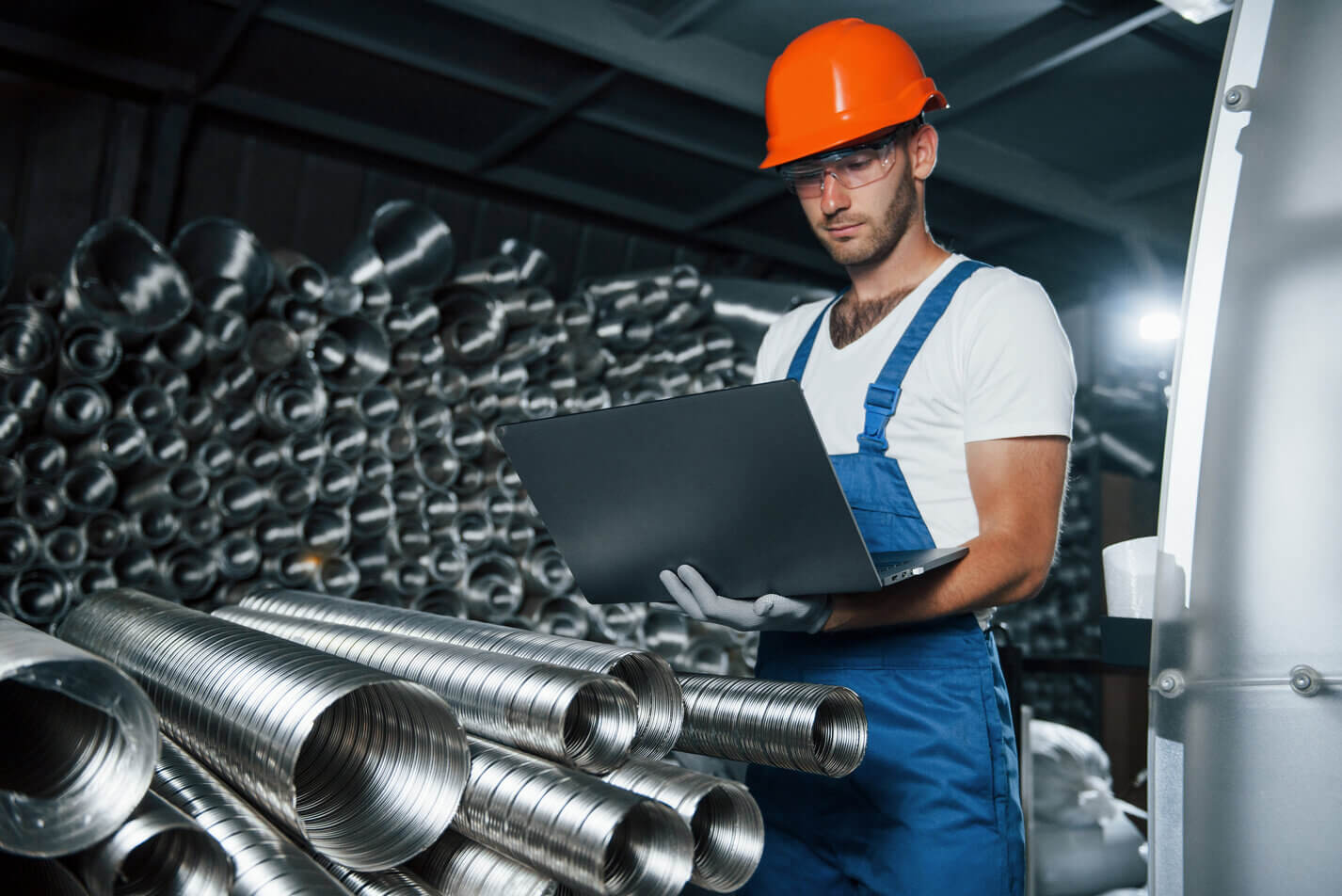
The manufacturing industry is huge: the National Association of Manufacturers reports that US manufacturing output topped an incredible $2.89 trillion in 2023. Every day, sectors from chemicals to electronics rely on strategic manufacturing processes to meet increasingly demanding production requirements.
Today, customers don’t only expect reliable, high-quality products from manufacturers—they also expect almost real-time delivery. As a result, production efficiency is paramount. In addition, recent global supply-chain issues have further incentivized the manufacturing sector to reevaluate processes, procedures, and policies for greater reliability and economic resilience. However, manufacturers must balance this with quality and safety.
To meet these needs, organizations can adopt different types of manufacturing processes depending on their products, their goals, and how their industry operates. In this article, we’ll talk all about the manufacturing process—the different types, potential challenges, and how manufacturers can streamline their approaches.
What is a manufacturing process?
Manufacturing is the process of making products on a large scale using machinery, skilled workers, or a combination of both. A manufacturing process refers to the specific approach a manufacturer applies to accomplish this. Depending on the product and organization, manufacturing processes can range from surprisingly simple to exceedingly complex.
The number of steps involved in any process depends on several factors, such as consumer demands, equipment required for assembly, and internal standard operating procedures (SOPs).
It’s worth mentioning that many individuals use the terms processing and manufacturing interchangeably. Though similar in meaning, there are some slight differences between them.
Common steps in the manufacturing process
While each manufacturer’s step-by-step process will vary based on methods used and what is being manufactured, most follow a similar flow:
- Research, market analysis, and price analysis
- Product design and prototyping
- Procuring raw materials and production planning
- Processing raw materials into components
- Assembly or fabrication of finished goods
- Quality control and testing
- Packaging, shipping, and distribution
In some cases, manufacturers will collapse multiple steps into one, while others might break one step into multiple. Let’s consider what these steps look like in practice.
Manufacturing process example: Laptop manufacturing
Let’s talk about how a laptop could be manufactured. A laptop manufacturer’s process may start with customer research, competitor analysis, and identifying how they can offer a comparable product at a cheaper price point.
Engineers and product development teams will then draft designs for a new laptop and make prototypes to ensure all the parts fit together precisely. After succeeding here, the next stage is inventory management. The manufacturer will procure necessary raw materials in bulk, including circuit boards, aluminum casings, and more. Next comes the production line in the factory where the manufacturer assembles these materials into finished goods according to a bill of materials.
Then testing occurs, which may include software and functionality testing and safety checks to ensure the product meets the necessary standards. Once the product is finished, it is packed and shipped to the company’s distribution network.
The eight types of manufacturing processes
There are many types of manufacturing processes, and each approach has benefits and drawbacks. Organizations need to take a holistic view of their market. To find the optimum manufacturing technique for your business, consider factors like the availability of raw materials, capital equipment costs, and staff skill levels.
In some cases, a combination of processes provides the best cost/benefit outcome for high-volume production, while in others, production methods are relatively fixed.
For example, fresh fruit juice processing is dictated by the seasonal availability of raw ingredients, and production managers should consider this when deciding on manufacturing methods.
1. Repetitive manufacturing
Repetitive manufacturing involves continually producing products of identical quality and quantity. It’s ideal for manufacturers looking to achieve a given production rate.
For example, say a facility wants to produce 50,000 bottles of water per hour. With minimal requirements and changeover, the manufacturer can adjust its assembly line’s production speeds based on consumer demands. Manufacturers of durable consumer goods (e.g., refrigerators, dishwashers, and dryers) often use repetitive manufacturing.
2. Discrete manufacturing
Like repetitive manufacturing, discrete manufacturing uses assembly lines for production.
However, this manufacturing method provides organizations with a greater degree of diversity.
Manufacturers can organize assembly line systems for product changeover frequencies. This means they can produce a more significant variation of product designs, qualities, and quantities. However, discrete manufacturing takes more time to set up.
Sectors that rely on this option include automakers, aircraft, clothing, smartphones, and toy manufacturers.
3. Continuous process manufacturing
Continuous process manufacturing is similar to repetitive manufacturing. However, it’s limited to products made from raw materials like liquids, gases, and powders. The sectors known for using this type of manufacturing include paper production, metal production, and oil refining.
Companies that make food products such as peanut butter, tomato sauce, and fruit juices also use continuous process manufacturing.
4. Batch process manufacturing
Batch process manufacturing is driven by the availability of raw materials or market demands. Once a batch is produced, machine operators clean production equipment in preparation for the next batch. The timing and scheduling of batch production usually align with customer demand.
Products manufactured through batch process manufacturing include newspapers, pharmaceuticals, and books, as well as food production.
5. Job shop manufacturing
This manufacturing process uses production areas or distinct workstations instead of assembly lines. Companies make customized products in small batches according to customer orders or sales forecasts.
Examples of job shop manufacturing include commercial printing presses and customized shoemaking. In addition, job shop manufacturing can be automated and converted to discrete or repetitive manufacturing when driven by demand.
6. Mass production
Mass production refers to the continuous production of substantial amounts of standardized products in a constant process. Large factories with assembly lines, such as car manufacturers and soda bottlers, use mass production techniques to reduce the overall unit cost of each product by ordering raw materials in bulk for a cheaper price.
Efficiency is key to gaining the benefits of mass production — aside from the benefits to the organization, cost-effective products are more affordable and accessible to consumers.
Automotives, electronics, clothing, and many other consumer goods are mass-produced using this repetitive, ‘flow production’ approach.
7. Mass customization
This approach combines the benefits of mass production with the ability to adapt products to meet individual customer requirements. This helps businesses balance the cost savings and operational efficiency of the mass production approach, but still offer tailored products to their customers.
Businesses can offer made-to-order features of a product while still keeping manufacturing costs similar to that of mass-produced products.
Any product that offers a choice of colored elements, modular add-ons, or mix-and-match options may be manufactured using mass customization, for example, a sofa with a choice of fabric colors and finishes.
8. 3D Printing
Also known as additive manufacturing, 3D printing is a relatively new manufacturing process. 3D printing uses a digital model to make three-dimensional products layer by layer via various raw materials such as metals and plastic polymers or composite plastics.
Though this type of manufacturing process has high startup costs, it provides savings in other areas. Businesses that employ 3D printing save on financial capital, raw materials, and various forms of waste.
Goods produced using 3D printing include building materials, musical instruments, shoes, firearms, prosthetic limbs, and medical devices.
Common bottlenecks in manufacturing & how to prevent them
Unfortunately, most production lines aren’t without their share of bottlenecks. It’s not unusual for unforeseen elements to slow manufacturing systems, limiting production capacity. Therefore, it’s essential to take a continuous improvement approach by analyzing processes for inefficiencies.
Common bottlenecks manufacturers should be watchful for include:
Throughput
Throughput is the amount of products an organization can produce within a specified period. The longer it takes to run a particular process from start to finish, the more the production costs mount up, so the aim is to reduce throughput time and gain cost efficiency.
Production can slow due to poorly maintained machinery, inefficient processes, ineffective use of people and resources, or a factory layout that isn't conducive to efficient work.
Tools such as the 5 Whys and Ishikawa diagrams can help you identify the root cause of the issue and resolve throughput bottlenecks. You may need to analyze your maintenance work orders to ensure equipment is being maintained properly, reconfigure your production line, or take a closer look at standard operating procedures.
A CMMS like MaintainX can provide valuable insights that make speeding up throughput an easy task.
Accumulation
Assembly line supervisors should scan for a build-up of products or materials several times throughout the day. It’s not unusual for products to get stuck when passing from one production phase to the next, and both machine and operator malfunctions can be at fault in such situations.
In some cases, improved worker training and more precise standard operating procedures are enough to fix the problem. Kanban cards or boards can also help control the amount of work in progress and limit the accumulation of excess inventory, which can lead to bottlenecks.
Many CMMS systems like MaintainX allow minimum and maximum inventory levels to be set, along with mapping out lead time for components and other critical information. MaintainX also includes work order management and reporting features for deeper insights into WIP times, MTTR, asset utilization, and more, which can help you manage product accumulation issues.
Downtime and idle time
Production lines that involve several machines operating at high volumes can be prone to experiencing unexpected breakdowns. Equipment downtime holds up production processes, often causing ripple effects across other departments. CMMS software like MaintainX can help O&M managers automate preventive maintenance scheduling to reduce the likelihood of equipment downtime.
Similar issues can be due to equipment or worker idle time, where a machine is in working order but not being used effectively. Comparing your production processes to lean manufacturing principles will help your organization analyze where small improvements can be made to utilizing equipment and people.
Full capacity
Every production unit has a built-in output capacity. Machines within each process stage typically work within a fractional percentage of their total power. However, if machine operators mistakenly set one device to work faster than the others, the entire system could collapse due to mistimed production processes.
Manufacturers can use the 5 Whys Method to determine the root cause of such productivity blocks. Then, after identifying primary issues, they should use lean manufacturing principles to minimize future capacity problems. Inspecting and maintaining machinery, as well as following standard operating procedures, is a good first step to ensure all equipment is functioning as planned.
SOPs and inspection checklists are easy to manage in a user-friendly system like MaintainX, which provides both technicians and production managers with the tools they need to carry out their roles effectively.
Streamline manufacturing processes with MaintainX
Manufacturers are increasingly pairing CMMS software with automated digital systems and machine sensors to eliminate bottlenecks, optimize processes, and achieve better ROI.
MaintainX can help you achieve this in your organization — see for yourself by quantifying potential cost savings with our ROI calculator
MaintainX mobile work order software allows production managers to create, oversee, and assign work orders, as well as standardize production processes with user-friendly checklists. Manage inventory with automated AI-powered alerts, reduce asset downtime, and streamline your entire manufacturing process with MaintainX.
Manufacturing Processes FAQs
What is Industry 4.0 and Why is It Important for Manufacturing Processes?
Industry 4.0, also known as the Fourth Industrial Revolution, refers to the integration of advanced digital technologies (like IoT, AI, Big Data, and automation) into the manufacturing process to create "smart factories" that are highly connected and efficient.
What is the Role of Automation in Modern Manufacturing?
Automation involves the use of machines and technology to perform tasks with minimal human intervention. It plays a crucial role in increasing efficiency, reducing labor costs, and improving precision in manufacturing processes.
What is the Role of Maintenance in Manufacturing?
Maintenance involves the activities and practices aimed at ensuring that equipment, machinery, and facilities in a manufacturing plant are in optimal working condition. It helps prevent breakdowns, extend equipment life, and maintain production efficiency.
What’s the difference between manufacturing and processing?
Processing is a broad term that includes all forms of manufacturing. However, organizations don’t always classify processing as manufacturing.
Processing refers to the mechanical or chemical actions that transform raw materials during production. On the other hand, manufacturing is a form of processing that yields finished products for customers.
Whereas the primary objective of manufacturing is always creating a product for a customer, the goal of processing, however, may not necessarily involve serving customers. Processing may occur on a smaller scale, while manufacturing is almost always a large-scale production.
What is mass production?
Mass production is the practice of producing surplus goods according to forecasted demand rather than actual present-day customer demand.
Mass production aims to create standardized products in large numbers, without deviations, so that all manufactured goods look, feel, and perform in the same way. For this reason, stringent quality control standards are necessary, as well as efficient manufacturing processes that allow workers to move through each stage of product development without setbacks.
Often, businesses can save money by investing upfront in a large number of raw materials for production, with surplus products stored in warehouses awaiting customer orders. Large stock holdings of raw materials combined with investment in processing equipment means mass production has high startup costs.
However, by manufacturing products in high volume, organizations can achieve economies of scale that are not possible when manufacturing to order or in smaller quantities.
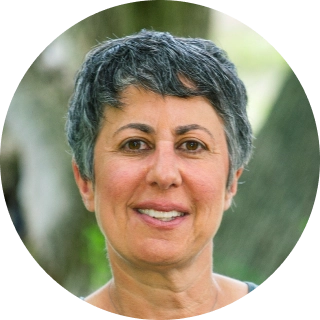
Caroline Eisner is a writer and editor with experience across the profit and nonprofit sectors, government, education, and financial organizations. She has held leadership positions in K16 institutions and has led large-scale digital projects, interactive websites, and a business writing consultancy.