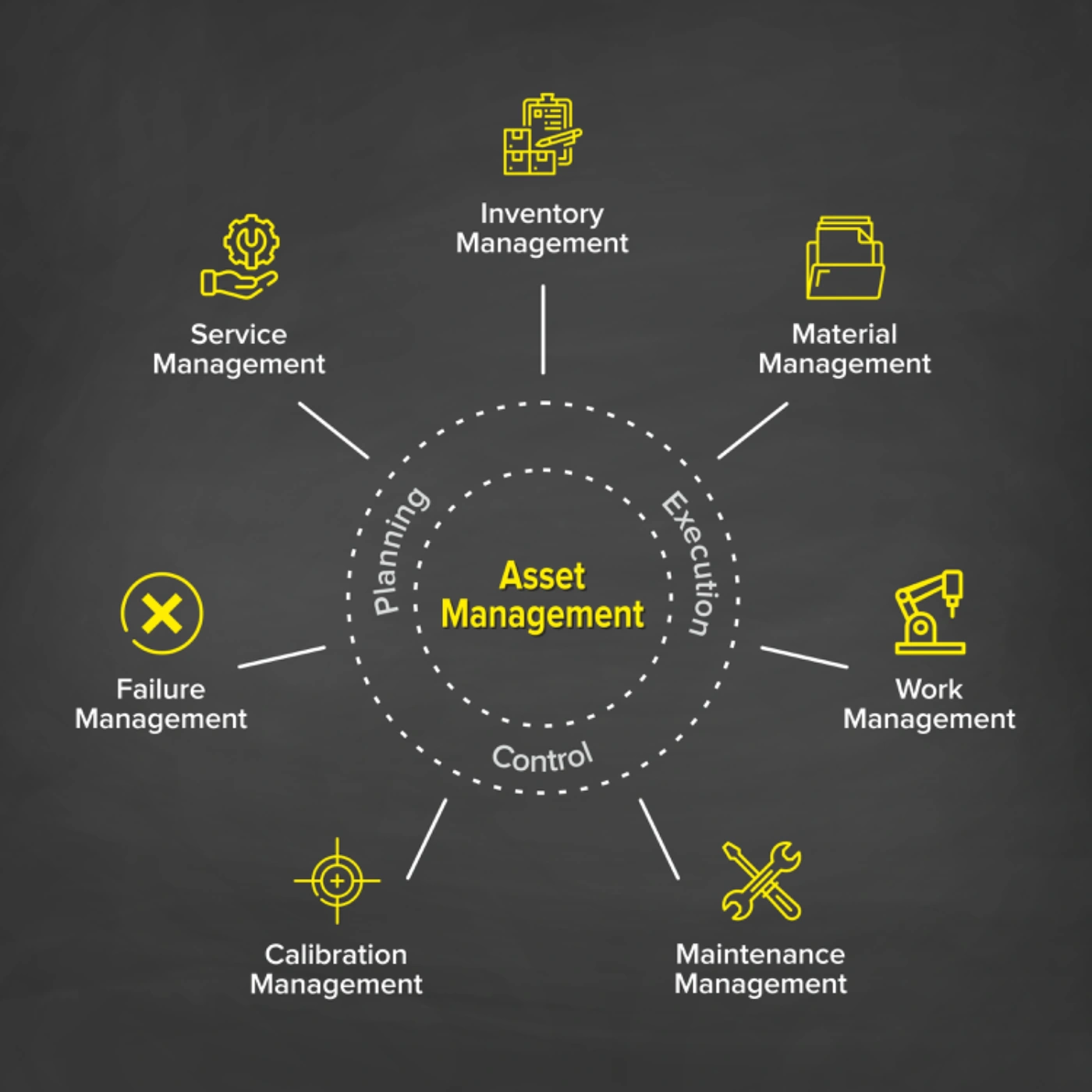
Enterprise asset management (EAM) is a strategy that uses software, systems, and services to manage maintenance and sustain a company’s physical and operational assets throughout the assets’ entire lifecycles.
Lifecycle management is a vital part of EAM, and it includes strategies to handle aspects such as procurement, installation, asset performance, asset maintenance, inventory management, asset utilization, asset tracking, and all other parts of the asset management process.
A proper EAM strategy aims to help teams optimize the quality of their physical assets and equipment, decrease downtime, and increase profitability by reducing operational costs and managing spare parts and supply chain challenges. Enterprise asset management should thus focus primarily on implementing preventive maintenance strategies. This strategy helps prevent breakdowns and prolong productive uptime for critical assets.
However, there are additional factors to consider when building an EAM strategy for your maintenance team. Let’s look at some best practices to apply when crafting your EAM approach.
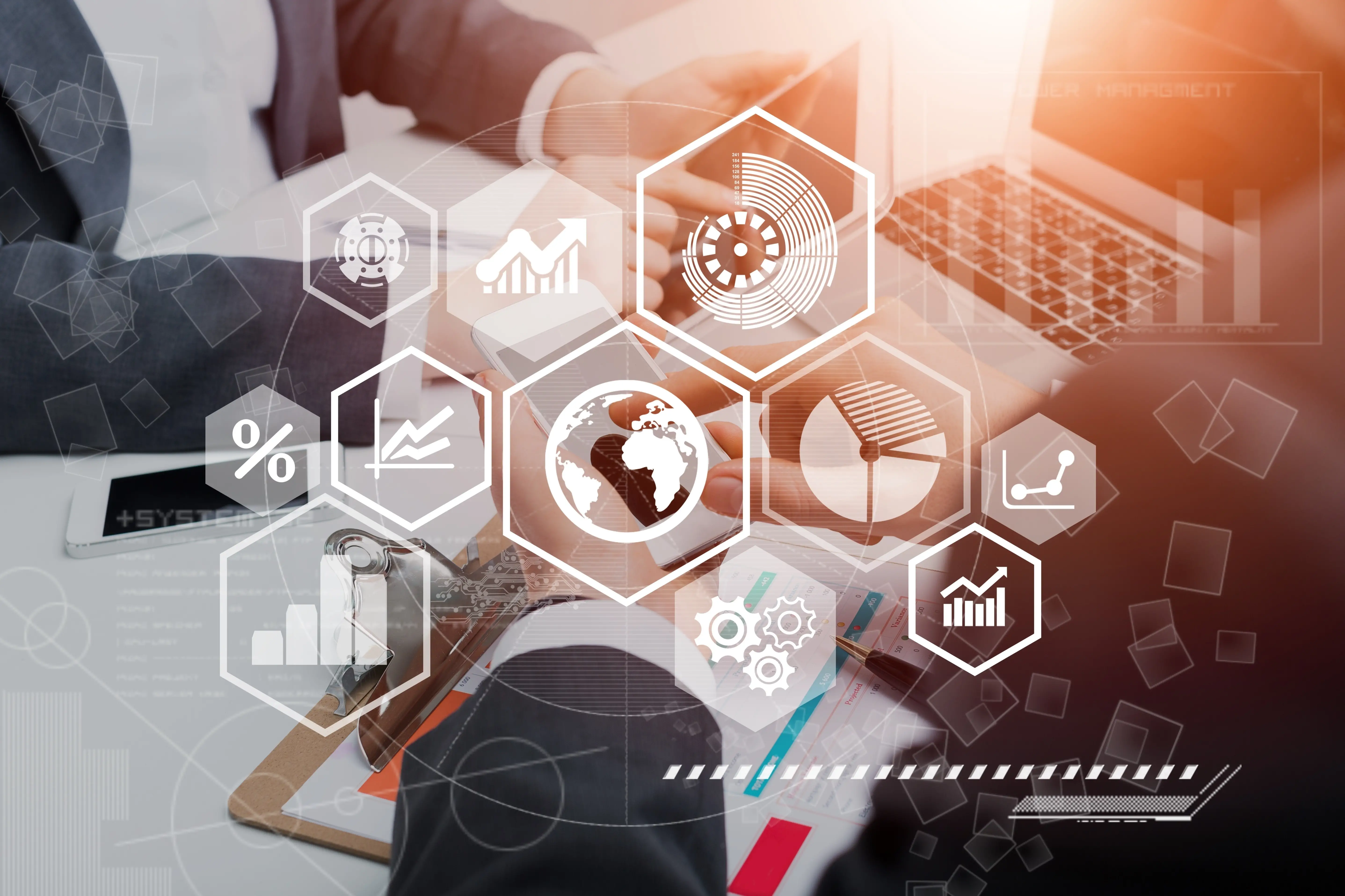
EAM Best Practices
How you choose to optimize your asset lifecycle management will look different for every team. A good system considers your facility and team’s unique circumstances.
What kinds of assets do you have? How long have you had them? What are your production goals? Outside of those questions, here are some standard principles to always remember.
Facilitate Easy Communication
Remember, EAM is all about the asset lifecycle. You want to get the best out of your assets before you even buy them and until you’re ready to dispose of them. Succeeding requires multiple teams or departments working closely to ensure this.
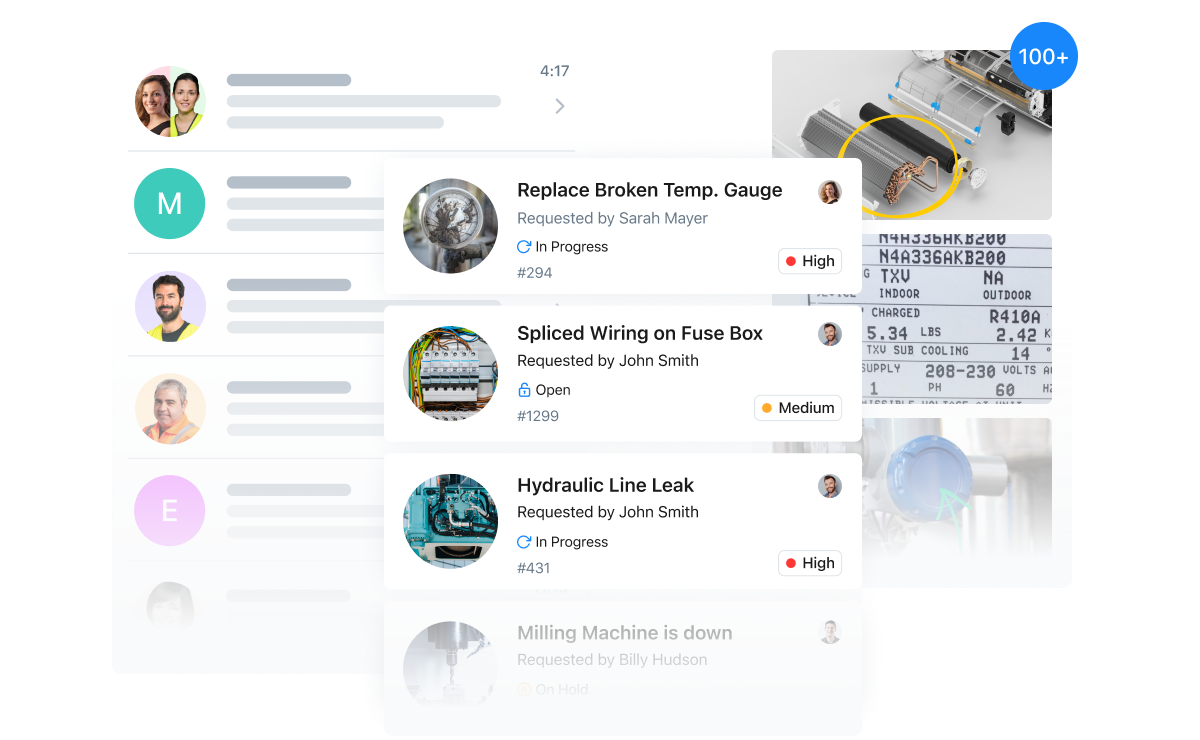
Procurement teams must work with finance teams to be sure the purchase aligns with the company’s financial standing and goals. Manufacturing teams must work with maintenance teams to ensure the assets run smoothly and are not out of commission due to breakdowns. Using enterprise asset management software (EAM software) is one way to help facilitate communication within your team. But more on that later.
Facilitate Collaboration and Accessibility
In addition to communication, you want to ensure that maintenance teams can collaborate across distances if necessary. This could be via ensuring that technicians can access assets or asset data on the go or by using connected worker platforms that allow workers to collaborate wherever they are.
Standardize Processes
This makes things much easier for your staff. As much as you want your workers to take initiative, you don’t want them confused and having to choose between multiple approaches to solve a problem.
Setting consistent guidelines for approaching any aspect of the lifecycle will save time. Having a consistent approach to your workflows will also help if things go wrong, as you can perform audits to identify the source of a problem.
Capture and Track Data
This principle is in line with aiming for a robust maintenance strategy. You can’t have a proper maintenance strategy without consistent data. For example, with preventive maintenance, good asset data can help you determine how to organize your maintenance strategy.
Predictive maintenance also depends on consistent asset information to identify and predict when breakdowns will likely occur based on past performance. Keeping track of such information allows for data-driven decision-making regarding optimizing your maintenance work and overall business processes.
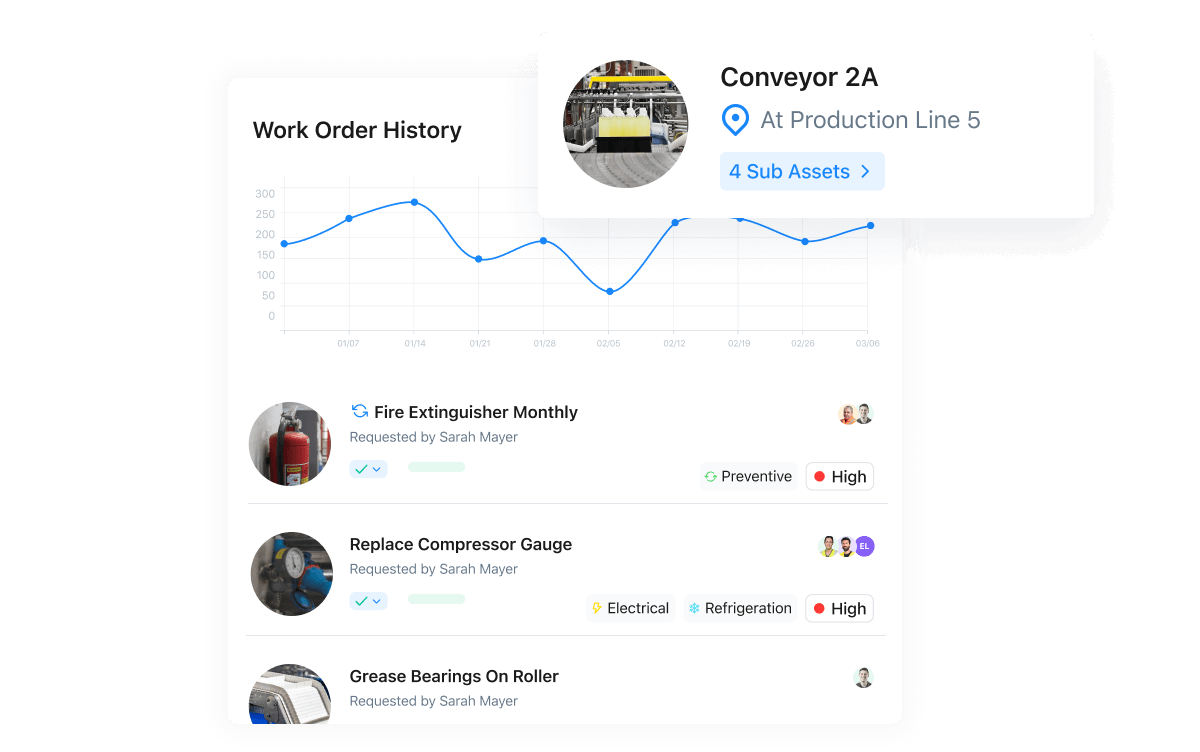
Use Preventive Maintenance
One of the main goals of an EAM strategy is to reduce costs. Doing this will involve reducing maintenance costs. Preventive Maintenance is one of the best ways to do this. It’s often more manageable and less costly to fix problems when they are still minor.
Ignoring a small problem might mean you spend much more money fixing a more significant problem later.
In the case of breakdowns, you lose in more than one way as the machine is also out of commission, which means less production and less revenue coming in. A good maintenance management strategy will include plans for reactive maintenance.
Still, you want to ensure you direct most of your efforts toward preventive actions. This approach will help save money, increase uptime, and prolong your asset life. Consider using a computerized maintenance management system (CMMS) to institute preventive maintenance for your team.
How Can EAM Software Help?
We’ve looked at some enterprise asset management best practices, but how can you execute these in the easiest way? If you’re considering a software solution, here are some ways that good software can help.
Helps Facilitate Communication
This may not be the first thing you think of when you consider EAM solutions. However, many EAM software on the market today go beyond work order management to offer communication avenues for team members. MaintainX, for example, is a work order software that allows for communication across departments and between workers via real-time chat.
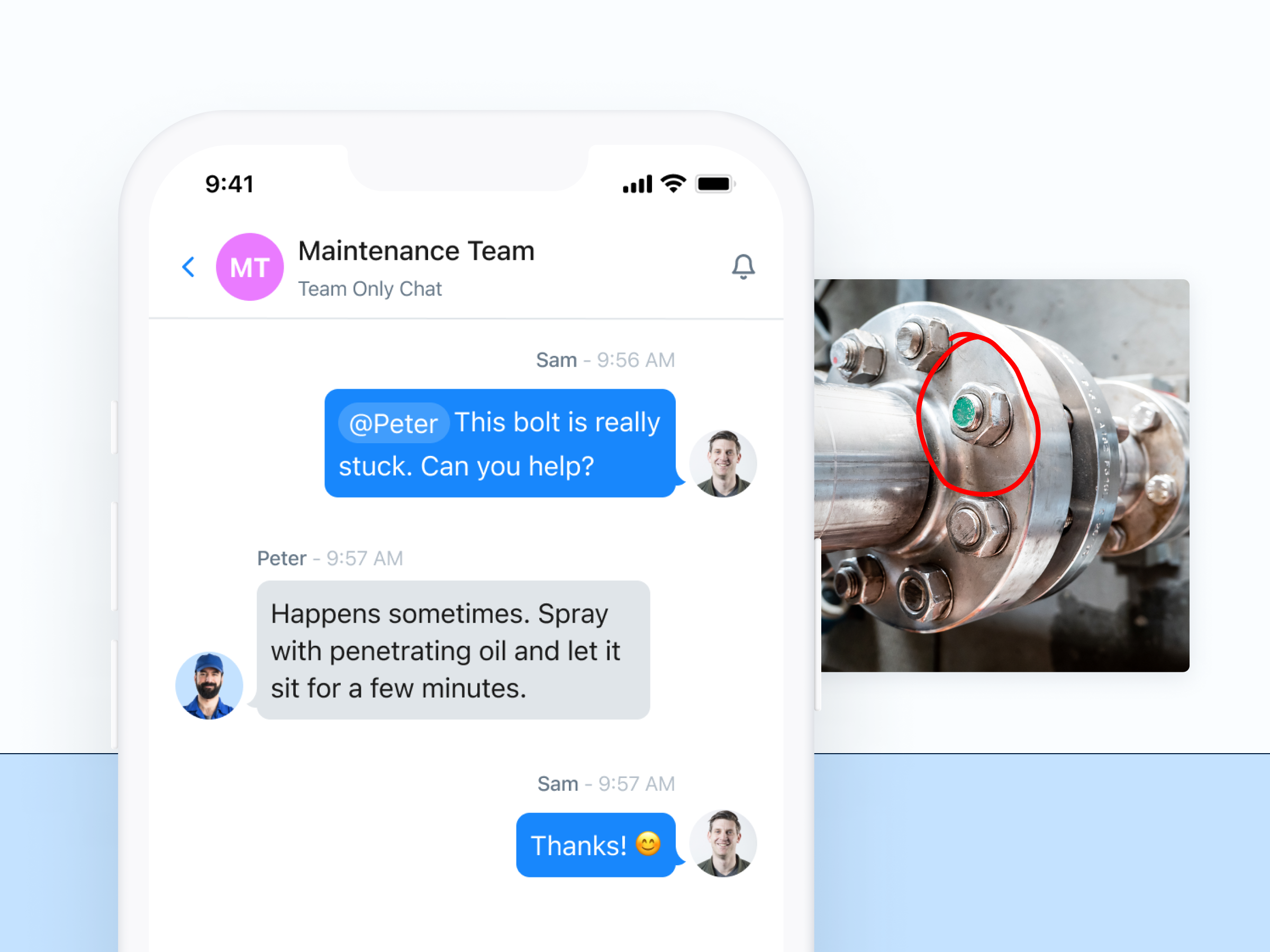
Helps with Standards
If you want to create standard operating procedures, you might want to go the pen-and-paper route, especially if it’s already working for you. However, enterprise asset management solutions seek to reduce operational costs, and one way to do this is to save time. Software can simplify your processes by allowing you to create digital SOPs that your staff can access via their mobile devices. MaintainX offers cloud-based storage and a global procedure library that enables you to access your SOPs as well as other global procedures.
Helps with Preventive Maintenance
EAM software can simplify your preventive maintenance by allowing you to automate work orders according to any maintenance schedule you like. A solution like MaintainX will enable you to create repeatable work orders in advance, along with work instructions, and assign the task to the appropriate technician.
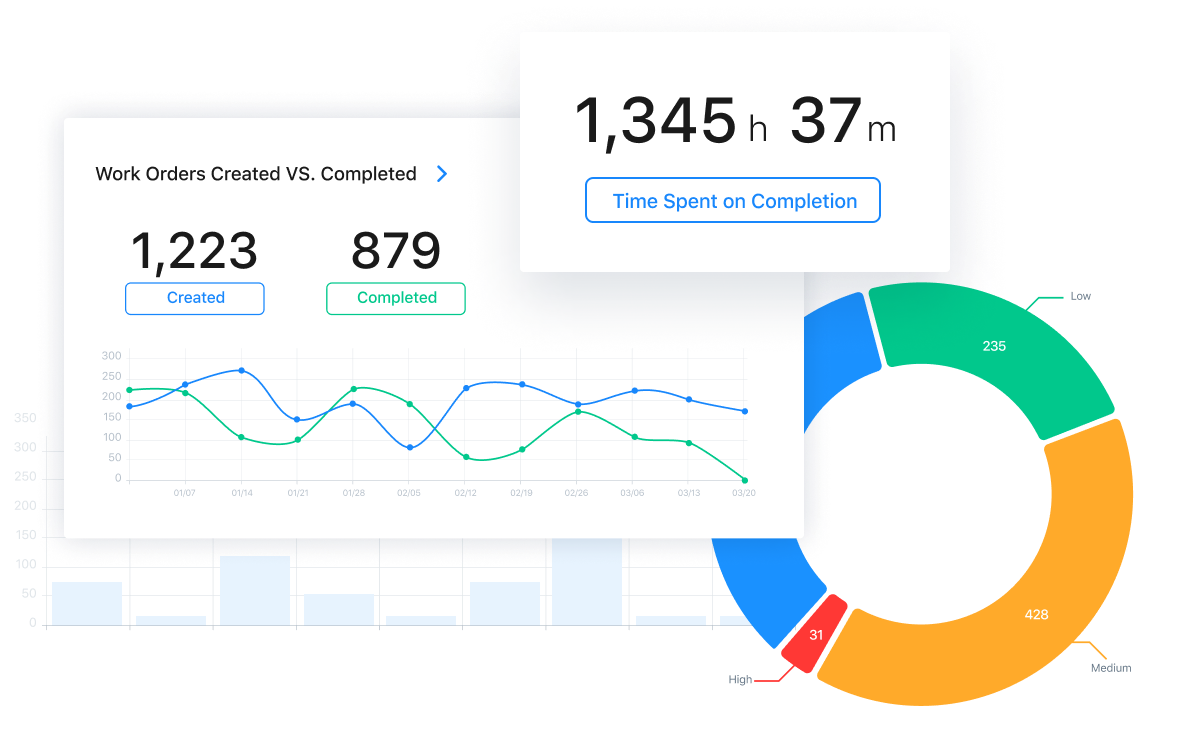
Helps with Tracking
To be sure that your maintenance activities are working as you want them to, you need to track your asset data. EAM systems can help you monitor your metrics and Key Performance Indicators (KPIs) to understand how you are doing. In addition to helping with structuring your preventive maintenance, you can use this data to perform audits and root cause analysis if need be.
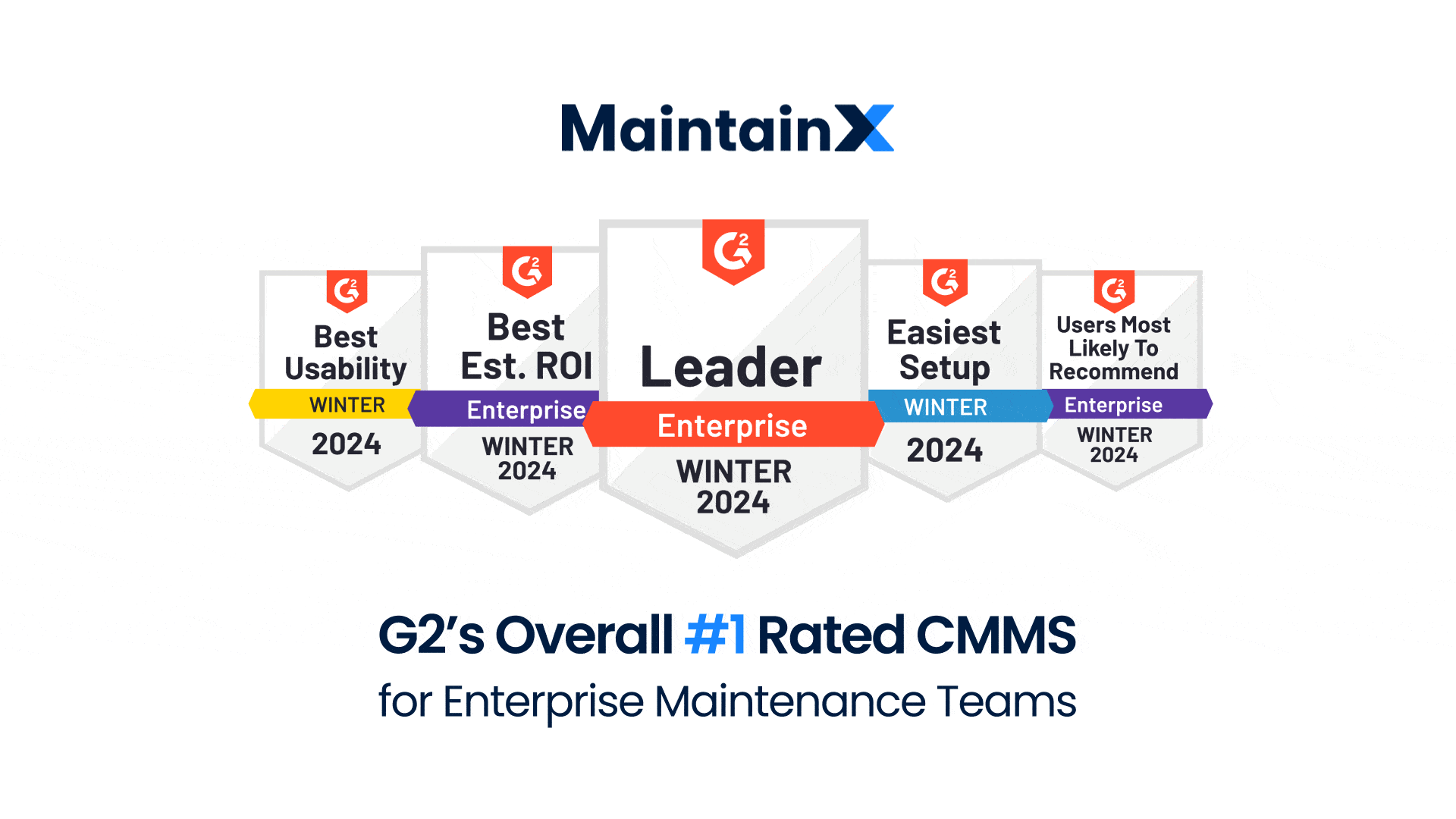
Simplify Your Enterprise Asset Management with MaintainX
Ready to take your Enterprise Asset Maintenance to the next level? Use MaintainX to streamline your workflows and optimize your business processes. With repeatable work orders, digital SOPs, and reporting dashboards, MaintainX can help you with:
- Asset Lifecycle Management
- Work Order Management
- Inventory Management
- Maintenance, Repair, and Operations (MRO) Materials Management
- Reporting Analytics
FAQs
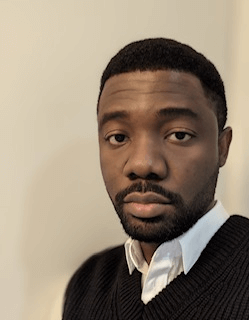
Lekan Olanrewaju is a content writer with years of experience in media and content creation. He has held positions at various media organizations, working with and leading teams at print magazines, digital publications, and television productions.