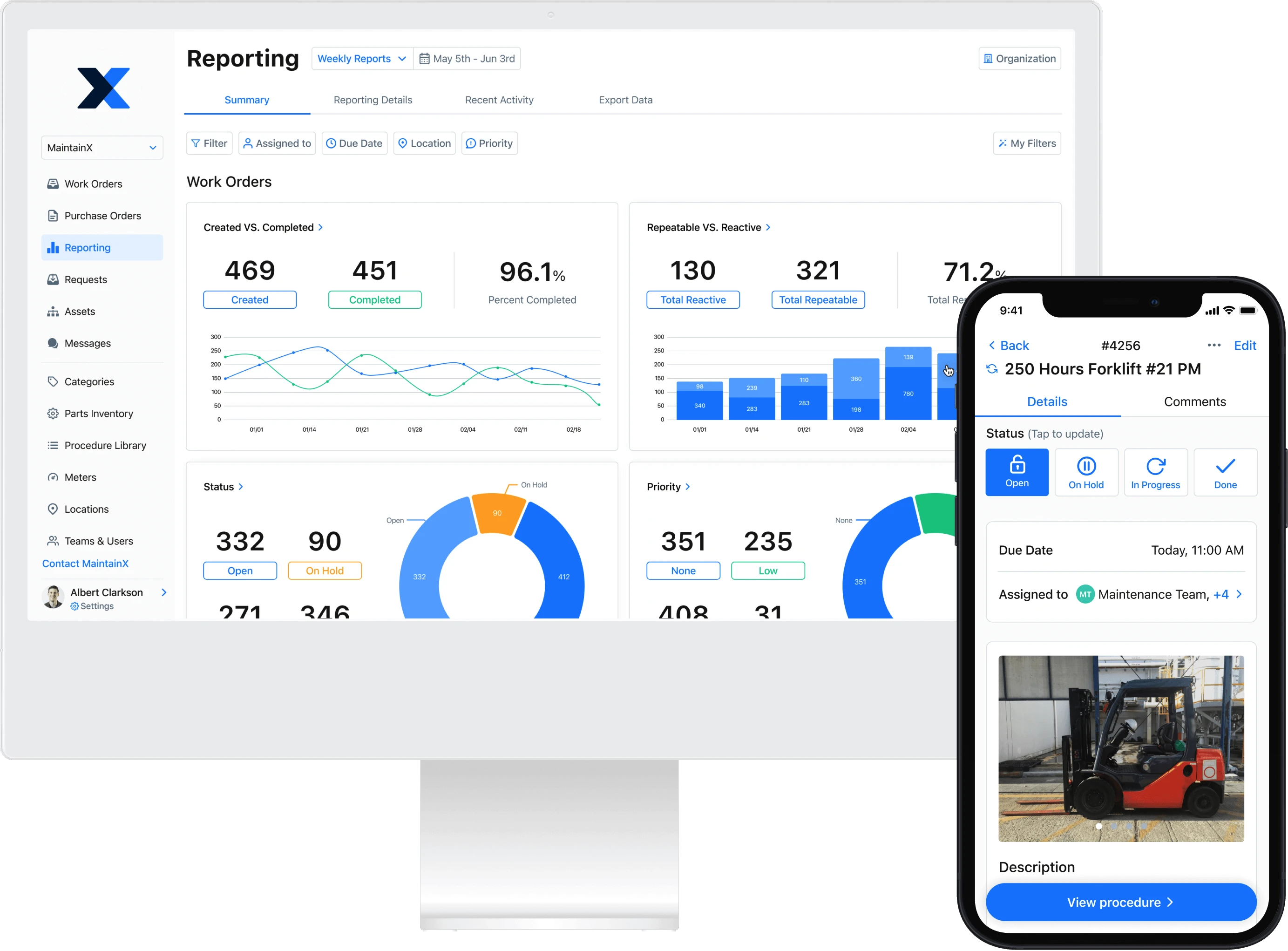
Manage Your Equipment with MaintainX
MaintainX is a CMMS system that helps simplify your maintenance processes. As you improve your equipment management, you will better understand the impact of your investment strategy. In addition, you’ll benefit from MaintainX’s range of features and how they can help improve the financial performance of your assets. For example, MaintainX can help manage your vendor partnerships, team communication, and SOP efficiency.
MaintainX will help you track your assets, establish and fine-tune your Standard Operating Procedures (SOPs), and improve maintenance efficiency. Check out MaintainX today.
FAQs
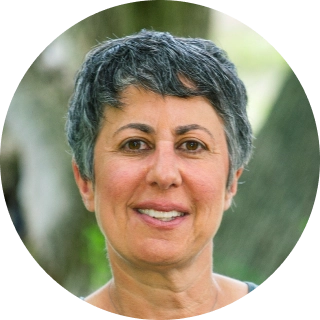
Caroline Eisner is a writer and editor with experience across the profit and nonprofit sectors, government, education, and financial organizations. She has held leadership positions in K16 institutions and has led large-scale digital projects, interactive websites, and a business writing consultancy.